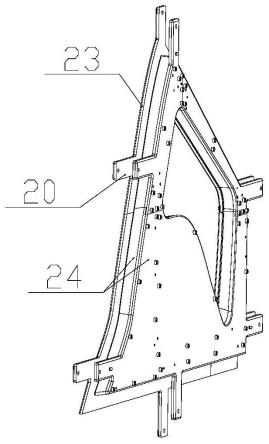
多隔框碳纤维复合材料s型进气道整体共固化成型工艺
技术领域
1.本发明涉及多隔框碳纤维复合材料s型进气道整体共固化成型工艺,属于复合材料成型技术领域。
背景技术:2.随着时代的快速发展,复合材料已然成为新型材料领域的研究热点之一。与传统材料相比,复合材料的比强度比模量更高,同时具有很好的抗疲劳、抗腐蚀以及耐高温性能,因此,在航空航天领域得到了广泛的应用。发动机是飞行器的核心部件,其性能对飞行器的飞行包线和飞行效能有着直接影响,而进气道作为位于整个推进系统最上游的重要气动部件,其气动性能和结构强度对整个飞机的效率和作战能力都有重要影响。现代军用战斗机就采用复合材料制造进气道,所得结构,可以增加构件设计的灵活性,充分利用复合材料的材料各向异性特性,为结构提供更高的力学性能,同时达到减重的目的。
3.碳纤维复合材料进气道,为层压板结构,在进行装配时,还需要与隔框,加强筋等进行连接。复合材料结构的连接形式主要有3种:胶接连接、机械连接和混合连接。不同连接形式存在不同的问题,例如胶接连接强度分散性大,较难传递大的载荷,胶接性能收环境影响大,存在老化问题;机械连接孔周应力集中,增重,结构的气动特性差与复材接触产生电偶腐蚀;混合连接重量及成本的增长幅度都非常大。复合材料结构不仅要承受复杂载荷,而且还要承受严苛环境因素考验,这些均可导致复合材料结构的性能变化或被破坏。连接结构是复合材料结构中最容易出现损伤或失效的区域,已有研究表明,近80%的结构失效是由连接结构造成的,复合材料连接结构的设计是制约复合材料在飞行器结构中进一步应用的瓶颈。同时,此种分体式结构,已不能现代战斗机的结构布局。
4.本发明提供了一种多隔框碳纤维复合材料s型进气道整体共固化成型工艺,仅用一次固化过程既能完成多个隔框与进气道的一体共固化成型。不需进行后续的连接工作,避免了隔框与进气道连接中各种问题与风险,也减少了装配周期及成本。
技术实现要素:5.多隔框碳纤维复合材料s型进气道由筒段蒙皮及若干隔框整体共固化成型,本发明专利核心技术是研制铺叠及固化组合工装,利用工装在s型进气道隔框两面交替铺叠,实现碳纤维复合材料多个隔框铺层连续,与进气道筒段一体共固化成型。
6.本发明的技术方案如下:
7.多隔框碳纤维复合材料s型进气道整体共固化成型工艺,步骤如下:
8.步骤1,进气道筒段蒙皮按照设计要求铺叠到预定层数,保持未固化状态。将进气道筒段蒙皮及其铺叠工装整体转移到隔框成型模型架上。
9.步骤2,在隔框成型模型架上安装隔框铺叠工装。铺叠筒段蒙皮边缘及隔框的1/2铺层,铺叠完成后,将隔框铺叠工装移下。
10.所述的隔框铺叠工装包括面板28、支臂20和销孔29,面板28根据筒段分离面分瓣,
每瓣面板28设有支臂20且为整体制造。销孔3开设在支臂20上,用于与隔框成型模型架连接。
11.步骤3,将隔框固化工装组装到隔框成型模型架上。组合隔框固化工装时,隔框固化工装与进气道筒段并非完全贴合,预留5mm组合间隙,该间隙需用多层呈直角梯形的硅橡胶填实,利用橡胶高温体积膨胀,保证隔框固化工装底部的蒙皮在固化时获得足够的压力,保证制件内部质量的同时避免在制件表面成压痕。
12.隔框固化工装24包括隔框固化模25、减重凹槽26、螺栓孔30、背板27、支臂20和销孔29。隔框固化模25侧边高度为隔框翻边宽度基础上增加20mm余量,外形面为隔框型面。隔框固化模25根据筒段分离面及单瓣重量进行分瓣,各分瓣间设计不同角度的脱模楔角,用以保证工装在固化后能够顺利脱模,不会损伤制件。隔框固化模25预留足够宽度及强度进行成型及连接后,非工作面中间部位抠减重凹槽26,目的为工装减重,以满足工装整体使用时的精准度及可操作性。每一分瓣工装上预留两个螺栓孔30,用于脱模时,与起销器连接。背板27上配备若干螺栓孔30,用于将隔框成型模组合成大块,保证其使用时的精度及稳定性。每块根据其连接工装的重量配备若干支臂20,其上配备销孔29,用于与隔框成型模型架连接,保证各个隔框的位置精度。
13.步骤4,将超过隔框固化模25高度的预浸料沿其成型模型面,压实到其侧面上。在隔框坯料与筒段蒙皮所成的r角位置,填充0
°
纤维捻条,避免该区域出现空腔。
14.步骤5,在步骤4铺叠的坯料上铺叠隔框剩下的1/2,相邻隔框的1/2及其两隔框间筒段的铺层。铺叠层数达到设计要求后,将隔框铺叠工装卸下,安装已铺叠1/2隔框的隔框固化工装及后续相邻隔框的隔框铺叠工装。之后逐次进行铺叠,直至完成所有隔框及筒段蒙皮的铺叠。
15.步骤6,利用真空袋进行真空封装时,分区进行封装,以隔框作为分界面,每段真空袋在此位置用密封胶条进行拼接密封。
16.本发明的有益效果:本发明创新性的提供了一种多隔框碳纤维复合材料s型进气道整体共固化成型工艺,环形隔框为整体成型,不需分块固化后再进行组装;多个隔框可实现铺层连续;在隔框成型模与筒段蒙皮间预留5mm余量,用于填充硅橡胶,利用其热膨胀进行隔框成型膜底部蒙皮;多层硅橡胶采用直角梯形结构堆叠,与隔框接触一侧为直角,另一侧为斜角,同时对最底层硅橡胶导30
°
斜角,避免硅橡胶在制件上留下压痕。仅用一次固化过程即能完成多个隔框与进气道的一体共固化成型,同时还能实现多个隔框铺层连续。可用于j型构型的隔框、t型构型的隔框、不同高度的隔框与筒段结构的共固化及胶接共固化。大幅提升了结构性能及先进性。不需进行后期的连接工作,避免了隔框与进气道连接中各种问题与风险,也减少了装配周期及成本。
附图说明
17.图1为隔框成型模型架示意图;
18.图2为基座部分示意图;
19.图3为前端支撑定位架示意图;
20.图4为左右限位座装置示意图;
21.图5为前后限位板示意图;
22.图6为后端支撑定位架示意图;
23.图7为上框架部分示意图;
24.图8为隔框成型模示意图;
25.图9为隔框固化工装示意图;
26.图10为隔框铺叠模示意图。
27.图中:1.基座;2.上框架;3.隔框成型模;4.底座;5.前端支撑定位架;6.后端支撑定位架;7.立柱;8.左右限位座;9.前后限位座;10.前支撑台;11.卡箍;12.长销;13.底座台;14.限位块;15.限位板;16.圆形限位环;17.限位卡箍;18.后支撑台;19.连接平台;20.支臂;21.方钢;22.梁;23.隔框铺叠工装;24.隔框固化工装;25.隔框固化模;26.减重凹槽;27.背板;28.面板;29.销孔;30.螺栓孔。
具体实施方式
28.以下根据附图和实施例对本发明的技术方案进行进一步说明。
29.1.铺叠进气道蒙皮至预设层数,可选用手工铺叠或自动铺丝。自动铺丝更优。
30.2.工装准备。将隔框铺叠模和隔框固化工装用清洁剂擦拭,直至用干净的白色抹布擦拭,其上无污物。清理完毕后,在隔框固化模25与预浸料接触位置涂刷脱模剂。铺叠模则严禁接触脱模剂,防止污染预浸料坯料。
31.3.工装组合。将完成铺叠的进气道蒙皮及其工装,整体转移到隔框成型工装型架上。将最左侧隔框铺叠模由支臂20上的销孔29组合到型架上。同时,用背板27与隔框固化模25连接成隔框固化工装。
32.4.裁剪预浸料。因隔框各处距离筒段高度不同,进行高度统计,根据不同高度进行分组。分组依据:隔框距筒段最短距离为a,各处距离为s,n为分组系数。
33.n=(s-a)/200,根据分组系数进行分组,n≤1的区域为一组,1<n≤2为一组,
34.2<n≤3为一组,以此类推。每组预浸料长度为a+200n,200mm宽,长度长度方向为0
°
纤维方向。
35.5.隔框铺叠。铺叠时,以筒段铺层坐标系为基准,每块预浸料裁片先铺叠筒段部分,沿纤维方向逐渐压实,直到铺叠到隔框位置。当前层筒段区域已被预浸料铺叠满后,隔框铺叠工装上,无预浸料的区域,需用预浸料单向带进行补铺。重复铺叠,直至隔框铺叠层数的1/2。
36.6.工装更换。将隔框铺叠模卸下,在要安装隔框固化工装的一侧,沿隔框的根部,呈直角梯形放置3层硅橡胶,接触隔框一侧为直角,紧贴隔框。最上层硅橡胶宽度为隔框成型模宽度+20mm,每一层比上一层宽8-12mm,最底层硅橡胶远离隔框的一侧,用壁纸刀在边缘修出30
°
斜角。防止硅橡胶边缘在固化后在制件上留下压痕。将该隔框固化工装安装在型架上,同时将相邻隔框的铺叠模也进行安装。
37.7.坯料压实。将铺叠完成的隔框高于隔框固化工装的坯料,压实到隔框固化工装侧面上,有褶皱部分,需将褶皱裁开,去掉多余坯料。缺失部分,需要补铺等厚度预浸料,预浸料拼接方式为对接。
38.8.预浸料铺叠。铺叠之前隔框剩余的1/2铺层,下一个框的1/2及其间筒段的铺层。铺叠完成后,将隔框铺叠模卸下,安装已铺叠1/2隔框的隔框固化工装及再下一个隔框的铺
叠模。
39.9.工艺辅料放置。因隔框垂直于地面,工艺辅料无法自然放置。需用压敏胶带将其固定在隔框的非工作面。
40.10.制真空袋,先做一端真空袋放置在筒段上两端头自然垂下,在筒段下方,将两个端头用一条密封胶条粘接在一起。其一侧用密封胶条粘在筒段成型模上,另一端粘贴上密封胶条后,不揭掉表面保护纸。
41.11.做相邻隔框间真空袋。重复步骤9后,揭掉步骤10的保护纸,与此次制作真空相邻的一侧进行粘接。粘贴位置在隔框位置,有支臂20的位置,不是真空袋互相粘接,而是两侧真空袋各粘在支臂20一面,需在支臂20上增加一条密封胶条,保证密封效果。
42.12.重复上述步骤9.10及11,直至所有隔框及筒段均被真空袋覆盖。制作真空袋的数量为隔框数量+1。
43.13.将工装整体放入热压罐中,进行固化。
44.14.脱模。先将隔框固化工装上的背板27取下,再依据脱模楔角,最先取楔角压在其他部分上的部分。用两个起销器同时连接工装上的两个螺栓孔30,两人同时进行敲击,使工装能够平行退出。按此方式逐次卸下隔框固化模25。
45.所述的隔框成型模型架包括基座1、上框架2和隔框成型模3。
46.所述的基座1包括底座4、前端支撑定位架5、后端支撑定位架6和立柱7。
47.底座4为双层格栅结构,前后两端为梯形,中段为矩形。前端支撑定位架5、后端支撑定位架6分别设置在底座4的前、后两端上方。
48.前端支撑定位架5包括前支撑台10,以及设置在前支撑台10上的左右限位座8和前后限位板9;左右限位座8包括两部分,一部分为内部为圆形、外部底侧为梯形的卡箍11,卡箍上设置长销12,用于与筒段工装进行定位;另一部分为底座台13,底座台13上设置两块固定限位块14,两限位块14相对的一面,是与卡箍11底部匹配的斜面。前后限位板9包括限位板15和圆形限位环16,限位板15为一平板,中心有孔,孔中配置圆形限位环16。圆形限位环16为中心有孔的圆形凸台,凸台一端突出段高度延伸出限位板15 20mm,直径与筒段工装匹配;另一端起连接作用,与限位板15采用螺栓连接,整体可从限位板15远离左右限位座8的一面取下。前支撑台10为矩形板架结构,前支撑台10上设置与左右限位座8和前后限位板9及底座4连接的螺孔,前支撑台10高度能需保证组合完成的隔框成型模3与底座4至少400mm的间隙。
49.后端支撑定位架6包括限位卡箍17与后支撑台18,限位卡箍17上部可拆卸,底部与上部连接后,内径与筒段工装匹配,限位卡箍17底部与后支撑台18固定。后支撑台18为方钢框架结构,后支撑台18高度需高于前支撑台10,同时与前支撑台10调整筒段工装角度,保证隔框姿态为垂直于地面。
50.底座4左右两侧对称设计立柱7,每侧立柱7数量与隔框数量相同。立柱7包括框架、连接平台19与支臂20。连接平台19位于框架顶端,用于与上框架2组合,连接平台19上设置4个孔,位于连接平台19矩形的四个顶点。两个对角线上位置为一组,其中一组为销孔,用于连接平台19定位;另一组为螺栓孔,用于两个连接平台19的连接。立柱7的框架内侧设置与隔框成型模3连接的支臂20。框架与底座4内侧连接区为圆弧形,可最大程度增加连接面积,提高立柱7稳定性。同时能保证与隔框成型模3的间距,保证足够的操作空间。
51.上框架2采用方钢管21连接若干梁22的形式。梁22的数量与隔框数量相同。梁22内侧为圆弧形,外侧为梯形,局部开对称减重口,通过方钢管21连接为一个整体。每个梁22上均设置与隔框成型模连接的支臂20。上框架2底部设置与立柱7顶端连接的连接平台19。
52.隔框成型模3包括隔框铺叠工装23和隔框固化工装24。所述隔框铺叠工装23分瓣制造,每瓣上均有与立柱7或上框架2连接的支臂20。用于隔框一半铺层的铺叠。隔框固化工装24包括两部分,一部分为隔框固化模25,隔框固化模25侧边高度为隔框翻边及20mm余量的高度,外形面为隔框型面。隔框固化模25为分瓣结构,各分瓣间设计工装不同角度的脱模楔角。保证工装在固化后能够顺利脱模,不会损伤制件。隔框固化模25预留足够宽度及强度进行成型及连接后,非工作面中间部位抠减重凹槽26,目的为工装减重,以满足工装整体使用时的精准度及可操作性。每一分瓣工装上预留两个螺栓口,用于脱模时,与起销器连接。隔框固化工装24的另一部分为背板27,用于将隔框成型模组合成大块,保证其使用时的精度及稳定性,背板27上设置支臂20,与立柱7或上框架2的支臂20连接,保证各个隔框的位置精度。
53.所述的隔框铺叠工装中面板28、支臂20为材质选用铝。隔框固化工装采用普通钢。