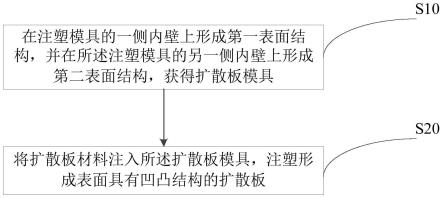
1.本技术涉及扩散板制造技术领域,尤其涉及一种扩散板模具及扩散板。
背景技术:2.相关技术中,扩散板的制作主要通过以下步骤完成:(1)混料;(2)配比;(3)混合搅拌;(4)热熔挤出,通过模具挤出冷却成型;(5)辊轮压膜;(6)覆膜,静电消除;(7)裁切加工;(8)清洗干燥;(9)下料。
3.但是,(7)所涉及的裁切加工技术只能加工平面规则结构,无法通过裁切加工技术加工形成平面凹凸结构。
4.申请内容
5.本技术的主要目的在于提供一种扩散板模具及扩散板,旨在解决使用裁切技术无法在扩散板表面形成凹凸结构的技术问题。
6.为实现上述目的,本技术提供一种扩散板模具,包括:
7.模具本体,所述模具本体内具有一注塑空间,且所述注塑空间具有相对的第一内侧壁和第二内侧壁;
8.其中,所述第一内侧壁具有第一表面结构,所述第一表面结构与所述扩散板的一侧表面相匹配,所述第二内侧壁具有第二表面结构,所述第二表面结构与所述扩散板的另一侧表面相匹配。
9.在一实施例中,所述第一表面结构为与晒纹对应的凹凸结构。
10.在一实施例中,所述第一表面结构通过化学腐蚀得到。
11.在一实施例中,所述第二表面结构为与网点和/或微结构对应的凹凸结构。
12.在一实施例中,所述第二表面结构通过化学腐蚀得到。
13.在一实施例中,所述第二表面结构通过激光加工得到。
14.在一实施例中,所述第一内侧壁和所述第二内侧壁均为平面。
15.在一实施例中,所述第一内侧壁和所述第二内侧壁均为曲面。
16.在一实施例中,所述扩散板模具尺寸不大于55inch。
17.本技术实施例提出的一种扩散板模具,通过模具本体,所述模具本体内具有一注塑空间,且所述注塑空间具有相对的第一内侧壁和第二内侧壁;其中,所述第一内侧壁具有第一表面结构,所述第一表面结构与所述扩散板的一侧表面相匹配,所述第二内侧壁具有第二表面结构,所述第二表面结构与所述扩散板的另一侧表面相匹配。由此,本技术通过在注塑模具两内侧壁上分别形成第一表面结构与第二表面结构,在注入扩散板材料且待其冷却后,便可将第一表面结构和第二表面结构转印到扩散板的表面,获得表面具有凹凸结构的扩散板,解决了无法通过扩散板裁切技术加工形成表面有凹凸结构的问题,避免裁切技术使扩散板出现毛边和异物等外观缺陷,同时,提高了雾度和透过率,从而减少了对显示光学和亮度的影响,除此之外,注塑扩散板还可以通过调整第二表面的网点结构和密度改善均匀性和led上方光斑等问题。
附图说明
18.图1为本技术扩散板制造方法第一实施例的流程示意图;
19.图2为本技术扩散板制造方法第二实施例的流程示意图
20.图3为本技术扩散板模具第一表面结构图;
21.图4为本技术扩散板模具第二表面结构图;
22.图5为本技术扩散板模具第一表面结构对应的晒纹图;
23.图6为本技术扩散板模具第二表面结构对应的网点和/或者微结构图。
24.本技术目的的实现、功能特点及优点将结合实施例,参照附图做进一步说明。
具体实施方式
25.应当理解,此处所描述的具体实施例仅仅用以解释本技术,并不用于限定本技术。
26.由于现有技术将扩散板制作原料注入模具,对其进行挤压成型后,还需要对其进行裁切加工,以获得所需要的外观形状。但是现有技术使用裁切形成的扩散板存在以下缺陷:
27.1、现有扩散板相对雾度和透过率低,对显示光学和亮度有影响,需提高电流使用,更耗电;
28.2、现有扩散板热收缩和热变形量大,在高温可靠性过程中不仅会使得扩散板的尺寸公差平面度大,还会影响光学显示;
29.3、现有扩散板采用裁切技术,只能加工平面规则架构,无法形成表面有凹凸结构或曲面结构的扩散板;
30.4、现有扩散板裁切技术易出现毛边,异物,黑白点和加工划伤等外观缺陷。
31.5、裁切导光板使用挤压成型的板材,原材料和表面结构已定形,定版后续不能根据个案要求调整光学。
32.本技术提供一种解决方案,模具本体,所述模具本体内具有一注塑空间,且所述注塑空间具有相对的第一内侧壁和第二内侧壁;其中,所述第一内侧壁具有第一表面结构,所述第一表面结构与所述扩散板的一侧表面相匹配,所述第二内侧壁具有第二表面结构,所述第二表面结构与所述扩散板的另一侧表面相匹配。由此,本技术通过在注塑模具两内侧壁上分别形成第一表面结构与第二表面结构,在注入扩散板材料且待其冷却后,便可将第一表面结构和第二表面结构转印到扩散板的表面,获得表面具有凹凸结构的扩散板,具有以下有益效果:
33.1、将扩散板材料注入扩散板模具内,可以形成表面具有凹凸结构或者曲面结构的扩散板;
34.2、扩散板材料注入扩散板模具内后,扩散板可以通过注塑一体成型,不需要再使用裁切技术再对其进行加工,从而可以避免因裁切技术给扩散板带来毛边,异物,黑白点和划伤等外观缺陷;
35.3、采用高雾高亮高流动性塑胶粒子,提高了雾度和透过率,减少了对光学显示和亮度的影响;
36.4、可以通过调整第二表面的网点结构和密度改善均匀性和led上方光斑等问题,可以降低led成本;
37.5、采用耐高温的硅系扩散剂,扩散剂在成型后不易发黄。
38.下面结合一些具体实施例进一步阐述本技术的发明构思。
39.请参阅图1,本发明实施例中,一种扩散板制造方法,包括以下步骤:
40.步骤s10、在注塑模具的一侧内侧壁上形成第一表面结构,并在所述注塑模具的另一侧内侧壁上形成第二表面结构,获得扩散板模具。
41.具体的,扩散板模具包括:模具本体,所述模具本体内具有一注塑空间,且所述注塑空间具有相对的第一内侧壁和第二内侧壁;其中,所述第一内侧壁具有第一表面结构,所述第一表面结构与所述扩散板的一侧表面相匹配,所述第二内侧壁具有第二表面结构,所述第二表面结构与所述扩散板的另一侧表面相匹配。
42.其中,扩散板模具可以是热塑性注塑模具、热固性塑料注塑模具、移动性注塑模具、固定式注塑模具等。参阅图3和图4,扩散板模具包括上模具10和下模具20,上模具10的下表面上具有一第一凹槽,下模具20的上表面上具有一第二凹槽。上模具10和下模具20合模后形成一模具本体,两个凹槽合模后即形成注塑空间。可以理解的,第一凹槽的槽顶壁上具有第一表面结构,第二凹槽的槽底壁上具有第二表面结构。
43.在本实施例中,第一表面结构与第二表面结构是指根据需要而在注塑模具两侧壁内形成的凹凸结构,因此获得两侧壁内具有凹凸结构的扩散板模具。扩散板模具两侧壁内的凹凸结构可以是晒纹、网点或者微结构对应的表面结构。如扩散板背面应当形成一微凸结构,则应当在下模具20的第二凹槽的槽底壁上形成与微凸结构对应的第二表面结构。
44.其中,可以通过化学腐蚀或者激光加工在注塑模具两内侧壁形成凹凸结构。如,使用硝酸、硫酸等具有腐蚀功能的化学物质,首先在注塑模具内侧壁确定凹凸结构的位置,再使用硝酸、硫酸等化学物质腐蚀内侧壁表面,从而获得扩散板模具。
45.步骤s20、将扩散板材料注入所述扩散板模具,注塑形成表面具有凹凸结构的扩散板。
46.本实施例中,通过在注塑模具的一侧内侧壁上形成第一表面结构,并在所述注塑模具的另一侧内侧壁上形成第二表面结构,获得扩散板模具;将扩散板材料注入所述扩散板模具,使得第一表面结构和第二表面结构转印到扩散板上,注塑形成表面具有凹凸结构的扩散板,从而可以获得表面具有凹凸结构的扩散板,解决了无法通过扩散板裁切技术加工形成表面有凹凸结构的问题,避免了因使用扩散裁切技术带来的毛边和异物等外观缺陷,提高了扩散板相对雾度和透过率,减少了对显示光学和亮度的影响,同时也减少了对电的消耗。
47.作为一个实施例中,在具体实现中,将扩散板材料注入所述扩散板模具,以质量分数计,所述扩散板材料包括:
48.95%-99.9%的高雾高亮高流动性塑胶粒子以及0.1%-5%扩散剂。
49.其中塑胶粒子是指塑胶以半成品形态进行储存、运输和加工成型的原料,属于高分子材料类别。雾度是指透明或半透明材料的内部或表面由于光漫射造成的云雾状或混浊的外观,以漫射的光通量与透过材料的光通量之比的百分率表示。高亮是指扩散般的透光率,即透过试样的光通量(luminous flux)和射到试样上的光通量之比,用百分数表示。高流动性是指熔液流动指数(melt flow rate,mfr),用于表示塑胶材料加工时的流动性指数,即先让塑料粒在一定时间(10分钟)内、一定温度及压力(各种材料标准不同)下,融化成
塑料流体,然后通过一直径为2.1mm圆管所流出的克(g)数。其值越大,表示该塑胶材料的加工流动性越佳,反之则越差。
50.在本实施例中扩散板材料为95%-99.9%的高雾高亮高流动性塑胶粒子以及0.1%-5%的扩散剂,其中高雾高亮高流动性塑胶粒子的熔体流动速率大于或者等于40cm3/min,因此,其1mm厚度光学性能为:雾度99.9%,透光率30%-85%,光扩散度50%-80%,并且所采用的扩散剂为耐高温的硅系扩散剂,从而使扩散板成型之后不易发黄。因此,本技术通过在注塑模具的一侧内侧壁上形成第一表面结构,并在所述注塑模具的另一侧内侧壁上形成第二表面结构,获得扩散板模具;将扩散板材料注入所述扩散板模具,可以获得55inch以下尺寸的扩散板,通过注塑成型,导光板分子结构更加紧密,其收缩性更小,防止高温对光学显示产生影响。并且通过扩散板模具,可以使扩散板表面结构达到多样化、形状异形化,避免了因使用扩散裁切技术带来的毛边和异物等外观缺陷。
51.进一步的,基于上述第一实施例,本技术提供扩散板制造方法第二实施例,参照图2,图2示出了扩散板制造方法第二实施例的流程示意图。
52.本实施例中,步骤s10,包括:
53.步骤s101、在注塑模具的一侧内侧壁上形成与晒纹对应的所述第一表面结构。
54.参阅图5,在本实施例中,晒纹是指模具表面处理的工艺,可以增进塑料零件的外观质感,使产品呈现多变化或全新的设计,主要是采用具有腐蚀性的化学药水,如硝酸、硫酸等,与模具产生化学反应,并控制反应过程来得到各种各样的效果。获取晒纹的主要流程为:1、清洗模具,即清洗模具油污;2、检测模具表面;3、保护无需晒纹区,不被药水腐蚀;4、采用dtt纹纸,将抗腐蚀的蜡转印到模具表面,形成花纹;5、配置药水,腐蚀纹区,在模具表面显露花纹;6、调整模具表面光泽。通过上述的操作步骤,便可获得内侧壁具有晒纹的扩散板模具,将表面结构为晒纹的内侧壁作为第一表面结构,并且第一表面结构与扩散板的一侧表面相匹配。
55.步骤s102、在注塑模具的所述另一侧内侧壁上形成与网点和/或微结构对应的所述第二表面结构。
56.参阅图6,网点和/或微结构是指为提高扩散板光源的的扩散效果,而对扩散板进行的粗糙化处理,从而解决灯眼和暗格现象,提升均匀性。采用激光加工在注塑模具的另一侧内侧壁上形成网点和/或微结构的主要流程为:将镜面磨仁放至超精密激光打点机,将预先设计完成的网点程序输入超精密激光打点机,调整合适的打点参数,对镜面模仁进行插射打点;通过激光聚焦,扫射镜面模仁,产生的高温,在镜面模仁上,按预先设计的网点排布进行加工,形成一个个排布有序的半圆球形凹坑。通过上述的操作步骤,便可获得另一侧内侧壁具有网点和/或微结构的扩散板模具,将表面结构为网点和/或微结构的内侧壁作为第二表面结构,并且第二表面结构与扩散板的另一侧表面相匹配。
57.在本实施例中,通过化学腐蚀或者激光加工在扩散板内侧壁分别形成具有晒纹的第一表面结构与具有网点和/或微结构的的第二表面结构,从而获得尺寸不大于55inch的扩散板模具,在注塑模具本体内具有注塑空间,且注塑空间内有相对的第一内侧壁与第二内侧壁,第一内侧壁具有第一表面结构,所述第一表面结构与所述扩散板的一侧表面相匹配,所述第二内侧壁具有第二表面结构,所述第二表面结构与所述扩散板的另一侧表面相匹配,且第一内侧壁和第二内侧壁均为平面或曲面。在获得扩散板模具后,将扩散板材料注
入扩散板模具,从而可以获得表面具有凹凸结构的扩散板,解决了无法通过扩散板裁切技术加工形成表面有凹凸结构的问题,避免了因使用扩散裁切技术带来的毛边和异物等外观缺陷,提高了扩散板相对雾度和透过率,减少了对显示光学和亮度的影响,同时也减少了对电的消耗。
58.基于同一发明构思,本技术还提供了一种扩散板,采用如上所述扩散板注塑成型的方法得到。
59.在一实施例中,所述扩散板的尺寸不大于55inch。
60.本实施例中,通过扩散板模具注塑成型的扩散板尺寸在55inch以下,也即不大于140厘米,可以根据需要选择对应尺寸的扩散板,避免了因成型的扩散板尺寸过大,需对其进行分割,并且对于分割后的边角,还需进行二次加工,会存在毛刺和异物等外观缺陷。
61.以上仅为本技术的优选实施例,并非因此限制本技术的专利范围,凡是利用本技术说明书及附图内容所作的等效结构或等效流程变换,或直接或间接运用在其他相关的技术领域,均同理包括在本技术的专利保护范围内。