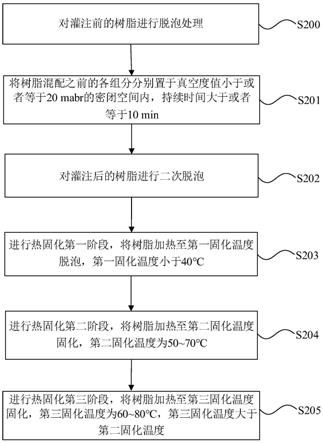
1.本发明涉及一种聚氨酯叶片的成型方法。
背景技术:2.目前风力发电叶片,在生产过程中通常采用双组份环氧灌注体系树脂,即体系在一定的负压条件下,树脂由外界注入到增强材料中,然后固化成型,现有技术中为了优化叶片质量,缩短生产周期,开发出了由多元醇(拜多78bd085)和异氰酸酯(德士模多44cp20)组成的热固性聚氨酯树脂,层合板力学性能、层间剪切性能和抗疲劳性能均满足风力涡轮机的风轮叶片,以该聚氨酯树脂体系与增强材料来制备风力发电叶片复合材料不仅能够明显降低重量,进而降低叶片整体的重量,来达到轻量化要求,而且,其相对便宜的树脂单价可以降低成本。
3.cn110884167a公开一种风力发电叶片聚氨酯树脂灌注结构及成型方法,通过调整优化管路流道设计,避免了少量位置由于流道设计不合理而导致的灌注时间延长,从而了提升生产效,改善聚氨酯复合材料制品在制造过程中易出现的灌注不良,并降低成型过程中的风险。cn112936910a公开一种兆瓦级风电叶片一体在线灌注设备,使得整个灌注系统处于一个密闭的空间当中,这样也减少的叶片气泡的数量,节约了维修成本,降低了人力成本,提高了产品良品率。cn107848158b公开一种制作风轮机叶片的方法,所述方法进一步包括在将所述树脂供应至所述模具之前,将所述第一区带中的所述模具预加热至第一温度,并且将所述第二区带中的所述模具预加热至大于所述第一温度的第二温度,即根据叶片各区域结构层厚度的不同选择不同的加热方式,使得获得低粘度树脂快速灌注的目的,来提高叶片制作效率,降低灌注耗时。cn109203513a公开一种内应力发白的解决方法,是借助调整预固化阶段和后固化阶段,有效的降低了应力,实现了减缓应力发白问题的目的。尽管有以上公开,气泡进入结构层导致的增强材料浸润不良,主要有三方面原因,第一、以现有的灌注设备,脱泡时间较短,很难在满足树脂即混即用的同时将树脂中的气泡消除,导致聚氨酯树脂组合物中残留有气泡;第二、聚氨酯树脂组合物由于黏度较低(固化时间60min、25摄氏度条件下,多元醇粘度50
±
20mpa
·
s,异氰酸酯粘度约为287mpa
·
s),树脂在转运过程中内部胶液晃动极易产生大量气泡;第三、树脂在结构层中流动时,结构层中的空气也会形成气泡进入树脂中。加之树脂在40℃条件下快速凝胶固化的特性,更使得气泡来不及从结构层中溢散而残留在结构层内或者辅助材料表面,从而降低风机叶片的成型质量,产生较大的制造维修及后期维护成本。
技术实现要素:4.本发明要解决的技术问题是为了克服现有技术中用于成型叶片的聚氨酯树脂中的气泡进入结构层导致的浸润不良而降低叶片的成型质量的缺陷,提供一种聚氨酯叶片的成型方法。
5.本发明是通过下述技术方案来解决上述技术问题:一种聚氨酯叶片的成型方法,
其包括步骤:
6.s10:对灌注前的树脂进行脱泡处理;
7.s20:对灌注后的树脂进行二次脱泡。
8.在本方案中,灌注前脱泡处理可以除去树脂中大部分的气泡,二次脱泡可以除去灌注前树脂脱泡时残留的气泡以及在灌注过程中新产生的气泡,从而解决气泡进入结构层中导致的增强材料浸润不良的问题,提高了叶片的成型质量。
9.较佳地,所述二次脱泡在树脂热固化过程中进行。
10.在本方案中,若通过在树脂热固化之前进行二次脱泡,则需要额外增加脱泡设备,费时而且步骤繁琐;树脂热固化后叶片已成型,气泡无法脱去;本方案通过在热固化过程中进行二次脱泡,既能够解决气泡导致的缺陷问题,又能够在树脂固化的同时进行脱泡,提高了叶片的成型效率,兼顾质量与效率。
11.较佳地,步骤s20包括步骤s21:进行第一热固化阶段,将树脂加热至第一固化温度脱泡,所述第一固化温度小于40℃。
12.在本方案中,通过设置较低的第一固化温度,使树脂不会快速凝胶固化,便于将树脂中的气泡除去,进而使树脂得以充分浸润结构层,从而获得更优异的结构层浸润树脂的效果。
13.较佳地,步骤s21是通过对真空体系持续抽真空来实现的。
14.在本方案中,以现有的真空体系和真空设备营造真空状态,使树脂中混入的气泡在真空压力下被剥离,操作简单,提高装备利用率。
15.较佳地,将树脂加热至所述第一固化温度的时间为1~3h;或者将树脂加热至所述第一固化温度的升温速率为5~10min/℃。
16.在本方案中,采用缓慢逐渐升温的方式,既能降低能耗,又能够兼顾脱泡效果和固化成型效率。
17.较佳地,在步骤s20之后包括步骤s30:进行第二热固化阶段,将树脂加热至第二固化温度固化,所述第二固化温度为50~70℃。
18.在本方案中,聚氨酯树脂反应活性为40℃以上会快速发生交联凝胶反应以使得其硬化,在此过程中会伴随大量反应热产生,此反应热与设定的加热叠加会导致温度过高而产生模具损伤或者产品的其他缺陷,设定第二固化温度为50~70℃,此温度的设定是树脂的固化特性来确定的,可以满足树脂的反应需求,使得树脂快速凝胶固化,同时考虑树脂反应放热会使树脂的温度进一步升高的因素,避免温度过高导致的结构层表面“鼓包”和pvc泡沫“烤糊”缺陷的产生。
19.较佳地,将树脂加热至所述第二固化温度的时间为0.5~3h;或者将树脂加热至所述第二固化温度的升温速率为2~5min/℃。
20.在本方案中,采用较高的升温速率逐渐升温,既可以以较快的速度完成固化,又可以兼顾叶片成型质量和效率。
21.较佳地,在步骤s30之后包括步骤s40:进行第三热固化阶段,将树脂加热至第三固化温度固化,所述第三固化温度为60~80℃,所述第三固化温度大于所述第二固化温度。
22.在本方案中,第三热固化阶段采用较高的第三固化温度,可以加强树脂反应的程度,进而加强其硬度及相应的热变形性能,防止其因固化不足而产生的性能不符合要求或
在脱模、转运过程中导致的变形等,而且避免了在固化过程中气泡来不及溢出结构层以及树脂来不及浸润结构层而导致的浸润不良缺陷和表面大量气泡的产生。
23.较佳地,将树脂加热至所述第三固化温度的升温速率大于或者等于2.5℃/min。
24.在本方案中,设定较高的第三固化温度的升温速率,快速升温至恒温阶段,提高叶片成型效率。
25.较佳地,步骤s10包括步骤s11:将树脂混配之前的各组分分别置于真空度值小于或者等于20mabr的密闭空间内,持续时间大于或者等于10min。
26.在本方案中,使得树脂灌注前脱泡效果更优,除泡更彻底,减少灌注过程中混入增强材料内的气泡数量。
27.较佳地,所述成型方法包括步骤:在开始铺设结构层时对模具内部进行预热,预热温度为35~55℃。
28.在本方案中,设定预热的步骤,在结构层铺设过程中使结构层内部保持较高的温度,便于提高后续步骤中的除湿效率,同时结构层中的水汽除去的越彻底,后续固化过程中产生的气泡越少。
29.较佳地,所述成型方法包括步骤:在结构层铺设之后对结构层进行除湿,在除湿结束前关闭预热。
30.在本方案中,预热后结构层的温度高于聚氨酯树脂灌注的适宜温度,提前关闭预热可以对结构层进行降温,以满足聚氨酯树脂的灌注条件,缩短等待结构层降温的时间,提高叶片成型效率。
31.本发明的积极进步效果在于:灌注前脱泡处理可以除去树脂中大部分的气泡,二次脱泡可以除去灌注前树脂脱泡时残留的气泡以及在灌注过程中新产生的气泡,从而解决气泡进入结构层中导致的增强材料浸润不良的问题,提高了叶片的成型质量。
附图说明
32.图1为本发明实施例1的聚氨酯叶片的成型方法的流程图。
33.图2为本发明实施例2的聚氨酯叶片的成型方法的流程图。
34.图3为本发明实施例2的固化温度与树脂中气泡数量关系的示意图。
35.图4为本发明实施例2的固化温度与时间的变化关系的示意图。
36.图5为本发明实施例3的聚氨酯叶片的成型方法的流程图。
37.图6为本发明实施例3的预热温度和预热时间与气泡数量变化关系的示意图。
具体实施方式
38.下面通过实施例的方式进一步说明本发明,但并不因此将本发明限制在所述的实施例范围之中。
39.实施例1
40.如图1所示,在本实施例中,公开了一种聚氨酯叶片的成型方法,其包括步骤:
41.s101:对灌注前的树脂进行脱泡处理;
42.s102:对灌注后的树脂进行二次脱泡。
43.在本实施例中,灌注前脱泡处理可以除去树脂中大部分的气泡,二次脱泡可以除
去灌注前树脂脱泡时残留的气泡以及在灌注过程中新产生的气泡,从而解决气泡进入结构层中导致的增强材料浸润不良的问题,提高了叶片的成型质量。
44.在其他优选的实施例中,二次脱泡在树脂热固化过程中进行,通过在热固化过程中进行二次脱泡,既能够解决气泡导致的缺陷问题,又能够以较快的速度完成固化,兼顾叶片成型质量与效率。在其他实施例中,二次脱泡也可以不在热固化过程中进行,例如,可以在灌注之后不启动热固化操作,即不对树脂加热直接进行抽真空脱泡。
45.具体地,将至少一种增强材料和/或夹芯材料、导流介质放置于模具内;将上述体系密封并抽真空形成真空体系,然后进行除湿;然后灌注树脂,在固化过程中进行二次脱泡,待固化后脱模制得聚氨酯风机叶片。
46.具体地,在本实施例中,所采用的模具为叶片壳体模具、大梁模具或者腹板模具,所采用的增强材料为玻璃纤维纱/束编织物、碳纤维纱/束编织物、玻碳纱/束混编织物、拉挤板材/片材,短切纤维毡/网,芳纶纤维纱/束/编织物等,所采用的夹芯材料为pvc泡沫板、pet泡沫板等,泡沫板上表面或下表面至少一个方向具有树脂引流槽,引流槽的宽度为1~2mm,槽间距为≥15mm。
47.其中在增强材料和/或夹芯材料、导流介质放置于模具后,在增强材料和/或夹芯材料、导流介质表面至少覆盖一层真空袋膜,边缘处使用密封胶条密封,并至少留出一个树脂注入口刺穿真空袋膜,用于灌注树脂;通过管路将树脂注入口连接至树脂混合设备,并在管路上留出至少一个抽气通道,用于对结构层进行抽真空除湿;对模具进行加热及对真空体系抽真空至真空袋膜内部真空度值达到0~20mbar,加热温度为30~45℃,优选40℃,除湿时间为1~3h。
48.所采用的树脂为聚氨酯组分a和聚氨酯组分b的组合物,聚氨酯组分a为一种或多种异氰酸酯的组合物,聚氨酯组分b为一种或多种有机多元醇,其中对灌注前的树脂进行脱泡处理为分别对聚氨酯组分a和聚氨酯组分b进行脱泡处理,可以采用现有技术中对聚氨酯树脂的脱泡技术,作为优选可以对聚氨酯组分进行少量多次脱泡,脱泡后的聚氨酯组分a和聚氨酯组分b按80-86:100比例进行混配获得聚氨酯树脂组合物。
49.实施例2
50.如图2和图4所示,在本实施例中,公开了一种聚氨酯叶片的成型方法,包括步骤:
51.s200:对灌注前的树脂进行脱泡处理;
52.s202:对灌注后的树脂进行二次脱泡;
53.s203:进行第一热固化阶段,将树脂加热至第一固化温度脱泡,第一固化温度小于40℃。
54.在本实施例中,第一固化温度更优选小于或者等于35℃,如图5所示,本实施例所采用的第一固化温度为35℃,二次脱泡是在树脂热固化过程中进行的,通过设置较低的第一固化温度,使树脂不会快速凝胶固化,便于将树脂中的气泡除去,进而使树脂得以充分浸润结构层,从而获得更优异的结构层浸润树脂的效果。
55.在本实施例中,步骤s21是通过对真空体系持续抽真空来实现的。以现有的真空体系和真空设备营造真空状态,使树脂中混入的气泡在真空压力下被剥离而除去,操作简单,提高装备利用率。在其他实施例中,也可以采用其他方式除去气泡,不采用抽真空的方式。
56.在本实施例中,将树脂加热至第一固化温度的时间为1~3h;或者将树脂加热至第
一固化温度的升温速率为5~10min/℃。如图5所示,本实施例中采用的持续升温时间为1.5h,采用缓慢逐渐升温的方式,降低能耗,又能够兼顾脱泡效果和固化成型效率。在其他实施例中,也可以采用其他升温速率和加热时间。
57.在本实施例中,步骤s203之后包括步骤s204:进行第二热固化阶段,将树脂加热至第二固化温度固化,第二固化温度为50~70℃。如图5所示,在本实施例中第二固化温度为60℃,聚氨酯树脂的组合物反应活性为40℃以上会快速发生交联凝胶反应以使得其硬化,在此过程中会伴随大量反应热产生,此反应热与设定的加热叠加会导致温度过高而产生模具损伤或者产品的其他缺陷,设定第二固化温度为50~70℃,此温度的设定是树脂的固化特性来确定的,可以满足树脂的反应需求,使得树脂快速凝胶固化,同时考虑树脂反应放热会使树脂的温度进一步升高的因素,避免温度过高导致的结构层表面“鼓包”和pvc泡沫“烤糊”缺陷的产生。在本实施例中,由于固化速度比较快,在第二固化阶段也会有少量气泡溢出。在其他实施例中,也可以不设置第二热固化阶段,采用其他加热固化温度来固化成型。
58.在本实施例中,将树脂加热至第二固化温度的时间为0.5~3h;或者将树脂加热至第二固化温度的升温速率为2~5min/℃。如图5所示,在本实施例中,将树脂加热至第二固化温度的时间为2h,采用较高的升温速率逐渐升温,既可以以较快的速度完成固化,又可以兼顾叶片成型质量和效率。在其他实施例中,也可以采用其他升温速率和加热时间。
59.在本实施例中,在步骤s204之后包括步骤s205:进行第三热固化阶段,将树脂加热至第三固化温度固化,第三固化温度为60~80℃,第三固化温度大于第二固化温度。如图5所示,在本实施例中,所采用的第三固化温度为75℃,第三热固化阶段采用大于第二热固化温度的较高的第三固化温度,可以加强树脂反应的程度,进而加强其硬度及相应的热变形性能,防止其因固化不足而产生的性能不符合要求或在脱模、转运过程中导致的变形等,而且避免了在固化过程中气泡来不及溢出结构层以及树脂来不及浸润结构层而导致的浸润不良缺陷和表面大量气泡的产生。在其他实施例中,也可以不设置第三热固化阶段,采用其他加热固化温度来固化成型。
60.将树脂加热至第三固化温度的升温速率大于或者等于2.5℃/min,如图5所示,在本实施例中,第三固化温度的升温速率为2.5℃/min,快速升温至恒温阶段,持续1~4h即可,本实施例中优选1~3h,设定较高的第三固化温度的升温速率,快速升温至恒温阶段,可以提高叶片成型效率,根据大量实验数据所得一般聚氨酯树脂在固化完成后以其纯树脂的残余放热量来表征其是否满足固化要求,通过本实施例制作的风机叶片及其部件,取样测试残余放热≤30g/j(表示其固化度≥95%),力学性能完全满足要求,而且避免了在固化过程中气泡来不及溢散出结构层以及树脂来不及浸润结构层而导致的浸润不良缺陷和表面大量气泡的产生。在其他实施例中,也可以采用其他升温速率。
61.在本实施例中,步骤s200包括步骤步骤s201:将树脂混配之前的各组分分别置于真空度值小于或者等于20mabr的密闭空间内,持续时间大于或者等于10min。在其他实施例中,对灌注前的树脂也可以采用其他现有技术中的脱泡手段。
62.实施例3
63.本实施例和实施例1以及实施例2基本相同,特别之处如下:如图3所示,还包括步骤s300:在开始铺设结构层时对模具内部进行预热,预热温度为35~55℃,设定预热的步骤,在结构层铺设过程中使结构层内部保持较高的温度,便于提高后续步骤中的除湿效率,
如图6所示,提高预热温度或者延长预热时间也会降低气泡产生的数量,即结构层中的水汽除去的越彻底,后续固化过程中产生的气泡越少,此步骤为优选步骤,根据叶片制作所处的环境温度的变化而定,一般环境温度大于或者等于40℃可不开启预热。
64.在本实施例中,在步骤s300之后还包括步骤s301:在结构层铺设之后对结构层进行除湿,在除湿结束前关闭预热。预热后结构层的温度高于聚氨酯树脂灌注的适宜温度,提前关闭预热可以对结构层进行降温,以满足聚氨酯树脂的灌注条件,缩短等待结构层降温的时间,提高叶片成型效率。作为优选,可以结构层除湿结束前1~2h关闭预热步骤对结构层进行降温,以满足灌注条件,其灌注适宜温度为布层表面温度为25~35℃左右,在其他实施例中,也可以不在除湿前关闭预热,可以在除湿结束后另进行冷却的步骤,以达到聚氨酯树脂的灌注条件。虽然以上描述了本发明的具体实施方式,但是本领域的技术人员应当理解,这仅是举例说明,本发明的保护范围是由所附权利要求书限定的。本领域的技术人员在不背离本发明的原理和实质的前提下,可以对这些实施方式做出多种变更或修改,但这些变更和修改均落入本发明的保护范围。