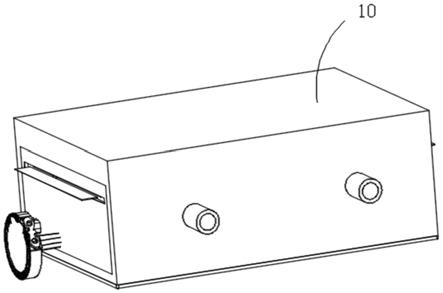
生物降解pbat/pla复合膜的制备装置及制备方法
技术领域
1.本发明涉及聚酯类可降解塑料领域,尤其涉及一种生物降解pbat(己二酸丁二醇酯和对苯二甲酸丁二醇酯的共聚物)/pla(聚乳酸)复合膜的制备装置及制备方法。
背景技术:2.目前,随着工业的发展,人们对制造出来的制品是否环保越来越重视,于是经过大量研究,研发出了高分子聚合物可降解环保材料pla,pla材料经过挤出、拉丝或注塑设备注射成型得到,由于pla材料价格昂贵,价格一直保持在40元/kg以上,导致目前市场上pla可降解环保材料制品较少。随着人们对环保问题越来越重视,“白色污染”和石油危机问题迫使人们对新型可生物降解无污染塑料制品的研究越来越多,在众多生物降解塑料中,聚己二酸-对苯二甲酸丁二酯和聚乳酸因具有良好的生物可降解性能而备受人们关注。
3.申请号为“cn201710761543.9”的专利文献公开了一种pbat/pla多层复合膜的制备方法。所述的制备方法包括以下步骤:首先用二氯甲烷溶解pla与pbat,再将逐层浇铸法得到pbat/pla多层复合膜,最后真空干燥密封保存。本发明的制备方法制备工艺简单,易于操作,所得产物具有良好的力学性能,能适用于包装领域;同时所生产的材料容易降解,对环境没有污染,耐久性良好,充分符合环保可持续发展的理念。
4.申请号为“cn201611142638.4”的专利文献公开了一种降解可控pbat/pla复合膜,包括如下组分及重量份数为:pbat50-60份,pla10-30份,碳酸钙10-20份,抗菌性增容剂0.5-2份,钛酸四丁酯0.5-2份;其中pla与碳酸钙的质量比为:1-3:1。本发明的一种降解可控pbat/pla复合膜,通过严格控制pla与碳酸钙的配比,限制其在1-3:1的范围内,通过调控pla与碳酸钙的比例可以将pbat/pla复合膜的降解时开始降解的时间控制在60天到90天之间,完全降解的时间在120天到150天。
5.上述专利文献揭示了现有技术中pbat/pla复合膜的制备存在以下缺陷:
6.1、市面上的pbat/pla复合膜的制备设备或方法比较复杂,制备效率低、速度慢;
7.2、市面上的pbat/pla复合膜的制备设备或方法存在pbat材料与pla材料复合程度差。
技术实现要素:8.为了克服现有技术的不足,本发明的目的之一在于提供一种生物降解pbat/pla复合膜的制备装置及制备方法,其能解决效率低、速度慢、复合程度差的问题。
9.本发明的目的之一采用如下技术方案实现:
10.一种生物降解pbat/pla复合膜的制备装置,包括外侧壳体组件、高压电极端、第一移动滴液辅助装置、第二移动滴液辅助装置、pla膜、至少两个间隔扶正板,所述外侧壳体组件设置有进口端、出口端,所述pla膜沿进口端插入并沿出口端流出;间隔扶正板设置于所述外侧壳体组件内并将所述外侧壳体组件内的腔体分割为第一反应腔体、第二反应腔体、末端腔体;所述第一移动滴液辅助装置设置于所述第一反应腔体,所述第二移动滴液辅助
装置设置于所述第二反应腔体;所述外侧壳体组件内设置有至少两个高压电极端使滴液辅助装置的上侧形成高压区间,pla膜沿所述高压区间移动;所述第一移动滴液辅助装置与所述第二移动滴液辅助装置结构相同,所述第一移动滴液辅助装置包括侧部无杆气缸、u型座、安装在u型座上的若干个平行分布的线体、用于沿线体移动滴液的移动滴液组件,所述无杆气缸固定于所述u型座的侧部,所述无杆气缸与所述移动滴液组件固定连接并带动所述移动滴液组件移动,所述移动滴液组件用于喷出pbat材质的液滴,在高压区间的作用下拉丝并与pla膜贴合以形成pbat/pla复合膜。
11.进一步地,所述外侧壳体组件的外侧设置有用于为第一反应腔体提供控温作用的第一进风管路、第一出风管路,所述第一进风管路的外侧设置有第一加热风机。
12.进一步地,所述外侧壳体组件的外侧设置有用于为第二反应腔体提供控温作用的第二进风管路、第二进风管路,所述第二进风管路的外侧设置有第二加热风机。
13.进一步地,所述第二加热风机的加热温度高于所述第一加热风机的加热温度,所述外侧壳体组件还设置有尾部吸气风机,所述尾部吸气风机的吸气端设置于末端腔体。
14.进一步地,所述第一加热风机用于第一反应腔体的温度加热至50-100摄氏度之间,所述第二加热风机用于第二反应腔体的温度加热至150-200摄氏度之间。
15.进一步地,所述间隔扶正板上设置有用于穿过pla膜的缺口,所述缺口的宽度为2-5cm。
16.进一步地,所述侧部无杆气缸的侧部设置有移动板,若干个移动滴液组件固定于移动板上;所述u型座设置有两个安装端,每一安装端上设置有若干个夹线组件,每一所述夹线组件包括u型夹、与u型夹配合安装的锁固螺丝,所述锁固螺丝用于线体固定于u型夹上。
17.进一步地,所述移动滴液组件设置有v型端面,所述移动滴液组件设置两个滴液喷头,两个滴液喷头设置于v型端面上,两个滴液喷头的出液方向呈锐角,线体位于两个滴液喷头之间。
18.一种生物降解pbat/pla复合膜的制备方法,包括以下步骤:
19.混合步骤:将pbat颗粒物与聚二甲基硅氧烷添加剂混合,加热形成待滴取混合物熔体;
20.拉丝步骤:待滴取混合物熔体通过计量泵输送至移动滴液组件,设置两个高压电极端,两个高压电极端形成高压区间,移动滴液组件滴取待拉丝液到高压区间内,待拉丝液体经高压作用生成纳米纤维丝;
21.贴合步骤:pla膜沿高压区间移动,纳米纤维丝沿pla膜的移动方向贴合到pla膜的表面,形成pbat/pla复合膜。
22.进一步地,在所述贴合步骤中,pla膜先经过第一反应腔体进行一次贴合,再经过第二反应腔体进行二次贴合,使第一反应腔体的温度小于第二反应腔体的温度,pla膜连续经过第一反应腔体、第二反应腔体后,继续让pla膜经过末端腔体,在末端腔体内设置吸气风机进行冷却并形成负压空间。
23.相比现有技术,本发明的有益效果在于:
24.所述第一移动滴液辅助装置设置于所述第一反应腔体,所述第二移动滴液辅助装置设置于所述第二反应腔体;所述外侧壳体组件内设置有至少两个高压电极端使滴液辅助
装置的上侧形成高压区间,pla膜沿所述高压区间移动;所述第一移动滴液辅助装置与所述第二移动滴液辅助装置结构相同,所述第一移动滴液辅助装置包括侧部无杆气缸、u型座、安装在u型座上的若干个平行分布的线体、用于沿线体移动滴液的移动滴液组件,所述无杆气缸固定于所述u型座的侧部,所述无杆气缸与所述移动滴液组件固定连接并带动所述移动滴液组件移动,使移动滴液组件喷出pbat材质的液滴,在高压区间的作用下拉丝并与pla膜贴合以形成pbat/pla复合膜,其移动滴液组件滴取待拉丝液到高压区间内,待拉丝液体经高压作用生成纳米纤维丝,pla膜先经过第一反应腔体进行一次贴合,再经过第二反应腔体进行二次贴合。使得本技术文件采用高压电极端与滴液辅助装置的配合在pla上快速复合,简化了pbat/pla复合膜的制备方法,提高了制备的效率,生产速度快,同时可以解决复合程度差的问题。
25.上述说明仅是本发明技术方案的概述,为了能够更清楚了解本发明的技术手段,而可依照说明书的内容予以实施,并且为了让本发明的上述和其他目的、特征和优点能够更明显易懂,以下特举较佳实施例,并配合附图,详细说明如下。
附图说明
26.图1为根据本发明一些实施例所示的生物降解pbat/pla复合膜的制备装置的立体图;
27.图2为图1所示生物降解pbat/pla复合膜的制备装置的侧视立体图;
28.图3为图1所示生物降解pbat/pla复合膜的制备装置的内部结构图;
29.图4为图1所示生物降解pbat/pla复合膜的制备装置的内部仰视结构图;
30.图5为图1所示生物降解pbat/pla复合膜的制备装置的局部立体图;
31.图6为图1所示生物降解pbat/pla复合膜的制备装置的另一局部立体图;
32.图7为图1所示生物降解pbat/pla复合膜的制备装置的又一局部立体图;
33.图8为根据本发明一些实施例所示的生物降解pbat/pla复合膜的制备方法的流程图。
34.图中:10、外侧壳体组件;11、进口端;12、出口端;13、第一反应腔体;14、第二反应腔体;15、末端腔体;101、第一进风管路;102、第一出风管路;103、第二进风管路;104、第二进风管路;105、尾部吸气风机;20、高压电极端;30、第一移动滴液辅助装置;40、第二移动滴液辅助装置;31、侧部无杆气缸;311、移动板;32、u型座;321、安装端;322、夹线组件;3221、u型夹;3222、锁固螺丝;33、线体;34、移动滴液组件;341、滴液喷头;50、高压区间;60、pla膜;90、间隔扶正板。
具体实施方式
35.下面,结合附图以及具体实施方式,对本发明做进一步描述,需要说明的是,在不相冲突的前提下,以下描述的各实施例之间或各技术特征之间可以任意组合形成新的实施例。
36.需要说明的是,当组件被称为“固定于”另一个组件,它可以直接在另一个组件上或者也可以存在居中的组件。当一个组件被认为是“连接”另一个组件,它可以是直接连接到另一个组件或者可能同时存在居中组件。当一个组件被认为是“设置于”另一个组件,它
可以是直接设置在另一个组件上或者可能同时存在居中组件。本文所使用的术语“垂直的”、“水平的”、“左”、“右”以及类似的表述只是为了说明的目的。
37.除非另有定义,本文所使用的所有的技术和科学术语与属于本发明的技术领域的技术人员通常理解的含义相同。本文中在本发明的说明书中所使用的术语只是为了描述具体的实施例的目的,不是旨在于限制本发明。本文所使用的术语“及/或”包括一个或多个相关的所列项目的任意的和所有的组合。
38.示例性地,本说明书实施例中的pbat的型号为th801 t;实施例中的pla的牌号为i ngeo 4032d。
39.请参阅图1-7,一种pbat(己二酸丁二醇酯和对苯二甲酸丁二醇酯的共聚物)、pla(聚乳酸)复合膜的制备装置,包括外侧壳体组件10、高压电极端20、第一移动滴液辅助装置30、第二移动滴液辅助装置40、pla膜60、至少两个间隔扶正板90,所述外侧壳体组件10设置有进口端11、出口端12,所述pla膜60沿进口端11插入并沿出口端12流出;间隔扶正板90设置于所述外侧壳体组件10内并将所述外侧壳体组件10内的腔体分割为多个腔体。例如,间隔扶正板90的数量为2个,所述2个间隔扶正板90将所述外侧壳体组件10内的腔体分割为第一反应腔体13、第二反应腔体14、末端腔体15;所述第一移动滴液辅助装置30设置于所述第一反应腔体13,所述第二移动滴液辅助装置40设置于所述第二反应腔体14;所述外侧壳体组件10内设置有至少两个高压电极端20使滴液辅助装置(例如,第一移动滴液辅助装置30、第二移动滴液辅助装置40)的上侧形成高压区间50,pla膜60沿所述高压区间50移动;所述第一移动滴液辅助装置30与所述第二移动滴液辅助装置40结构相同或相似。在本实施例中,所述第一移动滴液辅助装置30包括侧部无杆气缸31、u型座32、安装在u型座32上的若干个平行分布的线体33、用于沿线体33移动滴液的移动滴液组件34,所述无杆气缸31固定于所述u型座32的侧部,所述无杆气缸31与所述移动滴液组件34固定连接并带动所述移动滴液组件34移动,移动滴液组件34喷出pbat材质的液滴,在高压区间50的作用下拉丝并与pla膜60贴合以形成可生物降解pbat/pla复合膜。采用高压电极端20与滴液辅助装置的配合在pla上快速复合,加工效率高,速度快,同时可以解决复合程度差的问题。高压电极端20与滴液辅助装置之间形成上万伏的静电场,从而使pbat拉丝与pla复合。
40.优选的,所述外侧壳体组件10的外侧设置有用于为第一反应腔体13提供控温作用的第一进风管路101、第一出风管路102,所述第一进风管路101的外侧设置有用于加热的第一加热风机(图中未示出)。所述外侧壳体组件10的外侧设置有用于为第二反应腔体14提供控温作用的第二进风管路103、第二进风管路104,所述第二进风管路103的外侧设置有用于加热的第二加热风机(图中未示出)。
41.优选的,所述第二加热风机用于使第二反应腔体14的温度处于第二温度范围(例如,50-100摄氏度、50-60摄氏度、60-70摄氏度、70-80摄氏度、80-90摄氏度、90-100摄氏度、100-150摄氏度、100-110摄氏度、110-120摄氏度、120-130摄氏度、130-140摄氏度、140-150摄氏度等),所述第一加热风机用于使第一反应腔体13的温度处于第一温度范围(例如,150-200摄氏度、150-160摄氏度、160-170摄氏度、170-180摄氏度、180-190摄氏度、190-200摄氏度、200-250摄氏度、200-210摄氏度、210-220摄氏度、220-230摄氏度、230-240摄氏度、240-250摄氏度等)。设置第一反应腔体13、第二反应腔体14的目的在于:连续采用两个反应腔体来提高复合率,确保复合程度,同时设置第一反应腔体13、第二反应腔体14不同反应温
度的目的在于:在第一反应腔体13进行初步贴合,进行预热,在第二反应腔体14进行充分贴合。在实际加工过程中,只采用第一反应腔体13即可完成复合操作,复合程度高达98%以上,设置第二反应腔体14的目的在于:进一步提高复合程度(例如,超过99%),且可以提高复合的厚度(例如,复合厚度可以达到几十微米至几毫米,如20微米、30微米、50微米、100微米、300微米、500微米、1毫米、2毫米等)。通过进一步提高复合程度,可以极大减小复合层剥离的可能性。
42.优选的,所述第二加热风机的加热温度高于所述第一加热风机的加热温度(例如,第二加热风机的加热温度为50-150摄氏度,第一加热风机的加热温度为150-250摄氏度),所述外侧壳体组件10还设置有尾部吸气风机105,所述尾部吸气风机105的吸气端设置于末端腔体15。设置末端腔体15及尾部吸气风机105的目的在于:一方面提供一定的冷却作用,另一方面提供一定的负压作用,若出现机器故障,未完全复合的产品在负压作用下可以明显看出,进而减小错误率。
43.优选的,所述间隔扶正板90上设置有用于穿过pla膜60的缺口,所述缺口的宽度为2-5cm,为pla膜60在外侧壳体组件10的内部腔体中移动提供导向。
44.优选的,所述侧部无杆气缸31的侧部设置有移动板311,若干个移动滴液组件34固定于移动板311上;所述u型座32设置有两个安装端321,每一安装端321上设置有若干个夹线组件322用于夹持线体33。在本实施例中,每一所述夹线组件322包括u型夹3221、与u型夹3221配合安装的锁固螺丝3222,转动锁固螺丝3222使线体33固定于u型夹3221。在一些实施例中,夹线组件322也可以使用其他结构,例如卡扣结构,从而便于快速安装、拆卸及后续设备维护。所述移动滴液组件34设置有v型端面,所述移动滴液组件34设置两个滴液喷头341,两个滴液喷头341分别设置于v型端面的两个端面上,两个滴液喷头341的出液方向呈锐角,线体33位于两个滴液喷头341之间。pbat颗粒物与聚二甲基硅氧烷添加剂混合加热,采用滴液喷头341滴液至线体33。线体33与高压电极端20之间形成高压区间50,从而将液滴复合至pla膜。
45.优选的,第一移动滴液辅助装置30和第二移动滴液辅助装置40与高压电极端20之间的电压不同。例如,第二移动滴液辅助装置40与高压电极端20之间的电压高于第一移动滴液辅助装置30与高压电极端20之间的电压,从而进一步提高复合程度,极大减小复合层剥离的可能性。
46.请具体参阅图8,一种可生物降解pbat/pla复合膜的制备方法,包括以下步骤:
47.混合步骤:将pbat颗粒物与聚二甲基硅氧烷添加剂混合,加热形成待滴取混合物熔体;
48.拉丝步骤:待滴取混合物熔体通过计量泵输送至移动滴液组件,设置两个高压电极端,两个高压电极端形成高压区间,移动滴液组件滴取待拉丝液到高压区间内,待拉丝液体经高压作用生成纳米纤维丝;
49.贴合步骤:pla膜沿高压区间移动,纳米纤维丝沿pla膜的移动方向贴合到pla膜的表面,形成pbat/pla复合膜。
50.具体的,在所述贴合步骤中,pla膜先经过第一反应腔体进行一次贴合,再经过第二反应腔体进行二次贴合,第一反应腔体的温度小于第二反应腔体的温度。
51.具体的,pla膜连续经过第一反应腔体、第二反应腔体后,继续让pla膜经过末端腔
体,在末端腔体内设置吸气风机进行冷却并形成负压空间。
52.实施例一:
53.混合步骤:将pbat颗粒物与聚二甲基硅氧烷添加剂混合,加热至温度为50摄氏度以上形成待滴取混合物熔体,pbat颗粒物与聚二甲基硅氧烷添加剂的配比为95:5;
54.拉丝步骤:待滴取混合物熔体通过计量泵输送至移动滴液组件,设置两个高压电极端,两个高压电极端形成高压区间,移动滴液组件滴取待拉丝液到高压区间内,待拉丝液体经高压作用生成纳米纤维丝;
55.贴合步骤:pla膜沿高压区间移动,纳米纤维丝沿pla膜的移动方向贴合到pla膜的表面,pla膜连续经过第一反应腔体、第二反应腔体,控制第一反应腔体的反应温度为:50-60℃,控制第二反应腔体反应温度为150-160℃,形成pbat/pla复合膜。
56.实施例二:
57.混合步骤:将pbat颗粒物与聚二甲基硅氧烷添加剂混合,加热至温度为50摄氏度以上形成待滴取混合物熔体,pbat颗粒物与聚二甲基硅氧烷添加剂的配比为90:10;
58.拉丝步骤:待滴取混合物熔体通过计量泵输送至移动滴液组件,设置两个高压电极端,两个高压电极端形成高压区间,移动滴液组件滴取待拉丝液到高压区间内,待拉丝液体经高压作用生成纳米纤维丝;
59.贴合步骤:pla膜沿高压区间移动,纳米纤维丝沿pla膜的移动方向贴合到pla膜的表面,pla膜连续经过第一反应腔体、第二反应腔体,控制第一反应腔体的反应温度为:60-70℃,控制第二反应腔体反应温度为160-170℃,形成pbat/pla复合膜。
60.实施例三:
61.混合步骤:将pbat颗粒物与聚二甲基硅氧烷添加剂混合,加热至温度为50摄氏度以上形成待滴取混合物熔体,pbat颗粒物与聚二甲基硅氧烷添加剂的配比为85:15;
62.拉丝步骤:待滴取混合物熔体通过计量泵输送至移动滴液组件,设置两个高压电极端,两个高压电极端形成高压区间,移动滴液组件滴取待拉丝液到高压区间内,待拉丝液体经高压作用生成纳米纤维丝;
63.贴合步骤:pla膜沿高压区间移动,纳米纤维丝沿pla膜的移动方向贴合到pla膜的表面,pla膜连续经过第一反应腔体、第二反应腔体,控制第一反应腔体的反应温度为:70-80℃,控制第二反应腔体反应温度为170-180℃,形成pbat/pla复合膜。
64.对根据本技术方法生成的可生物降解pbat/pla复合膜的测试结果,如表1所示。
65.为了考察pbat/pla复合膜的贴合程度,实验组设置和实验结果如表1所示:
[0066][0067]
表1
[0068]
本技术的双层膜经过连续的灯光、水淋、烘干处理,查看两者的损耗差别,可以看出,现有技术中的双层膜在第二回合处理中就出现分离状况,在第三回合分离状况比较明显;而在本技术的双层膜处理的过程中,连续多个回合处理仅仅会造成双层膜的整体破损,而不会造成分离状况。
[0069]
上述实施方式仅为本发明的优选实施方式,不能以此来限定本发明保护的范围,本领域的技术人员在本发明的基础上所做的任何非实质性的变化及替换均属于本发明所要求保护的范围。