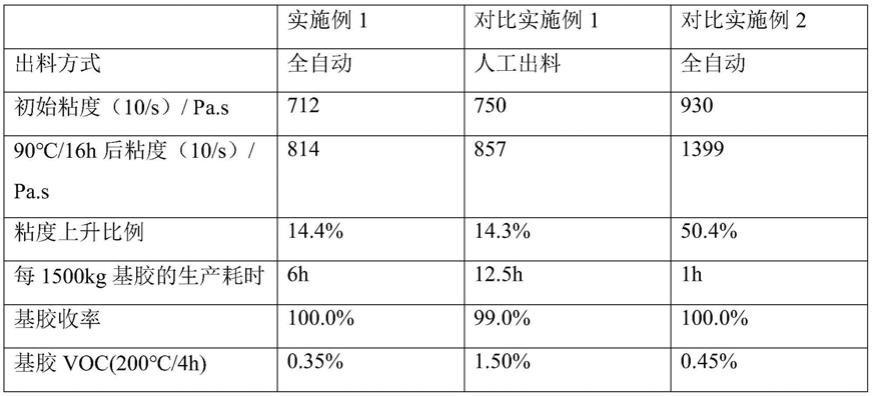
1.本发明属于液体硅橡胶生产领域,具体涉及一种加成型液体硅橡胶基胶的半连续生产工艺及其生产装置。
背景技术:2.加成型液体硅橡胶由于具有加工效率高,产品透明无味等优点,在硅橡胶制品领域的使用比例逐年提高,需求量越来越大。
3.加成型液体硅橡胶一般由a/b两种组分按照1:1经静态混合器混合均匀后,注入模具制成所需的硅橡胶制品,其中,a/b两种组分的生产过程当中都需要使用到液体硅橡胶基胶。经过多年的发展,液体硅橡胶基胶的生产工艺基本定型,通常为在捏合机中投入硅油、处理剂、白炭黑,混合均匀,升温至150℃左右真空脱低,再加入稀释硅油搅拌均匀即可。以常用的2000l容积的捏合机为例,所述方法生产一批次的基胶耗时通常为10~16小时,生产效率较低,严重制约了液体硅橡胶基胶的生产效率。另外,受制于捏合机的脱低效率,所述方法生产的液体硅橡胶基胶的voc往往较高,约为1.5%,无法直接满足婴童行业国标gb4806.2
‑
2015中规定的产品voc≤0.5%的要求。为此,行业中通常会对硅橡胶制品进行二段硫化(200℃/4h)以确保voc达标。二段硫化工艺虽可以降低voc但工艺较麻烦,因此免二段产品已经成为当下趋势。此外,液体硅橡胶基胶生产完成后,常经人工将粘稠的基胶从捏合机中扒出,不仅极其耗费人力而且具有很大的安全隐患。
4.中国专利cn102615801b公开了一种注射型双组分液体硅橡胶连续生产线,通过将硅油、白炭黑、处理剂在第一侧喂料机和第二侧喂料机中预混后,送入一级螺杆挤出机进行升温、脱低、稀释等处理,最终实现连续生产液体硅橡胶基胶,以提高生产效率。但使用喂料机预混白炭黑含量高达40%左右的硅油和白炭黑混合物极其困难,而如果混合阶段形成的粉胶混合物处理不佳,会直接影响液体硅橡胶基胶的抗结构化能力、胶料可操作时间和机械性能,对终产品品质影响极大。
5.中国专利cn205343730u公开了一种有机硅胶基础料连续化成套生产装置,包括依次连接的搅拌设备(例如捏合机或分散机)、螺杆机(例如双螺杆机)和三通阀的第一接口,三通阀第二接口与搅拌设备的入口连接,三通阀第三接口与高粘物料冷却器连接。但此种方法仅能用于生产具有一定流动性的糊状硅酮密封胶基础料,无法生产气相法白炭黑含量高达40%左右的液体硅橡胶粉胶,由于液体硅橡胶粉胶基本为固体状外观,无法通过增压泵将其从分散机或者捏合机中抽出。
技术实现要素:6.为解决现有技术中加成型液体硅橡胶基胶生产效率不高,粉胶混合物均匀混合难度大的技术问题,本发明提供一种加成型液体硅橡胶基胶的半连续生产工艺及其生产装置。
7.一种加成型液体硅橡胶基胶的半连续生产装置,包括依次连接的带螺杆挤出功能
的捏合机和双螺杆挤出机。
8.根据本发明,带螺杆挤出功能的捏合机出料口和双螺杆挤出机进料口直接相连或通过传送装置连接。在本发明的一个实施方式中,所述传送装置是传送带。
9.根据本发明,所述生产装置还包括第一硅油存储装置、处理剂存储装置、白炭黑存储装置,其分别通过管道与带螺杆挤出功能的捏合机连接,所述硅油存储装置、处理剂存储装置、白炭黑存储装置中的硅油、处理剂和白炭黑分别送入带螺杆挤出功能的捏合机中,进行混合制备粉胶。
10.根据本发明,优选,所述生产装置还包括中间混合装置,所述中间混合装置位于第一硅油存储装置和处理剂存储装置与带螺杆挤出功能的捏合机的连接管路上,相应的硅油存储装置、处理剂存储装置中的硅油和处理剂送入中间混合装置混合后,再送入带螺杆挤出功能的捏合机中。
11.根据本发明,优选,所述生产装置还包括硅油计量泵,所述硅油计量泵位于硅油存储装置的输出管线上,进入中间混合装置(当存在中间混合装置时)或者带螺杆挤出功能的捏合机(当不存在中间混合装置时)之前。
12.根据本发明,优选,所述生产装置还包括处理剂计量泵,所述处理剂计量泵位于处理剂存储装置的输出管线上,进入中间混合装置(当存在中间混合装置时)或者带螺杆挤出功能的捏合机(当不存在中间混合装置时)之前。
13.根据本发明,优选,所述生产装置还包括白炭黑泵,所述白炭黑泵位于白炭黑存储装置的输出管线上,进入带螺杆挤出功能的捏合机之前。所述泵能够将白炭黑分次加入带螺杆挤出功能的捏合机。在本发明的一个实施方式中,所述白炭黑泵采用气动隔膜泵。
14.根据本发明,所述带螺杆挤出功能的捏合机具有真空抽气口。
15.根据本发明,所述双螺杆挤出机包括依次布置的进料口段、热处理段、稀释段和冷却段。
16.根据本发明,所述双螺杆挤出机的进料口段具有真空抽气口。所述进料口段具有加热功能。
17.根据本发明,所述双螺杆挤出机的热处理段具有真空抽气口。热处理段具有加热功能。
18.根据本发明,所述双螺杆挤出机的稀释段具有真空抽气口。
19.根据本发明,所述双螺杆挤出机的筒体直径为110
‑
160mm,长径比为60
‑
75。在本发明的一个实施方式中,所述双螺杆挤出机的筒体直径为135mm,长径比为68。
20.根据本发明,所述生产装置还包括第二硅油存储装置,所述第二硅油存储装置与双螺杆挤出机的稀释段连接。
21.根据本发明,当用于粉胶制备的硅油和用于稀释的硅油是相同的硅油时,第一硅油存储装置和第二硅油存储装置可以统一为一个装置,也可以是独立的两个装置。
22.根据本发明,所述各真空抽气口与抽真空设备连接。
23.本发明还提供利用前述生产装置进行加成型液体硅橡胶基胶半连续生产的工艺方法:
24.(1)粉胶制备:将硅油、处理剂和白炭黑加入带螺杆挤出功能的捏合机中混合制备粉胶;
25.(2)脱低热处理稀释处理:将步骤(1)中制备的粉胶通过捏合机自带螺杆挤出,送至双螺杆挤出机进料口段,在真空条件下,在热处理段加热至150~180℃,并在热处理段中150~180℃真空下保持20~40分钟后,进入稀释段,与加入的稀释用硅油混合均匀,最后进入冷却段冷却后出料。
26.根据本发明,所述步骤(1)中,硅油和处理剂在加入带螺杆挤出功能的捏合机之前,先进行混合形成混合物。
27.根据本发明,所述步骤(1)中,白炭黑分次加入捏合机中。
28.根据本发明,所述步骤(1)中,硅油、处理剂和白炭黑混合均匀后,抽真空脱除混合过程中产生的氨气。
29.根据本发明,所述步骤(2)中,在进料口段、热处理段和稀释段均进行抽真空操作,以排出脱低、热处理和稀释过程中产生的低沸物和/或气泡。
30.根据本发明,所述步骤(2)中,粉胶进入双螺杆挤出机进料口段的速度为900
‑
1300kg/h。在本发明的一个实施方式中,所述速度为1150kg/h。
31.根据本发明,所述步骤(2)中,稀释用硅油加入双螺杆挤出机稀释段的速度为200
‑
500kg/h。在本发明的一个实施方式中,所述速度为380kg/h。
32.根据本发明,所述步骤(2)中,冷却到80℃以下,例如冷却到室温。
33.根据本发明,所述生产工艺方法还包括加成型液体硅橡胶基胶抗结构化和/或加成型液体硅橡胶基胶voc的检测步骤。
34.根据本发明,所述加成型液体硅橡胶基胶抗结构化检测方法:取制备的基胶在23℃条件下恒温1h后使用ta流变仪在10/s条件下测试其粘度;之后将剩余基胶放置于90℃烘箱中16h取出,在23℃条件下恒温1h后以相同条件测试10/s的粘度,以前后粘度及粘度上升比例来判断基胶抗结构能力。
35.在本发明的一个实施方式中,所述加成型液体硅橡胶基胶抗结构化检测方法为:取100g制备的基胶在23℃条件下恒温1h后使用ta流变仪在10/s条件下测试其粘度,完成后将剩余基胶放置于90℃烘箱中16h取出,在23℃条件下恒温1h后以相同条件测试10/s的粘度,以前后粘度及粘度上升比例来判断基胶抗结构能力。
36.根据本发明,所述加成型液体硅橡胶基胶voc检测方法:室温下取制备的液体硅橡胶基胶均匀涂布于载玻片上,置于200℃鼓风烘箱中烘烤4h后取出,置于干燥器中冷却1h后称量,液体硅橡胶基胶重量的失重比例即为基胶voc。
37.在本发明的一个实施方式中,所述加成型液体硅橡胶基胶voc检测方法为:室温下取5.00
±
0.2g制备的液体硅橡胶基胶均匀涂布于带有50
×
50
×
2mm凹槽的载玻片上,置于200℃鼓风烘箱中烘烤4h后取出,置于干燥器中冷却1h后称量,液体硅橡胶基胶重量的失重比例即为基胶voc。
38.在本发明中,处理剂是本领域已知的用于白炭黑的处理剂,包括但不限于:六甲基二硅氮烷、四甲基二乙烯基硅氮烷、七甲基二硅氮烷、乙烯基双封头、羟基硅油等。
39.本发明的生产装置和生产工艺适用于各类型加成型液体硅橡胶基胶的生产,所述硅油可以是本领域已知的用于相应基胶生产的各种硅油或其混合物,粘度范围可以是100~1000000cs。
40.与现有技术相比,本发明具有以下有益效果:
41.虽然本发明的生产工艺是半连续的(由带螺杆挤出功能的捏合机生产粉胶是按批次间歇进行的,双螺杆挤出机进行脱低热处理和稀释是连续进行的),但与全程用捏合机生产基胶的传统工艺相比,本发明的工艺仍使基胶的批次生产时间缩短了50%以上,大幅提高基胶生产效率、降低生产成本。
42.另外,本发明的方法在带螺杆挤出功能的捏合机中仅生产粉胶,粉胶不会粘附在捏合机中,且采用捏合机自带的螺杆出料,在节约传统人工出料和清理捏合机方法的大量时间同时,安全性也大幅提升。
43.第三,与现有技术中报道的其他的连续性生产工艺相比,本发明改进了粉胶生产设备和方法,进一步结合双螺杆挤出机的后处理工艺,提高了加成型液体硅橡胶基胶的抗结构化能力、胶料可操作时间和机械性能。且,双螺杆挤出机的密封效果好,脱低大幅优于捏合机,基胶voc大幅降低,可用于免二段加成型液体硅橡胶的生产。
附图说明
44.图1本发明加成型液体硅橡胶基胶的半连续生产设备装置和流程示意图。图中:1:第一硅油储罐;2:处理剂储罐;3:白炭黑储罐;4:中间混合装置
‑
混合罐;5:带螺杆挤出功能的捏合机;6:双螺杆挤出机进料口;7:双螺杆挤出机热处理段;8:第二硅油储罐;9:双螺杆挤出机稀释段;10:双螺杆挤出机冷却段;11、12、13、14:真空抽气口。
具体实施方式
45.下文将结合具体实施例对本发明的技术方案做更进一步的详细说明。应当理解,下列实施例仅为示例性地说明和解释本发明,而不应被解释为对本发明保护范围的限制。凡基于本发明上述内容所实现的技术均涵盖在本发明旨在保护的范围内。
46.除非另有说明,以下实施例中使用的原料和试剂均为市售商品,或者可以通过已知方法制备。
47.以下实施例中按照图1所示的设备装置和流程示意图,进行加成型液体硅橡胶基胶的半连续生产。本发明实施例中提供的加成型液体硅橡胶基胶的半连续生产装置,包括第一硅油储罐1、处理剂储罐2、白炭黑储罐3、混合罐4(中间混合装置)、带螺杆挤出功能的捏合机5和双螺杆挤出机,双螺杆挤出机包括进料口段6、热处理段7、稀释段9和冷却段10。硅油和处理剂分别从第一硅油储罐1和处理剂储罐2,经计量泵送入混合罐4混合,混合物送入带螺杆挤出功能的捏合机5;白炭黑经泵分次加入带螺杆挤出功能的捏合机5,两者在带螺杆挤出功能的捏合机5中混合制备粉胶。所述粉胶经捏合机的螺杆挤出,通过传送装置送入双螺杆挤出机进料口6,在双螺杆挤出机热处理段7进行热处理,进入双螺杆挤出机稀释段9,与来自于第二硅油储罐2的硅油进行混合稀释,进入双螺杆挤出机冷却段10冷却后出料。带螺杆挤出功能的捏合机5、双螺杆挤出机进料口6,双螺杆挤出机热处理段7,双螺杆挤出机稀释段9均有真空抽气口(分别为11、12、13、14),所述抽气口与抽真空设备相连,生产中抽真空,以脱除生产中产生的氨气、低沸物和气泡等。
48.实施例1:
49.(1)粉胶制备:使用计量泵从第一硅油储罐1和处理剂储罐2中分别抽取650kg粘度为60000cs的端乙烯基硅油和130kg六甲基硅氮烷至混合罐4中,混合20分钟后全部加入带
螺杆挤出功能的捏合机5中,再通过气动隔膜泵分次从白炭黑储罐3中抽取420kg比表面积为400m2/g的白炭黑加入带螺杆挤出功能的捏合机5中,搅拌均匀后通过真空抽气口11抽去捏合机5中产生的氨气。
50.(2)脱低热处理稀释过程:步骤(1)中准备好的粉胶通过捏合机自带螺杆挤出,并通过传送带按照1150kg/h传送速度匀速传送至筒体直径为135mm,长径比为68的双螺杆挤出机的进料口6,将物料加热至150℃(用时1分钟),通过真空抽气口12抽去升温过程中产生的低沸物。物料进入双螺杆挤出机热处理段7在150℃条件下剪切30min以上,并通过真空抽气口13持续脱除物料中的低沸物。通过计量泵以380kg/h的速度匀速从第二硅油储罐8中抽取粘度为60000cs的端乙烯基硅油,加入双螺杆挤出机稀释段9中,并混合均匀,通过真空抽气口14除去物料混合产生的气泡。物料进入冷却段10冷却至80℃以下,连续出料得到液体硅橡胶基胶。
51.(3)液体硅橡胶基胶抗结构化检测:取100g上述基胶在23℃条件下恒温1h后使用ta流变仪在10/s条件下测试其粘度,完成后将剩余基胶放置于90℃烘箱中16h取出,在23℃条件下恒温1h后以相同条件测试10/s的粘度,以前后粘度及粘度上升比例来判断基胶抗结构能力。
52.(4)基胶voc测试:室温下取5.00
±
0.2g上述基胶均匀涂布于带有50
×
50
×
2mm凹槽的载玻片上,置于200℃鼓风烘箱中烘烤4h后取出,置于干燥器中冷却1h后称量,液体硅橡胶基胶重量的失重比例即为基胶voc。
53.对比实施例1:
54.采用无螺杆挤出功能的捏合机进行基胶生产,在热处理之前的粉胶制备的操作方式和所用时间与实施例1相同,具体如下:
55.(1)基胶制备:使用计量泵从第一硅油储罐1和处理剂储罐2中分别抽取650kg粘度为60000cs的端乙烯基硅油和130kg六甲基硅氮烷至混合罐4中,混合20分钟后全部加入无螺杆挤出功能的捏合机中,再通过气动隔膜泵分次从白炭黑储罐3中抽取420kg比表面积为400m2/g的白炭黑加入捏合机中。搅拌均后,通过捏合机的真空抽气口11抽真空。升温至150℃(用时2
‑
3小时),在150℃真空条件下搅拌2h后,通过计量泵以380kg/h的速度匀速加入380kg粘度为60000cs的端乙烯基硅油,搅拌均匀,冷却至80℃出料得到液体硅橡胶基胶。
56.(2)液体硅橡胶基胶抗结构化检测:取100g上述基胶在23℃条件下恒温1h后使用ta流变仪在10/s条件下测试其粘度,完成后将剩余基胶放置于90℃烘箱中16h取出,在23℃条件下恒温1h后以相同条件测试10/s的粘度,以前后粘度及粘度上升比例来判断基胶抗结构能力。
57.(3)基胶voc测试:室温下取5.00
±
0.2g上述基胶均匀涂布于带有50
×
50
×
2mm凹槽的载玻片上,置于200℃鼓风烘箱中烘烤4h后取出,置于干燥器中冷却1h后称量,液体硅橡胶基胶重量的失重比例即为基胶voc。
58.对比实施例2
59.(1)基胶制备:将粘度为60000cs的端乙烯基硅油以650kg/h的进料速度,六甲基硅氮烷以130kg/h的进料速度,比表面积为400m2/g的气相法白炭黑以420kg/h的进料速度在喂料机中混合成团送入到一级螺杆挤出机中进行分散、捏合、研磨并加热升温至150℃~170℃,抽真空脱低,再以380kg/h的进料速度加入粘度为60000cs的端乙烯基硅油进行稀
释,冷却,得到连续法液体硅橡胶基胶。
60.(2)液体硅橡胶基胶抗结构化检测:取100g上述基胶在23℃条件下恒温1h后使用ta流变仪在10/s条件下测试其粘度,完成后将剩余基胶放置于90℃烘箱中16h取出,在23℃条件下恒温1h后以相同条件测试10/s的粘度,以前后粘度及粘度上升比例来判断基胶抗结构能力。
61.(3)基胶voc测试:室温下取5.00
±
0.2g上述基胶均匀涂布于带有50
×
50
×
2mm凹槽的载玻片上,置于200℃鼓风烘箱中烘烤4h后取出,置于干燥器中冷却1h后称量,液体硅橡胶基胶重量的失重比例即为基胶voc。
[0062][0063]
从上述实施例对比可见,采用本发明的生产方法,产品的批次生产时间由原来的12.5h降低为6h;产品初始粘度和老化后粘度与传统捏合机工艺生产的产品差异不大甚至略低;基胶生产过程无需人工出料,安全性大幅提高;基胶voc大幅降低,由原来的1.50%降低至0.35%,可以用于免二段硅橡胶的生产;基胶收率由原来99.0%提升至100%。
[0064]
本发明的发明人还研究了以喂料机或分散机作为粉胶制备装置,与一级螺杆挤出机配合,结果发现:得到的基胶,初始粘度(10/s)是930pa.s以上,90℃/16h后的粘度(10/s)上升为1399pa.s以上,粘度升高比例达50.4%,说明基胶抗结构能力差,推测原因可能是粉胶制备中处理不得当。
[0065]
以上,对本发明的实施方式进行了说明。但是,本发明不限定于上述实施方式。凡在本发明的精神和原则之内,所做的任何修改、等同替换、改进等,均应包含在本发明的保护范围之内。