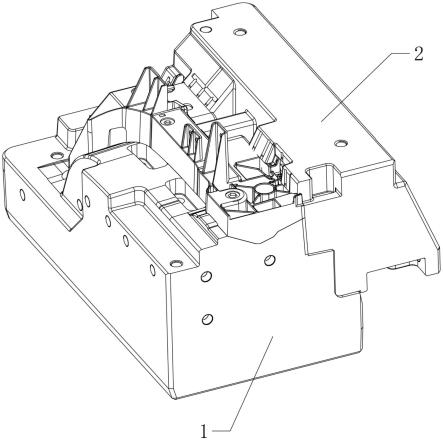
1.本实用新型涉及注塑模具技术领域,特别涉及一种结构紧凑的复合滑块斜抽出模结构。
背景技术:2.如图1所示的成型品为一种汽车前端框架7,其涉及多边形的孔位71的开设,该孔位在其所在面倾斜开设,使该孔位的侧壁与开模方向相对倾斜设置,如果采取人工打孔不够高效美观,而且容易导致损坏,因此需要注塑时一次成型。
3.为了实现注塑上述带有孔位的倒扣的成型品结构,现有的模具大多都是在滑杆下方直接设置连接油缸,在注塑成型时通过油缸的油杆上行,带动滑杆端部伸入成型腔内配合成型,注塑成型结束后通过油缸的油杆下行,带动滑杆端部脱离成型品消除倒扣,然后再对成型品进行顶出,由于油缸的伸缩精度不够高,通过油缸直接作用滑杆配合成型会导致成型品之间的孔位深度不一致,影响成型品的质量;另外油缸设置在模具的竖直方向上,增加了模具的高度,使模具整体结构不够紧凑,占用空间大。
技术实现要素:4.本实用新型的目的是提供一种结构紧凑的复合滑块斜抽出模结构,具有成型品脱出不易损坏、降低成本、减小模具高度、提高生产效率的效果。
5.本实用新型的上述技术目的是通过以下技术方案得以实现的:一种结构紧凑的复合滑块斜抽出模结构,包括有成型块和滑块,所述成型块倾斜开设有贯穿孔,所述贯穿孔贯穿所述成型块且一端连通型腔,所述贯穿孔内活动设有滑杆,所述滑杆一端设有弹性回复组件,所述弹性回复组件始终有驱使所述滑杆缩回所述贯穿孔内的运动趋势,所述滑块设有插柱,所述成型块对应所述插柱开设有滑移孔,所述滑移孔与所述贯穿孔连通,所述插柱与所述滑移孔滑动配合,所述插柱与所述滑杆之间设有导向结构,当所述滑块带动所述插柱相对远离所述成型块时,在所述导向结构的导向作用下,使得所述滑杆相对所述贯穿孔缩回。
6.通过采用上述技术方案,在初始状态下,滑杆处于回缩于贯穿孔内的状态。在合模注塑成型时,通过滑块贴紧成型块,使插柱插入滑移孔内,插柱与滑杆之间通过导向结构的导向作用,向型腔内推动滑杆,使滑杆上端部沿贯穿孔轴向方向倾斜向上伸出,弹性回复组件积攒弹性势能,上下模合模后并与滑块侧面、滑块上端面、以及滑杆端部配合形成型腔,随后进行注塑成型形成注塑品,此时滑杆端部在成型品内部形成带有孔位的倒扣,注塑成型结束后,开模时滑块在外部驱动力下远离成型块,插柱相对滑杆远离,插柱对滑杆的推力消失,然后通过弹性回复组件释放弹性势能,使滑杆端部沿贯穿孔轴向方向倾斜向下缩回,消除滑杆端部在成型品内形成的带有孔位的倒扣,另外滑杆活动式可拆卸安装在贯穿孔内,方便后续更换不同端部形状的滑杆,用于成型其他形状的孔位,具有成型品脱出不易损坏、降低成本、减小模具高度、提高生产效率的效果。
7.本实用新型的进一步设置为:所述导向结构包括倾斜设于所述插柱端部且间隔设置的两个导向叉,所述滑杆对应所述导向叉开设有导向槽,所述导向叉与所述导向槽滑移配合。
8.通过采用上述技术方案,当插柱横向插入滑杆的导向槽时,通过导向叉与导向槽之间的导向滑移配合,使滑杆相对插柱向上移动。
9.本实用新型的进一步设置为:所述导向叉上端倾斜开设有第一导向面,所述导向槽侧壁对应所述第一导向面开设有第二导向面,当所述导向叉靠近所述导向槽时,通过所述第一导向面与所述第二导向面的导向作用,使所述滑杆端部伸出所述贯穿孔。
10.通过采用上述技术方案,当插柱的导向叉靠近滑杆的导向槽时,通过第一导向面与第二导向面的导向配合,对滑杆给予一个向上的推力,使滑杆向上伸出贯穿孔配合参与注塑成型。
11.本实用新型的进一步设置为:所述导向叉与所述插柱的夹角设为165-175
°
之间。
12.通过采用上述技术方案,夹角的度数与插柱横向运动的速度相适配,当插柱横向速度一致时,过大的夹角会导致滑杆从成型品中脱离速度过快,容易导致孔位变形或者损坏。
13.本实用新型的进一步设置为:所述导向叉下端对应所述导向槽侧壁开设有避让面。
14.通过采用上述技术方案,避让面设计能够有效防止导向叉下端部与滑杆之间刚性接触导致损坏,能够提高本实用新型的使用寿命。
15.本实用新型的进一步设置为:所述弹性回复组件包括固定套、长螺栓和弹性件,所述固定套嵌于所述贯穿孔内并固定于所述成型块上,所述固定套开设有通孔,所述滑杆端面开设有螺纹孔,所述长螺栓穿过所述通孔与所述螺纹孔螺纹连接,所述弹性件活动设于所述固定套的腔室内并套设于所述长螺栓上,所述弹性件始终有驱使所述滑杆缩回所述贯穿孔内的运动趋势。
16.通过采用上述技术方案,在注塑成型时,插柱与滑杆导向配合,使滑杆顶起,由于固定套的底部是固定不动的,长螺栓沿着通孔方向倾斜向上运动,同时使弹性件被压缩;当注塑成型结束后,插柱远离滑杆,弹性件通过释放自身弹性势能,使长螺杆倾斜向下移动,直至滑杆的端部抵在固定套上,恢复至初始状态。
17.本实用新型的进一步设置为:所述固定套设有卡凸,所述成型块对应所述卡凸开设有凹槽,所述凹槽与所述贯穿孔连通,所述卡凸与所述凹槽嵌入抵挡配合。
18.通过采用上述技术方案,通过卡凸与凹槽的嵌入配合,使固定套隐藏式固定安装在成型块上,减少空间占用,结构紧凑。
19.本实用新型的进一步设置为:所述滑杆包括滑移部和止挡部,所述贯穿孔设为阶梯孔,所述滑移部与所述阶梯孔滑移配合,所述止挡部与所述阶梯孔的阶梯抵挡配合。
20.通过采用上述技术方案,滑杆的滑移部活动穿设在阶梯孔的细头端,且滑杆通过止挡部与阶梯孔的阶梯止挡限位,对滑杆的端部伸出阶梯孔的长度起到了限制作用。
21.本实用新型的进一步设置为:所述插柱一端一体成型设有连接部,所述滑块对应所述连接部开设有安装槽,所述连接部与所述安装槽嵌入配合,所述连接部通过外部螺栓固定连接在所述滑块上。
22.通过采用上述技术方案,插柱的连接部通过外部螺栓固定连接在滑块的侧壁,固定方式简单,固定效果稳定,且利于后续对插柱的保养或者更换。
23.综上所述,本实用新型具有以下有益效果:采用通过横向滑块的前后滑移带动插柱在滑移孔内轴向移动,并通过插柱与滑杆间的导向结构的导向作用,使滑杆在贯穿孔内轴向位移,当滑杆伸出贯穿孔时进行注塑成型,当滑杆缩回贯穿孔内时进行成型品脱模,具有成型品脱出不易损坏、降低成本、结构紧凑、提高生产效率的效果。
附图说明
24.图1是本实用新型成型品的结构图。
25.图2是本实用新型的结构图。
26.图3是本实用新型插柱靠近滑杆的纵向剖视图。
27.图4是本实用新型插柱远离滑杆的纵向剖视图。
28.图5是本实用新型滑杆、插柱、弹性回复组件的结构图。
29.图中:1、成型块;11、贯穿孔;12、滑移孔;13、凹槽;2、滑块;21、安装槽;3、滑杆;31、导向槽;310、第二导向面;32、螺纹孔;33、滑移部;34、止挡部;4、插柱;41、导向叉;410、第一导向面;411、避让面;42、连接部;5、弹性回复组件;51、固定套;511、通孔;512、卡凸;52、长螺栓;53、弹性件;6、型腔;7、成型品;71、孔位。
具体实施方式
30.下面结合附图对本实用新型作进一步的说明。
31.一种结构紧凑的复合滑块斜抽出模结构,如图2-4所示,包括有成型块1和滑块2,滑块2侧面设有横向驱动件,比如油缸,油缸用以驱动滑块2在水平方向做直线运动,成型块1沿竖向倾斜开设有贯穿孔11,本实用新型的贯穿孔11设为阶梯孔,阶梯孔贯穿成型块1且上端连通型腔6,阶梯孔内活动设有滑杆3,滑杆3下端设有弹性回复组件5,弹性回复组件5包括固定套51、长螺栓52和弹性件53,固定套51通过外部螺钉固定于成型块1上并嵌设于阶梯孔的大头端,固定套51开设有通孔511,滑杆3端面对应该通孔511开设有螺纹孔32,长螺栓52的杆部穿过通孔511与螺纹孔32螺纹连接,弹性件53活动设于固定套51的腔室内并套设于长螺栓52上,使弹性件53一端抵于固定套51的腔室的底部,弹性件53另一端与长螺栓52的头部相抵,使弹性件53始终有驱使滑杆3的端部抵于固定座的运动趋势,本实用新型的弹性件53设为复位弹簧,在初始状态下,滑杆3处于回缩于阶梯孔内的状态,在合模注塑成型前,通过滑块2贴紧成型块1,使插柱4插入滑移孔12内,插柱4与滑杆3之间通过导向结构的导向作用,使滑杆3顶起,由于固定套51的底部是固定不动的,长螺栓52沿着通孔511方向倾斜向上运动,同时使复位弹簧被压缩,滑杆3的端部伸入型腔6的内部并参与成型品7的孔位71的成型,然后开始注塑;当注塑成型结束后,插柱4远离滑杆3,复位弹簧通过释放自身弹性势能,使长螺杆倾斜向下移动,直至滑杆3的端部抵在固定套51上,恢复至初始状态。
32.如图3-4所示,滑块2设有插柱4,成型块1对应插柱4开设有滑移孔12,滑移孔12与阶梯孔连通,插柱4可沿滑移孔12轴向运动,插柱4与滑移孔12滑动配合,插柱4与滑杆3之间设有导向结构,当插柱4在滑移孔12内轴向运动时,通过导向结构的导向作用,使滑杆3在阶梯孔内轴向运动,当滑杆3端部伸出阶梯孔时,成型块1、滑块2、滑杆3端部配合形成型腔6;
插柱4一端一体成型设有连接部42,滑块2对应连接部42开设有安装槽21,连接部42与安装槽21嵌入配合,连接部42通过外部螺栓固定连接在滑块2上,插柱4的连接部42通过外部螺栓固定连接在滑块2的侧壁,固定方式简单,固定效果稳定,且利于后续对插柱4的保养或者更换。
33.如图4-5所示,导向结构包括倾斜设于插柱4端部且间隔设置的两个导向叉41,导向叉41下端对应导向槽31侧壁开设有避让面411,避让面411设计能够有效防止导向叉41下端部与滑杆3之间刚性接触导致损坏,能够提高本实用新型的使用寿命,滑杆3对应导向叉41开设有导向槽31,导向叉41与导向槽31滑移配合,导向叉41上端倾斜开设有第一导向面410,导向槽31侧壁对应第一导向面410开设有第二导向面310,当导向叉41靠近导向槽31时,通过第一导向面410与第二导向面310的导向作用,使滑杆3端部伸出贯穿孔11,当插柱4的导向叉41靠近滑杆3的导向槽31时,通过第一导向面410与第二导向面310的导向配合,对滑杆3给予一个向上的推力,使滑杆3向上伸出贯穿孔11配合参与注塑成型;导向叉41与插柱4的夹角设为165-175
°
之间,夹角的度数与插柱4横向运动的速度相适配,当插柱4横向速度一致时,过大的夹角会导致滑杆3从成型品7中脱离速度过快,容易导致孔位71变形或者损坏;导向叉41端部设为避让面411,避让面411设计能够有效防止导向叉41端部与滑杆3之间刚性接触导致损坏,能够提高本实用新型的使用寿命。
34.如图3-4所示,固定套51设有卡凸512,成型块1对应卡凸512开设有凹槽13,凹槽13与阶梯孔连通,卡凸512与凹槽13嵌入抵挡配合,通过卡凸512与凹槽13的嵌入配合,使固定套51隐藏式固定安装在成型块1上,减少空间占用,结构紧凑。
35.滑杆3包括滑移部33和止挡部34,滑移部33与阶梯孔滑移配合,止挡部34与阶梯孔抵挡配合,滑杆3的滑移部33活动穿设在阶梯孔的细头端,且滑杆3通过止挡部34与阶梯孔的台阶止挡限位,对滑杆3的端部伸出阶梯孔的长度起到了限制作用,在注塑成型准备阶段,滑杆3在阶梯孔内向上移动直至滑杆3的止挡部34与阶梯孔的阶梯相抵,使滑杆3的端部伸出阶梯孔进行注塑成型,当成型品形成后,滑杆3下移,使滑杆3的端部离开成型品7的孔位71,同时滑杆3的止挡部34与阶梯孔的阶梯之间形成有间隙,该间隙的距离为至少一个成型品7的孔位71的高度。
36.本实用新型的基本工作原理为:在初始状态下,滑杆3处于回缩于贯穿孔11内的状态。在合模注塑成型时,通过滑块2贴紧成型块1,使插柱4插入滑移孔12内,插柱4与滑杆3之间通过导向结构的导向作用,向型腔6内推动滑杆3,使滑杆3上端部沿贯穿孔11轴向方向倾斜向上伸出,弹性回复组件5积攒弹性势能,上下模合模后并与滑块2侧面、滑块2上端面、以及滑杆3端部配合形成型腔6,随后进行注塑成型形成注塑品,此时滑杆3端部在成型品7内部形成带有孔位71的倒扣,注塑成型结束后,开模时滑块2在外部驱动力下远离成型块1,插柱4相对滑杆3远离,插柱4对滑杆3的推力消失,然后通过弹性回复组件5释放弹性势能,使滑杆3端部沿贯穿孔11轴向方向倾斜向下缩回,消除滑杆3端部在成型品7内形成的带有孔位71的倒扣,另外滑杆3活动式可拆卸安装在贯穿孔11内,方便后续更换不同端部形状的滑杆3,用于成型其他形状的孔位71,具有成型品7脱出不易损坏、降低成本、减小模具高度、提高生产效率的效果。
37.以上所述仅是本实用新型的较佳实施方式,故凡依本实用新型专利申请范围所述的构造、特征及原理所做的等效变化或修饰,均包括于本实用新型专利申请范围内。