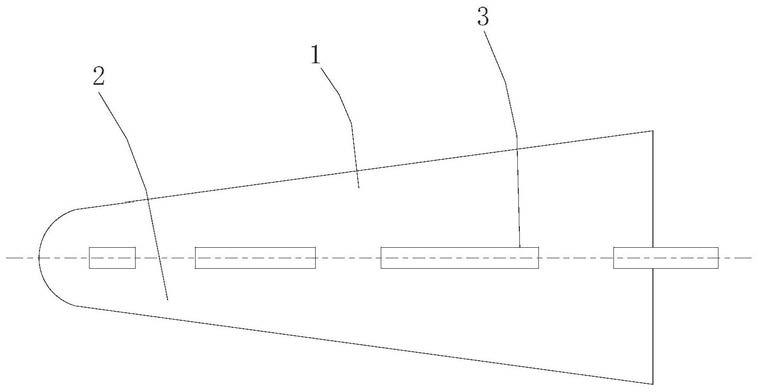
1.本发明属于复合材料成型领域,特别涉及一种舵和舵的制备工艺。
背景技术:2.应现代战略需要,由于飞行器在飞行阶段时,外部与空气摩擦产生的热量温度高,必须有热防护来保护飞行器不受到高温破坏。国外高马赫数飞机用热防护材料与结构的发展始于sr-71,上世纪60年代,形成以sr-71机用结构为代表的第一代热防护结构,这类防护结构以树脂基复合材料为基础(硅树脂、硅氧烷),将树脂基复合材料贴合于金属内蒙皮上,用于前缘热防护;上世纪90年代,形成以x-15为代表的第二代热防护结构,此时的钛合金生产技术已经成熟,x-15几乎全部使用钛合金作为外蒙皮,内部使用柔性热防护材料。本世纪初,形成以x-37b、x-43、x-51a为代表的第三代热防护结构,此时主要以陶瓷基复合材料和金属蜂窝为主干材料的热防护结构,这类结构构型相对负载,所用材料种类较多,隔热效果较为理想。
3.现有技术中,专利号:201920548128.x,发明名称:空气舵、空气舵连接组件和火箭,其公开了一种空气舵,包括防热套、连接件和芯体,防热套与芯体通过连接件可拆卸连接,连接件的数量至少为3个,连接件包括螺钉,防热套和芯体之间还包括粘胶层,通过粘胶使得防热套和芯体的固定更稳固,芯体和连接件均位于防热套的内部,防热套与芯体之间设有空腔,空腔的界面与芯体的侧截面相对应,达到隔热的同时可以使得芯体在受热膨胀的情况下填充空腔,避免了芯体积压防热套,因芯体的主要材料为金属,防热套的主要材料为高硅氧酚醛,金属在高温下的膨胀系数高于高硅氧酚醛受热使得膨胀系统,避免了在高温情况下造成防热套局部开裂影响空气舵的防热性能,其为一个多层结构,需要分为多个零部件进行加工,且仅有外部的防热套具有热防护的能力,热防护的承受能力不足。
技术实现要素:4.针对现有技术存在的问题,本发明设计了一种适用于飞行器的舵以及舵的生产工艺。
5.本发明的技术方案如下:一种舵,其特征在于:包括位于中间的金属骨架,在金属骨架的两侧分别设有第一隔热舵体和第二隔热舵体,第一隔热舵体和第二隔热舵体将金属骨架夹在中间固化成型为一体。
6.进一步的说,所述的第一隔热舵体和第二隔热舵体由高硅氧纤维和酚醛树脂模压而成。
7.进一步的说,所述的第一隔热舵体和第二隔热舵体上设有相互配合的连接结构。
8.舵的制备工艺,其包括用于固定金属骨架的骨架固定模、上预压模组以及下预压模组,其特征在于:包括以下步骤:s1:将舵面划分为若干个小区域,并通过重量计算得到各个小区域内所需的填料
的重量;s2:根据步骤s1中计算得到的各个小区域内的填料的重量进行准备填料,并将准备好的填料放置在保温环境中,所述的保温环境的温度是40-50℃;s3:先将上预压模组与骨架固定模进行组装,对预压模组和骨架固定模进行预热,填料前的压制模具的温度在65-75℃的范围内;s4:将步骤s2中准备的各个小区域内的填料放入各个小区域对应的上预压模组内;并进行预压定型,并通过紧固件对上预压模组进行固定,s5:翻转上预压模组和骨架固定模,并拆除骨架固定模,更换下预压模组,并重复步骤s3和步骤s4;将预先准备好的填料填入下预压模组对应的小区域内并进行预压定型,s6:对上预压模组和下预压模组进行整体升温加压固化,固化时间为4-6h,最后待上预压模组和下预压模组降温至50℃时泄压脱模。
9.进一步的说,脱模后根据产品变形数据可进行后固化处理,后固化处理的方式为:烘箱120℃,2h。
10.进一步的说,所述的步骤s4和步骤s5中的预压定型中预压的压力从10t逐步加压至100t,并使上预压模组和下预压模组合模缝小于等于0.1mm。
11.进一步的说,所述的步骤s6升温为每小时20-30℃。
12.进一步的说,所述的步骤s2中是通过油浴的方式对模具进行预热。
13.综上所述,本发明具有以下有益效果:1、本发明对舵的结构进行了改进,采用基于金属骨架的对称的结构设计,位于金属骨架两侧的第一隔热舵体和第二隔热舵体与金属骨架共固化一体成型,第一隔热舵体和第二隔热舵体由模压成型,结构简单,方便生产制造,改变了现有舵的结构形式,减少了零部件的设计和生产,降低了舵的生产成本。
14.2、本发明改进了舵的生产工艺,涉及一种用于高硅氧纤维/酚醛树脂复合材料生产舵的生产工艺,该工艺采用对产品区域合理划分,并精确向各个区域内填入合适质量的复合材料,以及采用与上述规划向配合的装模温度、升温速率、成型温度、模压压力和模压时间,在确保产品外部质量的同时也保证了产品内部质量的稳定性,从而获得高质量的产品,产品的合格率也得到了大幅的提升。
附图说明
15.图1为舵的截面示意图;图2为步骤s3中上预压模组与骨架固定模组装后的示意图;图3为步骤s5中拆除骨架固定模后上预压模组与下预压模组连接后的示意图;图4为步骤s3中上预压模组与骨架固定模组装后的俯视示意图;图5为基于图4的步骤s1对舵面划分的示意图;图中1为第一隔热舵体,2为第二隔热舵体,3为金属骨架,4为上预压模组,5为骨架固定模,6为下预压模组,7为连接结构。
具体实施方式
16.为使本发明实施例的目的、技术方案和优点更加清楚,下面将结合本发明实施例
的附图,对本发明实施例的技术方案进行清楚、完整地描述。显然,所描述的实施例是本发明的一部分实施例,而不是全部的实施例。基于所描述的本发明的实施例,本领域普通技术人员在无需创造性劳动的前提下所获得的所有其他实施例,都属于本发明保护的范围。
17.从背景技术中可知,现有技术中的飞行器的舵的结构件都是采用在舵的外部设置防热层来进行防热,在一些高速和长距离飞行器中外层的防热结构可能无法满足防热的需求,故需要对舵的结构和防热能力进行改进。
18.故本发明先设计了一种舵的结构,一种舵,其特征在于:包括位于中间的金属骨架10,金属骨架采用耐热、强度高且质量轻的金属板材进行镂空加工而成,主要起到一个辅助支撑和连接外部结构的功能,在金属骨架10的两侧分别设有第一隔热舵体11和第二隔热舵体12,第一隔热舵体11和第二隔热舵体12将金属骨架10夹在中间固化成型为一体,首先,本发明设计了一种由对称的隔热舵体和金属骨架共固化成型的舵,结构简单,隔热舵体即为该舵的热防护结构,使得舵的热防护能力得到大幅提升,满足新型飞行器的设计需求。
19.进一步的说,所述的第一隔热舵体11和第二隔热舵体12由高硅氧纤维和酚醛树脂模压而成,为了达到热防护的需求,采用高硅氧纤维和酚醛树脂的复合材料作为隔热舵体的材料,高硅氧纤维作为增强材料,酚醛树脂作为耐烧蚀基体材料。进一步的说,所述的第一隔热舵体11和第二隔热舵体12上设有相互配合的连接结构,所述的连接结构为第一隔热舵体与第二隔热舵体的连接面上形成有对应的凸部或凹部,所述的凸部或凹部可以采用半圆球形、圆柱形以及其他多边形结构等;通过两者的配合,一方面,在两者连接面的延伸方向起到一个限位作用,避免两个隔热舵体出现相互错位裂开的问题,另一方面,连接结构也增大了第一隔热舵体和第二隔热舵体的连接面积,提升两者之间的连接可靠性,也避免出现剥离开裂的问题。
20.在此结构基础上,本发明还设计了适应该结构的舵的制备工艺,有效克服了制造中以高硅氧纤维和酚醛树脂作为隔热舵体在加工中存在的问题,保证了填料的均匀性,继而在确保产品外部质量的同时也保证了内部质量的稳定性,提升了产品的合格率,并提高了生产效率。
21.具体的制备工艺如下:舵的制备工艺,其包括用于固定金属骨架的骨架固定模、上预压模组以及下预压模组,其特征在于:包括以下步骤:s1:将舵面划分为若干个小区域,并通过重量计算得到各个小区域内所需的填料的重量;此处主要克服高硅氧纤维和酚醛树脂的复合材料制备零件存在的困难,现有技术中都是将一定量的高硅氧纤维和酚醛树脂的复合材料整体放入模压模具内,然后通过压力驱使复合材料向产品的各个方向流动来填满,形成产品,但由于复合材料的流动性的问题,一次模压无法成型,需要不断的填料和模压,每次填料模压后都会形成一个相对固化的结合面,造成产品整体的结构强度较差,而本实施例中通过对舵面进行划分,并且通过重量计算得到各个小区域所需的填料的重量,一次填料即可将各个小区域对应填料放入模具对应的小区域中,精确填料,一次模压即可基本成型,克服了现有技术中多次填料多次模压带来的产品质量问题,同时,也可以将产品各个区域内的密度控制在可控范围内,防止密度差异过大的问题;s2:根据步骤s1中计算得到的各个小区域内的填料的重量进行准备填料,并将准
备好的填料放置在保温环境中,所述的保温环境的温度是40-50℃;因为是划分多个区域的,所以准备填料需要一定的时间,故在完整全部的填料准备之间需要对已经准备的填料进行保藏,故需要对填料进行保温,来保证填料方放入模具的指定区域后的流动性;s3:先将上预压模组与骨架固定模进行组装,对预压模组和骨架固定模进行预热,填料前的压制模具的温度在65-75℃的范围内;由于高硅氧纤维和酚醛树脂的复合材料的特性,保证其在模压时的流动性,在此温度范围内,各个小区域内的复合材料模压的初始阶段具有最强的流动性,且不容易出现高硅氧纤维和酚醛树脂分离,出较量最小的情况;进一步的是,模具温度的均匀性可以确保产品整体的固化速率一致性,基于本发明中采用分小区域填料的方式,能够更好的服务于产品的固化过程,不会出现温度的差异过大导致产品不同部位的先后固化造成产品损伤的问题;s4:将步骤s2中准备的各个小区域内的填料放入各个小区域对应的上预压模组内;并进行预压定型,并通过紧固件对上预压模组进行固定,此处完成上预压模组的预压和定型,并进行固定,方便下预压模组进行填料、预压和定型;s5:翻转上预压模组和骨架固定模,并拆除骨架固定模,更换下预压模组,并重复步骤s3和步骤s4;将预先准备好的填料填入下预压模组对应的小区域内并进行预压定型,此处完成下预压模组的填料、预压和定型;s6:对上预压模组和下预压模组进行整体升温加压固化,固化时间为4-6h,最后待上预压模组和下预压模组降温至50℃时泄压脱模,此处对产品整体进行加压固化,所述加压为恒定的压力,压力保持为100t,所述升温为阶段升温的方式,即达到一个温度保持一定的时间,然后在升温并保持的过程,总的升温和保持的时间即为固化时间,阶段式升温避免过高的模温会使塑料外层因先受到模具的高温快速硬化,可以将内层硬化过程中的产生的低分子挥发物排出,有效降低了制品中的内应力,保证了产品的质量;进一步的说,脱模后根据产品变形数据可进行后固化处理,后固化处理的方式为:烘箱120℃,2h,述后固化处理是为提高质量,制品脱模后常在烘箱中进行后处理,目的是提高制品的固化反应程度,通过提高温度,使尚未反应的基团间继续交联增加密度,去掉残留挥发分同时消除产品内应力,提高强度,减少问题的产生;进一步的说,所述的步骤s4和步骤s5中的预压定型中预压的压力从10t逐步加压至100t,并使上预压模组和下预压模组合模缝小于等于0.1mm,预压过程是迫使材料充满型腔并进行预固化的过程,合适的压力能够使产品结构紧密,外观质量高,同时,加压时间也十分关键,只有当树脂反应过程中,分子量增加造成的年度增加时,适合加压,这样才能使树脂本身既能在热压力下流动而又同时使纤维同树脂一起流动,这样才能获得较好的产品质量,否则,制品会由加压不当造成纤维裸露或压实效果差的缺陷;并通过合模后的合模缝的大小来对预压定型进行初步的判断;进一步的说,所述的步骤s6升温为每小时20-30℃,分阶段的缓慢升温,可以避免升温太快造成固化不均匀产生内应力的问题,同时也兼顾效率的问题,保证了生产效率是,本发明中结合固化时间的阶段式升温过程如下:在70℃左右进行预压制,固化时对应的升温过程是:90℃1h——110℃1h——130℃1h——160℃2h。
22.进一步的说,所述的步骤s2中是通过油浴的方式对模具进行预热,油浴具有更好的温度稳定性, 能够确保模具温差不大于5℃,便于后续填料后的预压过程中填料的流动
性,从而能够获得更好的产品质量。
23.综上所述,本发明具有以下有益效果:1、本发明对舵的结构进行了改进,采用基于金属骨架的对称的结构设计,位于金属骨架两侧的第一隔热舵体和第二隔热舵体与金属骨架共固化一体成型,第一隔热舵体和第二隔热舵体由模压成型,结构简单,方便生产制造,改变了现有舵的结构形式,减少了零部件的设计和生产,降低了舵的生产成本。
24.2、本发明改进了舵的生产工艺,涉及一种用于高硅氧纤维/酚醛树脂复合材料生产舵的生产工艺,该工艺采用对产品区域合理划分,并精确向各个区域内填入合适质量的复合材料,以及采用与上述规划向配合的装模温度、升温速率、成型温度、模压压力和模压时间,在确保产品外部质量的同时也保证了产品内部质量的稳定性,从而获得高质量的产品,产品的合格率也得到了大幅的提升。