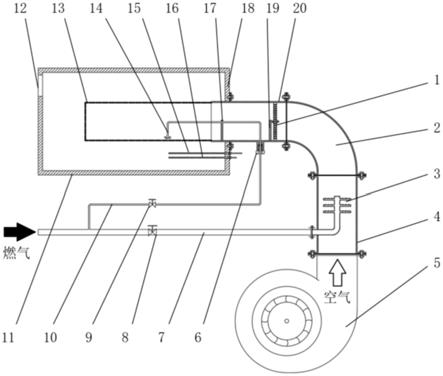
1.本实用新型涉及燃烧器技术领域,具体涉及一种金属表面燃烧器。
背景技术:2.近年来,随着国家环保法规日益严格,碳达峰和碳中和政策逐步落地,对生产制造环节中的节能减排技术提出了更高的要求。金属表面燃烧技术利用微孔金属筒和预混式燃烧,有效地提高了燃烧的均匀性和稳定性,避免燃料集中燃烧和局部高温,从而有效地降低锅炉的nox排放并提高锅炉的燃烧效率。
3.现有的金属表面燃烧器点火结构过于冗杂,造成流场和燃烧的不均匀分布,也制约了燃烧器尺寸的小型化。同时,现有的金属表面燃烧器的预混段结构过于简短,燃气不能与空气充分预混,也会导致局部燃烧强度过大,造成低效率、高nox排放的不良情况。
4.现有金属表面燃烧器的点火结构和预混段结构还有很大的提升空间。
技术实现要素:5.针对现有技术中存在的上述问题,本实用新型提供一种金属表面燃烧器,该燃烧器的结构更加紧凑,燃气预混效果更优,可在小炉膛锅炉中实现稳定燃烧和nox超低排放。
6.本实用新型公开了一种金属表面燃烧器,包括:
7.预混管道,所述预混管道的进气端连接有风机,所述预混管道内设有枝状燃气分布器,所述枝状燃气分布器的进气端穿过所述预混管道后与主燃气管相连;
8.末端管道,所述末端管道穿设在炉膛前墙上,所述末端管道的炉膛外进气端与所述预混管道的出气端相连、炉膛内出气端连接有微孔金属筒;所述末端管道内设有阻燃盘,所述微孔金属筒内设有内置点火喷嘴,所述内置点火喷嘴与点火燃气管相连,所述点火燃气管与所述主燃气管相连。
9.作为本实用新型的进一步改进,所述预混管道的出气端通过弯头与所述末端管道的进气端相连。
10.作为本实用新型的进一步改进,所述枝状燃气分布器包括:垂直管、轴心管和分支管;
11.所述垂直管垂直穿设在所述预混管道上,所述垂直管的进气端与所述主燃气管相连,所述垂直管的出气端与所述轴心管的进气端相连;
12.所述轴心管同轴设置在所述预混管道内,所述轴心管的出气端连通有多个所述分支管,每个所述分支管上均布有多个燃气孔。
13.作为本实用新型的进一步改进,所有所述分支管为多层结构且每层包含多个分支管,上下相邻两层的分支管交错布设。
14.作为本实用新型的进一步改进,所述阻燃盘通过阻燃盘支架固定于所述末端管道的内壁,且位置靠近所述末端管道的进气端。
15.作为本实用新型的进一步改进,所述点火燃气管通过燃气管支架固定于所述末端
管道的内壁,所述点火燃气管的末端设置所述内置点火喷嘴,所述内置点火喷嘴靠近所述微孔金属筒的内壁面。
16.作为本实用新型的进一步改进,所述点火燃气管经密封螺栓穿过所述末端管道的侧壁,并由此进入所述微孔金属筒的内部。
17.作为本实用新型的进一步改进,还包括:离子点火器和火焰探测器;
18.所述离子点火器和火焰探测器穿过所述炉膛前墙插入炉膛内部,位置靠近所述内置点火喷嘴;所述内置点火喷嘴的开孔朝向所述离子点火器和火焰探测器。
19.作为本实用新型的进一步改进,所述主燃气管安装有主燃气阀,点火燃气管安装有点火燃气阀。
20.与现有技术相比,本实用新型的有益效果为:
21.本实用新型内置点火喷嘴和点火燃气管,使燃烧器的体积小、结构简单,在满足燃烧器点火需求的同时,对燃烧器内部流场干扰小,提高了流动和燃烧的均匀性;
22.本实用新型枝状燃气分布器的燃气孔均匀而密集地分布在预混管道内部空间,燃气经燃气孔进入预混管道,避免了燃气在局部空间的聚集,让燃气和空气在预混管道内迅速混合;在弯头、阻燃盘和末端管道的进一步混合和扰动下,燃气和空气得到充分预混,提高了燃烧的均匀性和稳定性,降低了烟气的nox含量;
23.本实用新型的阻燃盘和枝状燃气分布器具有狭窄的流道,可以有效的防止回火的发生,提高了燃烧器的安全性。
附图说明
24.图1为本实用新型一种实施例公开的金属表面燃烧器的结构示意图;
25.图2为图1中预混管道和枝状燃气分布器的结构示意图;
26.图3为图1中末端管道、阻燃盘和内置点火喷嘴的结构示意图。
27.图中:
28.1、阻燃盘;2、弯头;3、枝状燃气分布器;31、垂直管;32、轴心管;33、分支管;34、燃气孔;4、预混管道;5、鼓风机;6、密封螺栓;7、主燃气管;8、主燃气阀;9、点火燃气阀;10、点火燃气管;11、炉膛;12、炉膛出口;13、微孔金属筒;14、内置点火喷嘴;15、离子点火器;16、火焰探测器;17、燃气管支架;18、炉膛前墙;19、阻燃盘支架;20、末端管道。
具体实施方式
29.为使本实用新型实施例的目的、技术方案和优点更加清楚,下面将结合本实用新型实施例中的附图,对本实用新型实施例中的技术方案进行清楚、完整地描述,显然,所描述的实施例是本实用新型的一部分实施例,而不是全部的实施例。基于本实用新型中的实施例,本领域普通技术人员在没有做出创造性劳动的前提下所获得的所有其他实施例,都属于本实用新型保护的范围。
30.下面结合附图对本实用新型做进一步的详细描述:
31.为进一步提高燃烧器的燃烧效率和稳定性、降低烟气排放,本实用新型通过紧凑的燃烧器结构和高效的预混段设计,可以达到更好的流场和燃气预混;同时,本实用新型通过阻燃盘的设计,可预防爆燃和回火的发生,提升设备的安全性能。为此,如图1-3所示,本
实用新型提供一种金属表面燃烧器,该燃烧器特别适应小炉膛锅炉使用;其包括:阻燃盘1、弯头2、枝状燃气分布器3、预混管道4、鼓风机5、密封螺栓6、主燃气管7、主燃气阀8、点火燃气阀9、点火燃气管10、炉膛11、炉膛出口12、微孔金属筒13、内置点火喷嘴14、离子点火器15、火焰探测器16、燃气管支架17、炉膛前墙18、阻燃盘支架19和末端管道20;具体的:
32.本实用新型的预混管道4和末端管道20为圆筒通道,预混管道4的进气端与鼓风机5的出风口相连、出气端与弯头2的进气端相连,弯头2的出气端末端管道20的进气端相连,末端管道20的出气端与微孔金属筒13相连;其中,预混管道4、弯头2和末端管道20之间的连接通过螺栓连接,末端管道20穿设在炉膛前墙18上,末端管道20的进气端设置在炉膛11外、出气端设置在炉膛11内,末端管道20在炉膛前墙18的管孔处进行密封固定。
33.本实用新型的预混管道4内设有枝状燃气分布器3,枝状燃气分布器3的进气端穿过预混管道4后与主燃气管7相连;通过主燃气管7和枝状燃气分布器3进入的燃气与通过鼓风机5进入的空气,在预混管道4内进行预混。具体的,如图2所示,本实用新型的枝状燃气分布器3包括:垂直管31、轴心管32、分支管33和燃气孔34;垂直管31垂直穿设在预混管道4上,垂直管4的外部进气端与主燃气管7相连,垂直管31的内部出气端与轴心管32的进气端相连;轴心管32同轴设置在预混管道4内,轴心管32的出气端连通有多个分支管33,每个分支管33在远离鼓风机5的方向上均匀布置有多个燃气孔34。进一步,所有分支管33为多层结构且每层包含多个分支管,上下相邻两层的分支管交错布设。
34.本实用新型的末端管道20内设有阻燃盘1,优选阻燃盘1通过阻燃盘支架19固定于末端管道20的内壁,且位置靠近弯头2;微孔金属筒13内设有内置点火喷嘴14,内置点火喷嘴14与点火燃气管10相连,点火燃气管10与主燃气管7相连。具体的:点火燃气管10经密封螺栓6穿过末端管道20的侧壁,并由此进入微孔金属筒13的内部;在末端管道20内,点火燃气管10通过燃气管支架17固定于末端管道20的内壁,点火燃气管10的末端设置内置点火喷嘴14,内置点火喷嘴14靠近微孔金属筒20的内壁面;离子点火器15和火焰探测器16穿过炉膛前墙18插入炉膛11内部,位置靠近内置点火喷嘴14;内置点火喷嘴14的开孔朝向离子点火器15和火焰探测器16;主燃气管7安装有主燃气阀8,点火燃气管10安装有点火燃气阀9。
35.本实用新型的工作原理为:
36.燃烧器点火工作前,主燃气阀8和点火燃气阀关闭9,燃气不进入燃烧器;鼓风机5开启进行吹扫,有效预防点火阶段爆燃的产生;
37.燃烧器点火时,主燃气阀8保持关闭,点火燃气阀9开启,离子点火器15工作,少量燃气从内置点火喷嘴喷14出并被点燃;当火焰探测器16检测到稳定的火焰信号后,开启主燃气阀8和鼓风机5,大量燃气通过枝状燃气分布器3进入预混管道4,与空气充分混合,流经弯头2和末端管道20,最终在微孔金属筒13的表面被点燃,待燃烧稳定后关闭点火燃气阀门9;
38.若点火失败或因其他原因火焰熄灭,迅速关闭主燃气阀8和点火燃气阀9,保持鼓风机5开启进行持续吹扫,以防止回火和再次点火时爆燃的发生。
39.本实用新型的优点为:
40.本实用新型内置点火喷嘴和点火燃气管,使燃烧器的体积小、结构简单,在满足燃烧器点火需求的同时,对燃烧器内部流场干扰小,提高了流动和燃烧的均匀性;
41.本实用新型枝状燃气分布器的燃气孔均匀而密集地分布在预混管道内部空间,燃
气经燃气孔进入预混管道,避免了燃气在局部空间的聚集,让燃气和空气在预混管道内迅速混合;在弯头、阻燃盘和末端管道的进一步混合和扰动下,燃气和空气得到充分预混,提高了燃烧的均匀性和稳定性,降低了烟气的nox含量;
42.本实用新型的阻燃盘和枝状燃气分布器具有狭窄的流道,可以有效的防止回火的发生,提高了燃烧器的安全性。
43.以上仅为本实用新型的优选实施例而已,并不用于限制本实用新型,对于本领域的技术人员来说,本实用新型可以有各种更改和变化。凡在本实用新型的精神和原则之内,所作的任何修改、等同替换、改进等,均应包含在本实用新型的保护范围之内。