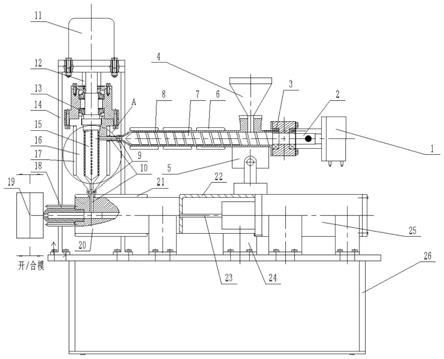
1.本发明属于高分子材料加工装置技术领域,具体涉及一种能够预先对已熔融的聚合物熔体进行解缠结处理,以提高聚合物的流动性能,再将处理后的聚合物熔体进行注射成型的注塑成型机。
背景技术:2.高分子材料具有种类丰富、性能优异、价格低廉等优点,被广泛地使用在人类的生产和生活中。塑料作为最重要的一类高分子材料,需经过加工而制成制品来使用。经过多年的发展,塑料加工已经有了多种成熟的成型方法,其中注塑成型方法具有一次成型制品、尺寸精确高,可加工塑料品种广泛,生产率高等优点,是聚合物加工最重要的方法之一。
3.注塑成型需使用注塑成型机(又称之为注塑机或注射机),目前生产中使用的注塑机大都属于往复螺杆式注塑机,它是通过外部加热和螺杆剪切的作用使进入注塑机料筒的塑料熔融,从而产生一定的流动性,再利用注塑机上的螺杆对熔融塑料施加一定的压力,使其从注塑机喷嘴射出而充满模具型腔,冷却后开模获得所需的制品。现有的注射成型一般分为合模、注射、保压、冷却(同时对塑料进行塑化)、开模和取出制品等几个阶段,故其是一种间歇性的成型方式。
4.当使用现有的注塑机注射高粘度的高分子材料或需要成型大型、薄壁塑料制件时,会因高分子材料的粘度高,流动性差,或因充模物料量大,所需时间长而面临充模困难的问题,严重时甚至不能顺利充满模具型腔。这时往往会使用高的熔体温度和注射压力,不仅使成型过程能耗增加,且高的熔体温度还容易导致高分子材料发生降解、性能降低,加剧成型制品的收缩和变形;高的注射压力则会导致成型制品的内应力较大等诸多缺陷。研究还表明,剪切场或振动场可以使聚合物熔体在作用方向上的流层间产生相对滑移,从而使缠结的高分子长链得到一定程度的解脱,引起粘度下降。但是,普通的注塑机在塑化时剪切时间短(通常只有几秒钟)、剪切作用弱,同时塑化好准备进入注射的塑料熔体大多聚集在料筒前端,不会再受螺杆旋转所产生的剪切作用,也就不大可能通过螺杆螺纹产生的剪切场来达到降低熔体粘度,改善高分子材料的流动性。因此,在预先设定注射成型温度下,现有注塑机也不具备降低聚合物熔体粘度的功能。
技术实现要素:5.本发明的目的是针对现有技术存在的问题,提供一种在设定温度下也可提高高分子材料流动性的注塑成型机。
6.本发明提供的可提高高分子材料流动性的注塑成型机,该注塑成型机是由依次连接的塑化机构、解缠结机构、注射机构、模具、支撑机构和机座构成,塑化机构、解缠结机构和注射机构由支撑机构固定支撑,支撑机构固定在机座上。
7.所述的塑化机构由液压马达、第一联轴器、第一轴承组、加料斗、第一加热套、塑化螺杆和第一料筒构成,第一料筒通过支撑机构中的第一支撑架固定在机座上,液压马达通
过第一联轴器与塑化螺杆尾部连接,塑化螺杆由第一轴承组支撑,加料斗固定在第一料筒上,第一加热套设置包覆在第一料筒外表面,塑化机构通过第一料筒前端的熔体流动通道与解缠结机构相连,该熔体流动通道上设置有阀门。
8.所述的解缠结机构由驱动电机、第二联轴器、第二轴承组、解缠结芯轴、第二加热套和第二料筒构成,解缠结机构通过支撑机构中的第二支撑架固定于机座上,解缠结芯轴通过位于上半段的第二轴承组固定在第二料筒内部,芯轴上端通过第二联轴器与驱动电机连接,第二料筒的筒壁右侧上部开有熔体流动通道与塑化机构的位于塑化螺杆头部前端的熔体流动通道相连接,第二料筒的筒壁下端也开有熔体流动通道,该熔体流动通道与注射机构相连,且该熔体流动通道上设置有阀门,
9.其特征在于在解缠结机构中所述解缠结芯轴外表面上沿轴向设置有若干列平行排列且凸起的一个个块筋;
10.所述的注射机构由第三支撑架固定在机座上,由注射喷嘴、储料缸、第三加热套、防护套、注射活塞和注射油缸构成,注射喷嘴由螺纹固定在储料缸前端,第三加热套设置在储料缸外表面,注射油缸控制注射活塞进行周期性往复运动,以将塑料熔体注射压入模具内。与解缠结机构的驱动电机匹配的
11.以上注塑成型机中还设置有可编程逻辑控制器(plc),可编程逻辑控制器(plc)是通过其的编程来操控解缠结机构的驱动电机来实现解缠结芯轴的周向旋转、周向振动、周向旋转与振动叠加的复合运动和周向线性加减转速四种运动方式。所述驱动电机为伺服电机。具体来说是通过外部输入的参数来控制,其中设定周向旋转的速度为v(rad/s)、周向振动的频率为f(hz)、周向振动的幅度为θ(rad)。复合运动可用周向旋转转速v(rad/s)、周向振动频率f(hz)和周向振动幅度θ(rad)三个参数进行控制;周向线性加减转速可通过最大转速v(rad/s)和旋转时间t(s)进行控制,即在0
‑
t/2内进行旋转速度由0线性增加至v的周向旋转运动,t/2
‑
t内进行旋转速度由v线性减少至0的周向旋转运动。因此,利用可编程逻辑控制器(plc)对伺服电机编程即可实现通过输入v、f、θ、v、t这5个参数来获取所需的运动模式。
12.以上注塑成型机中所述的驱动电机与解缠结芯轴之间还可根据需要配置减速器,这是本领域技术人员公知的常识。
13.以上注塑成型机中当解缠结芯轴的直径为30~50mm(进行批量生产时可根据需要增大芯轴直径),其外表面上设置的块筋至少为3列,优选3
‑
6列,更优选4
‑
5列,且呈均匀分布。如果解缠结芯轴的大于50mm,可根据需要按直径(mm)与列数10:1至5:1进行调整。
14.以上注塑成型机中所述解缠结芯轴外表面上每列设置的块筋之间的间隔为4
‑
6mm,且相邻两列块筋之间呈交错排列。
15.以上注塑成型机中所述解缠结芯轴外表面上设置的每一个块筋深度为3
‑
5mm,长为4
‑
6mm,宽为2
‑
4mm。
16.本发明与现有技术相比,具有以下有益效果:
17.1.由于本发明提供的可提高高分子材料流动性的注塑成型机在解缠结机构芯轴的外表面上沿轴向设置了若干列平行排列且凸起的块筋,其可随电机驱动的芯轴对从塑化机构输送过来的熔体进行搅动,因而可使熔融的高分子材料中缠结的分子链可以松解开来,改善高分子材料的流动性。
18.2.由于本发明提供的可提高高分子材料流动性的注塑成型机在解缠结机构芯轴的外表面上设置了若干列平行排列且凸起的块筋,相较现有解缠结机构中普通的螺杆螺纹会产生壁面滑移,造成物料表面和芯层受到的剪切力不同,这些垂直平行水平交错的块筋在物料输送期间能产生良好的混合作用,可增加塑料熔体所受到的剪切作用的均匀性,因而可以避免物料在层厚方向上因剪切不均匀所带来的解缠结效果差的缺点;同时块筋间的空间较大,可以有效增加熔体的容量,提高解缠结效率。
19.3.由于本发明提供的可提高高分子材料流动性的注塑成型机中还设置了与解缠结机构芯轴的外表面上设置的块筋匹配的、并可通过plc控制的驱动电机,因而能够实现块筋随芯轴进行周向旋转、周向振动、周向旋转与振动叠加的复合运动和周向线性加减转速四种运动方式,可对聚合物熔体进行解缠结,降低成型过程中的熔体粘度,克服由于高分子材料流动性差带来的各种制品缺陷,或在保持熔体粘度大体不变的情况下,大幅度地降低解缠结后高分子材料的成型温度或压力,实现低温成型,节能、环保效果非常显著。
20.4.由于本发明提供的可提高高分子材料流动性的注塑成型机中解缠结机构是垂直于地面摆放,因而可利用重力作用实现熔融聚合物的良好输送。
附图说明
21.图1为本发明提供的可提高高分子材料流动性的注塑成型机的结构示意图。
22.图2为图1中解缠结机构芯轴及外表面上设置块筋的局部a的放大结构示意图。
23.图3为利用本发明在不同成型条件下制得的聚碳酸酯长方形样条。说明与未经解缠结处理的样品相比,经解缠结处理后样品可在更低温度和压力下充满型腔。
24.图4为利用本发明注塑成型机制得聚碳酸酯样条充填长度随熔体温度和压力的变化趋势图。说明与未经解缠结处理的样品相比,经解缠结处理后样品可在更低温度和压力下充满型腔。
25.图中:1
‑
液压马达;2
‑
第一联轴器;3
‑
第一轴承组;4
‑
加料斗;5
‑
第一支撑架;6
‑
第一加热套;7
‑
塑化螺杆;8
‑
第一料筒;9
‑
阀门;10
‑
熔体流动通道;11
‑
驱动电机;12
‑
第二联轴器;13
‑
第二轴承组;14
‑
第二支撑架;15
‑
解缠结芯轴;16
‑
第二料筒;17
‑
第二加热套;18
‑
注射喷嘴;19
‑
模具;20
‑
储料缸;21
‑
第三加热套;22
‑
防护套;23
‑
注射活塞;24
‑
第三支撑架;25
‑
注射油缸;26
‑
机座;27
‑
块筋。
具体实施方式
26.下面通过实施例对本发明进行清楚完整的描述。有必要在此指出的是,以下实施例只用于对本发明进行进一步说明,不能理解为对本发明保护范围的限制,该领域的技术熟练人员可以根据上述本发明的内容做出一些非本质的改进和调整,这些非本质的改进和调整仍应属于本发明的保护范围。
27.实施例1
28.如图1所示,本实施例给出的可提高高分子材料流动性的注塑成型机是由依次连接的塑化机构、解缠结机构、注射机构、模具19、支撑机构和机座26构成,塑化机构、解缠结机构和注射机构由支撑机构固定支撑,支撑机构固定在机座26上。
29.其中所述塑化机构由液压马达1、第一联轴器2、第一轴承组3、加料斗4、塑化螺杆
7、第一加热套6和第一料筒8构成。第一料筒8通过支撑机构中的第一支撑架5固定在机座26上,液压马达1通过第一联轴器2与塑化螺杆7尾部连接,塑化螺杆7由第一轴承组3支撑,加料斗4固定在第一料筒8上,第一加热套6设置包覆在第一料筒8外表面,塑化机构通过第一料筒8前端的熔体流动通道10与解缠结机构相连,该熔体流动通道10上设置有阀门9。
30.所述的解缠结机构由驱动电机11、第二联轴器12、第二轴承组13、解缠结芯轴15、第二加热套17和第二料筒16构成。解缠结机构通过支撑机构中的第二支撑架14垂直固定于机座26上,解缠结芯轴15通过位于上半段的第二轴承组13固定在第二料筒16内部,其上端通过第二联轴器12与驱动电机11连接,而驱动电机11则与plc连接,并可通过plc控制解缠结芯轴15进行周向旋转、周向振动、周向旋转与振动叠加的复合运动和周向线性加减转速四种运动方式;所述驱动电机11为伺服电机;解缠结芯轴15外表面上沿轴向设置有若干列平行排列且凸起的一个个块筋27,见图2。本实施例的解缠结芯轴15直径为40mm,其上设置的块筋27为4列,且呈90
°
均匀分布在解缠结芯轴15外表面,每列设置的块筋27之间的间隔为5mm,且相邻两列块筋27之间呈交错排列,每一个块筋27深度为4mm,长为5mm,宽为3mm;第二料筒16的筒壁右侧上部开有熔体流动通道10与塑化机构中位于塑化螺杆头部前端的熔体流动通道10相连接,第二料筒16的筒壁下端也开有熔体流动通道10,该熔体流动通道10与注射机构储料缸20上的熔体流动通道10相连,且该熔体流动通道10上设置有阀门9。
31.所述的注射机构由第三支撑架24固定在机座26上,由注射喷嘴18、储料缸20、第三加热套21、防护套22、注射活塞23和注射油缸25构成,注射喷嘴18由螺纹固定在储料缸20前端,第三加热套21设置在储料缸20外表面,注射油缸25控制注射活塞23进行周期性往复运动,以将储料缸20内的塑料熔体注射压入模具19内成型。
32.使用时,在上一个成型周期的保压结束时(保压由注射活塞23进行),阀门9开启,液压马达1通过第一联轴器2驱动塑化螺杆7转动,塑料物料从加料斗4加入,塑化螺杆7在转动的同时向前输送塑料物料,塑料物料通过第一加热套6的加热作用和塑化螺杆7转动形成的剪切作用逐渐融化为熔体;塑料熔体通过熔体流动通道10进入第二料筒16内,plc控制驱动电机11通过第二联轴器12驱动解缠结芯轴15进行选择的周向旋转、周向振动、周向旋转与振动叠加的复合运动和周向线性加减转速的任一种运动方式转动,以使块筋27持续对进入第二料筒16的塑料熔体施加剪切作用,实现解缠结,并有效降低塑料熔体的粘度;同时随着已经解缠结的塑料熔体经过熔体流动通道10进入注射机构的储料缸20中,并推动注射活塞23向后退;当其后退到设定的塑化量时,塑化机构的液压马达1停止转动,同时阀门9关闭;注射活塞23向前运动,将储料缸20中的塑料熔体注射入模具19中,并进行保压,然后开模、取出制件进入下一个循环周期。需要特别说明的是,在整个循环周期中,解缠结芯轴15始终在驱动电机11的带动下进行转动,对第二料筒16中的塑料熔体施加剪切作用,因此可以获得良好的解缠结效果,从而大幅降低塑料熔体的粘度。
33.实施例2
34.如图1、2所示,本实施例给出的可提高高分子材料流动性的注塑成型机也是由依次连接的塑化机构、解缠结机构、注射机构、模具19、支撑机构和机座26构成,塑化机构、解缠结机构和注射机构由支撑机构固定支撑,支撑机构固定在机座26上。由于本实施例的塑化机构、解缠结机构、注射机构、模具19、支撑机构和机座26均与实施例1相同,就不一一赘述,所不同的是本实施例的解缠结芯轴15直径为50mm,其上设置的块筋27为6列,且呈60
°
均
匀分布在芯轴15外表面,每列设置的块筋27之间的间隔为6mm,且相邻两列块筋27之间呈交错排列,每一个块筋27深度为5mm,长为6mm,宽为4mm。
35.实施例3
36.如图1、2所示,本实施例给出的可提高高分子材料流动性的注塑成型机也是由依次连接的塑化机构、解缠结机构、注射机构、模具19、支撑机构和机座26构成,塑化机构、解缠结机构和注射机构由支撑机构固定支撑,支撑机构固定在机座26上。由于本实施例的塑化机构、解缠结机构、注射机构、模具19、支撑机构和机座26均与实施例1相同,就不一一赘述,所不同的是本实施例的解缠结芯轴15直径为30mm,其上设置的块筋27为3列,且呈120
°
均匀分布在芯轴15外表面,每列设置的块筋27之间的间隔为4mm,且相邻两列块筋27之间呈交错排列,每一个块筋27深度为3mm,长为4mm,宽为2mm。
37.应用例1
38.本应用例是采用实施例1给出的注塑成型机来注塑成型聚碳酸酯高分子材料。虽聚碳酸酯(pc)的性能优良,但粘度大,采用普通注射成型机时容易发生充模不完整的情况,故同时需要高的注射温度和高的注射压力,因此本应用例选其作为注射成型用的原材料。开启注塑成型机,并将由塑化螺杆7塑化好的pc熔体通过熔体流动通道10输入第二料筒16内进行解缠结处理后,运动方式采用周向旋转与振动叠加的复合运动,解缠结后的熔体进入储料缸20内进行注塑制得样条。在此过程中,注射压力保持600bar不变,模具温度固定为160℃以确保熔体能够较好地充填模具型腔,逐步调节第一加热套6、第二加热套17和第三加热套21的温度,记录pc熔体在不同温度(如280、290℃)下充填模具型腔的情况。具体结果见图3左部两根样条。
39.应用例2
40.本应用例与应用例1的材料、装置、解缠结芯轴运动方式和测试方法完全相同。不同之处在于,本例中将第一加热套6、第二加热套17和第三加热套21的温度都设定为310℃,逐步调节注塑系统的注射压力从400
‑
450bar,并记录pc熔体在不同压力下充填模具的型腔的情况。具体结果见图3右部三根样条。
41.应用对比例
42.本应用对比例与应用例1的材料、装置和测试方法完全相同。不同之处在于,本例中驱动电机11关闭,解缠结芯轴15为静止状态,此时,该注射成型过程相当于使用普通注射成型机进行注射成型,记录pc熔体在不同温度(290
‑
310℃)下充填模具型腔的情况。具体结果见图3中部四根样条。
43.为考察本发明的技术效果,将应用例1和应用对比例,应用例2和应用对比例得到的样条进行对比,如图3所示。从图3中可以看到,在当注塑成型机的解缠结系统工作时,设定注射压力p=600bar,只需将熔体温度从280℃提高到290℃就能使pc在注射时间范围内充满整个模具型腔;在应用对比例中,当解缠结系统停止工作时,相同压力下,熔体温度290℃时模具型腔还差1cm左右未被充满;逐步提高熔体温度,最终当温度达到310℃时才能充满型腔。对比图3中标号为a、b的样条可知,在其他条件相同的情况下,解缠结试样的加工温度可以比原始粒料降低20℃。当固定熔体温度为310℃时,从图3右侧的3根样条可知,310℃下解缠结试样最低可以在450bar的压力下充满型腔,而低于450bar会充填不满,对比标号为2和3的样条可知解缠结试样的成型压力可以比原始粒料降低25%。充填长度随熔体温度
和注射压力的变化趋势见图4。在更低的熔体温度和成型压力下加工材料,有利于降低残余应力,提高制品的力学性能。另外,当聚合物熔体在正常加工条件下难以填充模具腔体时(如成型薄壁深腔制品),通过解缠结处理的具有初始熔体粘度更低的解缠试样比未经解缠结处理的原材料相比更具有优越性。