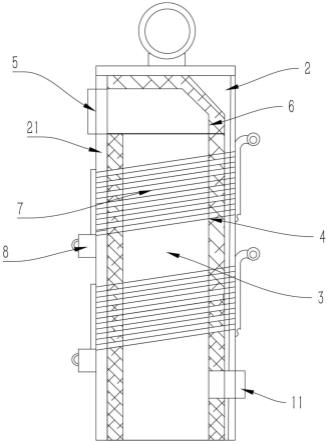
1.本发明涉及余热利用设备技术领域,具体涉及一种以全氟己酮作为导热介质的余热回收利用发电设备。
背景技术:2.余热回收利用技术是发电领域重要的组成部分,主要利用相关企业(包括但不限于冶炼、加工生产、电力)的余热烟气,由余热锅炉汇集主蒸汽进入发电机组进行发电,从而充分利用余热,提高发电的效率,极大的降低企业的成本;其中整个烟气余热的发电过程中,余热锅炉与发电机组的特性直接决定余热的利用率与发电效率,是影响余热回收利用的核心设备,目前余热锅炉是主要利用烟气对其受热面进行冲刷换热,再利用换热过得烟气去加热对应的水,使水受热产生饱和蒸汽,最后通过将饱和蒸汽输送到发电机组位置给发电电机发电,主要涉及到的换热介质是水,而整个余热的利用率和水的热交换效率息息相关。
3.相比于水而言,热交换高的换热介质有很多,通过替代热交换高的换热介质也能够有效的提高换热效率,但是在余热回收利用技术的具体过程中,除了考虑换热介质的换热效率之外,还需要考虑换热介质是否环保,输送过程中性质是否保持稳定,在现有的余热面加热下是否能够生成饱和蒸汽以及还需要判断生产的保护蒸汽是否会腐蚀管道,同时现有的余热回收利用发电设备还存在安全性能差,没有对应的安全保护措施,产生的污染废水也没有对应的处理装置,造成环境的污染,部分余热回收利用发电设备在使用过程中还存在密封性不好,容易泄漏的技术问题,所以亟需一种以全氟己酮作为导热介质的余热回收利用发电设备,在能够提高加热效率的同时,仍然能够稳定、环保和安全保证余热回收利用发电设备的正常使用。
技术实现要素:4.本发明提供一种以全氟己酮作为导热介质的余热回收利用发电设备,以解决上述现有技术存在的热交换效率低、汽化温度高、安全性差、没有环保处理设备、管道容易泄漏和发电过程中能耗高的技术问题。
5.本发明的一种以全氟己酮作为导热介质的余热回收利用发电设备采用如下技术方案:
6.一种以全氟己酮作为导热介质的余热回收利用发电设备,包括余热锅炉、汽轮发电机组和电控设备,余热锅炉的内部设置有竖向延伸的锅筒和两个在竖直方向堆叠设置的蒸发器,锅筒通过设置在余热锅炉侧壁上的锅炉进烟口与位于余热锅炉一侧的焙烧炉连通,蒸发器上设置有缠绕锅筒的流蒸发受热面,余热锅炉内分别设置有缠绕在对应蒸汽器中流蒸发受热面上的下降管道,下降管道的底部设置有主蒸汽管座,通过主蒸汽管座与汽轮发电机组连通,下降管道内部流通有液态全氟己酮,方便液态全氟己酮经过流蒸发受热面加热为全氟己酮蒸汽,最终进入到汽轮发电机组内部,锅炉进烟口垂直于锅筒设置,流蒸
发受热面覆盖锅筒的顶部和侧边。
7.进一步的,下降管道和主蒸汽管座之间设置有气液分离装置,方便全氟己酮蒸汽和全氟己酮液体的分离,保证进入主蒸汽管座的全氟己酮均为蒸汽形态。
8.进一步的,气液分离装置采用封隙档板和波纹板分离器结构,保证饱和蒸汽品质,防止饱和蒸汽携带全氟己酮液体。
9.进一步的,焙烧炉和锅炉进烟口之间设置有进口烟道,进口烟道分别与焙烧炉和锅炉进烟口的内部连通,余热锅炉的底部设置有开设在余热锅炉上的锅炉出烟口,锅炉出烟口通过其连接的出口烟道与设置在焙烧炉上的烟气处理装置连接。
10.进一步的,进口烟道与锅炉进烟口连接处以及出口烟道和锅炉进烟口之间设置有非金属膨胀节,在抵消金属的膨胀吸收的同时起到密封作用。
11.进一步的,主蒸汽管座的外端设置有出口蒸汽管道和分汽缸,出口蒸汽管道和汽轮机组之间设置有连接法兰和控制阀门,连接法兰的位置设置有起到密封作用的石墨垫片。
12.进一步的,出口蒸汽管道采用长线管道,出口蒸汽管道设置有管道膨胀节,出口蒸汽管道的拐角处设置有吸收三维膨胀的立体弯管。
13.进一步的,两组蒸发器的水平位置相互对应,上方的蒸发器与下方的连通设置,方便余热烟气从向下一次通过两组,两个蒸发器的内部设置有对流管束,对流管束均采用φ42
×
3.5的光管,管子材质20(gb/t3087-2008),对流管束管子顺列布置,横向节距120mm,纵向节距150mm,烟气横向冲刷受热面,烟气进口温度为590℃,出口温度360℃,受热面面积为119
㎡
。
14.进一步的,余热锅炉的内部设置有围绕流蒸发受热面分布的耐火保温部,耐火保温部的内侧采用耐火砖,耐火保温部的外侧采用轻型高效硅酸铝棉,保温效果好。
15.通过对锅炉余热回收系统的改造,能够保证余热烟气对余热锅炉内的流蒸发受热面进行冲刷换热,加热下降管道中的全氟己酮,余热锅炉设置两个蒸发器,进一步方便余热烟气依次通过蒸发器,最终排出炉外,全氟己酮进入到缠绕锅筒的下降管道中,进入锅筒的全氟己酮通过流蒸发受热面加热,使全氟己酮49℃以及以上温度时沸腾蒸发汽化,提高了余热热源的利用率,最终通过主蒸汽管座引出送至发电机组。
16.本发明的有益效果是:
17.1、本发明采用全氟己酮作为导热介质,全氟己酮的化学名称为全氟乙基异丙基酮,常温下为清澈、无色、无味的液体,沸点为49℃远低于水的沸点100℃,蒸发潜热为水的1/25,极易汽化,提高了余热热源的利用率,即实现了高效率热交,能够增大高质量饱和蒸汽量,从而实现提高发电机组发电量的目的,整个导热介质使用过程中,不仅热交效率高,而且没有污染,整个输送过程中通过非金属膨胀节、管道膨胀节和立体弯管方便对应的管道膨胀,增加使用寿命,通过连接法兰和石墨垫片防止泄漏。
18.2、本发明通过对锅炉余热回收系统的改造,能够保证余热烟气对余热锅炉内的流蒸发受热面进行冲刷换热,加热下降管道中的全氟己酮,余热锅炉设置两个蒸发器,进一步方便余热烟气依次通过蒸发器,最终排出炉外,全氟己酮进入到缠绕锅筒的下降管道中,进入锅筒的全氟己酮通过流蒸发受热面加热,使全氟己酮49℃以及以上温度时沸腾蒸发汽化,提高了余热热源的利用率,最终通过主蒸汽管座引出送至发电机组。
附图说明
19.图1为本发明的一种以全氟己酮作为导热介质的余热回收利用发电设备的结构示意图;
20.图2为本发明的一种以全氟己酮作为导热介质的余热回收利用发电设备中进口烟道和余热锅炉的连接示意图;
21.图3为为本发明的一种以全氟己酮作为导热介质的余热回收利用发电设备中出口蒸汽管道和连接法兰的连接示意图。
22.图中:1、焙烧炉;2、余热锅炉;3、锅筒;4、蒸发器;5、锅炉进烟口;6、流蒸发受热面;7、下降管道;8、主蒸汽管座;10、进口烟道;11、锅炉出烟口;12、出口烟道;13、烟气处理装置;14、非金属膨胀节;15、出口蒸汽管道;16、分汽缸;17、连接法兰;18、石墨垫片;19、管道膨胀节;20、立体弯管;21、耐火保温部。
具体实施方式
23.下面将结合本发明实施例中的附图,对本发明实施例中的技术方案进行清楚、完整地描述,显然,所描述的实施例仅仅是本发明一部分实施例,而不是全部的实施例。
24.实施例1:
25.如图1至图3所示,一种以全氟己酮作为导热介质的余热回收利用发电设备,包括余热锅炉2、汽轮发电机组和电控设备,余热锅炉2的内部设置有竖向延伸的锅筒3和两个在竖直方向堆叠设置的蒸发器4,锅筒3通过设置在余热锅炉2侧壁上的锅炉进烟口5与位于余热锅炉2一侧的焙烧炉1连通,蒸发器4上设置有缠绕锅筒3的流蒸发受热面6,余热锅炉2内分别设置有缠绕在对应蒸汽器中流蒸发受热面6上的下降管道7,下降管道7的底部设置有主蒸汽管座8,通过主蒸汽管座8与汽轮发电机组连通,下降管道7内部流通有液态全氟己酮,方便液态全氟己酮经过流蒸发受热面6加热为全氟己酮蒸汽,最终进入到汽轮发电机组内部,锅炉进烟口5垂直于锅筒3设置,流蒸发受热面6覆盖锅筒3的顶部和侧边。
26.两组蒸发器4的水平位置相互对应,上方的蒸发器4与下方的连通设置,方便余热烟气从向下一次通过两组,两个蒸发器4的内部设置有对流管束,对流管束均采用φ42
×
3.5的光管,管子材质20(gb/t3087-2008),对流管束管子顺列布置,横向节距120mm,纵向节距150mm,烟气横向冲刷受热面,烟气进口温度为590℃,出口温度360℃,受热面面积为119
㎡
。余热锅炉2的内部设置有围绕流蒸发受热面6分布的耐火保温部21,耐火保温部21的内侧采用耐火砖,耐火保温部21的外侧采用轻型高效硅酸铝棉,保温效果好。
27.下降管道7和主蒸汽管座8之间设置有气液分离装置,方便全氟己酮蒸汽和全氟己酮液体的分离,保证进入主蒸汽管座8的全氟己酮均为蒸汽形态。气液分离装置采用封隙档板和波纹板分离器结构,保证饱和蒸汽品质,防止饱和蒸汽携带全氟己酮液体。
28.焙烧炉1和锅炉进烟口5之间设置有进口烟道10,进口烟道10分别与焙烧炉1和锅炉进烟口5的内部连通,余热锅炉2的底部设置有开设在余热锅炉2上的锅炉出烟口11,锅炉出烟口11通过其连接的出口烟道12与设置在焙烧炉1上的烟气处理装置13连接。进口烟道10与锅炉进烟口5连接处以及出口烟道12和锅炉进烟口5之间设置有非金属膨胀节14,在抵消金属的膨胀吸收的同时起到密封作用。
29.主蒸汽管座8的外端设置有出口蒸汽管道15和分汽缸16,出口蒸汽管道15和汽轮
机组之间设置有连接法兰17和控制阀门,连接法兰17的位置设置有起到密封作用的石墨垫片18。出口蒸汽管道15采用长线管道,出口蒸汽管道15设置有管道膨胀节19,出口蒸汽管道15的拐角处设置有吸收三维膨胀的立体弯管20。
30.本发明在使用过程中,焙烧炉1产生余热烟气通过进口烟道10进入到余热锅炉2内部,冲刷流蒸发受热面6,对流蒸发受热面6进行加热,然后沿着锅筒3竖直向下,然后从锅炉出烟口11排出,进入对应的焙烧炉1上的烟气处理装置13进行处理,焙烧炉1以及对应的烟气处理装置13均采用现有技术,全氟己酮沿着下降管道7通过两个蒸发器4,经过流蒸发受热面6加热沸腾汽化,并且在气液分离装置的坐下取出液态全氟己酮,饱和蒸汽态的主蒸汽管座8引出送至发电机组,进行对应的发电,本发明涉及到的汽轮发电机组和电控设备均采用现有技术,总之本发明具有节省能耗、热交换效率高、安全性能好、绿色环保、不容易发生泄漏和使用方便的优点。
31.以上所述仅为本发明的较佳实施例而已,并不用以限制本发明,凡在本发明的精神和原则之内,所作的任何修改、等同替换、改进等,均应包含在本发明的保护范围之内。