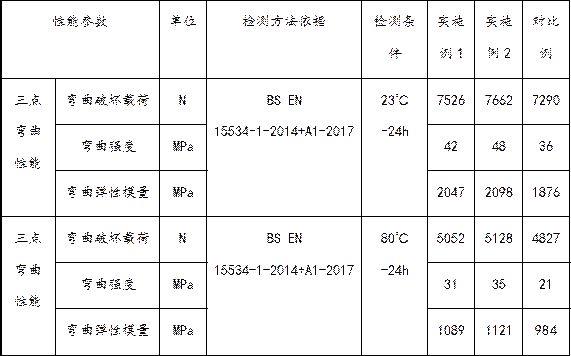
1.本发明涉及共挤发泡板技术领域,具体涉及一种增强发泡地板、其制备用的挤出模具和设备组。
背景技术:2.现有的复合地板多为密度板、木板等材料的板材与耐磨层等功能层复合而成,其具有较大的密度,单位体积地板的重量较大,为该类型复合地板的运输带来不便,运输成本较高。
3.为此,有采用发泡pvc材料代替至少部分上述的密度板、木板制备复合地板的技术方案,如授权公告号为cn 209603434 u的中国实用新型专利公开的一种耐候pvc地板,其包括有从上至下的耐磨层、稳定层、发泡层和排水层,各层之间通过涂覆粘结实现连接,其中,发泡层即采用发泡pvc材料,复合地板的密度得以降低,方便运输。
4.然而,当以发泡pvc材料作为复合地板的主要芯层材料时,该复合地板的弯曲弹性模量往往不足,即其容易在踩踏的压力下发生形变,给客户以不稳定、不安全的使用体验,使用寿命也难以保障。
5.为了克服这种弯曲弹性模量偏低的缺陷,往往需要增加地面龙骨铺设的密度,以对该复合地板形成足够的支撑,但铺设地面龙骨需要额外的空间,地面龙骨自身材料的成本和铺装成本也大大降低了pvc发泡类地板的市场竞争力。
6.为此,为了增加该复合地板的弹性模量,会在复合地板的芯层材料中设置玻璃纤维增强层,如上述的现有技术中,其稳定层中即设置有玻璃纤维,起到增强支撑的作用,又如申请公布号为cn 105003060 a的中国发明专利,公开了一种连续玻纤增强复合地板及其制造方法,其采用玻纤增强热塑预浸带,用于增强复合地板的最外层。
7.至此,pvc发泡类复合地板的机械强度问题得到了很大程度上的解决,然而,pvc发泡类复合地板自身强度的提升仍然存在瓶颈,并且即使增加了玻璃纤维增强层,pvc发泡类复合地板产品的强度也难以稳定的维持,时常会生产出强度不足的残次产品,造成生产成本的提高。
8.此类问题在室外使用地板的领域中尤为突出,由于户外地板在烈日的暴晒下往往会达到较高的温度,pvc发泡材料在高温下的弯曲弹性模量会迅速衰减,因此在室外使用地板领域对pvc发泡复合地板强度的要求会进一步提高,现有的pvc发泡类地板难以达到使用要求。
技术实现要素:9.针对上述问题,本技术以提升发泡类复合地板产品的机械强度和稳定性为目的,进行开发研究,提供了一种增强发泡地板、其制备用的挤出模具和设备组,制备出的增强发泡地板具有机械强度高、稳定性好、次品率低的优势。
10.本发明解决上述问题的技术方案如下:
增强发泡地板,包含有发泡芯体和增强件,所述增强件支撑的设置于所述发泡芯体的内部或表面上,所述发泡芯体的任一截面上空孔个数少于12个/平方分米;所述空孔为边缘上任意两点之间的最大距离大于0.5mm的孔。
11.作为上述技术方案的优选,制成所述发泡芯体的材料为pvc发泡材料。
12.作为上述技术方案的优选,制成所述增强件的材料为玻璃纤维浸渍材料。
13.作为上述技术方案的优选,所述增强件为玻璃纤维浸渍聚合物形成的材料,进一步优选为玻璃纤维浸渍abs工程塑料形成的玻璃纤维浸渍带。
14.作为上述技术方案的优选,所述增强件的数量为两个,且分别设置于所述发泡芯体相对的两个表面处。
15.作为上述技术方案的优选,所述增强发泡地板的至少一侧的表面处设置有防护层。
16.作为上述技术方案的优选,所述发泡芯体外包覆的设置有筒状的限位部。
17.作为上述技术方案的优选,所述发泡芯体的任一截面上空孔个数少于9个/平方分米,所述空孔边缘上任意两点之间的最大距离大于0.5mm。
18.挤出模具,用于制备上述任一技术方案所述的增强发泡地板,包含有贯通所述挤出模具的芯体材料流道以及设置于所述芯体材料流道侧部的增强件流道,增强件材料由所述增强件流道的增强件挤出口挤出,所述芯体材料流道内间隔的设置有若干个顺应于芯体材料流动方向的分隔流道,芯体材料从若干个所述分隔流道的芯体材料挤出口中挤出,且若干个所述芯体材料挤出口相平齐的设置。
19.作为上述技术方案的优选,所述增强件流道的数量为两个,且分别设置于所述芯体材料流道相对的两个外侧。
20.作为上述技术方案的优选,还包含有限位材料流道,所述限位材料流道包含有限位材料挤出段,所述限位材料挤出段的内侧壁形成筒状的限位型腔,所述限位材料挤出段的外侧壁包覆所述限位材料挤出段的内侧壁形成限位材料的挤出流道;所述限位材料挤出段的外侧壁轮廓与增强发泡地板的挤出轮廓的形状相适配;若干个所述芯体材料挤出口、所述增强件挤出口均设置于所述限位型腔内。
21.作为上述技术方案的优选,所述限位材料挤出段的外侧壁轮廓和内侧壁轮廓的横截面形状均为圆角矩形。
22.作为上述技术方案的优选,两个所述增强件挤出口分别设置于所述限位型腔内相对的两个内侧壁处,且所述增强件挤出口与所述限位型腔的内侧壁相邻的设置。
23.作为上述技术方案的优选,还包括若干个排气通道,所述排气通道的入口设置于相邻的两个所述芯体材料挤出口的连接处,所述排气通道的出口设置于挤出模具与周围环境大气的连通处。
24.作为上述技术方案的优选,所述分隔流道在芯体材料的挤出方向上包含有流道逐渐扩张的导向挤出段,所述导向挤出段扩张的终点即所述芯体材料挤出口。
25.作为上述技术方案的优选,所述导向挤出段是由四个导向面衔接后包围而成的筒状通道;所述导向面位于所述芯体材料挤出口的一侧为芯体材料挤出侧,相邻的两个所述芯体材料挤出口的所述芯体材料挤出侧共线。
26.作为上述技术方案的优选,还包括若干个排气通道,所述排气通道的入口设置于相邻两个所述芯体材料挤出口的所述芯体材料挤出侧的共线处,所述排气通道的出口设置于挤出模具与周围环境大气的连通处。
27.设备组,包含有上述任一技术方案所述的挤出模具,还包含有:芯体材料挤出装置,用于将芯体的材料挤入所述挤出模具的芯体材料流道内;增强件材料输送装置,用于将增强件材料输送至所述挤出模具的增强件流道内;限位材料挤出装置,用于将限位部的材料挤入所述挤出模具的限位材料流道内;冷却定型装置,用于冷却和定型从所述挤出模具中挤出的增强发泡地板材料;牵引装置,用于牵引经所述冷却定型装置冷却后的增强发泡地板材料。
28.作为上述技术方案的优选,设备组还包括防护层材料挤出装置,用于将防护层材料挤入所述挤出模具内。
29.作为上述技术方案的优选,所述增强件材料输送装置的数量为两个。
30.综上所述,本技术实施例具有以下有益效果:本技术实施例所述的增强发泡地板发泡均匀,有效的限制了大孔径空孔的形成,从而形成较为均一的发泡结构,而大孔径的空孔是导致发泡类地板的机械强度无法进一步提升的瓶颈,因此,本技术发明人克服了发泡类地板机械强度进一步提升的瓶颈,使得发泡增强地板的强度得以进一步提升,进而达到了户外地板的使用需求;并且,本技术实施例所述的增强发泡地板产品的成品性能稳定,残次品率得以大幅降低,节约了生产的材料成本和时间成本。
附图说明
31.图1为本技术实施例所述的增强发泡地板的截面结构示意图;图2为本技术实施例所述的挤出模具侧剖面结构示意图;图3为本技术实施例所述的挤出模具的挤出端口结构示意图;图4为本技术另一个实施例所述的挤出模具的挤出端口结构示意图;图5为图4的e区放大图;图6为本技术实施例所述的设备组结构示意图。
32.图中:a
‑
发泡芯体、b
‑
增强件、c
‑
防护层、d
‑
限位部;1
‑
挤出模具、1
‑1‑
芯体材料流道、1
‑
1.1
‑
芯体材料挤出口、1
‑
1.2
‑
导向挤出段、1
‑
1.21
‑
导向面、1
‑2‑
增强件流道、1
‑
2.1
‑
增强件挤出口、1
‑3‑
限位材料流道、1
‑
3.1
‑
限位材料挤出段、1
‑4‑
排气通道;2
‑
芯体材料挤出装置、3
‑
增强件材料输送装置、4
‑
限位材料挤出装置、5
‑
冷却定型装置、6
‑
牵引装置、7
‑
防护层材料挤出装置。
具体实施方式
33.下面将对本发明实施例中的技术方案进行清楚、完整地描述,显然,所描述的实施例仅仅是本发明一部分实施例,而不是全部的实施例。本发明中的实施例,本领域普通技术人员在没有做创造性劳动前提下所获得的所有其它实施例,都属于本发明保护的范围。
34.在现有技术中,芯体材料往往是一整个连续的流动空间,该空间的体积相对较大,会导致芯体材料在流道中就开始进行发泡,而流道中的发泡过程较难控制,流道中间部分的芯体材料发泡尤其困难,会导致发泡不均匀;且芯体材料在芯体材料流道中会因为挤出机进料量的波动而出现内部的空腔或在流动时产生紊流,也使得发泡不均匀;该现有技术参考之后的对比例;发泡不均匀就更容易产生前述的空孔,而本技术发明人发现,该空孔的数量越多,相应地板的强度下降的就越明显,出现残次品的可能性也越高。
35.下面结合附图以实施例和对比例对本发明进行详细说明。
36.实施例1:参考图1,增强发泡地板,主体为由pvc发泡材料构成的发泡芯体a,发泡芯体a的上下表面处分别设置有两个增强件b,发泡芯体a的外周包覆有筒状的限位部d,地板的上表面设置有防护层c;在本实施例中,增强件b为玻璃纤维浸渍abs工程塑料形成的玻璃纤维浸渍带,防护层c为asa塑料材料形成的层状物,限位部d为由pvc材料构成;本实施例所述的增强发泡地板中,通过模具控制发泡芯体a竖向截面为长140mm、宽24mm的矩形,其面积为0.336平方分米,在其多个竖向截面上,任意两点之间的最大距离大于0.5mm的空孔的数量最多为4个,其中多数竖向截面上,空孔的数量为1个或0个。
37.参考图2和图3,用于制备上述增强发泡地板的挤出模具,由多块模具板对接而成,其内部贯通的设置有芯体材料流道1
‑
1以及设置于芯体材料流道1
‑
1上下两侧的增强件流道1
‑
2,还设置有限位材料流道1
‑
3,芯体材料流道1
‑
1、增强件流道1
‑
2和限位材料流道1
‑
3相互独立,即其在模具中互不相通,这几个流道的出料口在挤出模具出料板上汇集至一个相对较小的区域,并以形成地板结构雏形的方式出料;其中,芯体材料流道1
‑
1内设置有空心的芯棒,芯棒内部并排设置有多个分隔流道,分隔流道的横截面形状大致为矩形;芯体材料从若干个所述分隔流道的芯体材料挤出口1
‑
1.1中挤出,玻璃纤维浸渍带由增强件流道1
‑
2上扁平的的增强件挤出口1
‑
2.1中挤出,pvc材料由限位材料流道1
‑
3的限位材料挤出段1
‑
3.1中挤出,若干个芯体材料挤出口1
‑
1.1、增强件挤出口1
‑
2.1和限位材料挤出段1
‑
3.1的出口相平齐;在上述若干个流道的出料口上,限位材料挤出段1
‑
3.1的内壁形成截面为圆角矩形的筒状限位型腔,限位材料挤出段1
‑
3.1的外侧壁包覆该限位型腔形成环形的限位材料的部分挤出流道,若干个芯体材料挤出口1
‑
1.1和两个增强件挤出口1
‑
2.1均被限位于该限位型腔内;具体的,两个增强件挤出口1
‑
2.1分别设置于限位型腔内相对的两个内侧壁处,且增强件挤出口1
‑
2.1与限位型腔的内侧壁相邻的设置,被挤出的限位材料pvc能够对限位型腔内的芯体材料进行限位,防止其发泡膨胀过度;相邻的两个芯体材料挤出口1
‑
1.1的连接处设置有排气通道1
‑
4的入口,排气通道1
‑
4的出口设置于挤出模具的侧部,与周围环境大气相连通。
38.在实际的产品质检标准中,要求地板竖向截面的空孔的个数小于4个,而采用本实
施例所述的模具所制备出的增强发泡地板能够满足常用规格地板产品的要求。
39.参考图6,用于制备上述增强发泡地板的设备组,包含有上述挤出模具1,还包含有:芯体材料挤出装置2,用于将芯体的材料挤入挤出模具1的芯体材料流道1
‑
1内;两个增强件材料输送装置3,用于将玻璃纤维浸渍带输送至挤出模具1的增强件流道1
‑
2内;限位材料挤出装置4,用于将pvc材料挤入挤出模具1的限位材料流道1
‑
3内;冷却定型装置5,用于冷却和定型从挤出模具1中挤出的增强发泡地板材料雏形;牵引装置6和切割装置,用于牵引经冷却定型装置5冷却后的增强发泡地板材料并进行切割;具体的,芯体材料挤出装置2和限位材料挤出装置4均为pvc发泡材料挤出机;增强件材料输送装置3为卷轴卷着的玻璃纤维浸渍材料卷材,再将该卷材以牵引装置6提供动力输入至挤出模具1内;冷却定型装置5除冷却外,还包含有对挤出模具1挤出材料的定型模具,定型模具对挤出材料进行限位,防止其发泡后过度膨胀而导致变形;牵引装置6、切割装置乃至牵引切割一体化装置均为本领域常用的设备,在此不予复述。
40.实施例2:参考图1,增强发泡地板,技术特征基本同实施例1,为了方便比较,本实施例的地板外型规格和实施例1所述的地板相同,不同之处在于:本实施例所述的增强发泡地板中,多个竖向截面上,任意两点之间的最大距离大于0.5mm的空孔的数量最多为3个,其中多数竖向截面上,空孔的数量为1个或0个。
41.参考图2~图5,用于制备上述增强发泡地板的挤出模具,技术特征基本同实施例1,不同之处在于:分隔流道在芯体材料的挤出方向上包含有流道逐渐扩张的导向挤出段1
‑
1.2,导向挤出段1
‑
1.2扩张的终点即芯体材料挤出口1
‑
1.1,导向挤出段1
‑
1.2由四个同样形状的导向面1
‑
1.21衔接后包围形成筒状通道;每个导向面1
‑
1.21位于芯体材料挤出口1
‑
1.1的一侧为芯体材料挤出侧,相邻的两个芯体材料挤出口1
‑
1.1的芯体材料挤出侧共线。
42.排气通道1
‑
4的入口设置于相邻两个芯体材料挤出口1
‑
1.1的芯体材料挤出侧的共线处。
43.参考图6,用于制备上述增强发泡地板的设备组,技术特征基本同实施例1,不同之处在于仅在于采用了本实施例所述的挤出模具1。
44.对比例:参考图1,增强发泡地板,技术特征基本同实施例1,为了方便比较,本实施例的地板外型规格和实施例1所述的地板相同,不同之处在于:本实施例所述的增强发泡地板中,多个竖向截面上,任意两点之间的最大距离大于0.5mm的空孔的数量最多可达8个,空孔的数量最多分布在4~6个。
45.参考图2,用于制备对比例增强发泡地板的挤出模具,技术特征基本同实施例1,不同之处在于:芯体材料流道1
‑
1为一整个连续的流道,没有设置有空心的芯棒以及多个并排的
分隔流道。
46.参考图6,用于制备上述增强发泡地板的设备组,技术特征基本同实施例1,不同之处在于仅在于采用了本实施例所述的挤出模具1。
47.为了方便对比,实施例1、实施例2和对比例采用了相同结构和材料制成地板,区别在于采用的挤出模具1的结构不同,进而使得发泡芯体a内的空孔的分布产生差别,然而:本领域技术人员公知,地板的发泡材料不局限于pvc材料,也可以是ps(聚苯乙烯)发泡材料,或者可以是pe(聚乙烯)发泡材料等等,本领域技术人员容易作出选择;同样的,增强件b也可以是玻璃纤维浸渍pp或pe材料所形成的玻璃纤维浸渍带,当增强件b采用玻璃纤维浸渍pp或pe材料所形成的的玻璃纤维浸渍带时,在与pvc发泡材料共挤出时还需在该玻璃纤维浸渍带表面涂覆ps(聚苯乙烯),以使其与pvc发泡材料更好的结合;同样的,在设备组中,还可以包括防护层材料挤出装置7,此时需要在挤出模具1中设置防护层材料挤出通道,防护层材料挤出装置7通常为asa塑料材料挤出机;因此上述实施例不应对权利要求书的保护范围产生限定。
48.实施例1、实施例2和对比例所述的增强发泡地板的性能对比见下表:表 实施例1、实施例2和对比例的地板性能测试参数相对于对比例,实施例1的地板在各项强度参数上均有明显提升,残次品率则从30
±
2%降低至8
±
1%,而相对于实施例1,实施例2的地板在各项强度参数上也均有提升,残次品率则从8
±
1%进一步降低至6
±
1%。
49.实施例1和对比例相比较,地板制备过程中的区别在于:实施例1采用了具备多个分隔流道的芯体材料流道1
‑
1,而对比例并未对芯体材料流道做分隔处理;需要说明的是,上述实施例、对比例所述的挤出模具1,在芯体材料流道1
‑
1中芯层材料不发生发泡或仅发生少量发泡,当各部分物料在出口挤出时,各物料之间并未形成紧密结构,需要在挤出模具1挤出端的冷却装置上接入一个定型模具,刚刚挤出后芯层材料发
生发泡,使发泡芯体a、增强件b和限位部d之间在定型模具内相结合,定型模具的形状根据地板的规格进行设计;实施例1中,芯体材料在多个分隔流道内输送,被挤出时,相邻的芯体材料挤出口1
‑
1.1之间存在间隔,该间隔为挤出的芯体材料提供了发泡空间,使得芯层材料的发泡更加均匀;同时,多个分隔流道,避免了在较大的整个芯体材料流道1
‑
1中因为挤出机进料量的波动而出现内部的空腔或在流动时产生紊流,可以使芯体材料在挤出时更加均匀;进一步的,分隔流道的口径相对较小,可以有效抑制芯体材料在芯体材料流道1
‑
1内的发泡反应,尽可能使使芯体材料从芯体材料挤出口1
‑
1.1出料之后再进行发泡,从而为地板各部分材料之间的结合提供更大的压力,在该压力下,相邻的芯体材料挤出口1
‑
1.1之间的间隔原本存在的空气会通过排气通道1
‑
4排出,尽量减少气泡和气孔的行成。
50.而在对比例中,芯体材料流道1
‑
1未进行分隔,会导致芯体材料流道1
‑
1中间部分的芯层材料发泡变得困难,且芯体材料在芯体材料流道1
‑
1中会因为挤出机进料量的波动而出现内部的空腔或在流动时产生紊流,使得发泡不均匀,更容易产生前述的空孔,而本技术发明人发现,该空孔的数量越多,相应地板的强度下降的就越明显,出现残次品的可能性也越高。
51.实施例2和实施例1相比较,地板制备过程中的区别在于:实施例2所采用的挤出模具1中,分隔流道在芯体材料的挤出方向上包含有流道逐渐扩张的导向挤出段1
‑
1.2,导向挤出段1
‑
1.2由导向面1
‑
1.21构成,每个导向面1
‑
1.21位于芯体材料挤出口1
‑
1.1的一侧为芯体材料挤出侧,相邻的两个芯体材料挤出口1
‑
1.1的芯体材料挤出侧共线。
52.实施例1中,由于相邻的芯体材料挤出口1
‑
1.1之间存在间隔,芯体材料挤出发泡并压合过程中,容易使该间隔中的部分气泡被夹在其中而无法排出,形成地板后会会增加空孔的数量,地板强度无法进一步提升,仍然存在相当的残次品出现概率。
53.在实施例2中,导向挤出段1
‑
1.2使得芯体材料在挤出时有一个渐变(逐渐变大)的挤出空间,该挤出空间除了起到实施例1中所述的“间隔”的作用外,还对芯体材料的发泡过程提供了一个缓冲,在逐渐变大的挤出空间内,芯体材料的发泡变得更加均匀;进一步的,设置导向面1
‑
1.21,并使得相邻的两个芯体材料挤出口1
‑
1.1的芯体材料挤出侧共线;芯体材料被挤出时,导向面1
‑
1.21起着导向的作用,芯体材料沿着导向面1
‑
1.21被挤出并同时进行发泡,每一个分隔流道内,芯体材料边缘处被挤出的终点即芯体材料挤出侧,相邻的两个芯体材料挤出口1
‑
1.1的芯体材料挤出侧共线时,相邻两个芯体材料挤出口1
‑
1.1内被挤出的芯体材料会在该共线处无空隙的汇合,在很大程度上解决了实施例1中所存在的问题;在发泡过程中仍可能会生成多余气体,因此,将排气通道1
‑
4的入口设置于相邻两个芯体材料挤出口1
‑
1.1的芯体材料挤出侧的共线处,能够将这部分气体排出。
54.申请人声明,以上所述仅为本发明的具体实施方式,但本发明的保护范围并不局限于此,所属技术领域的技术人员应该明了,任何属于本技术领域的技术人员在本发明揭露的技术范围内,可轻易想到的变化或替换,均落在本发明的保护范围和公开范围之内。