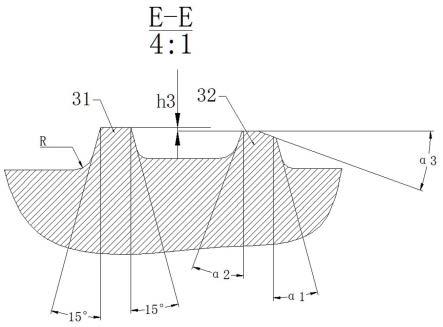
1.本发明涉及塑料挤出设备,具体涉及一种低烟无卤阻燃电缆料专用挤出螺杆。
背景技术:2.低烟无卤阻燃电缆料因其具有的无卤、阻燃特性已逐渐发展成为电线电缆行业主要的绝缘、护套材料之一;虽然,低烟无卤阻燃电缆料在电缆行业已经得到广泛的运用,但其加工性能与传统的pvc、pe材料有很大区别。
3.通常,低烟无卤阻燃聚烯烃的基材一般以乙烯和醋酸乙烯(eva)为主,再填充一部分阻燃剂、润滑剂、交联敏感剂等来降低发烟量,提高阻燃性能,提高挤出性能,可交联等。但由于其填充材料的比重较大,根据高分子材料厂家提供的数据,根据阻燃等级的不同,其阻燃剂的含量高达60%-70%。阻燃剂为不可融化的金属氢氧化物,熔融的粘度十分大,生产过程中,螺杆旋转产生的剪切力也相当大。材料分子间,材料与螺杆,材料与螺筒的摩擦比其材料相对严重,会产生大量的热,材料的机械性能下降,外观不良等不合格现象产生。这就决定了其螺杆、工艺的特殊要求。
4.螺杆为挤出机的主要部件。它直接关系到挤出机的应用范围和生产效率。为适应不同材料的加工需要,螺杆的形式有很多种。由于低烟无卤阻燃料采用大量的阻燃剂进行填充,挤出时其粘性较大,很容易造成聚合物的化学键断裂,产品的抗张强度和断裂伸长率等机械特性下降。一般挤出低烟无卤材料时,都需要使用无卤专用螺杆,这种常规型螺杆基本为剪切力较小的单螺纹型,压缩比一般在1.1-1.5左右;低烟无卤材料由于添加了大量的阻燃剂,熔料的流动性很差,容易受到高剪切产生自升温现,工艺温度难以控制并且挤出效率很低。
技术实现要素:5.本发明所要解决的技术问题在于提供一种低烟无卤阻燃电缆料专用挤出螺杆,挤出稳定性高、生产效率高。
6.为解决上述技术问题,本发明的低烟无卤阻燃电缆料专用挤出螺杆,包括进料段、塑化段、bm分离段、均化段,所述低烟无卤阻燃电缆料专用挤出螺杆上全程设置有主螺纹,其特征在于:在所述进料段,主螺纹螺距s1等于螺杆直径d;进料段的长度l1=5d;在所述塑化段,主螺纹螺距s2等于螺杆直径d,塑化段的长度l2=9d;在所述bm分离段,主螺纹螺距s31突变至1.5d;所述bm分离段上还设置有液相螺纹,所述液相螺纹的螺距s32>1.5d;所述液相螺纹的外径小于所述主螺纹的外径,其高度差h3为1mm~1.5mm;所述bm段的长度l3为7d~8d;在所述均化段,主螺纹螺距s4突变至1d;均化段的长度l4为3d~4d。
7.所述进料段的主螺纹螺槽等深,深度为h1;所述塑化段的主螺纹螺槽深度由h1渐变缩小至h2。
8.所述液相槽纹截面背推力面螺棱倾角由α1=15
°
渐变至α2=20
°
。
9.所述液相螺纹的螺棱表面沿其高度方向切削有α3=20
°
的倾角,所述倾角的起始端设置在液相螺纹的中线上、结束端设置在均化段一侧。
10.本发明根据低烟无卤阻燃电缆料的性质进行了优化设计,能够增大螺杆对熔料的推力、减小熔体剪切力和摩擦力从而减小挤出过程中电流过大和剪切热过大问题,极大地提高了挤出稳定性和生产效率。
附图说明
11.图1 是本发明的低烟无卤阻燃电缆料专用挤出螺杆的结构示意图;图2是所述螺杆的外径展开图;图3是所述螺杆的螺槽深度示意图图4是图2沿e-e线的剖视图。
具体实施方式
12.以下结合附图对本发明的具体实施方式作进一步说明。
13.如图1、图2、图3、图4可见,本发明的低烟无卤阻燃电缆料专用挤出螺杆,包括进料段1、塑化段2、bm分离段3、均化段4,所述低烟无卤阻燃电缆料专用挤出螺杆上全程设置有主螺纹31。
14.在所述进料段1,主螺纹31螺距s1等于螺杆直径d;进料段1的长度l1=5d;它的作用是一方面要把料斗来的塑料送到压缩段,另一方面是对塑料起预热的作用;在所述塑化段2,主螺纹螺距s2等于螺杆直径d,塑化段2的长度l2=9d;在所述bm分离段3,主螺纹31螺距s31突变至1.5d;所述bm分离段3上还设置有液相螺纹32,所述液相螺纹32的螺距s32>1.5d;所述液相螺纹32的外径小于所述主螺纹31的外径,其高度差为1mm~1.5mm;所述bm段3的长度l3为7d~8d;在所述均化段4,主螺纹螺距s4突变至1d;均化段4的长度l4为3d~4d。
15.作为实施方式之一,所述bm分离段3,主螺纹31螺距s31突变至1.5d,本段主螺距s31全程等距;所述液相螺纹32的螺距s32为1.52d~1.6d,本段液相螺纹全程等距;所述进料段1的主螺纹螺槽等深,深度为h1;所述塑化段2的主螺纹螺槽深度由h1渐变缩小至h2。
16.所述液相槽纹32截面背推力面螺棱倾角由α1=15
°
渐变至α2=20
°
。
17.所述液相螺纹32的螺棱表面沿其高度方向切削有α3=20
°
的倾角,所述倾角的起始端设置在液相螺纹32的中线上、结束端设置在均化段4一侧。
18.上述结构中,进料段1主螺纹31的螺距s1等于螺杆直径d,长度l1=5d,它的作用是一方面要把料斗来的塑料送到由塑化段2、bm分离段3组成的压缩段,另一方面是对塑料起预热的作用。
19.塑化段2的作用是接受进料段1输送过来的松散料,将它压实、软化,使包在料内的空气压回到进料段1,改善它的热传导性,使物料变得有适宜的粘度以吸收剪切的热量,这样就可以使全部物料均匀受热和混炼,塑料在这一段中开始软化,由固体逐渐变为熔融状态,成为连续的粘流体输送给bm分离段3,塑化段2主螺纹等距,主螺纹底径渐变缩小,在塑
化段2开始塑料由玻璃态变为高弹态,塑化段2结束部位已有少量的熔体料生成。
20.在熔料刚开始生成的部位设计一个bm分离段3,本段由两条螺距不同的螺纹组成,前一条即主螺纹31,其作为固相螺纹工作,后一条为液相螺纹32,这两条螺纹在螺杆中重迭而形成了作为熔融段的bm分离段3。
21.在bm分离段3上,每个主螺纹31的螺槽都被液相螺纹32划分为两个部分,由于液相螺棱螺纹外径比固相螺棱螺纹外径小,因此固相熔融而成的熔膜便越过了间隙进入了液相螺槽中,未熔固相仍留在固相螺槽内,这样就形成了固、液相的分离,此外由于主螺纹31螺距s31《液相螺纹32的螺距s32,因此在bm分离段3就形成了固相区间越来越窄,液相区间越来越宽的结构,这就适应了液相越来越多,固相越来越少以至消失的情况。
22.低烟无卤电缆料剪切热大,流动性差但比较容易塑化,bm分离段3主螺纹螺距s31——即熔体槽螺距——等于1.5*d,其大于塑化段2螺距,增大此段螺距一方面可以提高输送能力、提高挤出量、缩短物料在机筒内停留时间、减少剪切热,另一方面可以避免bm分离段3的液相螺纹开始部位固体槽容积突然减小从而引起堵塞或缺料的现象。
23.bm分离段3将固相与液相分离,可以实现低温挤出,提高挤出的平稳性,增加塑化能力,大幅提高挤出量,解决低烟无卤料多年来不能高速挤出的历史。
24.本低烟无卤阻燃电缆料专用挤出螺杆全程螺纹截面形状为梯形,进料段1、塑化段2、bm分离段3、均化段4螺纹断面上,螺棱与根径左右两侧有过渡圆角r,液相槽纹32截面背推力面螺棱倾角由α1=15
°
渐变至α2=20
°
,有利于熔融物料的流动,有较好的混合作用和均化作用;由于低烟无卤料流动性差,剪切热大,故将液相螺纹32的螺棱远端沿其高度方向切削为α3=20
°
的倾角,所述倾角的起始端设置在液相螺纹32的中线上、结束端设置在均化段4一侧。从而使液相螺纹32的螺棱有效宽度变窄,有利于减小或避免熔体料通过此间隙产生剪切热,实现稳定挤出。
25.均化段4是螺杆与机筒间产生压力最大的工作段,其压力来自螺杆的推力和网板等处的反作用力,是塑料“短兵相接”的直接地带,塑料在此阶段所受到的径向压力和轴向压力最大,均化段长度l4为3d~4d,长度较短但螺槽深度是普通低烟无卤深度的1.5倍左右,在满足熔料压实致密的基础上可适当减少物料的压力,可减小熔料在此段的压力波动,控制熔料在此段避免压力过大产生自升温现象,将完全塑化熔融的塑料定量、定压地由机头模具均匀地挤出。
26.作为实施方式之一,低烟无卤阻燃电缆料专用挤出螺杆全程长度l=1629mm;螺杆直径d=65mm。
27.1、进料段参数进料段1长度l1=325mm,主螺纹螺距s1=65mm,本段主螺纹全程等距;本段螺槽深度=9.2mm。
28.2、塑化段参数塑化段2长度l2=585 mm,主螺纹螺距s2=65mm;螺槽深度自9.2mm渐变缩小至6.5mm。
29.3、bm分离段参数bm分离段3长度l3=476mm;
此段开始处,主螺纹螺距s31突变至90mm,本段主螺纹全程等距;本段设置有液相螺纹32,所述液相螺纹32的螺距s32=99mm;本段主螺纹螺槽深度为6.5mm;所述液相螺纹32的外径小于所述主螺纹31的外径,其高度差h3为1mm~1.5mm;本段,所述液相槽纹32截面背推力面螺棱倾角由α1=15
°
渐变至α2=20
°
。
30.本段,所述液相螺纹32的螺棱表面沿其高度方向切削有α3=20
°
的倾角,所述倾角的起始端设置在液相螺纹32的中线上、结束端设置在均化段4一侧。
31.4、均化段参数均化段4长度l4=228mm,本段主螺纹螺距s1突变为65,全程等距;本段螺槽深度=6.5mm。
32.本发明的具体实施方式包括但不局限于上述实施例,在不背离本发明精神及其实质的情况下,熟悉本领域的技术人员可根据本发明作出各种相应的改变和变形,但仍然落入本发明的保护范围。