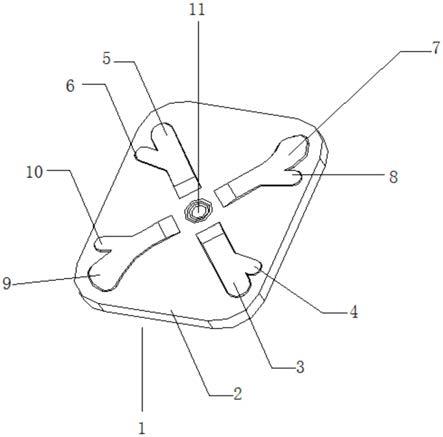
1.本实用新型涉及陶瓷成型技术领域,尤其是涉及一种陶瓷件引流模具结构。
背景技术:2.在注塑成型时,当型腔里存在孔洞、内嵌件以及产品厚度尺寸变化较大时,原料物质在模具内会发生两个方向以上的流动,当两股原料相接时,由于在冷却过程中会有困气,困气阻挠聚合物分子的缠绕效应,在两股原料结合处因未能完全融合而产生的细线,叫熔接线。
3.熔接线是在注塑充填过程中形成的,其结构、形状和性质与整个注塑成型过程密切相关。熔接线的存在不仅影响到产品的外观质量,而且对产品的力学性能及强度影响很大。熔接线是注塑领域最难处理的问题之一。
4.现有技术中,为尽量减少熔接线问题的出现,普遍采用为模具设计直线引流道,为增强流速,还会在引流道末端加上凸起结构。此方法能在一定程度上减少熔接线问题,但其缺陷在于:
5.1、产品内部结构越多,凸起结构的数量也会增加,将拉高生产成本;2、过多的凸起结构会增加原料注塑产生的涡流,易造成产品的内截面异常,降低产品的抗挤压强度;3、产品每个拐角只有一条直线引流,流动的原料通过直身引流到达凸起结构时流速降低,凸起结构两侧的流速反而加快,产生了两侧合流的熔接线;4、当产品有长短边又有内部结构时,单一的直线引流无法兼顾长边的流动速度和内部结构,直线引流指向长边时,有内部结构的拐角流速就降低,当指向拐角内部结构时,长边的流速就会降低,两种方式都会产生较多的熔接缺陷,会降低产品的外观良率和结构强度。
6.因此,为解决上述问题,需要设计一种能够有效克服产品熔接线的引流模具结构。
技术实现要素:7.本实用新型公开一种陶瓷件引流模具结构,能够克服上述现有引流结构无法消除熔接线,良率不高的缺陷。
8.本实用新型的一种陶瓷件引流模具结构,包括结构本体,所述结构本体包括上腔体和下腔体;在所述上腔体的一个表面设置进胶口,围绕所述进胶口设置所述引流通道,在所述引流通道上设置分叉而形成所述分叉通道,所述引流通道距离所述进胶口较近的一端与所述进胶口保持间距。
9.优选地,所述引流通道与所述进胶口较近的一端与所述进胶口的间距设置为相等间距。
10.优选地,所述引流通道为至少一条,所述引流通道的形状包括前端与后端宽度相等的长条形。
11.优选地,所述进胶口为至少一个,其形状设置为圆环内凹形状。
12.优选地,所述引流通道相对于上腔体表面呈凸起状,凸起高度为0.1-0.35cm。
13.优选地,所述引流通道为至少一条,所述引流通道的形状包括前端与后端宽度不相等的长条形。
14.优选地,所述引流通道为至少一条,设置为斜对角方向对称。
15.优选地,所述下腔体的下表面的型腔设置为内凹状,在所述下表面的型腔与边框结合处的四角设置为拐角,且为斜对角方向对称。
16.优选地,所述结构本体包括陶瓷和塑料材质。
17.优选地,所述分叉通道相对于所述引流通道的角度设置为0-90
º
。
18.综上,相对于现有技术,本实用新型的一种陶瓷件引流模具结构是取消现有技术中内部结构处的加强凸起结构,在直线引流道的基础上增加分叉,设置分叉通道,起到加强引流的指向加速作用,不会对后续操作工序产生不利的影响。在降低单片产品重量的同时,兼顾了产品内部结构和长短边的流速问题,有效减少注射过程中产生的涡流,提升产品的抗挤压强度,能有效克服熔接线缺陷,使产品最终成型后外观的熔接缺陷从过去的1.47%降到了0.00%。
附图说明
19.图1是本实用新型的一种陶瓷件引流模具结构的上腔体整体结构示意图;
20.图2是本实用新型的一种陶瓷件引流模具结构的下腔体背面示意图;
21.图3是本实用新型的一种陶瓷件引流模具结构的正面示意图;
22.图4是本实用新型的一种陶瓷件引流模具结构正面的a-a剖视图;
23.图5是本实用新型的一种陶瓷件引流模具结构的五通道结构示意图;
24.图6是本实用新型的一种陶瓷件引流模具结构的六通道结构示意图;
25.图7是本实用新型的一种陶瓷件引流模具结构的七通道结构示意图;
26.图8是本实用新型的一种陶瓷件引流模具结构的八通道结构示意图;
27.附图标记说明:
28.1-上腔体,2-上表面,3-引流通道a,4-分叉通道a,5-引流通道a,6-分叉通道a,7-引流通道b,8-分叉通道b,9-引流通道b,10-分叉通道b,11-进胶口,12-下腔体,13-型腔,14-边框,15-拐角a,16-拐角b,17-结构本体,18-引流通道c,19-引流通道d,20-引流通道e,21-引流通道f。
具体实施方式
29.为了更清楚说明本实用新型的目的、技术方案和特点,下文将详细描述本实用新型的实施例,所述实施例的示例在附图中示出,下文通过参考附图描述的实施例是示例性的,仅用于解释本实用新型,而不能简单理解为对本实用新型的限制。需要说明的是,在本实用新型的描述中,相关术语“中心”、“纵向”、“横向”、“长度”、“宽度”、“厚度”、“上”、“下”、“前”、“后”、“左”、“右”、“竖直”、“水平”、“顶”、“底”、“内”、“外”、“轴向”、“径向”、“周向”等指示的方位或位置关系为基于附图所示的方位或位置关系,仅是为便于描述本实用新型而简化述之,并非指示或暗示所指的装置或元件必须具有特定的方位、以特定的方位构造和操作,因而不能理解为对本实用新型的限制。
30.下面将结合附图1-8,以具体实施例对本实用新型作进一步地详细阐述:
31.实施例一
32.为克服现有的引流模具中直线引流道易出现熔接线的问题,如图1、图2和图4所示,本实用新型提供了一种陶瓷件引流模具结构,包括结构本体(17),所述结构本体(17)包括上腔体(1)和下腔体(12);在所述上腔体(1)的上表面(2)设置进胶口(11),围绕所述进胶口(11)设置所述引流通道a(3)、引流通道a(5)、引流通道b(7)和引流通道b(9),在上述各条引流通道上设置分叉而形成所述分叉通道a(4)、分叉通道a(6)、分叉通道b(8)和分叉通道b(10),上述引流通道距离所述进胶口(11)较近的一端与所述进胶口(11)保持一定间距。
33.所述引流通道a(3)、引流通道a(5)、引流通道b(7)和引流通道b(9)与所述进胶口(11)较近的一端的间距设置为相等间距。
34.所述引流通道为四条,分别是引流通道a(3)、引流通道a(5)、引流通道b(7)和引流通道b(9),设置为斜对角方向对称,上述引流通道a(3)和引流通道a(5)的形状对称设置为前端宽度与后端宽度相等的长条形,引流通道a(7)和引流通道a(9)的形状对称设置为前端宽度与后端宽度不相等的长条形,具体表现为后端宽度相比前端更宽。上述各条引流通道相对于上腔体(1)的上表面(2)呈现凸起状,凸起高度为0.1-0.35cm。
35.所述进胶口(11)为一个,其形状为圆环内凹形状,位置设置在上表面的中心位置。
36.所述分叉通道设置在所述引道通道上,分别为分叉通道a(4)、分叉通道a(6)、分叉通道b(8)和分叉通道b(10),相对于所述引流通道a(3)、引流通道a(5)、引流通道b(7)和引流通道b(9)的水平面,上述分叉通道的角度设置为0-90
º
。
37.所述下腔体(12)的下表面的型腔(13)设置为内凹状,在所述下表面的型腔(13)与边框(14)结合处的四角各设置一对拐角a(15)和拐角b(16),且呈斜对角方向对称。
38.所述结构本体(17)包括陶瓷和塑料材质。
39.实施例二
40.如图5所示,本实施例与实施例一区别在于:在所述上腔体(1)的上表面(2)设置进胶口(11),围绕所述进胶口(11)设置所述引流通道a(3)、引流通道a(5)、引流通道b(7)、引流通道b(9)和引流通道c(18),所述引流通道c(18)紧邻引流通道a(3)设置。
41.实施例三
42.如图6所示,本实施例与实施例一区别在于:在所述上腔体(1)的上表面(2)设置进胶口(11),围绕所述进胶口(11)设置所述引流通道a(3)、引流通道a(5)、引流通道b(7)、引流通道b(9)、引流通道c(18)和引流通道d(19),所述引流通道c(18)和引流通道d(19)分别紧邻引流通道a(3)和引流通道a(5)设置。
43.实施例四
44.如图7所示,本实施例与实施例一区别在于:在所述上腔体(1)的上表面(2)设置进胶口(11),围绕所述进胶口(11)设置所述引流通道a(3)、引流通道a(5)、引流通道b(7)、引流通道b(9)、引流通道c(18)、引流通道d(19)和引流通道e(20),所述引流通道c(18)、引流通道d(19)和引流通道e(20)分别紧邻引流通道a(3)、引流通道a(5)和引流通道b(9)设置。
45.实施例五
46.如图8所示,本实施例与实施例一区别在于:在所述上腔体(1)的上表面(2)设置进胶口(11),围绕所述进胶口(11)设置所述引流通道a(3)、引流通道a(5)、引流通道b(7)、引流通道b(9)、引流通道c(18)、引流通道d(19)、引流通道e(20)和引流通道f(21),所述引流
通道c(18)、引流通道d(19)、引流通道e(20)和引流通道f(21)分别紧邻引流通道a(3)、引流通道a(5)、引流通道b(9)和引流通道b(7)对称设置。
47.本实用新型为克服现有的引流模具中直线引流道易出现熔接线的问题,在注射成型分流技术方面,提供了一种陶瓷件引流模具结构,当呈流体状的陶瓷原料加压注射进入模具的进胶口时,原料按照进胶口的内凹圆形结构,呈现圆形流动状态并逐步充填模具,流动中的陶瓷原料遇到四条引流通道时,圆形的流动状态被引流通道改变,当趋于长方形的状态时使得长边先填充满,填充至分叉通道时,长边的填充速度再一次被加快,使其快于四个拐角的填充速度,引道通道的末端配合分叉通道使得四个拐角的填充速度加快,最后再逐渐填充至产品的短边。本实用新型在降低产品重量的同时,兼顾了内部结构和长短边的流速问题,有效减少注射过程中产生的涡流,提升产品的抗挤压强度,能有效克服熔接线缺陷,使产品最终成型后外观的熔接缺陷从过去的1.47%降到了0.00%。
48.本实用新型的生产流程如下:
49.1、设计有分叉通道的胚料图,用模流分析软件对注射过程进行模拟,达到预期效果后,制作及组装相应模具;
50.2、将组装好的模具固定在注塑机上生产,注射成型过程中进行注射成型分流技术的不断优化,得到相应产品;
51.3、注射完成的产品经cnc去除部分余量;
52.4、进行脱脂烧结,得到相应的烧结件;
53.5、对烧结件进行cnc整件精加工;
54.6、抛光打磨;
55.7、检测通过得到合格产品。
56.以上所述仅为本实用新型优选的实施例,本领域内普通技术人员在通读本说明书后,结合公知常识,应能联想到更多的具体实施方式,此类具体实施方式并不超脱本实用新型权利所要求的精神和原则,任何形式的等同替换或若干改进和润饰均应视为被本实用新型所包括的实施例,属于本实用新型的保护范围。