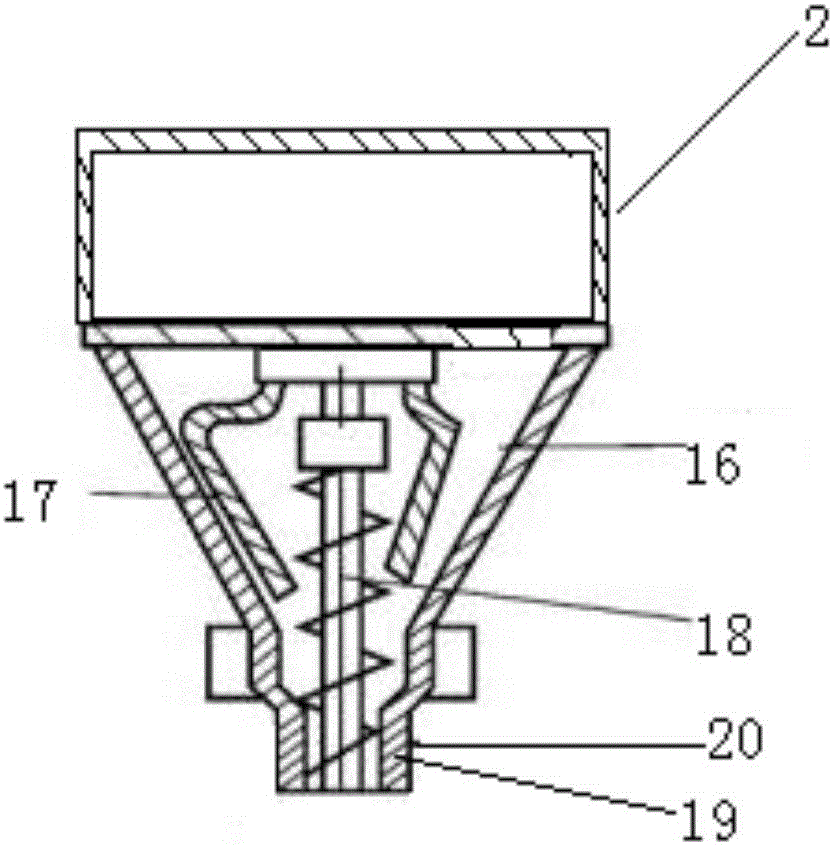
本发明属于吹塑供配料领域,尤其涉及一种基于PLC控制的自动供配料系统。
背景技术:
自动供配料系统已经逐步代替了传统的人工上料方式,在工业生产中具有普遍的适应性,但目前只是局限于单台机器的供配料自动化生产。
吹塑机的供配料自动化主要有两种形式,一种是混料机直接在与吹塑机螺杆相连接的料斗的上方,所需混料机台数多,费用昂贵;另一种是混料机直接放置在地面上,通过真空泵将混合后的原料传送到与吹塑机螺杆相连接的料斗上方,这种混料机以单片机方式控制,一旦发生故障,很难判断故障原因,找到解决方案,而且维修时间长,甚至影响生产。
技术实现要素:
为要解决的上述问题,本发明提供一种基于PLC控制的自动供配料系统。
本发明的技术方案:一种基于PLC控制的自动供配料系统,包括上料系统、混料机、总储存罐、分储罐、流量计、电磁阀、料位传感器、PLC控制器一种基于PLC控制的自动供配料系统,包括上料系统、混料机、总储存罐、分储罐、电磁阀、料位传感器、PLC控制器、自动控制显示板和工业电脑,其特征在于所述上料系统的出口与所述混料机连接,所述混料机与所述总储存罐连接,所述分储罐为多个,多个所述分储罐通过吸料管与所述总储存罐连通,所述分储罐与吹塑机连接,所述总储存罐与多个所述分储罐内均设置所述料位传感器,所述分储罐末端的所述吸料管上设置所述电磁阀,多个所述料位传感器均与所述PLC控制器和所述自动控制显示板连接,所述上料系统、所述混料机、所述总储存罐、所述分储罐均与真空系统连接,所述分储罐设置配料添加口。
所述上料系统为多个,所述上料系统包括进料仓、接料仓、称重控制仪表和检查口和上料系统出口,所述接料仓设置在进料仓下方,所述进料仓和所述接料仓均设置检查口,所述称重控制仪表设置在所述接料仓上,所述上料系统出口设置电磁阀,所述称重控制仪表与所述PLC控制器连接;
所述混料机包括料仓、搅拌器、计量螺杆、计量管和混料机出口,所述搅拌器和所述计量螺杆所述料仓内,所述计量管设置在所述混料机出口内;
所述自动控制显示板包括基板、标签栏、指示灯、液位显示屏和警示设备,所述标签栏、所述指示灯、所述液位显示屏和所述警示设备均设置在基板上。
所述警示设备为警示灯和蜂鸣器。
所述总储存罐和所述分储罐设置检查口。
本发明有益效果是:PLC控制器与设置在总储存罐和分储存罐上的电磁阀、料位传感器PLC根据各贮存罐缺料信号的快慢来排序供配料,根据需料情况自动排序,实现中央集中控制,通过检查输入输出点,可以迅速的判断故障出处,自动控制显示板和警示设备,方便了解生产情况,实时监控与反馈原料供应,确保生产过程中原料一直处于供需平衡状态。在发生故障及时警示便于维修,总体安全性高,生产工艺流程简单,生产成本低,效率高,维修方便。
附图说明
图1是本发明的结构示意图。
图2是本发明的混料机的剖面示意图。
附图中,1.上料系统,2.混料机,3.总储存罐,4.分储罐,5.吹塑机,6.电磁阀,7.料位传感器,8.PLC控制器,9.自动控制显示板,10.蜂鸣器,11.进料仓,12.接料仓,13.称重控制仪表,14.检查口,15.上料系统出口,16.料仓,17.搅拌器,18.计量螺杆,19.计量管,20.混料机出口,21.基板,22.标签栏,23.指示灯,24.所述液位显示屏,25.警示灯。
具体实施方式
下面结合附图对本发明的具体实施方式做出说明。
附图中,1.上料系统,2.混料机,3.总储存罐,4.分储罐,5.吹塑机,6.电磁阀,7.料位传感器,8.PLC控制器,9.自动控制显示板,10.蜂鸣器,11.进料仓,12.接料仓,13.称重控制仪表,14.检查口,15.上料系统出口,16.料仓,17.搅拌器,18.计量螺杆,19.计量管,20.混料机出口,21.基板,22.标签栏,23.指示灯,24.所述液位显示屏,25.警示灯。
本发明涉及一种基于PLC控制的自动供配料系统,包括上料系统、混料机、总储存罐、分储罐、流量计、电磁阀、料位传感器、PLC控制器、自动控制显示板,上料系统的出口与混料机连接,混料机与总储存罐连接,分储罐为多个,多个分储罐通过吸料管与总储存罐连通,分储罐与吹塑机连接供配料,总储存罐与多个分储罐内均设置料位传感器,料位传感器监测总储存罐与分储罐的原料的界面和料位的具体情况,分储罐末端的吸料管上设置电磁阀,上料系统、混料机、总储存罐、分储罐均与真空系统连接形成负压吸取原料,分储罐设置配料添加口,分储罐的配料添加口添加不同的配料如色母,用于生产不同的产品,控制原料的供给情况,多个料位传感器均与PLC控制器和自动控制显示板连接,PLC控制器按工艺配方要求控制上料系统的称量加料操作,同时通过料位传感器识别料位的具体情况,反馈到PLC控制器控制,PLC控制器将输出信号传递给电磁阀和真空系统的真空泵,直接控制吸料的多少,PLC根据各储存罐缺料信号的快慢来排序供配料,根据需料情况自动排序,实现中央集中控制,PLC控制器通过操作按钮实现。
上料系统为多个,上料系统包括进料仓、接料仓、称重控制仪表和检查口和上料系统出口,接料仓设置在进料仓下方,进料仓和接料仓均设置检查口,称重控制仪表设置在接料仓上,上料系统出口设置电磁阀,电磁阀和称重控制仪表与PLC控制器连接,上料系统采用全封闭机构,防止杂质混入原料,保证产品品质,上料系统的称重控制仪表确保各原料组分配比精确,检查口满足出现故障时的检修需要;
混料机包括料仓、搅拌器、计量螺杆、计量管和混料机出口,搅拌器和计量螺杆料仓内,计量管设置在混料机出口内,各原料组分在料仓的搅拌器和计量螺杆作用下搅拌均匀制成原料,并从混料机出口内的计量管流出,监测记录原料的流出量;
自动控制显示板包括基板、标签栏、指示灯、液位显示屏和警示设备,标签栏、指示灯、液位显示屏和警示设备均设置在基板上,标签栏标示各设备的名称,方便直观,指示灯包括,缺料指示灯或溢料指示灯亮起时各储罐临近达到缺料或溢料阈值,方便直观,液位显示屏直接显示料位传感器的数据,方便直观了解具体生产情况,警示设备在发生故障及时警示。
警示设备为警示灯和蜂鸣器,从视觉和听觉两方面进行警示引起工作人员注意。
总储存罐和分储罐设置检修口,检查口满足出现故障时的检修需要。
使用例:各原料组分通过上料系统进入混料机,上料系统采用全封闭机构,防止杂质混入原料,保证产品品质,上料系统的称重控制仪表确保各原料组分配比精确,各原料组分在料仓的搅拌器和计量螺杆作用下搅拌均匀制成原料,并从混料机出口内的计量管流出,监测记录原料的流出量,后进入总储存罐,多个分储罐通过吸料管与总储存罐连通,分储罐与吹塑机连接供配料,总储存罐与多个分储罐内均设置料位传感器,料位传感器监测总储存罐与分储罐的原料的界面和料位的具体情况,分储罐末端的吸料管上设置电磁阀,控制原料的供给情况,多个料位传感器均与PLC控制器和自动控制显示板连接,上料系统、混料机、总储存罐、分储罐均与真空系统连接形成负压吸取原料,分储罐设置配料添加口,分储罐的配料添加口添加不同的配料如色母,用于生产不同的产品,PLC控制器按工艺配方要求控制上料系统的称量加料操作,同时通过料位传感器识别料位的具体情况,反馈到PLC控制器控制,PLC控制器将输出信号传递给电磁阀和真空系统的真空泵,直接控制吸料的多少,PLC根据各储存罐缺料信号的快慢来排序供配料,根据需料情况自动排序,实现中央集中控制,简单有效。
与现有技术相比,PLC控制器与设置在总储存罐和分储存罐上的电磁阀、料位传感器PLC根据各贮存罐缺料信号的快慢来排序供配料,根据需料情况自动排序,实现中央集中控制,通过检查输入输出点,可以迅速的判断故障出处,自动控制显示板和警示设备,方便了解生产情况,实时监控与反馈原料供应,确保生产过程中原料一直处于供需平衡状态。在发生故障及时警示便于维修,总体安全性高,生产工艺流程简单,生产成本低,生产效率高,维修方便。
以上对本发明的一个实例进行了详细说明,但内容仅为本发明的较佳实施例,不能被认为用于限定本发明的实施范围。凡依本发明申请范围所作的均等变化与改进等,均应仍归属于本发明的专利涵盖范围之内。