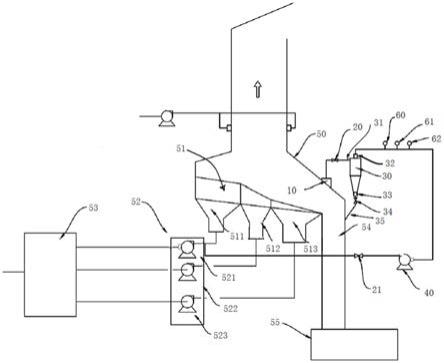
1.本发明涉及生物质燃料锅炉领域,具体地说是一种炉排炉一次风配风调节装置及调节方法。
背景技术:2.炉排炉是生活垃圾、生物质以及成型燃料焚烧处理和热能转化的主要设备,具有技术成熟、设备可靠、燃料适应性广等优点。为了达到促进燃尽、降低污染物排放的目的,炉排炉在配风时一般将燃烧用风分为一次风和二次风,一次风根据入炉燃料热值需要进行加热后从炉排下部送入焚烧炉,使炉排上的燃料干燥、热解、燃烧并燃烬,一次风加热温度一般在150~220℃,极端情况下可到250℃;二次风使用常温风或循环烟气从焚烧炉上部送入焚烧炉,促进气体可燃物燃尽。炉排炉的配风方式对于燃料燃尽、污染物生成和运行经济性都有重要的影响。
3.为解决现有的一次风配风方式经济性差、污染物生成量高的问题,现代焚烧炉多采用多级空预器加热、烟气再循环的方式改进一次风配风,与本发明比较接近的方案有:1.公开号为cn203980295u的实用新型公开了一种分级提升垃圾焚烧炉一次风温度的方式,通过一次风预热器利用汽机一级抽汽将一次风温提高到150℃,然后通过锅炉尾部烟道上的烟气空气预热器,将燃烧空气进一步加热到300℃。该方式的缺点是投资大、管路复杂、一次风系统阻力大,经济性较差。
4.2. 公开号为cn104566389b的发明公开了一种从焚烧炉尾部抽烟气,并从焚烧炉上部送入作为燃尽风的设计方案,这是与本发明最为接近的一种设计。该方案专注于炉内脱硝,实现了炉内低氮燃烧,增加了空气分级的效果,但是不能起到替代一次风的作用,不能降低空预器负荷,且由于燃尽风喷口流速大,系统压损高,运行成本较高。
5.3. 公开号为cn211084077u的实用新型公开了一种高温烟气再循环的设计,将余热锅炉出口高温烟气经过预除尘后由风机提升压力重新返回炉内,循环烟气分为两路进入焚烧炉,一路从炉膛上部进入,一路在给料口下方,循环烟气与进料口垃圾燃料混合后,将垃圾燃料预热干燥后一起进入焚烧炉。该方案能够降低一次风空预器热负荷,降低炉内nox生成量,但缺点是余热锅炉出口的烟气污染物浓度较高,容易引起风机的磨损和腐蚀,泄漏的烟气可能造成环境污染,另外,将高温烟气从进料口与垃圾燃料混合还具有一定的安全风险。
6.4. 公开号为cn 211119357u的实用新型公开了净化后烟气循环利用的方案,在引风机后取烟气,从焚烧炉上部喷入焚烧炉,起到替代部分二次风的作用,以降低炉内nox生成量。但该方式的缺点是无法降低一次风的加热成本,且会增加烟气净化系统的烟气量,整体经济性不佳。
7.现有炉排炉设备一般依赖空气预热器或者高温烟气再循环来提高一次风温度,依靠分级配风、烟气再循环来降低炉内氮氧化物生成量,针对炉排炉,现有的一次风配风技术还存在着如下不足:
1.经济性较差:空预器采用汽包饱和蒸汽或汽轮机一抽蒸汽进行加热,大量使用蒸汽会降低发电系统热效率,导致高品位能量的低效使用。
8.2.高温烟气循环方式有污染物泄漏以及设备腐蚀的风险:余热锅炉出口高温烟气含有高浓度污染物,如二氧化硫、氯化氢等,高温烟气还含有大量颗粒物,会导致设备腐蚀,密封不严密时会有污染物泄漏的风险。
9.3.常规烟气再循环取净化后低温烟气只能起到降低炉内nox生成量的作用,无法实现加热一次风的效果。
技术实现要素:10.本发明要解决的技术问题是针对上述现有技术的不足,而提供一种炉排炉一次风配风调节装置及调节方法,该发明可以减少干燥段一次风的用量,减少空预器热负荷,同时控制炉内总过量空气系数,降低氮氧化物的生成量,减少排烟热损失,提高系统经济效益。
11.为解决上述技术问题,本发明采用的技术方案是:一种炉排炉一次风配风调节装置,其特征在于:包括安装在炉排炉上的取烟气口、入口电动关断阀、旋风分离器、循环风机。
12.炉排炉包括设置在炉排炉炉膛内部的燃烧风室和落渣井。
13.炉排炉还包括与炉排炉炉膛相连的一次风机,以及与一次风机相连接的一次风空预器。
14.一次风通过一次风空预器后由一次风机送入燃烧风室。
15.所述燃烧风室包括水平方向顺次紧密排列的干燥段风室、燃烧段风室和燃尽段风室。
16.所述燃尽段风室一侧紧靠燃烧段风室,燃尽段风室的另一侧紧靠落渣井;所述落渣井顶端高度低于燃尽段风室顶端高度。
17.所述一次风机包括干燥段一次风机、燃烧段一次风机、燃尽段一次风机;干燥段风室和干燥段一次风机相连;燃烧段风室和燃烧段一次风机相连;燃尽段风室和燃尽段一次风机相连。
18.所述取烟气口设置在落渣井上方的炉拱处。
19.所述旋风分离器包括旋风分离器烟气入口、旋风分离器烟气出口、储灰仓和输灰管;所述旋风分离器烟气入口和旋风分离器烟气出口分别设置在旋风分离器顶部两侧;所述储灰仓设置在旋风分离器的底部;所述输灰管一端连接储灰仓,另一端连接至落渣井。
20.所述旋风分离器烟气入口通过烟气管路与取烟气口相连接,旋风分离器烟气出口通过烟气管路与循环风机的进风口相连接,循环风机的出风口通过烟气管路连接到干燥段一次风机的出风口气体管路上。
21.所述入口电动关断阀设置在取烟气口和旋风分离器烟气入口之间的烟气管路上。
22.作为本发明的进一步优选,所述储灰仓底部设置有周期性开启的卸灰阀。
23.作为本发明的进一步优选,落渣井的底部设置有定期除渣的捞渣机。
24.作为本发明的进一步优选,旋风分离器和循环风机之间的烟气管路上设置有用于监测一氧化碳浓度值的一氧化碳测点。
25.作为本发明的进一步优选,旋风分离器和循环风机之间的烟气管路上设置有用于
监测循环烟气温度值的温度测点。
26.作为本发明的进一步优选,旋风分离器和循环风机之间的烟气管路上设置有用于监测循环烟气量的流量计。
27.作为本发明的进一步优选,循环风机出风口和干燥段一次风机出风口之间的烟气管路上设置有出口电动关断阀。
28.作为本发明的进一步优选,循环风机采用变频器控制和水冷冷却方式;循环风机的风机叶片使用高强度、耐腐蚀合金钢为基材,且风机叶片表面涂装耐磨损的玻璃纤维增强树脂。
29.一种炉排炉配风调节方法,包括如下步骤:s1、开启开启入口电动关断阀,开启循环风机,从炉排炉燃尽段风室上方炉拱处的取烟气口抽取循环烟气。
30.s2、抽取的循环烟气通过旋风分离器烟气入口进入旋风分离器,分离出颗粒物后,循环烟气从旋风分离器烟气出口通过循环风机送至干燥段一次风机出口;颗粒物短期储存在储灰仓中,卸灰阀周期性开启,将颗粒物通过输灰管输送到落渣井内,并通过捞渣机除去。
31.s3、循环烟气与干燥段一次风混合后一起送入干燥段风室,穿过炉排间隙进入炉排炉燃烧区内。
32.s4、使用流量计,观测循环烟气的烟气流量,通过调节循环风机变频器,控制循环风机风门开度,使循环烟气量与总一次风量的比例在10%~25%之间。
33.s5、通过一氧化碳测点和温度测点,得到循环烟气中一氧化碳的浓度和循环烟气的温度,当一氧化碳浓度大于等于6000ppm且小于8000ppm、烟气温度大于等于400℃且小于450℃时,调节循环风机变频器,减小风机风门开度,使烟气中一氧化碳浓度小于6000ppm且循环烟气温度小于400℃;当一氧化碳浓度大于等于8000ppm,或者烟气温度大于等于450℃时,关闭循环风机,关闭入口电动关断阀,以保护烟气循环系统。
34.本发明具有如下有益效果:1、循环烟气替代了一部分乃至全部的干燥段一次风,减少了空气预热器的加热负荷,提高了系统整体的经济性。
35.2、由于循环烟气温度高于一次风温度,因此循环烟气可以起到更好的助燃效果,尤其适合在燃料热值比较低的工况下使用。
36.3、一次风配风调节后,一次风总量减少,使二次风口以下空间整体过量空气系数减小,在炉排炉的燃烧区形成了低过量空气的还原性燃烧气氛,有利于减少燃烧过程中氮氧化物的生成量,更加绿色环保。
37.4、系统设备少,投资节省,且系统阻力小,运行成本低,相比将循环烟气作为二次风的方式,将循环烟气作为一次风可以大大减少系统的阻力,运行成本显著节省。
附图说明
38.图1是本发明一种炉排炉一次风配风调节装置的示意图。
39.其中有:10.取烟气口;20.入口电动关断阀;21.出口电动关断阀;30.旋风分离器;31. 旋
风分离器烟气入口;32. 旋风分离器烟气出口;33.储灰仓;34.卸灰阀;35.输灰管;40.循环风机;50.炉排炉;51.燃烧风室;511. 干燥段风室;512. 燃烧段风室;513. 燃尽段风室;52.一次风机;521.干燥段一次风机;522.燃烧段一次风机;523.燃尽段一次风机;53. 一次风空预器;54. 落渣井;55. 捞渣机;60.一氧化碳测点;61.温度测点;62.流量计。
具体实施方式
40.下面结合附图和具体较佳实施方式对本发明作进一步详细的说明。
41.本发明的描述中,需要理解的是,术语“左侧”、“右侧”、“上部”、“下部”等指示的方位或位置关系为基于附图所示的方位或位置关系,仅是为了便于描述本发明和简化描述,而不是指示或暗示所指的装置或元件必须具有特定的方位、以特定的方位构造和操作,“第一”、“第二”等并不表示零部件的重要程度,因此不能理解为对本发明的限制。本实施例中采用的具体尺寸只是为了举例说明技术方案,并不限制本发明的保护范围。
42.如图1所示,一种炉排炉一次风配风调节装置,包括安装在炉排炉50上的取烟气口10、入口电动关断阀20、旋风分离器30和循环风机40。
43.炉排炉50包括设置在炉排炉50炉膛内部的燃烧风室51和落渣井54。
44.炉排炉50还包括与炉排炉50炉膛相连的一次风机52,以及与一次风机52相连接的一次风空预器53。
45.一次风通过一次风空预器53后由一次风机52送入燃烧风室51。
46.燃烧风室51包括水平方向顺次紧密排列的干燥段风室511、燃烧段风室512和燃尽段风室513。
47.燃尽段风室513一侧紧靠燃烧段风室512,燃尽段风室513的另一侧紧靠落渣井54;所述落渣井54顶端高度低于燃尽段风室513顶端高度。
48.一次风机52包括干燥段一次风机521、燃烧段一次风机522、燃尽段一次风机523;干燥段风室511和干燥段一次风机521相连;燃烧段风室512和燃烧段一次风机522相连;燃尽段风室513和燃尽段一次风机523相连。
49.取烟气口10设置在落渣井54上方的炉拱处。
50.一次风通常来自垃圾仓或锅炉间空气,一次风通过一次风空预器53加热后分别由干燥段一次风机521、燃烧段一次风机522和燃尽段一次风机523送入干燥段风室511、燃烧段风室512和燃尽段风室513,经炉排间隙进入炉排上部的料层,提供燃料干燥、燃烧所需的空气,一次风的加热温度根据燃料热值而定,一般在150℃~250℃范围内。
51.旋风分离器30包括旋风分离器烟气入口31、旋风分离器烟气出口32、储灰仓33和输灰管35。旋风分离器烟气入口31和旋风分离器烟气出口32分别设置在旋风分离器30顶部两侧;储灰仓33设置在旋风分离器30的底部;输灰管35一端连接储灰仓33,另一端连接至落渣井54。储灰仓33用于短期储存旋风分离器30分离出的颗粒物,通过卸灰阀34定期经过输灰管35排至落渣井54内,并通过捞渣机55送至灰库处理。
52.炉排炉50的燃尽段炉排处于料层燃烧的末期,主要为参与固定碳的燃尽过程,燃烧速度较慢,且由于风量供大于求,产生的燃烧后烟气温度较低,一般为250℃~450℃,烟气成分主要为空气,含有一定量co2和微量co,但是含有一定量的粉尘,约1~5g/m3,因而需要旋风分离器30分离颗粒物。
53.旋风分离器烟气入口31通过烟气管路与取烟气口10相连接,旋风分离器烟气出口32通过烟气管路与循环风机40的进风口相连接,循环风机40的出风口通过烟气管路连接到干燥段一次风机521的出风口气体管路上。
54.使用循环风机40抽取干燥段风室511内的高温烟气经过循环后替代了一部分乃至全部的干燥段一次风,由于循环烟气温度高于一次风温度,因此循环烟气可以起到更好的助燃效果,尤其适合在燃料热值比较低的工况下使用,减少了空气预热器的加热负荷,提高了系统整体的经济性。
55.入口电动关断阀20设置在取烟气口10和旋风分离器烟气入口31之间的烟气管路上,用于在不需使用炉排炉配风调节装置切断循环烟气。
56.旋风分离器30和循环风机40之间的烟气管路上设置有一氧化碳测点60,,用于监测一氧化碳浓度值。
57.旋风分离器30和循环风机40之间的烟气管路上设置有温度测点61,用于监测循环烟气温度值。
58.旋风分离器30和循环风机40之间的烟气管路上设置有流量计62,用于监测循环烟气量。
59.循环风机40出风口和干燥段一次风机521出风口之间的烟气管路上设置有出口电动关断阀21,用于在紧急情况下关闭炉排炉配风调节装置。
60.循环风机40采用变频器控制,水冷冷却方式;风机叶片使用高强度、耐腐蚀合金钢为基材,且风机叶片表面涂装耐磨损的玻璃纤维增强树脂,增加了风机的抗腐蚀耐磨损的能力。
61.炉排炉一次风配风经过调节后,一次风总量减少,使二次风口以下空间整体过量空气系数减小,在炉排炉的燃烧区形成了低过量空气的还原性燃烧气氛,有利于减少燃烧过程中氮氧化物的生成量,更加绿色环保。
62.相比于其他改进方法,本发明投资少、系统简单、运行成本低、系统设备少、投资节省且系统阻力小,运行成本低,相比将循环烟气作为二次风的方式,将循环烟气作为一次风可以大大减少系统的阻力,运行成本显著节省。
63.一种炉排炉配风调节方法,包括如下步骤:s1、开启开启入口电动关断阀20,开启循环风机40,从炉排炉70的落渣井54上方的炉拱处上方炉拱处的取烟气口10抽取循环烟气;s2、抽取的循环烟气送入旋风分离器烟气入口31,经过旋风分离器30分离出颗粒物后,循环烟气从旋风分离器烟气出口32通过循环风机40送至干燥段一次风机521的出口管路;s3、循环烟气与干燥段一次风混合后一起送入干燥段风室511,穿过炉排间隙进入炉排炉50燃烧区内;s4、通过流量计62,得到循环烟气的烟气流量;调节循环风机40变频器,控制循环风机40风门开度,使循环烟气量与总一次风量的比例在10%~25%之间;s5、通过一氧化碳测点60和温度测点61,得到循环烟气中一氧化碳的浓度和循环烟气的温度,当一氧化碳浓度大于等于6000ppm且小于8000ppm、烟气温度大于等于400℃且小于450℃时,调节循环风机40变频器,减小风机风门开度,使烟气中一氧化碳浓度小于
6000ppm且循环烟气温度小于400℃;当一氧化碳浓度大于等于8000ppm,或者烟气温度大于等于450℃时,关闭循环风机40,关闭入口电动关断阀20,以保护烟气循环系统。以上详细描述了本发明的优选实施方式,但是,本发明并不限于上述实施方式中的具体细节,在本发明的技术构思范围内,可以对本发明的技术方案进行多种等同变换,这些等同变换均属于本发明的保护范围。