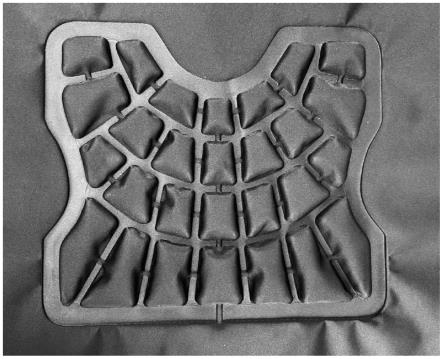
一种防漏气的tpu气囊及其制备方法
技术领域
1.本发明涉及气囊生产技术领域,具体涉及一种防漏气的tpu气囊及其制备方法。
背景技术:2.气囊由于其质量轻、较好的弹性和抗冲击能够力,被广泛应用于家居类坐垫、医疗类床垫、运动护具和包装材料等领域。但现有结构和制造工艺上的不同所得到气囊的质量参差不齐,容易出现漏气、不耐屈折或承重能力差等问题。如中国专利cn104118645b公开的一种包装气囊,包括多个阵列式排布的弹性气囊,多个弹性气囊之间通过软折边相互连接为平面体,在多个弹性气囊中纵向排列的相邻弹性气囊之间设有气囊通道,所述阵列式排布的多个弹性气囊中的纵向弹性气囊和横向弹性气囊皆呈直线排列。该结构的包装气囊通过多个进气口的设置增加了气囊的漏气风险和制备难度,整体承压性能较差。如中国专利申请cn201710609262.1公开了一种用于鞋面的充气放气气囊的制备方法,其外侧tpu薄膜通过热熔胶薄膜与内侧tpu薄膜在预定外形模具上用高频热压粘合形成封闭气室。该制备方法中通过热熔胶薄膜粘合得到的气囊粘接强度低,承重强度高时容易漏气,使用寿命短的问题。基于此,需对气囊的结构和制备工艺进行改进以解决上述问题。
技术实现要素:3.本发明的目的是为了解决上述现有技术的不足而提供一种防漏气的tpu气囊及其制备方法,所述气囊具有弹性高、承重强度高、耐屈折、防漏气和使用寿命长的特点,同时所述气囊的制备方法的灵活性高、生产成本低且操作简便。
4.本发明的目的通过下述技术方案予以实现:一种防漏气的tpu气囊制备方法,包括如下步骤:
5.步骤一、准备制作所述气囊所需的面层材料和底层材料;
6.步骤二、分别对面层材料和底层材料进行冲模处理得到上层气囊和下层气囊;
7.步骤三、将上层气囊与下层气囊贴合后进行预模压得到气囊胚;
8.步骤四、对步骤三所得气囊胚进行充气,对充气后的气囊胚进行二次模压得到所述气囊;
9.步骤五、对步骤四所得的气囊进行裁边和整型处理得到所述气囊成品。
10.进一步的,所述面层材料和底层材料均为tpu膜。tpu膜作为气囊的面层材料和底层材料使气囊具有优异的承重能力、抗冲击性、弹性、耐磨性和耐曲折性能,同时加工难度低,易于成型。
11.更进一步的,所述面层材料的上表面设置有弹性面料层,所述底层材料的下表面设置有布料层。所述弹性面料层和布料层的设置使所述面层材料和底层材料更易于加工成型和脱模,并通过不同弹性面料层和布料层的选择有效提升气囊的外观和质量。在本发明中,具体操作是:将面层材料的上表面涂覆胶黏剂,再将弹性面料层与面层材料的上表面贴合,待干燥后备用;将底层材料的下表面涂覆胶黏剂,再将布料层与底层材料的下表面贴
合,待干燥后备用。根据实际应用需要,所述面层材料与弹性面料层、底层材料与布料层也可通过热压粘接固定。
12.进一步的,所述气囊胚包括上层气囊以及设置于上层气囊下表面的下层气囊,所述上层气囊和下层气囊之间设置有多个气囊单体,多个所述气囊单体排列成多个气囊单体组,每个气囊单体组中的多个气囊单体呈依次排布,位于同一气囊单体组中相邻的气囊单体之间以及相邻的气囊单体组之间预设有气囊通道,所述tpu气囊胚预设有至少一条进气通道,所述气囊单体与进气通道连通,所述进气通道用于与外界相连通,所述上层气囊和下层气囊贴合并设有封边连接部,所述封边连接部围绕于气囊单体、气囊通道和进气通道。具体地,所述上层气囊设置有多个第一气囊腔,所述第一气囊腔是由上层气囊的部分区域向上凸起形成;所述下层气囊设置有多个第二气囊腔,所述第二气囊腔是由下层气囊的部分区域向下凸起形成。所述第一气囊腔与对应的第二气囊腔相连通形成所述气囊单体。
13.在发明中,先对面层材料和底层材料进行冲膜处理分别得到具有多个第一气囊腔的上层气囊和具有多个第二气囊腔的下层气囊,由上层气囊与下层气囊贴合形成气囊胚,所述气囊胚预设有至少一条进气通道和气囊通道得到所述气囊胚。所述气囊胚经进气通道和气囊通道将各气囊单体填充至所需要的饱和度,再将进气通道和气囊密封隔断使各气囊单体相互独立。通过上述结构的设置制得的气囊整体耐冲击性能和弹性好、耐屈折且防漏气,即使单个气囊单体破损也不影响气囊整体的承重缓冲性能,安全性高。
14.进一步的,所述步骤二的具体操作是:将面层材料或底层材料装入撑框中平展,并在高周波机安装好需要的形状模具,将撑框放置于高周波机的热熔平台上,启动高周波机将面层材料或底层材料热压成型,得到所述上层气囊或下层气囊。
15.进一步的,所述步骤二的具体操作是:采用冶具将面层材料或底层材料固定后,置于温度为130-180℃的烘箱内加热软化30-60s,再将软化后的面层材料或底层材料放入吸塑机的模具内,在真空负压条件下形成上层气囊或下层气囊。在实际操作中,所述吸塑机的真空度由面层材料或底层材料的厚度等参数进行适应性调整。
16.进一步的,所述步骤二的具体操作是:采用冶具将面层材料或底层材料固定后,置于温度为130-180℃的烘箱内加热软化30-60s,再将软化后的面层材料或底层材料放入成型作业台上,通过冷压模具施加压力将其压铸成型,压力为5-20kg/
㎡
,时间为30-60s,经脱模后得到所述上层气囊或下层气囊。
17.在发明中,通过上述步骤二的冲膜处理使上层气囊和下层气囊易于成型,操作灵活且生产效率高。
18.进一步的,所述步骤三的具体操作是:将步骤二所得的上层气囊放置于下层气囊的上表面,采用母模和平板模将上层气囊和下层气囊固定,然后将其置于高周波机上,使用0.8-1.2a电流,产生高周波电流10-40s,通过高周波加工将上层气囊和下层气囊除气囊单体、进气通道和气囊通道外的区域熔接在一起形成封边连接部,待冷却后拆除母模和平板模即得到所述气囊胚。
19.进一步的,所述步骤四的具体操作是:将充气装置的充气嘴插入进气通道进行充气后,采用第一封边模具固定与进气通道连通的多个气囊单体,并通过高周波机将进气通道密封隔断,然后采用第二封边模具固定所有气囊单体,并通过高周波机将进气通道和多个气囊通道密封隔断,使所述气囊的所有气囊单体之间均相互独立。在步骤四中,所述高周
波机的电流为0.8-1.2a,通电流时间为20-40s,温度为140-160℃。通过上述步骤四的操作提升了气囊的密封性和耐屈折性能,延长使用寿命。
20.进一步的,所述步骤四的具体操作是:将充气装置的充气嘴插入进气通道进行充气后,采用第二封边模具固定所有气囊单体,并通过高周波机将进气通道和多个气囊通道密封隔断,使所述气囊的所有气囊单体之间均相互独立,即气囊单体之间不连通。通过步骤四的操作将各气囊单体单独密封,即使单个气囊单体破损,也不影响所述tpu气囊整体的承重能力和弹性缓冲性能。在步骤四中,所述高周波机的电流为0.8-1.2a,通电流时间为20-40s,温度为140-160℃。上述步骤四的操作简单,生产效率高且时间短。
21.一种防漏气的tpu气囊,所述气囊由上述气囊的制备方法制成。
22.本发明的有益效果在于:本发明公开了一种防漏气的tpu气囊及制备方法,先对面层材料和底层材料进行冲膜处理得到上层气囊和下层气囊,再将上层气囊与下层气囊贴合预封边形成气囊胚,对气囊胚进行充气后进行二次模压得到所述气囊。所述制备方法操作简便、生产成本低且生产效率高,通过上述方法制得的气囊整体承重能力强、弹性耐冲击、耐屈折且不易漏气,即使单个气囊单体破损也不影响气囊整体的承重缓冲性能,安全性高。
附图说明
23.图1是本发明所述气囊胚的效果图。
24.图2是本发明所述气囊胚的结构示意图。
25.图3是本发明所述气囊胚的剖面结构图。
26.附图标记为:1-上层气囊、2-下层气囊、3-气囊单体、4-气囊通道、5-进气通道、6-封边连接部、31-第一气囊腔、32-第二气囊腔、7-弹性面料层、8-布料层。
具体实施方式
27.为了便于本领域技术人员的理解,下面结合实施例对本发明作进一步的说明,实施方式提及的内容并非对本发明的限定。
28.作为本发明优选的实施方式,如图1-3所示,本发明所述气囊胚包括上层气囊1以及设置于上层气2囊下表面的下层气囊3,所述上层气囊1和下层气囊2之间设置有多个气囊单体3,多个所述气囊单体3排列成多个气囊单体组,每个气囊单体组中的多个气囊单体3呈依次排布,位于同一气囊单体组中相邻的气囊单体3之间以及相邻的气囊单体组之间预设有气囊通道4,所述tpu气囊胚预设有至少一条进气通道5,所述气囊单体3与进气通道5连通,所述进气通道5用于与外界相连通,所述上层气囊1和下层气囊2贴合并设有封边连接部6,所述封边连接部6围绕于气囊单体3、气囊通道4和进气通道5。具体地,所述上层气囊1设置有多个第一气囊腔31,所述第一气囊腔31是由上层气囊1的部分区域向上凸起形成;所述下层气囊2设置有多个第二气囊腔32,所述第二气囊腔32是由下层气囊2的部分区域向下凸起形成。所述第一气囊腔31与对应的第二气囊腔32相连通形成所述气囊单体3。
29.进一步的,所述tpu气囊胚预设有一条进气通道5,所述进气通道5的出口开设于位于气囊胚边缘的一个气囊单体3。
30.进一步的,相邻的气囊单体组之间通过一条或多条气囊通道4连通,气囊通道4的两端分别开设于位于不同的气囊单体组的两个气囊单体3。
31.实施例1
32.一种防漏气的tpu气囊制备方法,包括如下步骤:
33.步骤一、准备制作所述气囊所需的面层材料和底层材料;
34.步骤二、分别对面层材料和底层材料进行冲模处理得到上层气囊1和下层气囊2;
35.步骤三、将上层气囊1与下层气囊3贴合后进行预模压得到气囊胚;
36.步骤四、对步骤三所得气囊胚进行充气,对充气后的气囊胚进行二次模压得到所述气囊;
37.步骤五、对步骤四所得的气囊进行裁边和整型处理得到所述气囊成品。
38.进一步的,所述面层材料和底层材料均为tpu膜,所述面层材料的上表面设置有弹性面料层7,所述底层材料的下表面设置有布料层8。
39.其中,所述步骤二的具体操作是:将面层材料或底层材料装入撑框中平展,并在高周波机安装好需要的形状模具,将撑框放置于高周波机的热熔平台上,启动高周波机将面层材料或底层材料热压成型,得到所述上层气囊1或下层气囊2。
40.其中,所述步骤三的具体操作是:将步骤二所得的上层气囊1放置于下层气囊2的上表面,采用母模和平板模将上层气囊1和下层气囊2固定,然后将其置于高周波机上,使用1.0a电流,产生高周波电流30s,通过高周波加工将上层气囊1和下层气囊2除气囊单体3、进气通道5和气囊通道4外的区域熔接在一起形成封边连接部6,待冷却后拆除母模和平板模即得到所述气囊胚。本实施例中,所述气囊胚预设有一条进气通道5,该进气通道5的出气口开设于其中一个气囊单体3,进气通道5与一个气囊单体3直接连通,并经由该气囊单体3与其他气囊单体3连通。
41.其中,所述步骤四的具体操作是:将充气装置的充气嘴插入进气通道5进行充气后,采用第一封边模具固定与进气通道连通的多个气囊单体3,并通过高周波机将进气通道5密封隔断,然后采用第二封边模具固定所有气囊单体3,并通过高周波机将多个气囊通道4密封隔断,使所述气囊的所有气囊单体3之间均相互独立,即所有气囊单体之间均不相互连通。在步骤四中,所述高周波机的电流为0.8a,通电流时间为30s,温度为150℃。
42.将上述实施例1的制备方法制得的tpu气囊进行纵向撕裂力(单位成品所受的拉力)、平面承受压力、撕裂强度、屈折性能测试和老化测试。其中,所述屈折性能采用qb/t 1471标准进行测定(常温条件下),所述纵向撕裂力测试采用gb/t 10654标准进行测定,所述老化测试采用gb/t 3903.7标准进行测定。上述实施例1所得气囊的测试结果为:纵向撕裂力为95kg,平面承受压力为780kg,撕裂强度为25kg/cm,老化测试时间大于180h,屈折性能大于80000次。
43.实施例2
44.一种防漏气的tpu气囊制备方法,包括如下步骤:
45.步骤一、准备制作所述气囊所需的面层材料和底层材料;
46.步骤二、分别对面层材料和底层材料进行冲模处理得到上层气囊1和下层气囊2;
47.步骤三、将上层气囊1与下层气囊2贴合后进行预模压得到气囊胚;
48.步骤四、对步骤三所得气囊胚进行充气,对充气后的气囊胚进行二次模压得到所述气囊;
49.步骤五、对步骤四所得的气囊进行裁边和整型处理得到所述气囊成品。
50.进一步的,所述面层材料和底层材料均为tpu膜,所述面层材料的上表面设置有弹性面料层7,所述底层材料的下表面设置有布料层8。
51.其中,所述步骤一的具体操作是:
52.其中,所述步骤二的具体操作是:采用冶具将面层材料或底层材料固定后,置于温度为160℃的烘箱内加热软化40s,再将软化后的面层材料或底层材料放入吸塑机的模具内,在真空负压条件下形成上层气囊1或下层气囊2。
53.其中,所述步骤三的具体操作是:将步骤二所得的上层气囊1放置于下层气囊2的上表面,采用母模和平板模将上层气囊1和下层气囊2固定,然后将其置于高周波机上,使用1.0a电流,产生高周波电流30s,通过高周波加工将上层气囊1和下层气囊2除气囊单体3、进气通道5和气囊通道4外的区域熔接在一起形成封边连接部6,待冷却后拆除母模和平板模即得到所述气囊胚。
54.其中,所述步骤四的具体操作是:将充气装置的充气嘴插入进气通道5进行充气后,采用第一封边模具固定与进气通道连通的多个气囊单体,并通过高周波机将进气通道5密封隔断,然后采用第二封边模具固定所有气囊单体3,并通过高周波机将多个气囊通道4密封隔断,使所述气囊的所有气囊单体3之间均相互独立,即所有气囊单体之间均不相互连通。在步骤四中,所述高周波机的电流为1.0a,通电流时间为20s,温度为140℃。
55.实施例3
56.一种防漏气的tpu气囊制备方法,包括如下步骤:
57.步骤一、准备制作所述气囊所需的面层材料和底层材料;
58.步骤二、分别对面层材料和底层材料进行冲模处理得到上层气囊1和下层气囊2;
59.步骤三、将上层气囊1与下层气囊2贴合后进行预模压得到气囊胚;
60.步骤四、对步骤三所得气囊胚进行充气,对充气后的气囊胚进行二次模压得到所述气囊;
61.步骤五、对步骤四所得的气囊进行裁边和整型处理得到所述气囊成品。
62.进一步的,所述面层材料和底层材料均为tpu膜,所述面层材料的上表面设置有弹性面料层7,所述底层材料的下表面设置有布料层8。
63.进一步的,所述步骤二的具体操作是:采用冶具将面层材料或底层材料固定后,置于温度为150℃的烘箱内加热软化40s,再将软化后的面层材料或底层材料放入成型作业台上,通过冷压模具施加压力将其压铸成型,压力为15kg/
㎡
,时间为40s,经脱模后得到所述上层气囊1或下层气囊2。
64.进一步的,所述步骤三的具体操作是:将步骤二所得的上层气囊1放置于下层气囊2的上表面,采用母模和平板模将上层气囊1和下层气囊2固定,然后将其置于高周波机上,使用1.2a电流,产生高周波电流20s,通过高周波加工将上层气囊1和下层气囊2除气囊单体3、进气通道5和气囊通道4外的区域熔接在一起形成封边连接部6,待冷却后拆除母模和平板模即得到所述气囊胚。
65.进一步的,所述步骤四的具体操作是:将充气装置的充气嘴插入进气通道5进行充气后,采用第一封边模具固定与进气通道连通的多个气囊单体3,并通过高周波机将进气通道5密封隔断,然后采用第二封边模具固定所有气囊单体3,并通过高周波机将多个气囊通道4密封隔断,使所述气囊的所有气囊单体3之间均相互独立,即所有气囊单体之间均不相
互连通。在步骤四中,所述高周波机的电流为1.0a,通电流时间为30s,温度为150℃。
66.将上述实施例3的制备方法制得的气囊进行纵向撕裂力(单位成品所受的拉力)、平面承受压力、撕裂强度、屈折性能测试和老化测试。上述实施例3所得气囊的测试结果为:纵向撕裂力为92kg,平面承受压力为770kg,撕裂强度为20kg/cm,老化测试时间大于180h,屈折性能大于80000次。
67.实施例4
68.一种防漏气的tpu气囊制备方法,包括如下步骤:
69.步骤一、准备制作所述气囊所需的面层材料和底层材料;
70.步骤二、分别对面层材料和底层材料进行冲模处理得到上层气囊1和下层气囊2;
71.步骤三、将上层气囊1与下层气囊2贴合后进行预模压得到气囊胚;
72.步骤四、对步骤三所得气囊胚进行充气,对充气后的气囊胚进行二次模压得到所述气囊;
73.步骤五、对步骤四所得的气囊进行裁边和整型处理得到所述气囊成品。
74.进一步的,所述面层材料和底层材料均为tpu膜。
75.其中,所述步骤二的具体操作是:将面层材料或底层材料装入撑框中平展,并在高周波机安装好需要的形状模具,将撑框放置于高周波机的热熔平台上,启动高周波机将面层材料或底层材料热压成型,得到所述上层气囊1或下层气囊2。
76.其中,所述步骤三的具体操作是:将步骤二所得的上层气囊1放置于下层气囊2的上表面,采用母模和平板模将上层气囊1和下层气囊2固定,然后将其置于高周波机上,使用1.0a电流,产生高周波电流30s,通过高周波加工将上层气囊1和下层气囊2除气囊单体3、进气通道5和气囊通道4外的区域熔接在一起形成封边连接部6,待冷却后拆除母模和平板模即得到所述气囊胚。
77.其中,所述步骤四的具体操作是:将充气装置的充气嘴插入进气通道5进行充气后,采用第一封边模具固定与进气通道5连通的多个气囊单体3,并通过高周波机将进气通道5密封隔断,然后采用第二封边模具固定所有气囊单体3,并通过高周波机将多个气囊通道4密封隔断,使所述气囊的所有气囊单体3之间均相互独立,即所有气囊单体之间均不相互连通。在步骤四中,所述高周波机的电流为1.2a,通电流时间为30s,温度为150℃。
78.实施例5
79.一种防漏气的tpu气囊制备方法,包括如下步骤:
80.步骤一、准备制作所述气囊所需的面层材料和底层材料;
81.步骤二、分别对面层材料和底层材料进行冲模处理得到上层气囊1和下层气囊2;
82.步骤三、将上层气囊1与下层气囊2贴合后进行预模压得到气囊胚;
83.步骤四、对步骤三所得气囊胚进行充气,对充气后的气囊胚进行二次模压得到所述气囊;
84.步骤五、对步骤四所得的气囊进行裁边和整型处理得到所述气囊成品。
85.进一步的,所述面层材料和底层材料均为tpu膜,所述面层材料的上表面设置有弹性面料层7,所述底层材料的下表面设置有布料层8。
86.进一步的,所述步骤二的具体操作是:采用冶具将面层材料或底层材料固定后,置于温度为130-180℃的烘箱内加热软化30-60s,再将软化后的面层材料或底层材料放入吸
塑机的模具内,在真空负压条件下形成上层气囊1或下层气囊2。
87.进一步的,所述步骤三的具体操作是:将步骤二所得的上层气囊1放置于下层气囊2的上表面,采用母模和平板模将上层气囊1和下层气囊2固定,然后将其置于高周波机上,使用0.8-1.2a电流,产生高周波电流10-40s,通过高周波加工将上层气囊1和下层气囊2除气囊单体3、进气通道5和气囊通道4外的区域熔接在一起形成封边连接部6,待冷却后拆除母模和平板模即得到所述气囊胚。
88.进一步的,所述步骤四的具体操作是:将充气装置的充气嘴插入进气通道5进行充气后,采用第二封边模具固定所有气囊单体,并通过高周波机将多个气囊通道4密封隔断,使所述气囊的所有气囊单体3之间均相互独立,即所有气囊单体之间均不相互连通。在步骤四中,所述高周波机的电流为1.2a,通电流时间为40s,温度为160℃。
89.在本发明中,通过上述实施例1-5的制备方法制得的tpu气囊成品性能均满足出货标准,其中纵向撕裂力均大于85kg,平面承受压力均处于600-800kg范围内,撕裂强度大于17kg/cm,老化性能测试大于168h,屈折性能大于80000次。由上述可知,本发明提供的tpu气囊制备方法制得的气囊具有优异的承重能力、耐撕裂性能和耐屈折性能,使用寿命长且不易漏气。
90.上述的具体实施例是对本发明技术方案和有益效果的进一步说明,并非对实施方式的限定。对本领域技术人员来说,在不脱离本发明构思的前提下任何显而易见的替换均在本发明的保护范围之内。