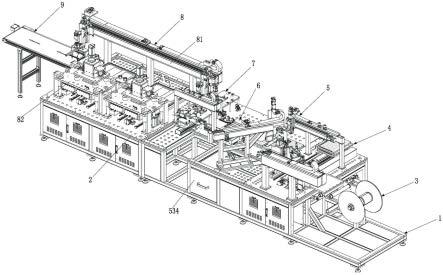
1.本发明涉及贴膜产品的生产加工设备领域,特别涉及一种包含正反面贴膜、离型膜撕膜、预压、加热加压等加工机构的双面贴合设备。
背景技术:2.随着社会的进步和科技的不断高速发展,人们的生活水平和生活质量正在不断提高。人们对手机、电脑、平板电脑等电子产品的质量要求越来越高,并且需求量越来越大。电子产品正日益成为人们日常生活中重要的必不可少的角色。
3.零件的贴膜是电子产品的生产过程必不可少的步骤之一,而市面上采用的方式为人工贴膜或设备贴膜,当现有的设备往往都是针对单一光学膜片与单一设备的组装,且需要通过多台处理不同工艺的设备分开处理,生产连续性差,效率低,不能够满足现在自动化生产的需求,此外由于需要分别由不同的设备进行处理,其中容易导致生产的不统一,影响产品质量。
技术实现要素:4.本发明的目的是:提供一种解决现有设备生产连续性差、生产效率低问题的双面贴合设备。
5.本发明的技术解决方案是:一种两面贴合设备,其特殊之处在于,包括机架、固定在所述机架的进料端的剥料装置、固定在所述机架的出料端的出料传送带装置、固定在机架上且位于所述剥料装置与出料传送带装置之间的底板,所述底板上沿加工次序依次安装有对位矫正贴膜装置、旋转撕膜装置、翻转送料装置、贴膜预压装置以及加热加压装置;
6.光学膜片在剥料装置中从光学膜卷中剥离,在对位矫正贴膜装置经过对位矫正后精准贴合在第一面板上,完成正面贴膜的产品在旋转撕膜装置中撕离光学膜片表面的离型膜,并通过翻转送料装置对第一面板进行翻面,转移至贴膜预压装置与第二面板的表面贴合且完成预压,预压完成后的产品转移至加热加压装置内进行真空压合,最后通过人工或出料传送带装置输出。
7.作为优选:所述剥离装置包括固定在机架上的第一立板、固设在第一立板上的放卷机构、剥料台、包胶辊机构、收卷机构及若干过辊,所述剥离装置还包括固定在底板上的放料平台;
8.所述放卷机构包括制动器以及由制动器控制的放卷辊,所述收卷机构包括收卷驱动电机及套装在所述收卷驱动电机的输出轴的收卷辊,所述剥料台的前端位于所述放料平台上方;
9.光学膜卷由放卷辊输出,依次经过剥料台前端、包胶辊,由收卷辊回收,光学膜片经过剥料台前端后,从光学膜卷处剥离至放料平台。
10.作为优选:所述对位矫正贴膜装置包括固定在底板的第一支架、固设在底板上的第一上料机构、活动安装在第一支架上且用于将光学膜片从所述剥料装置的放料平台转移
至第一上料机构的机械臂机构;
11.所述机械臂机构包括第一支承座、活动安装在第一支承座底面且用于吸附光学膜片的取料模组、活动安装在第一支承座的侧壁且用于矫正所述取料模组上的光学膜片的对位矫正模组、安装在第一支承座的前侧壁的滚压模组;
12.所述第一上料机构包括分别活动安装在底板上的第一上料平台与第二上料平台,所述第一上料平台位于所述第二上料平台的上方;
13.所述机械臂机构通过取料模组从剥料装置的放料平台吸附光学膜片,通过对位矫正模组对光学膜片的位置矫正调节后,取料模组的前端倾斜,光学膜片从前至后地贴合在所述第一上料平台或第二上料平台上的第一面板上,并通过滚压模组沿从前至后的方向对光学膜片表面滚压,排出空气及进一步贴合。
14.作为优选:所述旋转撕膜装置包括固设在底板上的第一转移机构、旋转平台机构以及撕膜机构,所述第一转移机构位于对位矫正贴膜装置与旋转平台机构之间,用于转移第一面板,所述撕膜机构与所述旋转平台机构并列设置;
15.所述旋转平台机构包括固设在底板上的第二支架、固定在第二支架底部的旋转电机组件、底面中心与所述旋转电机组件的输出端连接的旋转平台,所述旋转平台两侧分别为镜像设置的放料工位与撕膜工位;
16.所述撕膜机构包括固设在底板上的旋转台、固设在旋转台上的第三支架、活动安装在第三支架上的撕膜模组;
17.所述第一转移机构将第一面板转移至所述旋转平台的放料工位上,通过旋转电机组件旋转180
°
,转移至撕膜工位,所述撕膜模组沿第三支架位移至撕膜工位上方,夹取第一面板上贴合的光学膜片的离型膜后,沿第三支架沿远离撕膜工位方向移动,将离型膜撕离。
18.作为优选:所述旋转撕膜装置还包括固设在机架上的回收箱,所述第三支架位于所述回收箱的上方还固设有回收夹持机构;
19.所述回收夹持机构包括固定在第三支架上的手指气缸、分别固设在手指气缸两气爪上的夹持杆、固设在夹持杆上的感应器,当撕膜模组位移至回收工位时,所述回收夹持机构位于所述撕膜模组的下方,且感应器位置与撕膜模组的夹持头位置对应。
20.作为优选:所述翻转送料装置包括设置在底板上且位于旋转撕膜装置出料端的翻转机构、位于翻转机构与所述贴膜预压装置之间的送料机构;
21.所述翻转机构包括通过立柱固定在底板下方的载板、对置在所述载板的顶面的两侧板、对称设置在两所述侧板外侧的两伸缩气缸、固设在所述伸缩气缸的活塞杆端部的轴承座、连接两轴承座的连轴、通过固定环连接在连轴上且同步转动的翻转板、固定在侧板上且输出轴与连轴连接的翻转电机;
22.旋转平台上的放料工位与撕膜工位上对称穿设有与所述翻转板形状契合的翻转孔;
23.所述送料机构包括活动安装在底板上的送料平台、所述送料平台上穿设有若干相互垂直分布的滑槽,所述送料平台上还设有若干活动安装在滑槽上的限位件。
24.作为优选:所述贴膜预压机构包括固设在底板上的第二转移机构、第三上料平台、预压平台、第二上料机构、预压观察机构,所述第二转移机构位于所述翻转送料装置与预压平台之间,所述第二上料机构并列设置在第三上料平台与预压平台的侧面,所述预压观察
机构设置预压平台的侧面;
25.所述第三上料平台与预压平台上分别穿设有形状契合取料孔与放料孔,所述第三上料平台上滑动安装有若干件限位件;
26.所述第二上料机构包括活动安装在底板上的上料模组,所述上料模组包括上料气缸以及固设在所述上料气缸的活塞杆端部的取料板,所述取料板的板形与取料孔、放料孔的孔形对应;
27.所述预压观察机构包括活动安装在底板上的观察镜模组;
28.第二面板放置在所述第三上料平台上,通过限位件调节至设定位置,第二上料机构将第二面板转移至预压平台,所述第二转移机构将翻转后的第一面板吸附后输送至预压平台上方,准确预压在第二面板上,光学膜片与第二面板贴合;预压后,观察镜模组移动至预压平台上,通过观察镜模组对产品进行预压观察。
29.作为优选:所述加热加压装置包括设置在底板上的第三转移机构、设置在底板上且与第三转移机构并列设置的至少一组加热加压机构;
30.所述加热加压机构包括活动安装在底板上的下腔体模组、通升降气缸活动安装在底板且位于加热加压工位的上腔体模组;
31.所述下腔体模组的顶面设有加热底板;
32.所述上腔体模组包括与所述升降气缸的活塞杆连接的基板、固设在基板底面的加热加压腔体、固设在基板上的高度调节组件、由高度调节组件驱动相对于基板升降的加压组件、固设在加压组件底部的加热板,所述加热板位于所述加热加压腔体内,位于加热加压腔体的进料端的外侧壁上还固设有距离传感器;
33.所述第三转移机构吸附完成预压后的产品转移至加热底板上,下腔体模组运动至加热加压工位,高度调节组件通过距离传感器检测的与加热底板之间的间距及预设数值调节加热板的高度,升降气缸控制上腔体模组下降,加热加压腔体的底面与下腔体机构顶面紧密配合,形成密闭腔体,加压组件控制加热板下降与加热底板顶面贴合,对产品进行真空压合。
34.与现有技术相比,本发明的有益效果:
35.本发明提供的双面贴合设备包括依次连接的剥料装置、矫正贴膜装置、旋转撕膜装置、翻转送料装置、贴膜预压装置以及加热加压装置,通过本发明提供的双面贴合设备,能够实现利用光学膜卷连续生产贴膜产品的需求,提高生产的连续性以及生产效率;
36.本发明在光学膜片与第一面板贴合之前利用叫矫正贴膜装置对光学膜片横向与纵向进行调节,使其能与第一面板精准对位地从前至后依次贴附,在完成初步贴附后利用滚轮模组从前至后辊压,将光学膜片与第一面板之间的空气排出,进一步加固贴膜;
37.本发明在翻转前通过旋转撕膜装置撕离光学膜片表面粘贴的离型膜,并设有回收检测机构,利用回收检测机构检测是否完成离型膜的撕离,避免出现因离型膜的存在导致影响后续光学膜片与第二面板的贴附,影响生产效率;
38.本发明还设有预压观察机构,在预压完成后,工作人员对产品进行观察检测,及时检测出问题,提高成品的质量;
39.本发明采用的加热加压机构,在上腔体模组与下腔体模组配合之前,利用距离传感器进行测高,通过高度调节模组调节加热板的高度,加压模组对压板背部表面施加压力,
通过上述机构配合,实现精准控高加压,避免出现待处理产品受力不均或者压力过冲过大导致对产品损坏或影响产品质量的问题。
附图说明
40.图1是双面贴合设备的结构示意图;
41.图2是双面贴合设备的另一方向的结构示意图;
42.图3是剥料装置的结构示意图;
43.图4是第一上料机构的结构示意图;
44.图5是机械臂机构的结构爆炸示意图;
45.图6是旋转撕膜装置与翻转送料装置的结构示意图;
46.图7是旋转平台机构的结构爆炸示意图;
47.图8是撕膜组件的结构示意图;
48.图9是翻转机构的结构示意图;
49.图10是贴膜预压机构的结构示意图;
50.图11是加热加压装置的结构示意图;
51.图12是上腔体机构的结构剖面示意图。
具体实施方式
52.本发明下面将结合附图作进一步详述:
53.下面结合附图对本发明的较佳实施例进行详细阐述,以使本发明的优点和特征能更易被本领域人员理解,从而对本发明的保护范围做出更为清楚明确的界定。本发明所提到的方向用语,例如「上」、「下」、「前」、「后」、「左」、「右」、「顶」、「底」等,仅是参考附加图式的方向。因此,使用的方向用语是用以说明及理解本发明,而非用以限制本发明。
54.请参阅图1、图2所示,本发明提供一种两面贴合设备,包括机架1、固定在所述机架1的进料端的剥料装置3、固定在所述机架1的出料端的出料传送带装置9、固定在机架1上且位于所述剥料装置3与出料传送带装置9之间的底板2,所述底板2上沿加工次序依次安装有对位矫正贴膜装置4、旋转撕膜装置5、翻转送料装置6、贴膜预压装置7以及加热加压装置8;
55.请参阅图1~图3所示,所述剥料装置3包括固定在机架1上的第一立板31、通过第二立板32安装在第一立板31后侧的放料机构、固定在第一立板31内侧的剥料台34、包胶辊机构、收卷机构及若干过辊37,还包括固定在底板2上的收料平台38,所述剥料台34的前端位于所述收料平台38的上方;
56.所述放卷机构包括通过固定螺栓安装在第二立板31外侧的制动器、套装在所述制动器的输出轴上的放卷辊331;
57.所述剥料台34的前端成锐角设计,以便于更好的将光学膜片从保护膜上剥落;
58.所述包胶辊机构包括通过固定螺栓安装在第一立板31外侧的第一驱动电机组件、套装在所述第一驱动电机组件的输出轴且位于第一立板31内侧的包胶辊351、与所述包胶辊351并列设置的压紧辊352,所述压紧辊352一端通过轴承座滑动安装在第一立板31内侧的滑槽上,另一端与包胶辊351的端部通过连接件连接,所述压紧辊352的辊面与包胶辊351的辊面紧密配合;
59.所述收料机构包括通过固定螺栓安装在第一立板31外侧的第二驱动电机组件,套装在所述第二驱动电机组件的输出轴上且位于第一立板31内侧的收料辊361;
60.光学膜卷由放卷机构的放卷辊331输出,依次经过第一过辊37的下方、剥料辊34的前端、第二过辊37的上方、包胶辊351与压紧辊352之间的间隙后,由收料机构的收卷辊361回收,光学膜卷上的光学膜片经过剥料台的前端脱离光学膜卷表面,转移至收料平台38的表面;
61.所述收料平台38的表面布设有若干与真空阀连通的吸附孔,用于吸附光学膜片;
62.剥料装置的放卷辊与制动器连接,可以确保在无外力拉扯的情况下,不会输出光学膜卷,能够提高光学膜片的出料准确率,剥料装置通过第二驱动电机组件驱动收料辊收卷以及通过第一驱动电机驱动包胶辊转动,能够确保光学膜卷在放卷收卷的过程中,能够保持合适的张紧力,有利于提高出料准确率,减少人工调节的时间,提高出料效率。
63.请参阅图1、图2、图4、图5所示,所述对位矫正贴膜装置包括固定在底板2上的第一支架41、固设在底板2上的第一上料机构、设置在第一支架41上的第一横移直线模组43、活动安装在第一横移直线模组43上的机械臂机构,所述第一支架41位于第一横移直线模组43下方还设有第一离子风机411,所述机械臂机构滑动至第一横移直线模组43的左限位点,机械臂机构位于所述收料平台上方;所述机械臂机构滑动至第一横移直线模组43的右限位点,机械臂机构位于所述第一上料机构上方;
64.所述第一收料机构包括安装在底板2上的第一纵向直线模组421、安装在底板2上且对称布置在第一纵向直线模组421两侧的两纵向导轨422、滑动安装在两所述纵向导轨422上的第一上料平台423、固设在底板2上且用于驱动第一上料平台423沿纵向导轨422滑动的第三驱动电机组件425、滑动安装在第一纵向直线模组421上的第二上料平台424;
65.所述机械臂机构包括滑动安装在第一横移直线模组43上的第一升降直线模组451、活动安装在第一升降直线模组451上的第一支承座452、活动安装在所述第一支承座452底面且用于吸附光学膜片的取料模组、活动安装在所述第一支承座452的侧壁且用于矫正所述取料模组上的光学膜片的对位矫正模组、安装在所述第一支承座452的前侧壁的滚压模组455;
66.所述取料模组包括固定在第一支承座452顶面的第三立板4531、固定在第三立板4531侧壁的铰接座4532、与所述铰接座4532铰接的调节气缸4533、固定在调节气缸的活塞杆端部的连接件4534、顶面与所述连接件4534底面连接的吸附平台组件4535,所述取料模组还包括通过连轴安装在第一支承座452的两侧的第一连接座4536,所述第一连接座4536的底面与吸附平台组件4535的顶面后端连接,所述吸附平台组件4535在调节气缸4533的作用下,绕连轴旋转;
67.所述第一支承座452的两侧壁前端还设有限位杆4521,用于限制吸附平台组件前端的最高旋转高度;
68.所述吸附平台组件内4535包括依次连接的第一连接板45351、密闭板45352、吸附板45353。
69.所述对位矫正模组包括横向调节模组和纵向调节模组;
70.所述横向调节模组包括通过固定螺栓水平安装在第一支承座左侧壁的横向调节气缸45411、套装在所述横向调节气缸45411的缸体上的第二连接板45412、对置在第二连接
板45412两侧且穿过第一支承座452向第一支承座452的右侧壁延伸的两横向导向杆45413、连接两所述横向导向杆45413另一端的第二连接座45414、活塞杆端部通过固定螺栓安装在第二连接座45414顶面的第一升降气缸45415、套装在所述第一升降气缸45415的缸体上的第三连接板45416、通过两第一升降导向杆45417与所述第三连接板45416两侧连接的第一限位板45418;
71.所述纵向调节模组包括通过固定螺栓水平安装在第一支承座452的后侧壁的纵向调节气缸45421、套装在所述纵向调节气缸45421的缸体上的第四连接板45422、对置在第四连接板45422两侧且依次穿过第一支承座452向前延伸的两纵向导向杆45423、连接两所述纵向导向杆45423另一端的第三连接座45424、活塞杆端部通过固定螺栓安装在第三连接座45424顶面的第二升降气缸45425、套装在所述第二升降气缸45425的缸体上的第五连接板45426、通过两第二升降导向杆45427与所述第五连接板45426两侧连接的第二限位板45428。
72.所述辊压模组包括固定在第一支承座452的前端的第六连接板4551、安装在第六连接板4551顶面的第三升降气缸4552、对置在第六连接板4551外侧壁的升降导轨4443、通过滑块活动安装在所述升降导轨4553上且顶面与所述第三升降气缸4552的活塞杆端部连接的第一升降板4554、固定在第一升降板4554的外侧壁的第四连接座4555、等距布设在第四连接座4555顶面的若干气动阀4556、设置在第四连接座4555下方且由若干所述气动阀4556共同控制升降的第二升降板4557、通过两侧的第一连杆4558安装在第二升降板4557下方的滚轮4559;
73.所述第二升降板4557上还穿设有供y轴调节模组的纵向导向杆45423穿过的槽孔。
74.请参阅图1、图2、图6所示,所述旋转撕膜装置5包括固设在底板2上的第一转移机构51、旋转平台机构52以及撕膜机构;
75.请参阅图7所示,所述旋转平台机构52包括固设在底板2上的第二支架521、固定在第二支架521底部的旋转电机组件522、底面中心与所述旋转电机组件522的输出端连接旋转平台523;
76.所述旋转平台523为一体成型且关于中线结构对称的板体,所述旋转平台523左右两侧分别通过固定件安装有吸附平台54,所述旋转平台523的两侧对称穿设有翻转孔5231,所述吸附平台54包括密封板541与吸附板542,所述吸附板542上均匀穿设有若干吸附孔,所述密封板541与吸附板542之间形成密闭空间,所述密闭空间通过气管与真空阀连通;
77.请参阅图1、图2、图6、图8所示,所述撕膜机构包括固设在底板2上的旋转台(未示出)、固设在旋转台上的第三支架531、安装在第三支架531上的第二横移直线模组532、活动安装在第二横移直线模组532上的撕膜模组533,还包括固设在机架1上的回收箱534,所述第三支架531位于所述回收箱534的上方还固设有回收夹持机构;
78.所述第三支架531位于第二横移直线模组532下方还设有第二离子风机5311;
79.所述撕膜模组包括活动安装在第二横移直线模组532上的第二升降直线模组5331、活动安装在所述第二升降直线模组5331上的第二支承座5332,所述第二支承座5332的下端连接有承载平台,所述承载平台的侧面设置有撕膜组件;
80.所述撕膜组件533包括固定在所述载物平台顶面的撕膜气缸5333、固设在所述撕膜气缸5333的活塞杆端部的夹板5334、固设在所述载物平台底面的第五连接座5335、通过
两侧的第二连杆5336安装在所述第五连接座5335下的滚轮5337,所述夹板5334的底端凹设有与所述滚轮5337的形状契合的凹槽,所述凹槽的表面与所述滚轮4337的表面紧密配合;
81.所述回收夹持模组包括固定在第三支架531下部的手指气缸5351、固设在所述手指气缸5351的气爪上的夹持杆5352,所述夹持杆5352上还设有感应器5353,所述感应器5353用于检测撕膜组件撕膜后夹持的离型膜。
82.请参阅图1、图2、图6所示,所述翻转送料装置6包括设置在底板2上且位于旋转撕膜装置5出料端的翻转机构61、位于翻转机构61与所述贴膜预压装置7之间的送料机构62;
83.请参阅图9所示,所述翻转机构61包括通过立柱固定在底板2下方的载板611、对置在所述载板611上的两侧板612、对称设置在两所述侧板612外侧的两伸缩气缸613、固设在伸缩气缸613的活塞杆端部轴承座614、连接两轴承座614的连轴615、设通过固定件安装在连轴615且随连轴615同步转动的翻转板616、固设在其中一侧板612外侧且输出轴与所述连轴615连接的翻转电机617,所述翻转板616的形状与旋转平台523上穿设的翻转孔5231的形状契合;
84.所述翻转板616上均匀布设有若干用于吸附光学膜片的真空吸盘618。
85.请参阅图6所示,所述出料机构包括固定在底板2上的出料横移直线模组621以及出料导轨622、活动安装在所述出料横移直线模组和出料导轨上的出料平台623,所述出料平台623穿设有若干相互垂直的滑槽,所述出料平台623上设有若干活动安装在滑槽上的限位件624。
86.请参阅图1、图2、图10所示,所述贴膜预压机构7包括固设在底板2上的第二转移机构71、第三上料平台72、预压平台73、第二上料机构、预压观察机构,所述第二转移机构71位于所述翻转送料装置6与预压平台73之间,所述第二上料机构并列设置在第三上料平台72与预压平台73的侧面,所述预压观察机构设置预压平台73的侧面;
87.所述第三上料平台72与预压平台73上分别穿设有形状契合取料孔721与放料孔731,所述第三上料平台72上滑动安装有若干件76;
88.所述第二上料机构包括活动安装在底板2上的第二纵向直线模组741、活动安装在所述第二纵向直线模组741上的上料模组,所述上料模组包括上料气缸742以及固设在所述上料气缸742的活塞杆端部的取料板743,所述取料板743的板形与取料孔721、放料孔731的孔形对应;
89.所述预压观察机构包括活动安装在底板2上第三纵向直线模组751,以及活动安装在第三纵向直线模组751上的观察镜模组752。
90.请参阅图1、图2、图11所示,所述加热加压装置8包括设置在底板2上的第三转移机构81、设置在底板上且与第三转移机构81并列设置的至少一组加热加压机构82;
91.所述加热加压机构82包括固定在底板2上的送料驱动模组、对置在底板上的两升降驱动模组、通过送料驱动模组活动安装在底板2上的下腔体模组、通过两所述升降驱动模组相对于底板升降的上腔体模组;
92.所述送料驱动模组包括对置在底板2上的送料导轨8211、固设在底板2上且位于两送料导轨8211之间送料电机组件,所述送料电机组件包括送料电机8212、连接所述送料电机8212的输出轴且通过两侧轴承座安装在底板2上的第一丝杆8213、套装在所述第一丝杆8213上且固设在下腔体机构底面的第一丝杆螺母座8214。
93.所述下腔体模组31包括下腔体本体8231,所述下腔体本体8231的顶面下凹,形成型腔,所述下腔体本体8231的底面与第一丝杆螺母座8214连接,所述型腔内固设有加热底板8232。
94.所述升降驱动模组包括对置在底板2上的两升降气缸8221、设置在底板2上且分布于升降气缸8221两侧的两第一导向杆8222;
95.所述上腔体模组包括固定在两所述升降气缸8221的活塞杆端部且通过直线轴承套装在第一导向杆8222上的基板8241、通过若干固定在所述基板8241的底面且侧壁相互紧密配合形成的加热加压腔体8242、固设在所述基板8241顶面的高度调节组件以及由高度调节组件驱动相对于基板8241升降的加压组件,所述加压组件的底部还固设有加热板8245,所述加热板8245位于所述加热加压腔体8242内,位于加热加压腔体8242的进料端的外侧壁上还固设有距离传感器8246;
96.所述高度调节组件包括固设在基板8241上的第四支架82431、安装在第四支架82431上且输出轴向下延伸的升降电机82432、与所述升降电机82432的输出轴的第二丝杆82433;
97.所述加压模组包括通过丝杆螺母套装在所述第二丝杆82433上的第五支架82441、对置在第五支架82441两侧的两加压气缸82442、连接两所述加压气缸82442的活塞杆端部且套装在第四支架82431外侧的第二连接板82443、通过第二导向杆82444与所述第二连接板82443底面连接的加热板8245,所述加热板8245位于所述加热加压腔体8242内;
98.所述基板8241通过直线轴承套装在第二导向杆82444上,除导向外,还可用于实现加热加压腔体上部的密封。
99.所述第一转移机构51、第二转移机构71、第三转移机构81结构相同,包括转移支架、安装在转移支架上的转移直线模组、活动安装在转移直线模组上的转移模组,所述第三转移机构81上还活动安装有出料模组,用于将加成完成后的产品转移至出料传送带机构9。
100.本发明提供的双面贴合设备的产品贴膜方法,具体包括以下步骤:
101.步骤1,利用卷对卷模切方法对热熔胶膜卷进行模切,形成若干片成型在保护膜上的光学膜片,并在模切设备的收料端收料成光学膜卷:
102.步骤2,经步骤1处理后的光学膜卷套装在剥料装置的放卷机构上,光学膜卷由放卷机构的放卷辊放出,依次经过剥料台前端、包胶辊机构后,由收料机构的收料辊回收,光学膜卷经过剥料台前端时,光学膜片从保护膜上剥离,落入放料平台上;
103.步骤3,工人将第一面板放置在第一上料机构的上料平台,通过限位块调节至设定位置,第一面板随上料平台移动至贴膜工位;
104.步骤4,机械臂机构通过取料模组将光学膜片从放料平台转移至贴膜工位,通过对位矫正模组对光学膜片位置进行对位矫正后,准确贴附在第一面板的顶面;
105.步骤5,第一转移机构将放料平台上经所述步骤4处理后的第一面板转移至旋转平台机构的旋转平台的放料工位上,旋转电机组件控制旋转平台绕中心旋转180
°
后,第一面板转移至旋转平台的撕膜工位;
106.步骤6,撕膜模组沿第三支架位移至撕膜工位上方,夹持光学膜片上的离型膜后,沿第三支架向远离撕膜工位一侧移动,将离型膜撕离光学膜片顶面;
107.步骤7,翻转机构的伸缩气缸的活塞杆伸出,将经步骤6处理后的第一面板从旋转
平台机构的撕膜工位转移至翻转板上,随后翻转180
°
转移至送料机构的送料平台上,通过若干限位件进行位置调整;
108.步骤8,工人将第二面板放置在第三上料平台上,并通过若干限位件进行位置调节;
109.步骤9,第二上料机构将经所述步骤8位置调整后的第二面板从第三上料平台转移至预压平台,第二转移机构将经所述步骤7位置调整后的第一面板转移至预压平台上方,并与第二面板预压贴附;
110.步骤10,第三转移机构将经所述步骤9预压处理后的产品转移至加热加压机构的下腔体模组的加热底板上,下腔体模组在电机的驱动下沿底板上设置的导轨移动至加热加压工位;
111.步骤11,升降气缸控制上腔体模组下降,加热加压腔体底面与下腔体机构顶面紧密配合,形成密闭空间,对密闭空间进行抽真空处理;
112.步骤12,当密闭空间达到设定真空度,经过设定时间后,加压组件控制加热板下降,与加热底板的顶面贴合,对产品进行压合;
113.步骤13,产品压合完成后,上腔体模组与下腔体模组分别复位,第三转移机构将经过步骤12压合后的产品转移至出料传送带组件,随后输出至下一工序。
114.所述步骤1中热熔胶膜卷的模切方法,包括以下步骤:
115.步骤1-1,将两面分别贴合离型膜和保护膜的热熔胶膜卷放入模切设备中,通过模切设备的出料端放料;
116.步骤1-2,在模切设备的出料端与收料端之间进行设定尺寸的卷对卷模切,模切过程中不贯穿保护膜,形成若干片均匀排布在保护膜上的光学膜片,所述光学膜片上还贴合有离型膜;
117.步骤1-3,以保护膜为基带,模切设备的收料端将热熔胶膜卷收料成光学膜卷。
118.所述步骤4中的对位矫正贴膜方法,包括以下步骤:
119.步骤4-1,光学膜片通过取料模组转移至上料平台的上方,调节真空阀的输出,控制取料模组产生的上吸风弱于上料平台产生的下吹风,使光学膜片悬浮在取料模组与上料平台之间;;
120.步骤4-2,对位矫正模组通过控制x轴调节模组的第一限位板的伸缩与y轴调节模组的第二限位板的伸缩,分别调节光学膜片的横向位置和纵向位置;
121.步骤4-3,调节后的光学膜片与第一面板位置对应后,控制取料模组的前端向下倾斜,使光学膜片从前至后依次贴附在第一面板的顶面;
122.步骤4-4,机械臂机构的滚轮模组在气缸的作用下下降,与第一面板的顶面接触,随着上料平台的复位,滚轮模组的滚轮轮面从前至后依次对光学膜片表面滚压,排出光学膜片与第一面板之间空气,稳固光学膜片与第一面板之间的贴附。
123.所述步骤6与步骤7之间还包括撕膜检测及回收方法,包括以下步骤:
124.步骤6-1,撕膜组件位移至回收工位上方,回收夹持机构的感应器是否感应到离型膜,否,则跳至步骤6;是,则进入下一步;
125.步骤6-2,回收夹持机构的手指气缸工作,两夹持杆配合夹持撕膜组件上的离型膜;
126.步骤6-3,旋转台旋转设定角度后,手指气缸工作,两夹持杆将离型膜丢入回收箱中。
127.所述步骤9与步骤10之间还包括步骤9-1,完成预压后,观察镜模组在电机驱动下移动至预压平台上,工人通过观察镜模组对产品进行预压观察。
128.所述步骤10与步骤11之间还包括步骤10-1,下腔体模组移动至加热加压工位前,距离传感器检测与加热底板之间的间距,高度调节组件通过检测间距与预设数值调节加热板的初始高度。
129.所述步骤12中产品的压合方法,包括以下步骤:
130.步骤12-1,密闭腔体内达到设定真空度后,加热板在加压模组的驱动下下降第一设定距离,进行第一次压合;
131.步骤12-2,升降气缸控制上腔体模组上升第二设定距离,加热加压腔体底面与下腔体机构顶面形成间隙,形成非密闭腔体,加热板在加压模组的驱动下下降第二设定距离,进行第二次压合。
132.以上所述仅为本发明的较佳实施例,凡依本发明权利要求范围所做的均等变化与修饰,皆应属本发明权利要求的涵盖范围。