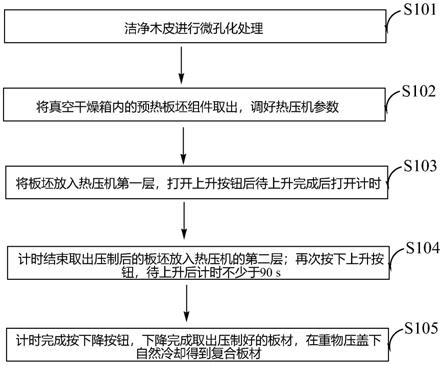
1.本发明属于木塑复合材料技术领域,尤其涉及一种聚丙烯木塑复合板、制备方法及应用。
背景技术:2.目前:木塑复合材料(wood-plastic-composites,简称wpc)。木塑复合材料是通过木质纤维或木粉与热塑性树脂为原料,混合后经过加工,制备而成的一种新型绿色环保的复合材料。
3.近年我国在木塑材料取得了一些成果,通过以木粉为填充料结合聚丙烯制备木塑复合板材,最后得到的板材,其冲击强度、拉伸强度和阻燃性都得到提高,能满足多种场合的生产工艺需求和使用性能。其板材不仅性能优异而且可回收再次利用。将木粉与废弃的塑料混合压制成木粉/聚丙烯(pp)复合材料。通过木粉使用量的改变研究板材的力学性能。结果显示,木粉含量的增加使其板材的力学性能先增加后减小。利用废弃的秸秆、稻壳、麻纤维等与热塑性树脂复合而制成木塑板材,相比传统木材更加耐腐蚀、耐水性好、不易开裂、寿命长、尺寸稳定性好等。通过热压成型制备高强全聚丙烯复合板材得到后的板材力学性能大大提高,也可以进行回收解决了环保问题。以聚丙烯膜为胶黏剂和桉木压制单木板/聚丙烯膜复合板材,研究不同的温度、时间和塑料的使用量对复合板材性能的影响。通过此方法得到的复合板材没有甲醛释放,并且聚丙烯是性能优异的热塑性树脂,制备得到的复合板材性能优异,节约环保以及零甲醛,适应当下生活追求的品质和健康。通研究聚丙烯复合材料采用连续纤维增强,得到的材料性能优异。通过使用两种短纤维,分别是再生聚酯和聚丙烯,通过热压成型制得纤维复合板材,其得到的复合材料力学性能达到优化。研究木粉/聚丙烯复合板材,其中加入异氰酸酯作为胶黏剂,得到的复合板材力学性能优异。通过采用钛酸酯偶联剂和铝酸酯偶联剂对木粉经过处理,改变时间和木粉含量,研究对wpc的力学性能影响,结论显示,偶联剂处理过的木板,增强了木粉与聚丙烯的界面相容性,使得复合材料的力学性能有所提高。使用马来酸酐接枝乙烯-辛烯共聚物对界面改性,改变界面相容性和木粉填充量制备木塑复合板材,研究其力学性能的变化,通过改变界面相容性制备的木塑复合板材的力学性能优于未改变界面相容性制备的复合板材。以低密度聚乙烯薄膜为胶黏剂和杨木板叠加制备木塑复合板材,利用温度的改变和使用改性剂硅烷偶联剂对木板表面处理,研究其力学性能的变化。研究结果,木板改性后的胶合强度好于木板为改性的所压制的板材。
4.复合材料常见的几种成型工艺。
5.模压成型:在成型温度下的模具中,放入颗粒、粉状等料,待树脂在模具内流动,增强材料也在流动,填满模具腔内。其要在高压力、耐高温的金属模具,高强度下完成。适合生产中小型复合材料制件。
6.热压成型:在高温下和高压下利用粘结剂发生黏流的特性,一定的时间下压制而成。特点:压力、温度均匀,模具简单适合制备较大的复合材料。在压制过程中可以考虑时
间、温度以及压力等各项变量对材料的影响。
7.挤出成型:通常由加料系统、温控系统、传动控制系统和机头口模等组成一个挤出过程,填料进入物料口,物料会经过固体、弹性体、黏流体最终变为固体的一个变化过程。挤出成型机通常有单螺旋挤出机和双螺旋挤出机。
8.注塑成型:在一定温度下,粒料通过注塑机、注塑模具经过冷却固化后,得到产品的方法。该方法适用形状复杂的的制件。其特点:效率高、生产速度快。
9.木塑复合板材是一种具有应用意义的新型材料。有利于降低塑料的使用量,有助于环境的保护;同时既可回收也可再利用,成为绿色经济型材料。在应用中,建筑方面:屋檐、凉亭、公共设施、地板、墙面等;生活方面:桌椅、教学用品、柜子、收纳箱、浴桶、滑雪板、拐杖、木塑球拍、蜂箱、高尔夫球棒以及生活中的各种模型器具;服务物流方面:木塑固定架、木塑保护罩等。耐腐蚀、结实等优良特性具有较大的竞争力和上升空间;装饰材料:门、装饰板材、线条、扶梯及护栏、天花吊顶等,木塑材料耐用零甲醛,在装修方面有很大的优势。木塑材料的应用非常广泛。
10.木塑复合板材具有耐水性、可塑性强、寿命长、色彩丰富、不易开裂、稳定性好等优良性能。木塑材料在各方面都得到需求,发展空间大、需求高,会被越来越广泛的使用。在自然资源大力的消耗下,开始追求绿色健康的生活,而木塑复合板材可以进行回收再次利用,降低资源的消耗,同时提供了更好的产品,相信木塑复合材料将会在未来成为主流的消费产品。大量的民用渔船,船的甲板将会使用到木塑复合板材,其耐腐蚀和耐水性,非常适合渔船上的使用,既为渔民节约成本,又可以使其达到船只的要求。铁路在这个高速发展的时代,在铁路建设中枕木的需求量很大,现在枕木还没有大量的用到木塑复合材料,在未来发展中wpc的优良特性也会在铁路建设中得到大量使用。相信在今后的发展中,木塑复合板材将会在这个时代扮演重要的角色。
11.通过上述分析,现有技术存在的问题及缺陷为:现有的复合板材存在生产过程中、使用过程中和使用后均存在甲醛释放,释放时间漫长;寿命短;木皮层与层粘附力低,强度不够;出现翘曲和变形。
12.解决以上问题及缺陷的难度为:市面上使用的非原木板材的制备过程中均使用胶粘剂,完全杜绝甲醛释放已不可能,给环境和生命造成伤害很大,后处理很麻烦,带来了经济上的负担和二次污染。以塑代胶制备木塑板材,但聚合物本身的可降解性和与木皮纤维的相容性较差等导致板材使用寿命受损,木皮与聚合物之间出现不可避免的界面,导致木皮层与层粘附力低,强度不够,出现翘曲和变形,若通过化学方法改善木皮表面疏水性能或使用超高分子量的聚合物等则无可避免地使用非绿色的化学试剂和大大增加了生产成本。
13.解决以上问题及缺陷的意义为:wpc结合了木材与塑料的很多优点。不但性能良好,而且能降低成本绿色环保。经过文献的阅读,研究wpc的意义:一可以减少木材的消耗保护地球环境;二是降低塑料的使用,木材与塑料的结合既可以回收也可以再利用,降低塑料对环境污染;三是通过木材与塑料的结合可以充分发挥木材和塑料的优点,降低成本的同时得到性能优良的产品。在呼吁绿色生活的时代,木塑复合材料不仅性能优良而且还可以回收再利用,对当下时代具有十分重要的意义。
技术实现要素:14.针对现有技术存在的问题,本发明提供了一种零甲醛木塑复合板、制备方法及应用。
15.本发明是这样实现的,一种零甲醛木塑复合板的制备方法,所述木塑复合板的制备方法包括:
16.第一步,将洁净木皮进行微孔化处理,微孔大小0.05-0.5mm2,孔密度250-4000m-2
,以实现聚合物对木皮的穿孔来提高板材的使用寿命和强度;
17.第二步,将真空干燥箱内的板坯组件取出,调好热压机参数(温度、压力、时间);
18.第三步,将板坯放入热压机第一层,打开上升按钮后待上升完成后打开计时,以使板材、聚合物之间的气体排出尽;
19.第四步,计时结束取出压制后的板坯放入热压机的第二层,打开水龙头按下冷却开关后再次按下上升按钮,待上升后计时不少于90s,保障聚合物流体和木皮表面实现相容接和聚合物流体进入木皮微孔实现穿插;
20.第五步,计时完成按下降按钮,下降完成取出压制好的板材。不同条件的板坯组合好后按第一步-第四步操作得到压制完成的复合板材,在重物压盖下(压力不低于3000n/m2)自然冷却,避免热压后冷却过程中出现的翘曲和变形。
21.进一步,所述木塑复合板的制备方法将锯好的木板最下面一面和最上面一面刷上液体石蜡油以防止木皮高温碳化和不粘附热压机。
22.进一步,所述木塑复合板的制备方法以热塑性聚合物薄膜代替胶黏剂制备木塑复合板材,聚合物包括聚丙烯、聚乙烯、聚氯乙烯等,从源头上杜绝甲醛来源。
23.进一步,所述木塑复合板的制备方法将木板放在模具上,裁剪好聚合物薄膜平铺在木板上,将裁减的边角膜补在木片空隙处;将组合好的坯,放入的真空干燥箱(温度为对应聚合物的软化点温度-粘流温度之间的某一温度),放置时间为100min。
24.进一步,所述木塑复合板的制备方法的压制温度设置为对应聚合物的粘流温度,预压时间为65s,压力为30t,加压时间不少于10min,冷却时间为90s。保障聚合物流体和木皮表面实现容接和聚合物流体进入木皮微孔实现完全穿插。
25.进一步,所述木塑复合板的制备方法的聚合物薄膜的制备包括:取聚合物颗粒于烧杯中,称取7.5-12g颗粒铺在镜面模具上呈一圆形;打开热压成型机,首先打开电源再打开油压,将温度调到聚合物对应粘流温度后将镜面模具放入热压成型机内,打开上升按钮待完全上升后,打开计时按钮,计时完成自动下降,将模具取出放到下面一层,关闭计时打开冷却,按上升经过60s的冷却再次下降,取出镜面模具便可以得到厚度约为0.35mm的圆形薄膜。
26.进一步,制备聚合物薄膜的工艺参数为温度设置为粘流温度,预压时间65s,加压时间45s,冷却时间60s,尽可排出颗粒间的气体,使得制备的聚合物膜薄而匀称。
27.本发明的另一目的在于提供一种由所述零甲醛木塑复合板的制备方法制备植物纤维/聚合物无污染复合材料的方法。
28.本发明的另一目的在于提供一种渔船用甲板,所述渔船用甲板为所述的聚丙烯木塑复合板。
29.本发明的另一目的在于提供一种铁路用枕木,所述铁路用枕木为所述的聚丙烯木
塑复合板。
30.结合上述的所有技术方案,本发明所具备的优点及积极效果为:本发明使用聚合物(聚丙烯、聚乙烯、聚氯乙烯等)与原木皮叠加而制备成零甲醛木塑复合材料;将洁净木皮进行微孔化处理,孔径0.05-0.5mm2,孔密度250-4000m-2
,以实现聚合物对木皮的穿孔来提高板材的使用寿命和强度。通过对聚丙烯薄膜的用量和木纹方向的变化,采用热压成型工艺成功制备了多层的木塑复合板材,并对其进行冲击性能、硬度、吸水率、老化试验等相关测试,研究了不同变量下材料的力学性能。结果表明,所制备的复合板材经权威检测机构检测未发现甲醛。使用双层聚合物且木纹交错排列制备的复合板材冲击强度最好,如孔密度1000m-2
的聚丙烯复合板材冲击强度达到3.43gpa(较未微孔化制备的木塑板材提高61.03%),吸水率最小是4.18%,远小于原木皮的吸水率(30.5%),且吸水不发泡。聚合物用量的增加可以使其板材结合更加牢固,减少木板表面孔隙,提高了冲击强度,降低了吸水率,提高了抗老化性能。
附图说明
31.图1是本发明实施例提供的聚丙烯木塑复合板的制备方法流程图。
32.图2是本发明实施例提供的聚丙烯膜压制工艺流程图。
33.图3是本发明实施例提供的聚丙烯/木板复合材料压制工艺流程图。
34.图4是本发明实施例提供的具体实验流程图。
35.图5是本发明实施例提供的顺木纹方向排列、交错排列的复合板材冲击强度图。
36.图6是本发明实施例提供的原木皮的吸水率图。
37.图7是本发明实施例提供的第3、7、9号样品的吸水率图。
具体实施方式
38.为了使本发明的目的、技术方案及优点更加清楚明白,以下结合实施例,对本发明进行进一步详细说明。应当理解,此处所描述的具体实施例仅仅用以解释本发明,并不用于限定本发明。
39.针对现有技术存在的问题,本发明提供了一种聚丙烯木塑复合板、制备方法及应用,下面结合附图对本发明作详细的描述。
40.如图1所示,本发明提供的木塑复合板的制备方法包括以下步骤:
41.s101:将洁净木皮进行微孔化处理,微孔大小0.05-0.2mm2,孔密度250-4000m-2
;
42.s102:将真空干燥箱内的板坯组件取出,调好热压机参数(温度、压力、时间);
43.s103:将板坯放入热压机第一层,打开上升按钮后待上升完成后打开计时;
44.s104:计时结束取出压制后的板坯放入热压机的第二层,打开水龙头按下冷却开关后再次按下上升按钮,待上升后计时不少于90s;
45.s105:计时完成按下降按钮,下降完成取出压制好的板材。不同条件的板坯组合好后按第一步-第四步操作得到压制完成的复合板材,在重物压盖下(压力不低于3000n/m2)自然冷却。
46.本发明提供的零甲醛木塑复合板的制备方法业内的普通技术人员还可以采用其他的步骤实施,图1的本发明提供的木塑复合板的制备方法仅仅是一个具体实施例而已。
47.下面结合实验对本发明的技术方案作进一步的描述。
48.本实验采用聚合物薄膜代替胶黏剂与木板相互叠加通过热压成型的方法制备得到木塑复合板材。通过对木板微孔化处理的方法改变木板与膜之间的接触面积、聚丙烯膜的使用量、木纹的方向来研究对力学性能的影响。本发明主要采用热压成型的方式,选用常规热塑性树脂,如聚丙烯、聚乙烯、聚氯乙烯等。
49.常规热塑性树脂一般无毒、无味的固体物质,耐酸碱、盐液以及多种有机溶解剂的腐蚀,具有高强度的机械性能、良好的高耐磨加工性能、耐化学性、耐热性、电绝缘性等。
50.1实验部分
51.1.1主要仪器、试剂及分析测试方法
52.1.1.1主要实验仪器和试剂
53.主要仪器见表1所示。
54.表1主要仪器
[0055][0056]
1.1.2主要化学试剂及原料
[0057]
主要试剂及原料见表2所示。
[0058]
表2主要试剂及原料
[0059][0060]
1.2设计实验
[0061]
按照本实验内容,考察以下内容:
[0062]
(1)微孔对木塑复合板材的影响。
[0063]
(2)木纹方向对木塑复合板材的影响。
[0064]
(3)膜的用量对木塑复合板材的影响。
[0065]
设计实验见表3所示。
[0066]
表3设计实验
[0067]
[0068][0069]
注:木皮面积为20*20cm2;木皮用量均为10片;使用的聚合物为聚丙烯;交错是木纹变换方向交错叠加;1张一层1张聚丙烯膜;2张一层2张聚丙烯膜;共10层木板。
[0070]
1.3原木皮的处理
[0071]
本实验需要准备好原材料,购买回来的原木皮使用锯子切锯成20
×
20cm2或25
×
25cm2的正方形木片,烘干,对原木皮进行微孔化处理,储备实验使用。
[0072]
1.4聚丙烯膜的制备
[0073]
步骤:取聚合物颗粒于烧杯中,称取7.5-12g颗粒铺在镜面模具上呈一圆形;打开热压成型机,首先打开电源再打开油压,将温度调到聚合物对应粘流温度后将镜面模具放入热压成型机内,打开上升按钮待完全上升后,打开计时按钮,计时完成自动下降,将模具取出放到下面一层,关闭计时打开冷却,按上升经过60s的冷却再次下降,取出镜面模具便可以得到厚度约为0.35mm的圆形薄膜。
[0074]
1.4.1制备聚合物薄膜的工艺参数
[0075]
表4工艺参数
[0076][0077]
1.4.2制备聚合物薄膜的工艺流程
[0078]
膜压制工艺流程如图2所示。具体包括:打开电源和油压;调整参数;放入模具;按下上升打开计时;取出模具放入下一层;打开水龙头并打开冷却;冷却完成取出模具;得到聚合物薄膜。
[0079]
1.5木塑复合板材的制备
[0080]
1.5.1板坯的制作及预热
[0081]
将切割的木板最下面一面和最上面一面刷上液体石蜡油(防止木板碳化)。本实验以聚合物代替胶黏剂制备木塑复合板材。
[0082]
步骤:示例,取出10张木片和9张聚合物薄膜。将木板放在模具上,裁剪好聚合物薄膜平铺在木板上,将裁减的边角膜补在木片空隙处;以此方式相互叠加膜和木板,木板总计10片。将组合好的“夹芯”板坯,放入真空干燥箱,设置温度为对应聚合物的软化点温度-粘流温度之间的某一温度,放置时间为100min。
[0083]
1.5.2木塑板材的压制
[0084]
实验通过以聚合物膜代替胶黏剂采用热压成型的方法来制备复合板材。热压成型的原理:对组坯好的板件加热压制成具有耐水性和一定机械强度的复合板材工艺过程。其特点:温度场和压力场均匀、成型模具简单、有利于制备较大的的板材制件。
[0085]
步骤:将真空干燥箱内的板坯组件取出,调好热压机参数;戴好防烫手套将板坯放入热压机第一层,打开上升按钮后待上升完成后打开计时,计时结束取出压制后的板坯放入热压机的第二层,打开水龙头按下冷却开关后再次按下上升按钮,待上升后计时90s,计
时完成按下降按钮,下降完成取出压制好的板材。不同条件的板坯组合好后按以上步骤操作便可得到压制完成的复合板材。
[0086]
1.5.3木塑板材压制的工艺参数
[0087]
表5木塑板材压制工艺参数
[0088][0089]
1.5.4木塑板材压制的工艺流程
[0090]
木塑板材压制工艺流程如图3所示。具体包括:组坯;放入真空干燥箱;打开电源和油压;设置参数;组坯放入热压机;打开上升;打开计时;计时完成打开水龙头;打开冷却;冷却完成按下降;取出压制好的板材。
[0091]
1.6物理机械性能、吸水率和老化试验的测试
[0092]
1.6.1冲击强度测试
[0093]
组合冲击试验机主要用于硬质塑料、玻璃钢、陶瓷、等非金属材料的材料,冲击强度运用到组合冲击试验机。
[0094]
冲击强度是衡量高分子材料韧性的一个重要指标,冲击强度按照公式(1)进行运算。
[0095]
αk=a/(bh)
ꢀꢀꢀꢀꢀꢀꢀꢀꢀꢀꢀꢀꢀꢀ
(1)
[0096]
公式(1)中,αk代表冲击强度,kj
·
m-2
;a代表冲断试样时所需要的功,j;b代表冲击处试样的宽度,mm;h代表冲击处试样厚度,mm。
[0097]
本实验采用组合冲击试验机(简支梁)。试样宽度为20.0mm,试样厚度为16.0mm,预仰角为160
°
。
[0098]
1.7.2硬度测试
[0099]
硬度是材料性能重要的一个性能指标,硬度测试通过xhr-150型塑料洛氏硬度计,所测试件厚度必须大于0.6mm。先安装好所需规格的球压头,再安装好试验台,调试好仪器后将制样放入试验台,缓慢转动旋杆使球压头缓慢压入试样当小指针从黑点转到红点,并且大指针指向“30”时,便启动按钮,加试验力时看大指针转动几圈,当卸试验力时大指针转动几圈,便可根据读数原理得到试样的硬度值。
[0100]
1.7.3吸水性能测试
[0101]
将聚丙烯木塑复合材料制样进行吸水测试,将制样在80℃下经过干燥后,称重m0将试样浸泡在恒温25℃的水浴内,分别按一定的时间取出试样,用干纸巾擦拭表面吸附的水分,重新称重m
t
,然后迅速放入水中浸泡,可以重复测试。制样吸水率wa(%)根据公式(2)计算:
[0102]
wa=(m
t-m0)/m0ꢀꢀꢀꢀꢀꢀ
(2)
[0103]
公式(2)中wa是吸水率,m
t
是浸泡时间t后的质量,g,m0是试样浸泡前的质量,g。
[0104]
1.7工艺流程
[0105]
具体实验流程图见图4所示。
[0106]
2试验结果
[0107]
2.1木塑复合板材冲击强度测定
[0108]
冲击强度测试环境:测试冲击量50j,环境温度25℃。示例聚丙烯木塑板材冲击强度绘制的点线图如图5所示。。
[0109]
由图5可以看出顺木纹排列的聚丙烯木塑板材的以下信息:
[0110]
(1)当孔数为0时,冲击强度是1.98gpa。
[0111]
(2)随着板材打孔数的增加,板材的冲击强度在不断提高。打孔数为40时,板材的冲击强度是3.13gpa。
[0112]
(3)孔数为40时,与无孔板材相比,板材冲击强度提高了58.08%。
[0113]
(4)可能的原因如下:
[0114]
①
木板自身具有一定的抗冲击性能,聚丙烯膜具有一定的机械强度,以聚丙烯膜为胶黏剂热压后的板材,拥有一定的抗冲击性能。
[0115]
②
打孔数增多,聚丙烯膜融化后,流进孔洞,粘结性更好,因此板材冲击性能得到提高。
[0116]
③
由于增加孔数,使得聚丙烯膜融化后更多的流入孔洞中,因此板与板之间的相互粘结性更高,冲击性能得到提升。
[0117]
由图5同样可以看出交错排列的聚丙烯木塑板材的以下信息:
[0118]
(1)板材无孔时,冲击强度是2.13gpa。
[0119]
(2)随着板材打孔数增多时,冲击强度也在提高;打孔数为40时,板材的冲击强度是3.43gpa。
[0120]
(3)与无孔板材相比,打孔数为40时,冲击强度提高了61.03%。
[0121]
(4)打孔数为均为40时,与顺木纹排列的板材相比,交错板材的冲击强度提高了0.3gpa,提升了9.58%。
[0122]
(5)可能的原因如下:
[0123]
①
木板自身具有一定的抗冲击性能,聚丙烯膜具有一定的机械性能,以聚丙烯膜为胶黏剂热压制备后,产生一定的抗冲击性能。
[0124]
②
打孔数增多,聚丙烯膜融化后,流进孔洞,粘结性更好,因此板材冲击性能得到提高。
[0125]
③
由于增加孔数,使得聚丙烯膜融化后更多的流入孔洞中,因此板与板之间的相互粘结性更高,冲击性能得到提升。
[0126]
④
交错排列时,木板与木板之间的纤维相互交呈一个网状,因此冲击性能得到提高。
[0127]
对比1张膜和2张膜所测试的聚丙烯型木塑板材冲击性能数据如表6所示。
[0128]
表6聚丙烯型木塑板材冲击强度测试数据
[0129][0130]
由表6可以看出以下信息:
[0131]
(1)与样品7相比,样品9的冲击强度提高了0.23gpa,提升了10.80%。
[0132]
(2)样品10的冲击强度比样品8的冲击强度提高了0.31gpa,提升了15.66%。
[0133]
(3)样品9的冲击强度比样品10的冲击强度提高了70mpa,提升了3.06%。
[0134]
(4)使用2张膜交错排列的板材冲击性能最佳。
[0135]
(5)可能的原因如下:
[0136]
①
同样的排列方式时,木板表面积有限,聚丙烯膜的使用量增加,在融化后充分进入木板的空隙内,粘结强度提高,板材粘结更加牢固,因此冲击性能得到提高。
[0137]
②
聚丙烯膜使用量相同时,交错排列使得木板与木板之间的纤维相互交错,呈网状结构,横纵向拉力相互叠加,冲击性能得到提高。
[0138]
2.2木塑复合材料硬度测试
[0139]
取出比较有对比性的材料检测复合板材的硬度。本测试用到塑料洛氏硬度计。分别选用样品初试验力:98.07n,压头规格:φ3.175mm,电源电压:ac220 v。
[0140]
表7硬度测试数据
[0141][0142]
由表7可以得出以下信息:
[0143]
(1)原木板的硬度值是37hre。
[0144]
(2)硬度值最大是9号样品39hre,最小是8号样品硬度值是36.7hre,差值在2.3。硬度值的变化范围不大,在一个稳定的范围内。
[0145]
(3)可能的原因如下:
[0146]
①
木板本身具有的一定的机械强度。
[0147]
②
聚丙烯膜具有一定的机械强度,使用量增加与复合板材之后,提高一些硬度值,影响较小。
[0148]
③
硬度是材料抗硬物压入的能力,此次设计制作工艺不改变木板自身性质,设计的变量也未影响木板自身具有的机械强度,而聚丙烯作为胶黏剂的存在,影响也甚微,因此
板材的硬度值在一个稳定变化范围内。
[0149]
④
木板自身之间存在的硬度差异。
[0150]
2.3原木皮吸水率的测定
[0151]
原木皮的吸水率见图6,可以看出以下信息:
[0152]
(1)吸水速度快,吸附20min后就达到饱和。
[0153]
(2)吸水率高,达到30.5%。
[0154]
(3)原因为:原木皮厚度很小,木质纤维表面极性基团多,导致吸水快而多。
[0155]
2.4聚丙烯木塑复合板材吸水率测定
[0156]
将三个比较有对比性的样品进行吸水测试,分别是样品3、样品7和样品9。
[0157]
表8样品基本详情
[0158][0159]
由图7可以看出样品3吸水性质的以下信息:
[0160]
(1)按照5min测试一次,吸水5min时,吸水率1.7%。
[0161]
(2)样品3的吸水率随着时间的增加而升高,当时间到45min时,吸水率达到最大为5.13%。超过45min吸水将趋于平稳,板材达到吸水饱和状态。
[0162]
(3)可能的原因如下:
[0163]
①
木板表面有纤维,纤维为亲水性物质,因此可以吸收一定量水分。
[0164]
②
在木板上造出5
×
8交错的小孔,可以增大木板与水分子接触面积,使木板具有较强的吸水性。
[0165]
③
聚丙烯为多孔高分子材料,孔隙比较多,具有较强的储水性能。因此,将聚丙烯热压于木板之间,更多的水分子可以储存于聚丙烯的孔道里面,大幅度提高木板的吸水率。
[0166]
④
随着时间增长,越来越多的水分子与木板和聚丙烯膜接触并进入到材料孔道之中,因此吸水率快速增大。
[0167]
⑤
时间延长到45min时,大部分孔道被水分子占据。因此,吸水率不再发生大幅度改变。
[0168]
由图7可以看出样品7吸水性质的以下信息:
[0169]
(1)按照5min测试一次,吸水5min时,吸水率是1.75%。
[0170]
(2)样品7的吸水率随着时间的增加而升高,时间在45min时,吸水率达到最大为5.22%。超过45min吸水量趋于平稳,吸水达到饱和状态。
[0171]
(3)与样品3相比,其最大吸水率低了0.09%,相差不大。
[0172]
(4)可能的原因如下:
[0173]
①
木板表面有大量木质纤维,纤维是亲水性物质,有一定的吸水能力。
[0174]
②
聚丙烯为多孔高分子材料,孔隙较多,具有较强的吸水能力。因此,更多的水分子可以储存在聚丙烯里,提高木板的吸水能力。
[0175]
③
随着时间的增长,越来越多的水分子进入木板的纤维里和聚丙烯的孔隙里,因此吸水率升高。
[0176]
④
当时间增长到45min时,大部分孔道被水分子占据,后来水分子被排斥,因此吸水量达到饱和状态。
[0177]
⑤
样品7未打孔,水分子进入的孔道有限,减少板材的储水量,因此吸水率略低于样品3。
[0178]
由图7可以看出样品9吸水性质的以下信息:
[0179]
(1)按照5min测试一次,吸水5min时,吸水率是1.45%。
[0180]
(2)随着时间的增加样品9的吸水率随时间增加而上升,时间在45min时,吸水率达到最大为4.18%,超过45min吸水将达到饱和状态。
[0181]
(3)与样品7相比,最大吸水率低了1.04%。
[0182]
(4)可能的原因如下:
[0183]
①
木板表面大量的纤维,纤维是亲水性的,具有一定吸水能力。
[0184]
②
随着时间的增长,越来越多的水分子进入板材的孔道里,因此吸水率升高。
[0185]
③
当时间增长至45min时,板材孔道被水分子占满,后续水分子进不来,因此板材处于吸水饱和状态。
[0186]
④
当使用两张聚丙烯膜,木板表面积有限,当膜融化时更多的进入木板的微孔隙中,限制木板一定的吸水能力,因此吸水率比样品7低一些。
[0187]
结论:
[0188]
(1)木塑复合板材的冲击强度随着打孔数的增加而提高;增大膜与板的接触面积,聚丙烯木塑复合板材冲击强度不断升高。
[0189]
(2)随着聚合物薄膜使用量的增加,复合板材的冲击强度也在提高。
[0190]
(3)交错排列压制的复合板材的冲击强度明显大于顺木纹排列压制的复合板材。
[0191]
(4)木塑复合材料的硬度之间的波动变化较小,在稳定范围内,由此表明此次实验变量的改变和热压成型的方法对板材的硬度值的影响甚微。
[0192]
(5)木塑复合板材的吸水率随着时间的增加而增大,聚合物薄膜的使用阻隔了水分进入板材,导致板材吸水率下降,吸水速度变缓。如聚丙烯木塑复合板材,当时间超过45分钟后,复合板材的吸水将达到吸水饱和的状态。吸水率大小排列:5
×
8交错1张膜>无孔交错1张膜>无孔交错两张膜。
[0193]
(6)使用2张聚丙烯膜制备的复合板材,冲击强度最好是3.43gpa,吸水率最低是4.18%,远远低于原木皮的吸水率(30.5%)。
[0194]
木塑复合材料是力学性能优异,尺寸稳定性好、不易开裂、零甲醛等优良的性能。在当下国家绿色生产、绿色出行、绿色生活的倡导下,木塑复合板材符合可持续学发展的目标。在如今,国内对木塑复合材料的研究很多,各种木塑复合板材也在被各个领域应用。不过还有一部分领域没有应用,可能对木塑板材了解的不够充足,新型材料的普及率不高,希望通过我的课题实验,对制作方法的简单化、性能优异化,对木塑复合材料认识可以贡献一点力量。如今,废物再利用和可回收也是热门话题,对于聚丙烯木塑复合板材来恰好具备了可回收再利用的特点,既起到节约资源的作用还保护环境,响应国家号召。因其造价成本低,制作简单,同时还可以拥有好的性能,在销售方面做到价格低廉且性能良好,可以被广
泛的接受和使用。
[0195]
以上所述,仅为本发明的具体实施方式,但本发明的保护范围并不局限于此,任何熟悉本技术领域的技术人员在本发明揭露的技术范围内,凡在本发明的精神和原则之内所作的任何修改、等同替换和改进等,都应涵盖在本发明的保护范围之内。