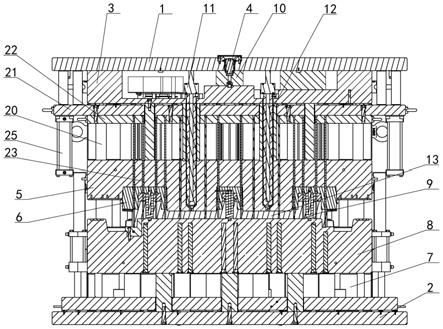
1.本实用新型涉及一种双层热流道式塑料围板箱底座模具,属于塑料模具领域。
背景技术:2.随和物流行业的不断发展,在运输化工化学等液体物品时,需要用到围板箱,围板箱由底座和四侧围板构成,底座采用塑料模具注塑加工成型。已有围板箱的体积小,相应的底座体积也小,传统塑料模具的热流道系统能够满足底座的流量注射要求。但体积小,运输效率低,为了提高围板箱的运输能力,必须要开发体积大的围板箱,在开发过程中,发现传统的热流道系统无法满足大型围板箱底座的流量注射要求,具体表现为塑料物料填充不充足,流量不均匀,产品表面出现大面积的缩影,为此,我们开发了一种双层热流道系统,可以满足大型围板箱底座的流量要求。
技术实现要素:3.本实用新型的目的是为了克服已有技术的缺点,提供一种热流道系统采用双层分流构成,使塑料物料流量均匀,填充饱满,提高产品成型率的双层热流道式塑料围板箱底座模具。
4.本实用新型双层热流道式塑料围板箱底座模具的技术方案是:包括模具定模复板和动模复板,定模复板上设置浇口,定模复板下设置流道板,流道板中设置热流道系统,流道板下设有定模侧顶出机构,定模侧顶出机构下设置定模板,定模板中是设置定模镶块,动模复板上安装模脚,模脚上安装动模板,动模板上设置动模镶块,动模板和动模镶块与定模板和定模镶块相配合构成模腔,其特征在于所述的热流道系统为双层热流道,包括第一层热流道和第二层热流道,所述第一层热流道为
×
字型热流道架,浇口连通
×
字型热流道架的交叉中心处a,所述第二层热流道包括四块独立的分流板,四块分流板各自嵌设在流道板中,
×
字型热流道架位于四块分流板的上方,且
×
字型热流道架的四个端点b分别连通四块分流板,每块分流板下至少连接两个以上热嘴,热嘴穿过流道板和定模板与模腔相连通,模腔中注塑产品。
5.本实用新型双层热流道式塑料围板箱底座模具,主要特点是将热流道系统设计为双层结构,包括第一层热流道和第二层热流道,所述第一层热流道为
×
字型热流道架,所述第二层热流道为四块独立的分流板,四块分流板各自嵌设在流道板中,浇口连通
×
字型热流道架的交叉中心处a,
×
字型热流道架的四个端点b分别连通四块分流板,每块分流板下至少连接两个以上热嘴,上热嘴连通模腔,注塑时,熔融的塑料原料从注塑机的喷头注入浇口,再流入
×
字型热流道架中,然后通过四个端点b分流到四块分流板中,最后通过热嘴注入模腔中,将产品注塑成型。其优点是:熔融的塑料原料通过第一层的
×
字型热流道架分流到第二层的四块分流板中,即从交叉中心处a流到四个端点b,使各块分流板流量均匀,再通过每块分流板上至少2个以上的热嘴注射,使模腔能够快速填充饱满,既缩短了注射时间,又保证流量均匀,填充充足,提高生产效率和产品质量。
6.本实用新型双层热流道式塑料围板箱底座模具,所述的
×
字型热流道架上设置上加热铜管。所述的四块分流板上均设置下加热铜管。上、下加热铜管分别对
×
字型热流道架和四块分流板进行预热加热,确保流经的熔融塑料原料不冷却凝固,保证流速和流量均匀。所述的定模侧顶出机构包括在流道板的两侧各设置垫块,两个垫块之间设置定模上顶板和定模下顶板,定模下顶板上连接定模顶针,定模顶针穿过定模板和定模镶块与产品相接触,在定模上顶板的两侧伸出垫块,并在两侧的伸出处各设置定模顶出油缸,定模顶出油缸的油缸杆连接定模复板。根据产品(围板箱底座)的外形和结构分析,产品成型后留在定模板和定模镶块上,因此产品的脱模采用定模侧顶出脱模方式,当模具开模后,定模顶出油缸带动定模上顶板下顶,定模上顶板带动定模下顶板,定模下顶板带动定模顶针将产品顶出模具外。
附图说明
7.图1是本实用新型双层热流道式塑料围板箱底座模具结构示意图;
8.图2是本实用新型的双层热流道系统剖面示意图;
9.图3是本实用新型的双层热流道系统俯视示意图;
10.图4是本实用新型的双层热流道系统立体示意图。
具体实施方式
11.本实用新型涉及一种双层热流道式塑料围板箱底座模具,如图1—图4所示,包括模具定模复板1和动模复板2,定模复板上设置浇口4,定模复板下设置流道板3,流道板中设置热流道系统,流道板下设有定模侧顶出机构,定模侧顶出机构下设置定模板5,定模板中是设置定模镶块6,动模复板上安装模脚7,模脚上安装动模板8,动模板上设置动模镶块9,动模板8和动模镶块9与定模板5和定模镶块6相配合构成模腔,所述的热流道系统为双层热流道,包括第一层热流道和第二层热流道,所述第一层热流道为
×
字型热流道架10,浇口4连通
×
字型热流道架10的交叉中心处a,所述第二层热流道包括四块独立的分流板11,四块分流板各自嵌设在流道板3中,
×
字型热流道架10位于四块分流板11的上方,且
×
字型热流道架10的四个端点b分别连通四块分流板11,每块分流板11下至少连接两个以上热嘴12,热嘴12穿过流道板3和定模板5与模腔相连通,模腔中注塑产品13。本方案的主要特点是将热流道系统设计为双层结构,包括第一层热流道和第二层热流道,所述第一层热流道为
×
字型热流道架10,所述第二层热流道为四块独立的分流板11,四块分流板各自嵌设在流道板3中,浇口4连通
×
字型热流道架10的交叉中心处a,
×
字型热流道架10的四个端点b分别连通四块分流板11,每块分流板11下至少连接两个以上热嘴12,上热嘴12连通模腔,注塑时,熔融的塑料原料从注塑机的喷头注入浇口4,再流入
×
字型热流道架10中,然后通过四个端点b分流到四块分流板11中,最后通过热嘴12注入模腔中,将产品13注塑成型。其优点是:熔融的塑料原料通过第一层的
×
字型热流道架10分流到第二层的四块分流板中,即从交叉中心处a流到四个端点b,使各块分流板流量均匀,再通过每块分流板上至少2个以上的热嘴12注射,使模腔能够快速填充饱满,既缩短了注射时间,又保证流量均匀,填充充足,提高生产效率和产品质量。所述的
×
字型热流道架10上设置上加热铜管15。所述的四块分流板11上均设置下加热铜管16。上、下加热铜管分别对
×
字型热流道架10和四块分流板进行预热加热,
确保流经的熔融塑料原料不冷却凝固,保证流速和流量均匀。所述的定模侧顶出机构包括在流道板3的两侧各设置垫块20,两个垫块之间设置定模上顶板21和定模下顶板22,定模下顶板上连接定模顶针23,定模顶针23穿过定模板和定模镶块与产品13相接触,在定模上顶板21的两侧伸出垫块,并在两侧的伸出处各设置定模顶出油缸25,定模顶出油缸25的油缸杆连接定模复板1。根据产品13(围板箱底座)的外形和结构分析,产品成型后留在定模板和定模镶块上,因此产品的脱模采用定模侧顶出脱模方式,当模具开模后,定模顶出油缸带动定模上顶板下顶,定模上顶板带动定模下顶板,定模下顶板带动定模顶针将产品顶出模具外。