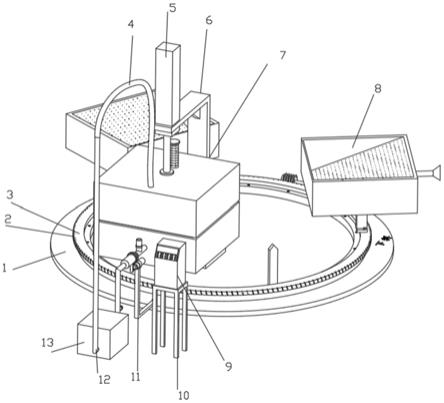
1.本发明涉及聚酯纤维制备技术领域,具体为一种聚酯纤维棉模塑成型加工方法及加工设备。
背景技术:2.聚氨酯发泡塑料具有优异的物理性能,相比于其它发泡塑料,其制备工艺非常适合于模塑成型,因此广泛应用于车辆座椅、高档沙发填充物。但随着人们对安全、环境方面关注度的不断提高,voc释放水平较高、阻燃性能不佳、透气性差等缺点逐渐暴露,找到一款合适的材料替换聚氨酯发泡势在必行。
3.合成纤维无纺棉传统上多作为保温、消音、过滤材料使用,合成纤维工业水平的不断提升,赋予无纺棉更佳的性能,低voc、阻燃、透气性能优异等渐渐凸显,开始进入居家生活领域,如床垫、沙发垫等。
4.合成纤维无纺棉用作座椅填充物的方案在安全、环保等方面优势明显,材料成本也有优势,迎合家居填充而开发的高回弹合成纤维丝,在物理性能和舒适性上也可以匹敌聚氨酯泡沫,但生产成型却成为的难题:现有的生产工艺下,无纺棉只能是卷材或者片材(如图),座椅则是三维的不规则形状(如图)。因此出现行业呼声很高,但实际进展缓慢的窘状。现有的成型方案是将多层裁片叠放在加热的模具中,然后上下模压合,加热无纺棉纤维到半熔融状态,使各层裁片融合在一起,然后模具冷却定型。定型时存在以下缺点:
5.需要将合成纤维预热到半熔融状态后放入预热的模具中,增加了作业时间差;
6.受工艺限制,裁片填充模具环节时间有限,因此裁片数量要少,填铺操作不能过于复杂,只能生产造型简单的产品,这也是阻碍合成纤维无纺棉大规模应用到车辆座椅的重要因素;
7.因此提出一种聚酯纤维棉模塑成型加工方法及加工设备以解决上述问题。
技术实现要素:8.本发明的目的在于提供一种聚酯纤维棉模塑成型加工方法及加工设备,以解决上述背景技术中提出问题。
9.为实现上述目的,本发明提供如下技术方案:一种聚酯纤维棉模塑成型加工设备,包括支撑板、气缸、控制器、电热风机和第一控制阀,所述支撑板的顶部中端处连接有z形板,所述z形板的顶部横向部位固定安装有气缸,所述气缸的输出端固定连接有聚酯纤维棉模塑成型的上模具,所述上模具的顶部固定连接有用于进气的软管,所述软管的外端固定连接有第一出气管,所述第一出气管与电热风机的输出端固定连接,所述电热风机的输出端固定连接有第一中间管,所述第一中间管的侧壁固定连接有进气管,所述进气管的外壁固定连接有第三控制阀,所述第一中间管的进气管端固定连接有第二中间管,所述第二中间管的固定安装有第一控制阀,所述第二中间管的进气端固定连接有第二圆锥,所述第二中间管的固定连接有限位块,所述限位块与电动推杆的输出端固定连接,所述第二中间管
的进气端固定连接有第二圆锥;
10.所述支撑板的顶部外沿处固定安装有驱动电机和轴承,所述轴承的内环通过螺栓固定连接有圆环,所述圆环的外壁均匀开设有涡轮槽,所述驱动电机输出端固定连接有转轴,所述转轴固定连接有涡轮,且涡轮和涡轮槽配合使用,所述圆环的顶部沿着圆周方向均匀固定连接有倒t形板,所述倒t形板的顶部固定连接有用于聚酯纤维棉模塑成型的下模具,所述下模具开设有用于出气的热气出气管,所述热气出气管的顶部连接有第二出气管,所述第二出气管固定安装有第二控制阀,所述热气出气管的外端固定连接有第一圆锥,所述第一圆锥和第二圆锥配合使用;
11.所述上模具的成型槽顶面和下模具的成型槽底面均匀用于气孔流动气孔,所述上模具和下模具均开设有空槽,所述下模具通过空槽与软管相通,所述下模具通过空槽与热气出气管相通;
12.所述上模具和和下模具连接有用于成型后的聚酯纤维棉模塑脱离的脱离结构,所述脱离结构包括第一弹簧、t形插杆、下推杆、半球体、直板和三角块,所述第一弹簧固定安装在下模具的顶部,所述第一弹簧的顶部固定连接有t形插杆,所述t形插杆的底部贯穿第一弹簧与上模具贴合滑动连接,且t形插杆的底部和上模具的成型槽顶面齐平,所述半球体固定连接有第二弹簧,所述第二弹簧处于恢复状态时第二弹簧带动半球体向下移动带动半球体的顶部与下模具的成型槽底面齐平,所述半球体的底部固定连接有下推杆,所述直板的顶部固定连接有三角块,所述下推杆与三角块的左侧面接触推动推杆向上移动,下推杆推动成型后的聚酯纤维棉模塑与下模具分离。
13.更进一步的,所述支撑板的外壁固定连接有l形支撑板,所述l形支撑板的直立顶部固定连接有电动推杆。
14.更进一步的,成型时所述电动推杆推动第二圆锥插在第一圆锥内,且第一圆锥的外壁与第二圆锥的内壁贴合接触。
15.更进一步的,成型加热时所述第三控制阀和第二控制阀处于关闭状态,第一控制阀处打开状态;成型常温冷却时所述第三控制阀和第二控制阀处于打开状态,第一控制阀处于关闭状态。
16.更进一步的,所述下模具的组数为3的倍数。
17.更进一步的,所述热气出气管固定安装在支撑板的顶部,且设置在下推杆的转动轨迹下方。
18.更进一步的,所述半球体和t形插杆均固定连接有限位块,所述半球体连接的限位块与上模具贴合接触时半球体的顶部与上模具的成型槽顶面齐平,所述t形插杆连接的限位块与下模具贴合接触时半球体的顶部与下模具的成型槽底面齐平。
19.更进一步的,所述空槽的侧壁固定安装有用于温度监测的温度感应器。
20.更进一步的,所述控制器连接有支撑架,所述支撑架、电热风机和支撑板均摆放在地面,所述控制器分别与气缸、电热风机、驱动电机、第一控制阀、第二控制阀和第三控制阀电性连接。
21.一种聚酯纤维棉模塑成型加工设备的加工方法,加工方法如下:
22.步骤一、上料位置处在z形板右侧壁的下模具的成型槽内将裁片逐层填铺;
23.步骤二、启动控制器启动驱动电机,驱动电机带动转轴转动,转轴带动涡轮转动,
涡轮通过圆环带动涡轮槽转动,涡轮槽带动裁片逐层填铺的下模具移动至上模具正下方,气缸带动上模具向下移动与下模具进行合模;
24.步骤三、启动电动推杆,电动推杆带动第二中间管移动,第二中间管带动第二圆锥插在第一圆锥内,关闭第二控制阀和第三控制阀,打开第一控制阀,启动电热风机,电热风机产生动力热空气通过第一出气管和软管进入上模具和下模具内,上模具和下模具温度150℃的热空气加热90min,然后继续升温,待温度稳定在165℃后继续加热15min,保温15min后关闭第一控制阀和电热风机的加热单元,打开第二控制阀和第三控制阀吹入常温空气,温度感应器监测温度低于75℃时成型结束,同时上料位置处进行上料;
25.步骤四、气缸带动上模具向上移动,上模具带动t形插杆向上移动,t形插杆与z形板接触时t形插杆向下移动,t形插杆的底部推动上模具内的聚酯纤维棉模塑与上模具分离,控制器启动驱动电机,驱动电机带动转轴转动,转轴带动涡轮转动,涡轮通过圆环带动涡轮槽转动,涡轮槽带动成型后的下模具移动,下模具带动下推杆与直板顶部的三角块接触,三角块推动下推杆向上移动,下推杆带动下模具内内的聚酯纤维棉模塑与下模具分离,便于成型后的聚酯纤维棉模塑在下料位置处从上模具和下模具内取出,同时,上料位置处进行上料、成型位置处进行成型。
26.本发明的有益效果是:
27.本发明启动控制器启动驱动电机,驱动电机带动转轴转动,转轴带动涡轮转动,涡轮通过圆环带动涡轮槽转动,涡轮槽带动裁片逐层填铺的下模具移动至上模具正下方,气缸带动上模具向下移动与下模具进行合模,方便上模具和下模具进行合模处理;
28.本发明上模具和下模具合模后电动推杆带动第二中间管移动,第二中间管带动第二圆锥插在第一圆锥内,关闭第二控制阀和第三控制阀,打开第一控制阀,启动电热风机,电热风机产生动力热空气通过第一出气管和软管进入上模具和下模具内,上模具和下模具温度150℃的热空气加热90min,然后继续升温,待温度稳定在165℃后继续加热15min,保温15min后关闭第一控制阀和电热风机的加热单元,打开第二控制阀和第三控制阀吹入常温空气,温度感应器监测温度低于75℃时成型结束,同时上料位置处进行上料,一次成型,无需将合成纤维预热到半熔融状态后放入预热的模具中,缩短了作业时间;
29.本发明气缸带动上模具向上移动,上模具带动t形插杆向上移动,t形插杆与z形板接触时t形插杆向下移动,t形插杆的底部推动上模具内的聚酯纤维棉模塑与上模具分离,控制器启动驱动电机,驱动电机带动转轴转动,转轴带动涡轮转动,涡轮通过圆环带动涡轮槽转动,涡轮槽带动成型后的下模具移动,下模具带动下推杆与直板顶部的三角块接触,三角块推动下推杆向上移动,下推杆带动下模具内内的聚酯纤维棉模塑与下模具分离,便于成型后的聚酯纤维棉模塑在下料位置处从上模具和下模具内取出,同时,上料位置处进行上料、成型位置处进行成型,上料、成型和下料同步进行,利于企业连续化生产,裁片填充模具环节时间常会,裁片数量大,利于实际填铺操作,利于成型各种形象的产品,有利于合成纤维无纺棉大规模应用到车辆座椅。
附图说明
30.为了更清楚地说明本发明实施例的技术方案,下面将对实施例描述所需要使用的附图作简单地介绍,显而易见地,下面描述中的附图仅仅是本发明的一些实施例,对于本领
域普通技术人员来讲,在不付出创造性劳动的前提下,还可以根据这些附图获得其他的附图。
31.图1为本发明结构示意图;
32.图2为本发明结构左视图;
33.图3为本发明结构后视图;
34.图4为本发明结构左仰视图;
35.图5为本发明结构剖视图;
36.图6为本发明的上模具及其连接结构剖视图;
37.图7为本发明的圆环连接结构示意图;
38.图8为本发明的合模时第二中间管及其连接结构示意图;
39.图9为本发明的图4的a处结构放大示意图;
40.图10为本发明的图5的b处结构放大示意图;
41.附图中,各标号所代表的部件列表如下:
42.1.支撑板 2.涡轮槽 3.圆环 4.软管 5.气缸 6.z形板 7.上模具 8.下模具 9.控制器 10.支撑架 11.l形支撑板 12.第一出气管 13.电热风机 14.第一圆锥 15.轴承 16.气孔 17.第一弹簧 18.t形插杆 19.电动推杆 20.第二圆锥 21.进气管 22.第一中间管 23.第二中间管 24.驱动电机 25.转轴 26.涡轮 27.下推杆 28.半球体 29.倒t形板 30.第二出气管 31.热气出气管 32.空槽 33.第二弹簧 34.温度感应器 35.限位块 36.连接杆 37.直板 38.三角块 39.第一控制阀 40.第二控制阀 41.第三控制阀。
具体实施方式
43.下面将结合本发明实施例中的附图,对本发明实施例中的技术方案进行清楚、完整地描述,显然,所描述的实施例仅仅是本发明一部分实施例,而不是全部的实施例。基于本发明中的实施例,本领域普通技术人员在没有作出创造性劳动前提下所获得的所有其它实施例,都属于本发明保护的范围。
44.下面结合实施例对本发明作进一步的描述。
45.实施例1
46.如图1、2、3、4、5、6、7、9所示的一种聚酯纤维棉模塑成型加工设备,包括支撑板1、气缸5、控制器9、电热风机13和第一控制阀39,支撑板1的顶部中端处连接有z形板6,z形板6的顶部横向部位固定安装有气缸5,气缸5的输出端固定连接有聚酯纤维棉模塑成型的上模具7,上模具7的顶部固定连接有用于进气的软管4,软管4的外端固定连接有第一出气管12,第一出气管12与电热风机13的输出端固定连接,电热风机13的输出端固定连接有第一中间管22,第一中间管22的侧壁固定连接有进气管21,进气管21的外壁固定连接有第三控制阀41,第一中间管22的进气管端固定连接有第二中间管23,第二中间管23的固定安装有第一控制阀39,第二中间管23的进气端固定连接有第二圆锥20,第二中间管23的固定连接有限位块35,限位块35与电动推杆19的输出端固定连接,支撑板1的外壁固定连接有l形支撑板11,l形支撑板11的直立顶部固定连接有电动推杆19,成型时电动推杆19推动第二圆锥20插在第一圆锥14内,且第一圆锥14的外壁与第二圆锥20的内壁贴合接触,第二中间管23的进气端固定连接有第二圆锥20;支撑板1的顶部外沿处固定安装有驱动电机24和轴承15,轴承
15的内环通过螺栓固定连接有圆环3,圆环3的外壁均匀开设有涡轮槽2,驱动电机24输出端固定连接有转轴25,转轴25固定连接有涡轮26,且涡轮26和涡轮槽2配合使用,圆环3的顶部沿着圆周方向均匀固定连接有倒t形板29,倒t形板29的顶部固定连接有用于聚酯纤维棉模塑成型的下模具8,下模具8的组数为3的倍数,方便上模具7和下模具8进行合模处理;
47.实施例2
48.实施例2是对实施例1的进一步改进。
49.如图1、2、4、5、8、10所示,下模具8开设有用于出气的热气出气管31,热气出气管31的顶部连接有第二出气管30,第二出气管30固定安装有第二控制阀40,热气出气管31的外端固定连接有第一圆锥14,第一圆锥14和第二圆锥20配合使用;上模具7的成型槽顶面和下模具8的成型槽底面均匀用于气孔流动气孔16,上模具7和下模具8均开设有空槽32,下模具8通过空槽32与软管4相通,下模具8通过空槽32与热气出气管31相通,成型加热时第三控制阀41和第二控制阀40处于关闭状态,第一控制阀39处打开状态;成型常温冷却时第三控制阀41和第二控制阀40处于打开状态,第一控制阀39处于关闭状态,空槽32的侧壁固定安装有用于温度监测的温度感应器34,控制器9连接有支撑架10,支撑架10、电热风机13和支撑板1均摆放在地面,控制器9分别与气缸5、电热风机13、驱动电机24、第一控制阀39、第二控制阀40和第三控制阀41电性连接,一次成型,无需将合成纤维预热到半熔融状态后放入预热的模具中,缩短了作业时间;
50.实施例3
51.实施例3是对实施例1的进一步改进。
52.如图1、5、6、7、9所示,上模具7和和下模具8连接有用于成型后的聚酯纤维棉模塑脱离的脱离结构,脱离结构包括第一弹簧17、t形插杆18、下推杆27、半球体28、直板37和三角块38,第一弹簧17固定安装在下模具8的顶部,第一弹簧17的顶部固定连接有t形插杆18,t形插杆18的底部贯穿第一弹簧17与上模具7贴合滑动连接,且t形插杆18的底部和上模具7的成型槽顶面齐平,半球体28固定连接有第二弹簧33,第二弹簧33处于恢复状态时第二弹簧33带动半球体28向下移动带动半球体28的顶部与下模具8的成型槽底面齐平,半球体28的底部固定连接有下推杆27,直板37的顶部固定连接有三角块38,下推杆27与三角块38的左侧面接触推动下推杆27向上移动,下推杆27推动成型后的聚酯纤维棉模塑与下模具8分离,热气出气管31固定安装在支撑板1的顶部,且设置在下推杆27的转动轨迹下方,半球体28和t形插杆18均固定连接有限位块35,半球体28连接的限位块35与上模具7贴合接触时半球体28的顶部与上模具7的成型槽顶面齐平,t形插杆18连接的限位块35与下模具8贴合接触时半球体28的顶部与下模具8的成型槽底面齐平,上料、成型和下料同步进行,利于企业连续化生产,裁片填充模具环节时间常会,裁片数量大,利于实际填铺操作,利于成型各种形象的产品,有利于合成纤维无纺棉大规模应用到车辆座椅。
53.使用时,一种聚酯纤维棉模塑成型加工设备的加工方法,加工方法如下:
54.步骤一、上料位置处在z形板6右侧壁的下模具8的成型槽内将裁片逐层填铺;
55.步骤二、启动控制器9启动驱动电机24,驱动电机24带动转轴25转动,转轴25带动涡轮26转动,涡轮26通过圆环3带动涡轮槽2转动,涡轮槽2带动裁片逐层填铺的下模具8移动至上模具7正下方,气缸5带动上模具7向下移动与下模具8进行合模,方便上模具7和下模具8进行合模处理;
56.步骤三、启动电动推杆19,电动推杆19带动第二中间管23移动,第二中间管23带动第二圆锥20插在第一圆锥14内,关闭第二控制阀40和第三控制阀41,打开第一控制阀39,启动电热风机13,电热风机13产生动力热空气通过第一出气管12和软管4进入上模具7和下模具8内,上模具7和下模具8温度150℃的热空气加热90min,然后继续升温,待温度稳定在165℃后继续加热15min,保温15min后关闭第一控制阀39和电热风机13的加热单元,打开第二控制阀40和第三控制阀41吹入常温空气,温度感应器34监测温度低于75℃时成型结束,同时上料位置处进行上料,一次成型,无需将合成纤维预热到半熔融状态后放入预热的模具中,缩短了作业时间;
57.步骤四、气缸5带动上模具7向上移动,上模具7带动t形插杆18向上移动,t形插杆18与z形板6接触时t形插杆18向下移动,t形插杆18的底部推动上模具7内的聚酯纤维棉模塑与上模具7分离,控制器9启动驱动电机24,驱动电机24带动转轴25转动,转轴25带动涡轮26转动,涡轮26通过圆环3带动涡轮槽2转动,涡轮槽2带动成型后的下模具8移动,下模具8带动下推杆27与直板37顶部的三角块38接触,三角块38推动下推杆27向上移动,下推杆27带动下模具8内内的聚酯纤维棉模塑与下模具8分离,便于成型后的聚酯纤维棉模塑在下料位置处从上模具7和下模具8内取出,同时,上料位置处进行上料、成型位置处进行成型,上料、成型和下料同步进行,利于企业连续化生产,裁片填充模具环节时间常会,裁片数量大,利于实际填铺操作,利于成型各种形象的产品,有利于合成纤维无纺棉大规模应用到车辆座椅。
58.在本说明书的描述中,参考术语
″
一个实施例
″
、
″
示例
″
、
″
具体示例
″
等的描述意指结合该实施例或示例描述的具体特征、结构、材料或者特点包含于本发明的至少一个实施例或示例中。在本说明书中,对上述术语的示意性表述不一定指的是相同的实施例或示例。而且,描述的具体特征、结构、材料或者特点可以在任何的一个或多个实施例或示例中以合适的方式结合。
59.以上公开的本发明优选实施例只是用于帮助阐述本发明。优选实施例并没有详尽叙述所有的细节,也不限制该发明仅为的具体实施方式。显然,根据本说明书的内容,可作很多的修改和变化。本说明书选取并具体描述这些实施例,是为了更好地解释本发明的原理和实际应用,从而使所属技术领域技术人员能很好地理解和利用本发明。本发明仅受权利要求书及其全部范围和等效物的限制。