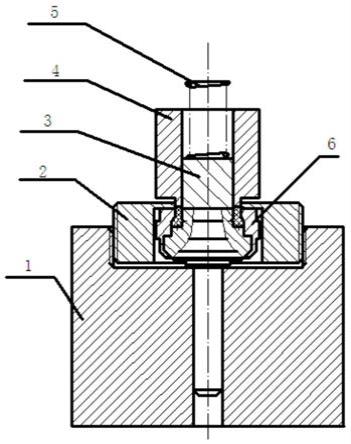
1.本发明属于机械加工技术领域,特别涉及一种复合式阀芯冷压成型工装及成型工艺。
背景技术:2.复合式阀芯是一种由多零件构成的软密封形式的阀芯,在液体火箭发动机中密封可靠性高,应用范围广,多项自动器采用该结构阀芯保证自动器功能可靠。软密封结构的密封材料有一定的弹性,与硬密封结构形式相比较,其密封性能更优,更利于航天产品质量保障。但是复合式阀芯成形过程中,非金属材料发生塑性变形,填充基体上的60
°
密封槽,阀芯非金属材料的充填质量会受到成形工艺方法、成形过程辅助工装的影响。成形工艺方法设计不合理会导致紧固零件失效,造成压力突然释放,阀芯冷塑成形失败。辅助工装设计不合理,会导致压力扩散,多数还会发生塑料剪切、撕裂现象,严重影响非金属密封件的力学性能。阀芯冷压成形工艺难度高,需综合控制多项参数,设计合理的辅助工装和工艺流程,多方面加严控制,才能保证复合式软密封结构的一次交检合格率。
技术实现要素:3.为了克服现有技术中的不足,本发明人进行了锐意研究,提供了一种液体火箭发动机复合式阀芯冷压成型工装及成型工艺,解决了复合式阀芯塑料密封环在限定范围内通过塑性变形,充分填充密封腔进而实现与金属紧密贴合的技术难题,有效实现了复合式阀芯的软密封结构制造,保证密封性能良好,从而完成本发明。
4.本发明提供的技术方案如下:
5.第一方面,一种复合式阀芯冷压成型工装,所述复合式阀芯包括阀芯基体、紧固件和塑料密封环,所述阀芯基体的小端为长柱状导向杆,大端为台阶块体结构,所述塑料密封环压装在阀芯基体的大端,通过所对应的台阶面限位,塑料密封环的高度满足安装后高出阀芯基体大端端面;所述紧固件压装在阀芯基体的大端,包覆塑料密封环;
6.所述成型工装包括底座、紧固套、导向柱、压杆和弹簧;所述底座的内腔为台阶孔结构,小孔直径大于阀芯基体的长柱状导向杆直径,用于容纳阀芯基体的长柱状导向杆,大孔为螺纹孔,与紧固套的外圆螺纹连接,用于固定复合式阀芯;
7.所述紧固套的内腔为台阶孔结构,大孔直径大于复合式阀芯最大外圆直径,小孔直径大于复合式阀芯塑料密封环的外径且小于紧固件的外径,用于包裹塑料密封环的外圆;
8.所述导向柱为圆柱样,外圆直径小于阀芯塑料密封环的内径,其下端置于塑料密封环的内孔中;
9.所述压杆为中空台阶样结构,内腔为纵向通孔,纵向通孔内配置所述导向柱,压杆的小端内外径与阀芯塑料密封环的内外径一致,且与阀芯塑料密封环的上表面接触,大端为压力机的受力面,用于借助压力机向塑料面施加压力;
10.所述弹簧的下部位于压杆的内腔中,下端与导向柱的上表面接触,上端为压力机的受力面,其长度大于导向柱总长与压杆总长之差,用于压住导向柱。
11.第二方面,一种复合式阀芯冷压成型工艺,包括如下步骤:
12.步骤1),将复合式阀芯的零件进行组装,先将塑料密封环压装在阀芯基体的大端上,通过所对应的台阶面限位,再将紧固件压装在阀芯基体上,包覆塑料密封环,塑料密封环的高度满足安装后高出阀芯基体大端端面;
13.步骤2),对紧固件采用收口或者销钉进行固定,根据复合式阀芯的结构特点,选择滚压紧固件一端的薄壁,使其与阀芯基体密切贴合或者直接使用销钉将紧固件和阀芯基体进行连接,防止紧固件相对移动或者转动;
14.步骤3),将组装后的复合式阀芯置于底座的内腔,阀芯基体的长柱状导向杆插入基座的小孔中;将紧固套套设在复合式阀芯外,并与基座的内圆螺纹连接;将压杆的小端插入紧固套的小孔中,与阀芯塑料密封环的上表面接触;将导向柱置于压杆的内腔中,然后在压杆的内腔中再插入弹簧,顶住导向柱;
15.步骤4),对复合式阀芯的塑料密封环进行保压,使阀芯塑料密封环充分受压,在限定范围内充分变形,充分填充基体上的60
°
环向密封槽;
16.步骤5),对阀芯表面进行机械加工,保证密封面平整。
17.根据本发明提供的一种复合式阀芯冷压成型工装及成型工艺,具有以下有益效果:
18.(1)本发明提供的一种复合式阀芯冷压成型工装及成型工艺,无需采用热压的方式来实现塑料的塑性变形,减少塑料加热成本;
19.(2)本发明提供的一种复合式阀芯冷压成型工装及成型工艺,采用压杆对塑料密封环进行加压,采用紧固套和导向柱对塑料密封环进行限位,提高了压力有效性,塑料变形的填充率高;
20.(3)本发明提供的一种复合式阀芯冷压成型工装及成型工艺,通过紧固套和导向柱设计,配合其他结构件,使本发明工艺方法避免了传统工艺方法设计不合理导致的紧固零件失效,造成压力突然释放,阀芯冷塑成形失败的问题,且工装设计合理,不会产生传统工装设计不合理,导致压力扩散、发生塑料剪切、撕裂现象、严重影响非金属密封件的力学性能的问题;
21.(4)本发明提供的一种复合式阀芯冷压成型工装及成型工艺,复合式阀芯冷压结束后对其进行表面加工,采用由塑料密封环非金属表面向两侧阀芯基体和紧固件金属表面进给的方式走刀可以有效控制金属铁屑的流向,避免伤到非金属。
附图说明
22.图1为本发明复合式阀芯冷压成型工装的结构示意图;
23.图2为本发明复合式阀芯冷压成型工装的底座结构图;
24.图3为本发明复合式阀芯冷压成型工装的紧固套结构图;
25.图4为本发明复合式阀芯冷压成型工装的导向柱结构图;
26.图5为本发明复合式阀芯冷压成型工装的压杆结构图;
27.图6为本发明涉及到的复合式阀芯的结构示意图;
28.图7为本发明涉及到阀芯表面机械加工方式示意图。
29.附图标号说明
[0030]1‑
底座;2
‑
紧固套;3
‑
导向柱;4
‑
压杆;5
‑
弹簧;6
‑
复合式阀芯;71
‑
阀芯基体;72
‑
紧固件;73
‑
塑料密封环。
具体实施方式
[0031]
下面通过对本发明进行详细说明,本发明的特点和优点将随着这些说明而变得更为清楚、明确。
[0032]
在这里专用的词“示例性”意为“用作例子、实施例或说明性”。这里作为“示例性”所说明的任何实施例不必解释为优于或好于其它实施例。尽管在附图中示出了实施例的各种方面,但是除非特别指出,不必按比例绘制附图。
[0033]
根据本发明的第一方面,提供了一种复合式阀芯冷压成型工装,所述复合式阀芯包括阀芯基体71、紧固件72和塑料密封环73,如图1和图6所示,所述阀芯基体71为t型结构,小端为长柱状导向杆,大端为台阶块体结构,所述塑料密封环73压装在阀芯基体71的大端,通过所对应的台阶面限位且该台阶面上加工有60
°
环向密封槽,塑料密封环73的高度满足安装后高出阀芯基体71大端端面,优选高出1~1.5mm;所述紧固件72压装在阀芯基体71的大端,包覆塑料密封环73;
[0034]
如图1所示,所述成型工装包括底座1、紧固套2、导向柱3、压杆4和弹簧5;如图2所示,所述底座1的内腔为台阶孔结构,小孔直径比阀芯基体71的长柱状导向杆直径略大,用于容纳阀芯基体71的长柱状导向杆,大孔为螺纹孔,与紧固套2的外圆螺纹连接,其作用是固定复合式阀芯;
[0035]
如图3所示,所述紧固套2的内腔也为台阶孔结构,大孔直径比复合式阀芯最大外圆直径略大,小孔直径大于复合式阀芯塑料密封环73的外径且小于紧固件72的外径,优选小孔直径比复合式阀芯塑料密封环73的外径大0.05
‑
0.15mm,其作用是将塑料密封环73的外圆包裹住,防止塑料密封环73受压向外侧变形;
[0036]
如图4所示,所述导向柱3为圆柱样,外圆直径小于阀芯塑料密封环73的内径,优选外圆直径比阀芯塑料密封环73的内径小0.05
‑
0.15mm,其作用是放在塑料密封环73的内孔中,防止塑料密封环73受压向内侧变形;
[0037]
如图5所示,所述压杆4为中空台阶样结构,内腔为纵向通孔,纵向通孔内配置所述导向柱3,压杆4的小端内外径与阀芯塑料密封环73的内外径一致,且与阀芯塑料密封环73的上表面接触,大端为压力机的受力面,外径无具体尺寸要求,其作用是借助压力机向塑料面施加压力;
[0038]
如图1所示,所述弹簧5的下部位于压杆4的内腔中,下端与导向柱3的上表面接触,上端为压力机的受力面,外径小于压杆4的内径,长度大于导向柱3总长与压杆4总长之差,优选长度为导向柱3总长与压杆4总长之差的1.5~2倍即可,其作用是压住导向柱3,防止塑料变形时将导向柱3顶出。
[0039]
在一种优选的实施方式中,所述底座1的大孔开口处为锥面结构,便于紧固套2与底座1的配合。
[0040]
在一种优选的实施方式中,所述紧固套2的高度大于、小于或等于底座1的大孔高
度,优选所述紧固套2的高度大于底座1的大孔高度,便于紧固套2的安装、拆卸。
[0041]
在一种优选的实施方式中,所述导向柱3两端圆形棱边均为锐边,不允许有倒角。
[0042]
在一种优选的实施方式中,所述弹簧5为压缩弹簧,直径不小于导向柱3直径的1/2。
[0043]
根据本发明的第二方面,提供了一种复合式阀芯冷压成型工艺,包括如下步骤:
[0044]
(1)将复合式阀芯的零件进行组装,先将塑料密封环73压装在阀芯基体71的大端上,通过所对应的台阶面限位,再将紧固件72压装在阀芯基体71上,包覆塑料密封环73,塑料密封环73的高度满足安装后高出阀芯基体71大端端面1~1.5mm;
[0045]
(2)对紧固件72采用收口或者销钉进行固定,根据复合式阀芯的结构特点,选择滚压紧固件71一端的薄壁,使其与阀芯基体71密切贴合或者直接使用销钉将紧固件72和阀芯基体71进行连接,防止紧固件72相对移动或者转动;
[0046]
(3)将组装后的复合式阀芯置于底座1的内腔,阀芯基体71的长柱状导向杆插入基座1的小孔中;将紧固套2套设在复合式阀芯外,并与基座1的内圆螺纹连接;将压杆4的小端插入紧固套2的小孔中,与阀芯塑料密封环73的上表面接触;将导向柱3置于压杆4的内腔中,然后在压杆4的内腔中再插入弹簧5,顶住导向柱3;
[0047]
(4)对复合式阀芯的塑料密封环73进行保压,使阀芯塑料密封环73充分受压,在限定范围内充分变形,充分填充基体上的60
°
环向密封槽;加压压力值根据塑料密封环73的受力面积计算得出,加压速度不大于1mm/min,保压时间根据塑料密封环73的受力面积计算得出,优选为10min
‑
15min;
[0048]
研究发现,加压速度不大于1mm/min,基本可以保证塑料密封环不会被压伤,若加压速度大于1mm/min,则有可能发生塑料密封环被压裂或导向柱3被向上顶起。
[0049]
(5)对阀芯表面进行机械加工,保证密封面平整,优选采用由塑料密封环73非金属表面向两侧阀芯基体71和紧固件72金属表面进给的走刀方式实施机械加工,如图7所示。
[0050]
实施例
[0051]
实施例1
[0052]
一种用于液体火箭发动机中吹除系统、燃料系统阀门中的复合式阀芯冷压成形工艺,步骤如下:
[0053]
(1)将复合式阀芯的零件进行组装,先将塑料密封环73压装在阀芯基体71的大端上,通过所对应的台阶面限位,再将紧固件72压装在阀芯基体71上,包覆塑料密封环73;塑料密封环73的高度满足安装后高出阀芯基体71大端端面1mm;
[0054]
(2)复合式阀芯的零件组装完成后,对紧固件72采用收口方式进行固定,对紧固件左端的薄壁进行滚压,使其与阀芯基体密切贴合进而固定(见图6);
[0055]
(3)将组装后的复合式阀芯置于底座1的内腔,阀芯基体71的长柱状导向杆插入基座1的小孔中;将紧固套2套设在复合式阀芯外,并与基座1的内圆螺纹连接;将压杆4的小端插入紧固套2的小孔中,与阀芯塑料密封环73的上表面接触;将导向柱3置于压杆4的内腔中,然后在压杆4的内腔中再插入弹簧5,顶住导向柱3;
[0056]
(4)对复合式阀芯的塑料密封环73进行保压,使塑料充分受压,在限定范围内充分变形,充分填充基体上的60
°
环向密封槽,塑料密封环73的受力面积为40.3mm2,加压压力值f为6000n,加压速度为1mm/min,保压时间为10min;
[0057]
(5)对阀芯表面进行机械加工,保证密封面平整,选采用由非金属表面向金属表面进给的走刀方式实施机械加工。
[0058]
采用上述工艺加工得到的复合式阀芯,阀芯密封表面质量良好,无撕裂、破损等影响使用的缺陷,密封性能良好,满足行业内密封要求。对阀芯进行剖切检查,基体上的60
°
环向密封槽填充饱满。
[0059]
以上结合具体实施方式和范例性实例对本发明进行了详细说明,不过这些说明并不能理解为对本发明的限制。本领域技术人员理解,在不偏离本发明精神和范围的情况下,可以对本发明技术方案及其实施方式进行多种等价替换、修饰或改进,这些均落入本发明的范围内。本发明的保护范围以所附权利要求为准。
[0060]
本发明说明书中未作详细描述的内容属本领域技术人员的公知技术。