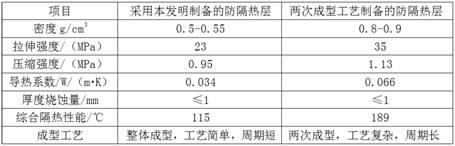
1.本发明涉及到一种低密度近零烧蚀复合材料的成型方法,属航空航天飞行器防隔热层制备领域。
背景技术:2.航天飞行器在大气层内高超速飞行,会受到严重的气动加热的影响,防隔热问题是航天飞行器设计面临的关键问题,随着长时间全程在大气层内高超声速飞行器的研制,对防隔热系统提出了轻质、低烧蚀和高效隔热的要求。
3.目前常见的防隔热层制备方法为高密度机织物防热层+低密度气凝胶隔热层,即预制体外层为2
‑
5层高密度酚醛树脂预浸料,内层制备成大小不等的网格区域,网格区域内填充5
‑
20mm低密度气凝胶材料。气凝胶与酚醛预浸料通过石英纤维缝合的方式连接,最后通过整体模压成型。该工艺制备的防隔热层抗烧蚀性能好,力学性能高,成型工艺简单。但该工艺制备的防隔热层材料存在大量的高密度网格筋加强区,使得材料整体密度偏高,且高密度网格筋加强区部位隔热性能较差,无法满足长时间高超声速飞行的要求。
4.另一种防隔热层制备方法为两次成型制备防隔热层,将防热层及轻质隔热材料进行组合,然后再依次固化成型,外层为2
‑
5层高密度预浸料,内层为10
‑
20mm低密度棉毡材料,外层材料采用模压工艺成型,内层材料采用rtm工艺成型。该工艺制备的防隔热层密度低,隔热性能好。但该工艺制备的防隔热层不同材料之间存在性能不匹配、热应力集中的问题,且工艺复杂、产品制备周期长。
5.因此,有必要设计一种超低密度的防隔热材料。要求整体净尺寸一体化成型,工艺简单,产品制备周期短;抗烧蚀性能好且具有高效隔热性能;整体性好,能够满足航空航天飞行器长时间高超声速飞行的要求。
技术实现要素:6.本发明的目的在于:提供一种低密度近零烧蚀复合材料的成型方法。防隔热层材料采用梯度密度设计,内层为低密度石英针刺毡隔热层材料,外层采用高密度2.5d石英纤维机织物防热层材料,内层采用三维针刺的方式成型针刺毡,外层采用缝合工装预压后缝合2.5d机织物,再合模整体rtm注胶成型。防隔热层整体性好,工艺简单,外形轮廓无需加工,适合大尺寸异形产品的整体成型。
7.本发明的技术方案是:一种低密度近零烧蚀复合材料的成型方法。它包括以下步骤: 1)、使用80目砂纸将金属壳体打磨粗糙,使用丙酮擦拭干净,静置30min以上使丙酮挥发干净。
8.2)、使用2
‑
5层石英针刺网胎预先z向针刺制备成针刺毡平板,然后根据所需厚度将针刺毡平板随形铺放到金属壳体上,并逐层进行z向针刺。使针刺毡能够随形紧实包覆在金属壳体上。然后使用蒙皮预压,使针刺毡具有一定的厚度及密度。
9.3)、针刺毡缝合完成后,借助缝合工装在针刺毡表面缝合1
‑
5层2.5d石英机织物,先将2.5d石英机织物铺在针刺毡上,然后沿舱段迎风面从两边依次向背风面组装缝合工装阴模进行预压,预压时间不小于24h,预压完成后,拆卸阴模,将机织物与针刺毡进行缝合,缝合方向为沿轴向缝合,使其成为一个整体。
10.4)、搭接处使用抽纱搭接缝合或对接缝合,为提高搭接处结构强度,可在搭接部位覆盖一层0.2
‑
1mm机织物,将此机织物与内层织物缝合连接。缝合完成后再组装缝合工装阴模进行预压定型,预压时间不小于24h。
11.5)、按照阴模侧板、上盖板、底板的拆卸顺序将金属壳体组件及织物预制体从缝合工装中拆卸出来。
12.6)、使用铜铲清理成型模具表面树脂,使用脱脂纱布蘸无水乙醇清理成型模具阴模內型面,使其光洁、无杂物。静置30min以上使酒精完全挥发,然后刷涂脱模剂,先用干净棉丝/脱脂纱布蘸少许脱模剂将模具整个外表面涂覆1遍,然后用干净棉丝将整个模具擦干。每隔至少(20
‑
30)min涂覆1遍,至少刷涂2遍,最后一遍刷涂后至少放置1小时方可使用。然后再安装密封条。
13.7)、按照成型模具合模要求将阴模及盖板组装起来,并用螺钉锁紧,使模具合模间隙≤0.1mm。
14.8)、通过氮气瓶向模具型腔充0.2mpa气压,保压30min,压力表显示值下降不超过0.05mpa。
15.9)、清洗注胶机,称取适量树脂转移到注胶机料筒中,如温度过低,可根据需要将模具及树脂进行预热。
16.10)、树脂脱泡,将注胶机料筒接到真空泵上,抽真空排泡,抽真空时间为10
‑
20min。
17.11)、将模具进胶端球阀通过四氟管连接到注胶机上,将模具出胶端球阀连接到真空泵上,打开真空泵对模具进行抽真空,抽真空时间不小于60min。
18.12)、打开注胶机出胶口阀门,开始真空吸附树脂,并开始计时。待模具小端面出胶管全部出胶后,计时结束。
19.13)、通过氮气瓶向注胶机中充0.1
‑
0.3mpa压力,保压10min,进行排泡,待四个出胶口均无气泡冒出时,关闭阀门,按照此方法排泡3次,直到无气泡。待排完泡后关闭进胶阀及出胶阀,拆掉注胶管及出胶管。将模具吊运到烘箱中进行加热固化。
20.14)、开启烘箱开始加热固化,固化条件为:室温—80℃,升温时间为120min,保温时间90min,80℃—105℃升温时间为50min,保温时间为500min。
21.15)、固化完成后自然降温至40℃拆模,使用什锦锉打磨试验件各边角毛刺,然后进行烘干,烘干条件:rt
→
80℃(升温时间120min,保温时间540min)烘干完成后关闭烘箱,自然降温至40℃以下取出产品;然后进行内部质量检验得到净尺寸产品。
22.所述步骤3中针刺毡厚度为17
‑
21mm,体密度为0.15
‑
0.25g/cm3。
23.所述步骤3中勾缝机织物厚度为2
‑
4mm,纤维体积含量为37
‑
45%。
24.所述步骤8中,可根据低密度树脂粘度确定预热温度,树脂粘度控制在200mpa
ꢀ▪
s以内,当温度<15℃时,可将树脂及模具预热到25℃。温度≥15℃时可不用预热。
25.所述步骤9中,真空脱泡的真空度为0.09至0.1mpa。
26.所述步骤12中,真空吸附树脂的真空度为0.09至0.1mpa。
27.本发明的有益效果在于:预制体外层为高密度2.5d石英纤维机织物防热材料,内层为低密度石英纤维针刺毡隔热材料,一次注胶整体成型,采用溶胶
‑
凝胶工艺制备成纳米孔结构复合材料。材料结构较为均一,加强区较少,且整体为纳米孔结构复合材料,隔热性能好,无隔热性能差区域。
28.该体系材料增强材料均为石英纤维织物,树脂为低密度酚醛杂化树脂,一次注胶固化,整体成型,能够避免不同树脂、不同固化工艺带来的性能不匹配、热应力集中的问题。且工艺简单,制备周期短。
29.预制体采用缝合工装预压后进行缝合,预制体尺寸精确,制备出来的产品粗胚表观缺胶、富树脂等缺陷较少。按照此工艺方法,该材料体系防隔热材料密度可达到0.5
‑
0.65g/cm3,相比于目前常见的0.8
‑
1.2g/cm3密度的防隔热材料,其在轻质化方面具有很大的优势,为后续航空航天飞行器防隔热材料的一个重要发展方向。
30.具体实施方式1使用80目砂纸将金属壳体打磨粗糙,使用丙酮擦拭干净,静置30min以上使丙酮挥发干净。
31.使用5层0.4mm石英针刺网胎预先z向针刺制备成2mm针刺毡平板,然后根据所需厚度将10层针刺毡平板随形铺放到金属壳体上,并逐层进行z向针刺。使针刺毡能够随形紧实包覆在金属壳体上,然后使用工艺蒙皮进行预压,预压时间不小于12h,使针刺毡厚度为20(
‑
1,1)mm。
32.针刺毡缝合完成后,借助缝合工装在针刺毡表面缝合1层4mm2.5d石英机织物,先将2.5d石英机织物铺在针刺毡上,然后沿舱段迎风面从两边依次向背风面组装缝合工装阴模进行预压,预压时间不小于24h,预压完成后,拆卸阴模,将机织物与针刺毡进行缝合,缝合方向为沿轴向缝合,使其成为一个整体。
33.搭接处使用抽纱搭接方式缝合,在搭接部位覆盖一层1mm机织物,将此机织物与内层织物缝合连接。缝合完成后再组装缝合工装阴模进行预压定型,预压时间不小于24h。
34.按照阴模侧板、上盖板、底板的拆卸顺序将金属壳体组件及织物预制体从缝合工装中拆卸出来。
35.使用铜铲清理成型模具表面树脂,使用脱脂纱布蘸无水乙醇清理成型模具阴模內型面,使其光洁、无杂物。静置30min以上使酒精完全挥发,然后刷涂脱模剂,先用干净棉丝/脱脂纱布蘸少许脱模剂将模具整个外表面涂覆1遍,然后用干净棉丝将整个模具擦干。每隔至少(20
‑
30)min涂覆1遍,至少刷涂2遍,最后一遍刷涂后至少放置1小时方可使用。然后再安装密封条。
36.按照成型模具合模要求将阴模及盖板组装起来,并用螺钉锁紧,使模具合模间隙≤0.1mm。通过氮气瓶向模具型腔充0.2mpa气压,保压30min,压力表显示值下降不超过0.05mpa。
37.清洗注胶机,称取适量树脂转移到注胶机料筒中,如温度过低,可根据需要将模具及树脂进行预热。将注胶机料筒接到真空泵上,抽真空排泡,抽真空时间为10
‑
20min。
38.将模具进胶端球阀通过四氟管连接到注胶机上,将模具出胶端球阀连接到真空泵上,打开真空泵对模具进行抽真空,抽真空时间不小于60min。打开注胶机出胶口阀门,开始
真空吸附树脂,并开始计时。待模具小端面出胶管全部出胶后,计时结束。
39.通过氮气瓶向注胶机中充0.2mpa压力,保压10min,进行排泡,待四个出胶口均无气泡冒出时,关闭阀门,按照此方法排泡3次,直到无气泡。待排完泡后关闭进胶阀及出胶阀,拆掉注胶管及出胶管。将模具吊运到烘箱中进行加热固化。
40.开启烘箱开始加热固化,固化条件为:室温—80℃,升温时间为120min,保温时间90min,80℃—105℃,升温时间为50min,保温时间为500min。固化完成后自然降温至40℃拆模,使用什锦锉打磨试验件各边角毛刺,然后进行烘干,烘干条件:rt
→
80℃(升温时间120min,保温时间540min)烘干完成后关闭烘箱,自然降温至40℃以下取出产品。然后进行内部质量检验得到净尺寸产品。
41.为了表明本发明制备的防隔热层各项性能,在同等条件下对本发明制备的防隔热层和两次成型工艺制备的防隔热层进行了对比试验,其具体结果如下表:。
42.具体实施方式2使用80目砂纸将金属壳体打磨粗糙,使用丙酮擦拭干净,静置30min以上使丙酮挥发干净。
43.使用5层0.4mm石英针刺网胎预先z向针刺制备成2mm针刺毡平板,然后根据所需厚度将9层针刺毡平板随形铺放到金属壳体上,并逐层进行z向针刺。使针刺毡能够随形紧实包覆在金属壳体上,然后使用工艺蒙皮进行预压,预压时间不小于12h,使针刺毡厚度为18(
‑
1,1)mm。
44.针刺毡缝合完成后,借助缝合工装在针刺毡表面缝合1层4mm2.5d石英机织物以及一层2mm2.5d机织物,先将2.5d石英机织物铺在针刺毡上,然后沿舱段迎风面从两边依次向背风面组装缝合工装阴模进行预压,预压时间不小于24h,预压完成后,拆卸阴模,将机织物与针刺毡进行缝合,缝合方向为沿轴向缝合,使其成为一个整体。
45.搭接处使用抽纱搭接方式缝合,在搭接部位覆盖一层1mm机织物,将此机织物与内层织物缝合连接。缝合完成后再组装缝合工装阴模进行预压定型,预压时间不小于24h。
46.按照阴模侧板、上盖板、底板的拆卸顺序将金属壳体组件及织物预制体从缝合工装中拆卸出来。
47.使用铜铲清理成型模具表面树脂,使用脱脂纱布蘸无水乙醇清理成型模具阴模內型面,使其光洁、无杂物。静置30min以上使酒精完全挥发,然后刷涂脱模剂,先用干净棉丝/脱脂纱布蘸少许脱模剂将模具整个外表面涂覆1遍,然后用干净棉丝将整个模具擦干。每隔至少(20
‑
30)min涂覆1遍,至少刷涂2遍,最后一遍刷涂后至少放置1小时方可使用。然后再安装密封条。
48.按照成型模具合模要求将阴模及盖板组装起来,并用螺钉锁紧,使模具合模间隙≤0.1mm。通过氮气瓶向模具型腔充0.2mpa气压,保压30min,压力表显示值下降不超过
0.05mpa。
49.清洗注胶机,称取适量树脂转移到注胶机料筒中,如温度过低,可根据需要将模具及树脂进行预热。将注胶机料筒接到真空泵上,抽真空排泡,抽真空时间为10
‑
20min。
50.将模具进胶端球阀通过四氟管连接到注胶机上,将模具出胶端球阀连接到真空泵上,打开真空泵对模具进行抽真空,抽真空时间不小于60min。打开注胶机出胶口阀门,开始真空吸附树脂,并开始计时。待模具小端面出胶管全部出胶后,计时结束。
51.通过氮气瓶向注胶机中充0.2mpa压力,保压10min,进行排泡,待四个出胶口均无气泡冒出时,关闭阀门,按照此方法排泡3次,直到无气泡。待排完泡后关闭进胶阀及出胶阀,拆掉注胶管及出胶管。将模具吊运到烘箱中进行加热固化。
52.开启烘箱开始加热固化,固化条件为:室温—80℃,升温时间为120min,保温时间90min,80℃—105℃升温时间为50min,保温时间为500min。固化完成后自然降温至40℃拆模,使用什锦锉打磨试验件各边角毛刺,然后进行烘干,烘干条件:rt
→
80℃(升温时间120min,保温时间540min)烘干完成后关闭烘箱,自然降温至40℃以下取出产品。然后进行内部质量检验得到净尺寸产品。
53.为了表明本发明制备的防隔热层各项性能,在同等条件下对本发明制备的防隔热层和两次成型工艺制备的防隔热层进行了对比试验,其具体结果如下表:。
54.具体实施方式3使用80目砂纸将金属壳体打磨粗糙,使用丙酮擦拭干净,静置30min以上使丙酮挥发干净。
55.使用5层0.4mm石英针刺网胎预先z向针刺制备成2mm针刺毡平板,然后根据所需厚度将12层针刺毡平板随形铺放到金属壳体上,并逐层进行z向针刺。使针刺毡能够随形紧实包覆在金属壳体上,然后使用工艺蒙皮进行预压,预压时间不小于12h,使针刺毡厚度为20(
‑
1,1)mm。
56.针刺毡缝合完成后,借助缝合工装在针刺毡表面缝合1层4mm2.5d石英机织物,先将2.5d石英机织物铺在针刺毡上,然后沿舱段迎风面从两边依次向背风面组装缝合工装阴模进行预压,预压时间不小于24h,预压完成后,拆卸阴模,将机织物与针刺毡进行缝合,缝合方向为沿轴向缝合,使其成为一个整体。
57.搭接处使用抽纱搭接方式缝合,在搭接部位覆盖一层1mm机织物,将此机织物与内层织物缝合连接。缝合完成后再组装缝合工装阴模进行预压定型,预压时间不小于24h。
58.按照阴模侧板、上盖板、底板的拆卸顺序将金属壳体组件及织物预制体从缝合工装中拆卸出来。
59.使用铜铲清理成型模具表面树脂,使用脱脂纱布蘸无水乙醇清理成型模具阴模內
型面,使其光洁、无杂物。静置30min以上使酒精完全挥发,然后刷涂脱模剂,先用干净棉丝/脱脂纱布蘸少许脱模剂将模具整个外表面涂覆1遍,然后用干净棉丝将整个模具擦干。每隔至少(20
‑
30)min涂覆1遍,至少刷涂2遍,最后一遍刷涂后至少放置1小时方可使用。然后再安装密封条。
60.按照成型模具合模要求将阴模及盖板组装起来,并用螺钉锁紧,使模具合模间隙≤0.1mm。通过氮气瓶向模具型腔充0.2mpa气压,保压30min,压力表显示值下降不超过0.05mpa。
61.清洗注胶机,称取适量树脂转移到注胶机料筒中,如温度过低,可根据需要将模具及树脂进行预热。将注胶机料筒接到真空泵上,抽真空排泡,抽真空时间为10
‑
20min。
62.将模具进胶端球阀通过四氟管连接到注胶机上,将模具出胶端球阀连接到真空泵上,打开真空泵对模具进行抽真空,抽真空时间不小于60min。打开注胶机出胶口阀门,开始真空吸附树脂,并开始计时。待模具小端面出胶管全部出胶后,计时结束。
63.通过氮气瓶向注胶机中充0.2mpa压力,保压10min,进行排泡,待四个出胶口均无气泡冒出时,关闭阀门,按照此方法排泡3次,直到无气泡。待排完泡后关闭进胶阀及出胶阀,拆掉注胶管及出胶管。将模具吊运到烘箱中进行加热固化。
64.开启烘箱开始加热固化,固化条件为:室温—80℃,升温时间为120min,保温时间90min,80℃—105℃升温时间为50min,保温时间为500min。固化完成后自然降温至40℃拆模,使用什锦锉打磨试验件各边角毛刺,然后进行烘干,烘干条件:rt
→
80℃(升温时间120min,保温时间540min)烘干完成后关闭烘箱,自然降温至40℃以下取出产品。然后进行内部质量检验得到净尺寸产品。
65.为了表明本发明制备的防隔热层各项性能,在同等条件下对本发明制备的防隔热层和两次成型工艺制备的防隔热层进行了对比试验,其具体结果如下表:。
66.具体实施方式4使用80目砂纸将金属壳体打磨粗糙,使用丙酮擦拭干净,静置30min以上使丙酮挥发干净。
67.使用5层0.4mm石英针刺网胎预先z向针刺制备成2mm针刺毡平板,然后根据所需厚度将11层针刺毡平板随形铺放到金属壳体上,并逐层进行z向针刺。使针刺毡能够随形紧实包覆在金属壳体上,然后使用工艺蒙皮进行预压,预压时间不小于12h,使针刺毡厚度为18(
‑
1,1)mm。
68.针刺毡缝合完成后,借助缝合工装在针刺毡表面缝合1层4mm2.5d石英机织物以及一层2mm2.5d机织物,先将2.5d石英机织物铺在针刺毡上,然后沿舱段迎风面从两边依次向背风面组装缝合工装阴模进行预压,预压时间不小于24h,预压完成后,拆卸阴模,将机织物
与针刺毡进行缝合,缝合方向为沿轴向缝合,使其成为一个整体。
69.搭接处使用抽纱搭接方式缝合,在搭接部位覆盖一层1mm机织物,将此机织物与内层织物缝合连接。缝合完成后再组装缝合工装阴模进行预压定型,预压时间不小于24h。
70.按照面板、上盖板、底板的拆卸顺序将金属壳体组件及织物预制体从缝合工装中拆卸出来。
71.使用铜片清理模具表面树脂,使用脱脂纱布蘸无水乙醇清理阴模內型面,使其光洁、无杂物。静置30min以上使酒精完全挥发,然后刷涂脱模剂,先用干净棉丝/脱脂纱布蘸少许脱模剂将模具整个外表面涂覆1遍,然后用干净棉丝将整个模具擦干。每隔至少(20
‑
30)min涂覆1遍,至少刷涂2遍,最后一遍刷涂后至少放置1小时方可使用。然后再安装密封条。
72.按照模具合模要求将阴模及盖板组装起来,并用螺钉锁紧,使模具合模间隙≤0.1mm。通过氮气瓶向模具型腔充0.2mpa气压,保压30min,压力表显示值下降不超过0.05mpa。
73.清洗注胶机,称取适量树脂转移到注胶机料筒中,如温度过低,可根据需要将模具及树脂进行预热。将注胶机料筒接到真空泵上,抽真空排泡,抽真空时间为10
‑
20min。
74.将模具进胶端球阀通过四氟管连接到注胶机上,将模具出胶端球阀连接到真空泵上,打开真空泵对模具进行抽真空,抽真空时间不小于60min。打开注胶机出胶口阀门,开始真空吸附树脂,并开始计时。待模具小端面出胶管全部出胶后,计时结束。
75.通过氮气瓶向注胶机中充0.2mpa压力,保压10min,进行排泡,待四个出胶口均无气泡冒出时,关闭阀门,按照此方法排泡3次,直到无气泡。待排完泡后关闭进胶阀及出胶阀,拆掉注胶管及出胶管。将模具吊运到烘箱中进行加热固化。
76.开启烘箱开始加热固化,固化条件为:室温—80℃,升温时间为120min,保温时间90min,80℃—105℃升温时间为50min,保温时间为500min。固化完成后自然降温至40℃拆模,使用什锦锉打磨试验件各边角毛刺,然后进行烘干,烘干条件:rt
→
80℃(升温时间120min,保温时间540min)烘干完成后关闭烘箱,自然降温至40℃以下取出产品。然后进行内部质量检验得到净尺寸产品。
77.为了表明本发明制备的防隔热层各项性能,在同等条件下对本发明制备的防隔热层和两次成型工艺制备的防隔热层进行了对比试验,其具体结果如下表: