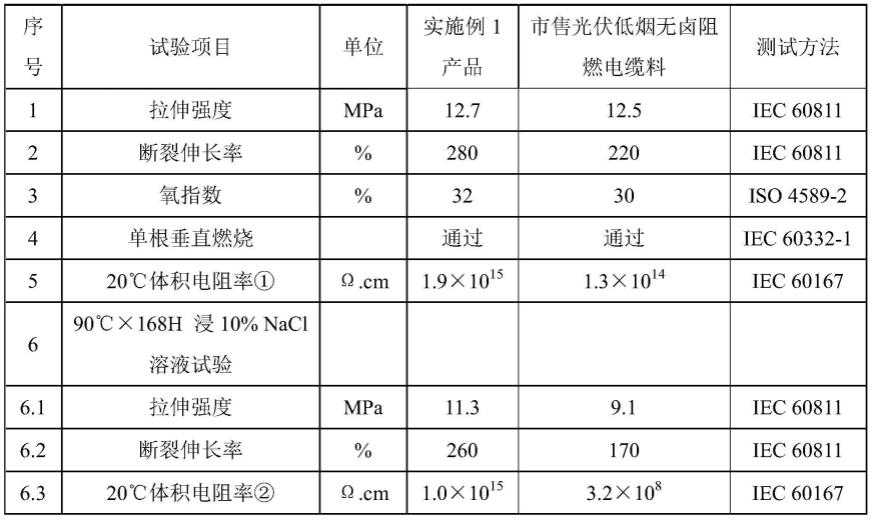
1.本实用新型涉及电缆技术领域,具体涉及一种海面漂浮光伏系统电缆的护套挤出设备。
背景技术:2.在碳中和、碳达峰的大背景下,各种新能源产业得到高速发展,其中太阳能发电作为一种高效的清洁能源已被广泛应用于各种场所,其中有家用屋顶光伏发电、地面光伏电站、水上漂浮光伏电站等。但是太阳能电站不可避免地需要庞大的空间,但在一些人口密集的地区和国家,可用于建设太阳能电站的土地却非常稀缺或很昂贵,有时两者兼有之。解决这一难题的方法之一就是将太阳能电站建造在水面上,或者海面上通过使用浮体架台支撑电板,并将所有电板连接在一起。
3.在现有技术中,应用于光伏系统的电缆中的绝缘层或护套层通常使用烯烃类聚合物作为基材,氢氧化铝、氢氧化镁等无机类含结晶水材料作阻燃剂,经共混、塑化、造粒而成的电缆料。现有的低烟无卤阻燃聚烯烃电缆料存在如下缺陷:
4.第1,常规光伏用无卤低烟聚烯烃阻燃绝缘层或护套层使用乙烯-乙酸乙烯共聚物、聚乙烯、氢氧化铝、氢氧化镁,制得的电缆材料中含有大量的无机阻燃剂,常规的表面处理是使用有机硅氧烷通过高混的方式进行。这种处理方法,对于无机阻燃剂表面的包覆效率比较高,亲水的氢氧根离子很容易与空气中的水蒸气结合,降低材料的绝缘电阻,增加电缆被击穿或短路的风险。
5.第2,常规光伏用无卤低烟聚烯烃阻燃电缆料中的聚合物基材中添加了大量的聚乙烯/乙烯-醋酸乙烯共聚物材料。这些材料在海上漂浮光伏系统中使用时,由于海风吹拂,线缆摇摆时局部容易产生疲劳,导致机械性能劣化甚至开裂现象。由于这两项严重的缺陷,导致常规光伏用无卤低烟聚烯烃阻燃电缆料在使用到海上漂浮光伏系统中时,会有很大的安全隐患。
6.第3,现有技术中的电缆在制备过程中,需要在导体绝缘层和护套层之间设置绕包带,通过绕包带来隔离绝缘层和护套层,然而,由于绕包带的设置需要单独绕包,导致制备工艺复杂,并且成本提高。
技术实现要素:7.本实用新型提供一种海面漂浮光伏系统电缆的护套挤出设备,本实用新型具有简化工艺以及降低成本的特点。
8.解决上述技术问题的技术方案如下:
9.海面漂浮光伏系统电缆的护套挤出设备,包括:
10.用于释放缆芯的放线架;
11.将护套料挤包在缆芯上以形成护套层的第二挤塑机,第二挤塑机位于放线架的下游;
12.对护套层进行冷却的冷却水槽,冷却水槽位于第二挤塑机的下游;
13.对护套层表面进行吹风的吹干机,吹干机位于冷却水槽的下游;
14.火花机,火花机位于吹干机的下游;
15.用于卷线的收线架,收线架位于火花机的下游;
16.还包括装有滑石粉的滑石粉收纳机构,滑石粉收纳机构位于放线架与第二挤塑机之间,滑石粉收纳机构上设有供缆芯穿过的输入孔和输出孔。
17.本实用新型具有如下优点:
18.当在导体上挤出绝缘层获得缆芯后,在缆芯上挤包护套层之前,不需要单独绕包一层绕包带来分隔绝缘层和护套层,而是在挤包护套层的挤塑机上游设置滑石粉收纳机构,使缆芯穿过滑石粉收纳机构时附上滑石粉,通过滑石粉来分隔隔绝缘层和护套层,以避免隔绝缘层和护套层粘连。由此可见,本实用新型在挤包护套层时,通过滑石粉收纳机构实现了分隔隔绝缘层和护套层,既简化了工艺,又降低了成本。
附图说明
19.图1为本实用新型中的海面漂浮光伏系统耐盐雾耐弯折电缆的剖面结构图。
20.图2为海面漂浮光伏系统电缆的护套挤出设备的示意图。
21.图3为滑石粉收纳机构的俯视图。
22.附图中的标记:
23.导体1,绝缘层2,护套层3,放线架11,第二挤塑机12,冷却水槽13,吹干机14,火花机15,收线架16,滑石粉收纳机构17,输入孔17a,输出孔17b,第一保护部件17c,主料斗18,搅拌轴19,搅拌叶片19a,第一副料斗20,通孔20a,第二保护部件20b,第二副料斗21,盖板22。
具体实施方式
24.实施例1
25.如图1至图3所示,海面漂浮光伏系统耐盐雾耐弯折电缆的制备方法,包括以下步骤:
26.s1,将绝缘料通过第一挤塑机挤出并包裹在导体1上形成绝缘层2,导体1上包裹绝缘层2后形成缆芯,所述绝缘料采用低烟无卤耐盐雾耐弯折的材料,将低烟无卤耐盐雾耐弯折的材料通过挤塑机挤包在镀锡铜导体上形成绝缘层2,保证导体1和绝缘层2之间无间隙。
27.本实施例中,导体1采用镀锡绞合铜绞线导体。镀锡绞合型软铜导体的制备过程为:铜杆经过拉丝机拉成裸铜丝,裸铜丝经过电镀或热镀锡的方式在铜丝表面形成一层均匀的金属锡镀层,镀锡铜线经过绞线机绞合成缆形成成品的镀锡绞合铜绞线导体。
28.s2,将护套料通过第二挤塑机12挤出并包裹在绝缘层2上形成外护套层3后获得电缆。所述护套料采用低烟无卤耐盐雾耐弯折的材料,将低烟无卤耐盐雾耐弯折的材料通过挤塑机挤包在绝缘层2上,使绝缘层2和护套层3紧密的结合在一起。
29.挤出护套层3时采用中压缩比螺杆,压缩比采用1.4-2.0,本实施例中,压缩比采用1.6,螺杆长径比选择25:1,第二挤塑机12的挤出温度从机筒一区到九区温度分别为:为100
±
10(机筒一区,加料段)、110
±
10(机筒二区,加料段)、130
±
10(机筒三区,塑化段)、140
±
10(机筒四区,塑化段)、150
±
10(机筒五区,塑化段)、150
±
10(机筒六区,塑化段)、160
±
10(机筒七区,塑化段)、170
±
10(机筒八区,均化段)、170
±
10℃(机筒九区,均化段),第二挤塑机内的螺杆的推送压力为压力18-25mpa,挤出速度10-150m/min。
30.优选的方式是,在步骤s1结束后,使绝缘层2的表面粘上滑石粉后,再执行步骤s2。当缆芯通过第二挤塑机时,可以避免高温和高压的作用导致护套层3和绝缘层2粘连在一起。
31.如图2至图3所示,在挤出护套层3时,采用的护套挤出设备的结构为:包括放线架11、第二挤塑机12、冷却水槽13、吹干机14、火花机15、收线架16、滑石粉收纳机构17,下面对护套挤出设备中的各部分及其关系进行详细说明:
32.如图2至图3所示,放线架11用于释放缆芯,即由导体1和绝缘层2形成的缆芯以卷绕的方式存储在放线架11上。第二挤塑机12将护套料挤包在缆芯上以形成护套层3,第二挤塑机12位于放线架11的下游;冷却水槽13对护套层3进行冷却,冷却水槽13位于第二挤塑机12的下游。吹干机14对护套层3表面进行吹风,使经过水冷却的护套层3表面以湿润转换为干燥的状态,吹干机14位于冷却水槽13的下游。火花机15用于测试护套层3在相应的电场下是否会被击穿,火花机15位于吹干机14的下游。在缆芯上挤出护套层3后获得电缆,电缆通过收线架16卷绕收线,收线架16位于火花机15的下游。
33.如图2至图3所示,滑石粉收纳机构17中装有滑石粉,滑石粉收纳机构17位于放线架11与第二挤塑机12之间,滑石粉收纳机构17上设有供缆芯穿过的输入孔17a和输出孔17b。缆芯依次从输入孔17a和输出孔17b穿过,缆芯经过滑石粉收纳机构17内部时,同时穿过滑石粉,从而滑石粉附在绝缘层2的表面,当第二挤塑机12在缆芯上挤出护套层3后,可以避免第二挤塑机12的高温和高压的作用导致护套层3和绝缘层2粘连在一起。
34.如图2至图3所示,滑石粉收纳机构17还包括用于隔离缆芯与输入孔17a孔壁面的第一保护部件17c,第一保护部件17c呈环状且与输入孔17a配合。通过第一保护部件17c的隔离作用,避免了缆芯在通过输入孔17a时与输入孔17a发生摩擦,防止输入孔17a的孔壁面对绝缘层2形成刮削,从而使绝缘层2的圆度得到保持,本实施例中第一保护部件17c优先采用海绵,海绵具有柔软的特点。
35.如图2至图3所示,滑石粉收纳机构17包括主料斗18、搅拌轴19、搅拌叶片19a、驱动器,主料斗18用于收纳滑石粉,所述输入孔17a和输出孔17b分别设置在主料斗18的两端;搅拌轴19位于主料斗18内的中下部,搅拌轴19的两端分别可转动地支撑在主料斗18上,搅拌叶片19a工作时使滑石粉形成翻腾状态,搅拌叶片19a与搅拌轴19固定,驱动器(图中未示出)驱动搅拌轴19旋转,驱动器与搅拌轴19连接。驱动器可以由电机、减速器和皮带传动机构组成,或者,驱动器由电机、减速器和齿轮传动机构组成。
36.如图2至图3所示,通过驱动器驱动搅拌轴19旋转,使搅拌叶片19a旋转,搅拌叶片19a使滑石粉形成翻腾的状态,这种能使更多的滑石粉附在绝缘层2的表面,同时,附在绝缘层2表面的滑石粉也会更均匀。
37.如图2至图3所示,滑石粉收纳机构17还包括接纳从输入孔17a中溢出的粉料的第一副料斗20,第一副料斗20设置在主料斗18设置输入孔17a的一侧,由于主料斗18内的滑石粉在搅拌叶片19a的驱动下呈翻腾状态,因此,可能会导致滑石粉通过输入孔17a溢出到主料斗18的外部,从而在本实施例中,通过第一副料斗20对从输入孔17a溢出的滑石粉进行收
纳,从而避免污染工作环境。
38.如图2至图3所示,本实施例中,第一副料斗20的开口所在高度位置,与主料斗18的开口所在高度位置相等,因此,在第一副料斗20上设有供缆芯穿过的通孔20a,同时滑石粉收纳机构17还包括用于隔离缆芯与通孔20a孔壁面的第二保护部件20b,第二保护部件20b呈环状且与通孔20a配合。
39.如图2至图3所示,通过第二保护部件20b的隔离作用,避免了缆芯在通过通孔20a时与通孔20a的孔壁发生摩擦,防止通孔20a的孔壁面对绝缘层2形成刮削,从而使绝缘层2的圆度得到保持,本实施例中第二保护部件20b优先采用海绵。
40.如图2至图3所示,滑石粉收纳机构17还包括接纳从输出孔17b中溢出的粉料的第二副料斗21,第二副料斗21设置在主料斗18设置输出孔17b的另一侧,由于表面附有滑石粉的绝缘层不能与海绵之类的保护部件接触,也不能与输出孔17b的孔壁面接触,因此,本实施例中,一方面将第二副料斗22的开口位于输出孔17b的下方,另一方面将输出孔17b的内孔设置成大于缆芯外径的至少2倍,以避免绕芯因晃动等因素与输出孔17b的孔壁面发生刮削。
41.如图2至图3所示,滑石粉在拌叶片20的驱动下呈翻腾状态,由于滑石粉本身呈粉末状态,在翻腾过程中容易飞散到主料斗18外部,对工作环境形成污染,因此,本实施例中的滑石粉收纳机构17还包括盖板22,所述盖板22的一端与主料斗18铰接,通过盖板22对主料斗18的开口进行遮挡,避免滑石粉四处飞散。
42.s3,采用电子辐照加速器对电缆进行辐照,使绝缘层2和护套层3交联成型。步骤s3中,使用能量为1.5至2.5mev、束流为10至40ma、扫描宽度为120cm的电子加速器对电缆进行辐照。
43.绝缘层2和护套层3均采用低烟无卤耐盐雾耐弯折的材料,本实施例中,低烟无卤耐盐雾耐弯折的材料由以下重量份的原料组成:聚合物基材100份,辐射接枝改性的无机阻燃剂100份,六苯氧基环三磷腈7份,二乙基次磷酸铝20份,三聚氰胺氰尿酸盐20份,纳米蒙脱土2份,抑烟剂八钼酸铵1份,复合抗氧剂4份,加工助剂4份,环保型色母粒4份。
44.所述聚合物基材由以下重量份的原料组成:10份接枝马来酸酐的化学相容剂,20份烯烃嵌段共聚物,55份va含量20%的乙烯-乙酸乙烯酯共聚物,5份乙烯-辛烯共聚物及5份ma含量22%的乙烯-甲基丙烯酸甲酯共聚物;其中化学相容剂为ldpe-g-mah、lldpe-g-mah、poe-g-mah构成的组合物。
45.辐射接枝改性的无机阻燃剂的制过备过程为:称取氢氧化铝和氢氧化镁混合物50kg,所述氢氧化铝与氢氧化镁的重量比为2:1。将1kg醋酸乙烯酯溶解到30l乙醇中,然后将氢氧化铝和氢氧化镁与溶解于乙醇中的醋酸乙烯酯共混均匀后放入真空密封袋进行抽真空后密封,然后进行伽马或电子束射线辐照,使醋酸乙烯酯中的基团接枝到氢氧化铝和氢氧化镁的表面。辐照吸收剂量为35kgy,辐照结束后对样品烘干后进行称重计算接枝率,接枝率为1%。
46.所述复合抗氧剂包括:2份主抗氧剂和1份辅助抗氧剂,其中,主抗氧剂为由以下物质构成的组合物:四[β-(3,5-二叔丁基-4-羟基苯基)丙酸]季戊四醇酯(1010)、β-(3,5-二特丁基-4-羟基苯基)丙酸十八酯(1076)、n,n
’‑
双[β-(3,5-二叔丁基-4-羟基苯基)丙酰]肼(1024)、二(2-甲基-5-叔丁基-4-羟基苯基)硫醚、4,4'-硫代双(6-叔丁基-3-甲基苯酚)
(300);辅助抗氧剂为硫代二丙酸双十二烷酯和硫代二丙酸二(十八)酯。
[0047]
加工助剂由交联敏化剂和润滑剂组成,交联敏化剂的重量份数为1份,润滑剂的重量份数为5份。交联敏化剂包括三羟甲基丙烷三甲基丙烯酸酯和三烯丙基异三聚氰酸酯。润滑剂由聚乙烯蜡、硬脂酸锌和硬脂酸钙、硅酮母粒及乙撑双硬脂酰胺组成。
[0048]
所述低烟无卤耐盐雾耐弯折的材料的制备过程为:将聚合物基材、无机阻燃剂、六苯氧基环三磷腈、二乙基次磷酸铝、三聚氰胺氰尿酸盐、纳米蒙脱土、抑烟剂八钼酸铵、复合抗氧剂、加工助剂和环保型色母粒按份数称取,投入到加压密炼机中,控制密炼机压力为2.53mpa,在密炼机中混炼至175℃,使各种组分混合均匀,形成混合软质胶状物;将得到的混合软质胶状物投入到双螺杆挤出机中挤出,得到颗粒状的低烟无卤耐盐雾耐弯折的材料,颗粒状的低烟无卤耐盐雾耐弯折的材料的长度为0.5cm,底面直径为0.25cm。将颗粒状的低烟无卤耐盐雾耐弯折的材料风冷后包装。
[0049]
双螺杆挤出机温度为:第一区130-145℃(加料段),第二区130-145℃(加料段),第三区130-145℃(塑化段),第四区130-145℃(塑化段),第五区130-145℃(塑化段),第六区130-145℃(塑化段),第七区130-145℃(塑化段),第八区130-145℃(均化段),第九区130-145℃(均化段),模头140-155℃,设定真空泵压力0.1-0.2atm。
[0050]
本实施例中,双螺杆挤出机温度为:第一区130℃(加料段),第二区132℃(加料段),第三区134℃(塑化段),第四区136℃(塑化段),第五区138℃(塑化段),第六区140℃(塑化段),第七区142℃(塑化段),第八区144℃(均化段),第九区145℃(均化段),模头150℃,设定真空泵压力0.15atm。
[0051]
将实施例1中采用低烟无卤耐盐雾耐弯折的材料的绝缘层2和护套层3制成的电缆,与现有市面上销售的光伏低烟无卤阻燃电缆料进行相关测试实验,检测和对比结果下面的如表1所示。
[0052]
表1测试实验对比结果
[0053]
[0054][0055]
(1),由表1所示,由表1中的对比指标
①
可以看出,市售光伏低烟无卤阻燃电缆料的体积电阻率指标明显低于实施例1产品指标。
[0056]
(2),由表1中的对比指标
①
和
②
可以看出,采用nacl溶液浸泡前后对20℃体积电阻率检测结果是,实施例1的产品浸泡前的值是:1.9
×
10
15
,实施例1的产品浸泡前的值是:1.0
×
10
15
,市售产品浸泡前的值是:1.3
×
10
14
,市售产品浸泡前的值是:3.2
×
108,经过对比可以看出,实施例1的产品在采用nacl溶液浸泡后,20℃体积电阻率略微下降,而实施例1的产品在在经过氯化钠溶液浸泡后仍能保持符合光伏标准要求的绝缘性能,可以确保电缆长期稳定运行。而市售产品在采用nacl溶液浸泡后,20℃体积电阻率呈指数级下降(下降了6个数量级),这会给电缆的安全运行带来很大的隐患,可能导致电缆过热、起火,引起安全事故。
[0057]
(3),由表1中的对比指标
③
可以看出,在经过10000次摇摆后,市售光伏低烟无卤阻燃电缆料制成的电缆外观已经出现明显的应力发白现象,而本实施例的产品外观还是正常的;在经过20000次摇摆后,市售光伏低烟无卤阻燃电缆料制成的电缆通过高压火花机的时候出现击穿现象,而本实施例的产品制成的电缆通过高压火花机时未出现报警,说明本实施例产品具有出色的柔韧性和回弹性和耐弯曲性,在摇摆晃动的条件下,不会出现因材料疲劳而导致开裂、破损现象,因而可以确保电缆安全有效的在海面漂浮光伏系统中应用。
[0058]
(4),由表1中的对比指标
④
可以看出实施例1产品在经过长期浸水(90
±
2℃
×
2016h)后绝缘耐压不击穿可以满足水上项目用防水的要求,而市售光伏低烟无卤阻燃电缆料制成的电缆经过长期浸水后绝缘击穿不能满足水上项目用防水的要求。
[0059]
(5),由表1中的对比指标
⑤
可以看出实施例1产品可以通过iec 60068-2-52的防盐雾试验,市售光伏低烟无卤阻燃电缆料制成的电缆无法达到此性能。
[0060]
实施例2
[0061]
实施例2与实施例1不同之处在于低烟无卤耐盐雾耐弯折材料的配比,具体如下:
[0062]
本实施例中,低烟无卤耐盐雾耐弯折的材料由以下重量份的原料组成:聚合物基材98份,辐射接枝改性的无机阻燃剂105份,六苯氧基环三磷腈6份,二乙基次磷酸铝23份,
三聚氰胺氰尿酸盐25份,纳米蒙脱土1份,抑烟剂八钼酸铵2份,复合抗氧剂5份,加工助剂5份,环保型色母粒5份。
[0063]
所述聚合物基材由以下重量份的原料组成:12份接枝马来酸酐的化学相容剂,22份烯烃嵌段共聚物,52份va含量25%的乙烯-乙酸乙烯酯共聚物,7份乙烯-辛烯共聚物及4份ma含量20%的乙烯-甲基丙烯酸甲酯共聚物;其中化学相容剂为ldpe-g-mah。
[0064]
辐射接枝改性的无机阻燃剂的制过备过程为:称取氢氧化铝和氢氧化镁混合物50kg,氢氧化铝与氢氧化镁的重量比为2:1。将1.5kg醋酸乙烯酯溶解到35l丙酮中,然后将氢氧化铝和氢氧化镁与溶解于丙酮中的醋酸乙烯酯共混均匀后放入真空密封袋进行抽真空后密封,然后进行伽马或电子束射线辐照,使醋酸乙烯酯中的基团接枝到氢氧化铝和氢氧化镁的表面。辐照吸收剂量为45kgy,辐照结束后对样品烘干后进行称重计算接枝率,接枝率为1.5%。
[0065]
所述复合抗氧剂包括:3份主抗氧剂和2份辅助抗氧剂,其中,主抗氧剂为由以下物质构成的组合物:四[β-(3,5-二叔丁基-4-羟基苯基)丙酸]季戊四醇酯(1010)、β-(3,5-二特丁基-4-羟基苯基)丙酸十八酯(1076)、n,n
’‑
双[β-(3,5-二叔丁基-4-羟基苯基)丙酰]肼(1024)、二(2-甲基-5-叔丁基-4-羟基苯基)硫醚、4,4'-硫代双(6-叔丁基-3-甲基苯酚)(300);辅助抗氧剂为硫代二丙酸双十二烷酯和硫代二丙酸二(十八)酯。
[0066]
加工助剂由交联敏化剂和润滑剂组成,交联敏化剂的重量份数为1.5份,润滑剂的重量份数为4.5份。交联敏化剂包括三羟甲基丙烷三甲基丙烯酸酯和三烯丙基异三聚氰酸酯。润滑剂由聚乙烯蜡、硬脂酸锌和硬脂酸钙、硅酮母粒及乙撑双硬脂酰胺组成。
[0067]
聚合物基材、无机阻燃剂、六苯氧基环三磷腈、二乙基次磷酸铝、三聚氰胺氰尿酸盐、纳米蒙脱土、抑烟剂八钼酸铵、复合抗氧剂、加工助剂和环保型色母粒按份数称取,投入到加压密炼机中,控制密炼机压力为3mpa,在密炼机中混炼至172℃,使各种组分混合均匀,形成混合软质胶状物;将得到的混合软质胶状物投入到双螺杆挤出机中挤出,得到颗粒状的低烟无卤耐盐雾耐弯折的材料,颗粒状的低烟无卤耐盐雾耐弯折的材料的长度为0.5cm,底面直径为0.25cm。将颗粒状的低烟无卤耐盐雾耐弯折的材料风冷后包装。
[0068]
本实施例中,双螺杆挤出机温度为:第一区131℃(加料段),第二区133℃(加料段),第三区134℃(塑化段),第四区135℃(塑化段),第五区137℃(塑化段),第六区149℃(塑化段),第七区141℃(塑化段),第八区143℃(均化段),第九区145℃(均化段),模头148℃,设定真空泵压力0.2atm。
[0069]
最后应说明的是:以上各实施例仅仅为本实用新型的较优实施例用以说明本实用新型的技术方案,而非对其限制,更不是限制本实用新型的保护范围;尽管参照前述各实施例对实用新型进行了详细的说明,本领域的普通技术人员应当理解:其依然可以对前述各实施例所记载的技术方案进行修改,或者对其中部分或者全部技术特征进行等同替换;而这些修改或者替换,并不使相应技术方案的本质脱离权利要求的保护范围。