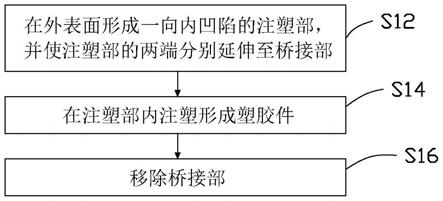
1.本技术涉及金属外壳的制作技术领域,具体涉及一种在金属外壳上注塑成型方法、金属外壳的制作方法及金属外壳。
背景技术:2.随着笔记本电脑的普及,人们对笔记本电脑的诉求越来越高,比如要求笔记本电脑轻薄、耐用、美观大气等。现有笔记本电脑为了适应轻薄以及美观大气的诉求,笔记本电脑的外壳多采用金属外壳。然而,笔记本电脑的外壳若为金属外壳,由于金属件的电磁屏蔽特性对于笔记本电脑的天线的影响非常大,会严重影响笔记本电脑信号的收发,从而导致笔记本电脑内的天线收发信号的能力减弱。为避免金属外壳对天线的屏蔽作用,需要对金属外壳在制作过程中进行改进,即在金属外壳成型后,在金属外壳与天线相对的位置预留通孔,该通孔通过塑胶注入以填充。如此,由于天线对应的位置为塑胶,使得天线收发信号的能力大大增强。
3.然而,在实际作业的过程中,塑胶注入通孔并塑性成型后会因塑性变形而与金属壳体的结合不够紧密,从而导致出现开裂以及表面凹凸不平的缺陷。
技术实现要素:4.鉴于以上内容,有必要提出一种在金属外壳上注塑成型方法、金属外壳的制作方法及金属外壳,以解决上述问题。
5.本技术一实施例提供一种在金属外壳上注塑成型方法,所述金属外壳具有相对设置的外表面及内表面,所述金属外壳的周侧具有折边以及凸伸于所述折边的两个桥接部,两个所述桥接部分别位于所述金属外壳的不同侧边;
6.所述注塑成型方法,包括:
7.在所述外表面形成一向内凹陷的注塑部,并使所述注塑部的两端分别延伸至所述桥接部;
8.在所述注塑部内注塑形成塑胶件;
9.移除所述桥接部。
10.在一些实施例中,所述注塑部包括第一沉槽以及位于所述第一沉槽两侧的第二沉槽,所述第一沉槽与所述第二沉槽之间具有贯穿所述外表面和所述内表面的第一通槽,所述第二沉槽与所述桥接部之间具有贯穿所述外表面和所述内表面的第二通槽。
11.在一些实施例中,所述第一沉槽的底部与所述内表面之间形成第一连接件,所述第二沉槽的底部与所述内表面之间形成第二连接件,所述第一连接件的两侧为曲面,所述第二连接件的两侧为曲面。
12.在一些实施例中,所述第二通槽内设置有嵌件,沿垂直于所述外表面的方向,所述嵌件靠近所述外表面的一端与靠近所述内表面的一端之间的距离小于所述外表面与所述内表面之间的距离。
13.在一些实施例中,所述塑胶件包括容置于所述注塑部内的第一塑胶件以及间隔设置于所述内表面的两个第二塑胶件,所述第一塑胶件与两个所述第二塑胶件连接,所述第二塑胶件在所述外表面上的垂直投影宽度大于所述第一塑胶件在所述外表面上的垂直投影宽度,所述第二塑胶件在所述外表面上的垂直投影与所述第一沉槽在所述外表面上的垂直投影存在部分重叠。
14.在一些实施例中,所述桥接部在所述外表面上的垂直投影宽度大于所述注塑部在所述外表面上的垂直投影宽度。
15.本技术的一实施例还提供一种金属外壳的制作方法,包括:
16.形成一金属坯体;
17.加工所述金属坯体以形成具有折边以及凸伸于所述折边的两个桥接部的金属外壳;
18.实施如上所述的在金属外壳上注塑成型方法;
19.对所述金属外壳进行精加工处理。
20.本技术的一实施例还提供一种金属外壳,用于与塑胶一体成型,
21.所述金属外壳在一预定位置形成有供所述塑胶注入的注塑部,
22.所述金属外壳的周侧具有折边以及凸伸于所述折边的两个桥接部,两个所述桥接部分别位于所述金属外壳的不同侧边,所述注塑部的两端分别延伸至所述桥接部,所述桥接部用于保持注入所述注塑部的塑胶并能够在所述塑胶成型后被移除。
23.在一些实施例中,所述注塑部包括第一沉槽以及位于所述第一沉槽两侧的第二沉槽,所述第一沉槽与所述第二沉槽之间具有贯穿所述外表面和所述内表面的第一通槽,所述第二沉槽与所述桥接部之间具有贯穿所述外表面和所述内表面的第二通槽。
24.在一些实施例中,所述塑胶件包括容置于所述注塑部内的第一塑胶件以及间隔设置于所述内表面的两个第二塑胶件,所述第一塑胶件与两个所述第二塑胶件连接,所述第二塑胶件在所述外表面上的垂直投影宽度大于所述第一塑胶件在所述外表面上的垂直投影宽度,所述第二塑胶件在所述外表面上的垂直投影与所述第一沉槽在所述外表面上的垂直投影存在部分重叠。
25.上述在金属外壳上注塑成型方法、金属外壳的制作方法及金属外壳,通过在金属外壳的折边设置凸伸的桥接部,桥接部可被移除,金属外壳在注塑时,桥接部具有保持塑胶以防止塑胶变形的作用,使得注入注塑部内的塑胶能够与金属外壳紧密结合,并使得塑胶的塑性变形较小、表面质量较好。所形成的塑胶件中基本不包含影响笔记本电脑天线信号收发的金属材料,也无需对塑胶件进行二次处理。由于桥接部为凸伸于折边设置,可通过简单的铣削、切割等处理方式实现桥接部的移除,桥接部的移除方式简单,不会损坏已经成型的塑胶件,有利于保持金属外壳的美观性。
附图说明
26.图1是本技术一实施例提出的注塑成型方法的流程示意图。
27.图2是本技术一实施例提出的金属外壳注入塑胶前的结构示意图。
28.图3是本技术一实施例提出的金属外壳注入塑胶前的又一角度结构示意图。
29.图4是本技术一实施例提出的金属外壳注入塑胶后的结构示意图。
30.图5是本技术一实施例提出的金属外壳注入塑胶后的又一角度结构示意图。
31.图6是图4所示的塑胶成型为塑胶件的结构示意图。
32.图7是本技术一实施例提出的金属外壳移除桥接部后的结构示意图。
33.图8是本技术一实施例提出的金属外壳的制作方法的流程示意图。
34.主要元件符号说明
35.金属外壳
ꢀꢀꢀꢀꢀꢀꢀꢀꢀꢀꢀꢀꢀꢀꢀꢀꢀꢀꢀ
100
36.折边
ꢀꢀꢀꢀꢀꢀꢀꢀꢀꢀꢀꢀꢀꢀꢀꢀꢀꢀꢀꢀꢀꢀꢀ
10
37.桥接部
ꢀꢀꢀꢀꢀꢀꢀꢀꢀꢀꢀꢀꢀꢀꢀꢀꢀꢀꢀꢀꢀ
12
38.外表面
ꢀꢀꢀꢀꢀꢀꢀꢀꢀꢀꢀꢀꢀꢀꢀꢀꢀꢀꢀꢀꢀ
20
39.内表面
ꢀꢀꢀꢀꢀꢀꢀꢀꢀꢀꢀꢀꢀꢀꢀꢀꢀꢀꢀꢀꢀ
30
40.注塑部
ꢀꢀꢀꢀꢀꢀꢀꢀꢀꢀꢀꢀꢀꢀꢀꢀꢀꢀꢀꢀꢀ
40
41.第一沉槽
ꢀꢀꢀꢀꢀꢀꢀꢀꢀꢀꢀꢀꢀꢀꢀꢀꢀꢀꢀ
42
42.第二沉槽
ꢀꢀꢀꢀꢀꢀꢀꢀꢀꢀꢀꢀꢀꢀꢀꢀꢀꢀꢀ
44
43.第一通槽
ꢀꢀꢀꢀꢀꢀꢀꢀꢀꢀꢀꢀꢀꢀꢀꢀꢀꢀꢀꢀꢀ
46
44.第二通槽
ꢀꢀꢀꢀꢀꢀꢀꢀꢀꢀꢀꢀꢀꢀꢀꢀꢀꢀꢀꢀꢀ
48
45.塑胶件
ꢀꢀꢀꢀꢀꢀꢀꢀꢀꢀꢀꢀꢀꢀꢀꢀꢀꢀꢀꢀꢀꢀꢀ
50
46.第一塑胶件
ꢀꢀꢀꢀꢀꢀꢀꢀꢀꢀꢀꢀꢀꢀꢀꢀꢀꢀꢀ
52
47.第二塑胶件
ꢀꢀꢀꢀꢀꢀꢀꢀꢀꢀꢀꢀꢀꢀꢀꢀꢀꢀꢀ
54
48.通孔
ꢀꢀꢀꢀꢀꢀꢀꢀꢀꢀꢀꢀꢀꢀꢀꢀꢀꢀꢀꢀꢀꢀꢀꢀꢀ
56
49.第一连接件
ꢀꢀꢀꢀꢀꢀꢀꢀꢀꢀꢀꢀꢀꢀꢀꢀꢀꢀꢀ
60
50.第二连接件
ꢀꢀꢀꢀꢀꢀꢀꢀꢀꢀꢀꢀꢀꢀꢀꢀꢀꢀꢀ
70
51.嵌件
ꢀꢀꢀꢀꢀꢀꢀꢀꢀꢀꢀꢀꢀꢀꢀꢀꢀꢀꢀꢀꢀꢀꢀꢀꢀ
80
52.转轴部
ꢀꢀꢀꢀꢀꢀꢀꢀꢀꢀꢀꢀꢀꢀꢀꢀꢀꢀꢀꢀꢀꢀꢀ
90
具体实施方式
53.下面详细描述本技术的实施方式,所述实施方式的示例在附图中示出,其中自始至终相同或类似的标号表示相同或类似的元件或具有相同或类似功能的元件。下面通过参考附图描述的实施方式是示例性的,仅用于解释本技术,而不能理解为对本技术的限制。
54.在本技术的描述中,需要理解的是,术语“中心”、“纵向”、“横向”、“长度”、“宽度”、“厚度”、“上”、“下”、“前”、“后”、“左”、“右”、“竖直”、“水平”、“顶”、“底”、“内”、“外”、“顺时针”、“逆时针”等指示的方位或位置关系为基于附图所示的方位或位置关系,仅是为了便于描述本技术和简化描述,而不是指示或暗示所指的装置或元件必须具有特定的方位、以特定的方位构造和操作,因此不能理解为对本技术的限制。此外,术语“第一”、“第二”仅用于描述目的,而不能理解为指示或暗示相对重要性或者隐含指明所指示的技术特征的数量。由此,限定有“第一”、“第二”的特征可以明示或者隐含地包括一个或者更多个所述特征。在本技术的描述中,需要说明的是,“多个”的含义是两个或两个以上,除非另有明确具体的限定。
55.在本技术的描述中,需要说明的是,除非另有明确的规定和限定,术语“安装”、“相连”、“连接”应做广义理解,例如,可以是固定连接,也可以是可拆卸连接,或一体地连接;可
以是机械连接,也可以是电连接或可以相互通讯,可以是直接相连,也可以通过中间媒介间接相连,可以是两个元件内部的连通或两个元件的相互作用关系。对于本领域的普通技术人员而言,可以根据具体情况理解上述术语在本技术中的具体含义。
56.在本技术中,除非另有明确的规定和限定,第一特征在第二特征之“上”或之“下”可以包括第一特征和第二特征直接接触,也可以包括第一特征和第二特征不是直接接触而是通过它们之间的另外的特征接触。而且,第一特征在第二特征“之上”、“上方”和“上面”包括第一特征在第二特征正上方和斜上方,或仅仅表示第一特征水平高度高于第二特征。第一特征在第二特征“之下”、“下方”和“下面”包括第一特征在第二特征正下方和斜下方,或仅仅表示第一特征水平高度小于第二特征。
57.下文的公开提供了许多不同的实施方式或例子用来实现本技术的不同结构。为了简化本技术的公开,下文中对特定例子的部件和设置进行描述。当然,它们仅仅为示例,并且目的不在于限制本技术。此外,本技术可以在不同例子中重复参考数字和/或参考字母,这种重复是为了简化和清楚的目的,其本身不指示所讨论各种实施方式和/或设置之间的关系。
58.请参见图1,本技术一实施例提供了一种在金属外壳上注塑成型方法的流程示意图,通过该方法能够减小塑胶(图未示)注塑后的塑性变形,进而增强塑胶与金属外壳的结合能力。
59.其中,塑胶可以为聚对苯二甲酸丁二醇酯(pbt,polybutylene terephthalate)和玻璃纤维(gf,glass fiber)的混合物。本实施例中,塑胶为60%的pbt和40%的gf混合材料。
60.可以理解地,在其他的实施例中,塑胶中pbt和gf的比例还可以为其他比例。塑胶还可以为聚苯硫醚(pps,polyphenylene sulfide)、聚酰胺(pa,polyamide)中的一者或二者的混合物。
61.请一并参见图2和图3,金属外壳100具有相对设置的外表面20及内表面30,金属外壳100的周侧具有折边10以及凸伸于折边10的两个桥接部12,两个桥接部12分别位于金属外壳100的不同侧边。
62.本实施例中,金属外壳100大致为矩形,两个桥接部12分别位于金属外壳100上相对的两个侧边上,两个桥接部12之间的连线靠近金属外壳100的上边沿且与金属外壳100的上边沿相平行。两个桥接部12所形成的闭合区域也可以理解为与笔记本电脑天线相对应的位置。
63.为了便于说明,本技术定义金属外壳100的长度方向/上边沿的延伸方向/下边沿的延伸方向为如图2所示的x轴方向,金属外壳100的宽度方向/左边沿的延伸方向/右边沿的延伸方向为如图2所示的z轴方向。侧边是指上边沿、下边沿、左边沿或右边沿。
64.可以理解地,在其他的实施例中,两个桥接部12还可以分别位于金属外壳100上相邻的两个侧边上;或者,两个桥接部12分别位于金属外壳100上相对的两个侧边上,然而两个桥接部12之间的连线与金属外壳100的上边沿或者左/右边沿不平行。本技术中,两个桥接部12的设置位置可以根据笔记本电脑天线的位置相应设置。
65.请继续参见图1,根据不同的需求,该流程图中的某些步骤可以省略。为了便于说明,仅示出了与本技术实施例相关的部分。在金属外壳100上注塑成型方法包括如下步骤。
66.步骤s12:在外表面20形成一向内凹陷的注塑部40,并使注塑部40的两端分别延伸至桥接部12。
67.具体地,可通过铣削加工处理在外表面20形成向内凹陷的注塑部40。也可以理解为,在外表面20形成一向内表面30凹陷的注塑部40,或者,在外表面20向内表面30加工形成一注塑部40。
68.本实施例中,金属外壳100的材质可以为铝合金、镁铝合金或其他适用于做笔记本电脑外壳的金属材质。然而,由于金属外壳100对笔记本电脑的天线具有信号屏蔽的作用,因此需要在与天线所对应的金属外壳100的位置设置塑胶以减少金属外壳100对天线的信号的屏蔽作用,从而增强天线的信号收发能力。
69.桥接部12可以为矩形、圆形、椭圆形或其他形状。沿如图2所示的y轴方向,桥接部12在外表面20上的垂直投影宽度大于注塑部40在外表面20上的垂直投影宽度。如此,桥接部12可保持注入注塑部40内的塑胶位于注塑部40内。其中,“宽度”是指垂直投影沿如图2所示的z轴方向的宽度。
70.在一实施方式中,沿如图2所示的x轴方向,注塑部40包括第一沉槽42以及位于第一沉槽42两侧的第二沉槽44,第一沉槽42与第二沉槽44之间具有贯穿外表面20和内表面30的第一通槽46,第二沉槽44与桥接部12之间具有贯穿外表面20和内表面30的第二通槽48,第二通槽48弯折延伸至桥接部12。可以理解为,沿如图2所示的x轴方向,注塑部40依次由第二通槽48、第二沉槽44、第一通槽46、第一沉槽42、第一通槽46、第二沉槽44、第二通槽48所组成。
71.可以理解地,在其他的实施方式中,注塑部40还可以包括更多或更少个沉槽,还可以包括更多或更少个通槽。然而,注塑部40中都应该包括至少一沉槽和至少一通槽,其中,沉槽用于增强金属外壳100在注塑时的结构强度,通槽用于增强塑胶与金属外壳100的结合能力。
72.第一沉槽42的底部与内表面30之间形成第一连接件60,第二沉槽44的底部与内表面30之间形成第二连接件70。如此,通过第一连接件60和第二连接件70,能够增强金属外壳100在铣削加工注塑部40后的结构强度,避免金属外壳100因出现注塑部40而使得强度减弱,进而导致金属外壳100在注塑时发生形变,从而导致塑胶不能够与金属外壳100紧密结合,减弱塑胶与金属外壳100的结合能力。
73.第一连接件60大致位于注塑部40的中间位置,第一连接件60靠近内表面30的一侧表面与内表面30位于同一平面;两个第二连接件70分别大致位于靠近桥接部12的一侧,第二连接件70靠近内表面30的一侧与内表面30不位于同一平面。如此,通过合理的设置第一连接件60和第二连接件70的位置,使得金属外壳100的结构强度得以保持,同时使得塑胶在注入后能够至少包裹住第二连接件70。
74.第一连接件60的两侧为曲面,第二连接件70的两侧也为曲面。第一连接件60的两侧优选为圆弧面,第二连接件70的两侧优选为圆弧面。如此,通过设置曲面,有利于增加塑胶与第一连接件60及第二连接件70之间的结合能力。
75.可以理解地,在其他的实施方式中,第一连接件60的两侧还可以为波浪面或其他曲面,第二连接件70的两侧还可以为波浪面或其他曲面。
76.本实施例中,两个第二通槽48内均设置有嵌件80。沿垂直于外表面20的方向,即如
图2所示的y轴方向,嵌件80靠近外表面20的一端与靠近内表面30的一端之间的距离小于外表面20与内表面30之间的距离。如此,通过嵌件80进一步增强金属外壳100在铣削加工注塑部40后的结构强度。同时,嵌件80通过满足上述要求,嵌件80不会凸伸于注塑部40,嵌件80能够被包裹在塑胶内;同时,通过嵌件80,金属外壳100还能够与外部结构或元件进行连接。
77.在一实施方式中,嵌件80大致为薄片结构,嵌件80的两端分别与注塑部40所对应的金属外壳100的表面连接。
78.可以理解地,在其他的实施方式中,嵌件80还可以杆状或其他结构。
79.可以理解地,在其他的实施例中,步骤s1可以省略,即在形成金属外壳100时,将注塑部40一并加工形成。如此,可省略步骤s12。
80.步骤s14:在注塑部40内注塑形成塑胶件。
81.具体地,对注塑部40进行注塑以在注塑部40内形成塑胶件。将一注塑模具(图未示)设置于金属外壳100的注塑部40,通过注塑模具的注塑口(图未示)对注塑部40注入塑胶,并使塑胶塑性成型以在注塑部40内形成塑胶件,注塑成型后,拆除注塑模具。
82.请一并参见图4、图5和图6,与注塑部40相对应地,在注塑部40内所形成的塑胶件50包括容置于注塑部40内的第一塑胶件52以及间隔设置于内表面30的两个第二塑胶件54,第一塑胶件52与两个第二塑胶件54一体成型。
83.第二塑胶件54在外表面20上的垂直投影宽度大于第一塑胶件52在外表面20上的垂直投影宽度。可以理解为,沿如图4所示的z轴方向,第一塑胶件52的宽度与注塑部40的宽度相同,第二塑胶件54的宽度大于第一塑胶件52和注塑部40的宽度。
84.第二塑胶件54在外表面20上的垂直投影与第一沉槽42在外表面20上的垂直投影存在部分重叠。可以理解为,沿如图4所示的x轴方向,每个第二塑胶件54远离桥接部12的一端与第一连接件60之间存在重叠。
85.如此,第一塑胶件52和第二塑胶件54通过满足上述条件,使得塑胶所形成的塑胶件50能够完全包裹住第一连接件60、第二连接件70及嵌件80,增强塑胶件50与金属外壳100的结合能力。
86.第一塑胶件52上具有因第二连接件70和嵌件80所形成的通孔56,即第二连接件70和嵌件80被包裹在第一塑胶件52的通孔56内。
87.本实施例中,对注塑部40进行注塑之前,还可以对金属外壳100上的第一连接件60、第二连接件70及注塑部40所对应的金属外壳100的表面进行t处理以形成微孔洞,从而增加塑胶所形成的塑胶件50与金属外壳100的结合强度。
88.具体地,t处理的流程大致为:脱脂处理,去除第一连接件60、第二连接件70及注塑部40所对应的金属外壳100的表面的油污;清洗,对第一连接件60、第二连接件70及注塑部40所对应的金属外壳100的表面进行清洗,由于金属容易与强碱发生化学反应,所以在脱脂处理后应该立即转入清洗;酸洗,通过酸液在第一连接件60、第二连接件70及注塑部40所对应的金属外壳100的表面进行蚀洞;t剂刻蚀,在第一连接件60、第二连接件70及注塑部40所对应的金属外壳100的表面通过t剂刻蚀形成更小的纳米孔。t处理后在第一连接件60、第二连接件70及注塑部40所对应的金属外壳100的表面形成20nm
‑
40nm的微孔和50nm
‑
80nm的晶粒突出,有利于增强塑胶所形成的塑胶件50与金属外壳100的结合能力。
89.步骤s16:移除桥接部12。
90.具体地,由于桥接部12为凸伸于折边10设置,可通过简单的铣削、切割等处理方式对桥接部12进行处理,从而移除桥接部12。如此,桥接部12的移除方式简单,不会损坏已经成型的塑胶件50,有利于保持金属外壳100注塑成型后的美观性。
91.请参见图7,移除桥接部12后,塑胶件50位于桥接部12的表面裸露出来。
92.请参见图8,本技术的一实施例还提供一种金属外壳的制作方法的流程示意图。根据不同的需求,该流程图中步骤的顺序可以改变,某些步骤可以省略。为了便于说明,仅示出了与本技术实施例相关的部分。金属外壳100的制作方法包括如下步骤。
93.步骤s22:形成一金属坯体(图未示)。
94.具体地,将延展性良好的金属材料利用冲压、挤压以及模具形成金属坯体,将金属坯体冷却并去除应力后以待进行后续工序。
95.步骤s24:加工金属坯体以形成具有折边10以及凸伸于折边10的两个桥接部12的金属外壳100。
96.具体地,利用计算机数控(cnc,computerized numerical control)机床对金属坯体进行加工,在金属坯体一侧形成可安装笔记本转轴的转轴部90,并在金属坯体的周侧形成折边10。在其中相对的两个侧边的折边10上形成桥接部12,桥接部12凸伸于折边10设置。还可以利用铣床对金属坯体进行铣削加工,使金属坯体满足尺寸、表面、质量要求。还可以利用钻床对金属坯体进行钻孔,以形成安装所需的螺纹孔等孔洞。
97.步骤s26:实施上述的在金属外壳100上注塑成型方法。
98.具体地,在金属外壳100上注入塑胶以形成塑胶件50。其中,塑胶件50与笔记本电脑上天线的位置相对应,避免金属外壳100影响笔记本电脑天线的信号收发能力。
99.步骤s28:对金属外壳100进行精加工处理。
100.具体地,经过cnc加工、铣削加工、钻床加工后的金属外壳100通常会产生飞边和毛刺等缺陷,注塑后的金属外壳100需要打磨以去除这些缺陷。另外,金属外壳100的表面质量不良,还可以通过磨削处理以提高金属外壳100的表面质量。
101.对金属外壳100进行精加工处理还包括倒角处理、抛光处理、拉丝处理、喷砂处理、阳极氧化处理中的至少一种。例如,可以对注塑后的金属外壳100依次进行抛光处理、拉丝处理、倒角处理、喷砂处理和阳极氧化处理。
102.可以理解地,在其他的实施例中,还可以对金属外壳100进行其他的精加工处理。
103.上述在金属外壳100上注塑成型的方向以及金属外壳100的制作方法,通过在金属外壳100的折边10设置凸伸的桥接部12,桥接部12可被移除,金属外壳100在注塑时,桥接部12具有保持塑胶以防止塑胶变形的作用,使得注入注塑部40内的塑胶能够与金属外壳100紧密结合,并使得塑胶的塑性变形较小、表面质量较好。所形成的塑胶件50中基本不包含影响笔记本电脑天线信号收发的金属材料,也无需对塑胶件50进行二次处理。由于桥接部12为凸伸于折边10设置,可通过简单的铣削、切割等处理方式实现桥接部12的移除,桥接部12的移除方式简单,不会损坏已经成型的塑胶件50,有利于保持金属外壳100的美观性。
104.本技术的一实施例还提供一种金属外壳,该金属外壳100用于与塑胶一体成型。请参见图2和图7,图2为金属外壳100将要与塑胶一体成型的中间产品,图7为金属外壳100与塑胶一体成型的最终产品。金属外壳100在一预定位置形成有供塑胶注入的注塑部40,金属外壳100的周侧具有折边10以及凸伸于折边10的两个桥接部12,两个桥接部12分别位于金
属外壳100的不同侧边,注塑部40的两端分别延伸至桥接部12,桥接部12用于保持注入注塑部40的塑胶并能够在塑胶成型后被移除。
105.本实施例中,“预定位置”是指与笔记本电脑天线对应的位置。
106.可以理解地,在其他的实施例中,“预定位置”还可以为与电子设备中安装收发信号元件相对应的位置。
107.在一实施方式中,注塑部40包括第一沉槽42以及位于第一沉槽42两侧的第二沉槽44,第一沉槽42与第二沉槽44之间具有贯穿外表面20和内表面30的第一通槽46,第二沉槽44与桥接部12之间具有贯穿外表面20和内表面30的第二通槽48。
108.与注塑部40相对应的,在注塑部40内形成的塑胶件50包括容置于注塑部40内的第一塑胶件52以及间隔设置于内表面30的两个第二塑胶件54,第一塑胶件52与两个第二塑胶件54一体成型,第二塑胶件54在外表面20上的垂直投影宽度大于第一塑胶件52在外表面20上的垂直投影宽度,第二塑胶件54在外表面20上的垂直投影宽度与第一沉槽42在外表面20上的垂直投影存在部分重叠。
109.上述金属外壳100,通过在金属外壳100的折边10设置凸伸的桥接部12,桥接部12可被移除,金属外壳100在注塑时,桥接部12具有保持塑胶以防止塑胶变形的作用,使得注入注塑部40内的塑胶能够与金属外壳100紧密结合,并使得塑胶的塑性变形较小、表面质量较好。所形成的塑胶件50中基本不包含影响笔记本电脑天线信号收发的金属材料,也无需对塑胶件50进行二次处理。由于桥接部12为凸伸于折边10设置,可通过简单的铣削、切割等处理方式实现桥接部12的移除,桥接部12的移除方式简单,不会损坏已经成型的塑胶件50,有利于保持金属外壳100的美观性。
110.对于本领域技术人员而言,显然本技术不限于上述示范性实施例的细节,而且在不背离本技术的精神或基本特征的情况下,能够以其他的具体形式实现本技术。因此,无论从哪一点来看,均应将实施例看作是示范性的,而且是非限制性的,本技术的范围由所附权利要求而不是上述说明限定,因此旨在将落在权利要求的等同要件的含义和范围内的所有变化涵括在本技术内。
111.最后应说明的是,以上实施例仅用以说明本技术的技术方案而非限制,尽管参照较佳实施例对本技术进行了详细说明,本领域的普通技术人员应当理解,可以对本技术的技术方案进行修改或等同替换,而不脱离本技术技术方案的精神和范围。