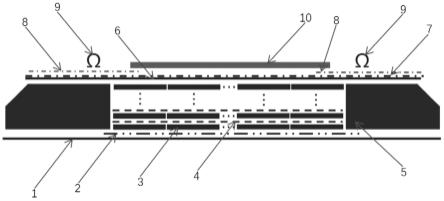
1.本发明属于风电叶片成型技术领域,具体是涉及到一种风电叶片一体灌注成型系统、方法及风电叶片。
背景技术:2.风机及叶片都有着大型化的发展趋势,拉挤板有着纤维含量高,复材质量稳定,在满足刚度和强度的前提下,采用碳纤维拉挤板材较传统玻璃钢叶片质量轻30%以上。采用拉挤板的风电叶片大梁能够有效减小叶片重量。
3.在风电叶片与大梁一体成型灌注方法中,是通过将拉挤板材码垛完成后直接吊入叶片模具一起真空灌注成型,而目前常规方法为在大梁区域的一侧布置注胶管道,向另一侧单向灌注,体系整体采用在叶片模具两侧抽气的方式使胶液进行流动。但上述方法存在下列问题:(1)大梁区域灌注为一侧单向灌注的方式,灌注时间较长,胶液在大梁区域的流动路径长,胶液中气体位移量及阻力大,容易导致气体残留而形成灌注缺陷;(2)拉挤板材之间存有层铺及拼接的缝隙,灌注过程中,胶液在拉挤板材之间的流动速度会大于胶液在玻纤层上流动浸润的速度,而在胶液从大梁区域另一侧流出之后,大梁上下两侧玻纤层上未被胶液浸润的部分,由于前方胶液产生的阻力,后方胶液很难继续前进并浸润该部分,从而会导致大梁区域浸渍不良、包胶等缺陷的产生。
技术实现要素:4.本发明要解决的技术问题是提供一种灌注效率高、灌注缺陷少的风电叶片一体灌注成型系统、方法及风电叶片。
5.本发明提供一种风电叶片一体灌注成型系统,包括在叶片模具中依次铺设的下表面玻纤层、大梁、上表面玻纤层及真空袋膜,大梁由数层拉挤板层铺形成,且大梁位于两组芯材之间;还包括设置在上表面玻纤层与真空袋膜之间的抽气袋和两组导流网,两组导流网分别位于两组芯材的上方并分别对应覆盖两组芯材与大梁侧边的衔接处,两组导流网之间设置有间隔,且两组导流网上均设置有注胶管,所述抽气袋位于大梁上方,抽气袋的两侧分别搭接在两个导流网上。
6.更进一步地,两两所述拉挤板的层间铺设有导流织物,所述导流织物的宽度与对应层的拉挤板宽度相同。
7.更进一步地,所述下表面玻纤层与最下层拉挤板之间设置有连续毡,所述连续毡的宽度大于等于最下层拉挤板的宽度。
8.更进一步地,两组所述导流网对应覆盖两组芯材与大梁侧边衔接处的一侧并延伸至拉挤板的上方,所述抽气袋的宽度小于最上层拉挤板的宽度,所述注胶管设置在位于芯材上方的导流网区域上。
9.更进一步地,每层所述拉挤板均由数个板材沿大梁的宽度方向铺设而成。
10.更进一步地,两组所述导流网延伸至拉挤板上方部分的宽度,分别小于最上层拉
挤板中位于最外两侧的板材的宽度。
11.更进一步地,所述抽气袋朝向真空袋膜的一面设置有观察窗。
12.本发明还提供一种风电叶片一体灌注成型方法,其特征是,包括以下步骤:
13.s1、在叶片模具内铺设下表面玻纤层,在下表面玻纤层上铺设连续毡,在连续毡上铺设由数层拉挤板和导流织物交错层铺形成的大梁,并在大梁的两侧分别铺设一组芯材,再铺设上表面玻纤层;
14.s2、在两组芯材上方分别各铺设一组导流网,使两组导流网对应覆盖两组芯材与大梁侧边的衔接处,并使两组导流网之间具有间隔,在两组导流网上各设置一根注胶管,大梁上方区域铺设抽气袋,并使抽气袋的两侧分别与两组导流网的一侧搭接;
15.s3、使用真空袋膜将叶片模具密封,通过真空管将体系与真空装置连接,形成真空体系后进行灌注。
16.更进一步地,所述s1中,先通过数层拉挤板和导流织物交错层铺并捆扎固定,以形成大梁,再将大梁吊入叶片模具中并铺设在连续毡上。
17.本发明还提供一种风电叶片,采用上述的一体灌注成型方法制备。
18.本发明的有益效果是,(1)通过在大梁双侧进胶、并大梁上方抽气的方式,胶量更充足,胶液在大梁区域移动的路径更短,有效减少了大梁区域的灌注时间,进而减少了整体灌注时间,提高了灌注效率,并且由于胶液在大量区域的移动路径变短,胶液流动时受到的阻力更小,气体位移量及阻力也更小,上方的抽气袋不仅可持续抽出拉挤板层间的气体,还可为大梁区域胶液的流动提供驱动力,有效降低灌注缺陷。(2)采用的为上抽气方式,符合气体向上流动的基本原则,气体位移量小的同时可以使气体穿越难度更小,脱泡效果更好。并且本发明仅针对拉挤大梁区域的上流道结构进行优化及调整,在保证提升产品质量,加快灌注方法的前提下,不会对产品铺设难度,材料用量成本,产品生产人工时等方面造成影响。
附图说明
19.附图1为本发明风电叶片一体灌注成型系统的结构示意图。
20.在图中,1-下表面玻纤层;2-连续毡;3-拉挤板;4-导流织物;5-芯材;6-上表面玻纤层;7-脱模布;8-导流网;9-注胶管;10-抽气袋。
具体实施方式
21.如附图1所示,本发明提供一种风电叶片一体灌注成型系统,包括在叶片模具中从下而上依次铺设的下表面玻纤层1、大梁上表面玻纤层6及真空袋膜,所述大梁为拉挤板大梁,由数层拉挤板3沿大梁的高度方向层铺形成,大梁的前缘侧和后缘侧各设置有一组芯材5,且芯材5与大梁的侧边相贴,即大梁位于两组芯材5之间且大梁的两侧分别与两组芯材5相贴。本发明还包括设置在上表面玻纤层6与真空袋膜之间的抽气袋10和两组导流网8,两组导流网8分别位于两组芯材5的上方,两组导流网8上均设置有注胶管9,而如图1所示,两组导流网8分别对应覆盖在两组芯材5与大梁侧边衔接处的上方,且两组导流网8之间设置有间隔,所述抽气袋10位于大梁区域的上方,且抽气袋10的两侧分别搭接在两个导流网8上。使用时,通过密封条将真空袋膜与叶片模具密封连接,并通过真空管将原有体系及抽气
袋与真空装置连接,形成真空灌注体系。
22.本发明提供的一体灌注成型系统,在原有风电叶片灌注成型系统的基础上,在两个芯材5上方区域分别增加了一组导流网8和注胶管9,大梁两侧区域均可有胶液进入灌注体系中,而在大梁上方区域设置抽气袋10并使抽气袋10两侧分别与两组导流网8搭接,抽气袋10抽气时控制导流网8上胶液向两个导流网8之间流动,具体为,导流网8上的胶液在重力作用向下流动至芯材5中,同时在抽气袋10的抽气作用下向大梁区域横向移动并浸润,相比传统的单侧进胶方式,本发明通过在大梁双侧进胶、并大梁上方抽气的方式,胶量更充足,同时胶液在大梁区域移动的路径更短,可缩减一半,有效减少了大梁区域的灌注时间,进而减少了整体灌注时间,提高了灌注效率,并且由于胶液在大梁区域的移动路径变短,胶液流动时受到的阻力更小,气体位移量及阻力也更小,上方的抽气袋10不仅可持续抽出拉挤板3层间的气体,还可为大梁区域胶液的流动提供驱动力,有效降低灌注缺陷。
23.其中,导流网8对应覆盖在芯材5与大梁侧边衔接处的上方,可使胶液能够通过芯材5孔径或梁边缝隙进入,从而利于胶液进入大梁下方的下表面玻纤层1处及中下层拉挤板3的层间。将抽气袋10的两侧分别与两组导流网8搭接,抽气袋10抽气时可使导流网8上部分胶液横向流动,保障胶液可流动至大梁区域上方的部分上表面玻纤层6上,提升胶液在上表面玻纤层6上的流动速度,优选两个导流网8之间为间隔设置,以避免胶液在上表面玻纤层6上的流动速度超过胶液在拉挤板3层间的流动速度,保证拉挤板3之间有足够时间使胶液能够完全充满缝隙,减少包胶的风险。
24.同时由于本发明采用的为抽气袋10设置在大梁区域的上方,即采用的为上抽气方式,相比于下抽气的方式,本发明抽气方式符合气体向上流动的基本原则,灌注过程体系中的气体位移量小的同时可以使气体穿越难度更小,脱泡效果更好。并且本发明仅针对拉挤大梁区域的上流道结构进行优化及调整,在保证提升产品质量,加快灌注方法的前提下,不会对产品铺设难度,材料用量成本,产品生产人工时等方面造成影响。
25.两两所述拉挤板3的层间铺设有导流织物4,可避免拉挤板3层间贴合过紧,保障拉挤板3的层间存在供胶液流动的通道,为了避免导流织物4因宽度不够而导致拉挤板3层间胶液出现局部堵塞,及为了避免导流织物4宽度过宽而导致拉挤板3侧面无法与芯材5相贴的情况,如图1所示,所述导流织物4的宽度与对应层的拉挤板3宽度相同。
26.如图1所示,所述下表面玻纤层1与最下层拉挤板3之间设置有连续毡2,通过设置连续毡2,避免最下层拉挤板3与下表面玻纤层1贴合过紧而导致胶液沿拉挤板3与下表面玻纤层1之间流动,从而产生的无法浸润下表面玻纤层1的情况,优选所述连续毡2的宽度大于等于最下层拉挤板3的宽度,保障位于大梁区域下方的下表面玻纤层1表面能够使胶液有效流动。
27.两组所述导流网8对应覆盖两组芯材5与大梁侧边衔接处的一侧并横向延伸至拉挤板3的上方,保障导流网8可完全覆盖芯材5与大梁侧边的衔接处,以保障胶液可梁边缝隙进入,所述注胶管9设置在位于芯材5上方的导流网8区域上,即两组注胶管9分别位于大梁两侧外的上方,可以保证胶液在向大梁区域流动的有序性,即保障胶液从大梁两侧同时向大梁中心区域移动。其中,抽气袋10的长度与大梁长度大致相同,优选所述抽气袋10的宽度小于最上层拉挤板3的宽度,即抽气袋10的宽度小于大梁的宽度。
28.由于叶片模具存在弧度,为了便于铺设大梁区域的拉挤板3,如图1所示,每层所述
拉挤板3均由数个板材沿大梁的宽度方向铺设而成,前述拉挤板3的宽度为该层拉挤板3中数个板材在大梁宽度方向上的总宽度。
29.如图1所示,两组所述导流网8延伸至拉挤板3上方部分的宽度,分别小于最上层拉挤板3中位于最外两侧的板材的宽度,即导流网8不会盖住最外侧板材与相邻板材之间的衔接处,保障胶液的流动路径为从大梁侧面进入并向中部流动,避免出现胶液从最外侧板材与相邻板材之间的衔接处进入板材缝隙,而导致大梁最外侧板材之间的胶液及气体流动受阻而产生的灌注缺陷。
30.所述抽气袋10朝向真空袋膜的一面设置有观察窗,便于观察大梁区域中胶液的流向,并以此作为参考,来控制注胶管9的关管时间。
31.本发明还提供一种风电叶片一体灌注成型方法,该成型方法基于上述的成型系统,具体包括以下步骤:
32.s1、开启叶片模具保温程序,在叶片模具内铺设下表面玻纤层1,在下表面玻纤层1上铺设连续毡2,控制连续毡2的宽度大于或等于大梁区域宽度,在连续毡2上铺设由数层拉挤板3和导流织物4交错层铺形成的大梁,并在大梁的前缘侧和后缘侧分别铺设一组芯材5,并使芯材5与大梁侧边相贴,再铺设上表面玻纤层6;
33.s2、在两组芯材5上方分别各铺设一组导流网8,使两组导流网8对应覆盖两组芯材5与大梁侧边的衔接处,并使两组导流网8之间留有间隔,在两组导流网8上位于芯材5上方的区域各设置一根注胶管9,并在大梁上方区域铺设抽气袋10,使抽气袋10的两侧分别与两组导流网8的一侧搭接;
34.s3、使用真空袋膜将壳体密封,通过真空管将体系与真空装置连接,形成真空体系并满足要求后进行灌注。在灌注完成后,设定并开启叶片模具加热固化程序,使制品固化。
35.其中,所述s1中,先通过数层拉挤板3和导流织物4交错层铺并捆扎固定,形成大梁,再吊入叶片模具中铺设在连续毡2上。具体为,先将拉挤板按设计长度及数量切断成数个板材,按照设计弦向依次平行排放,同层板材铺设完毕后,铺设导流织物4,再继续下一层板材的铺设,所述导流织物4与层间拉挤板3幅宽相同。铺设完毕后使用捆扎带捆扎固定,再吊入叶片模具中。在s1之后、s2之前还包括上表面玻纤层6上铺设脱模布7。
36.本发明还提供一种风电叶片,该风电叶片采用上述的一体灌注成型方法制备,所制备的产品灌注缺陷少,产品质量更好。