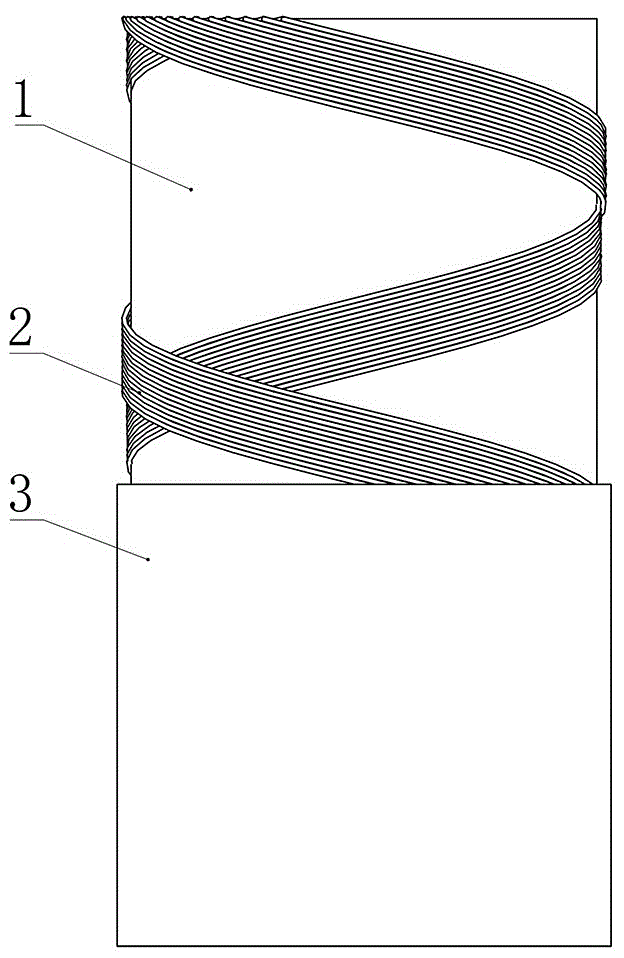
本发明涉及一种大口径高压柔性复合管用绕线及其使用方法,属于管输领域,尤其涉及纤维增强热塑性管道领域。
背景技术:
增强柔性复合管(reinforcedthermoplasticpipes,简称rtp管),是一种高压塑料复合管道,具有良好的柔韧性、抗腐蚀性、耐高压、耐冲击、耐磨损、重量轻、容易连接、可盘绕、长距离无接头快速铺设等特点,可以很好地克服钢管的腐蚀问题以及塑料管道的耐压问题,可应用在石油、天然气开采,高压长距离输送天然气以及各种需要较高压力输送介质的管线领域。
rtp产品通常由三层构成,内、外层为pe80、pe100以上材料,外层根据需要可选白色(地表铺设防紫外线)或黑色(埋地铺设);中间层为增强材料复合而成的增强带,增强材料可以为芳纶纤维、聚酯纤维或玻璃纤维等高强纤维。
现有的技术方案将各类纤维作为增强层以提高管道承压能力,已经具有较多成熟产品。syt6662.2-2012《石油天然气工业用非金属复合管第2部分:柔性复合高压输送管》所述,目前通用柔性复合管道最大内径150mm,公称压力6.4mpa/2.5mpa;内径90mm以下柔性复合管道公称压力最高达到12mpa。部分企业能够加工口径超过1m的柔性复合管道,但是承压能力较低,主要用于低压输水。
21世纪以来,管输行业大力推进“以塑代钢”战略发展方案,柔性复合管道以其优异的性能被列为重点发展方向,并向着高压力、大口径发展。油气输送领域,管道压力高,同时对大口径有着明确需求。目前长输管道主要采用钢制管道,最大口径达到1216mm,公称压力超过10mpa;现有柔性复合管压力和口径远远达不到同类钢制管道标准。
单纯增加增强层缠绕层数、厚度的方式,难以有效提高管道承压能力,不满足油气输送管道高压力、大口径的需要。主要在于:各类纤维强度高但韧性差,缠绕预紧力难以精确调节,必然造成内层纤维受力大,外层纤维受力小。柔性复合管道高压承载,通常内层纤维优先破坏,然后管道强度整体不足导致失效。
基于上述背景,研制新型柔性复合管用绕线及其使用方法,满足大口径、高压力需求,具有现实意义。
技术实现要素:
本发明的目的:为了克服现有纤维增强柔性复合管承压能力低,难以加工成大口径、高压力管道;从根本上解决柔性复合管道多层纤维受力不均匀的问题,以此提升纤维增强柔性复合管承压能力。
为达到上述目的,本发明采取的技术方案如下。
一种大口径高压柔性复合管用绕线,包括内芯、纤维束,其特征在于:内芯包含可挤压变形的柔性材料,内芯为线状物体;纤维束包含至少1根有机柔性纤维或无机柔性纤维,纤维束单向螺旋缠绕到内芯上。
内芯表面或内部设置沿内芯轴向布置的纵向纤维,或者内芯表面和内部同时设置沿内芯轴向布置的纵向纤维。
内芯为实心结构或者为中空管状结构。
纤维束缠绕方向与内芯轴线夹角范围为20°~80°。
纤维束与内芯体积比的取值范围为0.04:1~4:1。
纤维束选自碳纤维、碳化硅纤维、硼纤维、氮化硼纤维、玄武岩纤维、玻璃纤维、芳纶纤维、聚酯纤维、聚乙烯纤维、钢丝中的一种或多种的混合物。
内芯选自橡胶、聚乙烯、尼龙、聚偏二氟乙烯、聚苯硫醚、聚醚醚酮、聚醚酮酮或发泡聚乙烯中的一种或几种的混合物。
一种大口径高压柔性复合管用绕线使用方法,其特征在于:绕线螺旋缠绕到内衬层上,形成多层结构的增强层;所述增强层的相邻层之间,绕线缠绕方向相反;增强层的相邻层之间纤维束与内芯的缠绕方向相反,或者增强层的同一层内,采用纤维束与内芯缠绕方向相反的绕线并排布置。
绕线缠绕方向与管道轴线夹角范围为40°~70°,从增强层的内层向外层该夹角逐渐降低,或者逐渐增加,或者不变。
纤维束捻度从增强层的内层向外层逐渐降低,或者逐渐增加,或者不变。
纤维束缠绕方向与内芯轴线的夹角,从增强层的内层向外层逐渐降低,或者逐渐增加,或者不变。
纤维束与内芯体积比的取值,从增强层的内层向外层逐渐增加,或者逐渐降低,或者不变。
增强层的单一层中,至少2根绕线并排且添加粘结剂组成绕带。
通过缠绕或者挤塑方式,在增强层外设置保护层,所述保护层选自聚乙烯、尼龙、聚偏二氟乙烯、聚苯硫醚、聚醚醚酮、聚醚酮酮或发泡聚乙烯中的一种或几种的混合物;所述内衬层选自聚乙烯、尼龙、聚偏二氟乙烯、聚苯硫醚、聚醚醚酮、聚醚酮酮或发泡聚乙烯中的一种或几种的混合物。
所述绕线缠绕形成增强层后,用常规柔性纤维在所述增强层外侧缠绕形成多层结构,所述常规柔性纤维选自碳纤维、碳化硅纤维、硼纤维、氮化硼纤维、玄武岩纤维、玻璃纤维、芳纶纤维、聚酯纤维、聚乙烯纤维、钢丝中的一种或多种的混合物。
本发明具有的有益效果是:(1)本发明所述绕线及其使用方法,对缠绕预紧力不敏感,避免纤维缠绕预紧力变化对管道承压能力的影响,便于纤维增强柔性复合管道加工;(2)本发明通过多种途径调整所述绕线的结构特征,能够满足多层绕线同等受力的需求,从根本上解决了现有纤维缠绕造成内层受力大、外层受力小的问题;(3)通过本发明所述技术方案,能够将所述绕线加工成大口径、高压力柔性复合管道,满足油气管输及其他应用场合的需要。
附图说明
图1为纤维增强柔性复合管道结构简图。
图2为纤维增强柔性复合管道壁厚截面图。
图3为本发明所述绕线结构简图。
图4为本发明所述绕线的横截面示意图。
图中:1.内衬层;2.增强层;3.保护层;4.绕线;41.内芯;42.纵向纤维;43.纤维束。
具体实施方式
本发明不受下述实施实例的限制,可以根据本发明的技术方案和实际情况来确定具体的实施方式。上、下、左、右、前、后、内、外等位置关系是依据说明书附图1和图4的布局方向来确定的。
一种大口径高压柔性复合管用绕线,包括内芯41、纤维束43,其特征在于:内芯41包含可挤压变形的柔性材料,内芯41为线状物体;纤维束43包含至少1根有机柔性纤维或无机柔性纤维,纤维束43单向螺旋缠绕到内芯41上。内芯41挤压变形,其外侧单向缠绕的纤维束43在一定程度上松弛,以便将管道内压力传递到外层绕线4。绕线4的纤维束43正反两种缠绕方式,以便根据不同需要进行配合使用,最终降低多层纤维束43之间的切应力,并且使得各层绕线4受力更加均衡。
内芯41表面或内部设置沿内芯41轴向布置的纵向纤维42,或者内芯41表面和内部同时设置沿内芯41轴向布置的纵向纤维42。这样有效避免了内芯41强度不足,导致绕线4缠绕到管道上不能施加预紧力的问题。
内芯41为实心结构或者为中空管状结构。内芯41能够受到挤压变形,为进一步提升其变形能力,将内芯41设置为中空管状结构,以适应各类绕线4缠绕工况。
纤维束43缠绕方向与内芯41轴线夹角范围为20°~80°。该角度直接影响纤维束43的松紧程度,角度越大,内芯41挤压变形后纤维束43越松弛。根据不同管径、压力的纤维增强复合管道需要,该取值进行合理变化,且变化范围为20°~80°。
纤维束43与内芯41体积比的取值范围为0.04:1~4:1。该比值直接影响受挤压后纤维束43的松紧程度,纤维束43占比越小,内芯41挤压变形后纤维束43越松弛。根据不同管径、压力的纤维增强复合管道需要,该取值进行合理变化,且变化范围为0.04:1~4:1。
纤维束43选自碳纤维、碳化硅纤维、硼纤维、氮化硼纤维、玄武岩纤维、玻璃纤维、芳纶纤维、聚酯纤维、聚乙烯纤维、钢丝中的一种或多种的混合物。根据纤维增强柔性复合管道制造需要,选用合适的高强度纤维。
内芯41选自橡胶、聚乙烯、尼龙、聚偏二氟乙烯、聚苯硫醚、聚醚醚酮、聚醚酮酮或发泡聚乙烯中的一种或几种的混合物。根据纤维增强柔性复合管道制造需要,选用合适的内芯41材料,以适应复合管道不同缠绕层对纤维束43松紧程度的需要。
对于上述一种大口径高压柔性复合管用绕线4,采用如下方式加工成柔性复合管道。
一种大口径高压柔性复合管用绕线使用方法,其特征在于:绕线4螺旋缠绕到内衬层1上,形成多层结构的增强层2;所述增强层2的相邻层之间,绕线4缠绕方向相反;增强层2的相邻层之间纤维束43与内芯41的缠绕方向相反,或者增强层2的同一层内,采用纤维束43与内芯41缠绕方向相反的绕线4并排布置。这样将纤维束43正反缠绕的两种绕线4组合使用,绕线4受力更加均衡,降低层间切应力,降低同层中绕线4之间的作用力。
绕线4缠绕方向与管道轴线夹角范围为40°~70°,从增强层2的内层向外层该夹角逐渐降低,或者逐渐增加,或者不变。该角度直接影响绕线4承压后的松紧程度,角度越大,承压后自由变形空间越大,绕线4越松弛,有利于将管道内牙传递到外层绕线4。一般情况下,设置该夹角从增强层2的内层向外层该夹角逐渐降低,以便内层绕线4变形大,能够将压力逐层传递到外层,使得多层绕线4均匀受力。但是,在其他因素影响下,以及绕线4缠绕不同工艺参数组合情况下,存在需要将该角度从增强层2的内层向外层逐渐降低、或者逐渐增加、或者不变3种不同情况,进一步拓展了所述绕线4的使用范围。
纤维束43捻度从增强层2的内层向外层逐渐降低,或者逐渐增加,或者不变。纤维束43捻度增加有利于纤维束43抗疲劳、抵抗局部纤维断裂造成的影响;但是捻度过大,容易造成纤维受拉力后纤维之间切应力增大。在其他因素影响下,以及绕线4缠绕不同工艺参数组合情况下,存在需要将纤维束43捻度从增强层2的内层向外层逐渐降低、或者逐渐增加、或者不变3种不同情况,进一步拓展了所述绕线4的使用范围。
纤维束43缠绕方向与内芯41轴线的夹角,从增强层2的内层向外层逐渐降低,或者逐渐增加,或者不变。该夹角取值越大,绕线4受压后变形程度越大。通常,纤维束43缠绕方向与内芯41轴线的夹角,从增强层2的内层向外层逐渐降低,以便内层绕线4变形大,能够将压力逐层传递到外层,使得多层绕线4均匀受力。但是,在其他因素影响下,以及绕线4缠绕不同工艺参数组合情况下,存在需要将纤维束43缠绕方向与内芯41轴线的夹角从增强层2的内层向外层逐渐降低、或者逐渐增加、或者不变3种不同情况,进一步拓展了所述绕线4的使用范围。
纤维束43与内芯41体积比的取值,从增强层2的内层向外层逐渐增加,或者逐渐降低,或者不变。绕线4中,纤维束43占比越大,内芯41越小,内芯41受到挤压变形能力越差。通常纤维束43与内芯41体积比的取值,从增强层2的内层向外层逐渐增加,以便内层绕线4变形大,能够将压力逐层传递到外层,使得多层绕线4均匀受力。但是,在其他因素影响下,以及绕线4缠绕不同工艺参数组合情况下,存在需要将纤维束43与内芯41体积比的取值从增强层2的内层向外层逐渐降低、或者逐渐增加、或者不变3种不同情况,进一步拓展了所述绕线4的使用范围。
增强层2的单一层中,至少2根绕线4并排且添加粘结剂组成绕带。通过绕带逐层缠绕形成增强层2,提高加工制造效率。
通过缠绕或者挤塑方式,在增强层2外设置保护层3,所述保护层3选自聚乙烯、尼龙、聚偏二氟乙烯、聚苯硫醚、聚醚醚酮、聚醚酮酮或发泡聚乙烯中的一种或几种的混合物。保护层3对增强层2起到保护作用,隔绝外界介质,并防止紫外线对增强层2纤维的影响。内衬层1选自聚乙烯、尼龙、聚偏二氟乙烯、聚苯硫醚、聚醚醚酮、聚醚酮酮或发泡聚乙烯中的一种或几种的混合物。
绕线4缠绕形成增强层2后,用常规柔性纤维在所述增强层2外侧缠绕形成多层结构,所述常规柔性纤维选自碳纤维、碳化硅纤维、硼纤维、氮化硼纤维、玄武岩纤维、玻璃纤维、芳纶纤维、聚酯纤维、聚乙烯纤维、钢丝中的一种或多种的混合物。采用现有柔性纤维缠绕最外层(数层),方便现有保护层生产工艺直接应用到本发明所述大口径高压柔性复合管;并且最外层(数层)缠绕层无需设置为绕线4形成的弹性结构。
实施方案1:内衬层1管道内径600mm,内衬层1采用壁厚22mm的聚乙烯管,绕线4的内芯41采用直径3mm的实心橡胶线,纤维束43为芳纶纤维,内芯41表面设置沿内芯41轴向布置的芳纶纤维,纤维束43与内芯41体积比为0.7:1,绕线4缠绕方向与管道轴线夹角为55°,纤维束43捻度为零;绕线4螺旋缠绕到内衬层1上,形成8层结构的增强层2;所述增强层2的相邻层之间,绕线4缠绕方向相反;增强层2的相邻层之间纤维束43与内芯41的缠绕方向相反。各层绕线4中,纤维束43缠绕方向与内芯41轴线夹角从第1层到第8层分别为:60°(正旋缠绕),60°(反旋缠绕),50°(正旋缠绕),50°(反旋缠绕),40°(正旋缠绕),40°(反旋缠绕),30°(正旋缠绕),30°(反旋缠绕)。
通过实验,并借助改进后的tsai-wu准则进行有限元分析,实施方案1所述管道爆破压力接近33mpa。按照现有纤维增强柔性复合管加工技术,采用相同体积的芳纶纤维,平均缠绕8层形成增强层2;借助tsai-wu准则进行有限元分析,管道爆破压力接近23mpa。分析发现,本发明所述技术方案中,各层绕线4层的应力为内层高、外层底,但是相差幅度远小于芳纶纤维直接缠绕对应的应力差值,本发明所述技术方案将该管道承压能力提升40%左右。从上述分析可以看出,实施方案1中相关参数有进一步优化空间(比如改变各层中纤维束43缠绕方向与内芯41轴线夹角),最终使得各层绕线4均衡受力,能够进一步提升其承载能力。
总结:本发明采用纤维束43缠绕到柔性材质的内芯41上,制成绕线4后再缠绕形成多层结构的增强层2;并且通过改变各层中,纤维束43缠绕方向与内芯41轴线夹角、纤维束43与内芯41体积比、绕线4缠绕方向与管道轴线夹角、纤维束43捻度等方式,调整各层绕线4的松紧程度,实现各层绕线4均匀受力,最终提升纤维增强柔性复合管道的承压能力。
本发明从根本上解决了现有纤维缠绕造成内层受力大、外层受力小的问题,通过本发明所述技术方案,能够将所述绕线4加工成大口径、高压力柔性复合管道,满足油气管输及其他应用场合的需要。