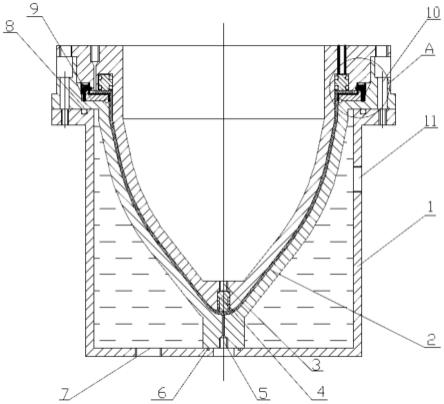
1.本发明属于飞行器领域,特别是涉及一种整流天线罩生产模具、天线罩的加工方法及整流天线罩。
背景技术:2.由于飞行器上的整流天线罩对结构和电磁性能要求较高,所以在制造该类产品时工艺相对复杂,对天线罩壁厚精度要求也较高。
3.原生产工艺每套模具每天只能生产一至两件该型天线罩,采用手工浸润树脂,树脂成份挥发对环境和健康带来不利影响,生产效率较低、成型产品壁厚不均匀,需要后期再加工处理,天线罩内、外表面存在大量的气泡和微孔,不仅产品质量一致性较差不能满足批产质量要求,同时不能满足大批量交付的周期要求;
4.传统的脱模手段,在凹模和成型后的产品存在脱模困难的问题。
技术实现要素:5.有鉴于此,本发明旨在提出一种整流天线罩生产模具、天线罩的加工方法及整流天线罩,以解决凹模与产品脱模困难的问题。
6.为实现上述目的,根据本发明的一个方面,提供一种整流天线罩生产模具,包括外壳、凹模、第二开孔、导热油入口、凹模脱模垫圈组件、导热油出口和凸模组件,所述外壳底壁上贯穿设置的开孔与凹模下端面上的第二开孔连通,所述外壳底壁和侧壁上分别开设导热油入口和导热油出口,所述外壳内设有凹模,所述凹模的下端面与外壳的底壁密封连接,所述外壳的上端面与凹模的凸缘下端面密封连接,所述凸模组件与凹模通过凹模脱模垫圈组件密封连接并在二者之间形成产品的成型腔体,所述凹模脱模垫圈组件用于脱模时与凸模组件配合使产品与凹模分离。
7.更进一步的,所述凸模组件包括第一开孔、脱模气塞、树脂接入孔、第三密封圈、凸模脱模垫圈、第三开孔、凸模本体和卡槽,所述第一开孔贯穿设置在凸模本体的底端,所述脱模气塞设置在第一开孔内,所述凸模本体的凸缘一侧贯穿设置有树脂接入孔,所述凸模本体凸缘另一侧贯穿设置有第三开孔,所述凸模脱模垫圈套接在凸模本体外壁与凸缘的转角处并通过第三密封圈进行密封,所述第三开孔的开口端朝向凸模脱模垫圈,所述卡槽设置在凸模本体的凸缘侧壁上,所述成型腔体与树脂接入孔的出口端连通。
8.更进一步的,所述凹模脱模垫圈组件包括卡合组件和凹模脱模垫圈本体,所述凹模脱模垫圈本体的侧壁上采用圆周均布的方式贯穿设置多个开槽,所述卡合组件设有多个,多个所述卡合组件一一对应的连接在开槽内;所述凹模脱模垫圈本体上侧与凸模本体密封连接,下侧与凹模密封连接。
9.更进一步的,所述卡合组件包括弹簧、锁止垫片、锁止垫片转轴和限位销,所述锁止垫片通过锁止垫片转轴转动连接在对应位置的所述开槽内,所述锁止垫片靠圆周外侧一端的上端面通过一个弹簧连接在开槽顶壁上,同侧下端面抵接在限位销的上端面上,所述
限位销卡合在凹模脱模垫圈本体上,密封成型时所述锁止垫片的另一端卡合在卡槽内。
10.更进一步的,所述凹模的下端面与外壳的底壁上端面通过第一密封圈密封连接,所述外壳的上端面与凹模的凸缘下端面通过第二密封圈密封连接。
11.根据本发明的另一个方面,提供利用上述整流天线罩生产模具加工整流天线罩的加工方法,包括以下步骤:
12.s1、在单独的凹模成型面上逐层铺设纤维布制作预制体;
13.s2、将所述凸模本体上提与所述凹模分离一定距离且二者的成型面均涂覆产品离模剂,在所述凹模成型面喷涂混有一定比例气相二氧化硅的复合材料层后对凹模进行加热使所述复合材料层进行快速固化;
14.s3、在固化的复合材料层上放置步骤s1中的所述预制体,将所述凸模本体下压至与凹模形成所述成型腔体且每个所述锁止垫片均卡合在卡槽内时,通过第一开孔、第二开孔和第三开孔对所述成型腔体抽真空处理,并将所述凹模预热;
15.s4、向所述成型腔体内注入树脂,树脂由上到下浸润所述预制体,当树脂从第二开孔流出时,停止加入树脂并对第二开孔进行锁止,后对凹模进行恒温加热,达到固化时间后对凹模进行冷却;
16.s5、提升凸模本体使其与凹模分离一段距离,分离过程中所述锁止垫片在弹簧和限位销的配合下使凹模脱模垫圈本体随凸模本体上升一端距离使凹模先与产品分离,所述锁止垫片从卡槽滑脱后凹模脱模垫圈本体落下,通过第一开孔和第三开孔通入气体使产品与凸模本体分离,完成脱模。
17.更进一步的,所述步骤s1中的每层纤维布之间喷胶。
18.更进一步的,所述步骤s3中的预热温度为50-60℃,抽真空后的所述成型腔体内真空负压压力为-0.095~-0.1mpa。
19.更进一步的,所述步骤s4中的树脂注入压力为0.2-0.3mpa,恒温加热温度为200℃,冷却温度为20-30℃。
20.根据发明的另一个方面,提供一种天线罩,它为三层结构,由外向内分别为外表面疏水耐老化层、外表面树脂导流纤维结构层和内表面树脂导流纤维层。
21.与现有技术相比,本发明的有益效果是:
22.1、通过高精度的凹凸双模具压制成型,保证了产品的尺寸精度;
23.2、预制体通过单独批量生产的方式,并利用真空辅助树脂传递,提高了生产效率;
24.3、提升凸模本体使其与凹模分离一段距离,分离过程中所述锁止垫片在弹簧和限位销的配合下使凹模脱模垫圈本体随凸模本体上升一端距离使凹模先与产品分离,当分离距离继续增大时所述锁止垫片从卡槽滑脱后凹模脱模垫圈本体落下;
25.4、利用压力和脱模气塞的辅助减小受力面积,便于凸模本体与产品进行分离且不易发生坏损;
26.5、精准的控制了树脂的固化温度和时间,保证了成型产品的强度和刚度和快速成型。
附图说明
27.构成本发明的一部分的附图用来提供对本发明的进一步理解,本发明的示意性实
施例及其说明用于解释本发明,并不构成对本发明的不当限定。在附图中:
28.图1为本发明所述的一种整流天线罩生产模具的结构示意图;
29.图2为本发明所述的图1的a部分局部放大示意图;
30.图3为本发明所述的凸模本体结构示意图;
31.图4为本发明所述的整流罩的结构示意图;
32.图5为本发明所述的凸模本体与产品的脱模示意图;
33.图6为本发明所述的凸模本体与产品脱模后凹模脱模垫圈组件的状态图。
34.外壳1;凹模2;第一开孔3;脱模气塞4;第二开孔5;第一密封圈6;导热油入口7;第二密封圈8;凹模脱模垫圈组件9;连接孔10;导热油出口11;弹簧12;锁止垫片13;锁止垫片转轴14;限位销15;凹模脱模垫圈本体16;压机设备连接孔17;树脂接入孔18;第三密封圈19;凸模脱模垫圈20;第三开孔21;凸模本体22;卡槽23。
具体实施方式
35.下面将结合本发明实施例中的附图,对本发明实施例中的技术方案进行清楚、完整地阐述。需要说明的是,在不冲突的情况下,本发明中的实施例及实施例中的特征可以相互组合,所描述的实施例仅仅是本发明一部分实施例,而不是全部的实施例。
36.参见附图说明本实施方式,根据本发明的一个方面,提供一种整流天线罩生产模具,包括外壳1、凹模2、第二开孔5、导热油入口7、凹模脱模垫圈组件9、导热油出口11和凸模组件,所述外壳1底壁上贯穿设置的开孔与凹模2下端面上的第二开孔5连通,所述外壳1底壁和侧壁上分别开设导热油入口7和导热油出口11,所述外壳1内设有凹模2,所述凹模2的下端面与外壳1的底壁密封连接,所述外壳1的上端面与凹模2的凸缘下端面密封连接,所述凸模组件与凹模2通过凹模脱模垫圈组件9密封连接并在二者之间形成产品的成型腔体,所述凹模脱模垫圈组件9用于脱模时与凸模组件配合使产品与凹模2分离,所述凹模2的下端面与外壳1的底壁上端面通过第一密封圈6密封连接,所述外壳1的上端面与凹模2的凸缘下端面通过第二密封圈8密封连接。
37.在本实施例中,所述凸模组件包括第一开孔3、脱模气塞4、树脂接入孔18、第三密封圈19、凸模脱模垫圈20、第三开孔21、凸模本体22和卡槽23,所述第一开孔3贯穿设置在凸模本体22的底端,所述脱模气塞4设置在第一开孔3内,所述凸模本体22的凸缘一侧贯穿设置有树脂接入孔18,所述凸模本体22凸缘另一侧贯穿设置有第三开孔21,所述凸模脱模垫圈20套接在凸模本体22外壁与凸缘的转角处并通过第三密封圈19进行密封,所述第三开孔21的开口端朝向凸模脱模垫圈20,所述卡槽23设置在凸模本体22的凸缘侧壁上,所述成型腔体与树脂接入孔18的出口端连通。
38.在本实施例中,所述凹模脱模垫圈组件9包括卡合组件和凹模脱模垫圈本体16,所述凹模脱模垫圈本体16的侧壁上采用圆周均布的方式贯穿设置多个开槽,所述卡合组件设有多个,多个所述卡合组件一一对应的连接在开槽内;所述凹模脱模垫圈本体16上侧与凸模本体22密封连接,下侧与凹模2密封连接。
39.在本实施例中,所述卡合组件包括弹簧12、锁止垫片13、锁止垫片转轴14和限位销15,所述锁止垫片13通过锁止垫片转轴14转动连接在对应位置的所述开槽内,所述锁止垫片13靠圆周外侧一端的上端面通过一个弹簧12连接在开槽顶壁上,同侧下端面抵接在限位
销15的上端面上,所述限位销15卡合在凹模脱模垫圈本体16上,密封成型时所述锁止垫片13的另一端卡合在卡槽23内。
40.所述凸模本体22和凹模2的成型面均为形面误差
±
0.025mm,表面粗糙等级为a级光亮面。
41.根据本发明的另一个方面,一种利用上述整流天线罩生产模具加工整流天线罩的加工方法,包括以下步骤:
42.s1、在单独的凹模2成型面上逐层铺设纤维布制作预制体,每层纤维布之间喷胶;
43.s2、通过压机设备连接孔17将凸模本体22连接到压机设备上,然后通过压机设备将所述凸模本体22上提与所述凹模2分离一定距离且二者的成型面均涂覆产品离模剂,在所述凹模2成型面喷涂混有一定比例气相二氧化硅的复合材料层后对凹模2进行加热使所述复合材料层进行快速固化,加热方式为从导热油入口7导入热油;
44.s3、在固化的复合材料层上放置步骤s1中的所述预制体,将所述凸模本体22下压至与凹模2形成所述成型腔体且每个所述锁止垫片13均卡合在卡槽23内时,通过第一开孔3、第二开孔5和第三开孔21对所述成型腔体抽真空处理,抽真空后的所述成型腔体内真空负压压力为-0.095~-0.1mpa,并将所述凹模2预热,预热方式为从导热油入口7导入热油,热油温度为50-60℃;
45.s4、从树脂接入孔18向所述成型腔体内注入树脂,注入压力为0.2-0.3mpa,树脂由上到下浸润所述预制体,当树脂从第二开孔5流出时,停止加入树脂并对第二开孔5进行锁止,后对凹模2进行恒温加热,恒温加热温度为200℃,同样通过热油来实现,达到固化时间后对凹模2进行冷却,冷却温度为20-30℃;
46.s5、提升凸模本体22使其与凹模2分离一段距离,分离过程中所述锁止垫片13在弹簧12和限位销15的配合下使凹模脱模垫圈本体16随凸模本体22上升一端距离使凹模2先与产品分离,当分离距离大于1.5mm时所述锁止垫片13从卡槽23滑脱后凹模脱模垫圈本体16落下,通过第一开孔3和第三开孔21通入0.7mpa气体使产品与凸模本体22分离,完成脱模。
47.上述步骤中,对于热油的温度改变,均通过模温机来实现。
48.在本实施例中,所述天线罩为三层结构,由外向内分别为外表面疏水耐老化层、外表面树脂导流纤维结构层和内表面树脂导流纤维层,所述的疏水耐老化层环氧树脂胶衣和2%质量分数气相二氧化硅的复合材料层,厚度均匀且厚度为0.15-0.2mm,是不含纤维的富树脂层,环氧树脂胶衣层自身材料耐腐蚀性能优良,而均匀混入气相二氧化硅结构剖面类似砖墙结构,形成了多层玻璃鳞片的隔离层,极大的提高了天线罩外壳体的耐化学腐蚀性,同时该致密层具有很好的疏水能力;外表面树脂导流纤维厚度均匀且厚度为0.2-0.25mm,采用长纤维毡层和高温固化的环氧树脂基体成型,该层可使成型表面降低孔隙率更加密实,同时对耐老化层和后续的外表面隔离层具有良好的粘接过度作用,利于树脂导流和浸润结构纤维布层;结构层采用s玻璃高强纤维织物和高温固化的环氧树脂基体成型,结构层厚度根据电性能和结构优化设计厚度为2-5mm,s玻璃高强纤维和高温固化的环氧树脂基体成型材料不仅结构强度满足设计要求,同时该材料具有非常优良的电磁透波性能,可以满足天线工作的性能指标要求;所述的内表面树脂导流纤维层所用的材料和厚度均为一致对称结构,如此设计能够防止结构层两侧所用材料性质不同使该夹层结构内存在不同内应力,造成产品出现弯曲变形现象,同时工艺成型更利于高效浸润结构纤维布层。
49.以上公开的本发明实施例只是用于帮助阐述本发明。实施例并没有详尽叙述所有的细节,也不限制该发明仅为所述的具体实施方式。根据本说明书的内容,可作很多的修改和变化。本说明书选取并具体描述这些实施例,是为了更好地解释本发明的原理和实际应用,从而使所属技术领域技术人员能很好地理解和利用本发明。