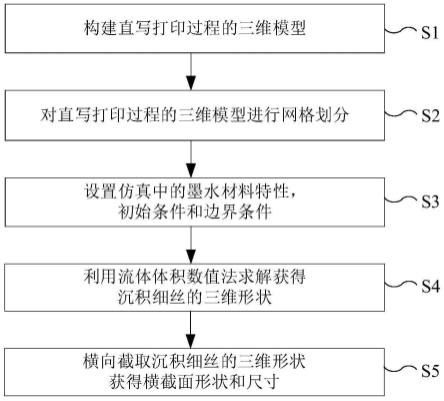
1.本发明涉及直写打印的工艺技术领域,特别涉及一种基于数值仿真的直写打印中沉积细丝的横截面预测方法。
背景技术:2.直写打印属于挤出式增材制造技术,是一种极具发展前景的先进制造技术,其最大的优势在于材料的普适性和制造过程的灵活性,可以将多种金属或非金属材料以较低成本和较高精度制造成复杂的三维零件。直写打印的工作原理为:首先,将材料制备为具有剪切变稀特性和粘弹特性的浆状或糊状的墨水;然后,利用直写打印机将制备的墨水通过喷嘴挤出为连续的细丝;最后,挤出的细丝通过层层堆积成为三维实体零件。
3.直写打印制造的零件的尺寸精度和表面粗糙度取决于沉积细丝的横截面形状和尺寸。墨水的材料特性(包括密度、表面张力系数和粘度)以及工艺参数将影响沉积细丝的横截面形状和尺寸。为提高直写打印制造的零件的尺寸精度,沉积细丝的横截面预测一直是直写打印工艺过程研究中的一个热点问题和关键技术。
4.目前,预测直写打印中沉积细丝横截面的方法有实验预测法、解析预测法和数值仿真预测法。实验预测法通过大量实验构建实验输入参数和实验结果的拟合模型,由于墨水材料的多样性和工艺参数的复杂性,该方法需要完成大量的实验才能获得较好的预测结果,存在着成本高、耗费大量时间和材料的问题。解析预测法通过对直写打印过程进行数学建模获得沉积细丝横截面的尺寸预测结果,该方法在数学建模过程中需要将沉积细丝横截面简化为恒定的简单形状,例如:公开发表的解析预测法在数学建模过程中将沉积细丝横截面简化为半椭圆形,圆形,方形等等固定的简单形状。然而,沉积细丝横截面的形状会随着墨水材料特性和工艺参数的变化而变化,并不是固定的简单形状。因此,解析预测法存在着精度较低的问题。相比于实验预测法和解析预测法,数值仿真预测法利用流体动力学数值仿真获得沉积细丝的三维几何模型从而获得横截面的形状和尺寸,能简单且精确地预测沉积细丝的横截面形状和尺寸,是目前在挤出式增材制造工艺过程分析领域的一个公认的最优预测方法。
5.目前,一些学者已经成功将数值仿真预测法应用于挤出式增材制造技术中的熔融沉积制造的沉积细丝横截面预测中,例如:comminal等人构建了熔融沉积制造的沉积细丝数值仿真模型用于预测沉积细丝的横截面;gosset等人对熔融沉积制造中的沉积细丝进行数值仿真研究获得了沉积细丝的横截面预测结果。然而,目前还未有充分考虑墨水材料特性和工艺参数设定的针对直写打印中沉积细丝横截面的数值仿真预测方法。
技术实现要素:6.本发明的目的是提供一种充分考虑墨水材料特性和工艺参数设定的基于数值仿真的直写打印中沉积细丝的横截面预测方法。
7.为此,本发明技术方案如下:
8.一种基于数值仿真的直写打印中沉积细丝的横截面预测方法,步骤如下:
9.s1、构建直写打印过程的三维几何模型,模型包括有喷嘴入口面、喷嘴内表面、喷嘴外表面、喷嘴底面、空气边界面和沉积基板面;
10.s2、对步骤s1构建的三维几何模型进行网格划分,其原则为:1)自喷嘴内表面至喷嘴内部形成的与喷嘴内径一致的圆柱形区域内、以及自喷嘴底面至其在沉积基板投影面之间形成的外径与喷嘴外径一致的圆柱形区域内均划分有密度最大网格;2)平行于横截面方向的网格密度大于垂直于横截面方向的网格密度;
11.s3、设置仿真中的墨水材料特性、相分数初始条件、以及各个表面的边界条件和边界初始条件;
12.s4、利用流体体积数值法求解获得沉积细丝的三维形状;
13.s5、利用图像处理软件对步骤s4得到沉积细丝进行横向截取,以获得沉积细丝的横截面形状和尺寸。
14.进一步地,在步骤s1中,三维长方体的顶面、前面、背面、左侧面和右侧面为空气边界面;三维长方体的底面为沉积基板面;自三维长方体的左侧顶面竖直向下设置圆柱形盲孔,且圆柱形盲孔的直径等于直写打印机中的喷嘴外径;在圆柱形盲孔内居中设置有直径小于圆柱形盲孔内径的圆柱形凸台,且圆柱形凸台的直径等于喷嘴的内径;圆柱形凸台的顶面与三维长方体的顶面齐平、底面与盲孔的底面齐平;圆柱形凸台的顶面为喷嘴入口面;圆柱形凸台的外侧面为喷嘴内表面;圆柱形盲孔的内侧面为喷嘴外表面;位于圆柱形盲孔的内侧面与圆柱形凸台的外侧面之间的圆柱形盲孔的环形底面为喷嘴底面。
15.进一步地,在步骤s3中,
16.墨水材料特性包括密度ρ、表面张力系数σ和粘度μ;
17.相分数初始条件为:自喷嘴内表面2至喷嘴内部区域(即圆柱形凸台所在区域)相分数为1,其他区域的相分数为0;
18.边界条件为:
①
设置喷嘴入口面的边界类型为入口边界,速度设置为喷嘴入口的墨水速度为ve;
②
设置喷嘴内表面、喷嘴外表面和喷嘴底面的边界类型为无滑移边界,对应无滑移条件;
③
设置空气边界面的边界类型为输入输出边界,边界条件为仿真中的实时动态计算值;
④
设置沉积基板面的边界类型为无滑移边界,对应无滑移条件,速度设置为喷嘴相对于沉积基板的水平移动速度vn。
19.进一步地,步骤s4的具体方法为:利用流体体积数值法求解每个网格的相分数,并取相分数值为0.5的曲面为沉积细丝的三维形状。
20.进一步地,步骤s1~步骤s4采用openform软件实现,步骤s5采用paraview软件实现。
21.相较于实验预测法和解析预测法,该基于数值仿真的直写打印中沉积细丝的横截面预测方法能简单且精确地预测直写打印中沉积细丝横截面的形状和尺寸;对比不同工艺参数条件下实际的横截面与本方法获得的预测横截面,两者的最大宽度预测相对误差为4.44%,最大高度预测相对误差为7.22%,证明了本发明提出的方法在横截面预测上的准确性以及对不同工艺参数的普适性,该方法合理有效且具有较高的预测精度和普适性。
附图说明
22.图1为本发明提出的基于数值仿真的直写打印中沉积细丝的横截面预测方法的流程图;
23.图2为本发明的基于数值仿真的直写打印中沉积细丝的横截面预测方法在步骤s1中构建的直写打印过程的三维几何模型的示意图;
24.图3为本发明的基于数值仿真的直写打印中沉积细丝的横截面预测方法在步骤s1中构建的直写打印过程的三维几何模型的关键参数示意图;
25.图4为本发明的基于数值仿真的直写打印中沉积细丝的横截面预测方法在步骤s2中获得的三维几何模型的网格划分示意图;
26.图5为本发明的基于数值仿真的直写打印中沉积细丝的横截面预测方法在步骤s3中设置的相分数初始条件示意图;
27.图6为本发明的实施例中由步骤s4中获得的沉积细丝的三维形状示意图;
28.图7为本发明的实施例中由步骤s5中获得的沉积细丝的横截面形状示意图。
具体实施方式
29.下面结合附图及具体实施例对本发明做进一步的说明,但下述实施例绝非对本发明有任何限制。
30.在本实施例中,针对某墨水在直写打印中沉积细丝的横截面预测和试验验证,以对本技术提出的方法进行进一步解释,并对该方法的有效性和准确性进行验证;该方法的具体实施步骤如下:
31.s1、利用几何建模软件构建直写打印过程的三维几何模型,模型包括有喷嘴入口面、喷嘴内表面、喷嘴外表面、喷嘴底面、空气边界面和沉积基板面;
32.如图2所示,该直写打印过程的三维几何模型由六类边界面组成:喷嘴入口面1、喷嘴内表面2、喷嘴外表面3、喷嘴底面4、空气边界面5和沉积基板面6;
33.具体地,该模型的外轮廓为一个三维长方体,三维长方体的顶面、前面、背面、左侧面和右侧面为空气边界面5;三维长方体的底面为沉积基板面6;自三维长方体的左侧顶面竖直向下设置圆柱形盲孔,且圆柱形盲孔的直径等于直写打印机中的喷嘴外径;在圆柱形盲孔内居中设置有直径小于圆柱形盲孔内径的圆柱形凸台,且圆柱形凸台的直径等于喷嘴的内径;圆柱形凸台的顶面与三维长方体的顶面齐平、底面与盲孔的底面齐平;圆柱形凸台的顶面为喷嘴入口面1;圆柱形凸台的外侧面为喷嘴内表面2;圆柱形盲孔的内侧面为喷嘴外表面3;位于圆柱形盲孔的内侧面与圆柱形凸台的外侧面之间的圆柱形盲孔的环形底面为喷嘴底面4;
34.如图3所示,在该直写打印过程的三维几何模型中,关键参数包括有:喷嘴内径dn,喷嘴外径dn,喷嘴高度ln,喷嘴底面到沉积基板的距离h,喷嘴入口的墨水速度ve和喷嘴相对于沉积基板的水平移动速度vn;其中,喷嘴入口的墨水速度ve施加于喷嘴入口面1;考虑到喷嘴与沉积基板间的运动是互相的,虽然在实际直写打印中是沉积基板不动,喷嘴相对于沉积基板运动,但为了简化数值仿真运算时间,在建模中,设定喷嘴固定不动,沉积基板相对于喷嘴运动,以将喷嘴相对于沉积基板的水平移动速度vn施加在沉积基板面6上;
35.因此,直写打印过程中在所使用的直写打印机设备和操作过程涉及的参数包括:
喷嘴内径dn,喷嘴外径dn,喷嘴高度ln,喷嘴底面到沉积基板的距离h、喷嘴相对于沉积基板的水平移动速度vn和喷嘴入口的墨水速度ve;
36.其中,喷嘴内径dn,喷嘴外径dn,喷嘴高度ln通过对直写打印机上的喷嘴测量得到,喷嘴底面到沉积基板的距离h、喷嘴相对于沉积基板的水平移动速度vn和活塞运动速度v
p
基于参数设定得到;另外,由于在直写打印过程中,喷嘴入口的墨水速度ve与直写打印机中的活塞直径d
p
、喷嘴内径dn和挤压墨水用的活塞运动速度v
p
相关,因此,由喷嘴入口的墨水速度ve公式:ve=(d
p
/dn)2v
p
确定;
37.在本实施例中,经测量,喷嘴内径dn=0.84mm,喷嘴外径dn=1.22mm,喷嘴高度ln=2.44mm;喷嘴底面到沉积基板的距离h设置为0.75mm;喷嘴相对于沉积基板的水平移动速度vn设置为4.8mm/s;基于直写打印机中的活塞直径d
p
为21.6mm,活塞运动速度v
p
设置为9.074
×
10-3
mm/s,喷嘴入口的墨水速度ve=(d
p
/dn)2v
p
=6mm/s;基于此,直写打印过程的三维几何模型利用openfoam软件(openfoam v1912)构建得到,具体通过在软件的blockmesh组件中依次进行模型边界点坐标定义、不同类型区块划分和边界确定,构建得到如上所述与实际打印过程相符的直写打印过程的三维几何模型;
38.s2、对步骤s1构建的三维几何模型进行网格划分;
39.为保证横截面预测结果的准确度以及减少计算的时间,针对直写打印过程的三维几何模型的网格划分的原则为:
40.1)自喷嘴内表面至喷嘴内部形成的与喷嘴内径一致的圆柱形区域(即圆柱形凸台所在区域)内、以及自喷嘴底面(即圆柱形盲孔底面)至其在沉积基板投影面之间形成的外径与喷嘴外径一致的圆柱形区域内均划分有密度最大网格;
41.2)平行于长方体横截面方向的网格密度大于垂直于长方体横截面方向的网格密度;另外,在本实施例中,由于沉积细丝集中在长方体下部区域内,因而为了进一步减少计算量和计算时间,长方体上部区域划分的网格比下部区域划分的网格稀疏,该划分方式为可选方式且不影响最终的预测结果。
42.在本实施例中,该步骤s2采用openfoam软件(openfoam v1912)作为网格划分软件,具体为软件中的blockmesh组件,实现对步骤s1建立的直写打印过程的三维几何模型进行网格划分;具体地,如图4所示,自喷嘴内表面至喷嘴内部形成的与喷嘴内径一致的圆柱形区域内、以及自喷嘴底面至其在沉积基板投影面之间形成的外径与喷嘴外径一致的圆柱形区域内划分形成的网格的最大单边尺寸为0.1mm;平行于横截面方向的网格的最大单边尺寸为0.2mm,垂直于横截面方向的网格的最大单边尺寸为0.4mm,以使平行于横截面方向的网格密度大于垂直于横截面方向的网格密度;
43.s3、设置仿真中的墨水材料特性、相分数初始条件、以及各个表面的边界条件和边界初始条件;
44.具体地,该步骤s3的具体操作步骤为:
45.s301、设置仿真中的墨水材料的密度ρ、表面张力系数σ和粘度μ;其中,密度ρ、表面张力系数σ为常数,可直接由墨水的材料参数试验获得;粘度μ随着剪切速率变化而变化,由公式表示,式中,μ为墨水的粘度,为剪切速率,μ0为墨水的零切粘度,τ0为墨水的屈服应力,k为墨水的粘度系数,n为墨水的流变系;μ0,τ0,k,n均由墨水的材料参数试验获得;
46.在本实施例中,仿真中的墨水材料特性(包括密度ρ、表面张力系数σ和粘度μ)的设置利用openfoam软件(openfoam v1912)下仿真文件中的constant文件夹中的transport properties设置而成;具体地,密度ρ=972kg/m3,表面张力系数σ=43mn/m,墨水的粘度μ随着剪切速率变化而变化,由公式表示,式中,为剪切速率,零切粘度μ0=1.58
×
106pa
·
s,屈服应力τ0=563pa,粘度系数k=867pa
·
sn,流变系数n=0.045;
47.s302、设置仿真中的相分数初始条件:
48.在3d打印过程的初始时刻,墨水充满喷嘴且还未被挤出;基于此,设置相分数的初始条件为:自喷嘴内表面2至喷嘴内部区域(即圆柱形凸台所在区域)的相分数为1,其他区域的相分数为0;如图5所示,颜色较深区域代表相分数为1,颜色较浅区域代表相分数为0;
49.在本实施例中,利用openfoam软件(openfoam v1912)下的仿真文件中的system文件夹中的set fields dict文件设置相分数初始条件:自喷嘴内表面2至喷嘴内部区域的相分数为1,其他区域的区域相分数为0;
50.s303、设置仿真中各个表面的边界条件和边界初始条件,其具体设置方式为:
51.①
设置喷嘴入口面1的边界类型为入口边界,速度设置为喷嘴入口的墨水速度为ve;
52.②
设置喷嘴内表面2、喷嘴外表面3和喷嘴底面4的边界类型为无滑移边界,对应无滑移条件;
53.③
设置空气边界面5的边界类型为输入输出边界,对应边界条件通过仿真实时计算得到;
54.④
设置沉积基板面6的边界类型为无滑移边界,对应无滑移条件,速度设置为喷嘴相对于沉积基板的水平移动速度vn;
55.在本实施例中,边界条件和初始条件利用openfoam软件(openfoam v1912)仿真文件中的0文件夹下的p_rhg文件和u文件进行设置;具体地,p_rhg文件用于设置各个表面的压力边界条件和压力初始条件,u文件用于设置各个表面的速度边界条件和速度初始条件;具体的设置情况如下表1所示;
56.表1:
[0057][0058]
s4、利用流体体积数值法求解获得沉积细丝的三维形状;
[0059]
采用流体体积法求解墨水挤出细丝与空气的边界以获得生物墨水挤出细丝的形状,即将生物墨水和空气视为单一的连续流体,通过构建和求解单一的连续流体的控制方
程得到连续流体中每个网格的相分数,然后通过相分数等于0.5的等值线确定挤出细丝的形状;具体求解过程如下:
[0060]
(1)相分数定义为式中,α为一个网格的相分数;vb为该网格中生物墨水的体积;vm为该网格的总体积;其中,从相分数的定义中可知α的取值为:
[0061][0062]
(2)由相分数得到生物墨水和空气等效的单一连续流体的密度和粘度:
[0063][0064]
式中,ρ为生物墨水和空气等效的单一连续流体的密度;μ为生物墨水和空气等效的单一连续流体的粘度;α为一个网格的相分数;ρb为生物墨水的密度;μb为生物墨水的粘度;ρa为空气的密度;μa为空气的粘度;
[0065]
(3)构建仿真中的控制方程,其由连续性方程、动量守恒方程和相分数方程构成;具体地,
[0066]
①
连续性方程为:
[0067]
式中,
·
表示散度运算符;u为生物墨水和空气等效的单一连续流体的速度场矢量;
[0068]
②
动量守恒方程为:
[0069]
式中,t为时间,表示矢量对时间一次求导符号,ρ为生物墨水和空气等效的单一连续流体的密度,u为生物墨水和空气等效的单一连续流体的速度场矢量,
·
表示散度运算符,表示梯度运算符,p为生物墨水和空气等效的单一连续流体的压力标量,μ为生物墨水和空气等效的单一连续流体的粘度,g为重力加速度矢量,f
σ
为表面张力矢量;
[0070]
其中,表面张力矢量公式为:式中,σ为生物墨水的表面张力系数;κ为生物墨水挤出细丝的表面形状曲率,κ由在仿真过程中实时计算的形状确定;表示梯度运算符;α为一个网格的相分数;
[0071]
③
相分数方程为:
[0072]
式中,t为时间,表示矢量对时间一次求导符号,
·
表示散度运算符,u为生物墨水和空气等效的单一连续流体的速度场矢量,ur为生物墨水和空气两种流体在挤出细丝表面的速度差;
[0073]
其中,ur由公式:计算得到,
[0074]
式中,min( )表示取最小值操作符,max( )表示取最大值符,| |表示取绝对值操作符,表示梯度运算符,c为压缩常数,c=1;
[0075]
(4)将步骤s3设置的仿真中的墨水材料特性、初始条件和边界条件代入至上述步骤(1)~(3)的各个方程中,以求解每个网格的相分数,并取相分数值为0.5的曲面为沉积细丝的三维形状;
[0076]
在本实施例中,通过在openfoam软件(openfoam v1912)中的inter foam求解器内导入经过网格划分的三维几何模型、以及仿真的墨水材料特性、相分数初始设置条件、边界条件和初始压力和速度条件,以求解出每个网格相分数,并取相分数取值为0.5的曲面为沉积细丝的三维形状。如图6所示,沉积基板面6上颜色较深细丝即为通过该数值仿真得到的预测沉积细丝的三维几何模型。
[0077]
s5、横向截取沉积细丝的三维形状获得横截面形状和尺寸:
[0078]
利用图像处理软件,对步骤s4获得该数值仿真得到的预测沉积细丝的三维几何模型进行横向剖面截取,得到预测沉积细丝的的横截面图像,进而得出预测沉积细丝的横截面形状和尺寸;
[0079]
在本实施例中,将经过步骤s4得到的预测沉积细丝的三维几何模型以几何文件的形式输出,并将几何文件导入至图像处理软件paraview 5.8.0中,利用paraview 5.8.0中提供的slice工具横向截取沉积细丝的三维形状,即可获得如图7所示的横截面形状和尺寸;在本实施例中,预测沉积细丝的横截面形状如图7所示为近似椭圆形,相应地,横截面宽度为1.10mm,横截面高度为0.74mm。
[0080]
为验证本技术的预测方法的准确性,在实际的直写打印机中装入该墨水,以与仿真中设置的工艺条件相同的工艺条件进行直写打印获得沉积细丝,同时在打印过程中用相机拍摄放置在直尺边上的沉积细丝的端面;通过将包含有沉积细丝端面和直尺的照片进行处理,根据沉积细丝端面与直尺标度的对比,得到实际打印出的沉积细丝的横截面的实际宽度为1.10mm、实际高度为0.75mm;可见,利用本技术提出的预测方法获得的沉积细丝横截面的预测宽度相对误差为0,预测高度相对误差为1.33%,证明了本发明提出的方法在横截面预测上的准确性。
[0081]
进一步地,为验证本发明提出的方法在不同工艺条件的普适性,将喷嘴底面到沉积基板的距离h分别设置为075mm,1.00mm和1.25mm三组参数,其他参数与上述实施例中的参数设置相同,进而获得了如下表2所示的三根沉积细丝横截面宽度和高度的预测结果;
[0082]
表2:
[0083]
喷嘴底面到沉积基板的距离h/mm0.751.001.25预测宽度/mm1.100.940.97预测高度/mm0.740.930.90
[0084]
相应地,根据对应的实际直写打印试验,获得了如下表3所示的横截面宽度和高度的实际测量结果;
[0085]
表3:
[0086][0087][0088]
根据表2的预测尺寸和表3的实际测量结果,计算得到如下表4所示的对沉积细丝
横截面的宽度预测相对误差和高度预测相对误差;
[0089]
表4:
[0090]
喷嘴底面到沉积基板的距离h/mm0.751.001.25宽度预测相对误差04.44%0高度预测相对误差1.33%4.12%7.22%
[0091]
根据表2~表4的测试结果可以看出,在不同的工艺条件下,最大宽度预测相对误差为4.44%,最大高度预测相对误差为7.22%,证明了本技术提出的预测方法在横截面预测上的准确性以及对不同工艺参数的普适性,该方法合理有效且具有较高的预测精度和普适性。
[0092]
本发明未详细公开的部分属于本领域的公知技术。尽管上面对本发明说明性的具体实施方式进行了描述,以便于本技术领域的技术人员理解本发明,但应该清楚,本发明不限于具体实施方式的范围,对本技术领域的普通技术人员来讲,只要各种变化在所附的权利要求限定和确定的本发明的精神和范围内,这些变化是显而易见的,一切利用本发明构思的发明创造均为保护之列。