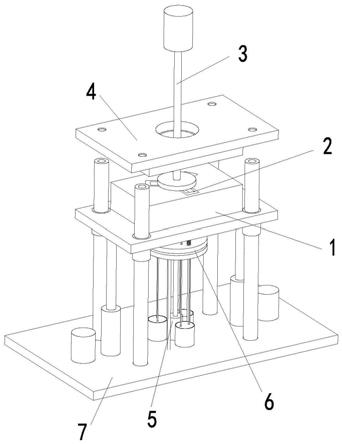
1.本发明涉及超声制造技术领域,尤其涉及一种新型超声塑化成型装置及控制方法。
背景技术:2.目前,聚合物微零件在电子通讯、航空航天等各个领域都有着广泛的应用,而微注射成型技术以其低廉的成本、便捷的加工等优势成为了研究人员的重点关注的对象,而微注射成型技术也存在填充困难、材料浪费等问题。
[0003]“超声塑化”技术应运而生,超声塑化技术有两种生产模式,一种为“超声塑化头塑化并注射”模式,此种模式会导致超声塑化头和塑化内腔剧烈摩擦,引起超声塑化头和塑化内腔磨损现象,另一种为“超声塑化头塑化、送料推杆注射”模式,此模式解决了超声塑化头和塑化内腔磨损现象,但是会导致刚塑化的聚合物被快速挤出,在填充过程中包裹有尚未塑化完成的聚合物小颗粒进入型腔,导致塑化不完全、塑化不均匀的问题,而且在针对超薄和微结构等特殊结构的产品,由于聚合物粘度大,会导致产品注射困难、注射不完全以及成型质量差的问题。。
技术实现要素:[0004]
本发明旨在一定程度上解决上述存在的技术问题,提供一种新型超声塑化成型装置及控制方法,能够解决超薄和微结构产品由于聚合物粘度大而导致注射困难、注射不完全以及成型质量差的问题。
[0005]
本发明解决其技术问题所采用的技术方案是:
[0006]
第一方面本技术提供了一种新型超声塑化成型装置,包括动模装置,模芯,超声塑化头,定模装置,送料装置,退料装置,所述动模装置固定在工作台,用于放入塑化聚合物;所述模芯设于动模装置内部,其朝外的端面设有模腔;所述超声塑化头设于动模装置上方,并覆盖模芯,该超声塑化头与外部超声发生器连接;所述定模装置设于超声塑化头外部并与动模装置贴合,使定模装置、动模装置、模芯及超声塑化头之间形成封闭的塑化空间;所述送料装置安装在工作台,并伸入动模装置内推动聚合物移动,将塑化后的聚合物挤入到模腔中;所述退料装置安装在工作台,并穿过动模装置与模芯连接,将模芯内加工成型的聚合物产品顶出。
[0007]
优选的,所述动模装置包括动模基板、动模液压杆、动模液压装置和动模板;所述动模液压装置固定在工作台,所述动模液压杆一端与动模液压装置传动连接,另一端螺栓固定在动模基板设置的安装孔内,并通过动模液压装置使动模液压杆带动动模基板上下运动,所述动模板安装在动模基板的上端面,动模板的上端面内陷设有用于固定模芯的深槽,所述动模基板与动模板靠近深槽的位置同轴心设有用于放入塑化聚合物的塑化腔,所述动模板围绕塑化腔并与模芯之间设有连通的进料口流道,所述模芯的进料口流道位置设有第一模腔温度传感器,所述模芯的模腔底面设有第二模腔温度传感器及模腔压力传感器。
[0008]
优选的,所述进料口流道表面靠近通孔的位置设有三角体凸台。
[0009]
优选的,所述工作台上安装有小油箱,所述小油箱通过设置的油泵与模芯内部的冷却油道连接,所述小油箱内部还安装有加热电阻丝及冷却油温度传感器。
[0010]
优选的,所述定模装置包括上固定板、隔热板、定模板和导柱,所述导柱的一端固定在工作台,另一端穿过动模基板与上固定板连接,所述动模基板设有四个与导柱相匹配的导孔,并在导孔内设有导套,通过导套使动模基板与导柱装配连接,所述隔热板安装在上固定板下端面,所述定模板安装在隔热板下端面,使定模板覆盖模芯的模腔并贴紧动模板的上端面,所述上固定板、隔热板及定模板与塑化腔同轴心的位置设有通孔,所述超声塑化头插设在通孔内并压紧动模板的上端面,使模芯的模腔呈密闭的结构。
[0011]
优选的,所述送料装置包括送料推杆和进给电机,所述进给电机安装在工作台,所述送料推杆的一端与进给电机传动连接,另一端伸入至塑化腔内并推动物料移动,所述送推杆位于塑化腔的端部设有送料压力传感器。
[0012]
优选的,所述退料装置包括上顶杆、下顶杆、退料上挡块、退料下挡块和退料下挡块支架,所述退料下挡块通过退料下挡块支架安装在工作台,所述退料上挡块安装在退料下挡块的上端面,所述下顶杆与退料上挡块固定连接,下顶杆外部套设有弹簧,所述上顶杆安装在下顶杆的端部并伸入至模芯设置的顶孔中,所述下顶杆的端部还设有线圈。
[0013]
第二方面本技术提供了一种新型超声塑化成型装置的控制方法,包括所述超声塑化成型装置,并通过控制模块设置超声塑化成型装置的工艺参数和系统参数,所述工艺参数包括超声频率f1、送料推杆速度v1、送料压力传感器的初始压力p1、冷却油预热的温度t1,所述系统参数包括超声塑化头与动模板的垂直距离h1、动模液压装置的速度b1、模腔压力传感器上限e1和下限阈值e2、模腔温度传感器一上限f1和下限阈值f2、模腔温度传感器二下限阈值f3、模腔温度传感器一凝固阈值c、模腔温度传感器二凝固阈值c,其具体包括如下工作阶段:
[0014]
s1.塑化注塑阶段:首先动模基板带动动模板下移,将聚合物放入动模板中心的塑化腔中,放入完毕后动模基板带动动模板上移,使动模板与定模板下端面密闭接触后超声塑化头开始振动,同时送料推杆推动聚合物上行,聚合物接触超声塑化头达到熔化温度熔化后被挤压至进料口流道中,随后超声塑化头继续作用进一步提升聚合物的温度,至使聚合物流至模芯的模腔中,并通过第一模腔温度传感器、第二模腔温度传感测量聚合物温度;
[0015]
s2.保压阶段:随着模芯的模腔内被充满聚合物时,压力传感器感应模腔内的压力变化,并控制送料推杆的送料速度;
[0016]
s3.冷却阶段:超声塑化头停止振动,保持送料压力不变,同时对冷却油进行泄压,使冷却油流回小油箱,并保持小油箱内冷却油温度不变,聚合物产品开始冷却,同时,当达到冷却标准时送料推杆被锁死,动模液压装置带动动模液压杆开始下行,此时送料推杆和上顶杆同时作用于聚合物产品,聚合物产品被顶出,并完成聚合物产品加工;
[0017]
s4.更新阶段:系统根据不同时间段对存储在控制模块中的系统参数曲线和工艺参数曲线进行更新,来进行下一次生产,直至工艺符合所有的设置条件,生成最优方案,锁定所有系统参数曲线和工艺参数曲线后将不执行更新阶段。
[0018]
优选的,所述s1阶段中若第一模腔温度传感器测量到的聚合物温度f0低于第一模腔温度传感器设置的下限阈值f2时,则通过增加所述送料推杆的送料压力p1、增加超声频率
f1和减小超声塑化头与动模板的垂直距离h1来使聚合物熔化更充分,直至达到此处温度传感器的下限阈值f2。
[0019]
优选的,所述s1阶段中若第一模腔温度传感器测量到的聚合物温度f0高于第一模腔温度传感器设置的上限阈值f1时,则通过减小送料推杆的送料压力p1、减小超声频率f1和增加超声塑化头与动模板的垂直距离h1来使聚合物熔化温度降低,直至回落至此处温度传感器的上限阈值f1以内。
[0020]
本技术实施例提供的上述技术方案与现有技术相比具有如下优点:
[0021]
能有效解决现有超声塑化技术中超声塑化头和塑化内腔磨损问题以及塑化不均匀、不完全问题,将超声塑化头、动模板、定模板、模芯整合在一起,形成封闭的塑化空间,同时本技术在塑化内腔被塑化挤出后,通过流道的时候,超声塑化头会继续作用于聚合物,使聚合物完全塑化,提高聚合物流入模芯型腔的初始温度,特别是针对超薄产品或者微结构产品,熔融状态下的聚合物流入模芯型腔后,模芯型腔上方的超声塑化头会保持振动,对型腔内聚合物保持高频振动的同时,增加型腔内聚合物注入压力,减少产品缺陷,能够解决超薄和微结构产品由于聚合物粘度大而导致注射困难、注射不完全以及成型质量差的问题,而且可设置多个不同模腔不同造型的模芯,且每个模芯加热系统彼此独立,可设置不同的预热温度,来实现一次注塑多个不同产品产出。
附图说明
[0022]
此处的附图被并入说明书中并构成本说明书的一部分,示出了符合本发明的实施例,并与说明书一起用于解释本发明的原理。
[0023]
为了更清楚地说明本发明实施例或现有技术中的技术方案,下面将对实施例或现有技术描述中所需要使用的附图作简单地介绍,显而易见地,对于本领域普通技术人员而言,在不付出创造性劳动性的前提下,还可以根据这些附图获得其他的附图。
[0024]
附图中:
[0025]
图1为本发明所述新型超声塑化成型装置总装结构示意图;
[0026]
图2为本发明所述新型超声塑化成型装置结构示意图;
[0027]
图3为图2中a处局部放大示意图;
[0028]
图4为本发明所述动模装置结构示意图;
[0029]
图5为本发明所述定模装置结构示意图;
[0030]
图6为本发明所述送料装置结构示意图;
[0031]
图7为本发明所述退料装置结构示意图;
[0032]
图8为本发明所述模芯结构示意图;
[0033]
图9为本发明所述新型超声塑化成型装置结构示意图;
[0034]
图10为本发明所述操作方法流程图。
[0035]
附图标号:1
‑
动模装置;101
‑
动模基板;102
‑
动模液压杆;103
‑
动模液压装置;104
‑
动模板;2
‑
模芯;3
‑
超声塑化头;4
‑
定模装置;401
‑
上固定板;402
‑
隔热板;403
‑
定模板;404
‑
导柱;405
‑
导套;5
‑
送料装置;501
‑
送料推杆;502
‑
进给电机;503
‑
送料压力传感器;6
‑
退料装置;601
‑
上顶杆;602
‑
下顶杆;603
‑
退料上挡块;604
‑
退料下挡块;605
‑
退料下挡块支架;606
‑
弹簧;607
‑
线圈;7
‑
工作台;8
‑
模腔;9
‑
塑化腔;10
‑
进料口流道;11
‑
第一模腔温度传感
器;12
‑
第二模腔温度传感器;13
‑
模腔压力传感器;14
‑
三角体凸台;15
‑
小油箱;16
‑
油泵;17
‑
加热电阻丝;18
‑
冷却油温度传感器。
具体实施方式
[0036]
为了对本发明的技术特征、目的和效果有更加清楚的理解,现对照附图详细说明本发明的具体实施方式。以下描述中,需要理解的是,“前”、“后”、“上”、“下”、“左”、“右”、“纵”、“横”、“竖直”、“水平”、“顶”、“底”、“内”、“外”、“头”、“尾”等指示的方位或位置关系为基于附图所示的方位或位置关系、以特定的方位构造和操作,仅是为了便于描述本技术方案,而不是指示所指的装置或元件必须具有特定的方位,因此不能理解为对本发明的限制。
[0037]
还需要说明的是,除非另有明确的规定和限定,“安装”、“相连”、“连接”、“固定”、“设置”等术语应做广义理解,例如,可以是固定连接,也可以是可拆卸连接,或成一体;可以是机械连接,也可以是电连接;可以是直接相连,也可以通过中间媒介间接相连,可以是两个元件内部的连通或两个元件的相互作用关系。当一个元件被称为在另一元件“上”或“下”时,该元件能够“直接地”或“间接地”位于另一元件之上,或者也可能存在一个或更多个居间元件。术语“第一”、“第二”、“第三”等仅是为了便于描述本技术方案,而不能理解为指示或暗示相对重要性或者隐含指明所指示的技术特征的数量,由此,限定有“第一”、“第二”、“第三”等的特征可以明示或者隐含地包括一个或者更多个该特征。对于本领域的普通技术人员而言,可以根据具体情况理解上述术语在本发明中的具体含义。
[0038]
以下描述中,为了说明而不是为了限定,提出了诸如特定系统结构、技术之类的具体细节,以便透彻理解本发明实施例。然而,本领域的技术人员应当清楚,在没有这些具体细节的其它实施例中也可以实现本发明。在其它情况中,省略对众所周知的系统、装置、电路以及方法的详细说明,以免不必要的细节妨碍本发明的描述。
[0039]
如图1
‑
3为实施例一中本技术提供了一种新型超声塑化成型装置,包括动模装置1,模芯2,超声塑化头3,定模装置4,送料装置5,退料装置6,所述动模装置1固定在工作台7,用于放入塑化聚合物;所述模芯2设于动模装置1内部,其朝外的端面设有模腔8;所述超声塑化头3设于动模装置1上方,并覆盖模芯2,该超声塑化头3与外部超声发生器连接;所述定模装置4设于超声塑化头3外部并与动模装置1贴合,使定模装置4、动模装置1、模芯2及超声塑化头3之间形成以供超声塑化头3振动的封闭的塑化空间,所述送料装置5安装在工作台7,并伸入动模装置1内推动聚合物移动,将塑化后的聚合物挤入到模腔8中;所述退料装置6安装在工作台7,并穿过动模装置1与模芯2连接,将模芯2内加工成型的聚合物产品顶出。
[0040]
其中,如图4所示,所述动模装置1包括动模基板101、动模液压杆102、动模液压装置103和动模板104;所述动模液压装置103固定在工作台7,所述动模液压杆102一端与动模液压装置103传动连接,另一端螺栓固定在动模基板101设置的安装孔内,并通过动模液压装置103使动模液压杆102带动动模基板101上下运动,所述动模板104安装在动模基板101的上端面,动模板104的上端面内陷设有用于固定模芯2的深槽,所述动模基板101与动模板104靠近深槽的位置同轴心设有用于放入塑化聚合物的塑化腔9,所述动模板104围绕塑化腔9并与模芯2之间设有连通的进料口流道10,所述模芯2的进料口流道10位置设有第一模腔温度传感器11,所述模芯2的模腔8底面设有第二模腔温度传感器12及模腔压力传感器13;
[0041]
具体的,所述进料口流道10表面靠近通孔的位置设有三角体凸台14,高分子材料的聚合物在挤入模腔8时,通过三角体凸台14能够隔挡熔化后聚合物产生的气泡以及未完全熔解的颗粒,提高聚合物排入到模腔8内的流动性,减少模腔8内聚合物气泡的产生,提高产品成型的质量。
[0042]
其中,如图9所示,所述工作台7上安装有小油箱15,所述小油箱15通过设置的油泵16与模芯2内部的冷却油道连接,所述小油箱15内部还安装有加热电阻丝17及冷却油温度传感器18。
[0043]
其中,如图5所示,所述定模装置4包括上固定板401、隔热板402、定模板403和导柱404,所述导柱404的一端固定在工作台7,另一端穿过动模基板101与上固定板401连接,所述动模基板101设有四个与导柱404相匹配的导孔,并在导孔内设有导套405,通过导套405使动模基板101与导柱404装配连接,所述隔热板402安装在上固定板401下端面,所述定模板403安装在隔热板402下端面,使定模板403覆盖模芯2的模腔8并贴紧动模板104的上端面,所述上固定板401、隔热板402及定模板403与塑化腔9同轴心的位置设有通孔,超声塑化头3与定模板403的通孔为间隙配合,间隙距离小于聚合物的溢料间隙;
[0044]
进一步的,所述超声塑化头3插设在通孔内并压紧动模板104的上端面,使模芯2的模腔8呈密闭的结构,其中,超声塑化头3与动模板104的垂直距离为超声振幅的1.2
‑
1.5倍,具体的,定模板403下端面与动模板104上端面接触,定模板403一端压住模芯2的模腔8外侧的部分,模芯2的模腔8内侧的部分被超声塑化头3下端面压住,同时超声塑化头3可根据注塑产品的需求对模芯2型腔部分进行全覆盖,从而将超声塑化头3、模腔8以及动模板104在塑化时集成一体,超声头工作时产生的振幅会传递到模腔8表面,同时与模腔8内的压力配合,能够更好的将聚合物挤入到模腔8内;
[0045]
其中,如图6所示,所述送料装置5包括送料推杆501和进给电机502,所述进给电机502安装在工作台7,所述送料推杆501的一端与进给电机502传动连接,另一端伸入至塑化腔9内并推动物料移动,所述送推杆位于塑化腔9的端部设有送料压力传感器503。
[0046]
其中,如图7所示,所述退料装置6包括上顶杆601、下顶杆602、退料上挡块603、退料下挡块604和退料下挡块支架605,所述退料下挡块604通过退料下挡块支架605安装在工作台7,所述退料上挡块603安装在退料下挡块604的上端面,所述下顶杆602与退料上挡块603固定连接,下顶杆602外部套设有弹簧606,所述上顶杆601安装在下顶杆602的端部并伸入至模芯2设置的顶孔中,所述下顶杆602的端部还设有线圈607;
[0047]
具体的,每个模芯2内上顶杆601的数量为两根,在模芯2的模腔8底部合理分布,下顶杆602圆柱的直径小于上顶杆601的圆柱直径,上顶杆601长度为模腔8下表面至动模板104深槽上表面的垂直距离,上顶杆601下端接触动模板104深槽上表面。
[0048]
本实施方式中能有效解决现有超声塑化技术中超声塑化头3和塑化内腔磨损问题以及塑化不均匀、不完全问题,将超声塑化头3、动模板104、定模板403、模芯2整合在一起,形成封闭的塑化空间,同时本技术在塑化内腔被塑化挤出后,通过流道的时候,超声塑化头3会继续作用于聚合物,使聚合物完全塑化,提高聚合物流入模芯2型腔的初始温度,特别是针对超薄产品或者微结构产品,熔融状态下的聚合物流入模芯2型腔后,模芯2型腔上方的超声塑化头3会保持振动,对型腔内聚合物保持高频振动的同时,增加型腔内聚合物注入压力,减少产品缺陷,能够解决超薄和微结构产品由于聚合物粘度大而导致注射困难、注射不
完全以及成型质量差的问题,而且可设置多个不同模腔8不同造型的模芯2,且每个模芯2加热系统彼此独立,可设置不同的预热温度,来实现一次注塑多个不同产品产出。
[0049]
如图10所示,第二方面本技术提供了一种新型超声塑化成型装置的控制方法,包括所述超声塑化成型装置,接通电源,退料装置6中线圈607通电产生电磁感应,上顶杆601下端吸附在下顶杆602上端,同时通过控制模块设置超声塑化成型装置的工艺参数和系统参数,所述工艺参数包括超声频率f1、送料推杆501速度v1、送料压力传感器503的初始压力p1、冷却油预热的温度t1,所述系统参数包括超声塑化头3与动模板104的垂直距离h1、动模液压装置103的速度b1、模腔压力传感器13上限e1和下限阈值e2、第一模腔温度传感器11上限f1和下限阈值f2、第二模腔温度传感器12下限阈值f3、第一模腔温度传感器11凝固阈值c、第二模腔温度传感器12凝固阈值c,其具体包括如下工作阶段:
[0050]
s1.塑化注塑阶段:首先动模基板101带动动模板104下移,将聚合物放入动模板104中心的塑化腔9中,放入完毕后动模基板101带动动模板104上移,使动模板104与定模板403下端面密闭接触后超声塑化头3开始振动,同时送料推杆501推动聚合物上行,聚合物接触超声塑化头3达到熔化温度熔化后被挤压至进料口流道10中,随后超声塑化头3继续作用进一步提升聚合物的温度,至使聚合物流至模芯2的模腔8中,并通过第一模腔温度传感器11、第二模腔温度传感12测量聚合物温度;
[0051]
具体的,所述s1阶段中若第一模腔温度传感器11测量到的聚合物温度f0低于第一模腔温度传感器11设置的下限阈值f2时,则通过增加所述送料推杆501的送料压力p1、增加超声频率f1和减小超声塑化头3与动模板104的垂直距离h1来使聚合物熔化更充分,直至达到此处温度传感器的下限阈值f2;
[0052]
当所述s1阶段中若第一模腔温度传感器11测量到的聚合物温度f0高于第一模腔温度传感器11设置的上限阈值f1时,则通过减小送料推杆501的送料压力p1、减小超声频率f1和增加超声塑化头3与动模板104的垂直距离h1来使聚合物熔化温度降低,直至回落至此处温度传感器的上限阈值f1以内,此时的送料推杆501的送料速度v1、送料推杆501的送料压力p1、超声塑化头3与所述动模板104的距离h1和超声频率f1数据存储在控制模块中;
[0053]
当聚合物流至模芯2的模腔8远端时,安装在进料口远端模芯2底面模腔8壁上的第二模腔温度传感器12将测量此时聚合物的温度f,若测量到的温度f低于所述第二模腔温度传感器12设置下限阈值f3时,则控制模块发送指令给加热电阻丝17,增加加热电阻功率,提升冷却油温度t0,当测量到的温度f高于第二模腔温度传感器12设置下限阈值f3时,保持加热电阻功率,同时将此时冷却油温度t1和加热电阻丝17功率数据存储在控制模块中;
[0054]
s2.保压阶段:随着模芯2的模腔8内被充满聚合物时,压力传感器感应模腔8内的压力变化,并控制送料推杆501的送料速度;
[0055]
具体的,安装在进料口远端模芯2底面模腔8壁上的压力传感器402接收到压力信号e0,若测量到的压力e0低于模芯2进料口远端的所述模腔压力传感器13设置下限阈值e2时,此时增加送料压力p1和送料速度v1,直至达到压力传感器阈值下限e2;若测量到的压力e0高于模芯2进料口远端的所述模腔压力传感器13设置上限阈值e1时,此时减小送料压力p1和送料速度v1,使压力e0符合要求,然后将此时的送料压力p1和送料速度v1存储在控制芯片701中;
[0056]
s3.冷却阶段:超声塑化头3停止振动,保持送料压力不变,同时对冷却油进行泄
压,使冷却油流回小油箱15,并保持小油箱15内冷却油温度不变,聚合物产品开始冷却,当进料口流道10表面的第一模腔温度传感器11测量的温度f0和进料口远端模芯2底面模腔8壁上的第二模腔温度传感器12测量的温度f都低于预设的凝固阈值c时,此时系统默认聚合物产品完成冷却,送料推杆501被锁死,动模液压装置103带动动模液压杆102开始下行,此时送料推杆501和上顶杆601同时作用于聚合物产品,聚合物产品被顶出,此时完成一整套聚合物生产流程;
[0057]
s4.更新阶段:系统根据不同时间段对存储在控制模块中的系统参数曲线和工艺参数曲线进行更新,来进行下一次生产,直至工艺符合所有的设置条件,生成最优方案,锁定所有系统参数曲线和工艺参数曲线后将不执行更新阶段。
[0058]
可以理解的,以上实施例仅表达了本发明的优选实施方式,其描述较为具体和详细,但并不能因此而理解为对本发明专利范围的限制;应当指出的是,对于本领域的普通技术人员来说,在不脱离本发明构思的前提下,可以对上述技术特点进行自由组合,还可以做出若干变形和改进,这些都属于本发明的保护范围;因此,凡跟本发明权利要求范围所做的等同变换与修饰,均应属于本发明权利要求的涵盖范围。