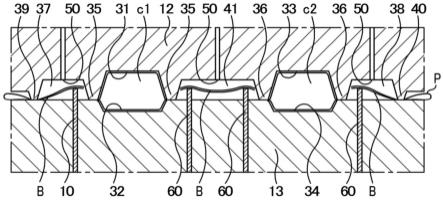
成型体的制造方法以及成型用模具
本技术是申请号:201880068848.4、申请日:2018年10月30日、发明名称“成型体的制造方法以及成型用模具”的中国发明专利申请的分案申请。
【技术领域】
1.本发明涉及成型体的制造方法、成型用模具以及成型体的制造装置,特别涉及在模具内去毛刺的新颖的成型体的制造方法、成型用模具以及成型体的制造装置。还涉及在汽车的空调用管道的成型品,可有效率地去除毛刺的毛刺去除方法、毛刺除去装置。
背景技术:2.已知,作为成型树脂材料而形成的成型品,有例如,安装于汽车的仪表板上的各种空调管道。这些空调管道可以通过吹塑成型从挤出机的模具挤出的型坯来容易地制造。
3.在进行吹塑成型的成型品(管材)中,在闭模的模具周围形成毛刺,去除毛刺为必要工序。通常,吹塑成型后的去毛刺通常使用按压机来进行,并且通过使用与成型品的外形相对应的模具对毛刺进行冲模来共同去除模具周围的毛刺。
4.例如专利文献1公开了在模具内进行吹塑成型的吹塑成型方法以及吹塑成型装置,通过使毛刺与模具积极接触从而提高冷却效率,提高毛刺的冷却效率。在吹塑成型中,等到毛刺充分冷却后通过按压机进行毛刺冲模成为损失时间和生产效率的主要原因。根据专利文献1所述的技术,可缩短从吹塑成型至去毛刺的一系列工序所需的时间从而提高生产效率。【现有技术文献】【专利文献】
5.【专利文献1】日本专利特开2016-83859号公报
技术实现要素:【发明要解决的课题】
6.然而,除吹塑成型之外,成型体周围形成毛刺的成型中,常识中的去毛刺工作是在从成型体取出模具之后用按压机和手作业进行,专利文献1所述的发明也不是例外。但是,适用按压机进行去毛刺时,若成型品的尺寸过大,按压机也不可避免地与此对应变大,需要极大的设备投资成为课题。另外,若成型品的大小和形状不同,按压机的形状也需要变更为于此对应的大小和形状,需要更多设备投资。
7.在这种情况,特别是在大型成型品的成型中,通过手作业切除形成于成型品周围的毛刺成为现实。具体而言,从模具取出带有毛刺的作为产品的成型体后,通常实施刀处理等人手处理的方法。在用手作业一个个切除大型成型品的毛刺的方法中,从模具取出后进行毛刺除去作业,工数多且每个成型品所需的去毛刺的时间变长,成为生产效率大大受损的主要原因。
8.本发明是鉴于这样的情况而完成的,以提供一种无需大型装置可有效率地去毛刺
的成型体的制造方法为目的、更以提供成型用模具、成型体的制造装置为目的。另外,本发明还以提供一种无需大型装置可有效率地去毛刺的毛刺去除方法为目的,更以提供毛刺除去装置为目的。【用于解决课题的手段】
9.为达到上述目的,本技术的第1发明的成型体的制造方法,其特征在于,在模具内进行成型体的成型的同时,从上述成型体分离形成于上述成型体周围的毛刺,成型体的成型后,在模具内对形成于成型体周围的毛刺的至少局部进行吹气而冷却,使突出部件对冷却的毛刺进行突出,从成型体分离上述毛刺。
10.另外,本发明的成型用模具是一种进行成型体的成型的成型用模具,其特征在于,上述成型用模具具备喷气机构和突出部件,在夹紧成型体外周部分的夹紧部外侧设置容纳毛刺的空间,上述喷气机构吹气于上述空间,上述突出部件突出于上述空间内。
11.本发明的成型体的制造装置,其具备进行成型体的成型的模具,在模具内进行成型体的成型的同时,从上述成型体分离形成于上述成型体周围的毛刺,上述模具具备喷气机构和突出部件,其中,上述喷气机构对形成于成型体周围的毛刺的至少局部进行吹气从而冷却,上述突出部件对冷却的毛刺突出,从成型体分离上述毛刺。
12.本发明的基本思想是在模具内进行去毛刺,通过由吹气进行的毛刺的冷却、由突出部件进行的毛刺的分离,抑制成型周期的减少的同时实现有效率的去毛刺。
13.另外,本技术的第2发明的毛刺去除方法是从模具取出成型的成型品,除去沿着分界线形成的毛刺的毛刺去除方法,其特征在于,在分界线附近由按夹具按压上述毛刺时,将成型品放置于接受台上的同时支撑毛刺的按夹具的抵接位置的外侧位置。另外,本发明的毛刺除去装置还是除去沿着从模具取出的成型品的分界线形成的毛刺的毛刺除去装置,其具备:在分界线附近按压上述毛刺的按夹具、用上述按夹具按压时放置成型品的第1接受台、支撑毛刺的按夹具的抵接位置的外侧位置的第2接受台。
14.在分界线附近用按夹具按压毛刺时,通过将成型品放置于接受台上的同时支撑毛刺的按夹具的抵接位置的外侧位置,此处成为支点,在作为作用点的按夹具的抵接位置有效施加按夹具的力,毛刺易于冲模。
15.另外,本发明的毛刺去除方法是从模具取出成型的成型品,除去沿着分界线形成的毛刺的毛刺去除方法,其特征为,在分界线附近由棒状的按夹具按压上述毛刺,从成型品分离上述毛刺。
16.另外,本发明的毛刺除去装置是除去沿着从模具取出的成型品的分界线形成的毛刺的毛刺除去装置,其特征在于,具备一种棒状的按夹具,上述按夹具在分界线附近按压上述毛刺。
17.通过将棒状的按夹具排列于成型品周围,可一次性除去毛刺,可对应于任何大小的成型品。另外,仅需改变棒状的按夹具的设置位置即可对应成型品的形状变化。【发明效果】
18.根据本发明,无需大型装置即可有效率地去毛刺。特别是,根据本发明,取出完成成型的成型体时已完成毛刺处理,可实现成型工序的大幅精简。另外,也可简单对应于成型品的大小或形状的变化。
【附图说明】
19.图1是示意性地表示第1实施方式中吹塑成型成型体时的状态的概略截面图。图2是表示除去毛刺之前的成型体的一个例子的概略俯视图。图3是说明从成型到去毛刺为止的动作的图,是表示成型体的成型工序的概略截面图。图4是表示由吹气进行的毛刺冷却工序的概略截面图。图5是表示突出部件的突出工序的概略截面图。图6是表示突出棒的一个例子的重要部分概略立体图。图7是表示突出棒的其他例子的重要部分概略立体图。图8是表示突出棒的另外的其他例子的重要部分概略立体图。图9是表示毛刺向突出棒侧按压的状态以及排气针刺向毛刺的状态的重要部分概略截面图。图10是表示在成型体间的空间形成倾斜面的模具例的概略俯视图。图11是图10所示的模具的概略截面图。图12表示部分放大使用图10以及图11所示的模具时的去毛刺工序的概略截面图。图13是表示在倾斜面形成锪平的状态的重要部分概略截面图。图14表示自动取出毛刺或成型品的成型线,是表示取出成型品的工序的图。图15是表示成型品的加工工序的图。图16是表示成型品的搬出工序的图。图17是表示成型品的废弃袋部分的成型状态的图,其中(a)表示未设置卡定工具时的成型状态,(b)表示设置卡定工具时的成型状态。图18是表示第2实施方式的毛刺除去装置的一个例子的概略侧视图。图19是表示将棒状的按夹具抵接于毛刺的状态的概略侧视图。图20是表示用棒状的按夹具冲模毛刺的状态的概略侧视图。图21是表示棒状的按夹具的排列状态的一个例子的概略立体图。图22是表示棒状的按夹具的排列状态的一个例子的概略俯视图。图23是表示隔着时差将棒状的按夹具按压于毛刺时的概略立体图。图24是表示切断和按夹具的组合例的概略俯视图。图25是表示切断和按夹具的组合例的概略侧视图。图26是表示分界线倾斜时形成的平坦面的一个例子的概略截面图。图27是表示在毛刺形成凸部(肋材)的状态的概略俯视图。图28是表示形成图27所示的凸部的工序的概略截面图。图29是表示在按夹具外侧设置接受台从而去毛刺的状态的概略截面图。
【具体实施方式】
20.以下,参照图面详细说明本发明的实施方式。
21.(1)第1实施方式第1实施方式中,参照图面以管的吹塑成型为例详细说明适用本发明的成型体的制造方法、成型用模具、以及成型体的成型装置的实施方式。
22.图1是说明吹塑成型作为成型体的管时的吹塑成型方法。吹塑成型时,首先,在挤
出机内将用于成型的树脂材料熔融混练制备成型用树脂。例如若为仅使用纯树脂成型时,根据需要加入改性材料于各种树脂材料的纯树脂熔融混练制作成型用树脂。使用回收树脂材料时,将预定比率的纯树脂加入粉碎的回收树脂材料混练制作成型用树脂。
23.用于成型的树脂材料可任意选择,可使用热塑性树脂例如聚丙烯等聚烯烃树脂。成型体(管1)为发泡成型体时,向成型用树脂添加发泡剂。
24.在挤出机内熔融混练这样准备的成型用树脂后,储存于塑模内的蓄能器,接下来储存预定的树脂量后将环状活塞向正交于水平方向的方向(垂直方向)下推。之后由图1所示的环状模具11的塑模缝隙以预定的挤出速度挤出圆筒状型坯p,使其从模具12,13之间挤出。之后,闭模模具12,13夹住型坯p,再以预定的压力范围向型坯p内吹入空气,从而使管1成型。
25.图2表示成型的管1的形状例,表示从模具12,13取出吹塑成型后的管1的状态。本例的管由2根平衡放置的管部2,3和连接这些管部2,3的连接管部4构成。另外,作为成型体的管1周围残留多余的型坯p作为毛刺b。
26.本实施方式的吹塑成型方法在模具12,13内进行上述管1的成型至毛刺b的分离。接下来参照图3~图5说明模具12,13的构成以及使用了这些的成型方法。应予说明,图3~图5表示对应于图2所示的管1的x-x线位置的截面。
27.管1的成型所使用的模具12,13形成有对应于管1形状的凹部,如图3所示,模具12,13形成有对应于管部2的凹部31,32、以及对应于管部3的凹部33,34。在此,由凹部31,32形成的模具12,13之间形成有对应于管部2的型腔(空间)c1,由凹部33,34形成的模具12,13之间形成有对应于管部3的型腔(空间)c2。
28.模具12,13的材质没有特别限定,可适用例如铝或钢。由于导热系数高且可有效冷却冲模毛刺,优选使用铝。
29.供给于模具12,13之间的型坯p在闭模后通过在其内部吹气塑形为模具12,13的凹部31,32或者凹部33,34的形状,塑形为模具12,13的凹部31,32或者凹部33,34形成的型腔c1,c2的形状。
30.另外,在各型腔c1,c2(即作为成型体的管1)的外周部分,各模具12,13具有互相对接的夹紧部。对应于管部2的型腔周围具有夹紧部35,对应于管部3的型腔周围具有夹紧部36。在这些夹紧部35,36型坯p被压碎,此部分成为成型体的分界线(pl)。
31.在此,残留于上述夹紧部35,36外侧的型坯p会成为毛刺b。在本实施方式,从作为成型体的管1分离该毛刺b的机构设于模具12,13。
32.首先,在模具12,13的夹紧部35,36外侧形成有容纳模具12的模具面后退而成的毛刺b的空间37,38。图3中,对应于管部2的型腔c1左侧的夹紧部35外侧形成有空间37,对应于管部3的型腔c2右侧的夹紧部36外侧形成有空间38。这些空间37或空间38内容纳夹紧部c1,c2附近的毛刺b。
33.另外,用自上述夹紧部35,36隔着预定的距离形成的夹紧部39,40堵住相反侧端部而形成上述空间37,38。即,将夹紧部35,36作为第1夹紧部,将夹紧部39,40作为第2夹紧部,上述空间37,38形成为这些夹紧部之间的空间。通过使空间37,38成为关闭空间从而使其成为防止从后述的喷气机构喷出的空气(冷气)从空间37,38泄露的结构。应予说明,喷气时为了从这些空间37,38放出空气,可将放气针插入空间37,38,也可设置其他放气机构。
34.各空间37,38设有喷气机构以及突出部件,使用这些从成型体(管1)分离毛刺b。具体而言,在本实施方式的图中,上侧的模具12对于上述空间37,38形成有用于喷气的喷气孔50。从该空气喷气孔50喷出空气(冷气),冷气喷向毛刺b。
35.另一方面,图中,下侧的模具13靠近夹紧部35,36的位置沿着夹紧部35,36排列的方式设置作为突出部件的突出棒60。突出棒60是直径20mm~30mm左右的棒状部件,以突出棒60的前端从模具13的模具面稍微突出的方式设置。通过使该突出棒60从模具面突出,从而朝向面对毛刺b的模具12的模具面按压毛刺b。
36.上述突出棒60的形态是任意的,例如图6所示可使用截面圆形的棒状体,如图7所示可使用在前端面中央具有凹部60a且具有圆环状突出部的棒状体。或者如图8所示可适用在前端具有稍微小径的凸部60b的棒状体等。无论如何突出棒60的前端的形态优选为,熔融状态的毛刺b被喷气按压时其形状被转录,通过挤出时卡定毛刺b从而防止毛刺b偏移。从该观点突出棒60的前端优选图7或图8所示的形状。
37.如上所述,突出棒60沿着夹紧部35,36排列,该间隔越狭窄切断能力上升。由此,突出棒60的排列间距(排列间隔)优选为170mm以内。
38.另外,作为突出棒60的运作手段例如可采用液压方式,可以是使突出棒60各自独立运作的方式,也可以是利用模具背板等同时运作的方式。根据成型体的形状,可以考虑通过改变突出棒60接触的时机使毛刺处理顺利进行,此时可通过调整各突出棒60的行程适宜调整。
39.管部2,3外侧的毛刺b如同上述内容,管部2,3之间的毛刺b也可适用同样的构成。但是,管2,3之间的毛刺b无需形成第2夹紧部,在管部2的夹紧部35和管部3的夹紧部36之间形成空间41,在此可设置用于喷气的喷气孔50或突出棒60。应予说明,在上述空间37,38的成型体侧(管部2侧或者管部3侧)排列了一处(一列)突出棒60,在空间41,管部2侧和管部3侧的2处排列有突出棒60。
40.接下来,说明使用这些模具12,13进行吹塑成型时的各工序。吹塑成型作为成型体的管1如上所述,用模具12,13夹住由环状模具11的塑模缝隙供给的型坯p,吹气于型坯p内将其塑形为模具12,13的型腔形状。图3说明该状态。型坯p夹在模具12,13之间而被塑形,在模具12,13的型腔c1,c2成型管部2以及管部3。
41.管部2,3的成型完成后,如图4所示由设于模具12的喷气孔50供给空气,对毛刺b的表面进行吹气。供给的空气优选冷气。另外,此处的吹气优选为空气接触夹紧部35,36附近毛刺b的方式。通过该吹气,毛刺b被冷却,在短时间内使刚性增加。
42.应予说明,上述吹气除冷却毛刺b的功能之外,还具有将毛刺b按压于突出棒60侧的作用。通过将毛刺b按压于突出棒60侧,突出棒60的突出引起的较大的行程将毛刺b按压于相反侧的模具12,从而使毛刺b彻底从成型体分离。
43.图9表示被来自喷气孔50的吹气毛刺b按压于设有突出棒60的模具13侧的状态。被吹气按压的毛刺b在初期阶段为熔融状态,由上述按压突出若干的突出棒60的前端形状被转录形成凹部。此时,突出棒60前端的至少局部成为从模具13突出的状态即可,例如突出棒60的形态成为图7或图8所示的形态时,使凹部60a周围圆环状的突出部和中央的凸部60b从模具13突出,其他部分可与模具13成为同一个平面。用突出棒60按压以形成凹部的状态被冷却的毛刺b时,突出棒60前端卡定于上述凹部,不会因毛刺b的滑行等导致位移,用突出棒
60用力按压毛刺b可使其从成型体分离。
44.另外,在图9所示的例中,模具13设有放气用排气针70,该排气针70穿刺由上述吹气按压的毛刺b,使毛刺b和模具12之间的空气有效排出。因此,排气针70自模具13的突出量优选设定为可以贯穿被吹气按压的毛刺b。但是,排气针70的突出量过大时,穿刺至毛刺b深处,用突出棒60按压毛刺b时难以从毛刺b拔出,优选从被吹气按压的毛刺b突出一点。
45.用上述吹气冷却毛刺b后,如图5所示的,用突出棒60按压刚性增加的毛刺b于相反侧的模具12,以从成型体撕下毛刺b的方式使其分离(切断)。管部2,3外侧的毛刺b在空间37,38,由设于夹紧部35,36附近的突出棒60的突出从成型体分离。管部2,3之间的毛刺b在空间41,由分别设于夹紧部35,36附近的2根突出棒60的突出从成型体分离。
46.由上所述,在模具12,13内从成型体分离毛刺b。即,在本实施方式的吹塑成型方法在模具内完成成型体的成型以及毛刺处理,可进行前所未有的有效的成型以及毛刺处理。
47.以上说明了适用了本发明的第1实施方式,但本发明不限于上述实施方式。在不脱离本发明要旨的范围内,可进行各种变更。
48.例如,可以是在模具内成型体的整周分离毛刺b的形式,但这时存在被彻底分离的毛刺残留在模具内的可能性。这种时候,使毛刺b分离达到毛刺b的部分与成型体连接的状态。上述连接部的分离可在从模具取出成型体后简单进行。
49.另外,在上述模具构成,例如成型体为大型且管部2和管部3之间的距离大时,毛刺b的大小也变大存在突出棒60的力量无法充分传向毛刺b的可能性。此时,在模具设置具有倾斜面的突出部,在倾斜面的顶部使面对面的模具之间的间隔变窄从而夹住这之间的毛刺b,可以可靠地执行各突出棒60的推入。
50.图10表示在管部2,3之间的区域中在图中上方的模具12形成倾斜面的例,图11为图10所示的模具的概略截面图。
51.如图10所示,在管部2,3之间的区域,沿着管部2,3的夹紧部35,36排列着突出棒60。管2,3之间的尺寸大时,即使吹气冷却毛刺b仍然导致毛刺b随意移动,无法充分施加突出棒60的力。
52.在此,在本例中,在模具12形成具有倾斜面81的梯状部82,使毛刺b夹在梯状部82。应予说明,图10中斜线区域为倾斜面81。
53.若在模具12形成具有上述倾斜面81的梯状部82,如图11所示,在该部分模具12和模具13的间隔变小。该间隔若为可维持毛刺b的程度,将成为模具12,13之间夹着毛刺b的状态,如图12所示,将此为支点可靠地向毛刺b传递突出棒60的力量,可顺利进行毛刺b的分离。
54.应予说明,在形成上述倾斜面81的情况下,例如在模具13设置排气针70时,如图13所示,优选面对排气针70的部分设置锪平部83,排气针70不碰撞模具12的倾斜面81。
55.在上一个实施方式说明了吹塑成型型坯p时的例,成型体的制造方法只要是用模具成型板材的方法等成型体周围形成毛刺的制造方法、成型用模具、制造装置,本发明可以应用于它们中的任何一个。
56.接下来,说明结合了上述成型体的制造装置的成型线。如上所述,上一个实施方式中在模具内完成了成型体的成型以及毛刺处理,可进行前所未有有效的成型以及毛刺处理。为了使其进一步有效,可使从毛刺的排除到成型体的输送的一系列工序自动化。
57.图14~图16表示成型线的一个例子。该成型线以具备成型成型体90(相当于上一个实施方式的管1)的模具12,23的成型装置为中心,在其周围配置成型体取出机构91、毛刺排除排出机构(毛刺抓取机器人92以及毛刺输送机93)、成型体90的加工机94、搬出成型体90的成型体搬出机95。
58.成型体取出机构91此处为关节型机器人,具备旋转的多关节臂91a,在其前端具有通过真空吸引等吸附成型体90的头部91b。成型的成型体90由多关节臂91a前端的头部91b吸附维持,随着多关节臂91a的旋转依次移送至加工机94、成型体搬出机95。
59.毛刺排出机构由毛刺抓取机器人92以及毛刺输送机93构成,在模具12、13内用毛刺抓取机器人92的2只臂92a,92b夹住从成型体90分离的毛刺(省略图示),自模具12,13引向毛刺输送机93。由于成型体90的毛刺为从模具12,13突出的形状,可用毛刺抓取机器人92的2只臂92a,92b轻松夹住该部分。
60.加工机94是加工从模具12,13取出的成型体90,例如切除细毛刺。
61.模具12,13中的成型体90的成型以及毛刺的分离完成后,如图14所示模具12,13开模的同时毛刺被毛刺抓取机器人92的2只臂92a,92b引出,被毛刺输送机93排出。另外,成型体90由多关节臂91a前端的头部91b吸附维持,从模具12,13取出。
62.接下来,如图15所示成型体90通过多关节臂91a的水平旋转运动移送至加工机94。移送至加工机94的成型体90切除细毛刺完成为产品。
63.如图16所示,用加工机94完成处理的成型体90通过多关节臂91a的水平旋转运动移送至成型体搬出机95并搬出。即,多关节臂91a旋转1次即可完成从成型体90的模具12,13取出至产品的搬出的一系列工序。
64.考虑到这种成型线的情况下,模具12,13开模时需要使成型体90维持在特定的模具(在此为模具13)。若维持成型体90的模具在每次成型时不同,则成型体取出机构91难以确保取出成型体90。例如,若成型体取出机构91设定为取出维持于模具13的成型体90,成型体90维持于模具12时无法取出。
65.为了消除此类不便,优选实施将成型体90卡定于一个模具。但是需要避免影响到成型体90的产品部分形状的情况。
66.为了实现上述目的,在维持成型体90侧的模具(例如模具13)的废弃袋部分设置帽螺栓96,将该头部96a塞入成型体90的废弃袋部分是有效的。例如在具有开口部的成型体(管等)的吹塑成型,无法在成型时在成型体90形成开口部,成型时以封闭成型体90的方式形成废弃袋部分,之后通过切除该废弃袋部分从而形成开口部。由于废弃袋部分从产品切除,即使在此塞入帽螺栓96也可在不影响产品的前提下在特定的模具13确保留下成型体90。
67.图17表示废弃袋部分的成型状态,其中(a)为未设置作为卡定工具的帽螺栓96的情况下的成型状态、(b)为设置帽螺栓96的情况下的成型状态。未设置帽螺栓96的情况下,废弃袋部分90a的成型状态等价于模具12,13。以该状态开模模具12,13,则存在成型体90留在模具12侧和留在模具13侧的情况。
68.相对于此,若在模具13设置帽螺栓96,帽螺栓96的头部96a将塞入废弃袋部分90a的预定的位置90b,废弃袋部分90a被卡住而成型体90一定会留在模具13侧。
69.应予说明,帽螺栓96应根据成型体90的尺寸和卡住的程度等选择适当的尺寸。帽
螺栓96的尺寸标准化未m8,m6等,选择这些中适当的尺寸设置在模具的废弃袋部分。帽螺栓96可像一般的螺栓安装于模具而容易更换。
70.(2)第2实施方式参照图面详细说明第2实施方式的毛刺去除方法以及毛刺除去装置。
71.图18表示适用了本发明的毛刺除去装置的简要构成。本实施方式的毛刺除去装置如图18所示,将多个按夹具102朝下方安装于上下移动的支撑基板101而成,用上述按夹具102向下方按压形成于放置在接受台103的成型品104周围的毛刺105,从而成型品104撕下毛刺105。
72.按夹具102为棒状的夹具,其前端为平坦面102a,用该平坦面102a向下方推入毛刺105。按夹具102只要是棒状则不限定其结构,例如可使用六角螺栓等。六角螺栓的头部为六角形,通过使其直径大于轴从而使前端面具有一定程度的面积,可稳定地推入毛刺105。另外,六角螺栓如同一般的螺栓通过旋转进退自如,利用此可调节长度。
73.应予说明,上述按夹具102的前端面为平坦面102a,但只要该平坦面102a设有突起,则可防止抵接于毛刺105时按夹具102侧滑。
74.支撑基板101在四个角形成插入孔,支撑轴106插入于此。另外,支撑基板101的背面侧设有按机构107,使该按机构107工作从而使支撑基板101沿着支撑轴106上下移动。特别是,用按机构107向下方推入支撑基板101从而使安装于支撑基板101的按夹具102向下方推入。
75.按夹具102安装于支撑基板101的下表面,例如在支撑基板101的下表面网格的各焦点可以安装按夹具102,通过选择安装按夹具102的交点,可沿着成型品104的外形形状(分界线)排列按夹具102。另外,通过改变安装各按夹具102的交点,可轻松对应成型品104的大小和形状的改变。
76.接下来,说明使用图18所示构成的毛刺除去装置的毛刺去除方法。
77.成型品104例如由吹塑成型得到,从塑模使型坯下垂的方式供给于模具之间,使模具闭模并将空气吹入内部,塑形为模具的型腔形状。在模具的型腔周围,型坯受模具挤压而压碎并形成分界线pl。另外,分界线pl外侧的剩余部分为毛刺105。
78.成型品104是由例如聚乙烯或聚丙烯等聚烯烃树脂形成的,但不限于此,也可以是由任意树脂材料形成的。另外,成型品104可以是非发泡的所谓实心成型品,也可以是由发泡树脂形成的发泡成型体。
79.从模具取出成型后的成型品104,此时周围残留毛刺105。在此,从模具取出的成型品104放置于图18所示的毛刺除去装置的接受台103上。接受台103具有与成型品104大致相同的形状、尺寸,以支撑成型品104的下方的方式形成。毛刺105形成于成型品104周围外方,其下方为没有接受台103的状态。
80.毛刺除去装置中,根据成型品104的形状、大小在支撑基板101排列棒状的按夹具102。图21以及图22表示按夹具102的排列状态。如图21以及图22所示,按夹具102以在成型品104的分界线pl外侧位置与毛刺105抵接的方式排列。优选按夹具102的设置位置与分界线pl的间隔不太大,优选在尽可能靠近分界线pl的位置推入毛刺105。由此,毛刺105从成型品104迅速分离。
81.按夹具102的设置间隔为任意,但设置间隔过大则难以顺利分离除去毛刺105。由
此,为了顺利分离除去毛刺105,优选保持适当间隔设置按夹具102。
82.将成型品104放置于接受台103上,在支撑基板101设置按夹具102后,使按机构107工作,如图19所示向下方推支撑基板101。于此同时下推按夹具102,其前端面102a抵接于毛刺105。如图20所示,若进一步向下方推支撑基板101,则毛刺105被按夹具102进一步推向下方。其结果为,毛刺105被撕下从成型品104快速分离除去。
83.根据使用本实施方式的毛刺除去装置的毛刺去除方法,可将除去残留在成型品104周围的大的毛刺105(去毛刺)所需的周期保持在10秒至20秒左右,与通过手工作业除去这种大的毛刺105时相比大幅降低。
84.以上为适用了本发明的毛刺除去装置、毛刺去除方法的基本构成,本发明的毛刺除去装置、毛刺去除方法可以进行各种设计变更。
85.例如,在之前的例中,在成型品104周围使各按夹具102同时抵接于毛刺105,也可将多个按夹具隔着时差按压于毛刺。根据成型品104的形态,毛刺105的分离难易度根据位置不同。这种情况下,毛刺105易断的位置(毛刺105的易切割部)附近用一个按夹具102按压后,用其他按夹具102按压排列了毛刺105的其他部分从而实现更顺利地除去毛刺105。
86.图23表示隔着时差将按夹具按压于毛刺的例子。这种情况下,首先,将按夹具102a推压向毛刺105易切断位置(毛刺105的易切割部)附近。由此,在按夹具102a附近毛刺105和成型品104之间成为破裂的状态。接下来,将其他按夹具102b按压于毛刺105,则通过推压按夹具102a形成的破裂c遍布整体,从而除去毛刺105。此时,推压按夹具102a之后推压相邻的按夹具102,若进一步按时间顺序从靠近按夹具102a的按夹具102推压,以由按夹具102a的按压形成的破裂为起点破裂逐渐蔓延,可非常顺利除去毛刺105。
87.为了隔着时差将按夹具102按压于毛刺,调节按夹具102的长度从而调节按夹具102的前端面102a和毛刺105的表面的间隔即可。若使按夹具102a的长度成为最长,使其他按夹具102b的长度短于按夹具102a,则通过支撑基板101的下推按夹具102a抵接于毛刺105后,其他按夹具102b将抵接于毛刺105。或者,使按夹具102a的长度成为最长,其他按夹具102随着距按夹具102a的距离变短,将按夹具102a推压至毛刺105后,可从靠近按夹具102a的位置的按夹具102按照时间顺序推压毛刺105。按夹具102的长度可轻松调节,例如使用六角螺栓于按夹具102的情况下,通过旋转该六角螺栓可单独调节长度。
88.另外,根据成型品104,有毛刺105存在难以切割部分的情况。例如图24所示,产品部104a的端部形成有废弃袋104b,形成有连接于废弃袋104b的吹入部104c的成型品104中,废弃袋104b和吹入部104c之间难以切割。这种情况下,可以组合使用切刀的切割和使用按夹具102的切割。
89.即,用刀切割图24所示的x-x线位置的同时,放置与其他部分的毛刺105对应的按夹具102,切除该部分的毛刺105。此时,如同上一个例子,可以用切刀切割的部分为几点,将此扩大的方式切除毛刺105整体。
90.图25表示组合使用切刀的切除和使用按夹具的切除的毛刺除去装置的一个例子。成型品104的产品部104a周围排列按夹具102的同时,吹入部104c的边界部分(图23的x-x线位置)设置有切刀111。按夹具102和切刀111均安装于支撑基板101的下方,通过下推支撑基板101使按夹具102和切刀111同时下降从而抵接于毛刺105。
91.接下来说明分界线pl非水平的成型品104的去毛刺。成型品104的分界线pl不限于
对成型品104整周水平的情况,还可以形成为与分界线pl倾斜的情况。
92.这种情况下,毛刺105也沿着分界线pl倾斜形成,按夹具102抵接于毛刺105的倾斜面。按夹具102抵接于毛刺105的倾斜面时,存在该力无法充分传递到毛刺105的可能性,存在妨碍毛刺105的切除的可能性。
93.这种情况下,沿着分界线pl倾斜形成的斜面毛刺105,如图26所示,通过在按夹具102抵接的位置形成平坦面105a,按夹具102的前端面102a密切接触毛刺105表面,可充分施加按夹具102的按压力。其结果为,在分界线pl倾斜的部分也可充分除去毛刺105。
94.作为毛刺105的形态可采用其他各种形态。例如,由于毛刺105不进行冷却则柔软,用按夹具102按压时,优选充分冷却。另外,毛刺105并非是单纯的板材状,而是在具有立壁的形状时强度高,方便用按夹具102切除。
95.考虑这些事项,如图27所示,优选在形成于成型品104周围的毛刺105形成凸部105b的形态。若在毛刺105形成凸部105b,毛刺105的机械强度增强,可用按夹具102轻松切除毛刺105。
96.上述毛刺105的凸部105b的形成可与成型品104的成型同时在模具内进行。图28表示毛刺105的成型工序。如图28所示,在模具121,122的型腔k1内塑形型坯的方式成型成型品104。另外,成型成型品104时,在型腔k1的外周部分用模具121,122夹住型坯将其压碎。上述压碎形成过程为,第1夹断部p1和第2夹断部p2压碎型坯,由第1夹断部p1在成型品104的外周部形成分界线pl,形成第2夹断部p2外侧的剩余部分105c。
97.图28所示的例中,对应于模具121,122的毛刺105的部分(第1夹断部p1和第2夹断部p2之间的部分)也形成空间k2,通过在此插入吹气针123吹气,可同时进行冷却和塑形。即,在对应于模具121,122的毛刺105的部分形成空间k2,将吹气针123插入该空间k2内进行吹气,则毛刺105接触模具121,122的壁面促进冷却。
98.另外,为了增加吹气针123的行程,优选在插入吹气针123的插入位置扩大空间k2,在本例中,关于吹气针123的插入位置,在模具121,122形成有凹部。因此,毛刺105根据该凹部塑形,作为结果,毛刺105形成有凸部105b。毛刺105中凸部105b的形成导致立壁的形成,从而使机械强度大幅增加。
99.由于上述毛刺105的冷却的促进和凸部105b的形成导致机械强度的增加,从模具121,122取出的成型品104的毛刺105的刚性优异,可使用按夹具102轻松冲模。
100.以这种形态切除毛刺105时,优选在毛刺105外侧也设置接受台,以用按夹具102进行按压。图29表示在毛刺105的外侧设置接受台的毛刺去除工序。如上所述,为了充分冷却毛刺105,提高机械强度,从模具121,122取出设有凸部105b的成型品104,放置成型品104于毛刺除去装置的接受台103。毛刺105下方无接受台103,相对于毛刺105的按夹具102抵接的位置的外侧(本例中是凸部105b外侧且是剩余部分105c内侧)设置接受台130,使其支撑成型品104的下表面和毛刺105外周部的下表面。
101.该状态下用按夹具102按压切除毛刺105。通过在按夹具102的抵接位置的外侧设置接受台130,此处成为支点,按夹具102的力有效施加于作为作用点的上述按夹具102的抵接位置,毛刺105易于冲模。另外,通过在按夹具102的抵接位置的外侧设置接受台130,具有毛刺105易于除去的优点。
102.接受台130的位置在上述按夹具102的抵接位置的外侧,优选作为容纳毛刺105中
通过吹气塑形的部分的外侧部分。即,按夹具102的抵接位置的外侧、第2夹断部p2的内侧。第2夹断部p2外侧的剩余部分105c是所谓的自由状态,即使用接受台130支撑此处也不会产生支点的功能。通过用接受台130支撑第2夹断部p2内侧附近,在一定程度上达到支撑具有刚性的部分,有效发挥支点的功能。
103.以上说明了适用本发明的第2实施方式,但本发明不限于上述实施方式。在不脱离本发明要旨的范围内,可进行各种变更。【符号说明】
104.1 管2、3 管部4 连接管部11 环状模具12、13 模具31、32、33、34 凹部35、36 夹紧部(第1夹紧部)37、38 空间39、40 夹紧部(第2夹紧部)41 空间50 喷气孔60 突出棒70 排气针81 倾斜面82 梯状部c1、c2 型腔90 成型体91 成型体取出机构92 毛刺抓取机器人93 毛刺输送机94 加工机95 成型体搬出机96 帽螺栓101 支撑基板102 按夹具103 接受台104 成型品105 毛刺105a 平坦面105b 凸部106 支撑轴107 按机构
111 切刀121、122 模具130 接受台。