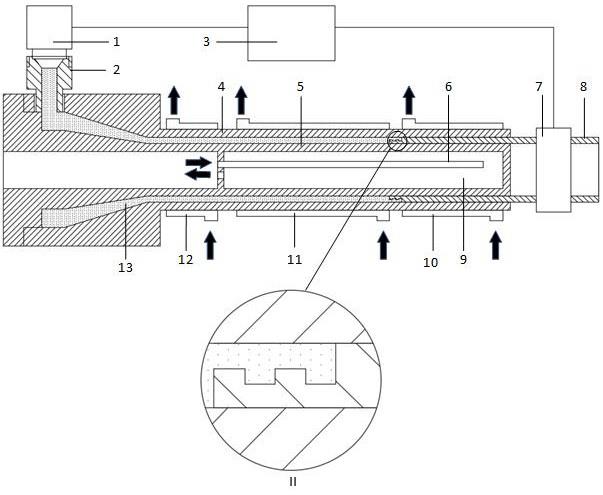
1.本发明涉及塑料管材连续挤出领域,具体涉及用于双环戊二烯聚合反应的管材连续挤出的装置及工艺。
背景技术:2.1985年,美国hercules公司和goodrich公司联手实现了聚双环戊二烯(简称pdcpd)材料的工业化,并在1987年开始商业应用。pdcpd是一种由单体双环戊二烯(简称dcpd)发生开环易位聚合反应聚合而成高分子材料,广泛应用于化工设备、工程机械、医疗设备、汽车配件等领域。2018年,中国大成普道新材料有限公司成立,标志着中国成为继美日之后全球第三个掌握pdcpd原料技术、工业化生产技术的国家。
3.pdcpd成型方法为反应注射成型(rim)工艺,dcpd原料粘度极低,模具成本和工艺成本都很低,成型材料具有低密度、强抗腐蚀性、高低温稳定性好、绿色环保的优点,其力学性能与传统塑料相当甚至更为出色,是一种优异的热固性工程塑料。pdcpd目前的应用主要是传统的单件,依赖于模具的rim成型方法。然可以预见,pdcpd在化工、卫浴、排污、给水等领域的单件的成功应用,预示着它在连续件也有广泛的应用前景,具体领域如化工管、排污管、输送管、城市地下管网等。然而dcpd原料不同于传统聚乙烯、聚丙烯等热熔性塑料,最大的特点有两点:第一,粘度极低,几乎接近水的粘度,不易保持其形状;第二,聚合过程发生化学反应,并且放出大量热,如果温度控制不好,制品会产生缺陷甚至报废。这两点是dcpd应用于管材连续挤出工艺要解决的难点。
技术实现要素:4.本发明所要解决的技术问题是提供一种用于双环戊二烯聚合反应的管材连续挤出装置,以及基于该装置的管材成型工艺;设计一个金属圆柱环作为辅助装置,通过牵引装置的配合,对dcpd原料施加背压让其得以保持管材形状,分三段温度控制,控制管材的连续稳定挤出。
5.本发明的技术方案是:设计一种用于双环戊二烯(简称dcpd)聚合反应的管材连续挤出装置,该装置包括混合头、注射口、口模和芯棒,其特征在于:设置三段介质环路控制装置的温度,分别是隔热介质环路、加热介质环路和冷却介质环路,隔热介质环路防止其右端的热量传递到左端,保持左边装置为低温状态,dcpd混合原料由注射口进入模腔时,受到加热介质环路的加热发生反应凝胶,经冷却介质环路冷却固化成型,而后退出模腔;芯棒的温度由中心空腔通以载温流体介质控制,由通道流入中心空腔最右端,再由中心空腔左端出口流出;模腔尾部设置金属圆柱环,在装置开启阶段,保持低粘度液态dcpd混合原料在模型内不流失,随着dcpd混合原料注入配合向右移动,直至原料凝胶、固化成型;所述金属圆柱环与dcpd混合原料接触处设计为矩形齿状,dcpd混合原料固化后与金属圆柱环相互咬合,再由牵引装置引曳拉出固化成型的管材;所述牵引装置的牵引力的大小和方向、混合头的注射压力由控制器协调
控制,在装置启动阶段,牵引装置施加给金属圆柱环的力方向向左,给液态dcpd混合原料施加背压,在稳定挤出阶段,牵引装置施加给金属圆柱环的力方向向右,克服dcpd混合原料固化段管材与模腔的摩擦力,需要与混合头的注射压力协调。
6.进一步地,所述三段介质环路的介质为载热流体,如水、热油等;所述隔热介质环路介质温度为22℃,该利于温度下保持dcpd混合原料中的催化剂活性;所述加热介质环路介质温度高于冷却介质环路介质温度10℃~20℃;所述中心空腔载温流体介质温度与冷却介质环路介质温度相同。
7.进一步地,所述的金属圆环的一端以所述的矩形齿状为截面绕中心轴形成不完整的环槽,不完整的环槽可便于清理固化的dcpd原料,以便下一周期重复使用金属圆环。
8.基于设计dcpd聚合反应的管材连续挤出装置,提出dcpd管材连续挤出成型工艺,其特征在于:模腔中的dcpd混合原料分三段进行温度控制,分别是隔热介质环路、加热介质环路和冷却介质环路,加热介质环路和冷却介质环路之间形成稳定的温差,衔接dcpd从吸热引发反应到被冷却定型两个过程,加热介质环路和中心空腔之间也需形成稳定的温差,使dcpd管材从外管壁向内管壁的方向反应,保证外管壁的表面质量;在挤出过程中,为确保dcpd液相、固液相和固相的连续性,控制器对混合头混合压力和牵引装置的牵引力进行协调控制,保证dcpd混合原料形成一定压力并且匀速稳定挤出;具体工艺步骤实施如下:步骤1:反应体系主要包括钨、钼基为主的催化剂和dcpd,催化剂与dcpd比列为800:1~1400:1,整个体系分为a、b两组分,体系温度维持在22℃左右;步骤2:隔热介质环路通22℃的流动介质,加热介质环路通75℃的流动介质,冷却介质环路和中心空腔通55℃的流动介质,使口模三段温度维持在22℃、70℃、50℃左右,芯棒温度维持在50℃左右;步骤3:金属圆柱环堵在模腔内,其左端应与加热介质环路右端对齐或者位于中间,可根据挤出速度和温度来调整;牵引装置首先对所述金属圆柱环起夹持作用,等待dcpd混合原料的注入;步骤4:启动阶段,待装置温度稳定后,a、b组分经过注射机过滤、按1:1计量,然后高压泵送至混合头对撞混合形成dcpd混合原料并经注射口注入模腔,对撞混合压力为5~6mpa;混合后经注射口注入模腔,形成对dcpd混合原料向右的推力f
15
,牵引装置对所述金属圆柱环施加向左的相反相等的牵引力f
14
,以形成背压,使dcpd混合原料充满模腔并保持连续性;步骤5:所述金属圆柱环在牵引装置的牵引下匀速向右移动,在加热介质环路区域,dcpd混合原料受热引发聚合反应,原料凝胶并逐渐固化成型管材,与模腔壁的摩擦力f逐渐增大,在此变化过程中,控制器应控制牵引装置对金属圆柱环施加的所述牵引力f
14
,使所述推力f
15
、所述摩擦力f与所述牵引力f
14
三力之和为零,进而dcpd混合原料匀速稳定向右移动;在dcpd混合原料固化后,其与金属圆柱环的矩形齿状结构咬合,便于牵引固化的dcpd混合原料;步骤6:稳定挤出阶段,当所述金属圆柱环被完全推出模腔后,dcpd混合原料在模腔内形成稳定的三相,液相、固液相和固相,固相即为固化成型的管材,在冷却介质环路区域进一步固化并且将反应放出的大量热量带走,避免发生过热和爆聚,最终达到出模温度;此时,固相代替了所述金属圆柱环的作用,而且固相与模腔壁的摩擦力基本稳定,此时设置
牵引装置对固相的牵引力f
14
向右并且为定值,保持管材的连续挤出成型;步骤7:通过切割装置将所述金属圆柱环从固相上切断,并清理残余的dcpd固相,以备下一次启动装置使用;由于所述金属圆柱环与固相咬合的结构是不完整环槽,使清理工作十分方便。
9.进一步地,由于所述对撞混合压力一般保持不变,因此所述推力f
15
由推力曲线表示,所述摩擦力f由摩擦力曲线表示,其随着固化进行逐渐增大直至稳定挤出阶段保持为常数,推力曲线与摩擦力曲线相加得合力曲线,合力曲线取反得牵引力曲线,此即为牵引力f
14
的工艺控制规律:牵引力f
14
首先方向向左,大小逐渐减小至零,而后反向向右,大小逐渐增大至一常数。
10.进一步地,隔热介质环路将其右端由于dcpd混合原料反应放热和加热介质环路的热量带走,防止其加热隔热介质环路左端的dcpd混合原料,造成提前反应固化,堵住模腔通道。
11.本发明的有益效果是:1.提出了一种pdcpd材料的新的应用方式及其生产方式——管材连续挤出,设计了连续挤出装置,特别设计了金属圆柱环及其控制装置,辅助液态dcpd形成背压,维持管材形状。
12.2.依据反应注射成型原理设计三段温度控制,第一段隔热介质环路将反应热与外热源与模具前部分开,防止造成dcpd提前固化堵住机头,加热介质环路和冷却介质环路分别触发反应和散热,通过控制为稳定的恒定的温度,保证管材成型质量。
13.3.提出了牵引力的控制曲线规律,保证dcpd物料液相、固液相和固相的连续性和致密性,保证管材成型质量和成型过程的连续性。
附图说明
14.附图1是本装置总体结构;附图2是带不完整槽环的金属圆柱环的三维图;附图3是稳态挤出阶段的dcpd三相分布图;附图4是牵引力f
14
、推力f
15
、摩擦力f控制曲线。
具体实施方式
15.下面将结合附图及具体实例对本发明进一步详述,方便本领域的技术人员在阅读了本发明以后进行指导生产,技术人员对发明的各种等价形式的修改或等同替换,而不脱离本发明的宗旨和范围,均应涵盖在本发明的保护范围之中。
16.dcpd聚合反应原理。dcpd的分子式为c
10
h
12
属于降冰片烯,钨、钼基催化剂和dcpd形成的a、b组分原料的粘度仅为0.3左右,流动性非常好,在没有约束的情况下不能保持固定的形状;在催化剂作用下,发生开环易位聚合反应聚合成高分子材料,现在广泛用作工程塑料;聚合过程中,dcpd中降冰片烯环开环聚合,由于环张力的释放,聚合反应是一个快速的强放热过程,生产实践表明,升温可达200℃。
17.参考附图1和附图3,本发明涉及的一种用于双环戊二烯简称dcpd聚合反应的管材连续挤出装置,包括混合头1、注射口2、口模4和芯棒5,其特征在于:设置三段介质环路控制
装置的温度,分别是隔热介质环路12、加热介质环路11和冷却介质环路10,三段介质环路的流体介质流动方向见附图1中的箭头,都是从下往上流保证流体域模具充分接触;隔热介质环路12的作用是防止其右端的热量传递到左端,保持左边装置为低温状态;芯棒5的温度由中心空腔9通以载温流体介质控制,由通道6流入中心空腔9最右端,再由中心空腔9左端出口流出;模腔尾部设置金属圆柱环8,其与dcpd混合原料13接触处设计为矩形齿状,并且以所述的矩形齿状为截面绕中心轴形成不完整的环槽,如附图2所示,dcpd混合原料13固化后与金属圆柱环8相互咬合,再由牵引装置7引曳拉出固化成型的管材。
18.金属圆环8的不完整的环槽可便于清理固化的dcpd原料,以便下一周期重复使用。
19.牵引装置7的牵引力的大小和方向、混合头1的注射压力由控制器3协调控制,在装置启动阶段,牵引装置7施加给金属圆柱环8的力方向向左,给液态dcpd混合原料13施加背压,在稳定挤出阶段,牵引装置7施加给金属圆柱环8的力方向向右,克服dcpd混合原料13固化段管材与模腔的摩擦力,需要与混合头1的注射压力协调。
20.三段介质环路的介质为载热流体,如水、热油等;所述隔热介质环路12介质温度为22℃,该利于温度下保持dcpd混合原料13中的催化剂活性;所述加热介质环路11介质温度高于冷却介质环路10介质温度10℃~20℃;所述中心空腔9载温流体介质温度与冷却介质环路10介质温度相同。
21.该装置的使用过程和成型工艺如下:模腔中的dcpd混合原料13分三段进行温度控制,实际上主要依据dcpd的反应原理来设置,dcpd原料常温下反应速率极低,但是一旦升温加热,会引发链反应,反应放热又进一步加速反应,因此反应速度极快,但是反应放出的大量热,如果不及时散热,会造成爆聚引起缺陷,因此需分两段控制,将引发反应的温度设置的尽可能高,放出热量热由更低温度的冷却介质带走;三段温度分别是隔热介质环路12、加热介质环路11和冷却介质环路10,加热介质环路11和冷却介质环路10之间形成稳定的温差,衔接dcpd从吸热引发反应到被冷却定型两个过程,加热介质环路11和中心空腔9之间也需形成稳定的温差,使dcpd管材从外管壁向内管壁的方向反应,保证外管壁的表面质量;在挤出过程中,为确保dcpd液相131、固液相132和固相133的连续性,控制器3对混合头1混合压力和牵引装置7的牵引力进行协调控制,保证dcpd混合原料13形成一定压力并且匀速稳定挤出;隔热介质环路12的作用主要是防止隔热介质环路12左端的dcpd混合原料13被加热,造成提前反应固化,堵住模腔通道。
22.下面是具体的工艺过程:反应体系主要包括钨、钼基为主的催化剂和dcpd,催化剂与dcpd比列为800:1~1400:1,整个体系分为a、b两组分,体系温度维持在22℃左右;隔热介质环路12通22℃的流动介质,加热介质环路11通75℃的流动介质,冷却介质环路10和中心空腔9通55℃的流动介质,使口模4三段温度维持在22℃、70℃、50℃左右,芯棒温度维持在50℃左右;金属圆柱环8堵在模腔内,其左端应与加热介质环路11右端对齐或者位于中间,可根据挤出速度和温度来调整;牵引装置7首先对所述金属圆柱环8起夹持作用,等待dcpd混合原料13的注入;启动阶段,待装置温度稳定后,a、b组分经过注射机过滤、按1:1计量,然后高压泵送至混合头1对撞混合形成dcpd混合原料13并经注射口2注入模腔,对撞混合压力为5~
6mpa;混合后经注射口2注入模腔,形成对dcpd混合原料13向右的推力f
15
,牵引装置7对所述金属圆柱环8施加向左的相反相等的牵引力f
14
,以形成背压,使dcpd混合原料13充满模腔并保持连续性;所述注射机在附图中没有表示出来,其作为配套的设备和本装置一起使用,注射机的作用是将a、b组分分两条输送路线,由计量泵进行计量、高压泵送,经过滤器后输送至混合头1进行两组分的对撞混合。
23.金属圆柱环8在牵引装置7的牵引下匀速向右移动,在加热介质环路11区域,dcpd混合原料13受热引发聚合反应,原料凝胶并逐渐固化成型管材,与模腔壁的摩擦力f逐渐增大,在此变化过程中,控制器3应控制牵引装置7对金属圆柱环8施加的所述牵引力f
14
,使所述推力f
15
、所述摩擦力f与所述牵引力f
14
三力之和为零,进而dcpd混合原料13匀速稳定向右移动;在dcpd混合原料13固化后,其与金属圆柱环8的矩形齿状结构咬合,便于牵引固化的dcpd混合原料13;稳定挤出阶段,当所述金属圆柱环8被完全推出模腔后,dcpd混合原料13在模腔内形成稳定的三相,液相131、固液相132和固相133,固相133即为固化成型的管材,在冷却介质环路10区域进一步固化并且将反应放出的大量热量带走,避免发生过热和爆聚,最终达到出模温度;此时,固相133代替了所述金属圆柱环8的作用,而且固相133与模腔壁的摩擦力基本稳定,此时设置牵引装置7对固相133的牵引力f
14
向右并且为定值,保持管材的连续挤出成型;通过切割装置将所述金属圆柱环8从固相133上切断,并清理残余的dcpd固相,以备下一次启动装置使用;由于所述金属圆柱环8与固相133咬合的结构是不完整环槽,使清理工作十分方便。
24.如附图4所示,由于所述对撞混合压力一般保持不变,因此所述推力f
15
由推力曲线15表示,所述摩擦力f由摩擦力曲线17表示,其随着固化进行逐渐增大直至稳定挤出阶段保持为常数,推力曲线15与摩擦力曲线17相加得合力曲线16,合力曲线16取反得牵引力曲线14,此即为牵引力f
14
的工艺控制规律:牵引力f
14
首先方向向左,大小逐渐减小至零,而后反向向右,大小逐渐增大至一常数。摩擦力f与固化度和温度有关,是被动的物理量;推力f
15
由注射压力决定,一般一个公益过程确定后,注射压力是一个常数,但会随着零件大小、原料特性、注射回路的复杂性有所调整;牵引力f
14
受控制,主要依据摩擦力f和推力f
15
来确定,总的控制规律为牵引力曲线14。