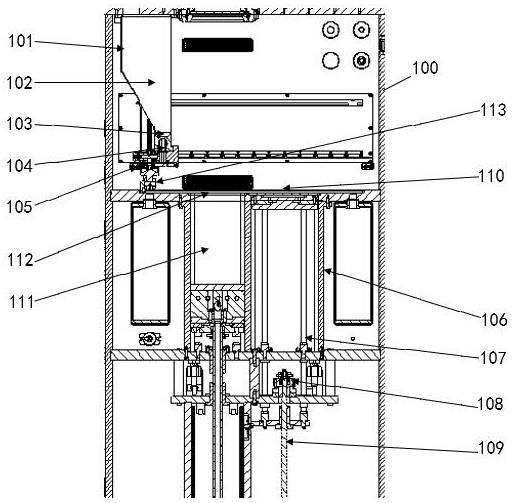
1.本实用新型涉及增材制造技术领域,具体涉及一种梯度功能材料合成和增材制造一体化机构。
背景技术:2.fgm材料与均一材料和复合材料不同,它是选用两种(或多种)性能和功能不同的材料,改变其组成和结构,从材料某一方位(一维、二维或三维)向另一方位连续(或准连续)地变化,使材料的性能和功能也呈现梯度化的非均质复合材料,即梯度功能材料(fgm),梯度功能类型有梯度功能连接型,即连接二个基体间的界面层呈梯度变化;梯度功能涂敷型,即在基体材料上形成组成渐变的涂层;梯度功能整体型,即组成从一侧到另一侧呈梯度渐变的结构材料;及其他梯度功能类型。
3.近年来,增材制造设备送粉舱大都采用单一的送粉机构、单一材料送粉、铺粉方式;有的虽然采用了双送粉机构,但仍然是单一材料送粉、铺粉,目的是提高效率和效果,尚未见fgm材料合成和增材制造一体化机构和技术,这一技术为现今国内和市场空白。
4.因此,发明一种梯度功能材料合成和增材制造一体化机构很有必要。
技术实现要素:5.为此,本实用新型提供一种梯度功能材料合成和增材制造一体化机构,通过fgm材料合成和增材制造一体化、集成化的制备工艺技术,就是对fgm材料合成采用激光扫描温度梯度烧结的方法,并同步增材制造出梯度功能结构,补了国内和市场的空白,解决了fgm材料合成和增材制造一体化机构和技术空白的问题。
6.为了实现上述目的,本实用新型提供如下技术方案:
7.一种梯度功能材料合成和增材制造一体化机构,包括支架、壳体、送粉舱伺服驱动系统、送粉舱升降机构、成型舱伺服驱动系统、成型舱升降机构、振镜控制卡、振镜、激光器、cnc系统、伺服驱动系统、激光系统和气氛系统,所述支架上固定安装送粉和铺粉机构,所述壳体上固定安装fgm材料合成和增材制造一体化机构,所述送粉和铺粉机构包括落粉机构和第一顶粉机构,所述落粉机构由落粉缸、落粉网板和落粉开合门和落粉控制装置组成,所述落粉缸、落粉网板和落粉开合门和落粉控制装置从上到下分布,所述第一顶粉机构由顶粉缸、顶粉推送装置、送粉舱升降系统、送粉舱送粉幅面、第一成型舱升降系统和成型舱铺粉幅面,所述送粉舱送粉幅面和成型舱铺粉幅面之间设有第一刮刀机构,所述顶粉缸、顶粉推送装置、送粉舱升降系统从上到下分布,所述第一刮刀机构位于所述落粉控制装置的下方,所述成型舱铺粉幅面位于所述第一刮刀机构的右侧,所述第一成型舱升降系统位于所述送粉舱送粉幅面的下方;
8.所述fgm材料合成和增材制造一体化机构包括送粉舱、成型舱和第二刮刀系统,所述送粉舱由第二落粉机构、第二顶粉机构和送粉升降系统组成,所述成型舱由成型缸、打印基板组件和第二成型舱升降系统组成,所述cnc系统连接和控制送粉舱伺服驱动系统,所述
cnc系统连接和驱动送粉舱升降机构,所述cnc系统连接和控制成型舱伺服驱动系统,所述cnc系统连接和控制激光系统。
9.优选的,所述落粉控制装置用于控制落粉量,所述第一刮刀机构在送粉舱送粉幅面和成型舱铺粉幅面之间双向刮粉。
10.优选的,所述送粉舱送粉幅面为第一落粉机构和第一顶粉机构分别送粉送达的幅面。
11.优选的,所述送粉舱和成型舱之间设有第二刮刀系统,所述第二刮刀系统位于所述第二落粉机构的下方。
12.优选的,所述cnc系统为开放式、组态型计算机数控制系统,所述气氛系统安装在所述壳体的左端,所述伺服驱动系统位于所述壳体的右侧。
13.优选的,所述振镜控制卡控制所述振镜偏转角度,所述打印基板组件位于所述第二刮刀系统的下方,所述打印基板组件、成型缸和第二成型舱升降系统从上到下分布。
14.优选的,所述振镜控制卡控制所述激光器的功率输出,所述成型缸底端连接第二成型舱升降系统。
15.优选的,所述cnc系统基于pc实现,所述第二顶粉机构位于所述打印基板组件的右侧。
16.优选的,所述cnc系统采用wondows操作系统。
17.优选的,所述cnc系统为八轴联动,所述cnc系统上具有i/o接口和模拟量接口。
18.本实用新型的有益效果是:
19.1、运用cnc系统的硬/软件系统,控制送粉舱和成型舱(铺粉舱)的升降系统、激光加热源的温控系统,实现同步地、融合一致地对每次送粉量、铺粉层厚和激光加热源温度等进行梯度控制,直至fgm材料合成和增材制造一体化成型,并提高成型效率和质量;
20.2、采用本发明的机构和技术,解决了梯度功能整体型,fgm材料合成的技术问题;进一步解决了fgm材料合成和增材制造一体化、集成化工艺制备的技术问题,填补了国内和市场的空白,拓宽了增材制造技术的应用领域,满足了军工和航空航天工业、科研和实验项目等高技术领域的需要;
21.3、发明符合增材制造技术,从单一材料向复合材料,特别是向fgm 材料合成的发展趋势;符合增材制造技术,向多材料、多工艺制备技术、特别是向fgm材料合成和增材制造一体化、集成工艺制备技术的发展趋势,具有广阔的市场前景和发展潜力;
22.4、cnc系统为开放式、组态型计算机数控制系统,基于pc的、采用wondows操作系统,可直接安装、运行应用软件,包括通用应用软件和专业应用软件,其中专业应用软件即为本发明的fgm材料合成和增材制造一体化、集成化工艺软件。
附图说明
23.图1为本实用新型送粉和铺粉机构示意框图;
24.图2为本实用新型fgm材料合成和增材制造一体化机构示意框图;
25.图3为本实用新型的控制和驱动系统框图。
26.图中:第一落粉机构101、落粉缸102、落粉网板103、落粉开合门104、落粉控制装置105、第一顶粉机构106、顶粉缸107、顶粉推送装置108、送粉舱升降系统109、送粉舱送粉幅
面110、第一成型舱升降系统111、成型舱铺粉幅面112、第一刮刀系统113、送粉舱201、成型舱202、第二落粉机构203、第二顶粉机构204、送粉升降系统205、成型缸206、打印基板组成207、第二成型舱升降系统208、第二刮刀系统209、cnc系统210、伺服驱动系统211、激光系统212、气氛系统213、送粉舱伺服驱动系统2、送粉舱升降机构3、成型舱伺服驱动系统4、成型舱升降机构5、振镜控制卡7、激光器8、气氛系统9。
具体实施方式
27.以下结合附图对本实用新型的优选实施例进行说明,应当理解,此处所描述的优选实施例仅用于说明和解释本实用新型,并不用于限定本实用新型。
28.参照说明书附图1
‑
3,该实施例的一种梯度功能材料合成和增材制造一体化机构,包括支架100、壳体200、送粉舱伺服驱动系统2、送粉舱升降机构3、成型舱伺服驱动系统4、成型舱升降机构5、振镜控制卡7、振镜8、激光器9、cnc系统210、伺服驱动系统211、激光系统212和气氛系统213,所述支架100上固定安装送粉和铺粉机构,所述壳体200上固定安装fgm材料合成和增材制造一体化机构,所述送粉和铺粉机构包括落粉机构101和第一顶粉机构106,所述第一落粉机构101由落粉缸102、落粉网板103和落粉开合门104和落粉控制装置105组成,所述落粉缸102、落粉网板103和落粉开合门104和落粉控制装置105从上到下分布,所述第一顶粉机构106由顶粉缸107、顶粉推送装置108、送粉舱升降系统109、送粉舱送粉幅面110、第一成型舱升降系统111和成型舱铺粉幅面112,所述送粉舱送粉幅面110和成型舱铺粉幅面112之间设有第一刮刀机构113,所述顶粉缸107、顶粉推送装置108、送粉舱升降系统109从上到下分布,所述第一刮刀机构113位于所述落粉控制装置105的下方,所述成型舱铺粉幅面112位于所述第一刮刀机构113的右侧,所述第一成型舱升降系统111位于所述送粉舱送粉幅面110的下方;
29.所述fgm材料合成和增材制造一体化机构包括送粉舱201、成型舱202和第二刮刀系统209,所述送粉舱201由第二落粉机构203、第二顶粉机构204和送粉升降系统205组成,所述成型舱202由成型缸206、打印基板组件207和第二成型舱升降系统208组成,所述cnc系统210连接和控制送粉舱伺服驱动系统2,所述cnc系统210连接和驱动送粉舱升降机构3,所述cnc系统210连接和控制成型舱伺服驱动系统4,所述cnc系统210连接和控制激光系统212;cnc系统210控制、驱动送粉舱升降机构3上下运动,按照cnc系统210的指令要求实现送粉量梯度控制;cnc系统210控制、驱动成型舱升降机构5上下运动,按照cnc系统210指令要求,实现每次每种材料铺粉层厚的梯度控制。
30.进一步地,所述落粉控制装置105用于控制落粉量,所述第一刮刀机构113在送粉舱送粉幅面110和成型舱铺粉幅面112之间双向刮粉。
31.进一步地,所述送粉舱送粉幅面110为第一落粉机构101和第一顶粉机构106分别送粉送达的幅面。
32.进一步地,所述送粉舱201和成型舱202之间设有第二刮刀系统209,所述第二刮刀系统209位于所述第二落粉机构203的下方。
33.进一步地,所述cnc系统210为开放式、组态型计算机数控制系统,所述气氛系统213安装在所述壳体200的左端,所述伺服驱动系统211位于所述壳体200的右侧。
34.进一步地,所述振镜控制卡7控制所述振镜8偏转角度,所述打印基板组件207位于
所述第二刮刀系统209的下方,所述打印基板组件207、成型缸206和第二成型舱升降系统208从上到下分布。
35.进一步地,所述振镜控制卡7控制所述激光器9的功率输出,所述成型缸206底端连接第二成型舱升降系统208,按照cnc系统210指令要求,与梯度送粉、梯度铺粉、梯度温度烧结等三联动,即实现了fgm材料合成和增材制造的构件一次成型。
36.进一步地,所述cnc系统210基于pc实现,所述第二顶粉机构204位于所述打印基板组件207的右侧。
37.进一步地,所述cnc系统210采用wondows操作系统。
38.进一步地,所述cnc系统210为八轴联动,所述cnc系统210上具有i/o接口和模拟量接口。
39.实施场景具体为:在使用本实用新型时,送粉控制采用顶粉机构106和落粉机构101二个送粉机构,分别装入性能和功能不同的两种材料,按fgm材料设计的要求,分别送料,梯度控制,避免每次送粉量过多或过少;其中刮粉控制采用第一刮刀系统113进行双向刮粉,提高刮粉的效率和质量;其中铺粉控制,是对每种材料每次铺粉层的厚进行梯度控制,但应确保两种材料每次铺粉层厚叠加后的总层厚是不变的,总层厚即是增材制造每次slm烧结的层厚;激光控制,对整体而言,由于两种材料每次铺粉的总层厚是不变的,但内部材料结构是不同的,一种材料梯度递增,另一种材料梯度递减,激光系统212同步控制加热源梯度温度烧结;但对每一个具体总层厚而言,其内部材料结构是不变的,因而激光系统212控制加热源进行相对恒温烧结;cnc系统210为开放式、组态型计算机数控系统,在其软件平台上,可直接安装运行应用软件,包括通用应用软件和专业应用软件、增材制造辅助设计软件,自动编程软件等;cnc系统210的配置软件提供工具、方法、组态等运行环境,组成一致的、完整的组态应用软件,运用cnc系统210的硬/软件系统,控制送粉舱201和成型舱202(铺粉舱)的升降系统、激光加热源的温控系统,实现同步地、融合一致地对每次送粉量、铺粉层厚和激光加热源温度等进行梯度控制,直至fgm材料合成和增材制造一体化成型,并提高成型效率和质量。
40.以上所述,仅是本实用新型的较佳实施例,任何熟悉本领域的技术人员均可能利用上述阐述的技术方案对本实用新型加以修改或将其修改为等同的技术方案。因此,依据本实用新型的技术方案所进行的任何简单修改或等同置换,尽属于本实用新型要求保护的范围。