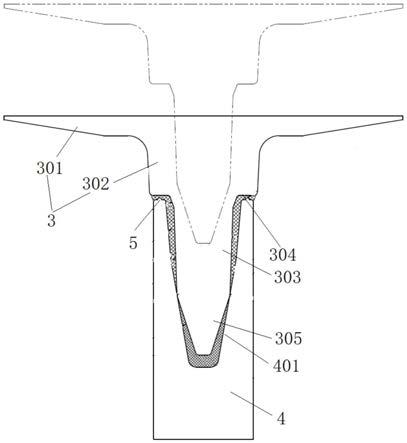
1.本发明涉及风力发电设备领域,特别是一种风电叶片腹板快速粘接结构及其快速成型方法。
背景技术:2.风电叶片的壳体与腹板通常采用分别灌注成型,之后通过胶粘合模完成组装。腹板通过两端类似l型的主粘接角与叶片壳体实现粘接。如图1所示,通常为了增加粘接可靠性,再完成主要粘接后,还会在腹板粘接角的另外一侧进行辅助粘接。这种工艺是目前叶片行业种应用最广的粘接合模工艺,优点是粘接方便,制造精度要求较低,对应的缺点是工序复杂,辅助粘接制作耗时费力,不利于生产提速,并且容易出现粘接缺陷,影响整个叶片安全性。
3.中国专利cn109822941a公开了一种用于风电叶片的腹板粘接脚、风电叶片及其成型方法,其腹板粘接脚的纵截面呈倒“t”字形,腹板平板结构插入两个所述腹板粘接脚之间。成型方法为:s1、通过腹板模具制作腹板平板结构;
4.s2、制作腹板粘接脚,使腹板粘接脚呈倒“t”字形,具有主体以及与所述主体连接的外延伸部及内延伸部;s3、使用两个腹板粘接脚,使两个所述腹板粘接脚相对设置,根据腹板平板的厚度来调整腹板粘接脚之间的距离;s4、将两个腹板粘接脚与主壳体通过树脂灌注成型;s5、将腹板平板插入两个腹板粘接脚之间,通过胶粘剂粘接,形成叶片。在该专利技术中,腹板平板结构与腹板粘接脚独立制作成型,当腹板尺寸有较小幅度调整时,不需要重新调整腹板模具,节省工时及腹板模具使用次数,风电叶片成型时,采用两个腹板粘接脚,保证腹板粘接脚模具的通用性及工艺的简便性,可以先将预制腹板粘接脚与主壳体连接,然后将腹板平板插入预制腹板粘接脚中,也可以先将腹板平板与预制腹板粘接脚灌注粘接形成腹板整体,再通过结构胶连接腹板整体与主壳体,通过胶粘剂将预制腹板粘接脚与腹板平板粘接。该专利技术对腹板尺寸适应性较差,需要根据腹板厚度来调整腹板粘接脚的距离,而且对于腹板的长度适应性也较差,易对腹板造成挤压,不能实现快速粘接。同时,该方式不能防止粘接剂的裂纹扩展,不容易收胶,粘接强度不高。
5.中国专利cn211334656u公开了一种复合材料风电叶片腹板粘接角一体式成型装置,其模具具有对称结构,模具包括上部和下部,上部中间设有凸起,两侧翻边,下部为底座,凸起两侧分别安装硅胶条,硅胶条与其靠近的翻边之间设有间隙,间隙处自硅胶条侧至翻边侧依次铺设导流层、脱模布层、布层、第一铺层和包裹层,第一铺层的外端设在翻边的边缘处,其成型步骤为:铺层
→
灌注
→
固化
→
脱模
→
修形。该装置能够使腹板粘接角、腹板一次性成型,增加了腹板的粘接宽度和强度,提高了工作效率,有效保证腹板粘接角一致性,提高了腹板的质量。该专利技术粘接结构和粘接工艺复杂,无法实现快速粘接,同时,该方式不能防止粘接剂的裂纹扩展,不容易收胶,粘接强度不高。
6.中国专利cn109882365a公开了一种碳纤维风电叶片腹板及其制备方法,包括两端的碳纤维腹板帽和中间的轻质连接板,碳纤维腹板帽与轻质连接板通过结构胶粘接,碳纤
维腹板帽的端部部分伸入到轻质连接板内部。轻质连接板的端部设有用于装配碳纤维腹板帽的凹槽,碳纤维腹板帽通过拉挤成型工艺制成t字型结构,顶端为弧形结构。成型步骤为:通过模具和拉挤成型工艺分别完成碳纤维腹板帽、轻质连接板的成型;将碳纤维腹板帽与轻质连接板粘接,进行补强处理,随后加热固化。相应地,该专利技术也是通过腹板直接与碳纤维腹板帽直接粘接,对腹板尺寸适应性较差,易对腹板造成挤压,不能实现快速粘接。同时,该方式不能防止粘接剂的裂纹扩展,不容易收胶,易出现流挂问题,粘接强度不高。
技术实现要素:7.本发明的发明目的在于:针对上述存在的问题,提供一种风电叶片腹板快速粘接结构及其快速成型方法,本发明通过将预制成型的t形结构腹板粘接角与搭接件分别同风电叶片壳体与腹板一起灌注共固化,成型后通过腹板粘接角与搭接件之间的双楔形搭接结构实现胶粘连接,可以快速完成风电叶片壳体与腹板的装配,提高了生产效率,本发明的双楔形搭接结构不仅具有更高的粘接强度,而且还能更好的防止粘接剂的裂纹扩展,解决目前叶片腹板粘接结构制作耗时费力,生产效率较低的问题,以及叶片粘接结构生产过程中易出现粘接缺陷,粘接质量较低的问题,克服了现有粘接结构所存在的不足。
8.本发明采用的技术方案如下:一种风电叶片腹板快速粘接结构,包括腹板和腹板粘接角,腹板的端部设置有搭接件,所述搭接件固定连接在腹板上,搭接件上设置有装配槽,所述装配槽内容纳有粘接剂,所述腹板粘接角固定连接在壳体上,腹板粘接角包括粘接底座和粘接凸台,所述粘接凸台设置在粘接底座上,并共同形成截面为t形的一体化结构,所述腹板粘接角通过粘接底座与叶片的壳体实现固定粘接,所述粘接凸台与装配槽插接配合形成粘接结构,进而实现腹板与叶片的壳体的快速粘接。
9.在本发明中,沿所述装配槽的深度方向,所述装配槽的槽宽逐渐变小形成v形开口结构,当粘接凸台插入装配槽内时,所述装配槽与粘接凸台接触并挤压和固定住粘接凸台。
10.在本发明中,所述粘接凸台部分收缩形成插入部,所述插入部朝向粘接凸台的一端收缩形成具有圆台结构的限位台,插入部的另一端与装配槽接触配合,所述限位台的端面用于与所述装配槽的槽面接触,以限制插入部插入装配槽中的深度。
11.在本发明中,所述插入部插入装配槽的一端倒角形成倒角结构。
12.在本发明中,所述限位台的端面或/和装配槽的端面上设置有向外凸起的具有环状结构的限位凸缘。
13.本发明还包括一种风电叶片的快速成型方法,包括以下步骤:
14.s1、通过拉挤工艺预制成型腹板粘接角和搭接件,所述腹板粘接角包括粘接底座和粘接凸台,所述粘接凸台设置在粘接底座上,并形成截面为t形结构,所述搭接件上设置有装配槽,所述装配槽用于与粘接凸台型面配合;
15.s2、将腹板粘接角和搭接件分别与叶片的壳体和腹板一起灌注固化形成一体化结构;其中,所述腹板粘接角通过粘接底座与叶片的壳体固定连接,所述搭接件远离装配槽的一端与腹板端部固定连接;
16.s3、向搭接件的装配槽内注入粘接剂,然后通过腹板粘接角的粘接凸台插入搭接件的装配槽内,并使用腹板挤压工装,完成腹板一端与壳体的粘接,同时清理装配槽中挤压出来的残余粘接剂;
17.s4、完成腹板一端的粘接后,进行叶片合模,先将与腹板另一端相对应的腹板粘接角部分插入腹板另一端搭接件的装配槽内,然后模具向腹板方向移动,在装配槽的导向作用下,腹板粘接角自动落入搭接件的装配槽内完成装配,清理装配槽中挤压出来的残余粘接剂,从而完成叶片与腹板的粘接。
18.在本发明中,沿所述装配槽的深度方向,所述装配槽的槽宽逐渐变小形成v形开口结构,当粘接凸台插入装配槽内时,所述装配槽与粘接凸台接触并挤压和固定住粘接凸台。
19.在本发明中,所述粘接凸台部分收缩形成插入部,所述插入部朝向粘接凸台的一端收缩形成具有圆台结构的限位台,插入部的另一端与装配槽接触配合,所述限位台的端面用于与所述装配槽的槽面接触,以限制插入部插入装配槽中的深度。
20.进一步,所述腹板粘接角与叶片的壳体粘接时,粘接面使用脱模布进行保护。
21.进一步,搭接件与腹板粘接时,搭接件的装配槽通过堵头进行封闭处理。
22.综上所述,由于采用了上述技术方案,本发明的有益效果是:
23.1、采用本发明的腹板快速粘接结构,可以快速完成风电叶片壳体与腹板的装配,提高了生产效率,本发明的双楔形搭接结构不仅具有更高的粘接强度,而且还能更好的防止粘接剂的裂纹扩展,相比于常规粘接结构及工艺,本发明可以有效节省粘接剂,且更易收胶,能有效地解决叶片残胶流挂问题,同时还能减轻叶片重量,具有更好的工艺性;
24.2、相比于常规粘接结构及工艺,本发明的腹板粘接成型工艺可以避免手工制作外侧粘接角,成型过程可实现腹板自动定位,不仅能提高定位精度,还能有效提高整个叶片腹板粘接效率;
25.3、双楔形搭接结构属于复合型粘接结构,常规腹板粘接失效形式以剥离和剪切混合失效为主,而双楔形搭接结构失效形式以粘接剂剪切失效为主,所以相比常规粘接结构,本发明的快速粘接结构具有更高的粘接强度;
26.4、本发明腹板粘接角与叶片壳体可一体灌注,主要粘接结构不易出现缺陷,并且双楔形搭接粘接结构安全可靠,全面提升了叶片腹板的粘接质量。
附图说明
27.图1是风电叶片常规腹板粘接结构示意图;
28.图2是本发明的一种腹板和叶片的壳体粘接后的结构示意图;
29.图3是本发明的一种搭接件与腹板粘接角粘接配合时的结构示意图;
30.图4是本发明的搭接件与腹板粘接角粘接装配前的结构示意图;
31.图5是本发明的搭接件与腹板粘接角粘接装配后的结构示意图;
32.图6是本发明的搭接件灌注堵头结构示意图;
33.图7是本发明的腹板的一端与腹板粘接角快速粘接时的结构示意图;
34.图8是本发明的腹板与腹板粘接角快速粘接后的结构示意图。
35.图中标记:1为壳体,2为腹板,3为腹板粘接角,301为粘接底座,302为粘接凸台,303为插入部,304为限位台,305为倒角结构,4为搭接件,401为装配槽,402为i区域,403为ii区域,5为限位凸缘,6为堵头。
具体实施方式
36.下面结合附图,对本发明作详细的说明。
37.为了使本发明的目的、技术方案及优点更加清楚明白,以下结合附图及实施例,对本发明进行进一步详细说明。应当理解,此处所描述的具体实施例仅仅用以解释本发明,并不用于限定本发明。
38.实施例1
39.如图1所示,图1为风电叶片常规腹板粘接结构示意图。腹板2的两端为“l”形粘接脚3,并通过该粘接脚3与叶片的壳体1实现粘接,为了增加粘接可靠性,还需要在该粘接脚3的另外一侧进行辅助粘接,这种粘接成型方式工序复杂,制作耗时费力,容易出现粘接缺陷而影响整个叶片的安全性。
40.为了解决现有腹板粘接结构所存在的问题,本发明提供了一种风电叶片腹板快速粘接结构,如图2和图3所示,该快速粘接结构包括腹板2和腹板粘接角3,腹板2的端部设置有搭接件4,所述搭接件4固定连接在腹板2上,搭接件4上设置有装配槽401,所述装配槽401内容纳有粘接剂,所述腹板粘接角3固定连接在壳体1上,腹板粘接角3包括粘接底座301和粘接凸台302,所述粘接凸台302设置在粘接底座301上(优选为垂直设置在粘接底座301的中部),并共同形成截面为t形的一体化结构,所述腹板粘接角3通过粘接底座301与叶片的壳体1实现固定粘接,所述粘接凸台302与装配槽401插接配合形成粘接结构,进而实现腹板2与叶片的壳体1的快速粘接。搭接件4的设置可以无需考虑腹板2厚度等尺寸影响,容易统一粘接结构标准,对腹板2尺寸适应性强,腹板粘接角3与搭接件4相配合,容易实现快速粘接。
41.如图3所示,考虑到腹板2与壳体1之间存在一定角度(一般为钝角),腹板粘接角3与壳体1灌注固化后,设粘接底座301的中心线与腹板2中心线的法线夹角设为粘接角度θ,粘接凸台302的中心线(或对称线)与腹板2中心线的法线夹角设为粘接角度ω,将腹板粘接角的粘接角度θ与ω设计为可变参数,即设定粘接底座301和粘接凸台302之间的夹角可变,进而可依据实际情况,实现预制不同角度的腹板粘接角3。例如,针对倾斜角在90
°
-100
°
范围时,我们可以通过预制一个具有θ角度的楔形块来调整腹板粘接角3与壳体1的粘接角度,进而保证腹板粘接角3与搭接件4处于垂直配合的状态,当倾斜角在100
°
-120
°
范围时,我们可以将腹板粘接角3的粘接底座预制成倾斜面,即预制具有ω角度的腹板粘接角3,由此可以通过预制不同角度的腹板粘接角3来实现标准化、统一化快速成型安装。
42.进一步地,在整个粘接过程中,为了保证粘接效率与质量,我们对腹板粘接角3与搭接件4进行了独特设计。如图4和图5所示,为了让腹板粘接角3可以方便地嵌入搭接件4中,沿所述装配槽401的深度方向,所述装配槽401的槽宽逐渐变小形成v形开口结构,构成i区域402,所述i区域402的底部继续向槽底方向延伸,装配槽401的槽宽继续逐渐变小形成v形开口结构,构成ii区域403,当粘接凸台302插入装配槽401内时,所述装配槽401与粘接凸台302接触并挤压和固定住粘接凸台302。具有v形结构的装配槽401与粘接凸台302实现线接触,由此无论粘接凸台302是以何种角度插入装配槽401中,搭接件4均能对粘接凸台302产生垂直于接触面的法向挤压力并由此固定住粘接凸台,能够快速实现装配和粘接操作,省时省力。
43.进一步地,为了更好地形成稳定粘接结构,对于腹板粘接角3的粘接凸台302来说,
粘接凸台302部分收缩形成插入部303,所述插入部303朝向粘接凸台302的一端收缩形成具有圆台结构的限位台304,所述环状凸缘404与所述插入部303接触配合,所述限位台304的端面用于与所述装配槽401的槽面接触,以限制插入部303插入装配槽401中的深度,同时通过端面接触实现载荷传递,以提高粘接强度以及实现精确装配,这种结构不仅可以便于装配,还能形成具有较高接头强度的双楔形搭接结构。
44.进一步地,如图4和图5所示,随着插入部303嵌入深度的增加,装配槽401内的粘接剂不断被挤出,在v形开口的导向作用下,腹板粘接角3嵌入到装配槽401的ii区域403,当腹板粘接角3嵌入深度持续增加时,装配槽401与插入部303发生接触,并产生垂直于接触面的法向挤压力f,该法向力将会给腹板2提供一个侧向力,在法向挤压力f和反挤压力相互作用下,插入部303将会被“锁定”在装配槽401内,从而形成稳定的粘接结构。当环状凸起部306与环状凸缘404完全接触后,会在装配槽401的底部(即在ii区域403的上方)形成封闭的腔体,进而防止粘接剂继续被挤出,并形成封闭空间,如图5所示,插入部303的尖端部304位于ii区域403内,其主体部分位于i区域402中,此时,倒角结构305的端面与装配槽401的槽底并未接触或完全接触,进而避免了因插入过深而破坏插入部303或/和装配槽401的结构,最终影响粘接结构的可靠性和安全性。
45.作为一种实施方式,考虑到粘接质量的问题,如图4和图5所示,插入部303与装配槽401相配合的一端倒角形成倒角结构304,倒角结构304的设置主要是为了增加粘厚度和粘接面积,提高粘接强度,插入部303的倒角结构也有利于槽底胶层的流动,由此防止胶层因挤压而产生气泡,从而影响粘接质量。
46.为了进一步地防止插入部303继续深入,所述限位台304的端面或/和装配槽401的端面上设置有向外凸起的具有环状结构的限位凸缘5,如图5所示,限位凸缘5能够进一步防止插入部303继续深入,最后在装配槽401的i区域402和ii区域403形成稳定可靠的搭接粘接结构。
47.在上述中,双楔形搭接结构属于复合型粘接结构,常规腹板粘接失效形式以剥离和剪切混合失效为主,而双楔形搭接结构失效形式以粘接剂剪切失效为主,所以相比常规粘接结构,本发明的快速粘接结构具有更高的粘接强度。
48.进一步地,上述粘接结构的风电叶片成型方法包括以下步骤:
49.s1、通过拉挤工艺预制成型腹板粘接角3和搭接件4;
50.s2、将腹板粘接角3和搭接件4分别与叶片的壳体1和腹板2一起灌注固化形成一体化结构,所述腹板粘接角3通过粘接底座301与叶片的壳体1固定连接,搭接件4远离装配槽401的一端与腹板2的端部固定连接;其中,在灌注固化时,需要依据腹板2定位数据确定好腹板粘接角3的定位,同时保证腹板粘接角3的垂直度;为了便于灌注脱模,通过堵头6将搭接件4的凹槽401封闭,灌注固化成型后,再取出堵头6,如图6所示;
51.s3、向搭接件4的装配槽401内注入粘接剂,然后通过腹板粘接角3的粘接凸台302插入搭接件4的装配槽401内,并使用腹板挤压工装,完成腹板2一端与壳体1的粘接(例如先完成叶片底部腹板粘接角3的粘接装配),同时清理装配槽401中挤压出来的残余粘接剂,如图7所示,此过程兼容原来腹板粘接工艺的挤压工装,叶片底部壳体1的腹板粘接角3可实现腹板2的自动定位,但需要保证腹板2的垂直度;
52.s4、完成腹板一端的粘接后,进行叶片合模,先将与腹板2另一端相对应的腹板粘
接角3部分插入腹板2另一端搭接件4的装配槽401内,然后模具向腹板2方向移动(例如在进行腹板2上端粘接结构时,可将顶部模具下移即可),在装配槽401的导向作用下,腹板粘接角3自动落入搭接件4的装配槽401内完成装配,清理装配槽401中挤压出来的残余粘接剂,从而完成叶片与腹板2的粘接,如图2和图8所示。
53.在上述成型方法中,所述腹板粘接角3与叶片的壳体1粘接时,粘接面使用脱模布进行保护。
54.实施例2
55.实施例2与实施例1相同,其不同之处在于,腹板一侧预制粘接翻边,并先按常规腹板方式进行粘接,之后另一侧按本发明所示的粘接方式进行腹板粘接。
56.实施例3
57.实施例3与实施例1相同,其不同之处在于,所述的腹板粘接角与腹板预先粘接,形成完整腹板结构,之后按常规叶片腹板粘接方式进行粘接。
58.以上所述仅为本发明的较佳实施例而已,并不用以限制本发明,凡在本发明的精神和原则之内所作的任何修改、等同替换和改进等,均应包含在本发明的保护范围之内。