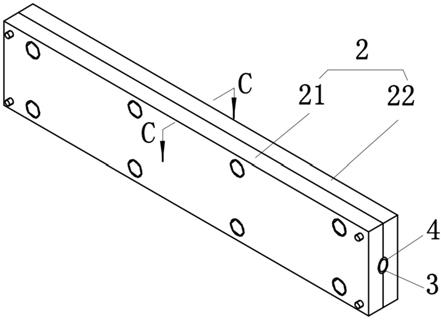
1.本实用新型属于复合材料技术领域,具体涉及一种复合材料管件成型模具。
背景技术:2.了解到现有复合材料细管类产品的成型方式通常是:先准备钢制芯模和碳纤维复合材料,然后按要求在钢制芯模的外表面铺贴多组复合材料铺层,之后进行热压固化成型,成型后抽取出钢制芯模,即完成碳纤维复合材料细管件的制备。然而这种加工方式存在着一些问题,即固化成型出来的复合材料细管件的外表面非常不光洁,严重影响了产品的外观质量。
3.因此,亟需有一种成型模具,能够解决上述背景技术中提出的问题。
技术实现要素:4.为了解决背景技术中提出的现有模具成型出来的复合材料细管类零件外表面粗糙的问题,本实用新型提供了一种复合材料管件成型模具,其具有成型出来的复合材料细管类零件外表面光滑的特点。
5.为了实现上述目的,本实用新型采用的技术方案为:
6.复合材料管件成型模具,包括硅胶芯模内涨成型工装和复合材料管件成型外模,所述硅胶芯模内涨成型工装用于成型硅胶芯模;所述复合材料管件成型外模沿轴向贯穿设有第一成型通孔,硅胶芯模设置在第一成型通孔内,硅胶芯模与第一成型通孔之间预留间隙。
7.优选地,所述硅胶芯模内涨成型工装包括第一工装和第二工装,第一工装的轴向上开设有第一通槽,第二工装的轴向上开设有第二通槽,第一通槽与第二通槽扣合后形成第二成型通孔。
8.优选地,所述第二成型通孔的横截面形状为圆形或椭圆形。
9.优选地,所述第二成型通孔的一端设置有灌注口。
10.优选地,所述灌注口的形状为漏斗状。
11.优选地,所述灌注口的横截面形状为非圆形。
12.优选地,所述灌注口的横截面形状为椭圆形。
13.优选地,所述灌注口的椭圆长边沿第一工装和第二工装的浇注端面的长边方向设置。
14.优选地,所述复合材料管件成型外模包括第一复合材料管件成型外模和第二复合材料管件成型外模,第一复合材料管件成型外模的轴向上开设有第三通槽,第二复合材料管件成型外模的轴向上开设有第四通槽,第三通槽与第四通槽扣合后形成第一成型通孔。
15.优选地,所述第一成型通孔的横截面形状为圆形或椭圆形。
16.与现有技术相比,本实用新型的有益效果在于:
17.1、本实用新型通过增设复合材料管件成型外模,并将原来的钢制芯模调整为硅胶
芯模,来实现提高成型出来的复合材料管件外表面光洁度的目的。具体地,热压成型过程中,硅胶芯模受热膨胀,铺贴在硅胶芯模外表面的复合材料铺层同时受到来自复合材料管件成型外模和硅胶芯模的压实作用,因此使得成型出来的管道外壁更加光滑,产品外观质量大大提高。
18.2、本实用新型通过在第二成型通孔的一端设置灌注口来实现方便高温液态硅胶原料浇注、提高浇注速度的目的;通过将灌注口的横截面形状设置为椭圆形,并且灌注口的椭圆长边沿第一工装和第二工装的浇注端面的长边方向设置,来实现在第一工装和第二工装的浇注端面的面积有限的情况下,尽可能合理的增大灌注口,进一步加快浇注速度,避免了在浇注过程中,由于浇注速度过慢导致先浇注的液态硅胶原料提前固结在第二成型通孔内壁上,从而影响后续液态硅胶原料的浇注效果,最终影响硅胶芯模的成型质量。
附图说明
19.图1为第一工装的主视图;
20.图2为第一工装的右视图;
21.图3为图1的a
‑
a视图;
22.图4为图3的i处放大图;
23.图5为第一工装的立体图;
24.图6为第二工装的主视图;
25.图7为第二工装的右视图;
26.图8为图6的b
‑
b视图;
27.图9为第二工装的立体图;
28.图10为硅胶芯模内涨成型工装的立体图;
29.图11为硅胶芯模内涨成型工装的右视图;
30.图12为硅胶芯模内涨成型工装的左视图;
31.图13为图12中j处的放大图;
32.图14为第一复合材料管件成型外模的主视图;
33.图15为第一复合材料管件成型外模的透视图;
34.图16为第二复合材料管件成型外模的主视图;
35.图17为第二复合材料管件成型外模的透视图;
36.图18为本实用新型的立体图;
37.图19为图18的c
‑
c视图;
38.图20为图19中k处的放大图。
39.其中,1
‑
硅胶芯模内涨成型工装;2
‑
复合材料管件成型外模;3
‑
硅胶芯模;4
‑
第一成型通孔;11
‑
第一工装;12
‑
第二工装;13
‑
第二成型通孔;14
‑
灌注口;15
‑
溢流槽;16
‑
密封槽;21
‑
第一复合材料管件成型外模;22
‑
第二复合材料管件成型外模。
具体实施方式
40.为了使本实用新型的目的及优点更加清楚明白,以下结合实施例对本实用新型进行进一步详细说明。应当理解,此处所描述的具体实施例仅仅用于解释本实用新型,并不用
于限定本实用新型。
41.实施例:
42.如图1
‑
图20所示,本实用新型为一种复合材料管件成型模具,包括硅胶芯模内涨成型工装1和复合材料管件成型外模2,硅胶芯模内涨成型工装1用于成型硅胶芯模3;复合材料管件成型外模2沿轴向贯穿设有第一成型通孔4,硅胶芯模3设置在第一成型通孔4内,硅胶芯模3与第一成型通孔4之间预留间隙。
43.其中,复合材料管件成型外模2为内表面光洁的钢制模具,复合材料管件成型外模2包括第一复合材料管件成型外模21和第二复合材料管件成型外模22,第一复合材料管件成型外模21的轴向上开设有第三通槽,第二复合材料管件成型外模22的轴向上开设有第四通槽,第三通槽与第四通槽扣合后形成第一成型通孔4,第一成型通孔4的横截面为椭圆形。具体地,第一复合材料管件成型外模21和第二复合材料管件成型外模22均为外形尺寸一致的长方体形状,其中,两者的长均为500mm,宽均为100mm,厚度均为20mm;第三通槽和第四通槽的形状尺寸一致,扣合后形成的第一成型通孔4的横截面为椭圆形,其中,椭圆的长边为14mm,短边为10mm。此外,为了方便将第一复合材料管件成型外模21与第二复合材料管件成型外模22进行固定,在第一复合材料管件成型外模21和第二复合材料管件成型外模22上都均匀开设了八个螺栓固定孔和四个定位孔。
44.硅胶芯模内涨成型工装1也是内表面光洁的钢制模具,用于浇注成型硅胶芯模3。硅胶芯模内涨成型工装1包括第一工装11和第二工装12,第一工装11的轴向上开设有第一通槽,第二工装12的轴向上开设有第二通槽,第一通槽与第二通槽扣合后形成第二成型通孔13,由于第二成型通孔13需要与第一成型通孔4相适配,因此第二成型通孔13的横截面形状也设置为椭圆形。与第一复合材料管件成型外模21和第二复合材料管件成型外模22类似,此处,第一工装11和第二工装12也都是外形尺寸一致的长方体形状,其中,第一工装11和第二工装12的长均为600mm,宽均为100mm,厚度均为20mm;第一通槽和第二通槽的形状尺寸也是一致,扣合后形成的第二成型通孔13的横截面为椭圆形,并且,椭圆的长边为11.5mm,短边为7.5mm,而第二成型通孔13的总长为500mm。其中,第一工装11和第二工装12上也都均匀开设了八个螺栓固定孔和四个定位孔,以便能够将第一工装11和第二工装12进行锁紧固定。
45.此外,第二成型通孔13的一端还设置有漏斗状的灌注口14,灌注口14的横截面形状为椭圆形,并且,灌注口14的椭圆长边沿第一工装11和第二工装12的浇注端面的长边方向设置。其主要目的是为了在合理范围内,使第一工装11与第二工装12的浇注端面上能够尽可能开设尺寸较大的灌注口14,从而方便后续高温液态硅胶原料的浇注。此处,灌注口14开口处的长边尺寸为75mm,短边尺寸为30mm,灌注口14沿轴向的长度尺寸为100mm。
46.除此之外,第一工装11的第一通槽所在面上还开设有溢流槽15和密封槽16,溢流槽15的径向尺寸略小于密封槽16,溢流槽15用于储存从第二成型通孔13中溢流出去的液态硅胶原料,而密封槽16用于安装密封垫,此处密封垫选用橡胶材质。其中,密封槽16沿轴向对称设置在第一通槽的两侧,而溢流槽15也是沿轴向设置,并且溢流槽15位于密封槽16与第一通槽之间。
47.还应当说明的是,本实施例中描述的只是复合材料管件横截面形状为椭圆形的情况,除此之外,也可以根据实际生产需要将复合材料管件横截面形状加工成圆形,此时,相
应地,第一成型通孔4和第二成型通孔13的截面形状也应该加工成圆形。
48.该复合材料管件成型模具的使用过程如下:
49.如图1
‑
20所示,使用时,先浇注硅胶芯模3,再成型复合材料管件。具体地,硅胶芯模3的浇注过程为:首先在密封槽16内安装橡胶密封垫,然后将第一工装11与第二工装12在高度方向上对齐之后进行扣合,形成第二成型通孔13和灌注口14,并用螺栓将第一工装11和第二工装12锁紧固定。之后,将扣合好的第一工装11与第二工装12移动至预先准备的钢板上,并使灌注口14的开口朝上,将用于成型硅胶芯模3的高温液态硅胶原料从灌注口14中缓缓倒入,至第二成型通孔13的内部即将充满时,停止倒入高温液态硅胶原料,等待第二成型通孔13内的高温液态硅胶原料完全冷却固化,最后,松开螺栓,拆开第一工装11和第二工装12,浇注的硅胶芯模3即固化成型,此后,拆掉密封槽16内安装的密封垫,并对第一工装11与第二工装12进行清理即可。复合材料管件的成型过程为:取出第一复合材料管件成型外模21和第二复合材料管件成型外模22,并在高度方向上对齐之后进行扣合,形成第一成型通孔4。然后按要求给前述准备的硅胶芯模3的外表面铺贴多组复合材料铺层,之后,将铺贴有复合材料铺层的硅胶芯模3安装到第一成型通孔4内,再用螺栓将第一复合材料管件成型外模21和第二复合材料管件成型外模22锁紧固定,随后进行热压固化成型,即可得到所需外表面光洁的复合材料细管件,至此,该复合材料管件成型模具的使用过程结束。