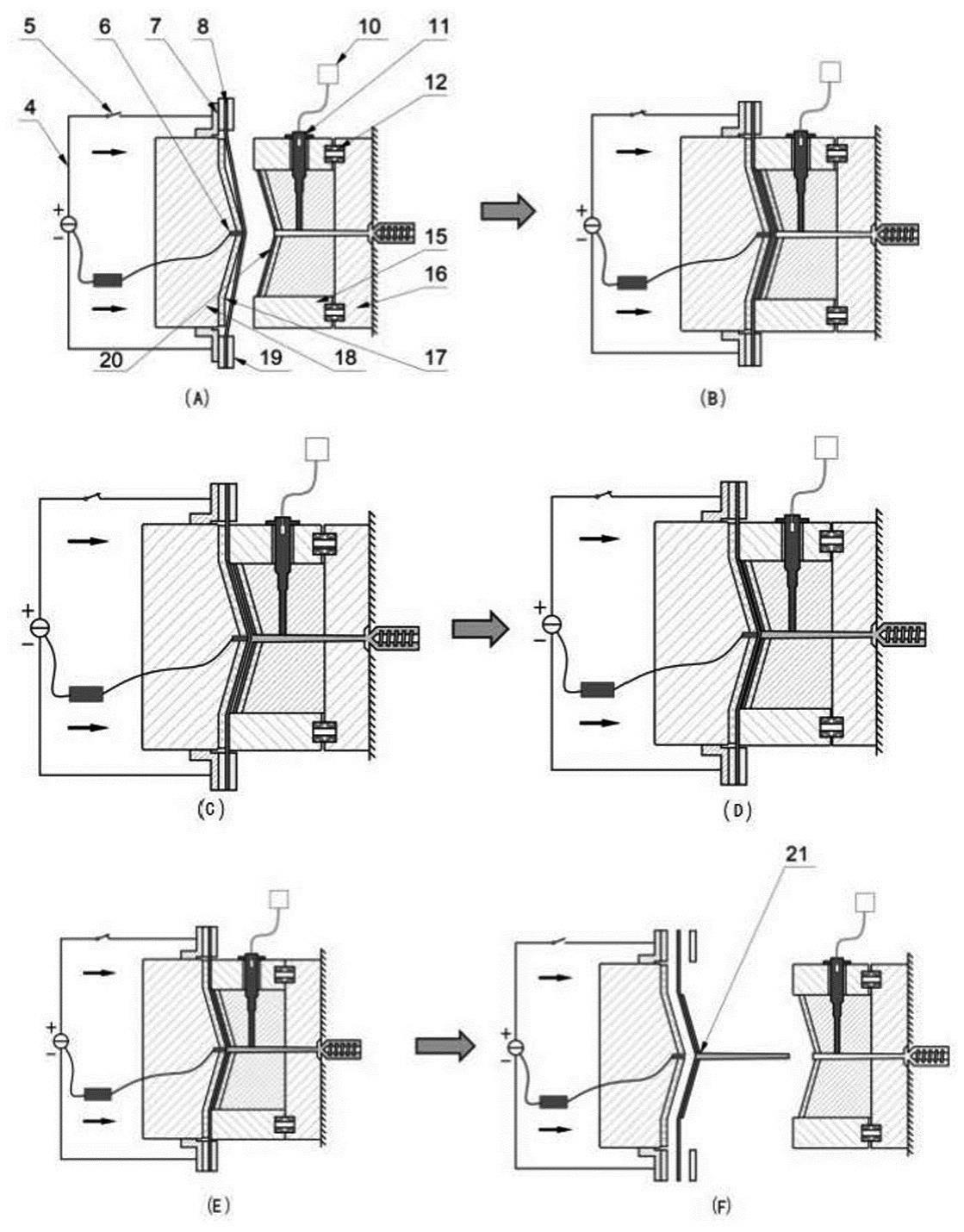
1.本发明属于轻质多材料复合构件制备成型技术领域,具体涉及一种碳纤维增强热塑性复合材料-金属复合构件的快速成型方法与装置。
背景技术:2.随着新能源大环境的变化,发展新能源汽车是推动绿色发展的战略举措,要突破整车轻量化等共性节能技术。汽车轻量化的途径主要有三种途径:结构优化、工艺技术改进、应用轻量化材料。轻量化材料的应用作为汽车轻量化基础和核心手段,是目前实现汽车轻量化最有效的途径。
3.目前以铝、镁、钛合金为代表的轻质金属材具有高比强度、导热导电性能好、阻尼减震性和电磁屏蔽性强、易加工成型等优点,成为汽车轻量化首选材料。作为新兴轻量化材料,碳纤维增强热塑性树脂基复合材料凭借其优良的强度、刚度、耐化学腐蚀、可回收及加工成本低等优点,广泛地应用于汽车、航空航天、医疗、军工、电子、仪表等诸多行业领域。由于汽车零部件承力状态不同,单一材料难以最大程度的满足汽车结构的轻量化要求。工程塑料、树脂基复合材料以及轻质金属等多种材料混合的设计理论、方法和相应工艺成为重要发展趋势。根据不同部位的功能强度要求,选择对应的合适材料,使得各材料优势得到充分发挥,以实现选材与零件功能的最优化。由于碳纤维增强热塑性树脂基复合材料和轻质金属材料的上述一系列优点,由轻质金属与热塑性树脂基复合材料组成的复合构件,对实现轻量化的推动进程具有极大的优势和应用背景,并日益成为国内外研究热点。
4.现有技术中,制造金属-热塑性树脂基复合材料复合构件的方法主要有机械紧固、粘合剂胶结和焊接工艺。对于机械紧固来说,由于二者拥有较大差异的硬度和弹性模量,会导致两种材料的一侧密封性较差,同时还会增加整个接头重量,预制孔还会增加接头应力集中现象的产生;对于粘合剂胶接来说,粘结剂固化时间较长,并且腐蚀和高温环境会弱化粘结界面,从而影响复合构件力学服役性能。对于焊接工艺来说,可以解决上述两种方法存在的问题,但由于金属熔点远高于热塑性树脂,焊接过程会对树脂基复合材料造成较大的热损伤。并且,现有复合材料-金属复合构件制造技术需要分别成型加工金属与纤维增强热塑性复合材料,成型周期长,生产效率低。因此,迫切需要发明一种工序简单、能耗低、粘结界面强度高的碳纤维增强热塑性复合材料-金属复合构件的制造方法。
技术实现要素:5.本发明为了高效快速制备高性能多材料体系复合构件,适应大批量自动化生产,同时能够节约能源,降低生产成本,开发了一种碳纤维增强热塑性复合材料-金属复合构件的快速成型方法,所述方法采用对应的成型装置实现,所述装置具体包括:自阻加热部分;所述自阻加热部分包括电源、pid控制器;所述电源通过导线与碳纤维编织布两端相连,所述pid控制器与温度传感器和电源相连,其中温度传感器用于测定
碳纤维编织布的温度;注塑-压缩模具:所述注塑-压缩模具包括动模板、定模板、推件板、和推件板芯块;所述动模板的两端设置有电极,所述电极包括固定铜电极和活动铜电极,用于固定碳纤维并使碳纤维编织布与电源相连;所述动模板和推件板芯块内侧设置有绝缘隔热材料层;所述定模板和推件板芯块固定安装,所述推件板与定模板之间设置有碟簧,以实现推件板在注塑-压缩过程和脱模过程中来回移动;金属嵌件安装在定模腔内;所述推件板芯块和动模板内侧的形状与复合构件的形状相适配;所述定模板、推件板芯块和金属嵌件由外侧到内侧贯穿设置有树脂注射流道,所述树脂注射流道与注射料筒相连;超声振动部分:所述超声振动部分包括超声发生器与超声振动子,所述超声振动子贯穿推件板和推件板芯块至所述树脂注射流道上方;所述成型方法具体包括:将碳纤维编织布铺层后采用活动铜电极固定在动模板绝缘隔热材料表面,并将表面处理后的金属嵌件放置于定模型腔内;将所述注塑-压缩模具初次合模,使碳纤维编织布与金属嵌件之间形成浸渍间隙;接通电源,将所述碳纤维编织布升温至预设温度并保温;开始注射熔融聚合物,并开启超声波发生器,将经过超声场作用后的熔融树脂注射至所述浸渍间隙;当间隙浸渍完成后,将所述注塑-压缩模具进行二次合模,至推件板与定模板之间的距离为0,完成熔融聚合物对碳纤维编织布厚度方向的浸渍及金属表面微结构的填充后,进行保压处理;保压处理后进行冷却,开模获得碳纤维增强热塑性复合材料-金属复合构件。
6.进一步的,所述固定铜电极上设置有活动铜电极的导轨,使固定铜电极和活动铜电极之间接触并可相互滑动;进一步的,所述将所述碳纤维编织布升温至预设温度并保温过程的预设温度为220-400℃,升温速率为80~350℃/min。
7.进一步的,所述树脂为pp、pa6、pa66或peek中的任意一种,所述树脂注射速率为30 ~ 90 mm/s,注射压力为30 ~ 80 mpa。
8.进一步的,所述超声过程的工作频率为10 ~ 60 khz,功率为0 ~ 6000 w。
9.进一步的,所述浸渍间隙为1-5mm,浸渍时间为10-30s。
10.进一步的,所述二次合模过程中压缩速率为0.5-10mm/s。
11.进一步的,所述保压压力为10-60mpa,保压时间为10-300s。
12.基于同一发明构思的,本发明实施例还提供了一种碳纤维增强热塑性复合材料-金属复合构件的快速成型装置,所述装置具体包括:自阻加热部分;所述自阻加热部分包括电源、pid控制器;所述电源通过导线与碳纤维编织布两端相连,所述pid控制器与温度传感器和电源相连,其中温度传感器用于测定碳纤维编织布的温度;注塑-压缩模具:所述注塑-压缩模具包括动模板、定模板、推件板、和推件板芯块;所述动模板的两端设置有电极,所述电极包括固定铜电极和活动铜电极,用于固定碳纤维并使碳纤维编织布与电源相连;所述动模板和推件板芯块内侧设置有绝缘隔热材料层;所述定模板和推件板芯块固定安装,所述推件板与定模板之间设置有碟簧,以实现推件板在
注塑-压缩过程和脱模过程中来回移动;金属嵌件安装在定模腔内;所述推件板芯块和动模板内侧的形状与复合构件的形状相适配;所述定模板、推件板芯块和金属嵌件由外侧到内侧贯穿设置有树脂注射流道,所述树脂注射流道与注射料筒相连;超声振动部分:所述超声振动部分包括超声发生器与超声振动子,所述超声振动子贯穿推件板和推件板芯块至所述树脂注射流道上方。
13.有益效果:(1)本发明的方法是基于注塑-压缩成型工艺,将金属板和碳纤维编织布作为嵌件,利用增强体碳纤维自阻加热的特性提供均匀温度场,并将超声波引入注塑工艺中以降低熔融聚合物粘度,最终实现碳纤维增强热塑性复合材料-金属复合构件一体化成型。实现了多材料异质复合构件“成型-连接”一体化制造,解决了传统制造技术中将碳纤维增强热塑性复合材料成型工艺与异质材料连接工艺分离导致的工序多、耗能高、连接强度低等难题。
14.(2)本发明将碳纤维编织布同时作为增强材料和加热源,利用其“体积内”的自阻加热效应, 快速加热,为碳纤维增强热塑性复合材料-金属复合构件成型提供均匀温度场,在大幅降低能耗的同时,解决了传统注塑成型过程纤维编织布温度低导致的纤维难以浸润的制造难题。
15.(3)本发明利用超声振动降低熔融聚合物粘度,改善聚合物流动性能,降低纤维浸润成型质量对注射压力的依赖,解决注射压力过大导致的纤维变形、断裂等缺陷问题;同时低粘度的熔融聚合物更有利于填充金属材料表面粗糙结构,形成粘结界面的机械铆接互锁结构,从而提升碳纤维增强热塑性复合材料与金属材料之间的粘度强度。
附图说明
16.图1是本发明提供的碳纤维增强热塑性复合材料-金属复合构件的快速成型装置的结构示意图;图2是本发明提供的碳纤维增强热塑性复合材料-金属复合构件的快速成型过程的工艺流程图;(a)为定位阶段、(b)为合模预热阶段、(c)为浸渍阶段、(d)为复合构件成型阶段、(e)为保压阶段、(f)为脱模阶段;图3是本发明提供的碳纤维增强热塑性复合材料-金属复合构件的结构示意图。
17.【附图标记说明】1、pid控制器;2、信号线;3、直流稳压电源;4、电源线;5、直流稳压电源开关;6、温度传感器;7、固定铜电极;8、碳纤维编织布;9、导线;10、超声发生器;11、超声振动子;12、碟簧组;13、推件板芯块;14、注射料筒;15、推件板;16、定模板;17、绝缘隔热材料层;18、动模板;19、活动铜电极;20、金属嵌件;21、碳纤维增强热塑性复合材料-金属复合构件;21a、连续碳纤维增强热塑性复合材料结构。
具体实施方式
18.为使本发明要解决的技术问题、技术方案和优点更加清楚,下面将结合附图及具体实施例进行详细描述。
19.在本发明实施例中,如图1所示,提供了碳纤维增强热塑性复合材料-金属复合构
件的快速成型装置的结构示意图,所述装置具体包括:自阻加热部分,用于提供热源及调整成型过程中碳纤维编织布温度历程;所述自阻加热部分包括电源3、pid控制器1;所述电源通过电源线与碳纤维编织布两端相连,所述pid控制器1与温度传感器6和电源3相连,其中温度传感器用于测定碳纤维编织布的温度;温度传感器6将成型过程中碳纤维编织布8温度反馈给pid控制器1,pid控制器1依据实际数据与目标温度数据的差值调整信号强度,电源3获得不同的信号强度后调整输出功率大小,以实现成型过程中等温浸渍。
20.注塑-压缩模具:所述注塑-压缩模具包括动模板18、定模板16、推件板15、和推件板芯块13;所述动模板18的两端设置有电极,所述电极包括固定铜电极7和活动铜电极19,用于固定并使碳纤维编织布8与电源3相连。由于碳纤维编织布8需要通电加热并在成型过程中维持目标温度,所以碳纤维编织布8与注塑-压缩模具之间需做好绝缘与隔热,具体措施为:将动模板18、推件板15外壁面喷涂耐高温绝缘涂层;在动模板18和推件板芯块13上安装绝缘隔热材料层17进行保温使型腔内部可以维持目标温度。所述定模板16和推件板芯块13固定安装,所述推件板15与定模板16之间设置有碟簧12,以实现推件板15在注塑-压缩过程和脱模过程中来回移动;金属嵌件20安装在定模腔内;所述推件板芯块13和动模板18内侧的形状与复合构件的形状相适配;所述定模板16、推件板芯块13和金属嵌件20由外侧到内侧贯穿设置有树脂注射流道,所述树脂注射流道与注射料筒14相连。注塑过程,模具初次合模,通过注塑机控制模具初次合模位置,在碳纤维编织布8与金属嵌件20表面形成预留浸渍间隙。预留浸渍间隙可有效避免碳纤维编织布8与金属嵌件20的接触,同时预留间隙区域的熔融聚合物在二次合模力作用下,实现熔融聚合物对碳纤维编织布厚度方向的浸渍及金属表面微结构的填充。
21.超声振动部分:所述超声振动部分包括超声发生器10与超声振动子11,所述超声振动子贯穿推件板15和推件板芯13至所述树脂注射流道上方。利用超声振动降低熔融聚合物粘度,改善聚合物流动性能,进而提升纤维浸渍质量及金属表面微结构填充。
22.如图2所示,本发明实施例还提供了碳纤维增强热塑性复合材料-金属复合构件超声振动-自阻加热复合注塑-压缩成型工艺流程:(a)定位阶段:首先将碳纤维维编织布8按一定铺层方式放在动模板18上的绝缘隔热材料层17上,碳纤维编织布8两端利用活动铜电极19夹紧,固定铜电极7上设置有活动铜电极19的导轨,固定铜电极7和活动铜电极19之间可在保证良好接触的同时实现相对滑动;并将经过表面处理后的金属嵌件20放置于定模型腔内。
23.(b) 合模预热阶段:连接好自阻加热回路后,进行注塑-压缩模具初次合模,动模板18推动推件板15向右移动,压缩碟簧12至指定位置(即,推件板与定模板的距离为1 ~ 5 mm),在碳纤维编织布8与金属嵌件20之间形成预留浸渍间隙(1 ~ 5 mm);同时活动铜电极19在碳纤维编织布8的牵引下向模具中心移动,直至碳纤维编织布与动模侧绝缘隔热材料层17表面完全贴合,打开电源开关5,碳纤维编织布8开始通电加热至目标温度(220 ℃~ 400 ℃),升温速率为80~350℃/min。
24.(c)浸渍阶段:当碳纤维编织布8升至目标温度后,碳纤维编织布开始保温;将熔融聚合物(其中热塑性树脂主要是指pp、pa6、pa66、peek等)注射至金属嵌件20与碳纤维编织布8间的预留浸渍间隙,注射速度为30 ~ 90 mm/s,注射压力为30 ~ 80 mpa,注塑机开始注
射熔融聚合物的同时启动超声波发生器10,使超声振动子11开始工作,超声振动子11端面直接在主流道内对熔体施加超声振动,其作用阶段包括整个间隙浸渍阶段、复合构件成型阶段以及保压阶段,超声波发生器工作频率为10 ~ 60 khz,功率为0 ~ 6000 w,浸渍时间为10-30s。
25.(d)复合构件成型阶段:进行模具二次合模,进一步压缩碟簧12,直至推件板15和定模板16之间的距离为0,压缩速度为0.5 ~ 10 mm/s,利用注塑-压缩成型工艺完成熔融聚合物对碳纤维编织布厚度方向的浸渍及金属表面微结构的填充,实现碳纤维增强热塑性复合材料浸润成型及其与金属板材的粘结。
26.(e)保压阶段:碳纤维编织布8继续通电以保证型腔内部的温度达到聚合物熔点以上,保证浸渍质量。保压压力为10 ~ 60 mpa,保压时间为10 ~ 300 s。保压结束时,碳纤维编织布8两端断电,超声波发生器10停止工作。
27.(f)脱模阶段:冷却结束后,模具开模并取出碳纤维增强热塑性复合材料-金属复合构件21,其结构如图3所示。
28.以下以具体实施例进行进一步说明。
29.实施例1材料选择增强体:t300碳纤维编织布热塑性树脂基材料:短纤增强聚丙烯,短纤质量分数为20%工艺流程及参数(1)金属嵌件表面预处理:将6061铝合金板材裁剪成合适尺寸的金属嵌件(总长为138 mm,宽为100 mm,沿长度方向对称折弯,折弯角度为120
°
),并对其表面进行阳极氧化处理,使金属嵌件表面形成粗糙结构。
30.(2)定位阶段:裁剪尺寸为206 mm
×
130 mm的碳纤维编织布,对齐铺层,铺层数目为4层,铺层厚度约为0.9 mm。将铺好的碳纤维编织布放置在动模板绝缘隔热材料层表面,采用活动电极19将其两端夹持,为了增加导电性,碳纤维编织布两端分别粘贴宽为25 mm的铜箔胶带; 同时将步骤(1)得到的金属嵌件20放置于定模型腔内。
31.(3)合模预热阶段:连接好自阻加热回路4后,模具进行初次合模,动模板18推动推件板15向右移动,预压缩碟簧12至推件板15和定模板16之间的距离为1.5 mm。活动铜电极19被碳纤维编织布8牵引向模具中心移动,将碳纤维编织布8固定在动模表面,在金属嵌件20与碳纤维编织布8之间形成1.5 mm厚的预留间隙;打开电源开关5,碳纤维编织布8开始通电加热,升温速率为200℃/min,温度升高至260℃。
32.(4)浸渍阶段:当碳纤维编织布8升至260 ℃后开始保温,注塑机注射熔融树脂至金属嵌件20与碳纤维编织布8之间的间隙区域,注射速度为30 mm/s,注射压力为30 mpa,熔体温度为250℃,模具温度为100℃。注塑机注射熔融树脂的同时启动超声波发生器10,超声振动子11开始工作,超声波发生器10的输出功率为100 w,超声振动子11工作频率为30 khz。
33.(5)复合构件成型阶段:间隙浸渍阶段完成后,模具进行二次合模,进一步压缩碟簧12,压缩速度为0.5 mm/s,从而推动间隙区域熔融树脂在碳纤维编织布厚度方向的浸渍,完成连续碳纤维增强热塑性复合材料结构21a的成型及金属嵌件20表面微结构的充填,实
现碳纤维增强热塑性复合材料结构与金属嵌件的粘结。
34.(6)保压阶段:复合结构成型阶段结束后,碳纤维编织布8继续通电,型腔内部温度维持稳定在250℃,保压压力为15 mpa,保压时间为150 s。保压结束后,碳纤维编织布8两端立即断电,并关闭超声波发生器10。
35.(7)脱模阶段:模具通入冷却液体,待型腔内部温度冷却至80℃时,模具开模,将碳纤维增强热塑性复合材料-金属复合构件21顶出,完成脱模。
36.实施例2材料选择增强体:t300碳纤维编织布热塑性树脂基材料:聚酰胺6 (pa6)金属嵌件:ti-6a1-4v 钛合金工艺流程及参数(1)金属嵌件表面预处理:将ti-6a1-4v 钛合金板材裁剪成合适尺寸的金属嵌件(总长为138 mm,宽为100 mm,沿长度方向对称折弯,折弯角度为120
°
),并对其表面进行阳极氧化处理,使金属嵌件表面形成粗糙结构。
37.(2)定位阶段:裁剪尺寸为206
×
130 mm的碳纤维编织布8,对齐铺层,铺层数目为6层,铺层厚度约为1.4 mm。将铺好的碳纤维编织布放置在动模板绝缘隔热材料层上,采用活动电极19将其两端夹持,为了增加导电性,碳纤维编织布两端分别粘贴宽为25 mm的铜箔胶带;同时将步骤(1)得到的金属嵌件20放置于定模型腔内。
38.(3)预热阶段:连接好自阻加热回路4后,模具进行初次合模,动模板18推动推件板15向右移动,预压缩碟簧12至推件板15和定模板16之间的距离为2.5 mm;活动铜电极19被碳纤维编织布8牵引向模具中心移动,将碳纤维编织布8固定在动模表面,在金属嵌件20与碳纤维编织布8之间形成2.5 mm厚的预留间隙;打开电源开关5,碳纤维编织布8开始通电加热,升温速率为220℃/min,温度升高至280 ℃。
39.(4)间隙浸渍阶段:当碳纤维编织布升至280 ℃后开始保温,注塑机注射熔融树脂至金属嵌件20与碳纤维编织布8之间的间隙区域,注射速度为50 mm/s,注射压力为50 mpa,熔体温度为280℃,模具温度为120℃。注塑机注射树脂的同时启动超声波发生器10,超声振动子11开始工作,超声波发生器10的输出功率为300 w,超声振动子11工作频率为40 khz。
40.(5)复合构件成型阶段:间隙浸渍阶段完成后,模具进行二次合模,进一步压缩碟簧12,压缩速度为1 mm/s,推动间隙区域熔融树脂在碳纤维编织布厚度方向的浸渍,完成连续碳纤维增强热塑性复合材料结构21a的成型及金属嵌件20表面微结构的充填,实现碳纤维增强热塑性复合材料结构与金属嵌件的粘结。
41.(6)保压阶段:复合结构成型阶段结束后,碳纤维编织布8继续通电,型腔内部温度维持稳定在280℃,保压压力为25 mpa,保压时间为200 s。保压结束后,碳纤维编织布8两端立即断电,并关闭超声波发生器10。
42.(7)脱模阶段:模具通入冷却液体,待型腔内部温度冷却至100℃时,模具开模,将碳纤维增强热塑性复合材料-金属复合构件21顶出,完成脱模。
43.实施例3材料选择
增强体:t700碳纤维编织布热塑性树脂基材料:聚醚醚酮(peek)金属嵌件:ti-6a1-4v 钛合金工艺流程及参数(1)金属嵌件表面预处理:将ti-6a1-4v 钛合金板材裁剪成合适尺寸(总长为138 mm,宽为100 mm,沿长度方向对称折弯,折弯角度为120
°
)的金属嵌件,并对其表面进行阳极氧化处理,使金属嵌件表面形成粗糙结构。
44.(2)定位阶段:裁剪尺寸为206
×
130 mm的碳纤维编织布,对齐铺层,铺层数目为6层,铺层厚度为1.4 mm。将铺好的碳纤维编织布放置在动模板绝缘隔热材料层表面,采用活动电极19将其两端夹持,为了增加导电性,碳纤维编织布两端分别粘贴宽为25 mm的铜箔胶带;同时将步骤(1)得到的金属嵌件放置于定模型腔内。
45.(2)预热阶段:连接好自阻加热回路4后,模具进行初次合模,动模板18推动推件板15向右移动,预压缩碟簧12至推件板15和定模板16之间的距离为3 mm。活动铜电极19被碳纤维编织布8牵引向模具中心移动,将碳纤维编织布8固定在动模表面,在金属嵌件与碳纤维编织布之间形成3 mm厚的预留间隙;打开电源开关5,碳纤维编织布8开始通电加热,升温速率为300℃/min,温度升高至380℃。
46.(3)间隙浸渍阶段:当碳纤维编织布升至380 ℃后开始保温,注塑机注射熔融树脂至金属嵌件20与碳纤维编织布8之间的间隙区域,注射速度为80 mm/s,注射压力为80 mpa,熔体温度为380℃,模具温度为180℃。注塑机注射熔融树脂的同时启动超声波发生器10,超声振动子11开始工作,超声波发生器10的输出功率为500 w,超声振动子11工作频率为45 khz。
47.(4)复合结构成型阶段:间隙浸渍阶段完成后,模具进行二次合模,进一步压缩碟簧12,压缩速度为2 mm/s,从而推动间隙区域熔融树脂在碳纤维编织布厚度方向的浸渍,完成连续碳纤维增强热塑性复合材料结构21a的成型及金属嵌件20表面微结构的充填,实现碳纤维增强热塑性复合材料结构与金属嵌件的粘结。
48.(5)保压阶段:复合结构成型阶段结束后,碳纤维编织布8继续通电,型腔内部温度维持稳定在380℃,保压压力为30 mpa,保压时间为300 s。保压结束后,碳纤维编织布8两端立即断电,并关闭超声波发生器10。
49.(6)脱模阶段:模具通入冷却液体,待型腔内部温度冷却至120℃时,模具开模,将碳纤维增强热塑性复合材料-金属复合构件21顶出,完成脱模。
50.本发明将碳纤维编织布固定在动模绝缘隔热材料层表面,并将裁剪好的金属嵌件放置于定模型腔内;模具初次合模,形成预留浸渍间隙;对碳纤维编织布通电,碳纤维在电流作用下快速升温至聚合物熔融温度以上后,开始注射熔融聚合物,同时启动超声波发生器,超声振动子端面在主流道内对熔体施加超声场,完成预留浸渍间隙处的填充。进行二次合模,完成熔融聚合物对碳纤维编织布厚度方向的浸渍及金属表面微结构的填充,实现碳纤维增强热塑性复合材料浸润成型及其与金属板材的粘结;保压一段时间后,碳纤维编织布两端断电,关闭超声波发生器,待聚合物冷却后获取碳纤维增强热塑性复合材料-金属复合构件。本发明将碳纤维增强热塑性复合材料成型及其与金属材料的粘结在注塑模具中集成,实现了多材料异质复合构件“成型-连接”一体化制造,解决了传统制造技术中将碳纤维
增强热塑性复合材料成型工艺与异质材料连接工艺分离导致的工序多、耗能高、连接强度低等难题。
51.以上所述是本发明的优选实施方式,应当指出,对于本技术领域的普通技术人员来说,在不脱离本发明所述原理的前提下,还可以作出若干改进和润饰,这些改进和润饰也应视为本发明的保护范围。