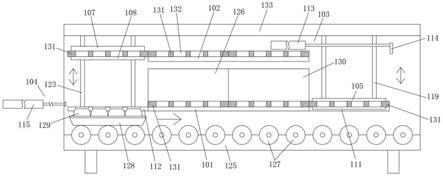
银耳基质装罐导向板循环输送机构
1.技术领域:
2.本实用新型涉及一种银耳基质装罐导向板循环输送机构。
3.
背景技术:4.现有的银耳自动化培养技术中,需要通过装罐机将银耳培养基质装入培养罐中。但由于培养罐质量较轻,在装罐过程中培养罐容易在培养基质的冲击下出现倾倒,或者出现培养罐的罐口与装罐机的输出口未正对,进而出现装罐失败。为了解决该问题,通常会在装罐机的输出口与培养罐之间放置导向板,培养基质穿过导向板后进入培养罐中。然而,现有技术中通常是人工对导向板进行取放,不仅操作不便,增加人工劳动强度,而且影响装罐效率。
5.
技术实现要素:6.本实用新型针对上述现有技术存在的问题做出改进,即本实用新型所要解决的技术问题是提供一种银耳基质装罐导向板循环输送机构,不仅设计合理,而且降低人工劳动强度,提高装罐效率。
7.为了实现上述目的,本实用新型采用的技术方案是:一种银耳基质装罐导向板循环输送机构,包括设于装罐机与培养罐输送组件之间且用于沿横向输送导向板的一对进料滑轨,一对进料滑轨的上方平行设有一对出料滑轨,所述进料滑轨的前侧设有用于将导向板提升至正对出料滑轨的顶料机构,所述顶料机构的上方设有用于推动提升后的导向板向后移动至出料滑轨的前推料机构;所述出料滑轨的后侧设有用于将导向板下放至正对进料滑轨的下料机构,所述进料滑轨的后侧设有用于推动下放后的导向板向前移动至进料滑轨的后推料机构。
8.进一步的,所述顶料机构包括与一对进料滑轨相平行的一对顶料座,所述顶料座由第一动力机构驱动沿竖向升降,顶料座的下端设有用于托住导向板的顶料托板;所述下料机构包括与一对进料滑轨相平行的一对下料座,所述下料座由第二动力机构驱动沿竖向升降,下料座的下端设有下料托板,所述下料托板由固定在下料座的纵向气缸驱动沿纵向移动。
9.进一步的,一对进料滑轨、一对出料滑轨、一对顶料座以及一对下料座在右方向对齐分布;一对进料滑轨的前、后侧分别平行设有一对前支撑滑轨和一对后支撑滑轨,所述前支撑滑轨与后支撑滑轨位于同一水平面,一对前支撑滑轨之间的间距与一对后支撑滑轨之间的间距相同,且均小于一对进料滑轨之间的间距。
10.进一步的,所述下料座的下端设有与下料托板相适应的纵向通孔,所述纵向气缸安装在纵向通孔内,纵向气缸驱动下料托板从纵向通孔伸出并托住导向板。
11.进一步的,所述前推料机构包括平行设于一对出料滑轨中间的前推料气缸,所述前推料气缸的气缸杆向前伸出且末端固定有前推料板,所述前推料板用于与导向板的前侧面中部相接触;所述后推料机构包括平行设于一对进料滑轨中间的后推料气缸,所述后推料气缸的气缸杆向前伸出且末端固定有后推料板,所述后推料板用于与导向板的后侧面中部相接触。
12.进一步的,所述第一动力机构包括第一连杆、第一曲柄、第一竖向导杆以及第一电机,所述第一连杆竖直设置,第一连杆的上端与顶料座相铰接,第一连杆的下端与第一曲柄的一端相铰接,所述第一曲柄的另一端与第一电机相连接;所述顶料座的前后两端分别与第一竖向导杆滑动配合;所述第二动力机构包括第二连杆、第二曲柄、第二竖向导杆以及第二电机,所述第二连杆竖直设置,第二连杆的上端与下料座相铰接,第二连杆的下端与第二曲柄的一端相铰接,所述第二曲柄的另一端与第二电机相连接;所述下料座的前后两端分别与第二竖向导杆滑动配合。
13.进一步的,所述培养罐输送组件包括若干根横向间隔均布的输送辊,所述输送辊沿纵向设置,输送辊上设有输料框,所述输料框内设有多个呈矩阵分布的培养罐;所述导向板上开设有与多个培养罐的罐口位置相对应的竖向落料孔。
14.与现有技术相比,本实用新型具有以下效果:本实用新型设计合理,可实现导向板在竖向呈环形循环输送,无需人工频繁对导向板进行取放操作,有效解放手工操作,提高培养基质装罐效率。
15.附图说明:
16.图1是本实用新型实施例的主视构造示意图;
17.图2是图1中的省略导向板的构造示意图;
18.图3是本实用新型实施例的左视构造示意图;
19.图4是图3中导向板向下移动后的状态示意图;
20.图5是图3的侧视构造示意图;
21.图6是本实用新型实施例的右视构造示意图;
22.图7是图6中导向板向上移动后的状态示意图;
23.图8是图7的侧视构造示意图;
24.图9是图2中的b-b剖面示意图;
25.图10是图2中的c-c剖面示意图。
26.图中:
27.101-进料滑轨;102-出料滑轨;103-前推料机构;104-后推料机构;105-顶料座;106-顶料托板;107-下料座;108-下料托板;109-纵向气缸;110-纵向通孔;111-前支撑滑轨;112-后支撑滑轨;113-前推料气缸;114-前推料板;115-后推料气缸;116-后推料板;117-第一连杆;118-第一曲柄;119-第一竖向导杆;120-第一电机;121-第二连杆;122-第二曲柄;123-第二竖向导杆;124-第二电机;125-培养罐输送组件;126-装罐机;127-输送辊;128-输料框;129-培养罐;130-基质压入工位;131-导向板;132-竖向落料孔;133-机架。
28.具体实施方式:
29.下面结合附图和具体实施方式对本实用新型做进一步详细的说明。
30.在本实用新型的描述中,需要理解的是,术语
“ꢀ
纵向”、
“ꢀ
横向”、
“ꢀ
上”、
“ꢀ
下”、
“ꢀ
前”、
“ꢀ
后”、
“ꢀ
左”、
“ꢀ
右”、
“ꢀ
竖直”、
“ꢀ
水平”、
“ꢀ
顶”、
“ꢀ
底”、
“ꢀ
内”、
“ꢀ
外”等指示的方位或位置关系为基于附图所示的方位或位置关系,仅是为了便于描述本实用新型,而不是指示或暗示所指的装置或元件必须具有特定的方位、以特定的方位构造和操作,因此不能理解为对本实用新型的限制。
31.如图1~10所示,本实用新型一种银耳基质装罐导向板循环输送机构,包括设于装
罐机126与培养罐输送组件125之间的一对进料滑轨101,一对进料滑轨101用于沿横向输送导向板131,一对进料滑轨101的上方平行设有一对出料滑轨102,一对出料滑轨102位于装罐机126上方,所述进料滑轨101的前侧设有用于将从进料滑轨101前端输出的导向板131向上提升至正对出料滑轨102的顶料机构,所述顶料机构的上方设有用于推动提升后的导向板131向后移动至出料滑轨102的前推料机构103;所述出料滑轨102的后侧设有用于将出料滑轨102后端输出的导向板131下放至正对进料滑轨101的下料机构,所述进料滑轨101的后侧设有用于推动下放后的导向板131向前移动至进料滑轨101的后推料机构104。进料滑轨、顶料机构、出料滑轨以及下料机构形成在竖向呈环形循环输送,实现导向板的循环输送。具体使用时,后推料机构将下料机构下放的导向板向前推动,之后下料机构向上移动至正对出料滑轨,进料滑轨上的其他导向板在该推力的作用下沿着进料滑轨向前移动,且在移动过程中与培养罐输送组件相同步,确保导向板与培养罐相正对,位于装罐机正下方的导向板起到装罐导向作用;而装罐结束后又在后推料机构的推力作用下向前移动至顶料机构,顶料机构将该导向板向上提升至正对出料滑轨,而前推料机构将该导向板向后推动,出料滑轨上的其他导向板在该推力的作用下沿着出料滑轨相后移动,下料机构呈接住从出料滑轨后端输出的导向板,依此循环,实现导向板的循环输送。
32.本实施例中,一对进料滑轨101和一对出料滑轨102均呈左右分布,且位置相对应,进料滑轨101和出料滑块102的截面可均呈l形状。
33.本实施例中,所述顶料机构包括与一对进料滑轨101相平行且左右位置相正对的一对顶料座105,所述顶料座105由第一动力机构驱动沿竖向升降,顶料座105的下端设有用于托住导向板131的顶料托板106,顶料托板与顶料座形成l形结构。
34.本实施例中,所述下料机构包括与一对进料滑轨101相平行且左右位置相正对的一对下料座107,所述下料座107由第二动力机构驱动沿竖向升降,下料座107的下端设有下料托板108,所述下料托板108由固定在下料座107的纵向气缸109驱动沿纵向移动。优选的,所述下料座107的下端设有与下料托108板相适应的纵向通孔110,所述纵向气缸109安装在纵向通孔110内,纵向气缸109驱动下料托板108从纵向通孔110伸出并托住导向板131。工作时,当下料座与出料滑轨相正对时,纵向气缸驱动下料托板伸出,以呈接从出料滑轨后端输出的导向板;之后下料座在第二动力机构的驱动下沿竖向下降至与进料滑轨正对。
35.本实施例中,一对进料滑轨101、一对出料滑轨102、一对顶料座105以及一对下料座107在右方向对齐分布。
36.本实施例中,一对进料滑轨101的前、后侧分别平行设有一对前支撑滑轨111和一对后支撑滑轨112,所述前支撑滑轨111与后支撑滑轨112位于同一水平面,一对前支撑滑轨111之间的间距与一对后支撑滑轨112之间的间距相同,且均小于一对进料滑轨101之间的间距。通过在进料滑轨101的后侧设置后支撑滑轨112,当下料机构带动导向板131向下移动至与进料滑轨101相正对时,后支撑滑轨112可对该导向板起到支撑效果,便于后续后推料机构104推动其向前移动,同时间距较小的后支撑滑轨112可避免对下料托板108产生干涉。同理,通过在进料滑轨101的前侧设置前支撑滑轨111,可对进料滑轨101前端输出的导向板131起到支撑效果,便于顶料托板106将该导向板向上顶起,同时间距较小的前支撑滑轨,可避免对顶料托杆产生干涉。
37.本实施例中,所述前推料机构103包括平行设于一对出料滑轨102中间的前推料气
缸113,所述前推料气缸113的气缸杆向前伸出且末端固定有前推料板114,所述前推料板114用于与导向板的前侧面中部相接触。工作时,当顶料托板106带动导向板向上移动至与出料滑轨102相正对时,此时顶料托板106位于前推料板114的左侧,前推料气缸113驱动前推料板114向后移动,前推料板114与导向板的前侧面中部相接触,前推料板114推动该导向板向后移动,此时出料滑轨102上的导向板相接触,在前推料板114的推力作用下,出料滑轨102上的导向板都向后移动。
38.本实施例中,所述后推料机构104包括平行设于一对进料滑轨101中间的后推料气缸115,所述后推料气缸115的气缸杆向前伸出且末端固定有后推料板116,所述后推料板116用于与导向板的后侧面中部相接触。工作时,当下料托板108带动导向板向下移动至与进料滑轨101相正对时,此时后推料板116位于导向板的后侧,后推料气缸115驱动后推料板116向前移动,后推料板116与导向板的后侧面中部相接触,后推料板推动该导向板向前移动,此时进料滑轨101上的导向板相接触,在后推料板116的推力作用下,进料滑轨101上的导向板都向前移动,即:新的导向板移动至装罐机正下方,而原先装罐机正下方的导向板则向前移动,这个移动过程与培养罐的输送相对应,使导向板与培养罐位置相对应。
39.本实施例中,如图6-8所示,所述第一动力机构包括第一连杆117、第一曲柄118、第一竖向导杆119以及第一电机120,所述第一连杆竖直设置,第一连杆的上端与顶料座相铰接,第一连杆的下端与第一曲柄的一端相铰接,所述第一曲柄的另一端与第一电机相连接;所述顶料座的前后两端分别与第一竖向导杆滑动配合。第一连杆、第一曲柄以及顶料座构成曲柄滑块机构,第一电机驱动第一曲柄旋转,第一曲柄旋转过程中通过第一连杆带动顶料座沿着第一竖向导杆移动,进而实现顶料座在竖向升降。
40.本实施例中,如图3-5所示,所述第二动力机构包括第二连杆121、第二曲柄122、第二竖向导杆123以及第二电机124,所述第二连杆竖直设置,第二连杆的上端与下料座相铰接,第二连杆的下端与第二曲柄的一端相铰接,所述第二曲柄的另一端与第二电机相连接;所述下料座的前后两端分别与第二竖向导杆滑动配合。第二连杆、第二曲柄以及下料座构成曲柄滑块机构,第二电机驱动第二曲柄旋转,第二曲柄旋转过程中通过第二连杆带动下料座沿着第二竖向导杆移动,进而实现下料座在竖向升降。
41.本实施例中,所述培养罐输送组件125包括若干根横向间隔均布的输送辊127,所述输送辊127沿纵向设置,输送辊由链条机构驱动旋转。应说明的是,这部分结构为现有技术,此处不做过多重复赘述。可通过控制程序的设定让输送辊的输送速度与后推料板的移动速度相对应,这样可使得导向板与输送辊的输送速度相对应,使两者的位置可以相对应,这些也都是现有技术,此处不做过多重复赘述。
42.本实施例中,输送辊127上设有槽型状的输料框128,输料框128的顶部为敞口,所述输料框128内设有十六个呈矩阵分布的培养罐129;所述导向板131上开设有与十六个培养罐的罐口位置相对应的十六个竖向落料孔132,当导向板与培养罐移动至装罐机正下方时,装罐机的输出口与竖向落料孔相衔接,培养基质从装罐机的输出口落入竖向落料孔,进而进入培养罐中。应说明的是,装罐机为现有设备,直接采购得到,此处不再对其构造及原理做过多重复赘述。
43.本实施例中,装罐机126与培养罐输送组件125均安装在机架133上。
44.具体实施过程:初始状态时,多个装有十六个呈矩阵分布的培养罐129的输料框
128在输送辊127上沿横向依次输送,进料滑轨101与出料滑轨102上均有两块导向板131,进料滑轨101上的两块导向板中,一块位于装罐机126的正下方,另一块位于基质压入工位130处(基质压入工位位于装罐机的前侧),而前支撑滑111轨上具有一块导向板,顶料托板106位于前支撑滑轨111的下侧,而下料托板108与出料滑轨102相正对,下料托板108上具有一块导向板,工作时:(1)第二电机125通过第二曲柄122和第二连杆121驱动下料座107沿着第二竖向导杆123向下移动,直至下料托板108位于后支撑滑轨112的下侧,此时下料托板108上的导向板落在后支撑滑轨112上,之后纵向气缸109驱动下料托板108收缩至纵向通孔110内,第二电机124通过第二曲柄122和第二连杆121驱动下料座104沿着第二竖向导杆123向上移动至初始位置,纵向气缸109驱动下料托板108伸出,以便呈接下一块导向板;(2)后支撑滑轨112上的导向板131与位于其下方的输料框128相正对,输送辊127驱动输料框128向前移动,而后推料气缸115驱动后推料板116向前移动,后推料板116与后支撑滑轨112上的导向板后侧面中部相接触,后推料板116推动该导向板向前移动,此时进料滑轨101上的导向板相接触,在后推料板116的推力作用下,进料滑轨101上的导向板都向前移动,即:新的导向板移动至装罐机126正下方,而原先装罐机126正下方的导向板则向前移动至基质压入工位130,而原先基质压入工位130处的导向板则移动至前支撑滑轨111上,这个移动过程与培养罐的输送相对应,使导向板与培养罐位置相对应;(3)第一电机120通过第一曲柄118和第一连杆117驱动顶料座105沿着第一竖向导杆119向上移动,顶料托板106与前支撑滑轨111处的导向板的底面相接触,顶料托板106带动该导向板向上移动至与出料滑轨102相正对,之后顶料座105向下复位;(4)前推料气缸113驱动前推料板114向后移动,前推料板114与导向板的前侧面中部相接触,前推料板114推动该导向板向后移动,此时出料滑轨102上的导向板相接触,在前推料板114的推力作用下,出料滑轨102上的导向板都向后移动,而从出料滑轨102后端输出的导向板则移动至下料托板108上,之后前推料板114向前复位;(5)重复步骤(1)-(4),实现导向板的循环输送。
45.本实用新型如果公开或涉及了互相固定连接的零部件或结构件,那么,除另有声明外,固定连接可以理解为:能够拆卸地固定连接( 例如使用螺栓或螺钉连接),也可以理解为:不可拆卸的固定连接(例如铆接、焊接),当然,互相固定连接也可以为一体式结构( 例如使用铸造工艺一体成形制造出来) 所取代(明显无法采用一体成形工艺除外)。
46.另外,上述本实用新型公开的任一技术方案中所应用的用于表示位置关系或形状的术语除另有声明外其含义包括与其近似、类似或接近的状态或形状。
47.本实用新型提供的任一部件既可以是由多个单独的组成部分组装而成,也可以为一体成形工艺制造出来的单独部件。
48.最后应当说明的是:以上实施例仅用以说明本实用新型的技术方案而非对其限制;尽管参照较佳实施例对本实用新型进行了详细的说明,所属领域的普通技术人员应当理解:依然可以对本实用新型的具体实施方式进行修改或者对部分技术特征进行等同替换;而不脱离本实用新型技术方案的精神,其均应涵盖在本实用新型请求保护的技术方案范围当中。