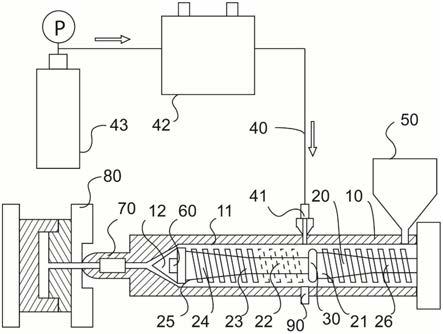
[0001]
本实用新型涉及注塑技术领域,尤其是涉及一种微孔发泡注塑成型塑化装置。
背景技术:[0002]
微孔发泡成型技术利用超临界流体,比如超临界二氧化碳或氮气作为物理发泡剂,将注塑成型工艺与发泡成型技术相结合形成了微孔发泡注塑成型工艺。
[0003]
然而,微孔发泡注塑成型工艺需采用超临界流体作为物理发泡剂,必须配备超临界流体增压设备先对普通钢气瓶中的气体进行增压(20~30mpa),然后再将超高压气体经专门注气口引入到注塑机螺杆中。
[0004]
该微孔发泡注塑成型过程需要使用超临界流体增压装置来增压气体,导致其设备昂贵,限制了其在工业中的广泛应用,因此有必要予以改进。
技术实现要素:[0005]
基于此,有必要针对上述问题,提供一种微孔发泡注塑成型塑化装置。
[0006]
一种微孔发泡注塑成型塑化装置,包括:
[0007]
注塑组件,包括料管、装配于所述料管的螺杆和喷嘴装置、安装于所述螺杆的第一单向阀,所述螺杆包括沿自身中轴线方向依次设置的第一压缩段、自洁段及混合段,所述自洁段的螺纹槽深度与所述第一压缩段所对应的螺纹槽深度的比例大于等于1.5且小于等于2.5,所述第一单向阀位于所述第一压缩段和所述自洁段之间,用于单向引导所述第一压缩段内处于熔融状态的聚合物进入所述自洁段;
[0008]
供料组件,连接至所述料管,用于向所述第一压缩段输送原料;
[0009]
低压供气组件,连接至所述料管,用于向所述料管内输出物理发泡剂;
[0010]
所述自洁段位于所述第一单向阀和所述混合段之间,所述物理发泡剂和所述聚合物自所述自洁段进入所述混合段后混合,并沿所述喷嘴装置输出,其中,所述自洁段的轴向长度占据螺杆的总长度的比例为15%~30%。
[0011]
在其中一个实施例中,所述螺杆还包括第二压缩段,所述混合段位于所述第二压缩段和所述自洁段之间,所述第二压缩段的螺纹槽深度自所述混合段向远离所述第一单向阀方向逐渐减小。
[0012]
在其中一个实施例中,所述螺杆还包括计量段,所述第二压缩段位于所述计量段和所述混合段之间,所述计量段的螺纹槽深度等于所述第二压缩段的最小螺纹槽深度,其中,所述混合段、第二压缩段和所述计量段的轴向长度总合占据螺杆的总长度的比例为30%~40%。
[0013]
在其中一个实施例中,所述注塑组件还包括安装于所述螺杆一端的第二单向阀,所述料管包括储料区和连通至所述储料区的喷嘴通道,所述第二单向阀位于所述储料区并与所述喷嘴通道相对设置,所述第二单向阀用于将所述计量段单向连通至所述储料区。
[0014]
在其中一个实施例中,所述螺杆还包括进料区,所述第一压缩段位于所述进料区
和所述第一单向阀之间,所述进料区的螺纹槽深度大于所述第一压缩段所对应的螺纹槽深度且所述进料区的一端螺纹槽深度逐渐减小并相交至所述第一压缩段,所述供料组件连通至所述进料区,其中,所述进料区和所述第一压缩段的轴向长度总合占据螺杆的总长度的比例为30%~45%。
[0015]
在其中一个实施例中,所述螺杆沿轴线方向的螺纹外径尺寸相同,所述螺杆的直径设为30mm-35mm,螺杆长径比为25-30。
[0016]
在其中一个实施例中,所述低压供气组件包括储气罐、连接至所述储气罐的调节件和安装于所述料管的进气阀,所述调节件连接于所述进气阀,用于输出流量及压力可调节的物理发泡剂。
[0017]
在其中一个实施例中,所述进气阀输出的物理发泡剂的气体压力范围大于1mpa且小于10mpa。
[0018]
在其中一个实施例中,所述自洁段设置有两圈及以上的连续螺纹。
[0019]
在其中一个实施例中,所述注塑组件还包括安装于所述料管的压力传感器,所述压力传感器与所述自洁段连通。
[0020]
本实用新型的微孔发泡注塑成型塑化装置中,第一压缩段的螺纹槽深度小于自洁段的螺纹槽深度,所以,聚合物熔体自第一压缩段进入自洁段的熔体压力减小,可以降低低压供气组件输出的物理发泡剂与聚合物熔体混合时的压力要求,实现低压气体混合,降低设备要求。
附图说明
[0021]
图1是本实用新型的微孔发泡注塑成型塑化装置的结构示意图;
[0022]
图2是本实用新型的螺杆的结构示意图。
[0023]
图中:10、料管;11、原料通道;12、储料区;20、螺杆;21、第一压缩段;22、自洁段;23、混合段;24、第二压缩段;25、计量段;26、进料区;30、第一单向阀;40、低压供气组件;41、进气阀;42、调节件;43、储气罐;50、供料组件;60、第二单向阀;70、喷嘴装置;80、模具装置;90、压力传感器。
具体实施方式
[0024]
以下将结合附图对本实用新型提供的微孔发泡注塑成型塑化装置作进一步说明。
[0025]
如图1和图2所示,本实用新型提供的微孔发泡注塑成型塑化装置包括:注塑组件、供料组件50和低压供气组件40。注塑组件包括料管10、装配于所述料管10的螺杆20和喷嘴装置70、安装于所述螺杆20的第一单向阀30,料管10设置有孔状的原料通道11,螺杆20插接连接于原料通道11内。螺杆20的外周壁设置有螺纹,螺杆20转动以使位于螺纹槽内的原料沿螺杆20的轴线方向移动输送。可选地,所述螺杆20沿轴线方向的螺纹外径尺寸相同,以使螺杆20与原料通道11的孔壁配合均衡,且装配方便。该螺杆可应用于100吨的吨位设备中,将螺杆20分区设置,可以促进气体和聚合物混合并减少螺杆长径比。所述螺杆的直径设为30mm-35mm,螺杆长径比为25-30,在一实施例中,所述螺杆的直径设为33mm,螺杆长径比为28。
[0026]
供料组件50连接至所述料管10,用于向所述第一压缩段21输送聚合物原料。低压
供气组件40连接至所述料管10,用于向所述料管10内输出物理发泡剂。供料组件50和低压供气组件40间隔设置并连接于料管10,以分别向注塑组件输送聚合物原料及物理发泡剂。其中,在螺杆20的原料传输方向上,供料组件50连接于螺杆20的前端,以输出固态颗粒状的聚合物原料,低压供气组件40远离供料组件50。
[0027]
螺杆20转动以驱动原料移动,螺杆20在轴线方向上划分不同区域,以执行不同的功能。所述螺杆20包括沿自身中轴线方向依次设置的第一压缩段21、自洁段22及混合段23,所述自洁段22的螺纹槽深度与所述第一压缩段21所对应的螺纹槽深度的比例大于等于1.5且小于等于2.5,例如,自洁段22的螺纹槽深度与所述第一压缩段21所对应的螺纹槽深度的比例为1.5、1.8、2、2.5等数值。可选地,自洁段22的螺纹槽深度为第一压缩段21的螺纹槽深度的两倍左右可实现熔体快速输送、稳定的气体输送。其中,所述自洁段的轴向长度占据螺杆的总长度的比例为15%~30%。自洁段22为数个连续螺纹,螺纹升角大,气体注射时熔体压力低,以减小聚合物熔体在所述自洁段22的熔体压力。
[0028]
第一压缩段21、自洁段22和混合段23为螺杆20在轴线方向连续分布的三个区域,自洁段22位于第一单向阀30和混合段23之间,自洁段22位于所述第一压缩段21的螺纹延伸方向,混合段23位于所述自洁段22的螺纹延伸方向。供料组件50向料管10输出原料,原料沿所述螺杆20的螺纹传输并输送,且所述原料在此过程中逐渐熔融形成聚合物熔体进入到第一压缩段21。聚合物熔体流出第一单向阀30后进入自洁段22其中,自洁段22的螺纹槽深度大于所述第一压缩段21所对应的螺纹槽深度,以减小聚合物熔体在所述自洁段22的熔体压力。
[0029]
所述自洁段22位于所述低压供气组件40的物理发泡剂输出的延伸方向,低压供气组件40输出的物理发泡剂注入自洁段22并与聚合物熔体混合,自洁段22的熔体压力降低,从而低压的物理发泡剂可以持续稳定的注入,实现熔体快速输送、稳定的物理发泡剂输送。所述第一单向阀30位于所述第一压缩段21和所述自洁段22的连接处,用于单向引导所述第一压缩段21内处于熔融状态的聚合物进入所述自洁段22,并阻止自洁段22的物理发泡剂和聚合物熔体反向流通。可选地,所述第一单向阀30为滑动环式单向阀、球单向阀式单向阀、反向螺纹形式单向阀或弹簧转动式单向阀中的一种。
[0030]
所述物理发泡剂和所述聚合物自所述自洁段22进入所述混合段23并混合,所述聚合物熔体和所述物理发泡剂沿所述自洁段22进入混合段23混合以形成混合物流体。其中,当聚合物熔体经过自洁段22后,在混合段23实现物理发泡剂和聚合物熔体的快速混合,包括聚合物熔体和物理发泡剂的分散混合与分布混合。可选地,所述物理发泡剂为二氧化碳、氮气、氦气、氩气、合成空气中的一种或多种。
[0031]
所述注塑组件在完成混合物流体后,将混合物流体通过喷嘴装置70输出至模具装置80,以制得发泡制品。
[0032]
第一压缩段21的螺纹槽深度小于自洁段22的螺纹槽深度,聚合物熔体自第一压缩段21进入自洁段22的熔体压力减小,可以降低低压供气组件40输出的物理发泡剂与聚合物熔体混合时的压力要求,实现低压气体混合,降低设备要求。可选地,所述低压供气组件40输出的物理发泡剂的气体压力范围大于1mpa且小于10mpa,微孔发泡注塑成型塑化装置无需配置超临界流体增压装置来增压气体,即可达到良好的发泡效果和稳定的发泡制品质量。可选地,自洁段22的螺纹槽深度为第一压缩段21的螺纹槽深度的1.5倍至2.5倍,以实现
熔体快速输送、稳定的气体输送。可选地,自洁段22设置有两圈及以上的连续螺纹。
[0033]
如图1和图2所示,在混合段23实现物理发泡剂和聚合物熔体的快速混合,其中,混合段23采用螺纹槽将多螺棱截面分开,多槽的混合段23可分割出大量的熔体条纹,实现聚合物熔体和物理发泡剂的分散混合与分布混合。混合段23的螺纹槽深度大于第一压缩段21螺纹槽深度的,并实现一定的泵送能力,提高混合物流体的输送效率及流体压力。可选地,所述螺杆20包括第二压缩段24,所述混合段23位于所述第二压缩段24和所述自洁段22之间。第二压缩段24位于所述混合段23的螺纹延伸方向,所述第二压缩段24的螺纹槽深度自所述混合段23向远离所述第一单向阀30方向逐渐减小。
[0034]
第二压缩段24位于混合段23的延伸方向,其中,第二压缩段24的螺纹槽深度自混合段23向另一自由端方向逐渐减小。即,连续的螺纹槽的底壁构成近似于锥形空间,以引导混合物流体逐渐压缩。第二压缩段24对聚合物熔体/物理发泡剂混合形成的混合物流体进行进一步的压实,促进聚合物熔体/物理发泡剂二者的均匀混合,第二压缩段24的螺纹槽的容积逐渐减小,可形成连续的压实效果和输出效果。
[0035]
其中,所述螺杆20包括计量段25,所述第二压缩段24位于所述计量段25和所述混合段23之间。计量段25位于所述第二压缩段24的螺纹延伸方向,所述计量段25的螺纹槽深度等于所述第二压缩段24的最小螺纹槽深度。计量段25用于定量及定压的计量混合物流体,以使微孔发泡注塑成型塑化装置输出的混合物流体的克数和压力可控。可选地,计量段25使用等距等深的浅槽螺纹,以使输送的混合物流体均匀,计量方便且精度高。
[0036]
其中,所述混合段23、第二压缩段24和所述计量段25的轴向长度总合占据螺杆20的总长度的比例为30%~40%,以使螺杆20输出的混合物流体实现气泡细腻均衡,定量稳定输出的效果。
[0037]
计量段25输出的混合物流体可控,以方便微孔发泡注塑成型塑化装置精确加工发泡制品。可选地,所述注塑组件还包括安装于所述螺杆20一端的第二单向阀60,所述料管10包括储料区12和连通至所述储料区12的喷嘴通道,所述第二单向阀60位于所述储料区12并与所述喷嘴通道相对设置,所述第二单向阀60用于将所述计量段25单向连通至所述储料区12。
[0038]
第二单向阀60为球式单向阀或滑动环式单向阀,第二单向阀60通过所受压力控制计量段25的混合物流体流入到储料区12。例如,第二单向阀60为球式单向阀,当储料区12内存储有计量段25连续输入的混合物流体,则储料区12压力增大,第二单向阀60的止逆球封闭,以阻断计量段25和储料区12。反之,当计量段25的压力大于储料区12的压力,则止逆球打开,以使计量段25的混合物流体进入到储料区12。同理,第二单向阀60为滑动环式单向阀时,通过滑动环与固定环脱离或抵接密封,以控制计量段25与储料区12的开和闭。
[0039]
混合物流体通过第二单向阀60存储于储料区12内,并与喷嘴通道连通。喷嘴装置70位于储料区12的延伸方向,并在储料阶段处于封闭状态。如喷嘴装置70采用自锁式喷嘴,自锁式喷嘴在储料阶段处于关闭状态,从而注塑组件的混合物流体能够保持在较高的压力下而不发生流涎。喷嘴装置70的关闭状态可通过机械式或电磁来控制,可通过气动、液压或机械结构的驱动单元来实现机械控制。喷嘴装置70将定量定压的混合物流体输出至模具装置80,以加工发泡制品。
[0040]
如图1和图2所示,供料组件50连接至所述料管10,用于向所述第一压缩段21输送
原料。其中,供料组件50包括连接于料管10的料斗,原料为固体颗粒。其中,螺杆20加热以将固体颗粒熔化形成完全塑化的黏流状态。可选地,所述螺杆20包括进料区26,所述第一压缩段21位于所述进料区26和所述第一单向阀30之间。进料区26位于所述第一压缩段21的螺纹延伸方向,所述进料区26远离所述第一单向阀30。所述进料区26的螺纹槽深度大于所述第一压缩段21所对应的螺纹槽深度且所述进料区26的一端螺纹槽深度逐渐减小并相交至所述第一压缩段21,所述供料组件50连通至所述进料区26。其中,所述进料区26和所述第一压缩段21的轴向长度总合占据螺杆20的总长度的比例为30%~45%。
[0041]
进料区26和第一压缩段21加热,以熔化原料。其中,进料区26采用等距等深的螺纹结构输送原料并加热。进料区26的一端螺纹槽深度逐渐减小并至第一压缩段21,以形成锥形槽结构。原料在该槽段受到挤压和剪切作用,同时对原料继续加热,以使原料在第一压缩段21熔融成为为完全塑化的黏流状,继而通过第一单向阀30进入自洁段22。可选地,自洁段22的螺纹槽深度小于或等于进料区26的螺纹槽深度,以提高自洁段22混合的均衡性。
[0042]
低压供气组件40输出物理发泡剂,并与熔融状态的聚合物混合,以形成混合物流体。可选地,所述低压供气组件40包括储气罐43、连接至所述储气罐43的调节件42和安装于所述料管10的进气阀41,所述调节件42连接于所述进气阀41,用于输出流量及压力可调节的物理发泡剂。可选地,所述进气阀41输出的物理发泡剂的气体压力范围大于1mpa且小于10mpa。
[0043]
储气罐43存储有相应压力的气体作为物理发泡剂,储气罐43存储的物理发泡剂的压力值大于1mpa且小于10mpa。如,储气罐43存储压力值为10mpa的气体,调节件42设为压力控制器,用于调节输出进气阀41输出的气体压力为5mpa。进气阀41与料管10连接,并将气体恒压恒流连续输送至料管10,以使气体与自洁段22的聚合物熔体混合。可选地,注塑组件还包括安装于料管10的压力传感器90,所述压力传感器90用于检测自洁段22的混合物流体压力。
[0044]
上述实施例所公开的微孔发泡注塑成型塑化装置可用于执行微孔发泡注塑成型工艺,微孔发泡注塑成型工艺包括以下步骤:
[0045]
步骤s101,供料组件50向料管10输出原料,原料沿所述螺杆20的螺纹传输并输送,且所述原料在此过程中逐渐熔融形成聚合物熔体进入到第一压缩段21。在本步骤中,聚合物原料从料斗进入料管10中,螺杆20旋转以将聚合物原料沿轴线方向螺旋前进输送。螺杆20的进料区26加热,聚合物受热初步熔融并沿螺杆20输送至第一压缩段21。聚合物原料在第一压缩段21受到挤压和剪切作用,并且第一压缩段21继续加热以使聚合物原料熔融成为完全塑化的黏流状。
[0046]
步骤s102,聚合物熔体流出第一单向阀30后进入自洁段22;低压供气组件40输出的物理发泡剂注入自洁段22并与聚合物熔体混合。其中,自洁段22的螺纹槽深度大于所述第一压缩段21所对应的螺纹槽深度,以减小聚合物熔体在所述自洁段22的熔体压力,所述聚合物熔体和所述物理发泡剂沿所述自洁段22进入混合段23混合以形成混合物流体。聚合物原料完全熔融后沿第一单向阀30导出至自洁段22,自洁段22的螺纹槽深度大于第一压缩段21的螺纹槽深度。聚合物熔体自第一压缩段21进入自洁段22后的熔体压力减小,低压供气组件40输出的物理发泡剂连续注入自洁段22并与聚合物熔体混合。由于,自洁段22的熔体压力降低,从而低压的物理发泡剂可以持续稳定的注入,实现熔体快速输送、稳定的物理
发泡剂输送。如,低压气体(如5mpa)从储气罐43中进入调节件42,再以恒定压力和流量通过进气阀41进入到料管10。可选地,自洁段22配置有一个压力传感器90,可实时监测熔体压力。
[0047]
步骤s103,所述注塑组件通过喷嘴装置70输出混合物流体。当聚合物熔体经过自洁段22后进入到混合段23,以实现物理发泡剂和聚合物熔体的快速混合。物理发泡剂和聚合物熔体混合后通过喷嘴装置70喷射至模具装置80,以制成发泡制品。
[0048]
进一步地,螺杆20配置有第二压缩段24,所述第二压缩段24的螺纹槽深度自所述混合段23向远离所述第一单向阀30方向逐渐减小。第二压缩段24对聚合物熔体/物理发泡剂混合形成的混合物流体进行进一步的压实,促进聚合物熔体/物理发泡剂二者的均匀混合,第二压缩段24的螺纹槽的容积逐渐减小,可形成连续的压实效果和输出效果。
[0049]
进一步地,所述螺杆20包括位于所述第二压缩段24的螺纹延伸方向的计量段25,所述计量段25的螺纹槽深度等于所述第二压缩段24的最小螺纹槽深度。第二压缩段24输出的混合物流体进入到计量段25,计量段25输出的混合物流体压力及数量可控,以方便微孔发泡注塑成型塑化装置精确加工发泡制品
[0050]
第二单向阀60为球式单向阀或滑动环式单向阀,第二单向阀60通过所受压力控制计量段25的混合物流体流入到储料区12。混合物流体通过第二单向阀60存储于储料区12内,并与喷嘴通道连通。喷嘴装置70位于储料区12的延伸方向,并在储料阶段处于封闭状态。
[0051]
喷嘴装置70的关闭状态可通过机械式或电磁来控制,可通过气动、液压或机械结构的驱动单元来实现机械控制。喷嘴装置70将定量定压的混合物流体输出至模具装置80,以加工发泡制品。
[0052]
步骤s104,当塑化完成后,混合物流体填充模具装置80的型腔、保压、发泡,冷却,打开模具,取出制品。
[0053]
微孔发泡注塑成型塑化装置的其它结构和原理与现有技术相同,这里不再赘述。
[0054]
以上所述实施例的各技术特征可以进行任意的组合,为使描述简洁,未对上述实施例中的各个技术特征所有可能的组合都进行描述,然而,只要这些技术特征的组合不存在矛盾,都应当认为是本说明书记载的范围。
[0055]
以上所述实施例仅表达了本实用新型的几种实施方式,其描述较为具体和详细,但并不能因此而理解为对实用新型专利范围的限制。应当指出的是,对于本领域的普通技术人员来说,在不脱离本实用新型构思的前提下,还可以做出若干变形和改进,这些都属于本实用新型的保护范围。因此,本实用新型专利的保护范围应以所附权利要求为准。