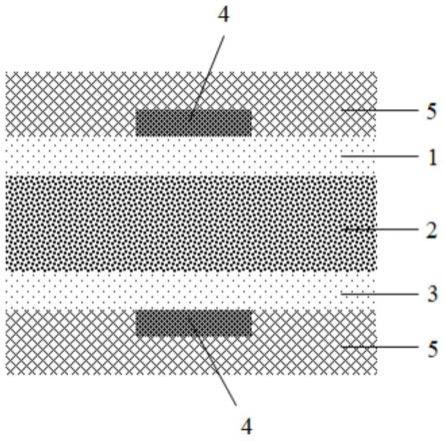
1.本发明属于汽车内饰件技术领域,涉及一种行李箱盖板及其制备方法和应用,尤其涉及一种高强度行李箱盖板及其制备方法和应用。
背景技术:2.行李箱盖板是车辆行李箱中的内饰之一,能取下或翻动,方便备胎及相关的物品放置在行李箱盖板上,起到装饰和必须的承重作用。
3.目前汽车行李箱盖板的材质选择主要包括pp板/gf板、pp蜂窝板、phc板,但随着suv、crv车辆的普及及后备箱市集的流行,行李箱盖板的承重要求日趋增大,采用上述材质制备的行李箱盖板的强度已不能满足使用要求,或者有些行李箱盖板的强度在普通气候条件下可以满足要求,但在一些极端气候条件(例如高温气候或者极寒气候)下其不能满足使用要求。
4.cn105058931a公开了一种汽车行李箱盖板的生产方法,包括以下步骤:行李箱盖板基材加热步骤、铺放pu板步骤、盖板大面毯喷胶步骤、小板与盖板大面毯粘合步骤、小板位置喷胶步骤、小面毯粘合步骤、裁剪步骤、行李箱盖板半成品喷胶步骤、行李箱盖板半成品保压步骤、在行李箱盖板粗品上安装附件步骤。该发明工艺稳定,确保了产品的准确度,同时提升了作业效率;整个生产过程没有有害物质产生,属于环保工艺。但该发明的行李箱盖板的基材为pp板和gf板复合而成的板体,行李箱盖板的强度有待进一步提高。
5.cn103395272a公开了一种汽车行李箱盖板的生产工艺,其采用以下工艺步骤:将面毯平放在斩刀模中斩切成所需的形状;所述面毯放在贴合模上固定,面毯的正面朝下,并对面毯的背面和基材的背面喷涂聚烯烃胶水,面毯的背面与基材的正面贴合,得到汽车行李箱盖板粗品;将行李箱盖板面料的正面与汽车行李箱盖板粗品中基材的背面贴合,得到汽车行李箱盖板半成品;最后将汽车行李箱盖板半成品放置在压合模中进行压制,压制好后形成汽车行李箱盖板。该发明的方法工艺简单、工序步骤少、生产过程中无有害物质的产生,环保无污染,降低了制造成本,大大提高了汽车行李箱盖板的装车精度要求及提升隔音效果。但该发明的行李箱盖板的基材为pp蜂窝板或者硬质木板,行李箱盖板的强度有待进一步提高。
6.因此,在本领域中,期望开发一种行李箱盖板,其具有较高的强度,并且可以适应各种气候条件。
技术实现要素:7.针对现有技术的不足,本发明的目的在于提供一种行李箱盖板及其制备方法和应用,具体提供一种高强度行李箱盖板及其制备方法和应用。
8.为达到此发明目的,本发明采用以下技术方案:
9.第一方面,本发明提供一种行李箱盖板的制备方法,所述制备方法包括以下步骤:
10.(1)预埋:将两片钢板分别预埋于模具的上下型腔内;
11.(2)按照从上到下的顺序将上层玻璃纤维毡、纸蜂窝和下层玻璃纤维毡铺放整齐,送入喷料舱,然后向上层玻璃纤维毡的上表面和下层玻璃纤维毡的下表面喷洒聚氨酯发泡料,得到半成品;
12.(3)压制成型带冲切:将步骤(2)得到的半成品送至模具中与步骤(1)预埋的钢板一起进行压制成型带冲切,得到盖板粗品;
13.(4)面毯滚胶:将面毯进行滚胶,得到滚胶后的面毯;
14.(5)包边:将步骤(3)得到的盖板粗品和步骤(4)得到的滚胶后的面毯放入包边设备中进行包边,得到所述行李箱盖板。
15.在本发明中,通过将两片钢板分别预埋于模具的上下型腔内,然后再与步骤(2)得到的半成品一起进行压制成型带冲切,聚氨酯发泡料发泡后可以将钢板包裹,从而使得制备的行李箱盖板具有较高的强度,承载性好,并且可以适用于各种气候条件;通过包边的步骤可以使得制备的行李箱盖板无锋利边缘。此外,采用本发明的制备方法,生产过程没有有害物质产生,环保节能。
16.本发明提供的行李箱盖板可以作为汽车行李箱盖板多功能使用。
17.需要说明的是,步骤(3)中,将步骤(2)得到的半成品送至模具中,半成品在模具中位于两片钢板之间,即,位于模具上型腔内的钢板在半成品的上方,位于模具下型腔内的钢板在半成品的下方。但本发明对于钢板的具体位置不作限定,例如,钢板的长度方向可以与半成品的长度方向平行,也可以与半成品的长度方向垂直,也可以与半成品的长度方向形成其他角度,当然,上下两片钢板可以对称放置,也可以不对称放置,这些可以根据客户的需求进行设置。
18.优选地,步骤(1)所述钢板的长度为500~1500mm,例如可以是600、700、800、900、1000、1100、1200、1300或1400mm等,宽度为20~100mm,例如可以是30mm、40mm、50mm、60mm、70mm、80mm或90mm等,厚度为0.5~3mm,例如可以是0.6mm、0.8mm、1mm、1.3mm、1.5mm、1.8mm、2mm、2.3mm、2.5mm或2.8mm等,但上述数值并不仅限于所列举的数值,该数值范围内其他未列举的数值同样适用。上述对钢板尺寸的限定指的是两片钢板的尺寸均在上述范围内,两片钢板的尺寸可以相同,也可以不相同。
19.若钢板的厚度过小,承载相对较差,若钢板的厚度过大,承载要求相对较高,但重量较重。
20.优选地,步骤(2)所述上层玻璃纤维毡和下层玻璃纤维毡的克重各自独立地为400~700g/m2,例如可以是450g/m2、500g/m2、550g/m2、600g/m2或650g/m2等,但并不仅限于所列举的数值,该数值范围内其他未列举的数值同样适用。
21.优选地,步骤(2)所述上层玻璃纤维毡和下层玻璃纤维毡的厚度各自独立地为0.5~2mm,例如可以是0.8mm、1mm、1.3mm、1.5mm或1.8mm等,但并不仅限于所列举的数值,该数值范围内其他未列举的数值同样适用。
22.作为本发明的优选技术方案,上层玻璃纤维毡和下层玻璃纤维毡的克重相同,厚度也相同。
23.优选地,步骤(2)所述纸蜂窝的克重为600~1800g/m2,例如可以是650g/m2、700g/m2、800g/m2、900g/m2、1000g/m2、1100g/m2、1200g/m2、1300g/m2、1400g/m2、1500g/m2、1600g/m2或1700g/m2等,但并不仅限于所列举的数值,该数值范围内其他未列举的数值同样适用。
24.优选地,步骤(2)所述纸蜂窝的厚度为10~30mm,例如可以是13mm、15mm、18mm、20mm、23mm、25mm或28mm等,但并不仅限于所列举的数值,该数值范围内其他未列举的数值同样适用。
25.优选地,步骤(2)所述聚氨酯发泡料的喷洒量为300~800g/m2,例如可以是350g/m2、400g/m2、450g/m2、500g/m2、550g/m2、600g/m2、650g/m2、700g/m2或750g/m2等,但并不仅限于所列举的数值,该数值范围内其他未列举的数值同样适用。本发明所述聚氨酯发泡料可以直接购买得到。
26.优选地,步骤(3)所述模具为热模。
27.优选地,所述热模的温度为80~140℃,例如可以是90℃、100℃、110℃、120℃或130℃等,但并不仅限于所列举的数值,该数值范围内其他未列举的数值同样适用。
28.优选地,步骤(3)所述压制成型带冲切的压力为5~20mpa,例如可以是6mpa、7mpa、8mpa、9mpa、10mpa、11mpa、12mpa、13mpa、14mpa、15mpa、16mpa、17mpa、18mpa或19mpa等,成型时间为50~60s,例如可以是51s、52s、53s、54s、55s、56s、57s、58s或59s等,但上述数值并不仅限于所列举的数值,该数值范围内其他未列举的数值同样适用。
29.优选地,步骤(4)所述面毯的克重为150~450g/m2,例如可以是180g/m2、200g/m2、230g/m2、250g/m2、280g/m2、300g/m2、330g/m2、350g/m2、380g/m2、400g/m2或430g/m2等,但并不仅限于所列举的数值,该数值范围内其他未列举的数值同样适用。
30.优选地,步骤(4)所述面毯的材质为聚对苯二甲酸乙二醇酯(pet),风格为起绒或者不起绒。
31.优选地,步骤(4)所述面毯的厚度为1~5mm,例如可以是2mm、3mm或4mm等,但并不仅限于所列举的数值,该数值范围内其他未列举的数值同样适用。
32.优选地,步骤(4)所述滚胶的胶水为聚氨酯胶,其可以直接购买得到。
33.优选地,步骤(4)所述滚胶的胶机温度为10℃~40℃,例如可以是15℃、20℃、25℃、30℃或35℃等,但并不仅限于所列举的数值,该数值范围内其他未列举的数值同样适用。
34.优选地,步骤(4)所述滚胶的滚胶量为10~25g/m2,例如可以是13g/m2、15g/m2、18g/m2、20g/m2或23g/m2等,但并不仅限于所列举的数值,该数值范围内其他未列举的数值同样适用。
35.作为本发明的优选技术方案,所述行李箱盖板的制备方法包括以下步骤:
36.(1)预埋:将两片长度为500~1500mm,宽度为20~100mm,厚度为0.5~3mm的钢板分别预埋于模具的上下型腔内;
37.(2)按照从上到下的顺序将克重为400~700g/m2的上层玻璃纤维毡、克重为600~1800g/m2的纸蜂窝和克重为400~700g/m2的下层玻璃纤维毡铺放整齐,送入喷料舱,然后按照300~800g/m2的喷洒量分别向上层玻璃纤维毡的上表面和下层玻璃纤维毡的下表面喷洒聚氨酯发泡料,得到半成品;
38.(3)压制成型带冲切:将步骤(2)得到的半成品送至模具中与步骤(1)预埋的钢板一起进行压制成型带冲切,得到盖板粗品;其中,模具为热模,压制成型带冲切的压力为5~20mpa,成型时间为50~60s;
39.(4)面毯滚胶:将克重为150~450g/m2的面毯进行滚胶,得到滚胶后的面毯;其中,
滚胶的胶水为聚氨酯胶,胶机温度为10℃~40℃,滚胶量为10~25g/m2;
40.(5)包边:将步骤(3)得到的盖板粗品和步骤(4)得到的滚胶后的面毯放入包边设备中进行包边,得到所述行李箱盖板。
41.第二方面,本发明提供一种行李箱盖板,所述行李箱盖板根据第一方面所述的制备方法制备得到。
42.第三方面,本发明提供一种如第二方面所述的行李箱盖板在汽车行李箱中的应用。
43.优选地,本发明提供的行李箱盖板应用于suv车型的行李箱。
44.相对于现有技术,本发明具有以下有益效果:
45.在本发明中,通过将两片钢板分别预埋于模具的上下型腔内,然后再与步骤(2)得到的半成品一起进行压制成型带冲切,聚氨酯发泡料发泡后可以将钢板包裹,从而使得制备的行李箱盖板具有较高的强度,承载性好(常温状态下的最大变形量为8-15mm),并且可以适用于各种气候条件;通过包边的步骤可以使得制备的行李箱盖板无锋利边缘。此外,采用本发明的制备方法,生产过程没有有害物质产生,环保节能。
附图说明
46.图1为本发明实施例1提供的行李箱盖板的结构示意图。
47.其中,1-上层玻璃纤维毡,2-纸蜂窝,3-下层玻璃纤维毡,4-钢板,5-聚氨酯发泡层。
具体实施方式
48.下面通过具体实施方式来进一步说明本发明的技术方案。本领域技术人员应该明了,所述实施例仅仅是帮助理解本发明,不应视为对本发明的具体限制。
49.本发明实施例及对比例所用的聚氨酯发泡料是由质量比为1:1.6的a料和b料混合得到,其中,a料的牌号为gn8007,b料的牌号为44v20l;聚氨酯胶的牌号为1923。
50.实施例1
51.在本实施例中提供一种行李箱盖板,制备方法包括以下步骤:
52.(1)预埋:将两片长度均为800mm,宽度均为60mm,厚度均为2mm的钢板分别预埋于模具的上下型腔内;
53.(2)按照从上到下的顺序将克重为500g/m2、厚度为1mm的上层玻璃纤维毡,克重为1200g/m2、厚度为20mm的纸蜂窝和克重为500g/m2、厚度为1mm的下层玻璃纤维毡铺放整齐,送入喷料舱,然后按照500g/m2的喷洒量分别向上层玻璃纤维毡的上表面和下层玻璃纤维毡的下表面喷洒聚氨酯发泡料,得到半成品;
54.(3)压制成型带冲切:将步骤(2)得到的半成品送至模具中与步骤(1)预埋的钢板一起进行压制成型带冲切,得到盖板粗品;其中,模具为热模(温度为120℃),压制成型带冲切的压力为15mpa,成型时间为55s;
55.(4)面毯滚胶:将克重为300g/m2、厚度为2.5mm、材质为pet的面毯进行滚胶,得到滚胶后的面毯;其中,滚胶的胶水为聚氨酯胶,胶机温度为25℃,滚胶量为20g/m2;
56.(5)包边:将步骤(3)得到的盖板粗品和步骤(4)得到的滚胶后的面毯放入包边设
备中进行包边,得到所述行李箱盖板。
57.其中,步骤(3)中,将步骤(2)得到的半成品送至模具中,半成品在模具中位于两片钢板之间,两片钢板对称放置,其长度方向与半成品的长度方向平行。
58.本实施例提供的行李箱盖板的结构示意图如图1所示,其中,聚氨酯发泡层由聚氨酯发泡料发泡得到。
59.实施例2
60.在本实施例中提供一种行李箱盖板,制备方法包括以下步骤:
61.(1)预埋:将两片长度均为500mm,宽度均为20mm,厚度均为0.5mm的钢板分别预埋于模具的上下型腔内;
62.(2)按照从上到下的顺序将克重为400g/m2、厚度为0.5mm的上层玻璃纤维毡,克重为600g/m2、厚度为10mm的纸蜂窝和克重为400g/m2、厚度为0.5mm的下层玻璃纤维毡铺放整齐,送入喷料舱,然后按照300g/m2的喷洒量分别向上层玻璃纤维毡的上表面和下层玻璃纤维毡的下表面喷洒聚氨酯发泡料,得到半成品;
63.(3)压制成型带冲切:将步骤(2)得到的半成品送至模具中与步骤(1)预埋的钢板一起进行压制成型带冲切,得到盖板粗品;其中,模具为热模(温度为80℃),压制成型带冲切的压力为5mpa,成型时间为50s;
64.(4)面毯滚胶:将克重为150g/m2、厚度为1mm、材质为pet的面毯进行滚胶,得到滚胶后的面毯;其中,滚胶的胶水为聚氨酯胶,胶机温度为10℃,滚胶量为10g/m2;
65.(5)包边:将步骤(3)得到的盖板粗品和步骤(4)得到的滚胶后的面毯放入包边设备中进行包边,得到所述行李箱盖板。
66.其中,步骤(3)中,将步骤(2)得到的半成品送至模具中,半成品在模具中位于两片钢板之间,两片钢板对称放置,其长度方向与半成品的长度方向平行。
67.实施例3
68.在本实施例中提供一种行李箱盖板,制备方法包括以下步骤:
69.(1)预埋:将两片长度均为1500mm,宽度均为100mm,厚度均为3mm的钢板分别预埋于模具的上下型腔内;
70.(2)按照从上到下的顺序将克重为700g/m2、厚度为2mm的上层玻璃纤维毡,克重为1800g/m2、厚度为30mm的纸蜂窝和克重为700g/m2、厚度为2mm的下层玻璃纤维毡铺放整齐,送入喷料舱,然后按照800g/m2的喷洒量分别向上层玻璃纤维毡的上表面和下层玻璃纤维毡的下表面喷洒聚氨酯发泡料,得到半成品;
71.(3)压制成型带冲切:将步骤(2)得到的半成品送至模具中与步骤(1)预埋的钢板一起进行压制成型带冲切,得到盖板粗品;其中,模具为热模(温度为140℃),压制成型带冲切的压力为20mpa,成型时间为60s;
72.(4)面毯滚胶:将克重为450g/m2、厚度为5mm、材质为pet的面毯进行滚胶,得到滚胶后的面毯;其中,滚胶的胶水为聚氨酯胶,胶机温度为40℃,滚胶量为25g/m2;
73.(5)包边:将步骤(3)得到的盖板粗品和步骤(4)得到的滚胶后的面毯放入包边设备中进行包边,得到所述行李箱盖板。
74.其中,步骤(3)中,将步骤(2)得到的半成品送至模具中,半成品在模具中位于两片钢板之间,两片钢板对称放置,其长度方向与半成品的长度方向平行。
75.实施例4
76.本实施例与实施例1不同之处仅在于,步骤(1)中两片钢板的厚度均为1mm。
77.实施例5
78.本实施例与实施例1不同之处仅在于,步骤(1)中两片钢板的厚度均为1.5mm。
79.实施例6
80.本实施例与实施例1不同之处仅在于,步骤(1)中两片钢板的厚度均为0.3mm。
81.对比例1
82.本对比例与实施例1不同之处仅在于,将步骤(1)中两片钢板均替换为相同尺寸的合金铝板。
83.对比例2
84.本对比例与实施例1不同之处仅在于,将步骤(1)中预埋于模具上型腔内的钢板替换为相同尺寸的碳纤维板。
85.对比例3
86.本对比例与实施例1不同之处仅在于,将步骤(1)中预埋于模具下型腔内的钢板替换为相同尺寸的玻纤板。
87.对实施例1-6以及对比例1-3提供的行李箱盖板进行常温状态下的最大变形量测试,测试方法如下:将行李箱盖板的四边用长度为1m、宽度为4.5cm的铝合金管支撑,将接触面积直径为100mm,重量为100kg的负荷压在行李箱盖板的中心位置,测试2h后的行李箱盖板的最大变形量。
88.性能测试结果如表1所示。
89.表1
[0090][0091]
由表1可以看出,本发明实施例1-5提供的行李箱盖板在常温状态下的最大变形量为8-15mm,承载性好。与实施例1相比,实施例6提供的行李箱盖板在常温状态下的最大变形量明显增大,这是由于钢板的厚度太小。与实施例1相比,对比例1-2提供的行李箱盖板在常温状态下的最大变形量均稍微增大,而对比例3提供的行李箱盖板在常温状态下的最大变形量明显增大。
[0092]
申请人声明,本发明通过上述实施例来说明本发明的行李箱盖板及其制备方法和应用,但本发明并不局限于上述实施例,即不意味着本发明必须依赖上述实施例才能实施。所属技术领域的技术人员应该明了,对本发明的任何改进,对本发明所选用原料的等效替换及辅助成分的添加、具体方式的选择等,均落在本发明的保护范围和公开范围之内。