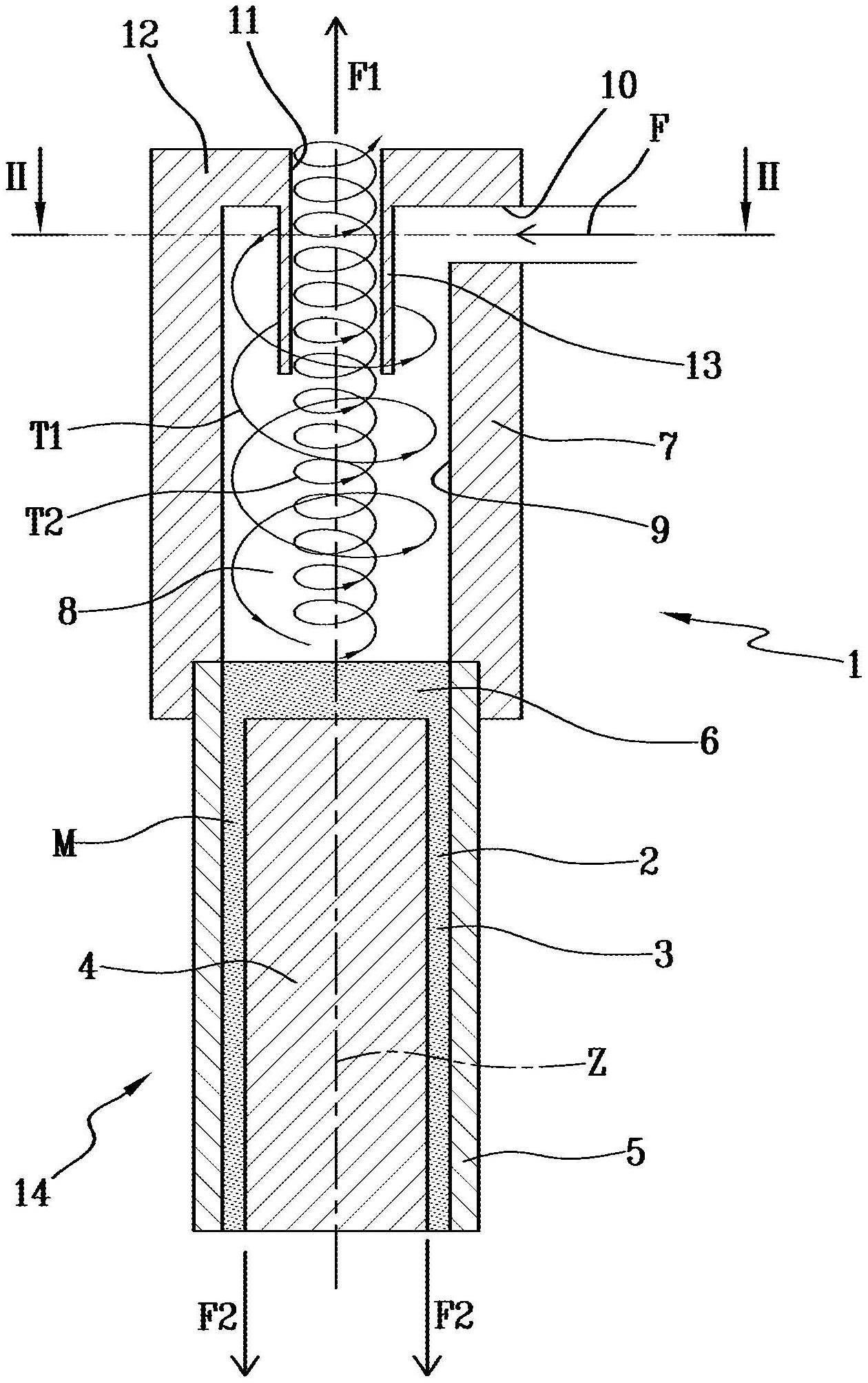
用于填充模具的设备和方法
1.本发明涉及一种用于利用可模制材料填充模具的设备和方法
。
2.可模制材料可以包括源自自天然纤维的材料,例如纤维素,该材料中可以可选地添加合成聚合物材料或各种类型的其他添加剂
。
3.特别地,源自自天然纤维的材料可以是粉末
、
颗粒或薄片的形式
。
这些各种形式的材料可以具有不同的团聚程度,也就是说,或多或少地团聚,这取决于源自自天然纤维的材料的特征和
/
或存在于天然纤维基材料中的水分
/
水或任何其他添加剂的量
。
4.另外,不是源自自天然纤维的其他可模制材料也可以是这些形式,并且可以用根据本发明的设备和方法进行加工
。
5.根据本发明的设备和方法特别地
(
但不排他地
)
适于填充旨在制造具有凹形形状的物体
(
例如容器或用于容器的盖
)
的模具
。
6.通常,源自自天然纤维的可模制材料
(
例如纤维素基材料
)
具有非常低的初始密度,并且需要以高压实度进行压制以获得良好质量的物体
。
这意味着,当模具填充有源自自天然纤维的材料时,需要填充初始体积,该初始体积与模制物体的最终体积相比相对较大
。
7.该操作是不容易的,还因为有时天然纤维基的可模制材料难以在模具内部流动,并且它们可能以非均匀的方式积聚在模具的一些区域中,从而使模具的其他区域几乎是空的
。
8.因此,难以以均匀的方式填充模具,以均匀的方式填充模具是获得良好质量的模制物体的重要要求
。
9.此外,当将源自自天然纤维的材料引入模具中时,在源自自天然纤维的材料内部可能含有大量的空气,而这些空气在获得最终物体之前必须从模具中消除
。
期望在填充期间从模具中去除最大可能量的空气,以减少在模制期间必须排出的空气量
。
10.本发明的一个目的是改进用于利用可模制材料填充模具的设备和方法,该可模制材料特别地包含源自自天然纤维的材料,例如纤维素
。
11.另一个目的是提供一种用于利用可模制材料
(
例如包含源自自天然纤维的材料
)
填充模具的设备和方法,其允许以均匀的方式填充模具
。
12.另一个目的是提供一种用于利用可模制材料
(
例如包含源自自天然纤维的材料
)
填充模具的设备和方法,其具有降低的构造难度并且具有简单的操作
。
13.另一个目的是提供一种用于利用可模制材料
(
例如包含源自自天然纤维的材料
)
填充模具的设备和方法,其可以在填充期间从模具排放空气
。
14.在本发明的第一方面中,提供了一种设备,该设备包括具有成型腔室的模具部分和用于利用可模制材料填充成型腔室的填充装置,填充装置包括用于可模制材料和空气的流的进入管道和与成型腔室连通的预备腔室,其中,进入管道在一位置处通向预备腔室,使得以螺旋运动的方式朝向成型腔室输送可模制材料和空气的流,从而将可模制材料与空气分离
。
15.在本发明的第二方面,提供了一种用于利用可模制材料填充模具的成型腔室的方法,该方法包括将可模制材料和空气的流输送到与成型腔室连通的预备腔室的步骤,其中,
可模制材料和空气的流在预备腔室中以螺旋运动的方式移动,以将可模制材料与空气分离,并且其中,与空气分离的可模制材料积聚在成型腔室中
。
16.由于本发明的第一方面和第二方面,特别是由于可模制材料和空气的流在预备腔室中的螺旋运动,在预备腔室中限定了旋风分离器
。
这允许空气有效地与可模制材料分离,使得进入成型腔室的空气量远小于进入预备腔室的流中存在的空气量
。
17.更具体地,在预备腔室内部的螺旋运动期间,可模制材料的颗粒撞击界定预备腔室的表面,这有助于可模制材料的颗粒与空气分离
。
然后颗粒积聚在成型腔室中,成型腔室可以在预备腔室的下方或上方
。
18.在预备腔室的出料口处,可模制材料
(
其包含很少的空气量或完全不包含任何空气
)
可以被均匀地压缩,以相对容易地产生期望的物体
。
换句话说,从进入成型腔室的预备腔室到达的可模制材料已经经历了一种“预压实”,从某种意义上说,该可模制材料已经损失了它最初包含的空气中的大量空气
。
这意味着当在成型腔室中压缩可模制材料时,可以更快和更容易地实现期望的压实度
。
19.根据本发明的第一方面的设备和由本发明的第二方面提供的方法还允许以简单的方式利用可模制材料填充成型腔室,因为它们不需要使机械部件运动以将空气与可模制材料分离
。
20.在本发明的第三方面中,提供了一种用于利用可模制材料成型物体的模具,该模具包括壳体
、
至少部分地容纳在壳体中的内成型元件
、
围绕内成型元件的中间元件,其中,在内成型元件与壳体之间可以限定中空空间,中间元件能够在后部位置定位在中空空间中,在后部位置中,可模制材料被接收在中空空间中,中间元件能够相对于内成型元件从后部位置朝向成型位置滑动,以减小中空空间的体积并且成型物体的侧向壁
。
21.在本发明的第四方面中,提供了一种用可模制材料成型物体的方法,该方法包括以下步骤:
[0022]-将可模制材料引入壳体中,内成型元件至少部分地容纳在壳体中,内成型元件由中间元件围绕;
[0023]-使中间元件相对于内成型元件向后运动,从而使可模制材料流入限定在内成型元件与壳体之间的中空空间中;
[0024]-使中间元件相对于内成型元件向前运动,以减小中空空间的体积并且成型物体的侧向壁
。
[0025]
通过使中间元件相对于内成型元件向后运动,也就是说,将中间元件定位在后部位置,可以在中空空间中产生一种负压,该负压将可模制材料吸引到中空空间中
。
这允许中空空间被有效地填充,即使该中空空间具有相当大的轴向尺寸或相对小的径向厚度,并且即使可模制材料不容易在模具中流动
。
[0026]
由此,可以获得以物体,在该物体中可模制材料已经在物体的几乎所有部分中以基本上均匀的方式被压实
。
[0027]
根据本发明的第三方面的模具和根据本发明的第四方面的方法不需要复杂的构造,因为它们可以仅使用所涉及的模具的部件的向前和向后运动
(
即,在轴向方向上的运动
)
来操作
。
也就是说,不需要横向运动或径向运动,横向运动或径向运动可能使模具的结构及其操作复杂化
。
[0028]
在一个实施例中,内成型元件是凸形成型元件
。
凸形成型元件可以界定布置在壳体的内部的成型腔室的一部分
。
[0029]
中间元件可以是围绕凸形成型元件的管状元件
。
[0030]
中空空间可以是限定在凸形成型元件与壳体之间的环形空间
。
[0031]
在本发明的第五方面中,提供了一种用于利用可模制材料成型物体的模具,该模具包括具有至少部分地围绕轴线的侧向部分的成型腔室,模具还包括具有周边管道的填充装置,该周边管道至少部分地围绕该轴线并且能够选择性地打开以将可模制材料供给到侧向部分中
。
[0032]
在本发明的第六方面中,提供了一种用于利用可模制材料在成型腔室中成型物体的方法,该成型腔室具有至少部分地围绕轴线的侧向部分,该方法包括选择性地打开至少部分地围绕轴线的周边管道以将可模制材料供给到侧向部分中的步骤
。
[0033]
由于本发明的第五方面和第六方面,可以以基本上均匀的压实度填充成型腔室,以获得质量良好的物体,特别地但不排他性地,该物体是凹形物体,诸如盖
、
容器或用于容器的预成型件
。
[0034]
在一个实施例中,成型腔室的侧向部分是围绕轴线的管状部分
。
[0035]
在一个实施例中,成型腔室具有横向部分,该横向部分横向于轴线闭合管状部分
。
[0036]
填充装置可以包括中心管道,该中心管道能够选择性地打开以将可模制材料供给到横向部分中
。
[0037]
参考附图可以更好地理解和实施本发明,附图示出了本发明的若干示例
、
非限制性实施例,在附图中:
[0038]
图1是用于利用可模制材料成型物体的设备的示意性截面视图;
[0039]
图2是沿着图1的平面
ii-ii
截取的截面;
[0040]
图3至图5是类似于图1的示意性截面视图,其中的每个图示出了根据相应的替代实施例的用于利用可模制材料成型物体的设备;
[0041]
图6是处于初始构造的用于成型物体的模具的示意性截面视图;
[0042]
图7是类似于图6的视图,示出了处于中间构造的模具;
[0043]
图8是类似于图6的视图,示出了处于最终成型构造的模具;
[0044]
图9是处于初始构造的用于成型物体的模具的替代实施例的示意性截面视图;
[0045]
图
10
是类似于图9的视图,示出了处于中间构造的模具;
[0046]
图
11
是类似于图9的视图,示出了处于最终成型构造的模具;
[0047]
图
12
是处于初始构造的用于成型物体的模具的另一替代实施例的示意性截面视图;
[0048]
图
13
是类似于图
12
的视图,示出了处于中间构造的模具;
[0049]
图
14
是类似于图
12
的视图,示出了处于最终成型构造的模具;
[0050]
图
15
是用于成型物体的模具在填充模具的成型腔室的侧向部分的步骤期间的示意性截面视图;
[0051]
图
16
是图
15
的模具在填充成型腔室的横向部分的步骤期间的示意性截面视图;
[0052]
图
17
是示出根据替代实施例的模具的示意性截面视图,该模具处于第一成型元件和第二成型元件间隔开的间隔开构造;
[0053]
图
18
是类似于图
17
的在填充模具的成型腔室的侧向部分的步骤期间的视图;
[0054]
图
19
是类似于图
17
的在填充模具的横向部分的步骤期间的视图;
[0055]
图
20
是类似于图
17
的在成型步骤期间的视图
。
[0056]
图1和图2示出了用于利用可模制材料
(
例如但非排他性地,包含源自自天然纤维
(
尤其是纤维素
)
的材料的可模制材料
)
填充模具的成型腔室的装置
1。
可模制材料可以是粉末
、
颗粒或薄片的形式
。
可模制材料可以可选地包括添加剂,诸如粘合物质
。
[0057]
装置1允许可模制材料被引入模具的成型腔室
2(
如图1中示意性地示出的
)
中,在该成型腔室中,可模制材料可以被成形以获得期望的物体
。
在所示的示例中,成型腔室2配置成型成具有凹形形状的物体,例如容器
、
用于容器的盖
、
用于容器的预成型件等
。
[0058]
其中限定成型腔室2的模具可以被包括在用于通过模压成型获得期望物体的模压成型设备中
。
[0059]
成型腔室2可以特别地包括旨在形成物体的侧向壁的围绕轴线z延伸的管状部分或侧向部分
3。
侧向部分3可以具有在垂直于轴线z的平面中截取的截面,该截面由圆形
、
或椭圆形
、
或具有任意数量的边的多边形等的外周边界定
。
[0060]
侧向部分3可以围绕轴线z延伸
360
°
,在这种情况下,侧向部分3具有围绕轴线z闭合的截面
(
也就是说,在垂直于轴线z的平面中截取的截面
)。
可替代地,侧向部分3可以围绕轴线z延伸小于
360
°
,在这种情况下,侧向部分3具有开放的截面
(
也就是说,在垂直于轴线z的平面中截取的截面
)
,例如呈“c”形或“u”形
。
[0061]
成型腔室2限定在模具部分
14
中,该模具部分适于与未示出的另一模具部分联合操作,以形成物体
。
模具部分
14
包括内成型元件4和外成型部件5,该内成型元件4从侧向部分3的内侧界定该侧向部分,该外成型部件围绕侧向部分3,也就是说,该外成型部件从外侧界定该侧向部分
。
因此,侧向部分3被限定在内成型元件4与外成型部件5之间
。
内成型元件4可以是凸形成型元件
。
[0062]
模具部分
14
还包括未示出的中间成型元件,该中间成型元件可在侧向部分3的内侧滑动,以形成物体的边缘区
。
在所示的示例中,中间成型元件是环形成型元件,旨在形成物体的环形边缘区
。
[0063]
中间成型元件定位在填充装置1的相对侧,也就是说,在图1中所示的成型腔室2的下端处
。
因此,中间成型元件在与引入可模制材料的一侧的相对侧闭合成型腔室
2。
[0064]
更详细地,侧向部分3沿着轴线z的尺寸大于要获得的物体沿着轴线z的尺寸
。
发生这种情况是因为填充成型腔室2的侧向部分3的可模制材料旨在由于上述中间成型元件而在轴向方向上被压缩,该中间成型元件在成型腔室2已经被填充之后在内成型元件4与外成型部件5之间滑动
。
由此,在成型期间减小了物体的侧向壁在平行于轴线z的方向上的尺寸
。
[0065]
成型腔室2还可以包括端部部分6,该端部部分旨在构建物体的横向壁,也就是说,当物体已经成型并且仍然在成型腔室2中时横向于
(
特别是垂直于
)
轴线z延伸的壁
。
[0066]
在所示的示例中,成型腔室2的端部部分6定位在侧向部分3的上方,使得所形成的物体是处于倒置位置的凹形物体,也就是说,具有面向下的凹面
。
然而,这种情况不是必需的,并且要成型的物体的其他布置是可能的
。
例如,侧向部分3可以定位在端部部分6的上方,以形成具有面向上的凹面的凹形物体
。
[0067]
填充装置1位于模具部分
14
的上方,用于利用从顶部向下流动的可模制材料填充
成型腔室
2。
这种情况不是必需的,并且在未示出的替代实施例中,填充装置1还可以相对于成型腔室2以不同的方式定位,例如在模具部分
14
的下方
。
[0068]
填充装置1包括外壳7,该外壳的内部限定预备腔室8,预备腔室8适于在可模制材料到达成型腔室2之前接收可模制材料
。
[0069]
外壳7由内表面9界定,该内表面在垂直于轴线z截取的截面的周边对应于或更具体地等于侧向部分3的截面的外周边
。
这避免了外壳7的内表面9与从内部界定外成型部件5的表面之间的不连续性
。
[0070]
在所示的示例中,内表面9具有带有圆形基部的柱体的形状,但是其他形状也是可能的,例如具有椭圆形基部的柱体,或具有多边形基部的棱柱,或其他形状,这取决于要获得的物体的形状
。
[0071]
填充装置1还具有进入管道
10
,可模制材料和空气的流f可以通过该进入管道进入预备腔室
8。
进入管道
10
定位成使得可模制材料和空气的流在预备腔室8中以围绕轴线z的螺旋运动朝向成型腔室2流动
。
为此目的,进入管道
10
可以在切向方向上通向预备腔室8,例如使得进入管道
10
的母线
(
在进入管道具有柱形形状的情况下
)
与预备腔室8的内表面9相切,如图2的示例所示
。
[0072]
更一般地,进入管道
10
可以至少在其端部部分处沿着纵向轴线a延伸,该纵向轴线a不相对于轴线z成径向,也就是说,该纵向轴线a不与轴线z相交
。
[0073]
进入管道
10
也可以沿着弯曲轴线延伸
。
在这种情况下,在进入管道
10
的端部区段中与弯曲轴线相切的直线不与轴线z相交
。
[0074]
换句话说,进入管道
10
配置成将可模制材料和空气的流f在不相对于轴线z成径向的方向上输送到预备腔室8中,使得流f撞击预备腔室8的内表面9并且沿着围绕轴线z的螺旋轨迹朝向成型腔室2引导
。
[0075]
进入管道
10
可以在靠近预备腔室8的一端的位置处
、
特别是在靠近预备腔室8的与预备腔室8的邻近成型腔室2的另一端相对的一端的位置处通向预备腔室
8。
[0076]
在所示的示例中,进入管道
10
通向预备腔室8的上部区域,并且可模制材料和空气的流f从顶部向下移动以到达成型腔室
2。
在替代实施例中,进入管道
10
可以位于不同的位置,并且可模制材料和空气的流f可以例如从底部向上运动
。
[0077]
旨在在进入管道
10
中流动的流f可以是可模制材料和压缩空气的流,在这种情况下,填充装置1包括定位在进入管道
10
上游的压缩空气源
(
未示出
)
,用于供应旨在与可模制材料混合的压缩空气
。
压缩空气将可模制材料推向预备腔室8并且从预备腔室推向成型腔室2,并且可以有助于使可模制材料在预备腔室8的内部沿着螺旋路径流动
。
[0078]
在替代实施例中,可以不存在压缩空气源
。
在这种情况下,流f是可模制材料与环境压力下的空气一起的流,在可模制材料在模具中被压实之前,空气介于可模制材料的颗粒之间
。
[0079]
与流f中的可模制材料的颗粒混合的空气的主要作用是将颗粒运送到预备腔室8的内部
。
[0080]
通过使流以螺旋运动的方式在预备腔室8的内部移动,存在于流f中的可模制材料的颗粒撞击内表面9并且与最初存在于流f中的空气分离
。
这允许空气与可模制材料分离
。
[0081]
填充装置1还包括用于使与可模制材料分离的空气从预备腔室8流出的出料管道
11。
在所示的示例中,出料管道
11
是轴向的,也就是说,沿着预备腔室8的轴线z延伸
。
[0082]
出料管道
11
可以定位在外壳7的与成型腔室2相对的区域中
。
在所示的示例中,出料管道
11
通向预备腔室8的上部区域,即使这种情况不是必需的
。
[0083]
在所示的示例中,出料管道
11
穿过外壳7的端壁
12
,端壁
12
横向于
、
特别是垂直于轴线z定位
。
[0084]
出料管道
11
还限定在管状突起
13
的内部,该管状突起从端壁
12
在预备腔室8的内部突出,也就是说,朝向成型腔室2突出
。
[0085]
管状突起
13
可以由柱形内表面界定
。
[0086]
管状突起
13
沿着轴线z的尺寸可以小于预备腔室8沿着轴线z的尺寸
。
[0087]
在操作期间,填充装置1和模具部分
14
最初处于填充位置,如图1所示,在该填充位置中,填充装置1和模具部分
14
沿着轴线z对准
。
在所示的实施例中,在填充位置中,填充装置1定位在模具部分
14
的上方
。
[0088]
可模制材料和空气的流f通过进入管道
10
被输送到预备腔室8中
。
如前所述,与可模制材料混合的空气可以在大于环境压力的压力下
(
压缩空气
)
或在环境压力下
。
流f在预备腔室8的内部围绕轴线z以螺旋运动的方式移动,也就是说,遵循螺旋轨迹
(
在图1和图2中表示指示为
t1)。
螺旋运动是沿着螺旋的运动,在所示的示例中,该螺旋是柱形螺旋
。
在未示出的一个实施例中,流f的螺旋运动可以沿着锥形螺旋
。
[0089]
流f的螺旋运动发生在预备腔室8的周边区域中,该周边区域可以与成型腔室2的侧向部分3轴向对准
。
[0090]
当流f以螺旋运动的方式移动时,可模制材料的颗粒撞击成型腔室8的内表面9并且与流f中存在的空气分离
。
与空气分离的可模制材料减速并且积聚在预备腔室8的与进入管道
10
相对的端部处,从而填充相邻的成型腔室
2。
[0091]
在所示的示例中,在图1中用字母m指示的可模制材料在重力作用下在成型腔室2的侧向部分3中下降,该侧向部分以特别有效的方式被填充,即使侧向部分3沿着轴线z的尺寸相当大和
/
或在径向方向上的尺寸相对较小
。
[0092]
可模制材料还到达成型腔室2的端部部分
6。
[0093]
由于流f在预备腔室8中的路径期间使大量的空气与可模制材料分离,因此积聚在成型腔室2中的可模制材料具有比流过进入管道8的可模制材料高得多的密度
。
由此,在随后的模压成型步骤期间更容易压制可模制材料,因为在压制期间必须从可模制材料中排出的空气量是有限的
。
换句话说,由于在预备腔室8中发生的空气分离,进入成型腔室2的可模制材料可以说是“预压实的”,这使得随后的成型更加容易
。
[0094]
因此,填充装置1用作旋风分离器,其与模具相关联,以将流f中存在的空气与随后填充模具的可模制材料分离
。
[0095]
与可模制材料分离的空气通过出料管道
11
从预备腔室8流出
。
更具体地,空气以围绕轴线z的螺旋运动从预备腔室8流出
。
如图1和图2所示,空气特别地遵循沿着螺旋的轨迹
t2
,该螺旋与限定轨迹
t1
的螺旋同轴,但是具有比限定轨迹
t1
的螺旋更小的半径
。
这意味着流出的空气运动所沿着的轨迹
t2
在流入的可模制材料和空气的流的轨迹
t1
的内侧
。
此外,流出的空气的运动发生在与流入的可模制材料和空气的流f的方向相反的方向上,从某种意义上来说,在所示的示例中,流出的空气从底部向上行进,而流入的可模制材料和空气的
流f从顶部向下行进
。
[0096]
未示出的抽吸器件可以与出料管道
11
相关联,以抽吸出存在于预备腔室8中的空气并且促进空气沿着轨迹
t2
流出,如图1的箭头
f1
指示的
。
[0097]
此外,其中包括成型腔室2的模具部分
14
设置有通气开口,以允许在成型期间排出仍存在于可模制材料中的空气
。
通气开口可以是轴向的,如图1的箭头
f2
指示的
。
作为上述的替代或补充,通气开口可以是径向的
。
[0098]
通气开口可以连接到抽吸源,以有助于空气从模具流出
。
抽吸源允许优化可模制材料对成型腔室2的填充,尤其是在成型腔室2定位在预备腔室8的上方并且因此无法利用重力来填充成型腔室2的情况下
。
[0099]
在成型腔室2已经填充有可模制材料之后,未示出的驱动装置使填充装置1和模具部分
14
相对于彼此运动,使得填充装置1和模具部分
14
不再沿着轴线z彼此对准
。
换句话说,驱动装置配置成使填充装置1与成型腔室2脱离
。
由此,模具部分
14
可以与未示出的另一模具部分接合,该另一模具部分布置成在横向于轴线z的端部部分6处闭合成型腔室
2。
[0100]
现在可以开始模压成型的步骤,在模压成型中,使包括成型腔室2的模具部分
14
和未示出的另一模具部分朝向彼此运动,以压实可模制材料并形成物体
。
[0101]
与成型腔室2的侧向部分3相关联的未示出的中间成型元件在侧向部分3的内侧朝向端部部分6滑动,以用于在端部部分6的相对侧形成物体的横向于轴线z延伸的边缘区
。
[0102]
在物体已经在模具中成型之后,可以打开模具,并且模具部分
14
可以与填充装置1接合,使得模具部分可以被再次填充
。
[0103]
在未示出的替代实施例中,出料管道
11
可以在内成型元件4中制成,而不是在外壳7的端壁
12
中制成
。
出料管道
11
可以特别地在内成型元件4的中心区中延伸,例如沿着轴线z延伸
。
在这种情况下,与可模制材料分离的空气通过以螺旋运动的方式穿过内成型元件4而从预备腔室8流出
。
限定流出的空气运动所沿着的螺旋轨迹的螺旋具有比限定流入的可模制材料和空气的流f的轨迹
t1
的螺旋更小的半径
。
在这种情况下,流入的空气在与流f相同的方向上运动,也就是说,在所示的示例中从顶部向下运动
。
抽吸器件可以与出料管道相关联,以抽吸出与可模制材料分离的空气并且帮助空气从模具部分
14
流出
。
替代实施例可以有助于更有效地填充成型腔室2的端部部分
6。
[0104]
在参考图1和图2描述的实施例中,可模制材料和空气的流的螺旋运动主要发生在预备腔室8中,并且基本上在端部部分6附近结束
。
图3示出了根据替代实施例的填充装置
21
,其与图1和图2的实施例的不同之处在于,可模制材料和空气的流f的螺旋运动不仅发生在预备腔室8中,而且还在成型腔室2的侧向部分3中继续
。
也就是说,从进入管道
10
进入的可模制材料和空气的流f沿着螺旋轨迹
t10
运动,该螺旋轨迹从预备腔室8的进入管道
10
所通向的区域穿过到预备腔室8的与成型腔室2相邻的端部,并且从该端部继续到限定在内成型元件4与外成型部件5之间的侧向部分
3。
这允许附带的可模制材料到侧向部分3中,从而帮助可模制材料填充侧向部分3,即使侧向部分3具有相当大的轴向尺寸和
/
或可模制材料不容易流动并且倾向于易于结块
(packed)。
螺旋轨迹
t10
可以延伸远至侧向部分3的与预备腔室8相对的端部
。
与可模制材料分离的空气通过遵循在内成型元件4中制成的运输管道
15
中延伸的螺旋轨迹
t20
返回到外部环境中
。
在所示的示例中,内成型元件具有管状形状,使得运输管道
15
从内成型元件4的一端延伸到另一端
。
然后,空气从内成型元件4流入预备腔
室8,直到其到达出料管道
11
,类似于图1所示
。
空气最终从出料管道
11
排放到外部环境中,如由箭头
f1
所指示的
。
[0105]
流出的空气流运动所沿的螺旋轨迹
t20
具有比可模制材料和空气的流f遵循的螺旋轨迹
t10
小的半径,并且定位在螺旋轨迹
t10
的内侧
。
螺旋轨迹
t20
沿着轴线z在模具部分
14
和填充装置
21
的中心区域中延伸
。
[0106]
为了使螺旋轨迹
t10
在侧向部分3中继续,可以对进入管道
10
的几何形状和尺寸特征和位置以及流入的可模制材料和空气的流f的特性
(
压力
、
流量等
)
采取措施,并且如果需要,可以在侧向部分3的与填充装置
21
相对的端部处提供抽吸源
。
[0107]
图4示出了根据替代实施例的填充装置
31
,其与图1和图2中所示的实施例的不同之处在于,填充装置
31
包括分配板
16
,以允许改善可模制材料在成型腔室2的端部部分6中的分配
。
[0108]
分配板
16(
其例如可以在平面图中具有圆形形状
)
固定到沿着轴线z定位的杆
17
的一端
。
分配板
16
主要在垂直于轴线z的平面中延伸
。
杆
17
可以延伸到预备腔室8的与成型腔室2相对的端部,穿过出料管道
11。
[0109]
在填充装置
31
中,与可模制材料分离并朝向出料管道
11
前进的空气的流在分配板
16
的上方开始
。
介于分配板
16
与凸形成型元件2之间的可模制材料不受流出的空气流的干扰,并且可以更好地填充端部部分
6。
[0110]
在这种情况下,流出的空气再次通过遵循螺旋轨迹
t2
朝向外部环境行进,该螺旋轨迹
t2
在可模制材料和空气的流f遵循的螺旋轨迹
t1
的内侧且围绕轴线z延伸
。
在所示的示例中,轨迹
t2
在设置管状突起
13
的区域中介于杆
17
与该管状突起之间
。
[0111]
图5示出了根据另一替代实施例的填充装置
41
,其与图4所示的实施例的不同之处在于,除了分配板
16
之外,还提供了另一分配板
18。
分配板
16
介于成型腔室2与另一分配板
18
之间
。
分配板
16
和另一分配板
18
两者相对于杆
17
固定
。
[0112]
另外,另一分配板
18
可以在平面图中具有圆形形状,并且在横向于,特别是垂直于轴线z布置的平面中延伸
。
分配板
16
和另一分配板
18
彼此平行
。
[0113]
在与可模制材料分离之后从预备腔室8流出的空气的流在另一分配板
18
的正上方开始,沿着轨迹
t2
进行螺旋运动
。
这改善了利用可模制材料对端部部分6的填充
。
在未示出的一个实施例中,板
16
和
/
或另一板
18
和
/
或杆
17
可以是穿孔的
。
[0114]
还可以提供数量多于两个的分配板
。
先前参考图1和图2关于替代实施例提到的内容也适用于图3至图5的实施例
。
特别地,在所示的所有示例中,模具部分
14
可以定位在填充装置的上方
。
[0115]
出料管道
11
可以穿过内成型元件4,而不是在外壳7的与模具部分
14
相对的壁上敞开
。
[0116]
在第一模具部分
14
中,可以有用于使仍然与可模制材料混合的空气流出的轴向和
/
或径向通气管道,该通气管道可选地设置有抽吸器件
。
抽吸源还可以与出料管道
11
相关联
。
[0117]
图6至图8示出了用于由可模制材料形成物体的模具
51
,该可模制材料特别是包含源自自天然纤维的材料
(
诸如纤维素
)
的材料
。
模具
51
特别适合于加工呈粉末
、
颗粒或薄片形式的可模制材料
。
模具
51
可以例如用于形成凹形物体,诸如盖
、
容器
、
用于容器的预成型
件
。
更一般地,如图8所示,在模具
51
中形成的物体可以包括侧向壁
65
和横向壁
64
,该侧向壁围绕在图6至图8中指示为
z1
的轴线延伸,该横向壁横向于
、
例如垂直于上述轴线延伸
。
侧向壁
65
可以具有各种形状,例如柱形
、
截头圆锥形
、
具有多边形或椭圆形截面的棱柱形,或者其他形状
。
横向壁
64
可以是扁平的或具有其他形状
。
[0118]
模具
51
可以包括在模压成型设备中
。
[0119]
模具
51
包括适于从内部成形物体的内成型元件
54。
内成型元件
54
可以是凸形成型元件
。
[0120]
中间元件
60
围绕内成型元件
54。
中间元件
60
可以成形为如管状元件
。
[0121]
中间元件
60
可以与内成型元件
54
直接接触,如图6至图8所示,在这种情况下,中间元件
60
直接围绕内成型元件
54。
在未示出的一个实施例中,其他部件可以介于内成型元件
54
与中间元件
60
之间,在这种情况下,中间元件
60
围绕内成型元件
54
,它们之间插入有这些部件
。
[0122]
模具
51
还包括适于从外部成形物体的凹形成型元件
58。
[0123]
内成型元件
54
和凹形成型元件
58
沿着模制轴线
z1
对准
。
在所示的示例中,模制轴线
z1
是竖直的,但是这种情况不是必需的,并且在未示出的实施例中,模制轴线
z1
可以是水平的或倾斜的
。
[0124]
由于未示出的运动装置,内成型元件
54
和凹形成型元件
58
可在间隔开构造与成型构造之间沿着模制轴线
z1
相对于彼此运动
。
在图中未示出的间隔开构造中,内成型元件
54
和凹形成型元件
58
彼此间隔开,使得可以从模具
51
移除成型的物体并且将要成型的新的可模制材料引入模具
51
中
。
在图8所示的成型构造中,可模制材料已经在内成型元件
54
与凹形成型元件
58
之间成型,从而获得物体
。
[0125]
在所示的示例中,凹形成型元件
58
定位在内成型元件
54
的上方
。
这种情况不是必需的,并且在未示出的实施例中,内成型元件
54
可以定位在凹形成型元件
58
的下方
。
[0126]
凹形成型元件
58
可以包括围绕模制轴线
z1
延伸的壳体
57
,该壳体具有例如管状形状
。
壳体
57
至少部分地围绕中间元件
60。
壳体
57
可以与中间元件
60
直接接触,如图6至图8所示,或者在未示出的替代实施例中,一个或多个部件可以介于壳体
57
与中间元件
60
之间
。
中间元件
60
围绕模制轴线
z1
延伸
。
[0127]
凹形成型元件
58
还包括横向成型表面
61
,用于从外部成形物体的横向壁
64
,也就是说,物体的横向于模制轴线
z1
定位的壁
。
壳体
57
从横向成型表面
61
朝向内成型元件
54
突出
。
[0128]
横向成型表面
61
可以在与壳体
57
分离的部件上制成,所述部件在任何情况下都相对于壳体
57
固定
。
可替代地,横向成型表面
61
和壳体
57
可以被包括在单个机械部分中
。
[0129]
在内成型元件
54
与壳体
57
之间限定中空空间
53
,中空空间
53
围绕模制轴线
z1
延伸
。
中空空间
53
可以是环形空间,例如具有柱形形状
。
[0130]
成型腔室
52
限定在模具
51
的内部,成型腔室
52
适于接收可模制材料
。
在成型腔室
52
中,可模制材料可以被压缩以形成期望的物体
。
更具体地,成型腔室
52
被限定在壳体
57
的内部
。
成型腔室
52
特别地被限定在凹形成型元件
58、
内成型元件
54
与中间元件
60
之间
。
成型腔室
52
具有可以根据在模具
51
中的成型过程的步骤而变化的形状和尺寸
。
中空空间
53
被包括在成型腔室
52
中
。
[0131]
中间元件
60
在横向于模制轴线
z1
的方向上由面向横向成型表面
61
的环形表面
62
界定
。
环形表面
62
适于形成物体的环形边缘
66
,如图8所示
。
内成型元件
54
在横向于模制轴线
z1
的方向上由面向横向成型表面
61
的前表面
63
界定
。
[0132]
还提供了用于使中间元件
60
和中空空间
53
相对于彼此运动的未示出的运动装置
。
运动装置可以例如与中间元件
60
相关联
。
由此,中间元件
60
可在中空空间
53
的内部以平行于模制轴线
z1
的线性运动进行运动
。
该线性运动交替地朝向横向成型表面
61
和远离横向成型表面
61
发生
。
[0133]
更具体地,中间元件
60
可在图7所示的后部位置
p1
中定位在中空空间
53
中,在该后部位置中,内成型元件
54
的相当大部分从中间元件
60
突出到成型腔室
52
的内部
。
在中间元件
60
的后部位置
p1
,中空空间
53
的体积处于其最大值
。
因此,可模制材料可以被接收在壳体
57
与内成型元件
54
之间
。
[0134]
中间元件
60
可相对于内成型元件
54
从后部位置
p1
朝向成型位置
p2
移位,如图8所示,在成型位置中,成型腔室
52
具有要获得的物体的形状,并且物体的环形边缘
66
成型为与中间元件
60
接触
。
在成型位置
p2
,内成型元件
54
从中间元件
60
突出得比其在后部位置
p1
从中间元件突出得更少
。
为了从后部位置
p1
到成型位置
p2
,可以使中间元件
60
在平行于模制轴线
z1
的方向上朝向横向成型表面
61
运动
。
除了后部位置
p1
和成型位置
p2
之外,中间元件
60
还可相对于内成型元件
54
定位在其他位置
。
例如,中间元件
60
可以定位在后部位置
p1
与成型位置
p2
之间的任何中间位置中,或者甚至定位在内成型元件
54
从中间元件
60
突出得比其在成型位置
p2
从中间元件突出得更少的位置中
。
[0135]
中间元件
60
可以定位在向前位置
p0
,如图6所示,在向前位置中,环形表面
62
与前表面
63
基本上对准,也就是说,环形表面
62
和前表面
63
沿着模制轴线
z1
基本上定位在相同的水平处
。
[0136]
中空空间
53
对应于成型腔室
52
的旨在形成物体的侧向壁
65
的区域
。
相反,成型腔室
52
的位于横向成型表面
61
与前表面
63
之间的一部分旨在形成横向壁
64。
[0137]
在操作期间,内成型元件
54
和凹形成型元件
58
最初处于图中未示出的间隔开构造,在间隔开构造中,成型腔室
52
是敞开的并且可从外部进入,使得可以从模具
51
中移除刚刚成型的物体
。
随后,使内成型元件
54
和凹形成型元件
58
彼此靠近并到图6所示的初始构造中,在初始构造中,成型腔室
52
被闭合并填充有可模制材料
。
可模制材料通过未示出的填充装置引入成型腔室
52
中
。
[0138]
在图6所示的初始构造中,成型腔室
52
具有比要成型的物体的体积大得多的体积,并且具有与要成型的物体的形状不同的形状
。
在所示的示例中,在图6所示的初始构造中,中间元件
60
的环形表面
62
沿着模制轴线
z1
与内成型元件
54
的前表面
63
基本上对准
。
因此,成型腔室
52
具有基本上柱形的形状
。
在该构造中,在内成型元件
54
与中间元件
60
之间没有限定中空空间
53。
[0139]
随后,如图7所示,在所示的示例中与中间元件
60
相关联的运动装置使中间元件
60
远离横向成型表面
61
运动
。
与凹形成型元件
58
一样,内成型元件
54
保持在它们之前的位置
。
中间元件
60
到达后部位置
p1
,在后部位置中,中空空间
53
的体积处于其最大值
。
这产生拉力,也就是说,将先前定位在横向成型表面
61
与前表面
63
之间的可模制材料吸引到中空空间
53
中的一种吸入或抽吸
。
该拉力类似于在注射器中当柱塞被向后拉动以吸入液体时发生
的拉力
。
由于上述拉力,即使中空空间
53
具有沿着模制轴线
z1
的相当大的尺寸或有限的径向厚度,可模制材料也可以相对容易地填充中空空间
53。
[0140]
换句话说,中间元件
60
的向后运动
(
也就是说,中间元件
60
远离横向成型表面
61
的运动
)
在中空空间
53
中产生负压,该负压允许可模制材料流入中空空间
53
并填充中空空间
53。
[0141]
在所示的示例中,可模制材料通过重力辅助流入中空空间
53。
[0142]
然而,如果内成型元件
54
不定位在凹形成型元件
58
的下方,则可模制材料在任何情况下都由于由沿着模制轴线
z1
远离横向成型表面
61
运动的中间元件
60
施加的拉力的作用而填充中空空间
53。
[0143]
在图7的构造中,填充成型腔室
52(
包括中空空间
53)
的可模制材料具有相对低的密度,该密度远低于形成的物体中的可模制材料的密度
。
[0144]
在已经达到图7的构造并且因此已经利用可模制材料填充中空空间
53
之后,驱动装置使内成型元件
54
和凹形成型元件
58
沿着模制轴线
z1
朝向彼此运动
。
内成型元件
54
由此穿入壳体
57
的内部以形成物体的横向壁
64。
同时,与中间元件
60
相关联的运动装置使中间元件平行于模制轴线
z1
朝向横向成型表面
61
运动,直到到达图8所示的成型位置
p2
,在该成型位置,环形表面
62
与横向成型表面
63
之间的距离基本上等于要获得的物体的高度
。
物体的侧向壁
65
以这种方式形成
。
[0145]
成型腔室
52
达到其确定的形状,并且可模制材料被压缩,直到可模制材料达到期望的密度,并且获得要成型的物体
。
模具
51
现在准备好返回到间隔开构造并且开始新的成型周期
。
[0146]
模具
51
可以具有未示出的通气开口,以允许最初与可模制材料混合的空气在物体成型时从成型腔室
52
流出
。
[0147]
图6至图8中所示的模具
51
允许获得质量良好的凹形物体,其中可模制材料具有基本上均匀的压实度,也就是说,实际上恒定的密度
。
[0148]
在构造和操作方面,模具
51
非常简单,因为该模具不需要其部件的径向运动,而是仅通过使构成该模具的元件在轴向方向上
(
即,平行于模制轴线
z1)
运动来操作
。
[0149]
通过在成型腔室
52
已经被填充和闭合之后使中间元件
60
远离横向成型表面
61
运动,在中空空间
53
中产生负压,该负压允许可模制材料在内成型元件
54
与壳体
57
之间流动,以便形成物体的侧向壁
65。
[0150]
图9至图
11
示出了根据替代实施例的模具
151
,其与图6至图8中所示的模具
51
的不同之处主要在于,其包括凹形成型元件
158
,该凹形成型元件
158
具有与模具
51
的凹形成型元件
58
不同的结构
。
[0151]
模具
151
的与模具
51
共同的部分将用与图6至图8中使用的相同的附图标记指示,并且将不再详细描述
。
[0152]
更具体地,凹形成型元件
158
包括面向中间元件
60
的推动器部件
67
,用于将可模制材料推入中空空间
53
中
。
推动器部件
67
围绕模制轴线
z1
延伸并且可以具有管状形状
。
[0153]
推动器部件
67
与中间元件
60
轴向对准
。
特别地,推动器部件
67
可以具有基本上等于中间元件
60
的对应横向尺寸的内横向尺寸和外横向尺寸,即使这种条件不是必需的
。
[0154]
凹形成型元件
158
还包括内芯
68
,该内芯由横向于
、
特别是垂直于模制轴线
z1
布置
的横向成型表面
161
界定
。
横向成型表面
161
面向内成型元件
54
的前表面
63。
[0155]
凹形成型元件
158
还包括壳体
157
,该壳体可以具有管状形状并且围绕模制轴线
z1
延伸
。
壳体
157
类似于图6至图8中所示的模具
51
的壳体
57。
[0156]
推动器部件
67
介于内芯
68
与壳体
157
之间
。
[0157]
提供了未示出的移位装置,用于使推动器部件
67
相对于内芯
68
和壳体
157
在平行于模制轴线
z1
的方向上以前后线性运动的方式运动
。
因此,推动器部件
67
可在内芯
68
与壳体
157
之间滑动
。
[0158]
特别地,移位装置配置成使推动器部件
67
运动,使得推动器部件基本上跟随中间元件
60。
[0159]
在操作期间,使模具
151
在图9所示的初始构造中,类似于图6所示的模具
51
的初始构造
。
在初始构造中,在凸形模元件
54
与凹形模元件
158
之间限定成型腔室
52
,成型腔室
52
充满可模制材料并且具有比要获得的物体大得多的体积,并且具有与要获得的物体不同的形状
。
在图9所示的初始构造中,推动器部件
67
的端表面
69
沿着模制轴线
z1
与横向成型表面
161
基本上对准,也就是说,端表面
69
与横向成型表面
161
基本上处于相同的水平处
。
类似地,中间元件
60
的环形表面
62
沿着模制轴线
z1
与内成型元件
54
的前表面
63
基本上对准
。
因此,成型腔室
52
可以是基本上柱形的
。
[0160]
随后,中间元件
60
相对于内成型元件
54
向后运动,也就是说,远离横向成型表面
161
运动,由此在内成型元件
54
与壳体
157
之间限定中空空间
53。
中间元件
60
到后部位置
p1
中,如图
10
所示,在该后部位置中,中空空间
53
的体积处于其最大值
。
中间元件
60
朝向后部位置
p1
的运动在中空空间
53
的内部产生负压,由此存在于成型腔室
52
中的可模制材料被吸入中空空间
53
中
。
[0161]
为了促进可模制材料流入中空空间
53
,中空空间可以连接到未示出的抽吸源,如由箭头k所指示,抽吸源将可模制材料抽吸到中空空间
53
中
。
[0162]
当中间元件
60
通过远离横向成型表面
161
运动而向后运动时,推动器部件
67
向前运动,从而使该推动器部件靠近内成型元件
54。
在一个实施例中,推动器部件
67
向前运动的量可以与中间元件
60
向后运动的量相同,由此使得推动器部件
67
和中间元件
60
的距离保持恒定
。
[0163]
通过使推动器部件
67
朝向中间元件
60
运动,推动器部件
67
朝向中空空间
53
推动介于端表面
69
与环形表面
62
之间的可模制材料
。
由推动器部件
67
施加的推力有助于可模制材料填充中空空间
53
,即使中空空间长和
/
或窄,或者即使可模制材料不容易流动
。
[0164]
在中空空间
63
已经被填充之后,使内成型元件
54
朝向内芯
68
运动以成形物体的横向壁
64。
中间元件
60
也朝向横向成型表面
161
向前运动,并且同时推动器部件
67
朝向内芯
68
向后运动,直到端表面
69
进入与横向成型表面
161
齐平的位置
。
端表面
69
和横向成型表面
161
由此形成物体的横向壁
64
的外表面
。
在高度已经减小的中空空间
53
中,成型物体的侧向壁
65
,该侧向壁的环形边缘
66
由中间元件
60
成形
。
[0165]
图
12
至图
14
示出了根据替代实施例的模具
251。
模具
251
在结构上类似于先前描述的模具
51
,但是与先前描述的模具不同地操作
。
[0166]
模具
251
包括凹形成型元件
258
,该凹形成型元件包括围绕模制轴线
z1
延伸的壳体
257
,内芯
268
被容纳在该壳体内
。
内芯
268
可在壳体
257
的内部在平行于模制轴线
z1
的方向
上前后滑动
。
为此目的,未示出的移位装置与内芯
268
相关联
。
内芯
268
由面向内成型元件
54
的横向成型表面
261
界定
。
[0167]
模具
251
的与模具
51
的部件基本上相同的其余部件将用图6至图8中使用的相同附图标记指示,并且将不再详细描述
。
[0168]
在操作期间,如图
12
所示,模具
251
在初始构造中,该初始构造与图6所示的模具
51
的初始构造基本上相同
。
中间元件
60
的环形表面
62
与内成型元件
54
的前表面
63
齐平
。
成型腔室
52
可以具有柱形形状
。
[0169]
随后,当内成型元件
54
保持在固定位置时,中间元件
60
向后运动,也就是说,远离前表面
63
运动,以产生中空空间
53。
这在中空空间
53
中产生负压,该负压将可模制材料拉入中空空间
53
中
。
[0170]
可模制材料流入中空空间
53
可以通过未示出的抽吸源来辅助,如由箭头k所指示的,抽吸源将可模制材料抽吸到壳体
257
与内成型元件
54
之间
。
[0171]
同时,如图
13
所示,使内芯
258
靠近内成型元件
54
,从而减小成型腔室
52
的体积
。
这具有以下双重效果:压缩存在于成型腔室
52
中的可模制材料以降低其密度;以及辅助可模制材料朝向中空空间
53
流动,以此方式可模制材料可以更容易地填充中空空间
53。
[0172]
在中间元件
60
已经到达图
13
所示的后部位置
p1
之后并且在中空空间
53
已经填充有可模制材料之后,中间元件
60
沿着平行于模制轴线
z1
的方向向前运动,以压缩存在于中空空间
53
中的可模制材料并且减小中空空间
53
的轴向尺寸
。
[0173]
同时,当壳体
257
保持在固定位置时,内芯
258
向后运动以返回到原始位置,在该原始位置中,内芯位于图
12
所示的初始构造
。
内成型元件
54
在平行于轴线
z1
的方向上朝向内芯
268
移位
。
内成型元件
54
以此方式跟随内芯
258
并且定位成与内芯相距一定距离,该距离等于物体的横向壁
64
的厚度,如图
14
所示
。
[0174]
由此获得期望的物体
。
[0175]
在先前描述的模具
51、151、251
的所有实施例中,在成型腔室
52
中
、
特别是在中空空间
53
中可以存在通气开口或通气孔,用于使与可模制材料混合的空气随着可模制材料被压缩而逐渐流出
。
[0176]
在先前描述的模具
51、151、251
的所有实施例中,中空空间
53
可以连接到未示出的抽吸源,以促进可模制材料填充中空空间
53。
[0177]
图
15
和图
16
示出了用于形成凹形物体
(
也就是说,具有围绕轴线延伸的侧向壁和横向于轴线延伸的横向壁的物体
)
的模具
351。
可以在模具
351
中形成的凹形物体的示例包括盖
、
容器
、
用于容器的预成型件
。
通过压缩可模制材料在模具
351
中形成物体,该可模制材料可以包括源自自天然纤维的材料并且可以以颗粒
、
薄片或粉末的形式进料到模具
351
中
。
[0178]
模具
351
包括成型腔室
352
,该成型腔室适于接收必须被压制以获得物体的可模制材料
。
如图
16
所示,成型腔室
352
包括侧向部分
353
,该侧向部分围绕轴线
z2
延伸并且旨在形成物体的侧向壁
。
侧向部分
353
可以是管状部分
。
成型腔室
352
还可以包括横向部分
356
,在该横向部分中可以形成物体的横向壁
。
[0179]
模具
351
包括适于成形物体的内表面的内成型元件
354。
内成型元件
354
可以是凸形成型元件
。
[0180]
内成型元件
354
具有横向于轴线
z2
布置的横向表面
363
,以界定横向部分
356。
[0181]
内成型元件
354
容纳在壳体
357
中,该壳体可以具有管状形状并且围绕轴线
z2
延伸
。
成型腔室
352
的侧向部分
353
识别在壳体
357
与内成型元件
354
之间
。
[0182]
模具
351
还包括用于利用可模制材料填充成型腔室
352
的填充装置
301。
[0183]
在所示的示例中,填充装置
301
定位在内成型元件
354
的上方,这促进填充成型腔室
352
,因为允许利用重力将可模制材料引入成型腔室
352
中
。
模具
351
配置成形成倒置构造的物体,也就是说,具有面向下的凹面
。
然而,这种情况不是必需的
。
在未示出的一个实施例中,填充装置可以定位在成型腔室
352
的下方,在这种情况下,成型腔室
352
可以借助于抽吸和
/
或加压空气来填充
。
[0184]
填充装置
301
包括容纳主体
364
,该容纳主体可以定位成与壳体
357
接触
。
[0185]
填充装置
301
具有用于将可模制材料供给到成型腔室
352
的横向部分
356
中的第一管道或中心管道
365。
中心管道
365
可以沿着轴线
z2
延伸
。
[0186]
更具体地,填充装置包括中间主体
367
,中心管道
365
形成在中间主体
367
的内部
。
中间主体
367
可以具有沿着轴线
z2
延伸的主要尺寸,也就是说长度
。
中间主体
367
可以具有管状形状,并且可以例如具有围绕轴线
z2
延伸的侧向壁
。
[0187]
在中心管道
365
的内部可运动的是闭合构件
366
,该闭合构件特别地成形为类似于杆,该闭合构件沿着轴线
z2
延伸并且与中心管道
365
同轴
。
由于中心管道
365
的中心部分被闭合构件
366
占据,因此中心管道
365
的用于可模制材料的运输截面的形状类似于环形
。
[0188]
闭合构件
366
可沿着轴线
z2
前后线性移位,以使中心管道
365
与成型腔室
352
的横向部分
356
连通,或者可替代地将中心管道
365
与横向部分
356
隔离
。
[0189]
特别地,闭合构件
366
可在图
15
所示的闭合位置与图
16
所示的打开位置之间运动,在闭合位置中,可模制材料不能从中心管道
365
流出,在打开位置,可模制材料可以从中心管道
365
朝向成型腔
352
流动,特别是朝向成型腔的横向部分
356
流动
。
由于未示出的驱动元件,闭合构件
366
可在闭合位置与打开位置之间移位
。
[0190]
在闭合位置,闭合构件
366
的一个端部
369
与中间主体
367
的内密封表面
368
接合,也就是说,与内密封表面
368
接触
。
端部
369
可以可选地是闭合构件
366
的渐缩形端部,例如斜切或倒圆端部
。
在打开位置,端部
369
与内密封表面
368
间隔开,以允许可模制材料从中心管道
365
朝向横向部分
356
通过,特别是通过限定在端部
369
与内密封表面
368
之间的环形通道
。
端部
369
在横向于轴线
z2
的方向上由前表面
375
界定,该前表面可以是平坦的
。
前表面
375
面向内成型元件
354。
[0191]
中心管道
365
配置成接收流入的可模制材料和空气
(
特别是压缩空气
)
的中心流或第一流
h1。
第一流
h1
通过中心管道
365
的与端部
369
相对的另一端部
(
在所示的示例中,也就是说通过上端
)
进入中心管道
365。
[0192]
模具还包括第二管道或周边管道
370
,用于将可模制材料供给到成型腔室
352
的侧向部分
353
中
。
在所示的示例中,周边管道
370
具有环形形状并且限定在容纳主体
364
与中间主体
367
之间的中空空间中
。
周边管道围绕轴线
z2
延伸
。
横向于轴线
z2
延伸的进入管道
310
通向周边管道
370
,例如在周边管道
370
的远离成型腔室
352
的区域中通向周边管道
。
进入管道
310
旨在将可模制材料和空气
(
例如可模制材料和压缩空气
)
的第二流或周边流
h2
输送到周边管道
370
中
。
[0193]
周边管道
370
可以由于挡板
371
而选择性地与成型腔室
352
的侧向部分
353
连通或
与侧向部分
353
隔离
。
在所示的示例中,挡板
371
被制成在中间部件
367
的加宽端部部分上
。
加宽端部部分由围绕轴线
z2
延伸并且可以具有截头圆锥形状的外密封表面
372
界定
。
外密封表面
372
适于以形状联接方式与可以在容纳主体
364
上制成的邻接表面
373
接合
。
邻接表面
373
可以具有形成在容纳主体
364
中的截头圆锥形斜面的形状,在从填充装置
301
朝向成型腔室
352
移位的情况下,周边管道
370
的外径在该截头圆锥形斜面处增加
。
[0194]
外密封表面
372
和内密封表面
368
制成位于中间主体
367
的相同高度处且分别在中间主体
367
的面向容纳主体
364
的侧向表面上和中间主体
367
的指向轴线
z2
的另一侧向表面上
。
[0195]
中间主体
367
进一步具有前密封表面
374
,该前密封表面可以横向于
、
特别是垂直于轴线
z2
定位
。
前密封表面
374
面向凸形成型元件
35。
前密封表面
374
可以是基本上平坦的,并且可以可选地成形为类似环形
。
前密封表面
374
适于紧邻内成型元件
354
,以将中心管道
365
与成型腔室
352
的侧向部分
353
隔离
。
[0196]
运动器件与中间主体
367
相关联,用于使中间主体
367
平行于轴线
z2
以线性运动的方式前后运动
。
[0197]
更具体地,中间主体
367
可在图
15
所示的向前位置与图
16
所示的后部位置之间运动
。
在向前位置中,前密封表面
374
与内成型元件
354
的横向表面
363
接触,而外密封表面
372
与容纳主体
364
的邻接表面
373
间隔开
。
由此,周边管道
370
打开并且与成型腔室
352
的侧向部分
353
连通
。
在后部位置,前密封表面
374
与内成型元件
354
间隔开,而外密封表面
372
与容纳主体
364
接触
。
由此,周边管道
370
被闭合
。
[0198]
模具
351
还包括未示出的中间成型元件,该中间成型元件可以成形为类似于环形成型元件,用于在填充装置
301
的相对侧
(
即,在图
15
和图
16
中的下侧
)
闭合成型腔室
352
的侧向部分
353。
中间成型元件还可以在侧向部分
353
中运动以压实可模制材料
。
[0199]
在操作期间,为了填充模具
351
,作用在中间主体
367
上的运动器件使中间主体位移到图
15
所示的向前位置,在该向前位置中,前密封表面
374
抵靠内成型元件
354
接触,特别是抵靠横向表面
363
接触
。
同时,作用在闭合构件
366
上的驱动元件将闭合构件位移到闭合位置,在该闭合位置中,端部
369
与中间主体
367
的内密封表面
368
接合
。
在闭合位置中,端部
369
还与内成型元件
354
的横向表面
363
接触
。
由此,中心管道
365
被闭合
。
[0200]
由于在向前位置中,中间主体
367
的外密封表面
372
与容纳主体
364
脱离,因此周边管道
370
是打开的
。
可模制材料和空气的流
h2
被输送到周边管道
370
中,并且从周边管道进入成型腔室
352
的侧向部分
353
中
。
由此,侧向部分
353
被填充
。
存在与侧向部分
353
相关联的多个通气孔
(
未示出
)
,这些通气孔例如在壳体
357
中制成,最初与可模制材料混合的过量空气可以通过这些通气孔从成型腔室
352
流出,特别是从环形部分
353
流出,如由箭头k所指示的
。
[0201]
应当注意,当中间主体
367
处于向前位置并且闭合构件
366
处于闭合位置时,也就是说,当发生图
15
所示的状况时,成型腔室
352
的横向部分
356
尚未限定,也就是说,横向部分的体积实际上为零
。
实际上,闭合构件
366
和中间主体
367
都与内成型元件
354
的横向表面
363
接触,并且可模制材料无法到达横向表面
363。
[0202]
还应当注意,在图
15
所示的中间主体
364
的向前位置,向外扩展的外密封表面
372
用作斜坡,以促进可模制材料从周边管道
370
朝向成型腔室
352
的侧向部分
353
流动
。
如在所
示的示例中,如果周边管道
370
的平均直径小于环形部分
353
的平均直径,则这是特别有用的
。
[0203]
挡板
371
的最大外径可以基本上等于挡板
371
在向前位置处与之接触的横向表面
363
的直径
。
这防止了可能阻碍可模制材料在挡板
371
与内成型元件
354
之间流动的台阶的存在
。
[0204]
此外,邻接表面
373
的几何形状
(
其可以成形为类似于斜面
)
使得可以避免尖锐边缘,该尖锐边缘可能使可模制材料不太容易从周边管道
370
进入侧向部分
353。
[0205]
中间主体
364
和闭合构件
366
保持在图
15
所示的位置,直到成型腔室
352
的侧向部分
353
已经被填充
。
此时,其上制成有挡板
371
的中间主体
364
向后运动,也就是说,沿着轴线
z2
远离内成型元件
354
运动,直到其到达图
16
所示的后部位置
。
由此,外密封表面
372
与容纳主体
364
的邻接表面
373
接触,从而闭合周边管道
370
,该周边管道不再与成型腔室
352
连通
。
[0206]
此外,闭合构件
366
向后运动,也就是说,平行于轴线
z2
远离内成型元件
354
运动
。
闭合构件
366
向后运动的量大于中间主体
364
向后运动的量,由此使得闭合构件与内密封表面
368
脱离并且运动到打开位置
。
因此,中心管道
365
打开,中心管道
365
通向成型腔室
352
的横向部分
356
的中心区域
。
[0207]
横向部分
356
与已经基本上被填充的侧向部分
353
连通
。
[0208]
当中间主体
367
运动到后部位置中时,除了闭合周边管道
370
之外,还限定了成型腔室
352
的横向部分
356。
发生这种情况是因为,当挡板
371
和闭合构件
366
远离内成型元件
354
运动时,在与横向表面
363
相邻的位置中产生空的空间,该空间对应于成型腔室
352
的横向部分
356。
[0209]
可模制材料和空气的流
h1
现在被供给到中心管道
365
中,并且从中心管道进入成型腔室
352
的横向部分
356
中
。
由此,成型腔室
352
的横向部分
356
也被填充
。
横向部分
356
具有例如在壳体
357
中制成的一个或多个通气孔
(
未示出
)。
通过通气孔,最初与可模制材料混合的过量空气可以从成型腔室
352
排出,如由箭头j所指示的
。
[0210]
现在通过使闭合构件
366
朝向内成型元件
354
运动而使闭合构件进入闭合位置,同时中间主体
364
保持在后部位置
。
在该构造中,挡板
371
的前密封表面
374
和闭合构件
366
的前表面
375
限定横向部分
356
的与内成型元件
354
的横向表面
363
相对的表面
。
当闭合构件
366
位于闭合位置并且中间主体
364
位于后部位置时,前密封表面
374
和前表面
375
可以可选地位于同一平面中
。
[0211]
现在可以使内成型元件
354
和壳体
357
相对彼此运动,以减小成型腔室
352
的体积并获得期望的物体
。
[0212]
图
17
至图
20
示出了与图
15
和图
16
中所示的模具
351
具有许多相似性的模具
451。
模具
451
的与模具
351
的类似部分共同的部分将用第一个数字是“4”而不是“3”并且最后两个数字与用于图
15
和图
16
中的相同模具部分的最后两个数字一致的附图标记来指示,不再进行详细描述
。
应当理解,除非另有明确说明,否则先前参考图
15
和图
16
描述的内容也适用于图
17
至图
20。
[0213]
模具
451
包括沿着轴线
z2
彼此对准的第一模具部分
421
和第二模具部分
422。
如图
17
所示,第一模具部分
421
包括内成型元件
(
或凸形成型元件
)454、
壳体
457
和中间成型元件
460
,中间成型元件介于内成型元件
454
与壳体
457
之间,用于形成物体的边缘区域
。
中间成
型元件
460
可以是环形成型元件,例如布置成用于形成物体的环形边缘区域
。
[0214]
第二模具部分
422
包括填充装置
401
,在所示的示例中,填充装置容纳在容纳构件
423
中,该容纳构件具有在横向于轴线
z2
的方向上由止动表面
425
界定的肩部
424。
该止动表面旨在抵靠第一模具部分
421
的邻接端部
426
接触,邻接端部
426
例如在壳体
457
上制成
。
[0215]
容纳构件
423
包括从止动表面
425
朝向第一模具部分
421
突出的突出部分
427。
突出部分
427
可以适于借助于形状联接与壳体
457
接合
。
为此目的,突出部分
427
的外径可以等于壳体
457
的内径
。
[0216]
容纳主体
464
和中间主体
467
定位在容纳构件
423
的内部,挡板
471
在中间主体
467
上制成
。
闭合构件
466、
容纳主体
464
和中间主体
467
被包括在填充装置
401
中,填充装置可相对于容纳构件
423
在平行于轴线
z2
的方向上前后线性运动,以穿入壳体
457
的内部或者可替代地从壳体
457
抽出
。
[0217]
在操作期间,模具
451
最初处于图
17
所示的间隔开构造,在该间隔开构造中,第一模具部分
421
和第二模具部分
422
彼此分离,使得可以从模具移除刚刚成型的物体
。
在间隔开构造中,止动表面
425
远离邻接端部
424。
[0218]
随后,第一模具部分
421
和第二模具部分
422
相互朝向彼此运动,直到它们达到图
18
所示的闭合模具构造,在闭合模具构造中,容纳构件
423
的止动表面
424
紧邻壳体
457
的邻接端部
425。
突出部分
427
现在被接收在壳体
457
内
。
[0219]
在所示的示例中,通过使第二模具部分
422
朝向第一模具部分
421
运动来达到闭合模具构造,第一模具部分沿着轴线
z2
保持固定,但是这种情况不是必需的
。
[0220]
填充装置
401
现在朝向内成型元件
454
移位
。
由此,填充装置
401
从容纳构件
423
出来
。
更具体地,如图
18
所示,闭合构件
466
和制造在中间主体
467
上的挡板
471
与内成型元件
454
的横向表面
463
接触
。
闭合构件
466
处于闭合位置,在该闭合位置,中心管道
465
与成型腔室
452
隔离
。
[0221]
容纳主体
464
尽管相对于中间主体
467
保持在后部位置,但也从容纳构件
423
的突出部分
427
突出,以朝向内成型元件
454
运动
。
[0222]
更详细地,容纳主体
464
被定位成使得邻接表面
473
与挡板
471
间隔开
。
由此,周边管道
470
打开,并且可模制材料和空气的流
h2
可以进入成型腔室
452。
[0223]
与参照图
15
和图
16
描述的其中周边管道
470
配置成仅将可模制材料供给到成型腔室的位于填充装置下方的管状部分中的实施例中发生的情况不同,在图
17
至图
20
的实施例中,周边管道
470
允许根据不同的布置将可模制材料供给到成型腔室
452
中
。
[0224]
更具体地,如图
18
所示,当挡板
471
与内成型元件
454
接触时,成型腔室
452
除了具有围绕内成型元件
454
的侧向部分
453
之外,还具有围绕填充装置
401
的管状附件
(tubular appendage)428。
管状附件
428
介于壳体
457
与容纳主体
464
之间
。
管状附件
428
和侧向部分
453
定位在周边管道
470
通向成型腔室
452
的区的两个相对侧上
。
[0225]
侧向部分
453
可以是管状的
。
[0226]
当可模制材料的流
h2
到达成型腔室
452
时,该流被分成两个二次流,即上升流
h21
和下降流
h22。
在所示的示例中,上升流
h21
向上流入管状附件
428
,而下降流
h22
向下流入成型腔室
452
的侧向部分
453。
[0227]
周边管道
470
在沿着轴线
z1
大致居中定位的区中
(
也就是说,在沿着成型腔室
452
的高度的大致中心区中
)
通向成型腔室
452。
与通过使可模制材料从成型腔室的一端轴向流动到另一端来填充成型腔室的情况相比,这允许更快地填充成型腔室
452。
如果成型腔室
452
具有相当大的高度,也就是说,沿着轴线
z2
具有相当大的尺寸,则这是特别明显的
。
[0228]
可模制材料继续沿着周边管道
470
流动,直到成型腔室
452
的侧向部分
453
和附件
428
都已经被填充
。
在填充期间,与可模制材料混合的过量空气可以通过合适的通气通道从成型腔室流出
。
通气通道可以例如被限定在中间成型元件
460
与壳体
457
之间的接合部中,用于使空气从成型腔室
452
的侧向部分
453
流出,如由箭头
a1
所指示的
。
可以在止动表面
425
与邻接端部
426
之间限定另一通气通道,使得空气可以从成型腔室
452
的管状附件
428
流出,如图
18
中的箭头
a2
所示
。
[0229]
当侧向部分
453
和管状附件
428
已经填充有可模制材料时,挡板
470
切换到后部位置,使挡板与容纳主体
464
接触,以闭合周边管道
470。
整个填充装置
401
远离内成型元件
454
运动
。
如图
19
所示,填充装置
401
特别地定位成使得挡板
471
的前密封表面
474
与容纳主体
464
的端部和突出部分
427
的另一端部共面,上述端部和另一端部面向内成型元件
454。
[0230]
这允许改变成型腔室
452
的形状,从而显著增加成型腔室的体积
。
特别地,限定成型腔室
452
的横向部分
456
,横向部分
456
在填充装置
401
与内成型元件
454
的横向表面
463
之间延伸
。
横向部分
456
占据管状附件
428
内部限定的整个空间,可选地占据管状附件
428
的整个高度
。
因此,管状附件
428
在成型腔室
452
中不再是可区分的
。
[0231]
通过使闭合构件
466
平行于轴线
z2
远离内成型元件
454
运动,使闭合构件进入图
19
所示的打开位置
。
由此,闭合构件
466
远离中间主体
467
运动,特别是远离挡板
471
运动,并且中心管道
465
与成型腔
452
连通,如图
19
所示
。
因此,进入中心管道
465
的可模制材料和空气的流
(
如由箭头
h1
所指示的
)
可以填充成型腔室
452。
[0232]
在该步骤中,与可模制材料混合的过量空气也可以通过合适的通气通道流出,如图
19
中由箭头
a1
和
a2
指示的并如先前参考图
18
描述的
。
[0233]
在先前描述的步骤结束时,成型腔室
452
的侧向部分
453
和横向部分
456
两者都已经填充有可模制材料
。
此时,闭合构件
466
进入闭合位置,以闭合中心管道
465。
[0234]
如图
20
所示,第一模具部分
421
和第二模具部分
422
朝向彼此运动以减小成型腔室
452
的体积,以压缩可模制材料并获得期望的物体
。
更具体地,包含在横向部分
456
中的可模制材料被压缩以形成物体的横向壁
429
,同时包含在环形部分
453
中的可模制材料被压缩以形成物体的侧向壁
430。
[0235]
在所示的示例中,通过使第二模具部分
422
在平行于轴线
z2
的模制方向上朝向第一模具部分
421
运动来压缩可模制材料
。
更具体地,第二模具部分
422
向下运动,如图
20
所示
。
[0236]
闭合元件
466
的前表面
475、
挡板
471
的前密封表面
474、
容纳主体
464
的端部和突出部分
427
的另一端部对准,例如它们位于公共平面中,以限定物体的横向壁
429
的外表面
。
[0237]
在所示的示例中,壳体
457
和内成型元件
454
也平行于轴线
z2
运动以压缩可模制材料
。
特别地,壳体
457
和内成型元件
454
在与第二模具部分
422
的运动相同的方向上运动,也就是说,在图
20
中向下运动
。
[0238]
也就是说,壳体
457
和内成型元件
454
朝向中间成型元件
460
运动,中间成型元件沿着轴线
z2
保持在固定位置
。
[0239]
换句话说,如图
20
所示,界定中间成型元件
460
的环形成型表面
431
的位置沿着轴线
z2
保持固定
。
通过使内成型元件
454
的横向表面
463
和第二模具部分
422
朝向环形成型表面
431
运动来形成物体
。
由此,可模制材料既在形成物体的侧向壁
430
的侧向部分
453
中被压缩,也在形成物体的横向壁
429
的横向部分
456
中被压缩
。
[0240]
当可模制材料被压缩时,包含在可模制材料中的空气继续通过先前描述的通气通道从模具
451
排出,如由箭头
a1
和
a2
所指示的
。
[0241]
由此,在具有相对简单的几何形状的模具中形成具有均匀压实度的物体,该模具的部件仅以轴向运动的方式被驱动
。
也就是说,避免了会使模具的设计和操作更复杂的径向运动
。
在到目前为止描述的所有实施例中,通气孔或开口或通道可以与抽吸器件相关联,以促进可模制材料的流动
。
[0242]
尽管到目前为止先前描述的所有实施例仅参考干燥形式的可模制材料,例如呈粉末
、
颗粒或薄片形式的可模制材料,但是也可以用呈浆料形式的可模制材料
(
特别是其中存在液体的可模制材料,例如粘合剂或水
)
操作
。
同样,在这种情况下,可以将空气和可模制材料的流供给到模具中,也就是说,使用空气来运送可模制材料
。
[0243]
在先前参考图1至图
20
描述的所有实施例中,所形成的物体,除了如在容器
、
用于容器的盖或预成型件的情况那样具有凹形形状,还可以具有在两端敞开的基本上管状形状,也就是说,所形成的物体可以具有在模制期间围绕模具的轴线延伸的侧向壁,同时可以不存在横向于轴线定位的横向壁
。
侧向壁可以围绕轴线延伸
360
°
,也就是说,具有围绕轴线闭合的管状形状,或者可以围绕轴线延伸小于
360
°
。
在后一种情况下,侧向壁可以例如具有“c”形或“u”形的截面
。
[0244]
侧向壁的截面可以具有所需的任何形状
。
特别地,侧向壁的截面可以具有不一定类似于环形的形状,也可以具有椭圆形
、
棱柱形
、
卵形或其他形状
。
[0245]
总而言之,在本发明的第三方面中,提供了一种用于利用可模制材料成型物体的模具,该模具包括壳体
(57
;
157
;
257)、
至少部分地容纳在壳体
(57
;
157
;
257)
中的内成型元件
(54)、
围绕内成型元件
(54)
的中间元件
(60)
,其中,在内成型元件
(54)
与壳体
(57
;
157
;
257)
之间可以限定中空空间
(53)
,中间元件
(60)
能够在后部位置
(p1)
定位在中空空间
(53)
中,在后部位置,可模制材料接收在中空空间
(53)
中,中间元件
(60)
能够相对于内成型元件
(54)
从后部位置
(p1)
朝向成型位置
(p2)
滑动,以减小中空空间
(53)
的体积并且成型物体的侧向壁
(65)。
[0246]
在一个实施例中,壳体
(57
;
157
;
257)
被包括在凹形成型元件
(58
;
158
;
258)
中,凹形成型元件
(58
;
158
;
258)
和内成型元件
(54)
能够沿着模制轴线
(z1)
相对彼此运动,以压缩可模制材料并且形成物体
。
[0247]
在一个实施例中,凹形成型元件
(58)
包括横向成型表面
(61)
,该横向成型表面横向于模制轴线
(z1)
延伸以成形物体的横向壁
(64)
,壳体
(57)
从横向成型表面
(61)
突出并且相对于横向成型表面
(61)
固定
。
[0248]
在一个实施例中,凹形成型元件
(158)
包括由横向成型表面
(161)
界定的内芯
(68)
,该横向成型表面横向于模制轴线
(z1)
延伸以成形物体的横向壁
(64)
,凹形成型元件
(158)
还包括介于内芯
(68)
与壳体
(157)
之间的推动器部件
(67)
,推动器部件
(67)
能够移位到从横向成型表面
(161)
突出的位置,用于将可模制材料推入中空空间
(53)
中
。
[0249]
在一个实施例中,推动器部件
(67)
能够通过配置成使推动器部件
(67)
运动的移位装置移位到突出位置,由此使得推动器部件
(67)
跟随中间元件
(60)。
[0250]
在一个实施例中,凹形成型元件
(258)
包括由横向成型表面
(261)
界定的内芯
(268)
,该横向成型表面横向于模制轴线
(z1)
延伸以成形物体的横向壁
(64)
,内芯
(268)
能够在壳体
(257)
内部在平行于模制轴线
(z1)
的方向上移位,以在中间元件
(60)
到达成型位置
(p2)
之前接近内成型元件
(54)
并且将可模制材料推入中空空间
(53)
中
。
[0251]
在一个实施例中,模具还包括能够连接到中空空间
(53)
的抽吸源,用于将可模制材料抽吸到中空空间
(53)
中
。
[0252]
在一个实施例中,中空空间
(53)
的形状类似于环形空间,并且中间元件
(60)
是管状元件
。
[0253]
在本发明的第四方面中,提供了一种用可模制材料成型物体的方法,该方法包括以下步骤:
[0254]-将可模制材料引入壳体
(57
;
157
;
257)
中,内成型元件
(54)
至少部分地容纳在壳体
(57
;
157
;
257)
中,内成型元件
(54)
由中
[0255]
间元件
(60)
围绕;
[0256]-使中间元件
(60)
相对于内成型元件
(54)
向后运动,从而使可模制材料流入限定在内成型元件
(54)
与壳体
(57
;
157
;
257)
之
[0257]
间的中空空间
(53)
中;
[0258]-使中间元件
(60)
相对于内成型元件
(54)
向前运动,以减小中空空间
(53)
的体积并且成型物体的侧向壁
(65)。
[0259]
在一个实施例中,使中间元件
(60)
向后运动的步骤包括在中空空间
(53)
中产生负压,该负压将可模制材料吸引到中空空间
(53)
中
。
[0260]
在一个实施例中,壳体
(57
;
157
;
257)
包括在凹形成型元件
(58
;
158
;
258)
中,并且此外,内成型元件
(54)
和凹形成型元件
(58
;
158
;
258)
沿着模制轴线
(z1)
朝向彼此运动,以压缩可模制材料并且形成物体的横向壁
(64)
,横向壁
(64)
横向于模制轴线
(z1)
延伸
。
[0261]
在一个实施例中,该方法还包括施加机械推力以使可模制材料流入中空空间
(53)
的步骤
。
[0262]
在一个实施例中,通过在中间元件
(60)
向后运动的同时使包括在凹形成型元件
(158)
中的推动器部件
(67)
朝向中空空间
(53)
运动来施加机械推力,推动器部件
(67)
介于壳体
(157)
与凹形成型元件
(158)
的内芯
(68)
之间
。
[0263]
在一个实施例中,通过在中间元件
(60)
向后运动的同时使包括在凹形成型元件
(258)
中的内芯
(268)
朝向内成型元件
(54)
运动来施加机械推力,内芯
(268)
由壳体
(257)
围绕
。
[0264]
在一个实施例中,该方法还包括在中间元件
(60)
向后运动的同时借助于抽吸源将可模制材料抽吸到中空空间
(53)
中的步骤
。
[0265]
在本发明的第五方面中,提供了一种用于利用可模制材料成型物体的模具,该模具包括具有至少部分地围绕轴线
(z2)
的侧向部分
(353
;
453)
的成型腔室
(352
;
452)
,模具
(351
;
451)
还包括具有周边管道
(370
;
470)
的填充装置
(301
;
401)
,该周边管道能够选择性地打开以将可模制材料供给到侧向部分
(353
;
453)
中
。
[0266]
在一个实施例中,成型腔室
(352
;
452)
进一步具有横向部分
(356
;
456)
,该横向部分横向于轴线
(z2)
闭合侧向部分
(353
;
453)
,填充装置
(301
;
401)
包括中心管道
(365
;
465)
,该中心管道能够选择性地打开以将可模制材料供给到横向部分
(356
;
456)
中
。
[0267]
在一个实施例中,中心管道
(365
;
465)
沿着轴线
(z2)
延伸,并且周边管道
(370
;
470)
至少部分地围绕中心管道
(365
;
465)
,周边管道
(370
;
470)
可选地具有环形形状
。
[0268]
在一个实施例中,模具还包括内成型元件
(354
;
454)
,该内成型元件由横向于轴线
(z2)
延伸的横向表面
(363
;
463)
界定,侧向部分
(353
;
453)
围绕内成型元件
(354
;
454)
,并且其中,填充装置
(401
;
501)
面向该横向表面
(363
;
463)。
[0269]
在一个实施例中,内成型元件
(354
;
454)
定位在填充装置
(301
;
401)
的下方
。
[0270]
在一个实施例中,填充装置
(401
;
501)
包括闭合构件
(366
;
466)
,该闭合构件能够在中心管道
(365
;
465)
的内部运动以打开或可替代地闭合中心管道
(365
;
465)
,填充装置
(401
;
501)
还包括挡板
(370
;
470)
,该挡板能够相对于周边管道
(371
;
471)
运动以打开或可替代地闭合周边管道
(371
;
471)。
[0271]
在一个实施例中,闭合构件
(366
;
466)
和挡板
(370
;
470)
能够定位成与内成型元件
(354
;
454)
的横向表面
(356
;
456)
接触,以将可模制材料引入侧向部分
(353
;
453)
中,闭合构件
(366
;
466)
和挡板
(370
;
470)
能进一步远离内成型元件
(354
;
454)
运动,以在内成型元件
(354
;
454)
与填充装置
(301
;
401)
之间限定成型腔室
(352
;
452)
的横向部分
(356
;
456)。
[0272]
在一个实施例中,填充装置
(301
;
401)
包括中间主体
(367
;
467)
,中心管道
(365
;
465)
形成在中间主体的内部,填充装置
(301
;
401)
还包括围绕中间主体
(367
;
467)
的容纳主体
(364
;
464)
,挡板
(370
;
470)
形成在中间主体
(367
;
467)
的端部部分中
。
[0273]
在一个实施例中,中间主体
(367
;
467)
的端部部分由内密封表面
(368)
界定,该内密封表面指向轴线
(z2)
并且能够与闭合构件
(366
;
466)
接合以闭合中心管道
(365
;
465)
,中间主体
(367
;
467)
的端部部分进一步由外密封表面
(372)
界定,该外密封表面能够与界定容纳主体
(364
;
464)
的邻接表面
(373)
接合,以闭合周边管道
(371
;
471)。
[0274]
在一个实施例中,中间主体
(367
;
467)
的端部部分进一步由前表面
(374)
界定,该前表面旨在在侧向部分
(352
;
452)
被填充时紧邻内成型元件
(354
;
454)
的横向表面
(363
;
463)。
[0275]
在一个实施例中,内密封表面
(368)
朝向轴线
(z2)
会聚,以将可模制材料从中心管道
(365
;
465)
朝向横向部分
(363
;
463)
的中心区运送,外密封表面
(369)
从轴线
(z2)
发散,以将可模制材料从周边管道
(370
;
470)
朝向侧向部分
(353
;
453)
输送
。
[0276]
在一个实施例中,成型腔室
(352
;
452)
还包括管状附件
(428)
,该管状附件围绕填充装置
(301
;
401)
并且与侧向部分
(363
;
463)
相邻
。
[0277]
在本发明的第六方面中,提供了一种用于利用可模制材料在成型腔室
(352
;
452)
中成型物体的方法,该成型腔室具有至少部分地围绕轴线
(z2)
的侧向部分
(353
;
453)
,该方法包括通过周边管道
(370
;
470)
将可模制材料供给到侧向部分
(353
;
453)
中的步骤
。
[0278]
在一个实施例中,成型腔室
(352
;
452)
具有横向部分
(356
;
456)
,该横向部分横向于轴线
(z2)
闭合侧向部分
(353
;
453)
,该方法还包括通过中心管道
(365
;
465)
将可模制材料供给到横向部分
(356
;
456)
中的步骤
。
[0279]
在一个实施例中,将可模制材料进给到横向部分
(356
;
456)
中的步骤发生在将可
模制材料进给到侧向部分
(353
;
453)
中的步骤之后
。
[0280]
在一个实施例中,侧向部分
(353
;
453)
围绕包括在模具
(351
;
451)
中的内成型元件
(354
;
454)
定位
。
[0281]
在一个实施例中,中心管道
(365
;
465)
能够由闭合构件
(366
;
466)
打开或闭合,并且周边管道
(370
;
470)
能够由挡板
(371
;
471)
打开或闭合
。
[0282]
在一个实施例中,当闭合构件
(366
;
466)
和挡板
(371
;
471)
与内成型元件
(354
;
454)
接触时,可模制材料被进给到侧向部分
(353
;
453)
中,然后内成型元件
(354
;
454)
和包括闭合构件
(366
;
466)
和挡板
(371
;
471)
的组件远离彼此运动,以在内成型元件
(354
;
454)
与包括闭合件
(366
;
466)
和挡板
(371
;
471)
的组件之间限定横向部分
(356
;
456)。
[0283]
在一个实施例中,该方法还包括压缩成型腔室
(352
;
452)
中的可模制材料以形成物体的步骤,压缩步骤包括减小侧向部分
(353
;
453)
沿着轴线
(z2)
的纵向尺寸的步骤和减小横向部分
(356
;
456)
沿着轴线
(z2)
的厚度的步骤
。
[0284]
在一个实施例中,减小横向部分
(356
;
456)
的厚度的步骤包括使内成型元件
(354
;
454)
和包括闭合构件
(366
;
466)
和挡板
(371
;
471)
的模具部分
(422)
中的一个朝向另一个运动,减小侧向部分
(353
;
453)
的纵向尺寸的步骤包括使内成型元件
(354
;
454)
和围绕内成型元件
(354
;
454)
的中间成型元件
(460)
中的一个朝向另一个运动,以成形物体的边缘区域
。
[0285]
在一个实施例中,当在周边管道
(370
;
470)
中流动的可模制材料和空气的流
(h2)
到达成型腔室
(352
;
452)
中时,该流
(h2)
被分成两个二次流
(h22、h21)
,这两个二次流在相反方向上流动以分别填充侧向部分
(353
;
453)
和与侧向部分
(353
;
453)
相邻的管状附件
(428)
;
453)
,管状附件
(428)
相对于内成型元件
(354
;
454)
与侧向部分
(353
;
453)
相反
。