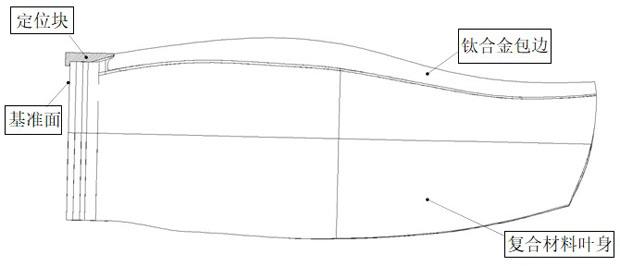
1.本发明涉及一种复合材料叶片金属包边的胶接方法。
背景技术:2.复合材料具有质量轻、比模量高、可设计性强、抗颤振性能好等优点,被应用在飞机叶片上。但复合材料叶片的抗外物冲击性能较差,因此需在复合材料叶片的前缘胶接钛合金包边,以提高叶片的抗外物冲击性能。传统的复合材料叶片钛合金包边的胶接主要依靠胶膜升温时的可流动性对胶接的间隙进行填充。然而,由于复合材料叶片为大曲率零件,复合材料叶身以及钛合金包边在制造过程中均存在型面误差,胶接面之间的间隙不均,胶膜在固化过程中无法将间隙全部填充。特别是曲率较大的位置,胶膜在固化时无法完全压实,导致胶接成型后的叶片存在弱粘接或脱粘的问题。研究发现,复合材料叶片胶接钛合金包边过程中,最容易出现弱粘接或脱粘的问题的是钛合金包边的鼻锥区,由于该区域的截面尺寸为渐变,厚度不均,胶膜难以精准填充,且固化时存在加压不足等问题,导致鼻腔型面胶接不合格。另外,传统的复合材料叶片与钛合金包边胶接方法,复合材料叶身与钛合金包边采用型面适配的定位方法,导致钛合金包边在复合材料叶片上的位置胶接前后存在偏差,影响了复合材料叶片的成型质量。因此,有必要对目前的胶接方法进行改进,以解决上述问题。
技术实现要素:3.针对上述存在的问题及为了达到上述的目的,本技术提供一种复合材料叶片金属包边的胶接方法,将钛合金包边的鼻锥区分段填充,同时采用增压块,达到鼻锥区胶膜难精准填充及满足固化压力的目的,解决了大曲率复合材料叶片钛合金包边弱粘接和脱粘的问题。具体技术方案如下:一种复合材料叶片金属包边的胶接方法,包括如下步骤:1)表面处理:将待胶接的钛合金包边的胶接面进行酸洗,待胶接的复合材料叶身前缘进行粗糙处理并清洗,并分别进行保护,避免污染;2)鼻锥区分段补偿:建立待胶接的钛合金包边的数模,将其鼻锥区划分成若干段,并通过数模计算出每段的截面面积,再根据每段的截面面积计算出该段需补偿胶膜的宽度;3)包边填充胶膜:根据要求在步骤1)处理后的钛合金包边的胶接面填充胶膜;其鼻锥区的胶膜根据步骤2)中计算的宽度剪裁填充;填充完毕后,在鼻锥区的胶膜上方放置均压板,然后将整个包边零件封装,使用烘箱进行热压;4)叶身铺贴胶膜:在步骤1)处理后的复合材料叶身的前缘铺贴一层胶膜,铺贴完成后,抽真空预压;5)合模热压实:将步骤3)中填充胶膜热压后的钛合金包边按照要求合模到步骤4)中铺贴了胶膜的复合材料叶身前缘;并将整个复合材料叶片封装,然后放入烘箱进行热压
实;6)加压固化:在步骤5)中热压实后的复合材料叶片的钛合金包边鼻锥区上放置增压块,然后再次封装,并送入热压罐进行加压固化。
4.作为优选的技术方案的,步骤1)中,所述复合材料叶身前缘进行粗糙处理为通过可剥布或打磨的方式实现;所述打磨为用120~220目的氧化铝砂纸打磨,所述清洗为用清洁的白色揩布或医用纱布沾工业丙酮洗,以白色揩布或医用纱布上无纤维颜色为准。
5.前述的复合材料叶片金属包边的胶接方法,步骤2)中,所述补偿胶膜的宽度的计算公式为:ln=n*san/h;其中,ln为补偿胶膜的宽度;n=1,2,3
…
;an为鼻锥区的分段,其长度根据实际情况设定;san为每段截面的面积;n为系数,其取值范围在0.8~1.5之间,用于补偿型面误差;h为胶膜的厚度。
6.作为优选的技术方案的,步骤3)中,所述包边填充胶膜,鼻锥区的胶膜为将剪裁后的胶膜卷成卷后进行填充;所述均压板为芳纶材质制成;所述烘箱进行热压的条件为:全程抽真空-90kpa~-98kpa,热压的温度为胶膜固化温度的1/3,热压的时间为60min~80min。
7.作为优选的技术方案的,步骤4)中,叶身铺贴胶膜后,抽真空为-60kpa~-198kpa,预压时间为5min~15min。
8.作为优选的技术方案的,步骤5)中,所述钛合金包边合模到复合材料叶身前缘为:以榫根上的某个平面作为钛合金包边定位的基准面,通过定位块合模;所述定位块基于所述基准面设计制作,其定位面1与复合材料叶身上的基准面贴合,其定位面2与钛合金包边端部的面贴合。
9.作为进一步优选的技术方案的,所述定位块由金属或碳纤复合材料等材料制成。
10.作为优选的技术方案的,步骤5)中,所述热压实的条件为:全程抽真空-90kpa~-98kpa,热压实温度为胶膜固化温度的1/3,热压时间为60min~80min。
11.作为优选的技术方案的,步骤6)中,所述增压块为上下两面面积不同的压块,且其面积小的一侧与钛合金包边完全贴合。
12.作为进一步优选的技术方案的,所述增压块为金属材料材料制成,其为类楔形结构,其面积大的一面为平面结构,面积小的一面为根据鼻锥区的外型面设计,使其能与鼻锥区完全贴合。
13.本发明的有益效果:与传统方法相比,本发明通过计算得到鼻锥位置胶膜的实际的厚度,并考虑型面的误差,在实际厚度的基础上乘以系数,实现鼻锥位置胶膜的精准填充;同时在鼻腔位置使用均压层对填充的胶膜的进行热压,在保证鼻腔型面的同时排出胶膜中的气体。
14.本发明基于在力不变的情况下减小截面面积可以增加压强的原理,通过辅助块实现增加钛合金包边鼻锥处的表面压强,解决了固化时存加压不足的问题,提高了零件的胶接质量。
15.本发明还通过定位块辅助定位,将钛合金包边定位至复合材料叶片上的理论位置,保证了零件胶接前后基准的统一,进一步保证了复合材料叶片的成型质量。
16.总体而言,本发明方法通过理论指导实践,以简单的方式有效解决了技术问题,方
案构思巧妙,取得了意想不到的技术效果,具有良好的实用价值。
附图说明
17.图1为本发明复合材料叶片金属包边的胶接方法钛合金包边鼻锥区胶膜热压示意图;图2为本发明复合材料叶身与钛合金包边的胶接示意图;图3为本发明钛合金包边与复合材料叶身合模示意图;图4为本发明的定位块结构示意图;图5为本发明的增压块结构示意图。
具体实施方式
18.下面将结合实施例及附图,对本发明的技术方案进行清楚、完整地描述,显然,所描述的实施例仅是本发明较佳实施例,而不是全部的实施例,亦并非是对本发明作其它形式的限制,任何熟悉本专业的技术人员可能利用所揭示的技术内容加以变更或改型等同变化。但是凡是未脱离本发明技术方案内容,依据本发明的技术实质对以上实施例所作的任何简单修改、等同变化与改型,仍属于本发明技术方案的保护范围。
19.实施例1本实施例是一种复合材料叶片金属包边的胶接方法,将钛合金包边的鼻锥区分段填充,同时采用增压块,达到鼻锥区胶膜难精准填充及满足固化压力的目的,解决了大曲率复合材料叶片钛合金包边弱粘接和脱粘的问题。具体步骤如下:1)表面处理:将待胶接的钛合金包边的胶接面进行酸洗;待胶接的复合材料叶身前缘进行粗糙处理;复合材料叶身表面若可剥布,撕除可剥布即可,若无可剥布,用120~220目的氧化铝砂纸打磨胶接区域,去除叶身表面的树脂,要求打磨均匀且不损伤纤维;打磨之后用清洁的白色揩布或医用纱布沾工业丙酮清洗待胶接表面,以白色揩布或医用纱布上无纤维颜色为准。胶接前,对钛合金包边的胶接面和复合材料叶身前缘进行保护,并分别进行保护,避免污染。
20.2)鼻锥区分段补偿:建立待胶接的钛合金包边的数模,如图1所示;将其鼻锥区划分成若干段,每段的长度根据实际情况设定,记为an(n=1,2,3
…
);通过数模计算出每段的截面面积,记为san;再根据每段的截面面积计算出该段需补偿胶膜的宽度,计算公式为:ln=n*san/h;其中,ln为补偿胶膜的宽度;n为系数,其取值范围在0.8~1.5之间,用于补偿型面误差;h为胶膜的厚度。一般鼻锥区是存在型面误差最大的区域,若其他区域也存在较大误差也可以通过上述方法进行建模分段或分区进行补偿,这种区域统称补偿区,增加补偿宽度的胶膜统称补偿胶膜,如图2所示。
21.3)包边填充胶膜:根据要求在步骤1)处理后的钛合金包边的胶接面填充胶膜;其鼻锥区的胶膜根据步骤2)中计算的宽度剪裁,卷成卷后填充到鼻锥区的鼻腔内,实现鼻锥区胶膜的精准填充。然后将整个包边零件封装,使用烘箱进行热压。填充完毕后,热压前,在鼻锥区的胶膜上方放置橡胶均压板,保证对填充的胶膜进行热压后的鼻腔型面,同时排出胶膜中的气体。烘箱热压的条件为:全程抽真空-90kpa~-98kpa,热压的温度为胶膜固化温度的1/3,热压的时间为60min~80min。
22.4)叶身铺贴胶膜:在步骤1)处理后的复合材料叶身的前缘铺贴一层胶膜,铺贴完成后,抽真空预压;抽真空为-60kpa~-198kpa,预压时间为5min~15min。
23.5)合模热压实:将步骤3)中填充胶膜热压后的钛合金包边按照要求合模到步骤4)中铺贴了胶膜的复合材料叶身前缘;并将整个复合材料叶片封装,然后放入烘箱进行热压实。本实施例中,所述钛合金包边合模到复合材料叶身前缘为:以榫根上的某个平面作为钛合金包边定位的基准面,通过定位块合模,如图3所示。所述定位块基于所述基准面设计制作,设有两个定位面,如图4所示,其定位面1与复合材料叶身上的基准面贴合,其定位面2与钛合金包边端部的面贴合,以保证零件胶接前后基准的统一,提高零件的胶接质量。所述定位块由金属或碳纤复合材料等材料制成。所述热压实的条件为:全程抽真空-90kpa~-98kpa,热压实温度为胶膜固化温度的1/3,热压时间为60min~80min。
24.6)加压固化:在步骤5)中热压实后的复合材料叶片的钛合金包边鼻锥区上放置增压块,然后再次封装,并送入热压罐进行加压固化。本实施例中,所述增压块为上下两面面积不同的压块,且其面积小的一侧与钛合金包边鼻锥区表面的完全贴合。所述增压块为金属材料制成,所述增压块的增压原理是基于在力不变的情况下减小截面面积可以增加压强,即通过在其中一个物体表面增加截面积更大的增压块,可实现增加零件表面压强的目的。本实施例中的增压块上下两面面积不同的压块,如图5所示,上面面积s2>下面面积s1,设p1为钛合金包边与s1接触面的压强,p2为罐压,则p1=p2*s2/s1,从而解决了鼻锥处面积小,固化时存在加压不足的问题,实现增加钛合金包边鼻锥处的表面压强,提高了胶接质量。
25.实施例2本实施例是根据实施例1中的胶接方法对发动机复合材料叶片钛合金包边的胶接。具操作如下:建立待胶接的钛合金包边的数模,将其鼻锥区划分成5段,记为a1,a2,a3,a4, a5,各段的长度均为5cm;通过数模计算出每段的截面面积为sa1=9mm
²
,sa2=12mm
²
,sa3=15mm
²
,sa4=18mm
²
,sa5=22mm
²
;再根据计算公式:ln=n*san/h计算出每段需补偿胶膜的宽度ln,n取1.1,胶膜的厚度h为0.25mm,得到l1=39.6mm,l2=52.8mm,l3=66mm,l4=79.2mm,l5=96.8mm。
26.将钛合金包边的胶接面进行酸洗;复合材料叶身前缘用200目的氧化铝砂纸打磨,然后用医用纱布沾工业丙酮清洗;然后分别对钛合金包边的胶接面和复合材料叶身前缘进行保护,备用。
27.在处理后的钛合金包边的胶接面填充胶膜,其鼻锥区的胶膜根据计算的宽度分段剪裁,然后卷成卷填充到鼻锥区的鼻腔内,并在鼻腔的胶膜上方放置芳纶均压板,然后将整个包边零件封装,使用烘箱进行热压,全程抽真空-95kpa,热压的温度为40℃,热压的时间为65min。同时在清洗后的复合材料叶身的前缘铺贴一层胶膜,并抽真空-80kpa预压15min。
28.以复合材料叶身榫根上的一个平面作为钛合金包边定位的基准面,定位块上上,将定位块安装在该基准面上,定位块的定位面1与该基准面相贴合,钛合金包边的端部与定位块的定位面2相贴合,使钛合金包边合模到复合材料叶身前缘。
29.然后将整个复合材料叶片封装,然后放入烘箱进行热压实:全程抽真空-98kpa,热压实温度为40℃,热压时间为80min。
30.热压实后,在钛合金包边的鼻锥区上放置增压块,如图5所示,该增压块为一类楔
形结构,其上面面积大的一面s1为平面结构,其下面面积小的一面s2为根据鼻锥区的外型面设计,使其能与鼻锥区完全贴合。放置增压块后再次封装,并送入热压罐进行加压固化,固化温度120℃,固化压力0.4mpa,保温时间90min,出罐后拆除封装材料即可。经检测,本实施例中,所得的复合材料叶片钛合金包边定位精准,包边与叶身间胶接紧密,鼻锥区型面胶接良好,不存在弱粘接或脱粘的问题。
31.总体而言,本发明方法理论指导实践,通过计算得到鼻锥位置胶膜的实际的厚度,并考虑型面的误差,在实际厚度的基础上乘以系数,实现鼻锥位置胶膜的精准填充;同时在鼻腔位置使用均压层对填充的胶膜的进行热压,在保证鼻腔型面的同时排出胶膜中的气体。通过基于在力不变的情况下减小截面面积可以增加压强的原理,通过辅助块实现增加钛合金包边鼻锥处的表面压强,解决了固化时存加压不足的问题,提高了零件的胶接质量。通过定位块辅助定位,将钛合金包边定位至复合材料叶片上的理论位置,保证了零件胶接前后基准的统一,进一步保证了复合材料叶片的成型质量,以简单的方式有效解决了技术问题,方案构思巧妙,具有良好的实用价值。
32.对于本领域技术人员而言,显然本发明不限于上述示范性实施例的细节,而且在不背离本发明的精神或基本特征的情况下,能够以其他的具体形式实现本发明。因此,无论从哪一点来看,均应将实施例看作是示范性的,而且是非限制性的,本发明的范围由所附权利要求而不是上述说明限定,因此旨在将落在权利要求的得同要件的含义和范围内的所有变化囊括在本发明内。不应将权利要求中的任何附图标记视为限制所涉及的权利要求。
33.此外,应当理解,虽然本说明书按照实施方式加以描述,但并非每个实施方式仅包含一个独立的技术方案,说明书的这种叙述方式仅仅是为清楚起见,本领域技术人员应当将说明书作为一个整体,实施例中的技术方案也可以经适当组合,形成本领域技术人员可以理解的其他实施方式。