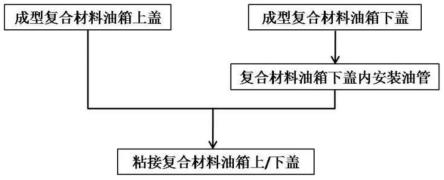
1.本发明属于弹载储油装置复合材料成型工艺技术领域,具体涉及一种轻量化弹载用复合材料油箱及其制造方法。
背景技术:2.当前国际环境日趋复杂,国际形式越加严峻,国家间的军备竞赛对先进武器装备的性能要求越来越高,而武器轻量化是飞航导弹领域长期以来追求的性能目标,也是实现其他装备性能的关联指标。油箱作为飞航导弹的关键部件,其重量对飞航导弹总重起决定性影响。
3.通常飞航导弹装载用油箱为金属油箱,而金属油箱主要有以下缺点:1)质量大;2)耐腐蚀能力差;3)易产生静电,安全性低;4)成型工艺复杂;5)加工制造成本高。
4.因此,为满足武器装备轻量化需求,同时解决上述金属油箱在飞航导弹领域的不足,复合材料油箱在飞航导弹领域应用的呼声越来越高。复合材料油箱具有质量轻、防腐蚀能力强、安全性高、制造简单、生产成本低等优点,可弥补金属油箱带来的不足,经查发现复合材料油箱在飞航导弹领域大型弹身舱段的应用仍属空白。
技术实现要素:5.有鉴于此,本发明的目的在于克服金属油箱在飞航导弹领域应用带来的不足,填补复合材料油箱在飞航导弹领域大型弹身舱段应用的空白,提供一种在飞航导弹领域应用的轻量化复合材料油箱的制造方法。
6.为达到上述目的,本发明的技术解决方案是:弹载用油箱壳体采用复合材料薄壁泡沫夹芯结构,同时飞航导弹油箱内部结构复杂,为满足其使用要求,将油箱分为上下两部分,即上盖和下盖,通过膨胀膜成型方法对复合材料油箱上盖和下盖分别成型,然后利用室温固化胶密封粘接上盖和下盖来制造复合材料油箱。其中,为满足结构强度和刚度要求,复合材料油箱内部的防晃板和筋板需与油箱上盖和下盖整体固化成型,且需要在防晃板和筋板的底部铺放加强筋以提高复合材料油箱抗压能力。采用此种方法成型,能够制造出长度大于2m且内部结构复杂承压能力强的复合材料油箱。
7.本发明通过以下技术方案实现:
8.一种轻量化弹载用复合材料油箱,包括复合材料油箱上盖和复合材料油箱下盖;所述复合材料油箱上盖和所述复合材料油箱下盖为薄壁泡沫夹芯结构,包括外蒙皮、泡沫、内蒙皮;所述复合材料油箱上盖和所述复合材料油箱下盖之间通过粘接胶密封。
9.进一步地,所述复合材料油箱上盖内部设置防晃板,防晃板与复合材料油箱上盖整体固化成型;所述复合材料油箱下盖内部设置防晃板和筋板,防晃板和筋板与复合材料油箱下盖整体固化成型;在防晃板和筋板的底部铺放加强筋以提高复合材料油箱的抗压能力。
10.进一步地,所述复合材料油箱的成型材料体系,包括纤维增强树脂(即外蒙皮、内
蒙皮的材料)、泡沫和胶膜。
11.优选地,所述纤维为碳纤维,纤维种类根据产品结构特点和设计承载进行选择,如t700级、t800级、t1000级等一种或几种,增强织物的形式可以是平纹织物、缎纹织物、斜纹织物、纬编织物及经编织物,优先选择具备良好的铺贴性能,能够满足复杂曲面构件的铺贴要求,并且与环氧树脂混合后有利于环氧树脂的浸润性,进一步提高成型质量。
12.优选地,根据固化要求,所述树脂为中温环氧树脂体系,树脂的具体种类没有特殊限制,根据设计要求选择,如9368、8522、6808、9a16、em817b、em134等的一种或几种。
13.优选地,所述泡沫为聚甲基丙烯酰亚胺(pmi)泡沫芯板,优先选择具备良好的弯曲铺贴性能,泡沫的具体种类没有特殊限制,根据设计要求选择,如xk110-ht、ck110-ht、a-110、c-110和af-110等的一种或几种。
14.优选地,根据固化要求,所述胶膜为中温胶膜,胶膜的具体种类没有特殊限制,根据设计要求选择,如j-47a、j-78b、j-69d和ad-36等的一种或几种。
15.进一步地,所述复合材料油箱的成型结构形式为外蒙皮+泡沫+内蒙皮,其中外蒙皮厚度为1.8-2.2mm,泡沫厚度为5.8-6.2mm,内蒙皮厚度为1.8-2.2mm,其中复合材料与泡沫以及泡沫与泡沫之间需铺放一层胶膜;油箱内防晃板和筋板也为泡沫夹芯结构(复合材料+泡沫+复合材料),其中防晃板的复合材料总厚度为1.5-2mm,泡沫厚度为2.8-3.2mm,筋板的复合材料总厚度为5.8-6.2mm,泡沫厚度为3.8-4.2mm。油箱上下盖内外蒙皮采用准各向同性铺贴方式。
16.一种轻量化弹载用复合材料油箱的制造方法,通过以下步骤实现:
17.步骤一:成型复合材料油箱上盖;
18.步骤二:成型复合材料油箱下盖;
19.步骤三:在复合材料油箱下盖中安装油管;
20.步骤四:粘接复合材料油箱上盖和复合材料油箱下盖。
21.进一步地,步骤一:成型复合材料油箱上盖,包括:
22.(1)根据油箱外形及内部结构尺寸,利用三维建模软件设计模具,要求模具内型与油箱上盖外型保持一致,模具内设计成型芯块保证油箱壳体内部复杂结构成型;
23.(2)根据建立好的三维结构模型制造成型模具,所述成型模具包括模具上/下盖板、前后边条、左右边条、成型芯块、预成型镶块以及加压紧固螺钉;所述模具下盖板与前后边条和左右边条组成上端开口的外型模具,待所有铺层结束后,由上盖板将模具封闭;所述成型芯块和预成型镶块用于成型油箱内部复杂结构,包括防晃板的整体成型以及设备口盖和左右口盖位置的预留,通过在成型芯块间放置橡胶膜进行加压升温膨胀得到满足内部质量和结构强度的油箱壳体;
24.(3)在所述上端开口的外型模具内依次铺放外蒙皮、加强筋、泡沫、内蒙皮,在外蒙皮和泡沫铺放完毕后各进行真空预压实一次;
25.(4)内蒙皮铺层结束后,在模具内按顺序铺放成型芯块、防晃板以及橡胶条;
26.(5)铺放完毕后,将上盖板扣到模具上,检测合模间隙,若合模间隙过大,需检查上盖板四周是否完全扣紧模具,有无卡塞等情况,若无卡塞,需紧固加压螺钉,直至满足合模间隙,完成模具合模;
27.(6)烘箱固化成型,将合模后的模具推进烘箱进行固化;
28.(7)脱模、修整:固化结束后,打开上盖板拆除掉模具内芯块,取出产品进行飞边修整得到复合材料油箱上盖。
29.进一步地,步骤二:成型复合材料油箱下盖,包括:
30.(1)根据油箱外形及内部结构尺寸,利用三维建模软件设计模具,要求模具内型与油箱下盖外型保持一致,模具内设计成型芯块保证油箱壳体内部复杂结构成型;
31.(2)根据建立好的三维结构模型制造成型模具,所述成型模具包括模具上/下盖板、前后边条、左右边条、成型芯块、预成型镶块以及加压紧固螺钉;所述模具下盖板与前后边条和左右边条组成上端开口的外型模具,待所有铺层结束后,由上盖板将模具封闭;所述成型芯块和预成型镶块用于成型油箱内部复杂结构,包括防晃板和筋板的整体成型以及过线孔和钢衬套位置的预留,通过在成型芯块间放置橡胶膜进行加压升温膨胀得到满足内部质量和结构强度的油箱壳体;
32.(3)在所述上端开口的外型模具内依次铺放外蒙皮、加强筋、泡沫、内蒙皮,在外蒙皮和泡沫铺放完毕后各进行真空预压实一次;
33.(4)内蒙皮铺层结束后,在模具内按顺序铺放成型芯块、防晃板、筋板以及橡胶条;
34.(5)铺放完毕后,将上盖板扣到模具上,检测合模间隙,若合模间隙过大,需检查上盖板四周是否完全扣紧模具,有无卡塞等情况,若无卡塞,需紧固加压螺钉,直至满足合模间隙,完成模具合模;
35.(6)烘箱固化成型,将合模后的模具推进烘箱进行固化;
36.(7)脱模、修整:固化结束后,打开上盖板拆除掉模具内芯块,取出产品进行飞边修整得到复合材料油箱下盖。
37.进一步地,步骤三:安装油管,包括:
38.得到复合材料油箱下盖后,利用开孔器对油箱下盖内部防晃板以及下盖前部和后部进行开孔,然后安装油管,同时对开孔处进行密封处理,拧紧固定油管的内外螺母完成油管的安装。
39.进一步地,步骤四:粘接复合材料油箱上/下盖,包括:
40.(1)在复合材料油箱上盖和下盖搭接区域均匀涂抹粘接胶;
41.(2)将上盖平稳扣到下盖上,确保搭接区域对接完全同时保证搭接缝中能够挤出粘接胶;
42.(3)采用绑带或在油箱上盖放置重物的方式进行加压固化;
43.(4)卸压、修整:固化结束后,对粘接区域进行打磨修整,确保表面平整无棱刺。
44.所述步骤一和步骤二中模具的精度为0~0.6mm,外型模具材料采用p20钢,内部芯块采用6061铝合金。
45.所述步骤一和步骤二在外型模具内铺放外蒙皮之前,需铺放一层增强织物。
46.所述步骤一和步骤二的外蒙皮采用单向预浸料铺放,铺放方式采用准各向同性铺放。
47.所述步骤一和步骤二的泡沫铺放采用单层泡沫,泡沫与预浸料之间铺放一层胶膜。
48.所述步骤一和步骤二中加强筋铺放位置位于防晃板位置的底部,替代原有泡沫,加强筋宽度9.8-10.2mm,厚度5.8-6.2mm。
49.所述步骤一和步骤二的内蒙皮采用单向预浸料铺放,铺放方式采用准各向同性铺放。
50.所述步骤一和步骤二的内蒙皮铺放结束后,需铺放一层增强织物。
51.所述步骤一和步骤二的内蒙皮铺放结束后,需用裁纸刀沿模具刻线将多余蒙皮裁减掉。
52.所述步骤一和步骤二的防晃板和筋板需要预制,预制后再随芯块一同铺放与内蒙皮连接,包覆防晃板和筋板的预浸料铺放方式采用准各向同性铺放。
53.所述步骤一和步骤二的单向预浸料铺层不采用搭接,只允许沿纤维方向对接,即对接缝隙平行于纤维方向,对接缝隙宽度≤2mm。织物预浸料铺层采用搭接,搭接宽度在15mm~25mm之间。相邻铺层的拼接位置不允许在同一处出现,需错开20mm以上。如果在同一位置拼接,至少应相隔4层铺层。
54.所述步骤一和步骤二的铺层应保持厚度光滑变化,铺层增减形成的厚度变化区及铺层跨越圆角或台阶处,不允许有架桥现象。
55.所述步骤一和步骤二的铺放泡沫时圆角处尽量多的铺放泡沫,无法铺放泡沫的空隙需用预浸料填实。
56.所述步骤一和步骤二的真空预压实参数要求为真空度≥0.09mpa,温度50
±
5℃,时间≥30min。
57.所述步骤一和步骤二拆除芯块时,未必严格按顺序拆除。
58.所述步骤三中油管安装需分别位于油箱的最高点和最低点位置。
59.所述步骤四中的粘接胶为室温固化粘接胶。
60.本发明与现有技术相比的有益效果:
61.(1)本发明提出了一种轻量化弹载用复合材料油箱的制造方法,克服了金属油箱质量大、耐腐蚀能力差、安全性低、成型难度高的缺点,填补了在飞航导弹领域使用复合材料油箱的空白。
62.(2)本发明创新性的使用薄壁复合材料泡沫夹芯结构制造复合材料油箱,不仅进一步减轻了油箱的重量,还大大降低了生产成本,既满足了设计要求,又具有良好的经济效益。
63.(3)往往弹载用油箱结构复杂,复合材料油箱替代困难,本发明提供了成型复杂结构件的新思路,解决了复合材料油箱壳体内部结构复杂难于成型的问题,与其他固化工艺相比,本发明固化工艺简单,操作方便,为后续同类型复合材料油箱的研制提供了有效的借鉴意义。
附图说明
64.图1是本发明实施例提供的一种轻量化弹载用复合材料油箱制造方法的流程图。
65.图2是本发明方法中复合材料油箱上盖壳体的轴测图。
66.图3是本发明方法中复合材料油箱上盖壳体成型模具的轴测图。
67.图4是本发明方法中复合材料油箱下盖壳体的轴测图。
68.图5是本发明方法中复合材料油箱下盖壳体成型模具的轴测图。
69.图6是本发明方法中复合材料油箱下盖安装油管示意图。
70.图7是本发明方法中复合材料油箱上/下盖粘接后的外形图。
71.附图标记说明:1—左口盖,2—右口盖,3—设备口盖,4,15—防晃板,5,19—搭接区域,6,20—下盖板,7,21—上盖板,8,22—前边条,9,23—后边条,10,24—左边条,11,25—右边条,12,26—成型芯块,13,27—预成型镶块,14,28—加压螺钉,16—筋板,17—钢衬套,18—过线孔,29—油管(低点),30—油管(高点)。
具体实施方式
72.为使本发明的技术方案能更明显易懂,特举实施例并结合附图详细说明如下。
73.实施例1
74.如图1所示,本实施例提供一种轻量化弹载用复合材料油箱的制造方法,该制造方法主要包括如下步骤:
75.(1)成型复合材料油箱上盖,所述上盖内含防晃板的整体成型以及口盖位置的预留;
76.(2)成型复合材料油箱下盖,所述下盖内含筋板和防晃板的整体成型以及过线孔、钢衬套等位置的预留;
77.(3)复合材料油箱下盖内安装油管,所述油管材质为5a06铝;
78.(4)使用室温固化粘接胶粘接复合材料油箱上/下盖,所述粘接胶为j-133c。
79.实施例2
80.图2是本发明的复合材料油箱上盖,包括左口盖1,右口盖2,设备口盖3,防晃板4,搭接区域5。图3是本发明的复合材料油箱上盖壳体成型模具,包括下盖板6,上盖板7,前边条8,后边条9,左边条10,右边条11,成型芯块12,预成型镶块13,加压螺钉14。
81.如图2、图3所示,本实施例提供一种成型复合材料油箱上盖的方法,步骤如下:
82.(1)根据产品结构及外形,兼顾铺层工艺和成型方法,综合各种条件利用三维建模软件建立实体模型,设计成型模具;按照设计思路,复合材料油箱上盖结构为薄壁泡沫夹芯结构(外蒙皮+泡沫+内蒙皮),铺层在成型模具内按阴模随型铺覆以确保产品外形尺寸,同时在阴模内放置防晃板、成型芯块、预成型镶块以及橡胶条等保证油箱内部复杂结构;
83.(2)成型材料根据产品特点和承载要求,本实施例选择铺覆性能好的t300级平纹碳布/9a16预浸料、t700级单向碳纤维/9a16预浸料、国产pmi泡沫(ck110-ht)以及j-47a中温胶膜;本实施例复合材料油箱上盖壳体所述外蒙皮厚度1.8-2.2mm,优选2mm,泡沫厚度为5.8-6.2mm,优选6mm,内蒙皮厚度为1.8-2.2mm,优选2mm;所述防晃板复合材料总厚度为1.5-2mm,优选2mm,泡沫厚度为2.8-3.2mm,优选3mm;
84.(3)通过三维数模软件对产品进行预浸料的展开放样,并利用autocad对下料样板进行优化排版设计,再使用数控裁布机下料,对剪裁好的预浸料进行铺层标记并叠层放置;
85.(4)清理成型模具,将模具内芯块按编号顺序取下,并依次排好,准备预成型镶块,用丙酮将成型模具阴模、预成型镶块以及成型芯块擦拭干净,将预成型镶块摆放在预留口盖的相应位置,最后将中温脱模剂均匀地涂于模具表面;
86.(5)首先沿模具内型面随形铺贴一层平纹碳布,然后按照[0/+45/90/-45/-45/90/+45/0]的铺层角度按顺序进行外蒙皮铺层,此铺层顺序重复一次;每层预浸料铺贴后不能出现气泡以及架桥等情况,铺贴完毕后对其进行真空预压实一次;
[0087]
(6)在防晃板位置的底部铺放加强筋,铺放完毕后在外蒙皮表面铺放泡沫的位置铺放一层中温胶膜,然后再铺放泡沫,所述加强筋宽度9.8-10.2mm,优选10mm,厚度5.8-6.2mm优选6mm,泡沫铺贴完毕后对其进行真空预压实一次;
[0088]
(7)再在泡沫之上铺放一层中温胶膜,最后同样按照[0/+45/90/-45/-45/90/+45/0]的铺层角度按顺序进行内蒙皮铺层,此铺层顺序重复一次;每层预浸料铺贴后不能出现气泡以及架桥等情况,然后铺贴一层平纹碳布;
[0089]
(8)模具内摆放芯块,芯块按编号顺序摆放,同时摆放防晃板和橡胶条,所述防晃板为复合材料泡沫夹芯结构,左右两侧复合材料厚度各为1mm,复合材料铺层顺序为准各向同性铺层,摆放防晃板时两侧包覆防晃板的复合材料要与内蒙皮进行搭接,所述橡胶条材质为耐高温硅橡胶,模具内铺放的橡胶条厚度为10mm和3mm两种,铺放于成型芯块形成的缝隙中;
[0090]
(9)合模,固化:扣紧模具上盖,紧固加压螺钉,检测合模间隙,保证合模间隙≤0.5mm;将模具推进烘箱进行固化,模具固化温度135
±
5℃,固化约2h;
[0091]
(10)脱模,修整:固化结束后,打开模具上盖板,拆除芯块,取出产品进行飞边修整后得到复合材料油箱上盖壳体。
[0092]
实施例3
[0093]
图4是本发明的复合材料油箱下盖,包括防晃板15,筋板16,钢衬套17,过线孔18,搭接区19。图5是本发明的复合材料油箱下盖壳体成型模具,包括下盖板20,上盖板21,前边条22,后边条23,左边条24,右边条25,成型芯块26,预成型镶块27,加压螺钉28。
[0094]
如图4、图5所示,本实施例提供一种成型复合材料油箱下盖的方法,步骤如下:
[0095]
(1)根据产品结构及外形,兼顾铺层工艺和成型方法,综合各种条件利用三维建模软件建立实体模型,设计成型模具;按照设计思路,复合材料油箱下盖结构为薄壁泡沫夹芯结构(外蒙皮+泡沫+内蒙皮),铺层在成型模具内按阴模随型铺覆以确保产品外形尺寸,同时在阴模内放置防晃板、筋板、成型芯块、预成型镶块以及橡胶条等保证油箱内部复杂结构;
[0096]
(2)成型材料根据产品特点和承载要求,本实施例选择铺覆性能好的t300级平纹碳布/9a16预浸料、t700级单向碳纤维/9a16预浸料、国产pmi泡沫(ck110-ht)以及j-47a中温胶膜;本实施例复合材料油箱下盖壳体所述外蒙皮厚度1.8-2.2mm,优选2mm,泡沫厚度为5.8-6.2mm,优选6mm,内蒙皮厚度为1.8-2.2mm,优选2mm;所述防晃板复合材料总厚度为1.5-2mm,优选2mm,泡沫厚度为2.8-3.2mm,优选3mm;所述筋板复合材料总厚度为5.8-6.2mm,优选6mm,泡沫厚度为3.8-4.2mm,优选4mm;
[0097]
(3)通过三维数模软件对产品进行预浸料的展开放样,并利用autocad对下料样板进行优化排版设计,再使用数控裁布机下料,对剪裁好的预浸料进行铺层标记并叠层放置;
[0098]
(4)清理成型模具,将模具内芯块按编号顺序取下,并依次排好,准备预成型镶块,用丙酮将成型模具阴模、预成型镶块以及成型芯块擦拭干净,将预成型镶块摆放在预留过线孔和钢衬套的相应位置,最后将中温脱模剂均匀地涂于模具表面;
[0099]
(5)首先沿模具内型面随形铺贴一层平纹碳布,然后按照[0/+45/90/-45/-45/90/+45/0]的铺层角度按顺序进行外蒙皮铺层,此铺层顺序重复一次;每层预浸料铺贴后不能出现气泡以及架桥等情况,铺贴完毕后对其进行真空预压实一次;
[0100]
(6)在防晃板位置的底部铺放加强筋,铺放完毕后在外蒙皮表面铺放泡沫的位置铺放一层中温胶膜,然后再铺放泡沫,所述加强筋宽度9.8-10.2mm,优选10mm,厚度5.8-6.2mm优选6mm,泡沫铺贴完毕后对其进行真空预压实一次;
[0101]
(7)再在泡沫之上铺放一层中温胶膜,最后同样按照[0/+45/90/-45/-45/90/+45/0]的铺层角度按顺序进行内蒙皮铺层,此铺层顺序重复一次;每层预浸料铺贴后不能出现气泡以及架桥等情况,然后铺贴一层平纹碳布;
[0102]
(8)模具内摆放芯块,芯块按编号顺序摆放,同时摆放防晃板、筋板和橡胶条,所述防晃板和筋板为复合材料泡沫夹芯结构,防晃板左右两侧复合材料厚度各为1mm,筋板左右两侧复合材料厚度各为3mm,复合材料铺层顺序为准各向同性铺层,摆放防晃板和筋板时两侧包覆防晃板和筋板的复合材料要与内蒙皮进行搭接,所述橡胶条材质为耐高温硅橡胶,模具内铺放的橡胶条厚度为10mm和3mm两种,铺放于成型芯块形成的缝隙中;
[0103]
(9)合模,固化:扣紧模具上盖,紧固加压螺钉,检测合模间隙,保证合模间隙≤0.5mm;将模具推进烘箱进行固化,模具固化温度135
±
5℃,固化约2h;
[0104]
(10)脱模,修整:固化结束后,打开模具上盖板,拆除芯块,取出产品进行飞边修整后得到复合材料油箱下盖壳体。
[0105]
实施例4
[0106]
如图6所示,在复合材料油箱下盖前端、后端以及内部防晃板上打油管孔,将油管29和油管30分别安装在油箱的最低点和最高点,然后在油管与复合材料的界面处抹上粘接胶并安装密封圈,然后紧固固定油管的内外螺母,完成油管的安装;所述最低点为油管与下盖内部底面接触的位置,所述最高点为油管与上盖内部底面接触的位置,所述密封圈为商购含氟材质的橡胶圈。
[0107]
其中,最高点油管为注油油管,为了确保油箱能够将油注满;最低点油管为排油油管,为了确保油箱能够将油排净。
[0108]
实施例5
[0109]
如图7所示,将复合材料油箱上盖和下盖水平平稳放置,然后在上盖和下盖的搭接区域均匀涂抹粘接胶,把上盖平稳扣到下盖上,利用绑带绑缚上/下盖进行加压固化,室温固化约12h,固化结束后,拆掉绑带,对粘接区域进行打磨修整,确保表面平整无棱刺;所述绑带为军用绑带,均匀间隔5条进行绑缚,确保粘接胶能够从上下盖的搭接区域流出且上下盖搭接区域无缝隙即可。
[0110]
经耐压性能测试,本发明制造的复合材料油箱完全满足使用要求,实现了轻量化复合材料油箱在大型弹身舱段领域的应用。
[0111]
本发明未详细说明部分为本领域技术人员公知技术。
[0112]
以上结合附图公开的本发明的具体实施例,其目的在于帮助理解本发明的内容并据以实施,本领域的普通技术人员可以理解,在不脱离本发明的精神和范围内,各种替换、变化和修改都是可能的。本发明不应局限于本说明书的实施例所公开的内容,上述的具体实施方式仅仅是示意性的,而不是限制性的,本领域的普通技术人员在本发明的启示下,在不脱离本发明宗旨和权利要求所保护的范围情况下,还可做出很多形式,这些均属于本发明的保护之内。