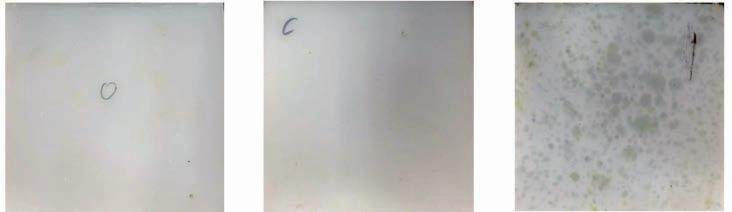
1.本发明涉及复合材料技术领域,具体涉及一种功能梯度聚烯烃板材的制备方法。
背景技术:2.已知的,聚烯烃通常指由乙烯、丙烯、1-丁烯、1-戊烯、1-己烯、1-辛烯、4-甲基-1-戊烯等α-烯烃以及某些环烯烃单独聚合或共聚合而得到的一类热塑性树脂的总称。聚烯烃现有的生产方法有高压聚合、低压聚合(包括溶液法、浆液法、本体法、气相法);聚烯烃具有相对密度小、耐化学药品性、耐水性好;良好的机械强度、电绝缘性等特点。可广泛用于薄膜、管材、板材、各种成型制品、电线电缆等领域。特别是在农业、包装、电子、电气、汽车、机械、日用杂品等方面有广泛的用途。
3.聚烯烃(po)较长、规整的分子链段决定了其比普通工程塑料具有更加优异的机械性能和力学性能,具有表现优异的耐冲击、耐磨损、耐化学腐蚀、及耐低温性能,但不可避免地存在表面硬度低、韧性及强度差等缺点。研究人员通过加入无机填料、调控分子量、与抗冲击材料共混等方法提高材料的韧性或者强度,但其强度和韧性总是互斥的,难以同时提高等,也就是说现有聚烯烃的制备方法难以同时提高聚烯烃的强度及韧性,因此急需一种功能梯度聚烯烃板材的制备方法来解决现存的问题。
技术实现要素:4.为克服背景技术中存在的不足,本发明提供了一种功能梯度聚烯烃板材的制备方法,本发明采用温度梯度/交联剂浓度梯度控制聚烯烃在热成型过程中压力方向上呈现不同结晶度/交联度的试样,由此制备功能梯度的聚烯烃。
5.为实现如上所述的发明目的,本发明采用如下所述的技术方案:一种功能梯度聚烯烃板材的制备方法,所述制备方法具体包括如下步骤:第一步、首先将模具放入液压平板热压机预热,然后将聚烯烃粉末倒入模具中;第二步、通过模压成型法将模具内的聚烯烃粉末压制成型;第三步、将聚烯烃板材从模具中脱离下来,得到目标聚烯烃板材。
6.所述的功能梯度聚烯烃板材的制备方法,所述第一步中液压平板热压机的温度为130℃~180℃,预热时间为5~8min。
7.所述的功能梯度聚烯烃板材的制备方法,所述第一步中模具的尺寸为10 cm * 10 cm * 4 mm。
8.所述的功能梯度聚烯烃板材的制备方法,所述第二步中聚烯烃粉末压制成型时,热压温度为130℃~180℃,压制时间为8~10min,压力为10mpa。
9.所述的功能梯度聚烯烃板材的制备方法,所述第二步中聚烯烃粉末压制成型后为温度梯度聚烯烃试样(po h-c)或浓度梯度聚烯烃试样(po 0-1)中的任意一种。
10.所述的功能梯度聚烯烃板材的制备方法,所述浓度梯度聚烯烃试样(po 0-1) 的填充方法为采用真空辅助法实现从底部到顶部按照从小到大的交联剂浓度的顺序填充。
11.所述的功能梯度聚烯烃板材的制备方法,所述浓度梯度聚烯烃试样(po 0-1) 的脱模工艺条件为直接剥离,在空气中缓慢冷却。
12.所述的功能梯度聚烯烃板材的制备方法,所述温度梯度聚烯烃试样(po h-c)的填充方法为采用真空辅助法以纯聚烯烃进行填充。
13.所述的功能梯度聚烯烃板材的制备方法,所述温度梯度聚烯烃试样(po h-c)的脱模工艺条件为在冷压过程中,控制上板温度为100℃,使试样缓慢冷却;控制下板温度为20℃,使试样快速冷却,进而实现试样结晶速率的快慢。
14.所述的功能梯度聚烯烃板材的制备方法,所述第三步中目标聚烯烃板材的厚度为4mm。
15.采用如上所述的技术方案,本发明具有如下所述的优越性:本发明通过控制聚烯烃板材的温度梯度和交联度形成梯度结构,再经过热压、冷却结晶步骤,实现试样在沿受力方向上的结晶梯度,提高其抗冲击性和能量吸收能力等,本发明可提高聚烯烃板材的抗冲击性和能量吸收能力,且具有高导热性,适合大范围的推广和应用。
附图说明
16.图1是本发明具体实施例中实施例1、实施例2、实施例3三组超高分子量聚乙烯样品图片,其中左侧的图片是无梯度结构,中间的图片是结晶梯度试件;右侧的图片是交联梯度试件,尺寸均为15*15*4 cm3;图2是本发明具体实施例中实施例2温度梯度超高分子量聚乙烯的不同层扫描电镜图片;图3是本发明具体实施例中实施例3温度梯度超高分子量聚乙烯的不同层扫描电镜图片;图4是本发明具体实施例中实施例1、实施例2、实施例3中所使用的模具结构示意图;图5是本发明具体实施例中实施例1、实施例2、实施例3中所使用模压成型工艺流程及参数。
具体实施方式
17.通过下面的实施例可以更详细的解释本发明,本发明并不局限于下面的实施例;结合附图1~5所示的一种功能梯度聚烯烃板材的制备方法,所述制备方法具体包括如下步骤:第一步、首先将模具放入液压平板热压机预热,然后将聚烯烃粉末倒入模具中;所述液压平板热压机的温度为130℃~180℃,预热时间为5~8min;所述模具的尺寸为10 cm * 10 cm * 4 mm;实施时,模具的具体结构如图4所示,即模具为方形结构,在模具的中部设置有放置聚烯烃粉末的空腔;第二步、通过模压成型法将模具内的聚烯烃粉末压制成型;实施时,所述聚烯烃粉末压制成型时,热压温度为130℃~180℃,压制时间为8~10min,压力为10mpa;所述聚烯烃粉末压制成型后为温度梯度聚烯烃试样(po h-c)或浓度梯度聚烯烃试样(po 0-1)中的任
意一种;所述浓度梯度聚烯烃试样(po 0-1) 的填充方法为采用真空辅助法实现从底部到顶部按照从小到大的交联剂浓度的顺序填充;所述浓度梯度聚烯烃试样(po 0-1) 的脱模工艺条件为直接剥离,在空气中缓慢冷却;所述温度梯度聚烯烃试样(po h-c)的填充方法为采用真空辅助法以纯聚烯烃进行填充;所述温度梯度聚烯烃试样(po h-c)的脱模工艺条件为在冷压过程中,控制上板温度为100℃,使试样缓慢冷却;控制下板温度为20℃,使试样快速冷却,进而实现试样结晶速率的快慢;第三步、将聚烯烃板材从模具中脱离下来,得到目标聚烯烃板材;实施时,所述目标聚烯烃板材的厚度为4mm。
18.本发明的具体实施例如下:实施例1:制备对照组纯超高分子量聚乙烯板材,包括以下步骤:(1)将模具放入平板热压机中预热5 min,上下模具温度为180℃,在预热好的模具中放入90g 超高分子量聚乙烯粉末,并压平;(2)将(2)中填充好的模具放入到平板热压机中,通过热压的方法成型,热压工艺参数为:上下模具温度为180℃,压力为10~15 mpa,热压时间为8~10 min;(3)将(2)中目标超高分子量聚乙烯板取出,室温冷却。
19.实施例2:制备温度梯度超高分子量聚乙烯板材,包括以下步骤:(1)将模具放入平板热压机中预热5 min,上下模具温度为180℃;(2)在(1)中预热好的模具中放入90g 超高分子量聚乙烯粉末,并压平,使粉末充斥整个模具;(3)将(2)中填充好的模具放入到平板热压机中,通过热压的方法成型。热压工艺参数为:上下模具温度为180℃,压力为10~15 mpa,热压时间为8~10 min;(4)在冷压机中预热另外两个模具,上板温度为100℃,下板温度为20℃;(5)将(3)中目标超高分子量聚乙烯板取出,迅速将其放于(4)中预热好的模具中,并给与冷压处理。冷压工艺参数为:上模具温度100℃,下模具温度20℃,冷压压力为1 mpa,冷压时间为5~10 min。
20.实施例3:制备浓度梯度超高分子量聚乙烯板材,包括以下步骤:(1)将模具放入平板热压机中预热5 min,上下模具温度为180℃;(2)在(1)中预热好的模具中放入15g 超高分子量聚乙烯粉末,并压平;再放入混合0.2%质量分数交联剂的超高分子量聚乙烯粉末,并压平;再放入混合0.4%质量分数交联剂的超高分子量聚乙烯粉末,并压平;再放入混合0.6%质量分数交联剂的超高分子量聚乙烯粉末,并压平;再放入混合0.8%质量分数交联剂的超高分子量聚乙烯粉末,并压平;再放入混合1.0%质量分数交联剂的超高分子量聚乙烯粉末,并压平;(3)将(2)中填充好的模具放入到平板热压机中,通过热压的方法成型。热压工艺参数为:上下模具温度为180℃,压力为10~15 mpa,热压时间为8~10 min;(4)将(3)中目标超高分子量聚乙烯板取出,室温冷却。
21.本发明在实施时,获得的聚烯烃板材可以是超高分子量聚乙烯,聚丙烯,低密度聚
乙烯,高密度聚乙烯,聚苯乙烯,聚甲基丙烯酸甲酯中的任意一种。聚烯烃的分子量为5万以上。平板热压机上下模具温度为130℃以上的任一温度。交联剂的含量为0.1%~10%的任一浓度;交联剂的种类可以是以下交联剂的任何一种:过氧化氢、过硫酸铵、过硫酸钾、过氧化苯甲酰、过氧化苯甲酰叔丁酯、过氧化甲乙酮等。聚烯烃以及交联剂的填充方法为以下方法的一种:真空辅助法、逐层铺平压实法等。
22.本发明在具体实施时,所述的两种功能梯度聚烯烃试样的填充方法除了真空辅助法外,还可以采用逐层平铺压实的方法。
23.此外,在本发明中所述的两种功能梯度聚烯烃试样的剥离方法可以采用以下方法中的任意一种:室温下冷却,放入凉水中冷却。
24.此外,在本发明中压制成型的温度可以为聚烯烃的熔点(130℃)以上的任一温度,时间可以为8分钟以上的任一时间。
25.本发明的有益效果如下:1、高抗冲击性能和高能量吸收能力,可吸收冲击带来的剧大能量。
26.2、具有梯度结构的聚烯烃在不牺牲材料强度的同时提高了其抗冲击性能。
27.3、该制备方法方法操作简便、高效。
28.本发明未详述部分为现有技术。
29.为了公开本发明的发明目的而在本文中选用的实施例,当前认为是适宜的,但是,应了解的是,本发明旨在包括一切属于本构思和发明范围内的实施例的所有变化和改进。