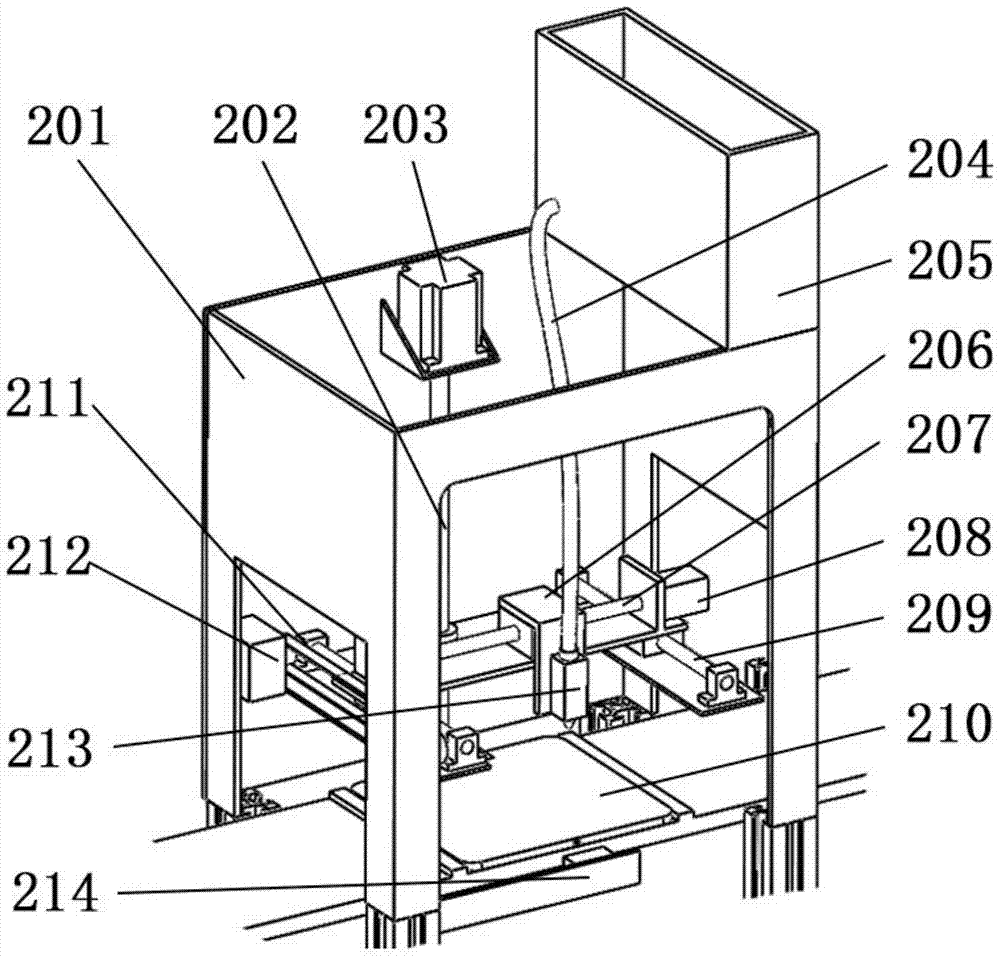
本发明属于快速成型技术领域,特别涉及一种新型并行多工位式工业生产3D打印机。
背景技术:快速成型技术是近年来快速发展起来的基于三维CAD模型数据通过逐层制造生产产品的技术总称,是第三次工业革命的代表性技术之一。它的优势体现在数字化制造和降维分层堆积制造,所以大大降低了制造的难度,对于内部结构越复杂的零件产品,其优势也越明显。目前快速成型技术广泛应用于生物医疗、航空航天、汽车制造等领域,但尚未应用于大规模工业化生产制造,主要原因是现有的快速成型工业生产技术还不成熟,制造成本高,生产效率低等。其实不论是国家战略发展还是制造业的改革,其对于这种快速成型技术工业化生产的潜在要求都是巨大的。因此,应当着力研究一种适合于快速成型技术工业生产的新型并行多工位式3D打印机,大力提高生产效率,加速推进快速成型技术的工业化应用。快速成型技术是利用快速成型设备直接将数字模型转化为实物成品的一种生产制造方式。所谓快速成型设备,则是一种可以直接将任意数字模型转化为最终实物成品的机器。目前主流快速成型技术其基本原理都是叠层制造,由快速原型机在X-Y平面内通过扫描形式形成工件的截面形状,而在Z坐标间断地作层面厚度的位移,最终形成三维制件,主要有以下几种方式:3DP技术:采用3DP技术的3D打印机使用标准喷墨打印技术,通过将液态连结体铺放在粉末薄层上,以打印横截面数据的方式逐层创建各部件,创建三维实体模型,采用这种技术打印成型的样品模型与实际产品具有同样的色彩,还可以将彩色分析结果直接描绘在模型上,模型样品所传递的信息较大。FDM熔融层积成型技术:FDM熔融层积成型技术是将丝状的热熔性材料加热融化,同时三维喷头在计算机的控制下,根据截面轮廓信息,将材料选择性地涂敷在工作台上,快速冷却后形成一层截面。一层成型完成后,机器工作台下降一个高度(即分层厚度)再成型下一层,直至形成整个实体造型。其成型材料种类多,成型件强度高、精度较高,主要适用于成型小塑料件。SLA立体平版印刷技术:SLA立体平版印刷技术以光敏树脂为原料,通过计算机控制激光按零件的各分层截面信息在液态的光敏树脂表面进行逐点扫描,被扫描区域的树脂薄层产生光聚合反应而固化,形成零件的一个薄层。一层固化完成后,工作台下移一个层厚的距离,然后在原先固化好的树脂表面再敷上一层新的液态树脂,直至得到三维实体模型。该方法成型速度快,自动化程度高,可成形任意复杂形状,尺寸精度高,主要应用于复杂、高精度的精细工件快速成型。SLS选区激光烧结技术:SLS选区激光烧结技术是通过预先在工作台上铺一层粉末材料(金属粉末或非金属粉末),然后让激光在计算机控制下按照界面轮廓信息对实心部分粉末进行烧结,然后不断循环,层层堆积成型。该方法制造工艺简单,材料选择范围广,成本较低,成型速度快,主要应用于铸造业直接制作快速模具。DLP激光成型技术:DLP激光成型技术和SLA立体平版印刷技术比较相似,不过它是使用高分辨率的数字光处理器(DLP)投影仪来固化液态光聚合物,逐层的进行光固化,由于每层固化时通过幻灯片似的片状固化,因此速度比同类型的SLA立体平版印刷技术速度更快。该技术成型精度高,在材料属性、细节和表面光洁度方面可匹敌注塑成型的耐用塑料部件。UV紫外线成型技术:UV紫外线成型技术和SLA立体平版印刷技术比较相似类似,不同的是它利用UV紫外线照射液态光敏树脂,一层一层由下而上堆栈成型,成型的过程中没有噪音产生,在同类技术中成型的精度最高,通常应用于精度要求高的珠宝和手机外壳等行业。但上述快速成型技术有打印速度慢,无法有效满足生产的需求;难以批量成产,成产成本过高;使用的材料受打印形式的限制等问题,而且打印出来的零件往往需要进行人工后期处理,工作效率不高。目前市面上常用的三维切片软件有Cura、Makerbot、Kisslicer等,但它们的功能均只局限于对模型进行单一的由下而上地切片,然后把切片数据发送到打印机进行打印,不能对模型的打印时间进行平均分配,并把相应时间段对应的切片分别发送到不同的打印机进行打印。流水线又称为装配线,是一种工业上的生产方式,指每一个生产单位只专注处理某一个片段的工作,以提高工作效率及产量;按照流水线的输送方式大体可以分为:皮带流水装配线、板链线、倍速链、插件线、网带线、悬挂线及滚筒流水线这七类流水线。一般包括牵引件、承载构件、驱动装置、涨紧装置、改向装置和支承件等组成。流水线可扩展性高,可按需求设计输送量、输送速度、装配工位等,在现有的企业中已得到广泛应用。
技术实现要素:针对现有技术的以上缺陷或改进需求,本发明提供了一种新型的适合于快速成型技术的并行多工位式3D打印机,其目的在于提高3D打印生产批量产品时的效率,由此解决传统3D打印生产效率低下的技术问题。在进行单件小批量式生产时,能够保证所有工位上的打印机任务能够平均分配,并且能够使工人能够对打印完成的零部件进行平均有序的后处理,相比起集中打印集中后处理更加协调。本发明所提出的一种并行多工位式3D打印机,其特征在于,包括计算机101、支架103、3D打印机组104和输送带系统106;其中3D打印机组104是根据需要并排放置多个工位的3D打印机;所述3D打印机还包括位置检测传感器214,用于模型在各个工位的准确定位;3D打印机组104、输送带系统106均安装在支架103上;输送带系统106包括伺服电机和传送带300;伺服电机用于驱动传送带;传送带300表面每隔一段距离有一对卡槽301,该卡槽301用于给打印基板定位;在每个卡槽之间的传送带300表面安装有一块定位磁铁302,定位磁铁302上吸附安装一个打印基板210,用于放置打印模型,打印基板为磁性材料;打印基板210侧边缘中心点设有定位标记303;位置检测传感器214用于检测每块打印基板210的位置,以第一个工位的打印基板210为基准,通过检测其余工位上的定位标记303的位置确定后续3D打印机中打印基板210的位置相对于设定位置的偏离量;计算机101与3D打印机组104的各个3D打印机相连,计算机101用于发送操作指令,并将三维模型切片,生成一系列带有序号的截面轮廓图,转换成3D打印机能够识别的代码,送至各个3D打印机进行打印作业;工作时,在计算机101中设定打印速度v,即喷头移动速度,根据3D打印机组104中3D打印机的数量N,将打印模型分块为N个打印时间均等的模型子块;将每个模型子块数据生成打印机能够识别的代码,分别发送到3D打印机组104中每一工位的打印机中;启动打印流程,打印基板在输送带系统106的作用下慢慢移动到各个工位3D打印机下方,每个工位的打印机开始执行各自的打印任务;当所有工位的打印机都完成打印任务,传送带300继续前进;最后一个工位打印机完成打印时,基板运动到输送带末端工位,该工位对应输送带上的定位磁铁302断电消磁,将模型推送到操作平台105上;取出操作平台105上的输出模型,完成打印作业。进一步的,所述的并行多工位式3D打印机中的计算机1根据喷头移动速度和运动路径,算出打印每个模型子块所需时间,再把所有模型子块打印时间相加获得打印零部件总时间T,根据生产线上工位打印机的数量N,重新划分模型子块,使每个模型子块打印时间为T/N。进一步的,所述的并行多工位式3D打印机,其打印原料采用热塑性材料。进一步的,所述的并行多工位式3D打印机,其定位标记303为一条黑色条带或一段凸台,与打印基板210侧边缘其他地方产生颜色或形状差异,能够让位置检测传感器214识别。进一步的,所述的并行多工位式3D打印机在打印作业中,各工位上3D打印机的位置检测传感器214采用光电传感器,其安装中心与该工位上3D打印机的打印原点平行重合。进一步的,所述的并行多工位式3D打印机在打印作业中,计算机101对每个工位打印机的打印轨迹在偏离方向上进行相等距离的补偿,使每个工位的3D打印机打印的部分不会与上一工位3D打印机打印的部分产生错位。进一步的,所述的并行多工位式3D打印机在打印作业中,当第一工位上的位置检测传感器214对准一块打印基板210上的定位标记303时,传送带300停止传动,其余工位上的位置检测传感器214检测其余打印基板210的偏移距离并在计算机101中进行打印轨迹的补偿。本发明提出的打印机有以下特点:1.改变现有间歇式作业方案,将产品分多个环节打印,一条生产线上各个工位打印机分别打印同一个零件的不同部分;2.有一套配套的产品传递机构,用于将已完成该环节打印任务的产品通过基板自给方式传送到下一环节进行打印;3.有一套自动下料机构,用于在打印材料不足时向计算机发出信号,通过控制系统完成自动下料。4.有一套检测识别装置,不同模型有不同识别码,该装置用于识别当前打印的模型,并有序地完成打印;5.有一台计算机,操作员能利用该计算机对整个批量式生产进行控制;总体而言,通过本发明所构思的以上技术方案与现有技术相比,由于采用3D打印机组打印并结合控制软件对打印过程进行合理有序的分工及控制,能够取得下列有益效果:1、模型批量式打印,该并行多工位式3D打印机彻底改变了现有的模式,批量式打印更加符合现代工业生产的特点,能充分利用人力、物力资源。2、能够观察整个打印过程。该并行多工位式3D打印机下工业生产过程中,模型的打印完全透明化,能够很明确地观察到各部分的打印过程,方便在自动化工业生产刚出现问题时及时发现和解决,避免了出现大批量问题产品的可能。3、实现不同部位打印不同材料。在一个实际的产品中,由于各部分的实际功用不同,对其强度、硬度、美观等要求都不太一样,在该并行多工位式3D打印机中能够通过计算机控制在不同部位打印具有不同性质的材料,最大程度降低打印成本和时间。4、靠识别码识别模型,实现完全个性自动化生产。在本发明中,提出用唯一标识码标识每个模型。在打印时,打印机上的标识装置先对标识码进行识别确认,然后按照相应轨迹打印模型,实现完全自动化生产,同时可随时更换识别码来打印其他模型,更加符合个性化生产的需求。5.当打印材料不足时,由打印机自动发出信号到计算机,并由计算机通过控制系统进行自动下料。6.当某一工位打印机打印出现故障时(如电机卡住或原料不足等),控制系统能够自动识别并对系统进行反馈,所在工位有一推送装置把基板自动推出传送带,避免该基板进入下一工位。7.并行多工位式生产节省时间。在传统模式下,打印机的工作是间歇式作业,一台打印机打印一个完整的模型,整个模型打印完后再进行后续加工形成产品,这样人力和打印机的闲置时间就比较多,也延长了产品的生产周期,提高了生产成本。同时,传统模式中是由人工备料并下料,务必延长了材料准备周期。而在本发明所提出的并行多工位式3D打印机中,一台打印机只打印模型的一部分,然后传送到下一个环节打印,这样模型打印的周期就被多个环节分解缩短了,同时改变了传统的间歇式作业方式,而且由自动下料装置完成备料过程,缩短了材料准备及上下料的周期,大大提高了生产效率。即原来的打印周期是一整个模型的打印时间,而在本发明的生产并行多工位式3D打印机中打印周期只是一个环节的时间,打印机采用不间断作业方式,备料过程智能自动。打印完后即可立即进行后续加工,在降低了打印周期的同时,也提高了人力资源和打印机的利用率。附图说明图1是并行多工位式3D打印机示意图;图2是单台3D打印机结构示意图;图3是输送带系统示意图;图4是检测传感器对准定位标记时3D打印机的工作示意图;图5是检测传感器检测到定位标记有偏差时3D打印机的工作示意图;图6是3D打印机组工作示意图;图7是模型分块示意图;图8是3D打印机喷头打印轨迹;在所有附图中,相同的附图标记用来表示相同的元件或结构,其中:图1中各个部件名称为:101-计算机,102-控制电柜,103-支架,104-3D打印机组,105-操作平台,106-输送带系统。图2中各个部件名称为:201-打印机外壳,202-Z向升降丝杠,203-Z向升降电机,204-送料导管,205-料桶,206-打印头固定架,207-X向移动丝杠,208—X向平移电机,209-Y向直线导轨,210-打印基板,211-Y向平移同步带,212-Y向平移电机,213-打印头,214-位置检测传感器。图3中各个部件名称为:300-传送带,301-卡槽,302-定位磁铁,303-定位标记。具体实施方式为了使本发明的目的、技术方案及优点更加清楚明白,以下结合附图及实施例,对本发明进行进一步详细说明。应当理解,此处所描述的具体实施例仅仅用以解释本发明,并不用于限定本发明。此外,下面所描述的本发明各个实施方式中所涉及到的技术特征只要彼此之间未构成冲突就可以相互组合。如图1所示,本实施例中的3D打印机包含8个模块,101为计算机。102为系统的控制电柜。103为支架,104是3D打印机组,根据系统的需要并排放置多个工位的打印机,下面实施例中3D打印机组共有四台3D打印机。105是操作平台。106是输送带系统,由一端的伺服电机驱动。3D打印机组104、操作平台105、输送带系统106均固定在支架103上。图2所示为打印机组中每一台打印机的详细结构示意图。打印机结构包括:打印机外壳201,Z向升降丝杠202,Z向升降电机203,送料导管204,料桶205,料桶中自带送料电机和送料机械机构,打印头固定架206,X向移动丝杠207,X向平移电机208,Y向直线导轨209,打印基板210,本实施例中采用不锈钢作为基板材料,Y向平移同步带,Y向平移电机212,打印头213,位置检测传感器214。传送带300结构如图3所示,同步带表面每隔一段距离(与打印机工位之间距离严格对应)有一对卡槽301,用于给打印基板定位,在每个卡槽之间、传送带300表面安装有定位磁铁302,用于给打印基板贴紧传送带300表面。打印基板210侧边缘中心点上有定位标记303,本实施例中定位标记采用激光打标的黑色条纹,宽度为0.5mm,用于给位置检测传感器214检测每个工位的位置,本实施例中位置检测传感器采用光电传感器,用于校准每个工位的打印机打印轨迹。本发明实施的具体步骤如下:如图1所示,在计算机中,先用三维切片软件将三维模型(本实施例采用Cura软件,输入模型格式为STL格式)进行切片,由计算机按层分解,具体实现原理为计算机对模型由下至上按一定的层厚截取横截面,生成由下至上一系列带有序号的截面轮廓图,以本实施为例,输入模型为一个底面直径为60mm,高度为70mm的圆锥,三维切片软件在高度方向上每隔0.1mm对模型进行切片,共产生700张截面轮廓图,截面轮廓图采用黑白BMP格式保存。在三维切片软件中设定打印速度,即喷头移动速度,本实施例中为120mm/s。对每一个截面,打印机喷头的运动路径采用轮廓偏置方式打印,如图8。并在三维切片软件中添加任务分配模块,具体实施方式为:根据喷头移动速度和运动路径,三维切片软件算出打印每一个切片层所需时间Ti,再把所有单层时间相加获得打印零部件总时间T,本实施例中单独打印一个完整圆锥模型共需要20分钟。根据生产线上工位(打印机)的数量(本实施例中为四台),把打印时间分为4个等份,相对应地将模型分块为a、b、c、d四个部分,四个工位上3D打印机分别打印四个模块,每个工位打印时间为T/4,本实施例中为5分钟,如图7所示。三维切片软件将每一部分的切片数据生成打印机能够识别的代码(一般为Gcode代码),并分别发送到每一工位的打印机中。以上步骤均可通过计算机101完成。常用的三维切片软件有Cura、Makerbot、Kisslicer等。对每一工位的打印机进行装料操作。往每个工位的打印机料桶205中装入打印原料(可以为粒料、丝材或液体),本实施例3D打印机中采用PLA丝材作为料桶中的原料。打印过程中料桶中原料会由送料装置自动通过送料导管添加到打印喷头中。启动控制系统,基板在传动系统的作用下慢慢移动到打印机下方,当位于第一个3D打印机工位上的检测传感器214对准一块打印基板210上的定位标记303时,传送带300停止传动。其余3D打印机工位上的检测传感器214检测各自对应的打印基板210上的定位标记303的偏移量并发送到计算机101中。若其余工位上的检测传感器均能对准各自对应的打印基板210上的定位标记303,3D打印机组开始工作,如图4。若其余工位上的检测传感器检测到各自对应的打印基板210上的定位标记303的位置相对于检测传感器中心的偏差时,检测传感器把偏差信号发送到计算机101,计算机101根据各个工位打印基板210的偏移量对打印轨迹进行校准,具体方法为对打印轨迹进行整体的平移,并重新发送到各个3D打印机中,确保打印轨迹无偏差,如图5,3D打印机组开始工作,每个工位的打印机执行各自的打印任务,当所有工位的打印机都完成打印任务,计算机控制系统控制传送带300继续前进。如此循环往复。如图6所示为打印过程示意图。打印原料采用热塑性材料,对于每一工位的打印机,其刚挤出的原料因为温度足够高,因此能够与上一工位打印好的模型部分共同熔融连接,不需要额外的连接方式或手段。当最后一个工位打印机完成打印时,该工位对应输送带上的电磁铁断电消磁,当基板运动到输送带末端时自动推送到操作平台105上,由操作人员进行取模型、清理基板、修整模型等后处理操作。在打印过程中由控制系统实现多工位任务智能分配,三维切片软件对各个工位打印机进行任务规划保证每个工位的打印时间相同,保证打印过程的协调性。本领域的技术人员容易理解,以上所述仅为本发明的较佳实施例而已,并不用以限制本发明,凡在本发明的精神和原则之内所作的任何修改、等同替换和改进等,均应包含在本发明的保护范围之内。