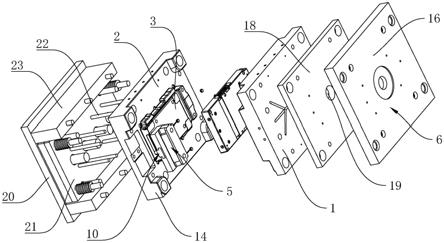
1.本实用新型属于模具技术领域,涉及一种可快速脱模的电动车电池盒注塑模。
背景技术:2.目前,共享电动自行车在各个城市逐渐普及,给市民的生活带来了更多的便利,同时绿色环保出行,因此得到大面积的推广,出于电动自行车的结构简约风格,电动车的电机一般都放在电池盒里。现有的共享电动自行车电池盒大多采用塑料材料制成,通过注塑模具进行大批量生产制造,现有的电动自行车电池盒模具在注塑过程中难以同步注塑成型电池盒侧孔,需要人工进行二次加工,导致塑件的成型周期较长,人工劳动强度较大。
3.为了克服现有技术的不足,人们经过不断探索,提出了各种各样的解决方案,如中国专利公开了一种电池盒注塑模具[申请号:201820739492.x],包括上模座和下模座,下模座四角处设有定位立柱,定位立柱外套设弹簧管,上模座上设有与定位立柱相对应的通孔,弹簧位于上模座与下模座之间,下模座底端中心设有模腔,模腔内设有伸缩顶杆和调节块,上模座顶端中心设有与伸缩顶杆相对应的顶杆孔,伸缩顶杆两侧对称地设有与调节块相配合的滑槽,调节块在所述滑槽内滑移,伸缩顶杆与气缸连接,上模座底端中心轴向设有环形凸模,凸模内设有注塑管,模腔与凸模通过定位立柱和通孔实现组合成模。本实用新型结构简单、使用方便,能够实现高效注塑;防止注塑模具发生偏移,保证顶出注塑模具的稳定性,扩大了同一套模具的适用范围,便于市场大范围推广使用。但是该方案在注塑过程中仍然难以同步注塑成型电池盒侧孔,需要人工进行二次加工,导致塑件的成型周期较长,存在人工劳动强度较大的缺陷。
技术实现要素:[0004]
本实用新型的目的是针对上述问题,提供一种可快速脱模的电动车电池盒注塑模。
[0005]
为达到上述目的,本实用新型采用了下列技术方案:
[0006]
一种可快速脱模的电动车电池盒注塑模,包括注塑上模和注塑下模,所述的注塑下模上设有电池盒成型凸起,所述的注塑上模底部设有电池盒成型凹腔,所述的电池盒成型凸起与电池盒成型凹腔的位置相对应且形状相配适,所述的注塑下模上还设有电池盒侧孔成型组件,所述的电池盒侧孔成型组件与电池盒成型凸起的位置相对应,所述的注塑上模上方设置注塑分流件。
[0007]
在上述的可快速脱模的电动车电池盒注塑模中,所述的电池盒侧孔成型组件包括设置于注塑下模上的侧孔成型滑座,所述的侧孔成型滑座上设有若干沿侧孔成型滑座中心线对称的电池盒侧孔成型杆,所述的电池盒侧孔成型杆与电池盒成型凸起的位置相对应。
[0008]
在上述的可快速脱模的电动车电池盒注塑模中,所述的注塑下模内设有滑座对位腔,所述的侧孔成型滑座底部延伸通入至滑座对位腔内且侧孔成型滑座与滑座对位腔相滑动配合,所述的侧孔成型滑座与注塑上模之间设有限位连接件。
[0009]
在上述的可快速脱模的电动车电池盒注塑模中,所述的限位连接件包括设置于注塑下模上的限位防偏块,所述的限位防偏块与注塑下模之间通过紧固螺栓相连,所述的侧孔成型滑座与限位防偏块相滑动配合。
[0010]
在上述的可快速脱模的电动车电池盒注塑模中,所述的注塑上模底部设有若干沿注塑上模中心线对称的滑座固定插杆,所述的侧孔成型滑座顶部设有若干沿侧孔成型滑座中心线对称的插孔,所述的滑座固定插杆与插孔的位置相对应且形状相配适。
[0011]
在上述的可快速脱模的电动车电池盒注塑模中,所述的注塑下模上设有若干沿注塑下模中心点呈矩形阵列分布的合模对位凸块,所述的注塑上模底部设有若干沿注塑上模中心点呈矩形阵列分布的合模对位凹槽,所述的合模对位凸块与合模对位凹槽相卡接配合。
[0012]
在上述的可快速脱模的电动车电池盒注塑模中,所述的注塑分流件包括设置于注塑上模上方的注塑主流板,所述的注塑主流板内设有注塑主管,所述的注塑主管与电池盒成型凹腔的位置相对应。
[0013]
在上述的可快速脱模的电动车电池盒注塑模中,所述的注塑主流板与注塑上模之间设有注塑管固定板,所述的注塑管固定板内设有注塑管固定孔,所述的注塑主管贯穿通过注塑管固定孔。
[0014]
在上述的可快速脱模的电动车电池盒注塑模中,所述的注塑下模下方设有固定底板,所述的固定底板上设有顶出杆固定板,所述的顶出杆固定板上设有若干顶出杆。
[0015]
在上述的可快速脱模的电动车电池盒注塑模中,所述的固定底板上设有若干沿固定底板中心线对称的防偏寸铁,所述的顶出杆固定板与防偏寸铁相滑动配合。
[0016]
与现有的技术相比,本实用新型的优点在于:
[0017]
1、本实用新型通过设置电池盒侧孔成型组件,在注塑过程中,通过电池盒侧孔成型组件可同步成型电池盒侧孔,注塑完成后移动电池盒侧孔成型组件,避免影响塑件脱模,无需二次加工电池盒侧孔,大大缩短了塑件的成型周期,降低了人工劳动强度,实用性较强。
[0018]
2、本实用新型通过设置滑座固定插杆和插孔,在合模时,将滑座固定插杆插入至插孔内,使得侧孔成型滑座在注塑过程中不会发生滑动,提高了塑件成型的精确度。
[0019]
本实用新型的其它优点、目标和特征将部分通过下面的说明体现,部分还将通过对本实用新型的研究和实践而为本领域的技术人员所理解。
附图说明
[0020]
图1是本实用新型的爆炸示意图。
[0021]
图2是本实用新型另一个方向的爆炸示意图。
[0022]
图3是本实用新型的局部爆炸示意图。
[0023]
图中:注塑上模1、注塑下模2、电池盒成型凸起3、电池盒成型凹腔4、电池盒侧孔成型组件5、注塑分流件6、侧孔成型滑座7、电池盒侧孔成型杆8、滑座对位腔9、限位连接件10、限位防偏块11、滑座固定插杆12、插孔13、合模对位凸块14、合模对位凹槽15、注塑主流板16、注塑管固定板18、注塑管固定孔19、固定底板20、顶出杆固定板21、顶出杆22、防偏寸铁23。
具体实施方式
[0024]
下面结合附图对本实用新型进行进一步说明。
[0025]
如图1-3所示,一种可快速脱模的电动车电池盒注塑模,包括注塑上模1和注塑下模2,所述的注塑下模2上设有电池盒成型凸起3,所述的注塑上模1底部设有电池盒成型凹腔4,所述的电池盒成型凸起3与电池盒成型凹腔4的位置相对应且形状相配适,所述的注塑下模2上还设有电池盒侧孔成型组件5,所述的电池盒侧孔成型组件5与电池盒成型凸起3的位置相对应,所述的注塑上模1上方设置注塑分流件6。
[0026]
在本实施例中,在注塑时,将注塑上模1和注塑下模2相互靠近,使得电池盒成型凸起3与电池盒成型凹腔4相互紧贴配合,形成完整的型腔,熔融物料通过注塑分流件6注入至型腔内,在注塑过程中,通过电池盒侧孔成型组件5可同步成型电池盒侧孔,注塑完成后移动电池盒侧孔成型组件5,避免影响塑件脱模,无需二次加工电池盒侧孔,大大缩短了塑件的成型周期,降低了人工劳动强度,实用性较强。
[0027]
结合图1、图3所示,所述的电池盒侧孔成型组件5包括设置于注塑下模2上的侧孔成型滑座7,所述的侧孔成型滑座7上设有若干沿侧孔成型滑座7中心线对称的电池盒侧孔成型杆8,所述的电池盒侧孔成型杆8与电池盒成型凸起3的位置相对应。
[0028]
具体地说,侧孔成型滑座7用以连接固定电池盒侧孔成型杆8,在合模后,电池盒侧孔成型杆8延伸通入至型腔内,通过电池盒侧孔成型杆8可同步辅助成型电池盒侧孔,无需二次加工电池盒侧孔,大大缩短了塑件的成型周期,降低了人工劳动强度,实用性较强。
[0029]
结合图1、图3所示,所述的注塑下模2内设有滑座对位腔9,所述的侧孔成型滑座7底部延伸通入至滑座对位腔9内且侧孔成型滑座7与滑座对位腔9相滑动配合,所述的侧孔成型滑座7与注塑上模1之间设有限位连接件10。
[0030]
本实施例中,滑座对位腔9用以放置侧孔成型滑座7,在注塑完成后,将侧孔成型滑座7向远离电池盒成型凸起3一端移动,使得电池盒侧孔成型杆8从电池盒塑件侧部抽离,避免塑件下一步脱模,限位连接件10对侧孔成型滑座7起到限位的作用,避免侧孔成型滑座7在移动过程中发生角度偏移。
[0031]
所述的限位连接件10包括设置于注塑下模2上的限位防偏块11,所述的限位防偏块11与注塑下模2之间通过紧固螺栓相连,所述的侧孔成型滑座7与限位防偏块11相滑动配合。
[0032]
本实施例中,通过限位防偏块11与侧孔成型滑座7之间的滑动配合,对侧孔成型滑座7起到限位作用,避免侧孔成型滑座7在移动过程中发生角度偏移。
[0033]
结合图2、图3所示,所述的注塑上模1底部设有若干沿注塑上模1中心线对称的滑座固定插杆12,所述的侧孔成型滑座7顶部设有若干沿侧孔成型滑座7中心线对称的插孔13,所述的滑座固定插杆12与插孔13的位置相对应且形状相配适。
[0034]
本实施例中,在合模时,将滑座固定插杆12插入至插孔13内,使得侧孔成型滑座7在注塑过程中不会发生滑动,提高了塑件成型的精确度。
[0035]
所述的注塑下模2上设有若干沿注塑下模2中心点呈矩形阵列分布的合模对位凸块14,所述的注塑上模1底部设有若干沿注塑上模1中心点呈矩形阵列分布的合模对位凹槽15,所述的合模对位凸块14与合模对位凹槽15相卡接配合。
[0036]
本实施例中,在合模过程中,将合模对位凸块14与合模对位凹槽15相互靠近,通过
合模对位凸块14与合模对位凹槽15之间的卡接配合,完成合模,合模精度较高。
[0037]
所述的注塑分流件6包括设置于注塑上模1上方的注塑主流板16,所述的注塑主流板16内设有注塑主管,所述的注塑主管与电池盒成型凹腔4的位置相对应。
[0038]
本实施例中,在注塑过程中,熔融物料通过注塑主管注入至型腔内,完成注塑。
[0039]
结合图1所示,所述的注塑主流板16与注塑上模1之间设有注塑管固定板18,所述的注塑管固定板18内设有注塑管固定孔19,所述的注塑主管贯穿通过注塑管固定孔19。
[0040]
本实施例中,注塑管固定板18和注塑管固定孔19用以固定注塑主管,确保注塑主管的安装精度。
[0041]
结合图1、图2所示,所述的注塑下模2下方设有固定底板20,所述的固定底板20上设有顶出杆固定板21,所述的顶出杆固定板21上设有若干顶出杆22。
[0042]
本实施例中,顶出杆固定板21用以固定顶出杆22,在注塑完成后,移动顶出杆固定板21,通过顶出杆固定板21带动顶出杆22移动,将塑件从注塑下模2处顶出。
[0043]
结合图1所示,所述的固定底板20上设有若干沿固定底板20中心线对称的防偏寸铁23,所述的顶出杆固定板21与防偏寸铁23相滑动配合。
[0044]
本实施例中,在顶出杆固定板21移动过程中,通过顶出杆固定板21与防偏寸铁23之间的滑动配合,可避免顶出杆固定板21在移动过程中发生角度偏移,提高了顶出的精确度。
[0045]
本实用新型的工作原理是:
[0046]
在注塑时,将注塑上模1和注塑下模2相互靠近,使得电池盒成型凸起3与电池盒成型凹腔4相互紧贴配合,形成完整的型腔,在合模时,将滑座固定插杆12插入至插孔13内,使得侧孔成型滑座7在注塑过程中不会发生滑动,提高了塑件成型的精确度,
[0047]
熔融物料通过注塑主管注入至型腔内,进行注塑,侧孔成型滑座7用以连接固定电池盒侧孔成型杆8,在合模后,电池盒侧孔成型杆8延伸通入至型腔内,通过电池盒侧孔成型杆8可同步辅助成型电池盒侧孔,无需二次加工电池盒侧孔,大大缩短了塑件的成型周期,降低了人工劳动强度,实用性较强,
[0048]
在注塑完成后,将侧孔成型滑座7向远离电池盒成型凸起3一端移动,使得电池盒侧孔成型杆8从电池盒塑件侧部抽离,避免塑件下一步脱模,限位防偏块11对侧孔成型滑座7起到限位的作用,避免侧孔成型滑座7在移动过程中发生角度偏移,
[0049]
在注塑完成后,移动顶出杆固定板21,通过顶出杆固定板21带动顶出杆22移动,将塑件从注塑下模2处顶出,在顶出杆固定板21移动过程中,通过顶出杆固定板21与防偏寸铁23之间的滑动配合,可避免顶出杆固定板21在移动过程中发生角度偏移,提高了顶出的精确度。
[0050]
本文中所描述的具体实施例仅仅是对本实用新型精神作举例说明。本实用新型所属技术领域的技术人员可以对所描述的具体实施例做各种各样的修改或补充或采用类似的方式替代,但并不会偏离本实用新型的精神。
[0051]
尽管本文较多地使用注塑上模1、注塑下模2、电池盒成型凸起3、电池盒成型凹腔4、电池盒侧孔成型组件5、注塑分流件6、侧孔成型滑座7、电池盒侧孔成型杆8、滑座对位腔9、限位连接件10、限位防偏块11、滑座固定插杆12、插孔13、合模对位凸块14、合模对位凹槽15、注塑主流板16、注塑管固定板18、注塑管固定孔19、固定底板20、顶出杆固定板21、顶出
杆22、防偏寸铁23等术语,但并不排除使用其它术语的可能性。使用这些术语仅仅是为了更方便地描述和解释本实用新型的本质,把它们解释成任何一种附加的限制都是与本实用新型精神相违背的。