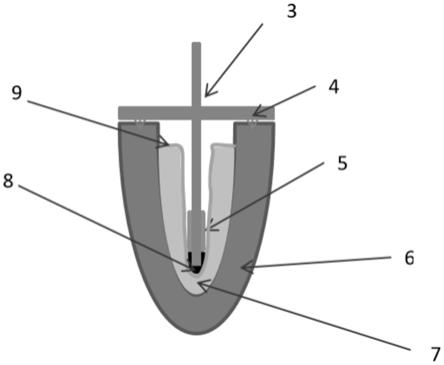
一种v形复合材料零件的补偿加压方法
技术领域
1.本发明属于复合材料制造领域,使用一种自主设计的装置在v形结构的复合材料零件成型过程中增大对v形结构尖部的压力,具体来讲就是提供一种在复合材料零件固化时在真空袋外辅助增压的装置,然后用该装置获得质量合格的v形复合材料产品。
背景技术:2.随着复合材料越来越多的应用到航空结构产品中,飞机的垂尾前缘整流罩目前也开始采用了复合材料作为其材质,但垂尾前缘整流罩多为v形结构,v形内部含有蜂窝夹芯,此种结构在热压罐成型的复合材料制造工艺中通常选用匹配零件v形外轮廓的阴模形式的模具进行成形,由于零件其v形尖端部位由于面积很小,很难在热压罐的气压环境中得到足够的压力,因此此类产品大量出现v形尖部加压不良,导致脱粘、分层、空隙密集等内部缺陷,这些内部质量问题导致零件迟迟不能研制成功,产生大量产品报废,造成很大的经济损失,并导致客户的不满。
技术实现要素:3.针对现有技术中存在的上述不足之处,本发明提供一种简单、操作方便的工艺方法,以获得复合材料v形结构在成型过程中对于v形尖端加压不足的部位进行加压补偿。
4.为解决以上问题,本发明采用如下的技术方案:
5.一种v形复合材料零件的补偿加压方法,所述补偿加压方法首先分析v形复合材料零件7的欠压位置及其成型模具6的结构,设计与其成型模具6可以组合固定的如图2所示的补偿加压装置,该装置包含施压杆3、模具定位板4(作为基础板)、施压弹簧5、压力分散过渡装置8,其中压力分散过渡装置8由如图1所示的与施压杆连接装置1和压力分散板2组成,该装置可以对v形复合材料零件7尖端部位加压较弱的位置,采用真空袋9进行外施压,所施加的压力可控且均匀分布在欠压位置,使其在补充加压的同时不会出现压痕阶差,这种补充加压弥补了v形复合材料零件7尖部面积较小导致的热压罐压力施加不足的问题,使得产品固化后内部质量能够的到较大的改善。所述补偿加压方法包括以下步骤:
6.第一步,制作压力分散板2:按表1的铺层将碳纤维织物预浸料后依次与未硫化橡胶铺叠在一起,封装真空袋,热压罐固化成形,固化温度180
±
5℃,固化压力700
±
30kpa,固化后形成压力分散板2。
7.表1压力分散板铺层
8.层号材料角度p1未硫化橡胶n/ap2碳纤维织物预浸料0
°
p3碳纤维织物预浸料45
°
p4碳纤维干布0
°
p5碳纤维织物预浸料45
°
p6碳纤维织物预浸料45
°
p7未硫化橡胶n/a
9.第二步,将与施压杆连接的装置1嵌入压力分散板2,使二者相对固定。
10.第三步,按零件7的v形外侧形面设计成形模具6,成型模具6采用普通钢制,阴模形式,阴模内部形面符合零件7的外形,框架结构,沿v形外形开口方向顶部设计水平台面,用于与模具定位板4进行固定。
11.第四步,将v形复合材料零件7的成型模具6进行铺叠前准备,涂刷脱模剂并烘干。
12.第五步,将v形复合材料零件7以正常阴模形式铺叠在成型模具6中,将v形复合材料零件用真空袋9真空封装,在成型模具6上固定本装置的模具定位板4,模具定位板4中部设有用于穿过施压杆3的通孔,固定的位置为设定施压杆位于欠压部位的正上方,在欠压位置放置已固定在一起的压力分散板2和与施压杆连接装置1,再将施压杆3压入已放置在欠压位置的于施压杆连接装置1中,并锁死施压杆,使其仅能向下移动,不能向上移动,然后调节施压弹簧5,使施压杆通过压力分散板施加的压力适宜,并留有热膨胀余量,之后一并进热压罐固化,得到内部质量合格的v形复合材料零件产品。
13.第六步,将压力分散板2和与施压头连接的装置1连接后在真空袋9外放入v形复合材料零件7欠压位置,确保压力分散板2随形贴合。
14.第七步,在欠压位置上方将基础板4与成型模具6固定,将施压杆3与模具定位板4相对固定锁死,使施压杆3只能向下移动不能向其他方向移动。
15.第八步,调节施压弹簧5的施压度,使得压力分散板2紧贴产品欠压位置真空袋9外,并对袋内产品施加一定的压力,在压紧欠压位置的前提下,再依据成型模具6的尺寸适当补充压紧施压弹簧一部分以补偿模具热膨胀。
16.第九步,将上述组合后共同移至热压罐,进行固化,固化按产品的固化参数进行,固化时热压罐的压力正常施加在产品表面,在v形尖部面积较小部位由施压杆、施压弹簧和压力分散板共同作用额外施压,保证适当补压,固化后脱模即得表面和内部质量良好的复合材料v形零件。
17.本发明具有如下的优点和有益效果为:
18.本发明能够利用在真空袋外部的装置,对袋内复合材料零件v形部位尖部位置由于面积过小导致的热压罐气压压力不足的情况进行局部部位的压力补偿,补偿压力直接作用于欠压位置,能够直接改善该处的内部质量,且施加的压力在欠压位置与其他位置存在分散过渡,避免出现局部压力过于集中导致的此处出现压痕、阶差等表面质量问题。
附图说明
19.图1是补充加压装置的结构示意图;
20.图2是压力分散过渡装置结构示意图。
21.图中:1与施压杆连接装置;2压力分散板;3施压杆;4模具定位板;5施压弹簧;6成型模具;7v形复合材料零件;8压力分散过渡装置;9真空袋。
具体实施方式
22.下面结合附图和实施例对本工艺方案进行详细地说明:
23.如图1所示,根据欠压位置的形状及欠压状态设计并制造压力分散过渡装置。如图2所示,将v形复合材料零件封装制袋,在成型模具6上固定本装置的模具定位板4,固定的位置为欠压部位的正上方,在欠压位置放置压力分散过渡装置8,再通过施压杆3将施压头压入欠压位置的压力分散过渡装置8中,并锁死施压杆3,使其仅能向下移动,不能向上移动,然后调节施压弹簧5,使施压头施加的压力适宜,并留有热膨胀余量,之后一并进热压罐固化,得到内部质量合格的v形复合材料零件产品。
24.本发明在真空袋9外利用机械加压装置进行加压,补偿了热压罐施加在产品v形部位压力不足的情况,同时采用压力分散过渡装置8调节了机械加压的压力分布不均情况,使其均匀分散,得到良好的产品内部质量,该装置的使用操作简单,易于掌握,制造成本低,便于推广,该技术节省了大量的生产成本,同时实现了复合材料v形结构制造的突破。
25.一种v形复合材料零件的补偿加压技术,包括以下步骤:
26.1)制作压力分散板2:按预设铺层将碳纤维织物预浸料、未硫化橡胶、压力条铺叠在一起,封装真空袋,热压罐固化成形,固化温度180℃,固化压力700kpa,固化后形成压力分散板2。
27.2)将与施压头连接的装置1嵌入分散板是二者相对固定。
28.3)将v形复合材料零件成型模具6进行铺叠前准备,涂刷脱模剂并烘干固化。
29.4)将v形复合材料零件产品7正常阴模形式铺叠在模具6中,按图2所示正常封装制真空袋9,注意真空袋褶皱打在压力分散板之外,欠压位置真空袋不要打褶。
30.5)将压力分散板2和与施压头连接的装置1连接后在真空袋外放入产品7欠压位置,确保压力分散板随形贴合。
31.6)在欠压位置上方将基础板4与模具6固定,将施压杆3与基础板相对固定锁死,使施压杆只能向下移动不能向其他方向移动。
32.7)调节施压弹簧的施压度,使得压力分散板紧贴产品欠压位置真空袋外,并对袋内产品施加一定的压力,在压紧欠压位置的前提下,再依据成型模具6的尺寸适当补充压紧施压弹簧一部分以补偿模具热膨胀。
33.8)将上述组合后共同移至热压罐,进行固化,固化按产品的固化参数进行,固化时热压罐的压力正常施加在产品表面,在v形尖部面积较小部位由施压杆、施压弹簧和压力分散板共同作用额外施压,保证适当补压,固化后脱模即得表面和内部质量良好的复合材料v形零件。
34.以上所述实施例仅表达本发明的实施方式,但并不能因此而理解为对本发明专利的范围的限制,应当指出,对于本领域的技术人员来说,在不脱离本发明构思的前提下,还可以做出若干变形和改进,这些均属于本发明的保护范围。