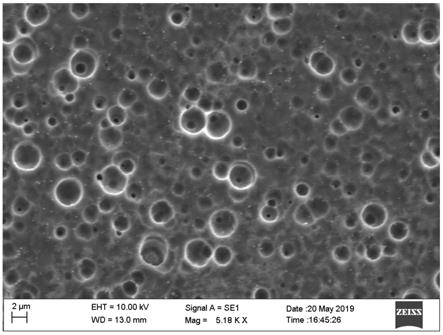
1.本发明涉及封装外壳加工技术领域,尤其涉及一种塑料封装外壳的制备方法。
背景技术:2.半导体器件的塑料封装外壳通常采用灌封的工艺,其流程通常为:将加工的金属引线框架镀金,在金属引线框架上焊接或粘结芯片,在芯片的镀金区域和金属引线框架表面上键合金丝做电路互连;用灌胶机把液态的热固性环氧树脂灌封芯片和金属引线框架,再加热使环氧树脂固化,使所有的缝隙都被填充,不允许有空腔,得到内部为实心的器件。上述结构中,芯片完全被热固性的环氧树脂包裹,散热性较差。若采用塑料腔体,则由于塑料与金属引线的气密性较差,影响芯片的寿命。
技术实现要素:3.针对以上技术问题,本发明提供一种塑料封装外壳的制备方法,其采用注塑工艺制备塑料环与金属热沉形成密封腔体,并对金属引线进行处理,增强其与塑料结合的气密性,不仅达到气密性密封,且提高了器件的散热性能。
4.为达到上述发明目的,本发明实施例采用了如下的技术方案:
5.第一方面,本发明实施例提供一种塑料封装外壳的制备方法,具体包括以下步骤:
6.制备金属引线框架;
7.将所述金属引线框架的预设区域在酸性微蚀溶液中进行微坑刻蚀,然后覆以含有硫键的有机物分子膜;
8.制备注塑模具,所述注塑模具包括上模和下模,所述上、下模扣合形成环状的型腔,在所述注塑模具上加工与所述金属引线框架的预设区域适配的凹槽;
9.将所述金属引线框架的预设区域限位在扣合的所述注塑模具内,通过注塑工艺形成设有金属引线框架的塑料环,其中,所述金属引线框架的一端伸入所述塑料环的环腔用于与芯片键合,另一端伸出所述塑料环的外侧壁用于与外部电路连接;
10.在所述塑料环的底部粘接金属热沉。
11.该制备方法采用注塑工艺制备设有金属引线框架的塑料环,再将所得塑料环与金属热沉和盖板形成密封腔体,并同时结合对金属引线框架预设区域的微坑刻蚀和覆膜处理,金属引线框架的预设区域形成的微坑可增加其与塑料的接触表面积,覆膜后,有机物分子膜能够通过硫键同时与塑料和金属产生化学反应,使塑料与金属牢固结合,从而增强其与塑料结合的气密性,使所得塑料封装外壳不仅达到气密性密封,且提高了器件的散热性能。
12.优选地,所述金属引线框架通过冲制或刻蚀的方法制得。
13.优选地,所述金属引线框架的预设区域还设有贯通其上下表面的通孔用于所述上、下模内塑料的交联,能够增加与塑料互相咬合,在能够提高互锁的强度。
14.优选地,所述塑料封装外壳的制备方法还包括注塑用于盖封所述塑料环的盖板。
15.所述上模和下模扣合后呈台阶状,所述金属引线框架的一端设置在台阶上。
16.可选地,在所述下模的上表面设有2个以上用于注塑工艺中顶杆顶出成型件的顶出孔,在所述下模的下表面设有2个以上用于注塑工艺中顶杆顶出成型件的顶出孔,便于注塑后将模具内的塑料从模具中推出。
17.优选地,所述微坑刻蚀的步骤包括:
18.将所述金属引线框架的预设区域除油除渣、去除氧化膜,完成预处理;
19.将预处理后的所述金属引线框架的预设区域浸入酸性微蚀试剂中,55~65s后取出,水洗;所述酸性微蚀试剂中含有40~60g/l的铁氰化钾、80~120g/l的盐酸、40~60g/l的硝酸、250~350g/l的氯化铵、20~30g/l的氯化铜和50~70g/l的硫酸,溶剂为水。金属引线框架的预设区域表面经除油除渣、去除氧化膜后,其表面不连续的自然氧化膜可被去除。上述酸性微蚀试剂在特定的浸泡时间内能够能够使金属引线框架的预设区域形成微坑,增加金属引线与塑料的接触面积,并吸附一定的胺类物质,有助于金属表面与塑料之间形成锚栓结构,增加结合紧密性。
20.优选地,所述酸性微蚀试剂含有45~55g/l的铁氰化钾、90~110g/l的盐酸、45~55g/l的硝酸、280~320g/l的氯化铵、22~28g/l的氯化铜和55~65g/l的硫酸。各成分进一步优选的浓度为:50g/l的铁氰化钾、100g/l的盐酸、50g/l的硝酸、300g/l的氯化铵、25g/l的氯化铜和60g/l的硫酸。
21.优选地,所述微坑刻蚀的步骤还包括:将水洗后的所述金属引线框架的预设区域经碱性水溶液除渣、酸性水溶液活化,烘干。碱性水溶液能够中和金属引线框架的预设区域可能残存的酸性微蚀试剂,并进一步去除其表面残留的氧化疏松层,完成除渣处理。随后使用酸性水溶液,能够中和碱液,活化金属引线框架的预设区域表面,增加其对胺类物质的吸附。经碱性水溶液除渣、酸性水溶液活化后,金属引线框架的预设区域即可形成大量密布的纳米级微坑,进一步增加金属引线框架的预设区域的比表面积,增加其与塑料的接触面积。
22.优选地,所述碱性水溶液除渣的具体步骤为:将水洗后的所述金属引线框架的预设区域浸于25~40℃浓度为40~60g/l的烧碱溶液中4~6min,取出后迅速进行水洗。烧碱溶液的浓度可进一步优选采用50g/l。浸泡时间优选为5min。
23.所述酸性水溶液活化的步骤包括:将经碱性水溶液除渣的所述金属引线框架的预设区域浸于酸性水溶液中4~6min,取出后迅速进行水洗;所述酸性水溶液含有80~120g/l的硫酸、80~120g/l的磷酸和80~120g/l的草酸氨。酸性水溶液中各溶质的成分进一步优选采用100g/l的硫酸、100g/l的磷酸和100g/l的草酸氨。浸泡时间优选为5min。
24.在酸性微蚀试剂、碱性水溶液、酸性水溶液中浸泡后可水洗2次以上,以彻底洗去酸性微蚀试剂、碱性水溶液和酸性水溶液。
25.所述酸性微蚀试剂、酸性水溶液的温度优选采用25~45℃。
26.优选地,所述覆以含有硫键的有机物分子膜的步骤包括:将完成微坑刻蚀的所述金属引线框架的预设区域浸于55~65℃的成膜液10~15min,取出后在20s之内水洗,干燥,其中所述成膜液中含有0.4~0.8mol/l三聚硫氰酸或三聚硫氰酸三钠,5~10g/l二甲基亚砜和5~10g/l成膜树脂,溶剂为55~75%乙醇。所述成膜树脂可选自环氧树脂、酚醛树脂或胺基树脂。优选为胺基树脂。经过该覆膜操作后,经过微坑刻蚀的金属引线框架的预设区域能够形成一层厚度为70
‑
1500nm的含有硫键的氧化膜,该氧化膜内含有的硫醇类物质能够
分别与塑料和金属发生化学反应,使塑料与金属引线框架的预设区域紧密结合,达到气密效果。
27.优选地,所述除油除渣、去除氧化膜的步骤为:将拟处理的金属引线框架的预设区域在除油脱脂溶液中浸泡至油污脱离后,取出,用热水清洗,以去除金属引线框架的预设区域表面的油污及残留;再将除油除渣处理后的金属引线框架的预设区域浸没于10~30wt%的盐酸溶液中4~6min,用于去除金属引线框架的预设区域表面的氧化膜。所述氧化膜依据金属的种类不同而不同。
28.优选地,所述干燥的方式可选择风干和烘干。烘干的温度可采用75~85℃,时间为3~5min。烘干处理后得到的金属引线应进行密闭封装,以防止氧化。
29.优选地,塑料的材质为lcp(液晶聚合物)、lcp改性材料、pps、ps、pbt等耐高温工程塑料,塑料内有玻璃纤维或矿物粉末做填料。
30.金属热沉的材质为铜及铜合金、钨铜、钼铜、cpc、cmc等高导热金属材料。
31.金属引线的材质为铜及铜合金、铝及铝合金、可伐合金等材料。用上述微坑刻蚀的参数条件对以上材质的金属引线进行处理后,金属引线表面可布满直径≤5μm,深度≥1μm的微坑。
32.本发明的有益效果在于:
33.用经过上述微坑刻蚀和覆膜处理得到的金属引线框架的预设区域具有大量覆有含有硫键的有机物分子膜的纳米级微坑,使金属与塑料之间产生纳米级物理接合与化学反应链接合的双重结合。其中纳米级物理接合是指金属引线框架的预设区域表面形成的纳米级微坑使塑料与金属引线之间进行咬合,形成“锚栓效应”,如图1所示;化学反应链接合是指金属引线框架的预设区域表面及纳米级微坑表面形成的有机物分子膜,该有机物分子膜通过其含有的硫键同时与塑料和金属产生化学反应,使塑料与金属引线框架的预设区域牢固结合。
34.采用注塑工艺制备设有经上述微坑刻蚀和覆膜处理的金属引线框架的塑料环,再将所得塑料环与金属热沉和盖板形成密封腔体,所得塑料封装外壳不仅达到气密性密封,且提高了器件的散热性能。
35.金属引线框架预设区域之外的部分可根据需要选择同时进行以上微坑刻蚀和覆膜的处理,本发明对此不做限定,但按本发明的方法对预设区域以外的金属引线进行处理的技术方案也包含在本方面的保护范围之内。
附图说明
36.图1为“锚栓效应”的原理示意图;图中,1代表金属引线,2代表纳米级微坑,3代表氧化膜;
37.图2
‑
3为本发明实施例1中经微蚀处理的金属引线的sem图片;
38.图4为经过本发明实施例1处理后的金属引线的sem图片。
具体实施方式
39.为了使本发明的目的、技术方案及优点更加清楚明白,以下结合附图及实施例,对本发明进行进一步详细说明。应当理解,此处所描述的具体实施例仅仅用以解释本发明,并
不用于限定本发明。
40.实施例1
41.本实施例提供了一种塑料封装外壳的制备方法,塑料材质为液晶聚合物,金属引线的材质为铜。具体包括以下步骤:
42.s1、冲制金属引线框架;
43.s2、将金属引线框架的预设区域进行微坑刻蚀和覆膜处理:
44.(1)将金属引线框架的预设区域在除油脱脂溶液中浸泡至油污脱离后,取出,用热水清洗2次,再浸没于20wt%的盐酸溶液中5min,完成除油除渣、去除氧化铜、氧化亚铜膜的预处理。
45.(2)将预处理后的金属引线框架的预设区域进行微坑刻蚀:
46.①
将预处理后的金属引线框架的预设区域浸入35℃的酸性微蚀试剂中,60s后取出,水洗2次。本实施例的酸性微蚀试剂中含有50g/l的铁氰化钾、100g/l的盐酸、50g/l的硝酸、300g/l的氯化铵、25g/l的氯化铜和60g/l的硫酸,溶剂为水。
47.②
将水洗后的金属引线框架的预设区域浸于35℃浓度为50g/l的烧碱溶液中5min,取出后迅速水洗2次。
48.③
将完成碱性水溶液除渣并水洗的金属引线框架的预设区域浸于35℃的酸性水溶液中5min,取出后迅速水洗2次。本实施例的酸性水溶液含有100g/l的硫酸、100g/l的磷酸和100g/l的草酸氨。
49.将经上述微坑刻蚀的金属引线框架的预设区域表面置于电镜下观察,其形貌如图2、3所示,在金属引线框架的预设区域的表面形成了大量、密集的微坑,从图中可以估算,微坑的直径不大于4μm。
50.(3)用成膜液在完成微坑刻蚀的金属引线框架的预设区域进行覆膜:将完成微坑刻蚀的金属引线框架的预设区域浸于60℃的成膜液中15min,取出后在20s之内水洗;成膜液中包括0.6mol/l三聚硫氰酸,7.5g/l二甲基亚砜和7.5g/l成膜树脂,溶剂为65%乙醇。
51.(4)干燥:使用脱水机风淋2分钟,再在80
±
5℃条件下烘干,然后在常温条件下降至室温。将经上述处理方法得到的金属引线框架的预设区域置于电镜下观察,如图4所示,金属引线框架的预设区域的纳米微坑被新形成的膜状物覆盖,但基本对微坑形态无影响。
52.s3、制备注塑模具,注塑模具包括上模和下模,上、下模扣合形成环状的型腔,在注塑模具上加工与金属引线框架的预设区域适配的凹槽;
53.s4、将金属引线框架的预设区域限位在扣合的注塑模具内,通过注塑工艺形成设有金属引线框架的塑料环,其中,金属引线框架的一端伸入塑料环的环腔用于与芯片键合,另一端伸出塑料环的外侧壁用于与外部电路连接;
54.s5、在塑料环的底部粘接金属热沉,并注塑用于盖封塑料环的盖板。
55.实施例2
56.本实施例提供了一种塑料封装外壳的制备方法,塑料材质为lcp改性材料,金属引线的材质为铜锌合金。具体包括以下步骤:
57.s1、刻蚀加工金属引线框架;
58.s2、将金属引线框架的预设区域进行微坑刻蚀和覆膜处理:
59.(1)按实施例1的方法对金属引线框架的预设区域进行预处理。
60.(2)将预处理后的金属引线框架的预设区域进行微坑刻蚀:
61.①
将预处理后的金属引线框架的预设区域浸入40℃的酸性微蚀试剂中,63s后取出,水洗2次;本实施例的酸性微蚀试剂中含有45g/l的铁氰化钾、90g/l的盐酸、45g/l的硝酸、280/l的氯化铵、22g/l的氯化铜和55g/l的硫酸,溶剂为水。
62.②
将水洗后的金属引线框架的预设区域浸于40℃浓度为45g/l的烧碱溶液中5.5min,取出后迅速水洗2次。
63.③
将完成碱性水溶液除渣并水洗的金属引线框架的预设区域浸于40℃的酸性水溶液中5.5min,取出后迅速水洗2次;本实施例的酸性水溶液含有90g/l的硫酸、90g/l的磷酸和90g/l的草酸氨。
64.将经上述微坑刻蚀的金属引线置于电镜下观察,在金属引线框架的预设区域的表面形成了大量、密集的微坑。
65.(3)用成膜液在完成微坑刻蚀的金属引线框架的预设区域进行覆膜:将完成微坑刻蚀的金属引线框架的预设区域浸于60℃的成膜液中15min,取出后在20s之内水洗;成膜液中包括0.5mol/l三聚硫氰酸三钠,8g/l二甲基亚砜和8g/l成膜树脂,溶剂为70%乙醇。
66.(4)干燥:使用脱水机风淋2分钟,再在80
±
5℃条件下烘干,然后在常温条件下降至室温。将经上述处理方法得到的金属引线框架的预设区域置于电镜下观察,金属引线框架的预设区域表面的纳米微坑被新形成的膜状物覆盖。
67.s3、制备注塑模具,注塑模具包括上模和下模,上、下模扣合形成环状的型腔,在注塑模具上加工与金属引线框架的预设区域适配的凹槽;本实施例的金属引线框架的预设区域还设有贯通其上下表面的通孔用于上、下模内塑料的交联。
68.s4、将金属引线框架的预设区域限位在扣合的注塑模具内,通过注塑工艺形成设有金属引线框架的塑料环,其中,金属引线框架的一端伸入塑料环的环腔用于与芯片键合,另一端伸出塑料环的外侧壁用于与外部电路连接;
69.s5、在塑料环的底部粘接金属热沉,并注塑用于盖封塑料环的盖板。
70.实施例3
71.本实施例提供了一种塑料封装外壳的制备方法,塑料材质为pps,金属引线材质为铜铝合金。具体包括以下步骤:
72.s1、冲制金属引线框架;
73.s2、将金属引线框架的预设区域进行微坑刻蚀和覆膜处理:
74.(1)按实施例1的方法对金属引线框架的预设区域进行预处理。
75.(2)将预处理后的金属引线框架的预设区域进行微坑刻蚀:
76.①
将预处理后的金属引线框架的预设区域浸入30℃的酸性微蚀试剂中,57s后取出,水洗2次;本实施例的酸性微蚀试剂中含有55g/l的铁氰化钾、110g/l的盐酸、55g/l的硝酸、320g/l的氯化铵、28g/l的氯化铜和65g/l的硫酸,溶剂为水。
77.②
将水洗后的金属引线框架的预设区域浸于30℃浓度为55g/l的烧碱溶液中4.5min,取出后迅速水洗2次。
78.③
将完成碱性水溶液除渣并水洗的金属引线框架的预设区域浸于30℃的酸性水溶液中5.5min,取出后迅速水洗2次;本实施例的酸性水溶液含有110g/l的硫酸、110g/l的磷酸和110g/l的草酸氨。
79.将经上述微坑刻蚀的金属引线框架的预设区域置于电镜下观察,在金属引线框架的预设区域的表面形成了大量、密集的微坑。
80.(3)用成膜液在完成微坑刻蚀的金属引线框架的预设区域进行覆膜:将完成微坑刻蚀的金属引线框架的预设区域浸于60℃的成膜液中15min,取出后在20s之内水洗;成膜液中包括0.7mol/l三聚硫氰酸,6g/l二甲基亚砜和6g/l成膜树脂,溶剂为60%乙醇。
81.(4)干燥:使用脱水机风淋2分钟,再在80
±
5℃条件下烘干,然后在常温条件下降至室温。将经上述处理方法得到的金属引线框架的预设区域置于电镜下观察,金属引线引线框架的预设区域表面的纳米微坑被新形成的膜状物覆盖。
82.s3、制备注塑模具,注塑模具包括上模和下模,上、下模扣合形成环状的型腔,在注塑模具上加工与金属引线框架的预设区域适配的凹槽;本实施例的金属引线框架的预设区域还设有贯通其上下表面的通孔用于上、下模内塑料的交联。本实施例中上模和下模扣合后呈台阶状,金属引线框架的一端设置在台阶上。
83.s4、将金属引线框架的预设区域限位在扣合的注塑模具内,通过注塑工艺形成设有金属引线框架的塑料环,其中,金属引线框架的一端伸入塑料环的环腔用于与芯片键合,另一端伸出塑料环的外侧壁用于与外部电路连接;
84.s5、在塑料环的底部粘接金属热沉,并注塑用于盖封塑料环的盖板。
85.实施例4
86.本实施例提供了一种塑料封装外壳的制备方法,塑料材质为ps,金属引线的材质为铝硅合金。具体包括以下步骤:
87.s1、刻蚀加工金属引线框架;
88.s2、将金属引线框架的预设区域进行微坑刻蚀和覆膜处理:
89.(1)按实施例1的方法对金属引线框架的预设区域进行预处理。
90.(2)将预处理后的金属引线框架的预设区域进行微坑刻蚀:
91.①
将预处理后的金属引线框架的预设区域浸入45℃的酸性微蚀试剂中,65s后取出,水洗2次。本实施例的酸性微蚀试剂中含有40g/l的铁氰化钾、80g/l的盐酸、40g/l的硝酸、250g/l的氯化铵、20g/l的氯化铜和50g/l的硫酸,溶剂为水。
92.②
将水洗后的金属引线框架的预设区域浸于40℃浓度为40g/l的烧碱溶液中6min,取出后迅速水洗2次。
93.③
将完成碱性水溶液除渣并水洗的金属引线框架的预设区域浸于45℃的酸性水溶液中4min,取出后迅速水洗2次。本实施例的酸性水溶液含有80g/l的硫酸、80g/l的磷酸和80g/l的草酸氨。
94.将经上述微坑刻蚀的金属引线框架的预设区域置于电镜下观察,在金属引线框架的预设区域的表面形成了大量、密集的微坑。
95.(3)用成膜液在完成微坑刻蚀的金属引线框架的预设区域进行覆膜:将完成微坑刻蚀的金属引线框架的预设区域浸于55℃的成膜液中15min,取出后在20s之内水洗;成膜液中包括0.4mol/l三聚硫氰酸三钠,5g/l二甲基亚砜和5g/l成膜树脂,溶剂为55%乙醇。
96.(4)干燥:使用脱水机风淋2分钟,再在80
±
5℃条件下烘干,然后在常温条件下降至室温。将经上述处理方法得到的金属框架的预设区域置于电镜下观察,金属引线微坑刻蚀表面的纳米微坑被新形成的膜状物覆盖。
97.s3、制备注塑模具,注塑模具包括上模和下模,上、下模扣合形成环状的型腔,在注塑模具上加工与金属引线框架的预设区域适配的凹槽;本实施例的金属引线框架的预设区域还设有贯通其上下表面的通孔用于上、下模内塑料的交联。本实施例中上模和下模扣合后呈台阶状,金属引线框架的一端设置在台阶上,在下模的上表面设有2个用于注塑工艺中顶杆顶出成型件的顶出孔。
98.s4、将金属引线框架的预设区域限位在扣合的注塑模具内,通过注塑工艺形成设有金属引线框架的塑料环,其中,金属引线框架的一端伸入塑料环的环腔用于与芯片键合,另一端伸出塑料环的外侧壁用于与外部电路连接;
99.s5、在塑料环的底部粘接金属热沉,并注塑用于盖封塑料环的盖板。
100.实施例5
101.本实施例提供了一种塑料封装外壳的制备方法,塑料材质为pbt,金属引线的材质为可伐合金。具体包括以下步骤:
102.s1、冲制金属引线框架;
103.s2、将金属引线框架的预设区域进行微坑刻蚀和覆膜处理:
104.(1)按实施例1的方法对金属引线框架的预设区域进行预处理。
105.(2)将预处理后的金属引线框架的预设区域进行微坑刻蚀:
106.①
将预处理后的金属引线框架的预设区域浸入25℃的酸性微蚀试剂中,55s后取出,水洗2次。本实施例的酸性微蚀试剂中含有60g/l的铁氰化钾、120g/l的盐酸、60g/l的硝酸、350g/l的氯化铵、30g/l的氯化铜和70g/l的硫酸,溶剂为水。
107.②
将水洗后的金属引线框架的预设区域浸于25℃浓度为60g/l的烧碱溶液中4min,取出后迅速水洗2次。
108.③
将完成碱性水溶液除渣并水洗的金属引线框架的预设区域浸于25℃的酸性水溶液中6min,取出后迅速水洗2次。本实施例的酸性水溶液含有120g/l的硫酸、120g/l的磷酸和120g/l的草酸氨。
109.将经上述微坑刻蚀的金属引线框架的预设区域置于电镜下观察,在金属引线框架的预设区域的表面形成了大量、密集的微坑。
110.(3)用成膜液在完成微坑刻蚀的金属引线框架的预设区域进行覆膜:将完成微坑刻蚀的金属引线框架的预设区域浸于65℃的成膜液中10min,取出后在20s之内水洗;成膜液中包括0.8mol/l三聚硫氰酸三钠,10g/l二甲基亚砜和10g/l成膜树脂,溶剂为75%乙醇。
111.(4)干燥:使用脱水机风淋2分钟,再在80
±
5℃条件下烘干,然后在常温条件下降至室温。将经上述处理方法得到的金属框架的预设区域置于电镜下观察,金属引线框架的预设区域表面的纳米微坑被新形成的膜状物覆盖。
112.s3、制备注塑模具,注塑模具包括上模和下模,上、下模扣合形成环状的型腔,在注塑模具上加工与金属引线框架的预设区域适配的凹槽;本实施例的金属引线框架的预设区域还设有贯通其上下表面的通孔用于上、下模内塑料的交联。本实施例中上模和下模扣合后呈台阶状,金属引线框架的一端设置在台阶上,在下模的上表面设有2个用于注塑工艺中顶杆顶出成型件的顶出孔。在下模的下表面设有2个以上用于注塑工艺中顶杆顶出成型件的顶出孔。
113.s4、将金属引线框架的预设区域限位在扣合的注塑模具内,通过注塑工艺形成设
有金属引线框架的塑料环,其中,金属引线框架的一端伸入塑料环的环腔用于与芯片键合,另一端伸出塑料环的外侧壁用于与外部电路连接;
114.s5、在塑料环的底部粘接金属热沉,并注塑用于盖封塑料环的盖板。
115.按照gjb548的方法1014条件a4的方法对实施例1~5所得塑料封装外壳进行气密效果的检测,使用氦气检漏。经检测,漏率≤1*10
‑8pa
·
m3/s(he)。
116.以上所述仅为本发明的较佳实施例而已,并不用以限制本发明,凡在本发明的精神和原则之内所作的任何修改、等同替换和改进等,均应包含在本发明的保护范围之内。