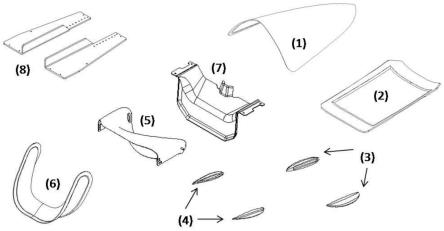
1.本发明属于复合材料成型技术领域,特别涉及一种雪车曲面薄壁复合材料结构件的制造方法。
背景技术:2.相较于木材、钢材、不锈钢、铝合金等,纤维增强复合材料作用于体育器材的优势表现在:1)较强的可设计性。不断完善的复合材料成型技术提升了设计体育运动器材的空间和自由度,更易于获取各种产品相应的成型方法,甚至能够以实际运动选手本身特点为依据实现体育运动器材的定制,从而提升体育器材的人性化和实用性;2)良好的力学性能。体育器材需兼顾使用性能和力学性能,在比强度、比模量和比弹性方面表现突出的纤维增强复合材料还具有良好的阻尼减震性能,成为体育器材主要原料之一;3)重量较轻,体育运动器材的运动(如高尔夫球杆、自行车、滑雪板等)大多借助人力完成,要求器材越轻越好,相比于金属杆应用碳纤维增强材料后的球杆的力学性能得以明显提高(仅达到金属杆重量的30%~50%)。
3.雪车自1924年成为冬奥比赛项目后进入大众视野,但由于地理位置劣势,我国对该项目的关注较晚,国内对复合材料雪车的自主开发更是长期处于空白状态,运动员们训练和比赛用车均源自于进口。然而,国外雪车从外部尺寸到内部尺寸、空间等都是基于欧洲运动员的身材尺寸设计的,对于中国运动员而言,会造成其使用难度大,困难多;此外,购买国外车辆,日常维护方便性差,整车调校难度高,不利于运动员成绩提升。针对上述情况,有必要提供一种复合材料雪车装置及成型方法,使雪车具有低摩擦、减阻、轻质、高强等特点。
技术实现要素:4.为了克服现有技术中的不足,本发明人进行了锐意研究,提供了一种雪车曲面薄壁复合材料结构件的制造方法,设计可更换的、符合中国运动员的人体结构的前段上盖、前段下盖、前保险杠罩、后保险杠罩、腰撑、内造型面、车架防护罩和腿托板,提出每种结构件相对应的成型模具和成型方法,解决了雪车模式化单一性问题,同时可以有效降低运动员更替需要替换整车的成本,从而完成本发明。
5.本发明提供的技术方案如下:
6.一种雪车曲面薄壁复合材料结构件的制造方法,所述雪车曲面薄壁复合材料结构件包括前段上盖、前段下盖、前保险杠罩、后保险杠罩、腰撑、内造型面、车架防护罩和腿托板,所述前段上盖、前段下盖、前保险杠罩、后保险杠罩、腰撑、内造型面和车架防护罩均为纤维增强树脂基复合材料结构件,所述腿托板为纤维增强树脂基复合材料蒙皮与泡沫芯材组合的夹层结构件;前段上盖、前段下盖、前保险杠罩、后保险杠罩、腰撑、内造型面、车架防护罩和腿托板的成型模具分别为前段上盖阴模成型模具、前段下盖阴模成型模具、前保险杠罩阴模成型模具、后保险杠罩阴模成型模具、腰撑阴模成型模具、内造型面阴模成型模具、车架防护罩阳模成型模具、以及腿托板阳模成型模具,各结构件通过在相应的成型模具
上铺覆纤维增强树脂基预浸料,再通过固化得到。
7.根据本发明提供的一种雪车曲面薄壁复合材料结构件的制造方法,具有以下有益效果:
8.(1)本发明提供的一种雪车曲面薄壁复合材料结构件的制造方法,对各薄壁复合材料结构件提供了针对性的制备方法,在保证结构件外形面尺寸精度的同时提高了结构件的可靠性和适用性;
9.(2)本发明提供的一种雪车曲面薄壁复合材料结构件的制造方法,结构件的外形结构可以针对运动员的人体结构、发力特点及操作习惯进行专门设计,有助于提高运动员的赛事成绩;通过螺栓固定于复合材料雪车车体,结构件成型相较于车体成型具有成本低、周期短的特点,适于为运动员进行私人订制服务。通过本发明的实现,可以有效降低:
①
运动员更替需要替换整车的成本;
②
多赛道训练造成的运输成本;
③
作为娱乐项目私人购买的成本。
附图说明
10.图1为雪车复合材料结构件的示意图;
11.图2为前段上盖阴模成型模具;
12.图3为前段下盖阴模成型模具;
13.图4为前保险杠罩阴模成型模具;
14.图5为后保险杠罩阴模成型模具;
15.图6为内造型面阴模成型模具;
16.图7为车架防护罩阳模成型模具;
17.图8为腿托板阳模成型模具。
18.附图标号说明
19.1-前段上盖;2-前段下盖;3-前保险杠罩;4-后保险杠罩;5-腰撑;6-内造型面;7-车架防护罩;8-腿托板。
具体实施方式
20.下面通过对本发明进行详细说明,本发明的特点和优点将随着这些说明而变得更为清楚、明确。
21.在这里专用的词“示例性”意为“用作例子、实施例或说明性”。这里作为“示例性”所说明的任何实施例不必解释为优于或好于其它实施例。尽管在附图中示出了实施例的各种方面,但是除非特别指出,不必按比例绘制附图。
22.本发明提供了一种雪车曲面薄壁复合材料结构件的制造方法,所述雪车曲面薄壁复合材料结构件包括前段上盖1、前段下盖2、前保险杠罩3、后保险杠罩4、腰撑5、内造型面6、车架防护罩7和腿托板8,所述前段上盖1、前段下盖2、前保险杠罩3、后保险杠罩4、腰撑5、内造型面6和车架防护罩7均为纤维增强树脂基复合材料结构件,所述腿托板8为纤维增强树脂基复合材料蒙皮与泡沫芯材组合的夹层结构件;前段上盖1、前段下盖2、前保险杠罩3、后保险杠罩4、腰撑5、内造型面6、车架防护罩7和腿托板8的成型模具分别为前段上盖阴模成型模具、前段下盖阴模成型模具、前保险杠罩阴模成型模具、后保险杠罩阴模成型模具、
腰撑阴模成型模具、内造型面阴模成型模具、车架防护罩阳模成型模具、以及腿托板阳模成型模具,各结构件通过在相应的成型模具上铺覆纤维增强树脂基预浸料,再通过固化得到。具体地,阴模成型模具的内形面和阳模成型模具的外形面用于预浸料的铺层,用阴模成型模具的内形面保证前段上盖1、前段下盖2、前保险杠罩3、后保险杠罩4、腰撑5和内造型面6的外形面尺寸精度,用阳模成型模具的外形面保证车架防护罩7和腿托板8的内形面尺寸精度。
23.在一种优选的实施方式中,所述前段上盖1、前段下盖2包含变厚度截面结构,其主体厚度为2.5~3.5mm,加厚区为8~12mm;
24.所述前保险杠罩3、后保险杠罩4、腰撑5、内造型面6、车架防护罩7为等厚度结构,其厚度为2.5~4.5mm;
25.所述腿托板8为夹层结构,其单边蒙皮厚度为2~3mm,泡沫芯材厚度为4~6mm。
26.在一种优选的实施方式中,所述前段上盖阴模成型模具的成型区域为空间曲面结构,外形投影为三角形;
27.所述前段下盖阴模成型模具的成型区域为空间曲面结构,外形投影为等腰梯形;
28.所述前保险杠罩阴模成型模具、后保险杠罩阴模成型模具的成型区域为小舟结构;
29.所述腰撑阴模成型模具、内造型面阴模成型模具的成型区域为空间异形曲面结构;
30.所述车架防护罩阳模成型模具的成型区域为空间异形曲面结构,结构复杂,存在空间狭小的内陷峡谷结构,最窄处尺寸仅有12mm;
31.所述腿托板阳模成型模具的成型区域为倒角r=45
°
的立方体结构。
32.在一种优选的实施方式中,所述预浸料中的纤维选自碳纤维或碳/玻混杂纤维;所述基体树脂选自环氧树脂、双马来酰亚胺树脂、聚酰亚胺树脂或氰酸酯树脂中的一种;所述纤维与基体树脂的质量比为1~1.5:1。优选地,所述预浸料中碳纤维的拉伸强度>5gpa、拉伸模量》250gpa,玻璃纤维为s级;所述基体树脂为环氧树脂,可耐高低温交变-196~180℃;所述复合材料冲击后压缩强度(cai)》250mpa。
33.所述腿托板(8)的泡沫芯材选自硬质聚氨酯泡沫、硬质聚氯乙烯泡沫、聚苯乙烯泡沫、聚甲基丙烯酰亚胺泡沫或酚醛树脂泡沫中的一种,优选为聚甲基丙烯酰亚胺泡沫,泡沫密度0.75~1.1g/cm3,压缩强度≥1.05mpa。
34.在一种优选的实施方式中,所述前段上盖1、前段下盖2的成型方式,包括如下步骤:
35.s1.组装前段上盖阴模成型模具或前段下盖阴模成型模具;
36.s2.在前段上盖阴模成型模具或前段下盖阴模成型模具上铺覆一层预浸料,预浸料中的纤维采用碳纤和玻纤质量比为2~3.5:1的碳/玻混杂纤维,预浸料中的树脂采用环氧树脂;
37.s3.预浸料铺层采用随形的方式,在突变区域将局部纤维切断,并在缝隙补料;具体地,所述预浸料铺层采用随形的方式的步骤中,铺层方式具体为:1)采用随形的方式铺层,通过刮板排除气泡使预浸料与模具紧贴无缝隙;2)预浸料铺覆过程中外界不施加拉力,避免预浸料固化过程中出现应力集中导致复合材料发生形变。所述在突变区域将局部纤维
切断,并在缝隙补料的步骤,通过如下方式实施:切断由突变区域造成的预浸料褶皱部分的纤维,裁去交叠部分,使预浸料与模具紧贴无褶皱。
38.s4.重复步骤s2和步骤s3,直至铺层的厚度为2.5mm~3.5mm;
39.s5.对步骤s4铺覆的预浸料进行真空辅助压实处理,每铺覆1~1.5mm进行一次真空辅助压实处理;真空辅助压实的压力为0.05~0.1mpa,真空辅助压实时间为1~4h;
40.s6.加厚区铺层采用逐层递减的铺层方式,直至铺层总厚度为8~12mm;具体地,所述加厚区铺层采用逐层递减的铺层方式的步骤,通过如下方式实施:根据预浸料厚度d1、加厚区厚度d2及加厚区递减宽度a,加厚区铺层按照宽度a/(d2/d
1-1)逐层递减;
41.s7.对步骤s6铺覆的预浸料进行真空辅助压实处理,每铺覆2~3mm进行一次真空辅助压实处理;真空辅助压实的压力为0.05~0.1mpa,真空辅助压实时间为1~2h;
42.s8.在前段上盖阴模成型模具或前段下盖阴模成型模具上用密封胶带对产品进行密封处理;
43.s9.在前段上盖阴模成型模具或前段下盖阴模成型模具上进行固化真空袋包覆;
44.s10.将包覆后的产品和模具送入热压罐(或者烘箱),进行固化;固化温度为120~140℃,升温速率20~30℃/h,固化压力为0.5~1.5mpa,固化时间为3~4h;
45.s11.依次拆除真空袋、密封胶带,再将阴模成型模具卸掉,得到前段上盖或前段下盖复合材料构件。
46.在一种优选的实施方式中,所述前保险杠罩3、后保险杠罩4、腰撑5、内造型面6的成型方法,包括如下步骤:
47.s1.组装相应的阴模成型模具;
48.s2.在阴模成型模具上铺覆一层预浸料,预浸料中的纤维采用碳纤维,预浸料中的树脂采用环氧树脂、双马来酰亚胺树脂、聚酰亚胺树脂或氰酸酯树脂中的一种;
49.s3.预浸料铺层采用随形的方式,在确定区域将局部纤维切断,并在缝隙补料;具体地,所述预浸料铺层采用随形的方式的步骤中,针对前保险杠罩3和后保险杠罩4,铺层方式具体为:采用随形的方式铺层,在成型模具的侧壁区域切断纤维,每层预浸料的断口位置错开;针对腰撑5,铺层方式具体为:采用随形的方式铺层,在成型模具的圆角内陷区域切断纤维,每层预浸料的断口位置错开;针对内造型面6,铺层方式具体为:采用随形的方式铺层,在成型模具的平板区切断纤维,每层预浸料的断口位置错开。
50.s4.重复步骤s2和步骤s3,直至铺层的厚度为2.5mm~4.5mm;
51.s5.对步骤s4铺覆的预浸料进行真空辅助压实处理,每铺覆1~1.5mm进行一次真空辅助压实处理;真空辅助压实的压力为0.05~0.1mpa,真空辅助压实时间为1~4h;
52.s6.在阴模成型模具上用密封胶带对产品进行密封处理;
53.s7.在阴模成型模具上进行固化真空袋包覆;
54.s8.将包覆后的产品和模具送入热压罐(或者烘箱),进行固化;固化温度为100~350℃,升温速率10~50℃/h,固化压力为0.5~1.5mpa,固化时间为2~10h;
55.s9.依次拆除真空袋、密封胶带,再将阴模成型模具卸掉,得到前保险杠罩3、后保险杠罩4、腰撑5、内造型面6复合材料构件。
56.在一种优选的实施方式中,车架防护罩7的成型方法,包括如下步骤:
57.s1.组装车架防护罩阳模成型模具;
58.s2.在车架防护罩阳模成型模具上的内陷峡谷结构处灌入硅胶,室温固化后,得到硅胶软模,用于辅助压实该区域预浸料;
59.s3.在车架防护罩阳模成型模具上铺覆一层预浸料,预浸料中的纤维采用碳纤维,预浸料中的树脂采用环氧树脂、双马来酰亚胺树脂、聚酰亚胺树脂或氰酸酯树脂中的一种;
60.s4.预浸料铺层采用随形的方式,具体地,车架防护罩的铺层方式具体为:采用随形的方式铺层,在车架防护罩阳模成型模具的侧壁区域切断纤维,每层预浸料的断口位置错开;在内陷峡谷结构区域用镊子及玻璃棒进行辅助铺层;
61.s5.重复步骤s3和步骤s4,直至铺层的厚度为2.5mm~4.5mm;
62.s6.对步骤s5铺覆的预浸料进行真空辅助压实处理,每铺覆1~1.5mm进行一次真空辅助压实处理,内陷峡谷结构区域放入硅胶软模后再进行真空辅助压实;真空辅助压实的压力为0.05~0.1mpa,真空辅助压实时间为1~4h;
63.s7.在车架防护罩阳模成型模具上用密封胶带对产品进行密封处理;
64.s8.在车架防护罩阳模成型模具上放入硅胶软模后进行固化真空袋包覆;
65.s9.将包覆后的产品和模具送入热压罐(或者烘箱),进行固化;固化温度为100~350℃,升温速率10~50℃/h,固化压力为0.5~1.5mpa,固化时间为2~10h;
66.s10.依次拆除真空袋、密封胶带、硅胶软模,再将阴模成型模具卸掉,得到车架防护罩复合材料构件。在一种优选的实施方式中,腿托板8的成型方法,包括如下步骤:
67.s1.组装腿托板阳模成型模具;
68.s2.在腿托板阳模成型模具上铺覆一层预浸料,预浸料中的纤维采用碳纤维,预浸料中的树脂采用环氧树脂或氰酸酯树脂中的一种;;
69.s3.重复步骤s2,直至铺层的厚度为2mm~3mm;;
70.s4.对步骤s3铺覆的预浸料进行真空辅助压实处理,每铺覆1~1.5mm进行一次真空辅助压实处理;真空辅助压实的压力为0.05~0.1mpa,真空辅助压实时间为1~4h;
71.s5.裁切泡沫芯材至厚度为4mm~6mm,并用基体树脂溶液对泡沫表层涂刷进行封孔处理;
72.s6.在步骤s4压实的预浸料上放置步骤s5处理好的泡沫芯材;
73.s7.在泡沫芯材外围用宽度为3mm~6mm的预浸料进行铺层,直至与泡沫芯材厚度一致,用于对泡沫尺寸定型,避免固化过程中泡沫芯材受压变形;
74.s8.在泡沫芯材上表面,重复步骤s2进行上层蒙皮的铺覆,直至铺层厚度为2mm~3mm;
75.s9.在腿托板阳模成型模具上用密封胶带对产品进行密封处理;
76.s10.在腿托板阳模成型模具上进行固化真空袋包覆;
77.s11.将包覆后的产品和模具送入热压罐(或者烘箱),进行固化;固化温度为200~250℃,升温速率30~60℃/h,固化压力为0.3~0.6mpa,固化时间为2~6h;
78.s12.依次拆除真空袋、密封胶带,再将阳模成型模具卸掉,得到腿托板复合材料构件。
79.实施例
80.如图2~6所示,前段上盖阴模成型模具、前段下盖阴模成型模具、前保险杠罩阴模成型模具、后保险杠罩阴模成型模具、腰撑阴模成型模具和内造型面阴模成型模具,成型铺
覆是在阴模上进行,阴模保证产品外部形面,采用真空袋包覆和固化。
81.如图7~8所示,车架防护罩阳模成型模具和腿托板阳模成型模具,成型铺覆是在阳模上进行,阳模保证产品内部形面,采用真空袋包覆和固化。
82.实施例1
83.一种采用阴模成型具有变厚度截面结构的雪车曲面薄壁复合材料结构件的成型方法,以前段下盖为例,包括如下步骤:
84.s1.组装前段下盖阴模成型模具,所述前段下盖阴模成型模具的成型区域为空间曲面结构,外形投影为等腰梯形;
85.s2.在前段下盖阴模成型模具上铺覆一层预浸料,预浸料选择碳纤和玻纤质量比为2.5:1的碳/玻混合纤维增强环氧树脂,碳纤维的拉伸强度>5gpa、拉伸模量》250gpa,玻璃纤维为s级,环氧树脂可耐高低温交变-196~180℃;
86.s3.预浸料铺层采用随形的方式,在突变区域将局部纤维切断,并在缝隙补料;铺覆过程中通过刮板排除气泡使预浸料与模具紧贴无缝隙;预浸料铺覆过程中外界不施加拉力,避免预浸料固化过程中出现应力集中导致复合材料发生形变;切断由突变区域造成的预浸料褶皱部分的纤维,裁去交叠部分,使预浸料与模具紧贴无褶皱;
87.s4.重复步骤s2和步骤s3,直至铺层的厚度为3mm;
88.s5.对步骤s4铺覆的预浸料进行真空辅助压实处理,每铺覆1~1.5mm进行一次真空辅助压实处理,真空辅助压实的压力为0.05mpa,真空辅助压实时间为2h;
89.s6.加厚区铺层采用逐层递减的铺层方式,直至铺层总厚度为12mm;根据预浸料厚度d1(0.25mm)、加厚区厚度d2(12mm)、结构件主体厚度d3(3mm)及加厚区递减宽度a(100mm),加厚区铺层按照宽度a/[(d
2-d3)/d
1-1]=(2.86mm)逐层递减;
[0090]
s7.对步骤s6铺覆的预浸料进行真空辅助压实处理,每铺覆2~3mm进行一次真空辅助压实处理,真空辅助压实的压力为0.05mpa,真空辅助压实时间为2h;
[0091]
s8.在前段下盖阴模成型模具上用密封胶带对产品进行密封处理;
[0092]
s9.在前段下盖阴模成型模具上进行固化真空袋包覆;
[0093]
s10.将包覆后的产品和模具送入热压罐,进行固化,最终固化温度为140℃,升温速率20℃/h,固化压力为0.6mpa,固化时间为3h;
[0094]
s11.依次拆除真空袋、密封胶带,再将阴模成型模具卸掉,得到前段下盖复合材料构件。所得前段下盖复合材料厚度方向尺寸误差《0.3mm,加厚区位置尺寸误差《0.3mm,冲击后压缩强度(cai)》250mpa。
[0095]
实施例2
[0096]
一种采用阴模成型等厚度截面结构的雪车曲面薄壁复合材料结构件的成型方法,以内造型面为例,包括如下步骤:
[0097]
s1.组装内造型面阴模成型模具,所述内造型面阴模成型模具的成型区域为空间异形曲面结构;
[0098]
s2.在内造型面阴模成型模具上铺覆一层预浸料,预浸料选择碳纤维增强聚酰亚胺树脂,碳纤维的拉伸强度>5gpa、拉伸模量》250gpa,;
[0099]
s3.预浸料铺层采用随形的方式,在成型模具的平板区切断纤维,每层预浸料的断口位置错开,并在缝隙补料;
[0100]
s4.重复步骤s2和步骤s3,直至铺层的厚度为4mm;
[0101]
s5.对步骤s4铺覆的预浸料进行真空辅助压实处理,每铺覆1~1.5mm进行一次真空辅助压实处理,真空辅助压实的压力为0.1mpa,真空辅助压实时间为2h;
[0102]
s6.在内造型面阴模成型模具上用密封胶带对产品进行密封处理;
[0103]
s7.在内造型面阴模成型模具上进行固化真空袋包覆;
[0104]
s8.将包覆后的产品和模具送入热压罐,进行固化,最终固化温度为350℃,升温速率40℃/h,固化压力为1.4mpa,固化时间为2h;
[0105]
s9.依次拆除真空袋、密封胶带,再将阴模成型模具卸掉,得到内造型面复合材料构件。所得内造型面复合材料厚度方向尺寸误差《0.3mm,冲击后压缩强度(cai)》250mpa。
[0106]
实施例3
[0107]
一种采用阳模成型等厚度截面结构的雪车曲面薄壁复合材料结构件的成型方法,以车架防护罩为例,包括如下步骤:
[0108]
s1.组装车架防护罩阳模成型模具,所述车架防护罩阳模成型模具的成型区域为空间异形曲面结构,存在空间狭小的内陷峡谷结构,最窄处尺寸仅有12mm;
[0109]
s2.在车架防护罩阳模成型模具上的内陷峡谷结构处灌入蓝色硅胶,成型硅胶软模;
[0110]
s3.在车架防护罩阳模成型模具上铺覆一层预浸料,预浸料选择碳纤维增强氰酸酯树脂,碳纤维的拉伸强度>5gpa、拉伸模量》250gpa;
[0111]
s4.预浸料铺层采用随形的方式,在车架防护罩阳模成型模具的侧壁区域切断纤维,每层预浸料的断口位置错开,并在缝隙补料;在内陷峡谷结构区域用镊子及玻璃棒进行辅助铺层;
[0112]
s5.重复步骤s3和步骤s4,直至铺层的厚度为3mm;
[0113]
s6.对步骤s5铺覆的预浸料进行真空辅助压实处理,每铺覆1~1.5mm进行一次真空辅助压实处理,内陷峡谷结构区域放入硅胶软模后再进行真空辅助压实;真空辅助压实的压力为0.1mpa,真空辅助压实时间为2h;
[0114]
s7.在车架防护罩阳模成型模具上用密封胶带对产品进行密封处理;
[0115]
s8.在车架防护罩阳模成型模具上放入硅胶软模后进行固化真空袋包覆;
[0116]
s9.将包覆后的产品和模具送入热压罐,进行固化,最终固化温度为200℃,升温速率50℃/h,固化压力为0.6mpa,固化时间为4h;
[0117]
s10.依次拆除真空袋、密封胶带,再将阳模成型模具卸掉,得到车架防护罩复合材料构件。所得车架防护罩复合材料厚度方向尺寸误差《0.3mm,内陷峡谷结构成型尺寸精度
±
0.2mm,冲击后压缩强度(cai)》250mpa。
[0118]
实施例4
[0119]
一种采用阳模成型具有夹层结构的雪车曲面薄壁复合材料结构件的成型方法,以腿托板为例,包括如下步骤:
[0120]
s1.组装腿托板阳模成型模具,所述腿托板阳模成型模具的成型区域为倒角r=45
°
的立方体结构;
[0121]
s2.在腿托板阳模成型模具上铺覆一层预浸料,预浸料选择碳纤维增强双马来酰亚胺树脂,碳纤维的拉伸强度>5gpa、拉伸模量》250gpa;
[0122]
s3.重复步骤s2,直至铺层的厚度为2mm;
[0123]
s4.对步骤s3铺覆的预浸料进行真空辅助压实处理,每铺覆1~1.5mm进行一次真空辅助压实处理,真空辅助压实的压力为0.05mpa,真空辅助压实时间为2h;
[0124]
s5.裁切聚甲基丙烯酰亚胺泡沫芯材至厚度为5mm,泡沫密度0.75g/cm3,压缩强度≥1.05mpa,用基体树脂溶液对泡沫表层进行封孔处理;
[0125]
s6.在步骤s4压实的预浸料上放置步骤s5处理好的泡沫芯材;
[0126]
s7.在泡沫芯材外围用宽度为4mm的预浸料进行铺层,直至与泡沫芯材厚度一致;
[0127]
s8.在泡沫芯材上表面,重复步骤s2进行上层蒙皮的铺覆,直至铺层厚度为2mm;
[0128]
s9.在腿托板阳模成型模具上用密封胶带对产品进行密封处理;
[0129]
s10.在腿托板阳模成型模具上进行固化真空袋包覆;
[0130]
s11.将包覆后的产品和模具送入热压罐,进行固化,最终固化温度为250℃,升温速率50℃/h,固化压力为0.3mpa,固化时间为5h;
[0131]
s12.依次拆除真空袋、密封胶带,再将阳模成型模具卸掉,得到腿托板复合材料构件。所得腿托板复合材料型尺寸精度
±
0.2mm,外观良好无塌陷,冲击后压缩强度(cai)》250mpa。
[0132]
以上结合具体实施方式和范例性实例对本发明进行了详细说明,不过这些说明并不能理解为对本发明的限制。本领域技术人员理解,在不偏离本发明精神和范围的情况下,可以对本发明技术方案及其实施方式进行多种等价替换、修饰或改进,这些均落入本发明的范围内。本发明的保护范围以所附权利要求为准。
[0133]
本发明说明书中未作详细描述的内容属本领域技术人员的公知技术。