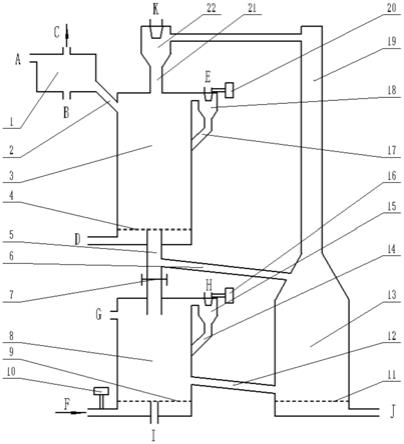
1.本发明涉及冶金领域或者煤炭燃烧脱硫领域或者环境处理领域,特别涉及一种耦合微波技术的化学链燃烧定向脱硫工艺及装置。
背景技术:2.随着经济的快速发展和社会的不断进步,以化石能源为主体的能源消耗量不断上升。然而传统化石能源在生产、运输和利用过程中对环境造成了严重的破坏,其主要燃烧产物co2、so
x
、no
x
等更是当前温室效应和酸雨等环境问题的主要元凶。而化学链燃烧(chemical looping combustion,clc)技术借助载氧体(oxygen carrier,oc)将传统的燃烧过程分为两步进行,利用载氧体中的晶格氧将燃料氧化,避免了燃料与空气的直接接触,从而有效抑制了热力型和快速性no
x
的生成;此外,在燃料反应器出口生成的co2没有被n2稀释,无需设置分离装置,从而避免了co2分离所需的高耗能过程。由此可见,clc技术是一种具有co2内分离的洁净高效燃烧技术。
3.尽管clc技术可以有效抑制no
x
的排放,同时也可以对co2进行捕集,但却无法避免so
x
的产生及排放。受到地理分布与沉积环境的影响,我国煤中硫含量的变化范围较大,约为0.02%
‑
10.48%。硫分>2.00%的煤的保有储量占全国保有储量的9.90%。有效的利用中高硫煤甚至高硫煤,将会一定程度缓解我国能源需求压力。
4.在煤的clc过程中,煤中的硫会对反应过程造成一定的影响。这主要体现在:在燃料反应器中,硫可能会与载氧体发生反应生成含硫化合物,从而对载氧体的反应性能及稳定性产生影响,而气相含硫物质(如h2s、so
x
、cos等)也会对反应器出口的co2纯度造成影响,特别是当co2中含硫气体(h2s、so
x
)的浓度高于50ppm时,会造成s在地表沉积以及对运输的管道的腐蚀等问题,进而影响co2的运输和封存利用;在空气反应器中,载氧体中生成的含硫化合物可能会进一步与空气中的o2发生反应而生成so
x
,从而对环境造成危害。
5.经过前期针对煤中硫在clc过程中的迁移转化规律的研究发现,煤中大部分的硫会在燃料反应器出口以so2和h2s的形式逸出,少量的硫在空气反应器出口以so2的形式逸出。尽管可以通过添加的脱硫剂的方法脱除一部分含硫化合物,但是燃料反应器出口气相含硫化合物的浓度依然可能超过100ppm,从而严重影响了co2的纯度及其后续的捕集和封存过程,如何降低燃料反应器中co2中的含硫气体浓度是亟待解决的问题。
技术实现要素:6.针对现有技术中存在的不足,本发明提供了一种耦合微波技术的化学链燃烧定向脱硫工艺及装置,通过耦合微波技术,在含硫固体燃料进入燃料反应器前,将其中的s元素以气态形式析出,通过与载氧体反应形成金属硫化物,并利用载氧体在各反应器中的循环,使其定向循环至空气反应器再释放s元素并脱除。一方面实现从源头脱硫,使燃料反应器中产生的co2被捕集后无需进一步脱硫而符合利用、封存条件;另一方面,通过载氧体的循环,将s元素定向迁移至空气反应器并释放为含硫气体,可以利用传统的脱硫装置对含硫污染
物进行脱除,降低运行成本,提升可靠性。
7.本发明是通过以下技术手段实现上述技术目的的。
8.一种耦合微波技术的化学链燃烧定向脱硫工艺,包括如下步骤:
9.微波脱硫阶段:将固体燃料和h2加入微波反应器中,通过微波频率使固体燃料进行脱硫反应,脱硫之后的固体燃料进入足氧燃料反应器,产生的含硫气体单独或者与流化介质混合后进入贫氧燃料反应器内;
10.化学链燃烧阶段:脱硫之后的固体燃料与进入足氧燃料反应器内的流化介质发生汽化反应后,与载氧体在足氧燃料反应器中进行还原反应;部分未反应和反应的载氧体通过调节阀进入贫氧燃料反应器,通过控制进入贫氧燃料反应器载氧体的进入量,从而控制贫氧燃料反应器内的过氧系数r;剩余的载氧体输入空气反应器;通过第一旋风分离器将高纯度co2从足氧燃料反应器内分离;
11.含硫气体固定阶段:在贫氧燃料反应器中,被流化介质携带进入的含硫气体与未反应的载氧体生成金属硫化物,流化介质同时起到流化作用,金属硫化物与剩余的载氧体进入空气反应器;通过第二旋风分离器将高温流化介质从贫氧燃料反应器内分离;
12.恢复晶格氧和释放硫阶段:在空气反应器中,反应的载氧体通过与空气反应,使失氧的载氧体恢复为含有晶格氧的载氧体;金属硫化物与空气反应生成载氧体和含硫气体;所述空气反应器内生成的载氧体输入足氧燃料反应器,所述空气反应器内生成的含硫气体通过ar旋风分离器分离。
13.进一步,所述微波反应器工作的微波频率为1ghz,辐射时长为30s。
14.进一步,所述足氧燃料反应器的温度为800
‑
1200℃,所述足氧燃料反应器的过氧系数r为1.9
‑
2.0。
15.进一步,所述贫氧燃料反应器的温度为700
‑
1000℃;通过监测贫氧燃料反应器进口的含硫气体的浓度,控制所述调节阀的开度,使所述贫氧燃料反应器中过氧系数r控制在0.8
‑
0.9。
16.进一步,所述空气反应器内的温度为800
‑
1250℃。
17.一种耦合微波技术的化学链燃烧定向脱硫工艺的的装置,包括微波反应器、空气反应器、足氧燃料反应器和贫氧燃料反应器;所述微波反应器通过脱硫燃料输送管道与足氧燃料反应器连通;所述足氧燃料反应器底部通过燃料反应器连接管路与贫氧燃料反应器连通,所述燃料反应器连接管路上安装带有粉末流量计的调节阀,用于调节贫氧燃料反应器内的过氧系数r;所述足氧燃料反应器底部设有流化介质入口d;所述足氧燃料反应器底部通过第一回料管与空气反应器连通;所述贫氧燃料反应器底部通过第二回料管与空气反应器连通;所述贫氧燃料反应器底部设有混合流化介质入口f;所述空气反应器通过空气反应器提升管与ar旋分分离器连通,所述ar旋分分离器通过ar旋风分离器料腿与足氧燃料反应器连通。
18.进一步,所述空气反应器、足氧燃料反应器和贫氧燃料反应器反应器下部设有布风板。
19.进一步,所述足氧燃料反应器上部安装第一旋风分离器,所述第一旋风分离器上设有高纯度co2出口e,所述第一旋风分离器通过第一旋风分离器料腿连通足氧燃料反应器,用于将部分未反应的固体燃料和载氧体返回足氧燃料反应器;
20.所述贫氧燃料反应器上部安装第二旋风分离器,所述第二旋风分离器上设有高温流化介质出口h,所述第二旋风分离器通过第二旋风分离器料腿连通贫氧燃料反应器,用于使分离出的固体颗粒返回足氧燃料反应器。
21.本发明的有益效果在于:
22.1.本发明所述的耦合微波技术的化学链燃烧定向脱硫工艺,通过增加微波反应器,在特定条件下,固体燃料中的约70%的s以气态h2s形式分离,使足氧燃料反应器出口的含硫气体浓度明显下降,有效的保证了co2的纯度,以及后续的运输及封存过程的有效进行,并且减少了燃料反应器中脱硫剂(石灰石、云母石等)的使用。
23.2.本发明所述的耦合微波技术的化学链燃烧定向脱硫工艺,在贫氧燃料反应器进口和出口分别设置第一烟气分析仪和第二烟气分析仪,用来实时监测气体的浓度,将第一烟气分析仪与调节阀关联,当浓度变化时调节阀随之改变,当含硫气体浓度升高时,则调节阀的开度也调大,从而控制贫氧燃料反应器中载氧体的循环量,保证贫氧燃料反应器中较低的过氧系数r,在该条件下载氧体更易于与含硫气体(h2s、cos、cs2等)反应生成金属硫化物,通过回料管路定向迁移至空气反应器中,在空气反应器中金属硫化物中的s被氧化为so2,只需在空气反应器尾部安装一套传统的脱硫装置,即可达到定向脱硫的效果。
24.3.本发明所述的耦合微波技术的化学链燃烧定向脱硫工艺,载氧体一方面在足氧燃料反应器中用于化学链燃烧供氧,另一方面在贫氧燃料反应器中与含s气体反应,达到固定s元素的目的,便于其定向迁移至空气反应器后释放s元素,减少含s气体对捕集的co2的纯度的影响,充分利用脱硫装置对s元素的脱除。
25.4.本发明所述的耦合微波技术的化学链燃烧定向脱硫工艺,微波反应器用于脱除煤中部分s;足氧燃料反应器接受脱除部分s的煤,燃烧放热,得到低硫co2气体;贫氧燃料反应器接受微波反应器析出的含s气体,通过与载氧体反应生成金属硫化物,固定s元素;空气反应器供氧,为载氧体回复晶格氧,与金属硫化物反应生成so2,将so2释放,利用尾部脱硫装置脱硫。通过几个主要部件的相互配合,将s元素从气态转为固态并定向迁移至空气反应器后转回气态,便于后续脱除工作。
附图说明
26.图1为本发明所述的耦合微波技术的化学链燃烧定向脱硫装置的示意图。
27.图2a为现有技术的铜基载氧体在不同过氧系数r方案下足氧反应器出口含硫气体浓度分布图。
28.图2b为本发明的铜基载氧体在不同过氧系数r方案下足氧反应器出口含硫气体浓度分布图。
29.图3a为现有技术的镍基载氧体在不同过氧系数r方案下足氧反应器出口含硫气体浓度分布图。
30.图3b为本发明的镍基载氧体在不同过氧系数r方案下足氧反应器出口含硫气体浓度分布图。
31.图4为本发明所述的耦合微波技术的化学链燃烧定向脱硫工艺的流程图。
32.图5为本发明铜基载氧体下贫氧燃料反应器中不同过氧系数r下的产物分布图。
33.图中:
[0034]1‑
微波反应器;2
‑
脱硫燃料输送管道;3
‑
足氧燃料反应器;4
‑
第一布风板;5
‑
燃料反应器连接管路;6
‑
第一回料管;7
‑
调节阀;8
‑
贫氧燃料反应器;9
‑
第二布风板;10
‑
第一烟气分析仪;11
‑
ar布风板;12
‑
第二回料管;13
‑
空气反应器;14
‑
第二旋风分离器料腿;15
‑
第二旋风分离器;16
‑
第二烟气分析仪;17
‑
第一旋风分离器料腿;18
‑
第一旋风分离器;19
‑
空气反应器提升管;20
‑
第三烟气分析仪;21
‑
ar旋风分离器料腿;22
‑
ar旋分分离器;a
‑
固体燃料进料口;b
‑
h2进气口;c
‑
含硫气体出口;d
‑
流化介质入口;e
‑
高纯度co2出口;f
‑
混合流化介质入口;g
‑
载氧体入口;h
‑
高温流化介质出口;i
‑
排渣口;j
‑
空气入口;k
‑
含硫贫氧热烟气出口。
具体实施方式
[0035]
下面结合附图以及具体实施例对本发明作进一步的说明,但本发明的保护范围并不限于此。
[0036]
下面详细描述本发明的实施例,所述实施例的示例在附图中示出,其中自始至终相同或类似的标号表示相同或类似的元件或具有相同或类似功能的元件。下面通过参考附图描述的实施例是示例性的,旨在用于解释本发明,而不能理解为对本发明的限制。
[0037]
在本发明的描述中,需要理解的是,术语“中心”、“纵向”、“横向”、“长度”、“宽度”、“厚度”、“上”、“下”、“轴向”、“径向”、“竖直”、“水平”、“内”、“外”等指示的方位或位置关系为基于附图所示的方位或位置关系,仅是为了便于描述本发明和简化描述,而不是指示或暗示所指的装置或元件必须具有特定的方位、以特定的方位构造和操作,因此不能理解为对本发明的限制。此外,术语“第一”、“第二”仅用于描述目的,而不能理解为指示或暗示相对重要性或者隐含指明所指示的技术特征的数量。由此,限定有“第一”、“第二”的特征可以明示或者隐含地包括一个或者更多个该特征。在本发明的描述中,“多个”的含义是两个或两个以上,除非另有明确具体的限定。
[0038]
在本发明中,除非另有明确的规定和限定,术语“安装”、“相连”、“连接”、“固定”等术语应做广义理解,例如,可以是固定连接,也可以是可拆卸连接,或一体地连接;可以是机械连接,也可以是电连接;可以是直接相连,也可以通过中间媒介间接相连,可以是两个元件内部的连通。对于本领域的普通技术人员而言,可以根据具体情况理解上述术语在本发明中的具体含义。
[0039]
如图1所示,本发明所述的耦合微波技术的化学链燃烧定向脱硫的装置,包括微波反应器1、空气反应器13、足氧燃料反应器3和贫氧燃料反应器8;所述微波反应器1上分别设有固体燃料进料口a、h2进气口b和含硫气体出口c;所述微波反应器1通过脱硫燃料输送管道2与足氧燃料反应器3连通;所述足氧燃料反应器3内设有第一布风板4,所述足氧燃料反应器3底部设有流化介质入口d,所述足氧燃料反应器3上部安装第一旋风分离器18,所述第一旋风分离器18上设有高纯度co2出口e,所述高纯度co2出口e处安装第三烟气分析仪20,所述第一旋风分离器18通过第一旋风分离器料腿17连通足氧燃料反应器3,用于将部分未反应的固体燃料和载氧体返回足氧燃料反应器3;所述足氧燃料反应器3底部通过燃料反应器连接管路5与贫氧燃料反应器8连通,所述燃料反应器连接管路5上安装调节阀7,用于调节贫氧燃料反应器8内的过氧系数r;所述足氧燃料反应器3底部通过第一回料管6与空气反应器13连通;所述贫氧燃料反应器8内设有第二布风板9,所述足氧燃料反应器3底部设有混合
流化介质入口f,混合流化介质入口f进入的是流化介质与含硫气体的混合气体,所述混合入口f处安装第一烟气分析仪10,用于检测流化介质与含硫气体中的含硫浓度;所述足氧燃料反应器3上部还设有载氧体入口g,用于补充载氧体。所述贫氧燃料反应器8上部安装第二旋风分离器15,所述第二旋风分离器15上设有高温流化介质出口h,所述高温流化介质出口h处安装第二烟气分析仪16,用于监测贫氧燃料反应器8出口含硫气体浓度;所述第二旋风分离器15通过第二旋风分离器料腿14连通贫氧燃料反应器8,用于使分离出的固体颗粒返回足氧燃料反应器3。所述贫氧燃料反应器8底部通过第二回料管12与空气反应器13连通;所述贫氧燃料反应器8底部设有排渣口i;所述空气反应器13内设有ar布风板11,所述空气反应器13底部设有空气入口j,所述空气反应器13通过空气反应器提升管19与ar旋分分离器22连通,所述ar旋分分离器19通过ar旋风分离器料腿21与足氧燃料反应器3连通。所述ar旋分分离器21上设有含硫贫氧热烟气出口k。
[0040]
实施例1
[0041]
化学链燃烧的载氧体选择合成载氧体,铜基载氧体则采用浸渍法制备cuo/sio2,其中cuo/sio2的质量比例为50:50。固体燃料采用忻州煤,流化介质选择水蒸气和co2的混合气体。表1为忻州煤的工业分析与元素分析。
[0042]
表1忻州煤的工业分析与元素分析
[0043][0044]
煤中无机硫含量较高,其中硫酸盐硫在高温下也不容易分解,尤其是硫酸钙。所以煤中硫有大约10%的硫以硫酸盐硫的形式存在,不参与反应。
[0045]
对于现有技术的化学链双循环流化床:
[0046]
首先关闭微波加热器1相关功能,关闭调节阀7和第二回料管12,利用其余组件模拟传统化学链双循环流化床,新载氧体、脱硫剂和固体燃料从固体燃料入口a进入反应器,足氧燃料反应器3中温度设置为800
‑
1200℃,过氧系数r控制在2.0左右,空气反应器13温度设置为800
‑
1250℃,在此条件下运行,尾部co2收集中so2的浓度如图2a所示,气体中s的浓度为195.24ppm,高于co2其后续的捕集和封存过程的要求浓度。改变燃料反应器中的过氧系数r,其余条件不变,监测尾部co2收集中so2的浓度,如图2a所示,s浓度均超标。其中燃料反应器中发生的主要反应如下:
[0047]
2.153c
58.6833
h
31.75
s
0.91875
(h2o)
6.2361
(n2)
0.9287
+291.658cuo=
[0048]
291.658cu+126.757co2+47.615h2o+1.978so2+1.464n2[0049]
而即使改变足氧燃料反应器中的过氧系数r,其余条件不变,监测尾部co2收集中so2的浓度,如图2a所示,s浓度均超标。
[0050]
本发明所述的耦合微波技术的化学链燃烧定向脱硫工艺,包括如下步骤:
[0051]
微波脱硫阶段:在微波反应器1中,h2从h2进气口b进入,煤从固体燃料进料口a加入,微波频率为1ghz,辐射时长30s,煤中的s元素与h2反应生成h2s,脱硫之后的煤通过脱硫燃料输送管道2进入足氧燃料反应器3,煤粉经微波反应器热解后以含硫合成气体(h2、co、co2、h2o、n2和h2s)的形式逸出进入贫氧反应器,合成气体中h2、co、co2、h2o和n2各自占比为
45%、32%、10%、10%和3%。含硫合成气占煤粉总质量的40%,h2s在合成气中量很少,但是h2s占全硫中的70%。含硫合成气体经运输与流化介质混合后从流化介质与含硫气体混合入口f通入贫氧燃料反应器8底部。
[0052]
煤化学链燃烧阶段:在足氧燃料反应器3中,足氧燃料反应器3为鼓泡床,温度设置为800
‑
1200℃,脱硫后的煤从脱硫燃料输送管道2进入足氧燃料反应器3,在足氧燃料反应器3中与来自空气反应器13中的载氧体混合,并流下行,流化气体(一般为水蒸气和二氧化碳)从流化介质入口d通入足氧燃料反应器3底部,足氧燃料反应器3内的过氧系数r控制在2.0左右,固体燃料与载氧体发生还原反应,还原反应中的氧均来自固体热载体中的晶格氧,载氧体被还原。在足氧燃料反应器3上部设置第一旋风分离器18,产生的气体从高纯度co2出口e离开,冷凝除水后为高纯度的co2。部分未反应的固体燃料和反应与未反应的载氧体从第一旋风分离器料腿17返回足氧燃料反应器3继续参与反应。反应结束后,载氧体经燃料反应器连接管路5从上部足氧燃料反应器3迁移至下部贫氧燃料反应器8,燃料反应器连接管路5上设有调节阀7,通过调节阀7控制贫氧燃料反应器8中载氧体的循环量,从而保证贫氧燃料反应器8中具有较低的过氧系数r,多余载氧体通过燃料反应器连接管路5一侧的第一回料管6直接返回空气反应器13,足氧燃料反应器3中发生的主要反应如下:
[0053]
5.442c
35.21
h
19.05
s
0.18375
(h2o)
3.741
(n2)
0.557
+437.075cuo=
[0054]
437.075cu+191.619co2+72.196h2o+so2+1.516n2[0055]
含硫气体固定阶段:在贫氧燃料反应器8中,贫氧燃料反应器8为鼓泡床,温度设置为700
‑
1000℃,反应与未反应的载氧体通过燃料反应器连接管路5从上部进入贫氧氧燃料反应器8,在贫氧反应器8进口和出口分别安装第一烟气分析仪10和第二烟气分析仪16,进行监测贫氧反应器8混合气体进口f中的含硫气体浓度和贫氧燃料反应器8的高温流化介质出口h中的含硫气体的浓度,将第一烟气分析仪10与调节阀7关联,通过计算将不同浓度下气体所对应的过量系数反馈给调节阀7,再通过控制两个燃料反应器之间的连接管路上的调节阀7的开度,从而控制载氧体的循环量,调节阀7将微波反应器1出口的含硫合成气对应过量系数为0.8
‑
0.9的载氧体掉入贫氧反应器,不同过氧系数r下产物分布如图5所示。在当前的0.8
‑
0.9的过氧系数r时,含硫气体中的h2s气体和未反应的载氧体易发生反应生成铜硫化物(一般为cu2s、cus),含硫气体与流化气体(co2)从流化介质与含硫气体混合入口f通入贫氧燃料反应器8底部,新载氧体从载氧体入口g加入,接着与被流化介质携带进入的含硫气体发生反应,铜硫化物(cu2s、cus)和反应与未反应的载氧体从第二回料管12返回空气反应器13。贫氧燃料反应器8上部设有第二旋风分离器15,分离出的固体颗粒从下部料腿14返回贫氧燃料反应器8继续参与反应,高温流化介质从高温流化介质出口h离开,其中基本不含气态s,该气体经处理后重新从f通入贫氧燃料反应器8中。固体残渣从底部的排渣口i排出。贫氧燃料反应器8发生的主要反应如下:(含硫气体以h2s举例)
[0056]
2cuo+h2s(g)+h2(g)=cu2s+2h2o(g)
[0057]
h2s(g)+cuo=cus+h2o(g)
[0058]
恢复晶格氧释放硫阶段:在空气反应器13中,空气反应器13内温度设置为800
‑
1250℃,
[0059]
铜硫化物和载氧体与从空气反应器13底部通入的空气j发生反应,一方面为失氧的载氧体回复晶格氧,另一方面与铜硫化物发生氧化反应,使铜硫化物恢复为载氧体并释
放含硫气体,主要为so2。经空气反应器提升管19后通过上部的ar旋风分离器22分离,贫氧含硫气体通过含硫贫氧热烟气出口k离开,后接常规脱硫装置脱硫,而得到的固体载氧体颗粒通过ar旋风分离器料腿21送至足氧燃料反应器3与固体燃料反应。完成一轮循环。空气反应器13发生的主要反应如下:
[0060]
2cu+o2(g)=2cuo
[0061]
cu2s+2o2(g)=2cuo+so2(g)
[0062]
2cus+3o2(g)=2cuo+2so2(g)
[0063]
利用第三烟气分析仪20监测该装置尾部co2收集中so2的浓度如图2b所示,在此处收集到的气体含硫浓度为49.10ppm,低于要求的50ppm。改变足氧燃料反应器中的过氧系数r,其余条件不变,监测尾部co2收集中so2的浓度,如图2b所示,s浓度均符合要求。
[0064]
实施例2
[0065]
现有技术化学链双循环流化床:
[0066]
采用镍基载氧体,通过浸渍法制备氧载体nio/al2o3,其中nio/al2o3的质量比例为40:60。其他条件不变,监测得到该发明改进后的装置和传统化学链双循环流化床尾部co2收集中so2的浓度,如图3a所示。传统化学链双循环流化床中燃料反应器中过氧系数r=2.0时,其中发生的主要反应如下:
[0067]
2.092c
58.6833
h
31.75
s
0.478125
(h2o)
6.2361
(n2)
0.7
+280.675nio(s)=
[0068]
280.675ni(s)+122.736co2+46.245h2o+so2+1.464n2[0069]
燃料反应器出口含硫气体浓度在145.70ppm。改变燃料反应器中的过氧系数r,其余条件不变,监测尾部co2收集中so2的浓度,如图3a所示,s浓度均超标。
[0070]
本发明所述的耦合微波技术的化学链燃烧定向脱硫工艺:
[0071]
采用镍基载氧体,通过浸渍法制备氧载体nio/al2o3,其中nio/al2o3的质量比例为40:60。其他条件不变,监测得到该发明改进后的装置和传统化学链双循环流化床尾部co2收集中so2的浓度,如图3b所示。该装置中足氧燃料反应器中过氧系数r=2.0时,其中发生的主要反应如下:
[0072]
10.458c
58.6833
h
31.75
s
0.095625
(h2o)
6.2361
(n2)
0.7
+1395.376nio=
[0073]
1395.376ni+613.682co2+231.227h2o+so2+7.32n2[0074]
足氧燃料反应器出口含硫气体浓度在48.06ppm。改变足氧燃料反应器中的过氧系数r,其余条件不变,监测尾部co2收集中so2的浓度,如图3b所示,s浓度均符合要求。
[0075]
综合以上实施例,对比本发明和现有技术可以发现,采用本发明工艺流程后,在尾气中s元素减少幅度可达67%,效果显著。
[0076]
应当理解,虽然本说明书是按照各个实施例描述的,但并非每个实施例仅包含一个独立的技术方案,说明书的这种叙述方式仅仅是为清楚起见,本领域技术人员应当将说明书作为一个整体,各实施例中的技术方案也可以经适当组合,形成本领域技术人员可以理解的其他实施方式。
[0077]
上文所列出的一系列的详细说明仅仅是针对本发明的可行性实施例的具体说明,它们并非用以限制本发明的保护范围,凡未脱离本发明技艺精神所作的等效实施例或变更均应包含在本发明的保护范围之内。