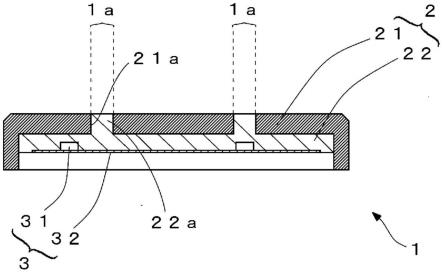
1.本发明涉及对在汽车、家电产品、音频设备等中使用的来自led(发光二极管:light emitting diode)等光源的光进行引导而进行显示的照明显示面板及其制造方法。
背景技术:2.以往,作为将led等光源配置在背面而在汽车、家电产品、音频设备等中使用的照明显示面板,如专利文献1所示,在树脂面板的表面设置有基于印刷等的装饰层,树脂面板以及装饰层具有透过部分,通过在这些背面侧配置光源,从而从照明显示面板的前表面侧识别光源的闪烁。
3.另外,若光源与树脂面板及装饰层的透过部分对置地配置,则必须通过透过部分从照明显示面板的前表面侧看到光源的形状,或必须配置与透过部分的数量相应的光源,因此,在透过部分以外的部分的背面侧配置光源,使来自光源的光全反射到透过部分并进行引导的情况也在专利文献1中公开。
4.现有技术文献
5.专利文献
6.专利文献1:日本特开平10-116044号公报
技术实现要素:7.发明所要解决的课题
8.但是,以往的照明显示面板在树脂面板的背面侧的空间配置有光源,在树脂面板与光源之间存在空气层。因此,从光源照射的光的一部分在树脂面板的空气层界面被反射,无法高效地使其从照明显示面板射出。
9.另外,由于在树脂面板的背面侧的空间配置有光源,因此还存在照明显示面板整体变厚,无法广泛地利用树脂面板的背面侧的空间的问题。
10.并且,在照明显示面板向设备等组装时,必须在不同的工序中进行光源和树脂面板的安装,花费时间和劳力。
11.因此,本发明的目的在于提供一种导光效率良好、实现省空间化、组装工序变得简单的照明显示面板及其制造方法。
12.用于解决课题的方案
13.以下,作为用于解决课题的方案,对多个方式进行说明。这些方式可以根据需要任意组合。
14.本发明的照明显示面板具有能够进行照明显示的显示部位并构成箱体的一部分。
15.照明显示面板具备:具有第一成形部和第二成形部的树脂面板和光源安装基板。
16.树脂面板的第一成形部除了显示部位以外而存在。树脂面板的第二成形部配置于第一成形部的背面侧,且在不存在第一成形部的部分具有与第一成形部嵌合的凸部。另外,第二成形部由将引导至显示部位的光透过的透光树脂构成,第一成形部由与第二成形部相
比光的透过率低的不透明树脂构成。
17.光源安装基板配置于树脂面板的背面侧,且具有引导至显示部位的光的光源和安装有光源的薄膜基板。另外,光源安装基板的至少光源由第二成形部封固。
18.根据这些结构,从光源照射的光不经由空气层,而是在作为导光板(光导)发挥功能的第二成形部内透过,且透过显示部位而向树脂面板2的上方放出。也就是,由于没有空气层界面的反射,因此能够使从光源照射的光高效地从照明显示面板射出。
19.另外,由于光源安装基板的光源内置于树脂面板内,因此能够实现由照明显示面板1整体占据的空间的省空间化。
20.而且,由于树脂面板与光源安装基板一体化,因此部件数量减少,照明显示面板向设备等的组装工序变得简单。
21.进一步而言,由树脂面板的透光树脂构成的第二成形部配置在由不透明树脂构成的第一成形部的背面侧,在不存在第一成形部的部分具有与第一成形部嵌合的凸部。因此,即使不在树脂面板的前表面设置装饰层,也能够通过由不透明树脂构成的成形成形体即第一成形部进行照明显示。因此,不会像装饰层那样随时间经过或因磨损等而剥离等而引起漏光。
22.另外,由于照明显示面板构成箱体的一部分,因此也存在树脂面板的形状变得复杂的情况,即使在这样的树脂面板的前表面不设置装饰层,也能够进行照明显示,这在工序方面也非常优异。
23.另外,由于光源安装基板配置于树脂面板的背面侧,光源安装基板的至少光源由作为导光板发挥功能的第二成形部封固,因此光源安装基板不位于第二成形部的前表面侧,而是位于背面侧。换言之,是从前表面起第一成形部、第二成形部、光源安装基板的层叠顺序。因此,即使在构成第一成形部的不透明树脂是与透光树脂相比从光源照射的光的透射率低、且不具有完全遮断光的功能的树脂的情况下,即在第一成形部中也较弱地放出光的情况下,光源安装基板的基板也不会妨碍第一成形部中的弱的放出光。也就是,与光源安装基板位于第二成形部的前表面侧的情况相比,照明显示面板的装饰的自由度高。
24.以下,对本发明的照明显示面板的优选方案进行说明。
25.作为一个方案,在第二成形部中,由第一成形部覆盖且向显示部位引导光的导光路径部分的厚度为0.2mm~1.0mm。
26.根据该结构,由于导光路径部分的壁厚较薄,因此能够实现照明显示面板的薄型化。因此,在将照明显示面板组装到设备等时,能够在照明显示面板的背后较大地取得其他部件的收纳空间。
27.作为一个方案,优选不存在第一成形部的部分为贯通孔,第二成形部的凸部嵌合于贯通孔的内壁面。
28.根据该结构,能够以在暗的背景中发光的方式显示文字、标志、图像等。
29.另外,作为一个方案,优选第二成形部的凸部嵌合于第一成形部的侧面。
30.根据该结构,能够以在发光的背景中遮光的方式显示文字、标志、图像等。
31.另外,作为一个方案,优选第二成形部的凸部在前表面具有细微凹凸。
32.根据该结构,能够对显示部位赋予消光等装饰功能、扩散效果或透镜效果等光学功能等。
33.另外,作为一个方案,优选还具备对树脂面板的前表面进行装饰的装饰层。
34.根据该结构,对于能够进行照明显示的显示部位以外的部分,与由第一成形部呈现的单色的不透明色的装饰相比,设计的自由度高,也能够应对复杂的形状、多色化、各种图案。
35.本发明的照明显示面板的制造方法具备以下的工序。
36.首先,在低压成形模具的上模,以上述光源的安装面朝向下方的方式设置上述光源安装基板。
37.接着,向低压成形模具的下模所具有的模腔注入计量出的透光树脂材料。
38.接着,在低压成形模具合模后,一边压缩模腔一边以低压填充透光树脂材料并使其固化,从而在第二成形部成形的同时,以利用第二成形部至少封固光源的方式将第二成形部与光源安装基板一体化。
39.接着,在嵌件成形模具内,以第二成形部侧朝向模腔的方式设置光源安装基板和第二成形部的一体成形品。
40.最后,在嵌件成形模具合模后,向嵌件成形模具的模腔注射填充由熔融状态的热塑性树脂构成的不透明树脂材料并使其固化,从而在第一成形部成形的同时,将第一成形部与光源安装基板和第二成形部的一体成形品一体化。
41.在作为树脂成形法而采用通常已知的注射成形法的情况下,为了利用螺杆以高速、高压将熔融树脂注射到模腔内,若在成形第二成形部的同时与光源安装基板一体化,则产生光源安装基板的光源因树脂压力而破损或移动等问题。
42.与此相对,根据上述结构,在使第二成形部成形的同时与光源安装基板一体化时,一边压缩模腔一边填充透光树脂材料,因此即使模腔内的树脂压力不高,也能够使透光树脂材料充分地流动,透光树脂材料到达模腔内的各个角落。因此,能够在第二成形部成形时不产生光源的破损、移动地封固光源。
43.另外,通过由压缩引起的透光树脂材料的流动,即使第二成形部为薄壁,透光树脂材料也到达模腔内的各个角落。因此,能够防止在第二成形部的一部分产生具有不完全的填充部分的缺陷。在第二成形部中,位于第一成形部的背后而向显示部位引导光的导光路径部分的壁厚变得极薄,因此特别有效。
44.进一步而言,安装于光源安装基板的光源、其他电子部件的厚度的选择自由度也高。也就是,不需要选择第二成形部的成形时不易受到树脂压力的影响的薄型的电子部件。另外,由于不易受到第二成形部成形时的树脂压力的影响,因此也不需要另外利用灌封等手段来保护或加强(固定)电子部件。
45.另外,本发明的照明显示面板的制造方法也可以在将第二成形部与光源安装基板一体化之后,不使用光源安装基板和第二成形部的一体成形品进行嵌件成形。
46.例如,也可以在光源安装基板和第二成形部的一体成形品上层压另外成形的第一成形部。
47.另外,本发明的照明显示面板的制造方法优选使第二成形部与光源安装基板及第一成形部同时一体化。
48.即,在注入透光树脂材料之前,在低压成形模具的下模所具有的模腔中设置另外成形的第一成形部。
49.此外,在上述的各制造方法中,优选低压成形模具为压缩成形模具,向加热后的下模所具有的模腔注入由未固化的热固性树脂构成的透光树脂材料后,将低压成形模具合模。
50.另外,在上述的各制造方法中,优选低压成形模具是注射冲压成形模具,在将低压成形模具合模后,向下模所具有的模腔注射注入由熔融状态的热塑性树脂构成的透光树脂材料。
51.另外,作为一个方案,优选低压成形模具的下模在与第二成形部的凸部的前表面对应的部分具有细微凹凸。
52.根据该结构,由于一边压缩模腔一边填充透光树脂材料并使其固化,因此,通过由压缩引起的透光树脂材料的流动,透光树脂材料可靠地到达设置于下模的细微凹凸的最深部。因此,形成于树脂面板的细微凹凸能够以准确的尺寸形成至细部。
53.另外,作为一个方案,优选还具备在嵌件成形模具内设置用于对树脂面板的前表面进行装饰的装饰片的工序。
54.根据该结构,在对具有第一成形部和第二成形部的树脂面板进行双色成形的同时,能够在树脂面板的前表面形成装饰层,生产效率良好。
55.此外,作为一个方案,优选层压工序中使用的第一成形部与用于对树脂面板的前表面进行装饰的装饰片预先一体化。
56.另外,作为一个方案,优选在低压成形工序中使用第一成形部的情况下,该第一成形部与用于对树脂面板的前表面进行装饰的装饰片预先一体化。
57.根据该结构,由于第一成形部与装饰片预先一体化,因此在第一成形部与装饰片的显示部位的对位等产生不良的情况下,能够在第二成形部及光源安装基板的一体化前排除,因此作为照明显示面板的成品率高。
附图说明
58.图1是表示第一实施方式的照明显示面板的一例的俯视图。
59.图2是表示图1的照明显示面板的aa线剖面的剖视图。
60.图3是表示第一实施方式的照明显示面板的制造工序的一例的剖视图。
61.图4是表示第一实施方式的照明显示面板的制造工序的一例的剖视图。
62.图5是表示第一实施方式的照明显示面板的制造工序的一例的剖视图。
63.图6是表示第一实施方式的照明显示面板的制造工序的一例的剖视图。
64.图7是表示第一实施方式的照明显示面板的制造工序的一例的剖视图。
65.图8是表示第一实施方式的照明显示面板的制造工序的一例的剖视图。
66.图9是表示第一实施方式的照明显示面板的制造工序的另一例的剖视图。
67.图10是表示第一实施方式的照明显示面板的制造工序的另一例的剖视图。
68.图11是表示第一实施方式的照明显示面板的制造工序的另一例的剖视图。
69.图12是表示第一实施方式的照明显示面板的制造工序的另一例的剖视图。
70.图13是表示第一实施方式的照明显示面板的制造工序的另一例的剖视图。
71.图14是表示第二实施方式的照明显示面板的一例的俯视图。
72.图15是表示图14的照明显示面板的bb线剖面的剖视图。
73.图16是表示第二实施方式的照明显示面板的制造工序的一例的剖视图。
74.图17是表示第二实施方式的照明显示面板的制造工序的一例的剖视图。
75.图18是表示第二实施方式的照明显示面板的制造工序的一例的剖视图。
76.图19是表示第二实施方式的照明显示面板的制造工序的另一例的剖视图。
77.图20是表示第二实施方式的照明显示面板的制造工序的另一例的剖视图。
78.图21是表示第二实施方式的照明显示面板的制造工序的另一例的剖视图。
79.图22是表示第二实施方式的照明显示面板的制造工序的另一例的剖视图。
80.图23是表示第二实施方式的照明显示面板的制造工序的另一例的剖视图。
81.图24是表示第二实施方式的照明显示面板的制造工序的另一例的剖视图。
82.图25是表示使用了其他显示图案的树脂面板的照明显示面板的例子的俯视图。
83.图26是表示图25的照明显示面板的cc线剖面的剖视图。
84.图27是表示使用了其他显示图案的树脂面板的照明显示面板的例子的俯视图。
85.图28是表示在显示部位具有细微凹凸的照明显示面板的例子的俯视图。
86.图29是表示图28的细微凹凸的形成方法的例子的剖视图。
87.图30是表示使用了注射冲压成形模具的低压成形的例子的剖视图。
88.图31是表示使用了注射冲压成形模具的低压成形的例子的剖视图。
89.图32是表示使用了注射冲压成形模具的低压成形的例子的剖视图。
具体实施方式
90.第一实施方式
91.1.照明显示面板的构造
92.以下,使用附图对本公开的第一实施方式的照明显示面板1进行说明。图1是表示本发明的照明显示面板的一例的俯视图。图2是表示图1的照明显示面板的aa线剖面的剖视图。
93.照明显示面板1具有能够对文字、标志、图像等进行照明显示的显示部位1a而构成箱体的一部分,具备树脂面板2和光源安装基板3。另外,树脂面板2呈在矩形状的平面部分的周围具有立起部分的薄的箱型形状。
94.树脂面板2具有:第一成形部21,其除了显示部位1a之外存在;以及第二成形部22,其配置于第一成形部21的背面侧,在不存在第一成形部21的部分具有与第一成形部21嵌合的凸部22a。
95.如图1和图2所示,在本实施方式中,不存在第一成形部21的部分是贯通孔,第二成形部22的凸部22a嵌合于该贯通孔的内壁面21a。另外,第二成形部22的凸部22a的前表面为平滑面,第二成形部22的凸部22a与第一成形部21的前表面为同一平面。
96.另外,第二成形部22由透光树脂构成,第一成形部21由不透明树脂构成。在此,透光树脂是包含透明树脂和半透明树脂的概念。另外,在此,不透明树脂是指包含由于自身具有颜色而不透明的树脂和被颜料等着色而不透明的树脂的概念。并且,在此,不透明树脂是与透光树脂相比,从光源31照射的光的透射率低的树脂,是包含不具有完全遮断光的功能的树脂。第二成形部22及第一成形部21除了具有形成作为树脂面板2的箱体的形状的功能以外,还具有与从光源31照射的光有关的功能。
97.第二成形部22配置为能够使从光源31照射的光透过并向树脂面板2的显示部位1a引导。另外,光源31的配置不需要配置在显示部位1a的正下方,也可以如图2所示的两个光源31中的左侧的光源31那样也配置在第一成形部21的背面。在该情况下,从光源31照射的光在第二成形部22中的与第一成形部21的背面接触的导光路径部分中一边反复进行全反射一边被引导至显示部位1a的正下方,因此光源31不会通过显示部位1a从外部被观察到。
98.在第二成形部22中,优选的是,由第一成形部21覆盖并向显示部位1a引导光的导光路径部分的厚度为0.2mm~5.0mm。若导光路径部分的厚度为5.0mm以下,则导光路径部分的壁厚较薄,能够实现照明显示面板1的薄型化。但是,如果导光路径部分的厚度不是0.2mm以上,则导光功能显著降低。更优选导光路径部分的厚度为0.2mm~1.0mm。
99.另一方面,第一成形部21为了形成基于光源31的光的特定的显示图案,以抑制不需要的出光的方式配置。因此,构成第一成形部21的不透明树脂优选具有遮光性,例如着色为黑色。但是,例如在为了提高装饰效果而想要以比第二成形部22低的光度漏出光的情况下等,也可以不由第一成形部21完全遮光而将第一成形部21的一部分着色为半透明。即,第一成形部21的光的透射率比第二成形部22的光的透射率低即可。在图1所示的例子中,在暗的背景中并列显示两个发亮的箭头符号。
100.此外,第一成形部21作为由树脂构成的成形体来构成树脂面板2的一部分,因此不会如薄膜、印刷薄膜那样随时间经过或磨损等而剥离。
101.光源安装基板3在薄膜基板32上安装有光源31。构成薄膜基板32的树脂例如是聚对苯二甲酸乙二醇酯(pet)树脂、环烯烃聚合物(cop)树脂、聚碳酸酯(pc)树脂、聚酰亚胺(pi)树脂等。
102.此外,在该薄膜基板32的安装有光源31的面上形成有与光源31连接的未图示的布线。并且,也可以在该薄膜基板32上安装驱动光源31的驱动电路作为集成电路。
103.另外,作为光源31,除了led以外,还能够使用oled(有机发光二极管:organic light emitting diode)。另外,在使用印刷方式的oled的情况下,在本说明书中,直接在薄膜基板32上形成各印刷层也包含在“安装”中。
104.如图2所示,光源安装基板3的光源31被第二成形部22封固。因此,从光源31照射的光不经由空气层而透过第二成形部22,透过显示部位1a而朝向树脂面板2的上方放出。
105.如后所述,第二成形部22在向低压成形模具的下模所具有的模腔注入计量后的透光树脂材料后,一边压缩模腔一边以低压填充透光树脂材料并使其固化而成形。也就是,使用低压成形法。这是因为,在通常已知的注射成形法中,若在注射成形模具内设置光源安装基板3,则有可能因高压的树脂压力而产生光源31的破损或移动。
106.在本实施方式中,作为低压成形法使用压缩成形法。压缩成形是在加热后的模具的凹部(模腔)中注入由未固化的热固性树脂构成的成形材料后进行合模,一边压缩一边以低压进行填充并固化(硬化)的成形法。
107.因此,在使用压缩成形法的情况下,构成第二成形部22的透光树脂例如为有机硅树脂、聚氨酯树脂、环氧树脂等热固化性树脂、它们的组合。
108.另一方面,第一成形部21如后文所述那样通过通常已知的注射成形法成形。因此,构成第一成形部21的树脂例如是聚碳酸酯(pc)树脂、abs树脂、聚甲基丙烯酸甲酯(pmma)树脂等热塑性树脂、它们的组合。
109.2.照明显示面板的制造方法(制法1)
110.以下,使用图3~图8,对第一实施方式的照明显示面板1的制造方法进行说明。
111.在图3中,压缩成形模具7的上模71和下模72以合模前的状态表示。首先,以光源31的安装面朝向下方的方式将光源安装基板3设置于压缩成形模具7的上模71(参照图3)。
112.此外,光源安装基板3例如使用吸引用孔由空气吸引而吸附于上模71。
113.接着,向压缩成形模具7的下模72所具有的模腔72a注入计量出的未固化的热固性树脂作为透光树脂材料10(参照图4)。
114.在图4中示出了由形成模腔72a的底面的模腔块722和形成模腔72a的侧面的框架块721构成的下模72。
115.在框架块721的下部设置有弹簧723。在上模71与下模72合模前,框架块721通过弹簧723而处于上升位置。因此,即使将透光树脂材料10注入下模72,也不会从模腔72a向模具外溢出。
116.此外,在图3~图5所示的压缩成形法中,固定模腔块722使框架块721升降,但也可以固定框架块721而使模腔块722升降,也可以使框架块72和模腔块722双方升降距离不同地进行升降。
117.另外,在模腔块722中内置有加热器724,下模72被加热。
118.接着,以使模腔72a成为密闭状态的方式对压缩成形模具7进行合模。接着,在将压缩成形模具7合模后,一边利用上模71压缩模腔72a,一边将透光树脂材料10以低压填充并固化(硬化)(参照图5)。
119.即,上模71的下表面周围将下模72的框架块721按下,由此对下模72的模腔72a以及注入其中的透光树脂材料10进行压缩。由此,设置于上模71的光源安装基板3的光源31成为浸在未固化的透光树脂材料10中的状态。
120.在该状态下,在下模72的模腔72a中,透光树脂材料10通过加热而固化,从而成形出第二成形部22。
121.此外,在图5所示的压缩成形法中,示出了使上模71相对于下模72下降而对下模72的模腔72a以及注入其中的透光树脂材料10进行压缩的情况,但也可以使下模72相对于上模71上升。
122.如图6所示,所成形的第二成形部22以利用第二成形部22封固光源31的方式与光源安装基板3一体化。
123.根据上述的压缩成形,在成形第二成形部22的同时与光源安装基板3一体化时,一边压缩模腔72a一边填充透光树脂材料10,因此即使模腔72a内的树脂压力不高,也能够使透光树脂材料10充分地流动,透光树脂材料10到达模腔72a内的各个角落。因此,在第二成形部22成形时能够不会产生光源31的破损、移动地封固光源31。在图6所示的例子中,不仅光源31,除了光源安装基板3的背面以外的整体都由透光树脂材料10封固。
124.另外,通过由压缩引起的透光树脂材料10的流动,从而即使第二成形部22为薄壁,透光树脂材料10也到达模腔72a内的各个角落。因此,能够防止在第二成形部22的一部分产生具有不完全的填充部分的缺陷。在第二成形部22中,位于第一成形部21的背后而向显示部位1a引导光的导光路径部分的壁厚变得极薄,因此特别有效。
125.进一步而言,对于安装于光源安装基板3的光源31、其他电子部件的厚度,选择自
由度高。也就是,不需要选择不易受到第二成形部22成形时的树脂压力的影响的薄型的电子部件。另外,由于不易受到第二成形部22成形时的树脂压力的影响,因此也不需要另外利用灌封等手段来保护或加强(固定)电子部件。
126.接着,在由凸模81和凹模82构成的嵌件成形模具8内,以第二成形部22侧朝向模腔83的方式设置光源安装基板3和第二成形部22的一体成形品13(参照图7)。
127.在图7所示的嵌件成形模具8的例子中,凸模81和凹模82上下开闭,一体成形品13收纳在位于下侧的凹模82内。一体成形品13的第二成形部22侧通过凸部22a的前表面与凹模82接触。另一方面,一体成形品13的光源安装基板3侧在合模时整体与凸模81相接。另外,在本实施方式中,未图示的注射成形机为立式,与图7所示的凸模81的射出口84连接。
128.最后,在嵌件成形模具8合模后,从注射口84向嵌件成形模具8的模腔83注射填充由熔融状态的热塑性树脂构成的不透明树脂材料11并使其固化(参照图8)。由此,能够在第一成形部21成形的同时,使第一成形部21与光源安装基板3和第二成形部22的一体成形品13一体化。
129.从嵌件成形模具8内取出的照明显示面板如图1和图2所示。
130.3.照明显示面板的另一制造方法(制法2)
131.在上述制法1中,说明了在将第二成形部22与光源安装基板3一体化后,使用光源安装基板3和第二成形部22的一体成形品13进一步进行嵌件成形从而与第一成形部21一体化的情况,但在本实施方式的照明显示面板1中,并不限定于该制法。
132.即,在图9所示的本制法2中,在将第二成形部22与光源安装基板3一体化后,在光源安装基板3和第二成形部22的一体成形品13上层压另外成形的第一成形部21。
133.本制法2与制法1不同的主要方面仅是层压工序,因此省略其他工序的说明。
134.本制法2中的层压中使用的另外成形的第一成形部21可以通过通常已知的注射成形法进行成形。即,如图10所示,在由凸模810和凹模820构成的注射成形模具80的模腔830中,从注射口840注射填充由熔融状态的热塑性树脂构成的不透明树脂材料11并使其固化。
135.使用的不透明树脂材料11与制法1的嵌件成形时使用的材料相同。
136.返回图9,在光源安装基板3和第二成形部22的一体成形品13上层压另外成形的第一成形部21时,使用粘接剂15进行贴合。
137.作为粘接剂15,除了oca(optical clear adverive:光学粘接片)以外,还可以使用公知的层压用粘接剂。
138.此外,在图9所示的例子中,将粘接剂15设置在第一成形部21侧,但粘接剂15也可以设置在一体成形品13的第一成形部21侧进行贴合。
139.4.照明显示面板的另一制造方法(制法3)
140.在上述制法1和上述制法2中,说明了在将第二成形部22与光源安装基板3一体化后,将光源安装基板3和第二成形部22的一体成形品13进一步与第一成形部21一体化的情况,但在本实施方式的照明显示面板1中,并不限定于上述制法1和上述制法2。
141.即,在图11~图13所示的本制法3中,在压缩成形中,将第二成形部22与光源安装基板3以及另外成形的第一成形部21同时一体化。
142.首先,在注入透光树脂材料10之前,在压缩成形模具70的下模720所具有的模腔720a中设置另外成形的第一成形部21(参照图11)。
143.本制法3中使用的另外成形的第一成形部21能够通过与上述制法2中的第一成形部21同样的材料以及成形方法(参照图10)来成形。
144.但是,由热塑性树脂构成的第一成形部21构成为,在第二成形部22成形时不会溶解到完全不能维持形状的程度。因此,在本制法3中使用的构成第一成形部21的树脂优选具有与第二成形部22成形时的加热温度同等或比其高的软化温度。
145.在图11中示出了由形成模腔720a的底面的模腔块7220和形成模腔720a的侧面的框架块7210构成的下模720。
146.在框架块7210的下部设置有弹簧7230。在上模710和下模720的合模前,框架块7210通过弹簧7230位于上升位置。因此,即使将透光树脂材料10注入到下模720中,也不会从模腔72a0溢出。
147.此外,如图11所示,本制法3的压缩成形模具70的下模720与上述制法1及制法2的低压成形模具7不同,在形成模腔720a的底面的模腔块7220上未设置与第二成形部22的凸部22a对应的凹部。第一成形部21的贯通孔211相当于该凹部。
148.另外,在模腔块7220中,与上述制法1及制法2同样地内置有加热器7240,下模720被加热。
149.接着,在下模720的设置有第一成形部21的模腔720a中,与上述制法1和制法2同样地,将计量出的未固化的热固性树脂作为透光树脂材料10注入(参照图12)。
150.接着,以使模腔720a成为密闭状态的方式将压缩成形模具70合模。接着,在将压缩成形模具70合模后,一边用上模710压缩模腔720a一边将透光树脂材料10以低压填充并固化(硬化)(参照图13)。
151.即,上模710的下表面周围按压下模720的框架块7210,由此对下模720的模腔72a以及注入其中的透光树脂材料10进行压缩。由此,设置于上模710的光源安装基板3的光源31成为浸在未固化的透光树脂材料10中的状态。
152.在该状态下,在下模720的模腔720a中,透光树脂材料10通过加热而固化,从而成形出第二成形部22。
153.此外,即使设置于下模720的模腔720a的第一成形部21在贯通孔211的内壁面21a与下模720之间具有未图示的下凹部,透光树脂材料10也会因基于压缩的透光树脂材料10的流动而到达下凹部。
154.这样成形的第二成形部22以利用第二成形部22封固光源31的方式将第二成形部22与光源安装基板3及第一成形部21一体化(参照图2)。
155.第二实施例
156.1.照明显示面板100的构造
157.在上述第一实施方式中,对树脂面板2的前表面露出的情况进行了说明,但在本发明的照明显示面板中,并不限定于此。
158.例如,图14是表示第二实施方式的照明显示面板的一例的俯视图。图15是表示图14的照明显示面板的bb线剖面的剖视图。
159.本第二实施方式的照明显示面板100还具备对树脂面板2的前表面进行装饰的装饰层4,这一点上与第一实施方式不同。在图14以及图15所示的照明显示面板100中,装饰层4覆盖树脂面板2的整个前表面,附加照明显示以外的装饰性。在图14所示的照明显示面板
100的例子中,在显示部位100a以外的部分形成木纹图案,进而在其上赋予标志“abcdefg”。
160.装饰层4例如是装饰片41。
161.装饰片41具备基膜和图案层。基膜使用透明的树脂。基膜的材料例如从由聚酯树脂、聚对苯二甲酸乙二醇酯(pet)树脂、丙烯酸树脂、聚碳酸酯树脂、聚对苯二甲酸丁二醇酯(pbt)树脂、三乙酰纤维素树脂、苯乙烯树脂或abs树脂构成的树脂膜、丙烯酸树脂与abs树脂的多层膜、或丙烯酸树脂与聚碳酸酯树脂的多层膜中选择。基膜的厚度例如优选从30μ0的多层膜、或的范围选择。
162.图案层是用于表现图案等外观设计的层。图案层例如通过凹版印刷法或丝网印刷法形成于基膜。构成图案层的材料例如包含丙烯酸系树脂、氯乙烯-乙酸乙烯酯共聚树脂、热塑性聚氨酯系树脂、聚酯系树脂等树脂和添加于树脂的颜料或染料。另外,图案层例如也可以是使用经绝缘处理的铝糊剂或镜面油墨而实施了金属质感外观设计的图案层。
163.装饰片41即使在向基膜的图案层形成中产生印刷、涂装的不良情况,也仅废弃装饰片41的不良部分即可。因此,相对于树脂面板2与光源安装基板3的一体成形品,与在成形后直接进行印刷、涂装的情况相比成品率高。
164.装饰片41也可以形成用于提高表面强度而赋予耐擦伤性的硬涂层。另外,也可以在装饰片41上形成用于提高与树脂面板2之间的粘接性的粘接层。
165.装饰片41的显示部位100a的图案层透明。因此,在装饰片41的显示部位100a,从光源31照射的光透过基膜及图案层而向外部放出。
166.如上所述,本第二实施方式的照明显示面板100通过具备装饰层4,与第一成形部21呈现的单色的不透明色的装饰相比,设计的自由度高,也能够应对复杂的形状、多色化、各种图案。
167.2.照明显示面板100的制造方法(制法4)
168.以下,使用图16~图18,对第二实施方式的照明显示面板100的制造方法进行说明。
169.本第二实施方式的照明显示面板100的制造方法与第一实施方式的照明显示面板1的制造方法仅装饰片41的包覆工序不同在本制法4的情况下,在第一实施方式的制法1中的嵌件成形工序中包覆装饰片41。
170.即,在由凸模81和凹模82构成的嵌件成形模具8内,以图案层(未图示)侧朝向模腔83的方式设置用于装饰树脂面板2的前表面的装饰片41(参照图16)。
171.装饰片41例如使用吸引用孔由空气吸引而吸附于凹模82的内表面。另外,在图16所示的例子中,装饰片41以沿着凹模82的模腔83的内表面的方式预成形。
172.接着,在由凸模81和凹模82构成的嵌件成形模具8内,以第二成形部22侧朝向模腔83的方式,设置与上述制法1的压缩成形(参照图3~6)同样地成形的光源安装基板3和第二成形部22的一体成形品13(参照图17)。
173.在图17所示的嵌件成形模具8的例子中,一体成形品13的第二成形部22侧通过凸部22a的前表面与以沿着凹模82的模腔83的内表面的方式配置的装饰片41接触。
174.接着,在嵌件成形模具8合模后,从注射口84向嵌件成形模具8的模腔83注射填充由熔融状态的热塑性树脂构成的不透明树脂材料11并使其固化(参照图18)。由此,在第一成形部21成形的同时,能够使第一成形部21与光源安装基板3和第二成形部22的一体成形
品13、装饰片41一体化。
175.其他与制法1中的嵌件成形工序相同,因此省略说明。
176.3.照明显示面板100的制造方法(制法5)
177.在上述制法4中,对在嵌件成形工序中包覆装饰片41的情况进行了说明,但在本第二实施方式的照明显示面板100中,并不限定于该制法。
178.即,在图19所示的本制法5中,在将第二成形部22与光源安装基板3一体化后,在光源安装基板3和第二成形部22的一体成形品13层压与用于装饰树脂面板2的前表面的装饰片41预先一体化的另外成形的第一成形部21。
179.本制法5与制法4不同的主要方面仅是层压工序,因此省略其他工序的说明。
180.层压的带有装饰片41的第一成形部21可以通过嵌件成形法进行成形。
181.即,首先,在由凸模810和凹模820构成的注射成形模具80的模腔830中,以图案层侧朝向模腔830的方式设置用于装饰树脂面板2的前表面的装饰片41(参照图20)。
182.装饰片41例如使用吸引用孔由空气吸引而吸附于凹模820的内表面。另外,在图20所示的例子中,装饰片41以沿着凹模820的模腔830的内表面的方式预成形。
183.接着,如图21所示,在由凸模810和凹模820构成的注射成形模具80的模腔830中,从注射口840注射填充由熔融状态的热塑性树脂构成的不透明树脂材料11并使其固化。
184.使用的不透明树脂材料11与制法1的嵌件成形时使用的材料相同。
185.返回图19,在光源安装基板3和第二成形部22的一体成形品13层压带有装饰片41的第一成形部21时,与第一实施方式的制法2同样地使用粘接剂15进行贴合。
186.此外,在图19所示的例子中,将粘接剂15设置在第一成形部21侧,但粘接剂15也可以设置在一体成形品13的第一成形部21侧进行贴合。
187.4.照明显示面板100的制造方法(制法6)
188.在上述制法4以及上述制法5中,说明了在将第二成形部22与光源安装基板3一体化后,将光源安装基板3和第二成形部22的一体成形品13进一步与带有装饰片41的第一成形部21一体化的情况,但在本实施方式的照明显示面板100中,并不限定于上述制法4以及上述制法5。
189.即,在图22~图24所示的本制法3中,在压缩成形中,将第二成形部22与光源安装基板3以及另外成形的带有装饰片41的第一成形部21同时一体化。
190.首先,在注入透光树脂材料10之前,在压缩成形模具70的下模720所具有的模腔720a中设置另外嵌件成形的带有装饰片41的第一成形部21(参照图22)。
191.本制造方法6中使用的另外嵌件成形的带有装饰片41的第一成形部21可以通过与上述制法5中的带有装饰片41的第一成形部21同样的材料以及成形方法(参照图20~21)成形。
192.接着,在下模720的设置有带有装饰片41的第一成形部21的模腔720a中,与上述制法1~5的压缩成形同样地,将计量出的未固化的热固性树脂作为透光树脂材料10注入(参照图23)。
193.接着,以使模腔720a成为密闭状态的方式将压缩成形模具70合模。接着,在将压缩成形模具70合模后,一边压缩模腔720a一边将透光树脂材料10以低压填充并使其固化(硬化)(参照图24)。
194.其他方面与上述制法1~5的压缩成形相同,因此省略说明。
195.[各种变化例]
[0196]
(变化例1)
[0197]
在上述的第一实施方式以及第二实施方式中,对不存在第一成形部21的部分为贯通孔,并在该贯通孔的内壁面21a嵌合有第二成形部22的凸部22a的情况进行了说明,但本发明中的树脂面板并不限定于此。
[0198]
图25是表示使用了其他显示图案的树脂面板的照明显示面板103的例子的俯视图。图26是表示图25的照明显示面板的cc线剖面的剖视图。
[0199]
如图25及图26所示,在本变化例中,树脂面板23在第一成形部213的侧面213b嵌合有第二成形部223的凸部223a。更详细而言,第二成形部223包覆平面箭头形状的第一成形部213的周围以及背面。即,对平面箭头形状的第一成形部21的周围进行照明。也就是,以在发光的背景中以遮光的方式对箭头符号进行显示。
[0200]
此外,在图25以及图26所示的变化例1中,树脂面板23的第二成形部223在俯视时包围第一成形部213的周围,但树脂面板24的第二成形部224在俯视时也可以仅与第一成形部214相邻(参照图27)。
[0201]
(变化例2)
[0202]
另外,在上述的第一实施方式以及第二实施方式中,对树脂面板2的第二成形部22的凸部22a在前表面具有平滑面的情况进行了说明,但本发明中的树脂面板并不限定于此。
[0203]
例如,在本变化例2中,树脂面板25的第二成形部225的凸部225a在前表面具有细微凹凸50(参照图28)。这些细微凹凸50发挥消光等装饰功能、扩散效果或透镜效果等光学功能等。
[0204]
为了使第二成形部225的凸部225a在前表面形成如上所述的细微凹凸50,如图29所示,压缩成形模具7的下模72在与第二成形部225的凸部225a的前表面对应的部分具有细微凹凸51。
[0205]
如上所述,在基于压缩成形的第二成形部225的成形中,一边压缩模腔72a一边填充透光树脂材料10并使其固化,因此,通过由压缩引起的透光树脂材料10的流动,透光树脂材料10可靠地到达设置于下模72的形成模腔72a的面的细微凹凸51的最深部。
[0206]
(变化例3)
[0207]
另外,在上述的第一实施方式及第二实施方式中,说明了在照明显示面板的制造方法中,低压成形模具为压缩成形模具7、70,在被加热的下模72、720所具有的模腔72a、720a中注入由未固化的热固性树脂构成的透光树脂材料10后,将低压成形模具合模的情况,但本发明中的照明显示面板的制造方法并不限定于此。
[0208]
例如,在本变化例3中,低压成形模具是注射冲压成形模具9,在将低压成形模具合模后,在下模92所具有的模腔92a中注射注入由熔融状态的热塑性树脂构成的透光树脂材料90。
[0209]
以下,对使用了注射冲压成形模具9的低压成形的各工序的变化例进行说明。
[0210]
在图30中,注射冲压成形模具9的上模91和下模92以合模前的状态表示。首先,在注射冲压成形模具9的上模91上,以光源31的安装面朝向下方的方式设置光源安装基板3(参照图30)。
[0211]
另外,光源安装基板3例如使用吸引用孔由空气吸引而吸附于上模91。
[0212]
接着,在以使模腔92a成为密闭状态的方式将注射冲压成形模具9合模后,将计量出的熔融状态的热塑性树脂作为透光树脂材料90向注射冲压成形模具9的下模92所具有的模腔92a注射注入(参照图31)。
[0213]
在图31中示出了由形成模腔92a的底面的模腔块922和形成模腔92a的侧面的框架块921构成的下模92。另外,示出了设有通往模腔92a的射出口94的上模91。
[0214]
另外,在框架块921的下部设置有弹簧923。在上模91与下模92的紧固前,框架块921通过弹簧923位于上升位置。
[0215]
作为在注射冲压成形法中使用的热塑性树脂。例如是聚碳酸酯(pc)树脂、abs树脂、聚甲基丙烯酸甲酯(pmma)树脂、它们的组合等。
[0216]
接着,在将透光树脂材料90射出到模腔92a内之后,一边利用上模91压缩模腔92a一边以低压填充透光树脂材料90并使其冷却固化(参照图32)。
[0217]
即,上模91的下表面周围将下模92的框架块921压下,由此对下模92的模腔92a以及注入其中的透光树脂材料90进行压缩。由此,设置于上模91的光源安装基板3的光源31成为浸在透光树脂材料90中的状态。
[0218]
在该状态下,熔融状态的透光树脂材料90在下模92的模腔92a中冷却固化,从而成形出第二成形部22。
[0219]
此外,在图32所示的注射冲压成形法中,示出了使上模91相对于下模92下降而对下模92的模腔92a以及注入其中的透光树脂材料90进行压缩的情况,但也可以使下模92相对于上模91上升。
[0220]
这样,注射冲压成形的第二成形部22与压缩成形的情况同样,以利用第二成形部22封固光源31的方式与光源安装基板3一体化(参照图6)。
[0221]
此外,被注射冲压成形的第二成形部22与第一成形部21均由热塑性树脂构成。因此,第二成形部22和第一成形部21中的在制法1、3、4和6中先成形的一方构成为,在之后成形的另一方成形时不会溶解到完全不能维持形状的程度。即,先成形的树脂优选具有与后成形时的加热温度同等或比其高的软化温度。
[0222]
(变化例4)
[0223]
另外,在上述的第二实施方式中,对照明显示面板100还具备装饰片41作为对树脂面板2的前表面进行装饰的装饰层4的情况进行了说明,但本发明中的照明显示面板并不限定于此。
[0224]
例如,装饰层4也可以通过例如丝网印刷法在树脂面板2的前表面直接形成图案层。
[0225]
另外,在上述的第二实施方式中,对图案层在装饰片41的显示部位100a成为透明的情况进行了说明,但也可以使图案层在显示部位100a成为半透明形成。在将上述的图案层直接形成于树脂面板2的情况下也是同样的。
[0226]
并且,装饰片41也可以在层构成中具备触摸传感器片。
[0227]
(变化例5)
[0228]
另外,在上述的第一实施方式以及第二实施方式中,对树脂面板2在周围具有立起部分的形状的情况进行了说明,但本发明的照明显示面板并不限定于此。
[0229]
例如,树脂面板2的形状也可以是在周围没有立起部的平板形状。在该情况下,与其他成形部件组合而构成箱型形状的箱体。另外,树脂面板2的形状也可以是其他复杂的形状。
[0230]
关于其他结构,在本说明书中公开的实施方式在所有方面均为例示,应理解为本发明的范围并不限定于此。只要是本领域技术人员,就能够容易地理解在不脱离本发明的主旨的范围内能够进行适当的改变。因此,在不脱离本发明的主旨的范围内进行了改变的其他实施方式当然也包含在本发明的范围内。
[0231]
产业上的利用可能性
[0232]
本发明能够用于汽车、家电产品、音频设备等。
[0233]
符号的说明
[0234]
1、100、103~105—照明显示面板,1a、100a—显示部位,2、23~25—树脂面板,21—第一成形部(不透明),211—贯通孔,21a—内壁面,21b—侧面,22、223~225—第二成形部(透光),22a、223a~225a—凸部,3—光源安装基板,31—光源,32—薄膜基板,4—装饰层,41—装饰片,50、51—细微凹凸,7、70—压缩成形模具,71、710—上模,72、720—下模,72a、720a—模腔,721、7210—框架部块,722、7220—模腔块,723、7230—弹簧,724、7240—加热器,8—嵌件成形模具,81—凸模,82—凹模,83—模腔,84—射出口,10、90—透光树脂材料,11—不透明树脂材料,13—一体成形品,15—粘接剂,80—注射成形模具,810—凸模,820—凹模,830—模腔,840—射出口,9—注射冲压成形模具,91—上模,92—下模,92a—模腔,921—框架部块,922—模腔块,923—弹簧,94—射出口。