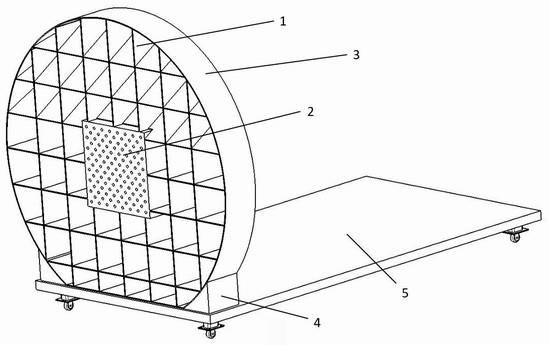
1.本发明涉及热压罐成型工艺过程,具体为一种热压罐内置温控格栅。
背景技术:2.热压罐成型工艺是将单层预浸料按预定方向铺叠成的复合材料毛胚、蜂窝夹芯结构及胶接结构等,用真空袋密封,靠放在模具上,在热压罐中经历升温加压、高温保温、降温泄压等过程,使复合材料固化成设计需要的形状的方法。作为这一工艺流程的主要生产设备,热压罐是一个带有加压、加热系统,能承受和调控温度、压力的大型专用压力容器,通常为一端封闭,另一端开门的近圆柱体,为航空热固性复合材料的压实、固化成型提供高温高压环境。使用热压罐工艺进行复合材料制件生产具有较强的灵活性,只要不超过其极限的最大温度和压力,便可以为多种材料、不同外形复合材料制件的固化过程进行加热、加压。
3.然而,现有技术中由于热压罐的罐体本身对温度和压力有较高的耐受要求,制造成本较为昂贵;此外,由于热压罐的尺寸较大及模具排布密度较大,受提供高温高压的方式影响,温度、压力变化响应不及时,气流阻碍较大,在靠后方的模具温度来不及变化,导致前后模具温差较大,温度控制精度差,导致这也成为这一工艺方法的瑕玷。
技术实现要素:4.针对现有热压罐工艺过程中存在的上述问题,本发明公开了一种热压罐内置温控格栅,其特征在于外形基于流体力学原理设计,对来流气体整流,以改善整个罐内气流流动,进而改善温度场的均匀性。
5.本发明技术方案:一种热压罐内置温控格栅,所述温控格栅包含格栅板、带小孔的挡板、保护外板。其中,所述格栅板中设有水平格栅、垂直格栅,所述格栅板外接于保护外板;所述保护外板与热压罐内部相连接。
6.进一步的,所述水平格栅和垂直格栅交错排布,将整个迎风截面分割成若干个小单元;所述格栅板上半部的倾斜板与水平方向成一定角度设置,其余格栅板为水平放置垂直于迎风面。
7.进一步的,所述保护外板的内部连接在格栅板外缘,外部连接热压罐内部,起包裹作用,防止格栅板边缘误伤。
8.更进一步的,所述格栅板中部设有带小孔的隔板,小孔的孔径不太大以至于失去阻挡作用,也不应小以使气体流动受阻;小孔均匀分布在所述隔板上。在本实施例提供的此种模型中小孔直径为30毫米,沿水平、竖直方向相邻的两小孔中心间距为120毫米。
9.作为本技术的一种优选实施方式,所述温控格栅还设有固定底座以及推车本体,所述固定底座上部与保护外板相固接,下部直接连接于推车车体,用于固定格栅板。
10.作为本技术的一种优选实施方式,所述格栅板上半部的倾斜板与水平方向成一定角度,在此实施方式中倾斜角度为30
°
,进入热压罐方式为随推车导轨进入罐体中。
11.采用此倾斜版整流的原因是流体有由偏离原本流动方向,改为随着凸出的物体表
面流动的倾向,当流体与它流过的物体表面之间存在表面摩擦时,只要曲率不大,流体就会顺着该物体表面流动。此格栅在热压罐工作前跟随摆放模具的推车进入热压罐,置于热压罐进风口以改善进入热压罐内部的气流,减小工装之间气流阻碍的影响,在罐盖的中心位置附近处,高温气体聚集,靠近此处的工装温度升高的速率总是过快,同样不利于整个罐内工装加热过程中的均匀性。为了尽可能地避免高温的过分集中,以提高罐内各处工装升温过程的均匀性和一致性,在格栅板的中心部位采用带小孔的挡板。其中,小孔的孔径不应太大以至于失去阻挡作用,也不应小以使气体流动受阻;小孔的排布错落有致,使得此处气流通过的流量比起无控制时更小,在迎风截面上尽可能均匀。
附图说明
12.图1为一种热压罐内置温控格栅及推车整体三维结构图;图2为一种热压罐内置温控格栅及推车整体三维结构正视图;图3为一种热压罐内置温控格栅在热压罐内放置整体三维结构图;图4为一种热压罐内置温控格栅在热压罐内放置整体三维结构正视图;图5为未添加内置温控格栅的流场示意图;图6为已添加内置温控格栅的流场示意图;图1中的标号名称:1.格栅板 2.带小孔的挡板 3.保护外板 4.固定底座 5.推车本体;图3中的标号名称:6.热压罐罐体 7.出风口 8.进风口。
具体实施方式
13.本发明公开了一种热压罐内置温控格栅。为使本发明的目的、技术方案及效果更加清晰和明确,本发明参照附图,对温控格栅的工作过程、原理及改善效果作进一步详细说明。应当理解,此处所描述的具体实施仅用以解释本发明,并不用于限定本发明。对于其他罐筒直径的热压罐,可以采用等比例缩放的方式对格栅尺寸进行调整。
14.实施例1如图1至图4所示,本实施例提供的一种热压罐用内置温控格栅,所述温控格栅包含格栅板1、带小孔的挡板2、保护外板3。其中,所述格栅板1中设有水平格栅、垂直格栅,所述格栅板外接于保护外板3;所述保护外板与热压罐内部相连接。
15.进一步的,所述水平格栅和垂直格栅交错排布,将整个迎风截面分割成若干个小单元;所述格栅板上半部的倾斜板与水平方向成角度设置,其余水平格栅为水平放置垂直于迎风面。
16.进一步的,所述保护外板的内部连接在格栅板外缘,外部连接热压罐内部,起包裹作用,防止格栅板边缘误伤。
17.更进一步的,所述格栅板中部设有带小孔的隔板,小孔的孔径不太大以至于失去阻挡作用,也不应小以使气体流动受阻;小孔均匀分布在所述隔板上。在本实施例提供的此种模型中小孔直径为30毫米,沿水平、竖直方向相邻的两小孔中心间距为120毫米。
18.作为本技术的一种优选实施方式,所述温控格栅还设有固定底座4以及推车本体5,所述固定底座4上部与保护外板相固接,下部直接连接于推车车体5,用于固定格栅板。
19.作为本技术的一种优选实施方式,所述格栅板上半部的倾斜板与水平方向成一定角度,在此实施方式中为30
°
,进入热压罐方式为随推车导轨进入罐体中。
20.热压罐成型工艺是将单层预浸料按预定方向铺叠成的复合材料毛胚、蜂窝夹芯结构及胶接结构等,用真空袋密封,靠放在模具上,在热压罐中经历升温加压、中高温保温、降温泄压等过程,使复合材料固化成设计需要的形状的方法。本发明在原有工艺上将格栅板置于进气口,可以改善气流组织,减小气流阻碍作用,帮助高温载热气体沿倾斜壁板方向向上流动,用均匀整流的流动取代经碰撞偏转流向的流动,从而消除或减弱该处位置上工装型板表面温度的波动,提高升温过程的稳定性。在这里,格栅板上侧的倾斜板与水平方向呈30
°
角。在罐盖的中心位置附近处,高温气体聚集,靠近此处的工装温度升高的速率总是过快,同样不利于整个罐内工装加热过程中的均匀性。本发明还基于计算流体力学软件,进行了仿真计算,并对格栅的整流效果进行了对比,具体如图5、图6所示。
21.图5为未添加温控格栅的内部流场示意图,图6为添加温控格栅的内部流场示意图。本发明实施案例中选取的热压罐模型罐筒直径3.6米,罐身长8米,有效容积81.4立方米,罐内外壁间进气道缝隙宽度60毫米,回风口边长2米,进气段长度取500毫米。常规热压罐中,由于工装之间存在气流阻碍,导致同个工装不同部位、不同工装之间存在较大温差,整个温度场均匀性较差。
22.该温控格栅采用如上述结构,格栅板中部设有带小孔的隔板,小孔的孔径不太大以至于失去阻挡作用,也不应小以使气体流动受阻;小孔均匀分布在所述隔板上。在本实施案例中,小孔直径为30毫米,沿水平、竖直方向相邻的两小孔中心间距为120毫米。
23.可以发现,位于罐头部的格栅板极大地改善了主要工作腔段内的气流向下倾斜聚集的趋势,除了在格栅板的下半部区域仍能保证气体的通过以外,上半部分的倾斜横板能够帮助将气体稳定地导向罐体上部区域,即在靠近入口位置装置的格栅板能够通过梳理和改善气流组织的流动,对温度场施加了被动的控制,从而提升了罐内垂直于流向方向上的流场及温度场的均匀性。